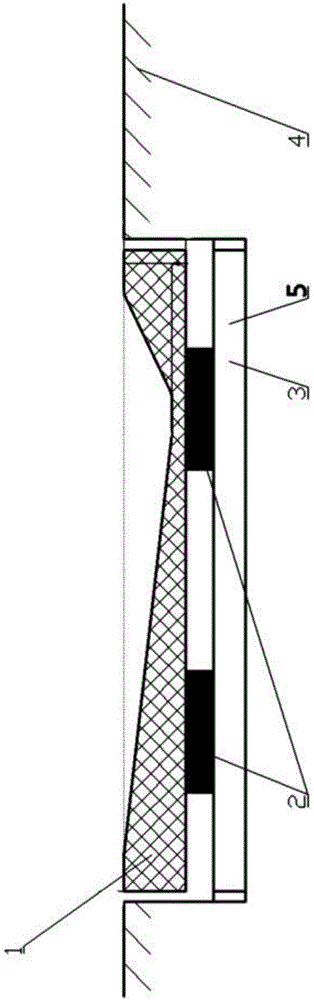
本实用新型涉及汽车零部件模拟试验领域,具体涉及一种用于车轮模拟实况冲击试验的凹陷障碍物。
背景技术:
:目前在进行车轮模拟冲击试验时,往往采用台架方法来进行径向冲击、13度冲击等试验,从而考察车轮在各种冲撞条件下的反应并判断车轮是否符合汽车生产商及使用者的要求。台架试验是对现实驾驶条件的模拟,其模拟结果可能无法完全反映实际驾驶过程中遇到各种不理想路面的真实反应。为了提供交通事故条件下的车辆质量,整车厂商往往使用真车冲撞墙面等试验来考察整车在交通事故下的表现。然而目前还没有针对车轮等零部件在非事故条件下的考验来进行试验的方法和装置。技术实现要素:为了在非事故条件下对车轮等零部件进行模拟实况冲击试验,本实用新型提供了一种用于车轮模拟实况冲击试验的凸起障碍物。本领域的技术人员知道,在汽车的行驶过程中可能遭遇路面上的凹陷物。该凹陷物可能是泥土路面、沥青路面和水泥路面上的凹陷部分,路面涂层型减速带等等。汽车当行驶通过以上的路面结构时,车胎将对车轮造成一定的作用力。该作用力随后通过轴和悬挂系统分散到车身。作为直接面对冲击的汽车零部件,车轮在这一行驶事件中可能遭受损伤。作为车轮生产企业,中信戴卡希望在更接近现实状态的条件下进行车轮性能检测。因此,本实用新型的实用新型人开发了如下的凹陷障碍物。在本实用新型的一个方面,提供了一种用于车轮模拟实况冲击试验的凸起障碍物,由凹陷障碍物块(1)、三轴力传感器(2)、传感器底座(3)和槽沟(5)构成,其特征在于:所述的槽沟(5)位于测试路面(4)上;传感器底座(3)安放在槽沟(5)的底部;三轴力传感器(2)的一端安装在传感器底座(3)的上表面,另一端安装到凹陷障碍物块(1)的下表面;所述的凹陷障碍物块(1)沿槽沟(5)的长度方向的横截面具有梯形的凹陷;并且,所述的凹陷障碍物块(1)设置为当安装完毕后,凹陷的梯形的底边和路面(4)平齐。在本实用新型一个优选的方面,所述的凹陷障碍物块(1)沿槽沟(5)的长度方向的横截面上部的梯形的底边为80-120mm,顶边为1200-1500mm,高为80-120mm,凹陷障碍物块(1)的顶部宽度为1400-1800mm。在本实用新型一个优选的方面,所述的凹陷障碍物块(1)沿槽沟(5)的长度方向的横截面的等腰梯形部分的长底边长度为1400mm,短底边长度为100mm,梯形的高度为100mm,凹陷障碍物块(1)的顶部宽度为1600mm。在本实用新型一个优选的方面,所述的三轴力传感器(2)的量程为72kN,精确度为1%。在本实用新型一个优选的方面,凹陷障碍物块(1)由钢、铸铁、工程塑料或者铝合金制成。在本实用新型一个优选的方面,所述的凹陷障碍物块(1)的上表面覆盖有保护层。在本实用新型一个优选的方面,所述的保护层是厚度为5~10mm的橡胶、塑料、钢或者铝合金。在本实用新型一个优选的方面,所述的三轴力传感器(2)的数量为四个。在本实用新型一个优选的方面,所述的凹陷障碍物选自以下的一种:(A)所述的凹陷障碍物块(1)沿槽沟(5)的长度方向的横截面的等腰梯形部分的长底边长度为1400mm,短底边长度为100mm,梯形的高度为100mm,凹陷障碍物块(1)的顶部宽度为1600mm;(B)所述的凹陷障碍物块(1)沿槽沟(5)的长度方向的横截面的等腰梯形部分的长底边长度为1200mm,短底边长度为80mm,梯形的高度为80mm,凹陷障碍物块(1)的顶部宽度为1400mm;(C)所述的凹陷障碍物块(1)沿槽沟(5)的长度方向的横截面的等腰梯形部分的长底边长度为1500mm,短底边长度为120mm,梯形的高度为120mm,凹陷障碍物块(1)的顶部宽度为1800mm。在本实用新型的其他方面,还提供了以下的技术方案:一种车轮模拟实况冲击试验的标准障碍物,由标准障碍物块(1)、三轴力学传感器(2)、传感器底座(3)构成,按图2所示镶嵌在路面上。标准障碍物块(如图3所示),宽度为500mm,截面的实际形状是在一个1600×170的矩形上,挖去一个倒梯形块。挖去的梯形形状为:长底边1300mm,短底边100mm,高100mm。短底边两端点到长底边端点长度分别为250mm,1050mm。三轴力学传感器购自密西根科技公司。传感器底座用于固定传感器。连接方式:在路面上事先挖好的凹坑中放置传感器底板(3)并通过膨胀螺栓将底板固定好,取四个三轴力学传感器(2)布置在传感器底板(3)上,用螺栓固定好。将标准障碍物放置与四个三轴传感器上,用螺栓将传感器与标准障碍物块固定在一起。本实用新型的凹陷障碍物的优点在于:结构简单、检测灵敏且能够很好地模拟道路表面的各种凹陷障碍物对车轮的影响。附图说明以下,结合附图来详细说明本实用新型的实施方案,其中:图1是本实用新型用于车轮模拟实况冲击试验的凹陷障碍物的布置平面图;图2是本实用新型用于车轮模拟实况冲击试验的凹陷障碍物的剖面结构原理图;图3是本实用新型用于车轮模拟实况冲击试验的凹陷障碍物的凹陷障碍物块(1)的俯视图;以及图4是本实用新型用于车轮模拟实况冲击试验的凹陷障碍物的凹陷障碍物块(1)的截面图;图中:1-凹陷障碍物块、2-三轴力传感器、3-传感器底座、4-路面、5-槽沟。具体实施方式除非另外地说明,本实用新型中所使用的三轴力学传感器购自密西根科技公司,其产品型号为TR3D-C-16K。该三轴力学传感器是应变类型的三轴力学传感器,其精确度为1%,量程为72kN。尽管做了以上的限定,本领域一般技术人员知道,其他类型的三轴力学传感器也可以被使用,只要其满足三个方向测力的条件。本领域一般技术人员还知道,还可以使用灵敏度更高且量程更广的六分力传感器来作为检测传感器使用。对比例1本对比例的凹陷障碍物是以下的物品:在试验用道路上首先开挖一道宽度为1650mm的沟槽,并且在沟槽内安装传感器底座。在传感器底座上安装四只三轴力传感器,并且在力传感器上再安装自制的钢板,钢板表面与路面平齐,且钢板表面有长(道路方向)1000mm,宽400mm,深100mm的矩形深坑,然后在矩形坑两端铺垫泥土,直到两侧都成为缓坡。这种道路障碍通常见于我国道路上因路面破损而出现的凹坑。用一定速度的车辆去通过障碍物,设置在障碍物底下的四个三轴力传感器连接高速数字采集仪,能得到冲击过程中的力学曲线,通过对四个传感器进行数学耦合,计算出障碍物的受的合力。实施例1本实施例的凹陷障碍物由凹陷障碍物块(1)、三轴力传感器(2)、传感器底座(3)和槽沟(5)构成,其特征在于:所述的槽沟(5)位于测试路面(4)上;传感器底座(3)安放在槽沟(5)的底部;三轴力传感器(2)的一端安装在传感器底座(3)的上表面,另一端安装到凹陷障碍物块(1)的下表面;所述的凹陷障碍物块(1)沿槽沟(5)的长度方向的横截面具有梯形的凹陷;并且,所述的凹陷障碍物块(1)设置为当安装完毕后,凹陷的梯形的底边和路面(4)平齐。所述的凹陷障碍物块(1)沿槽沟(5)的长度方向的横截面的等腰梯形部分的长底边长度为1400mm,短底边长度为100mm,梯形的高度为100mm,凹陷障碍物块(1)的顶部宽度为1600mm。在道路上设置的凹坑中,将障碍物、三轴力传感器、传感器底板按上述连接方式固定,用一定速度的车辆去通过障碍物,设置在障碍物底下的四个三轴力学传感器连接高速数字采集仪,能得到冲击过程中的力学曲线,通过对四个传感器进行数学耦合,计算出障碍物的受的合力,即为冲击力。实施例2本实施例的凹陷障碍物由凹陷障碍物块(1)、三轴力传感器(2)、传感器底座(3)和槽沟(5)构成,其特征在于:所述的槽沟(5)位于测试路面(4)上;传感器底座(3)安放在槽沟(5)的底部;三轴力传感器(2)的一端安装在传感器底座(3)的上表面,另一端安装到凹陷障碍物块(1)的下表面;所述的凹陷障碍物块(1)沿槽沟(5)的长度方向的横截面具有梯形的凹陷;并且,所述的凹陷障碍物块(1)设置为当安装完毕后,凹陷的梯形的底边和路面(4)平齐。所述的凹陷障碍物块(1)沿槽沟(5)的长度方向的横截面的等腰梯形部分的长底边长度为1200mm,短底边长度为80mm,梯形的高度为80mm,凹陷障碍物块(1)的顶部宽度为1400mm。在道路上设置的凹坑中,将障碍物、三轴力传感器、传感器底板按上述连接方式固定,用一定速度的车辆去通过障碍物,设置在障碍物底下的四个三轴力学传感器连接高速数字采集仪,能得到冲击过程中的力学曲线,通过对四个传感器进行数学耦合,计算出障碍物的受的合力,即为冲击力。实施例3本实施例的凹陷障碍物由凹陷障碍物块(1)、三轴力传感器(2)、传感器底座(3)和槽沟(5)构成,其特征在于:所述的槽沟(5)位于测试路面(4)上;传感器底座(3)安放在槽沟(5)的底部;三轴力传感器(2)的一端安装在传感器底座(3)的上表面,另一端安装到凹陷障碍物块(1)的下表面;所述的凹陷障碍物块(1)沿槽沟(5)的长度方向的横截面具有梯形的凹陷;并且,所述的凹陷障碍物块(1)设置为当安装完毕后,凹陷的梯形的底边和路面(4)平齐。所述的凹陷障碍物块(1)沿槽沟(5)的长度方向的横截面的等腰梯形部分的长底边长度为1500mm,短底边长度为120mm,梯形的高度为120mm,凹陷障碍物块(1)的顶部宽度为1800mm。在道路上设置的凹坑中,将障碍物、三轴力传感器、传感器底板按上述连接方式固定,用一定速度的车辆去通过障碍物,设置在障碍物底下的四个三轴力学传感器连接高速数字采集仪,能得到冲击过程中的力学曲线,通过对四个传感器进行数学耦合,计算出障碍物的受的合力,即为冲击力。实施例4将对比例1和实施例1-3的装置按照描述的方法来进行对比试验,试验参数和结果记录在表1中。使用的模拟车辆为真车,具体地为大众迈腾牌轿车。每组试验进行3次试验并且取平均值。表1:对比例1和实施例1-3的装置的冲击试验结果试验组试验车速(/km·h-1)障碍物受合力(/KN)对比例16442.3实施例16443.8实施例26439.6实施例36448.1从表1的数据可见,实施例1-3的障碍物受合力的数值与对比例1的实际障碍物相比,其差别最高为13.7%,其差别最低为3.5%;由此可见,本实用新型的实施例1-3的障碍物能够跟好地模拟两种现实的障碍物。其中,实施例1的障碍物模拟现实的障碍物最好。当前第1页1 2 3