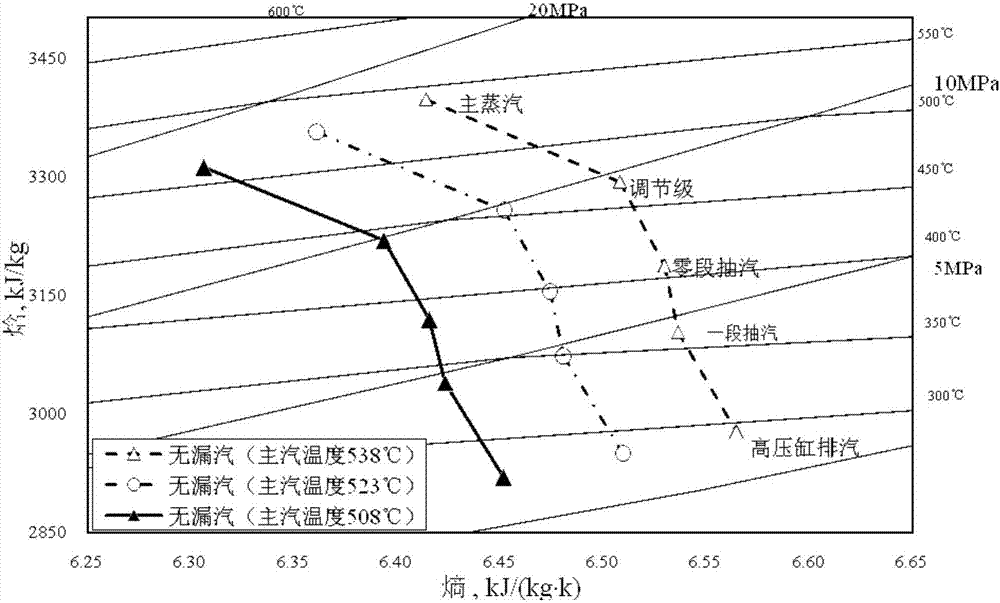
本发明属于火力发电领域,具体涉及一种汽轮机高压缸通流级效率异常的诊断方法。
背景技术:
:
在火力发电领域中,汽轮机是将蒸汽热能转化为电能的关键设备之一,国内汽轮机的发展路线是“引进产品-引进技术-部分设备自主生产-完全独立生产-独立开发创新型产品”。随着设计和制造水平的提高,国内汽轮机制造厂的生产和研发出的部分产品性能已经接近国际一流水平,但部分型号汽轮机仍然存在很多问题,汽轮机高压缸通流级效率异常(低于设计值)是常见的问题之一。通常来说,汽轮机高压缸通流级效率异常有两种情况:(1)由于设计或制造存在缺陷造成高压缸通流级效率真实偏低。(2)高压缸内部有高品质蒸汽漏汽至抽汽管道或者抽汽腔室有节流现象,导致实测通流参数异常目前,造成实测通流级效率异常。国内汽轮机设备性能验收试验或大修试验均有相关试验标准参考(比如PTC6 2004和GB/T 8117),试验标准或规程对汽轮机性能试验的操作流程、试验需要的测点种类及数量和试验仪表的精度作了详细要求,但均未提及高压缸通流级效率异常等汽轮机故障诊断分析相关方法。
技术实现要素:
:
本发明的目的是提供一种汽轮机高压缸通流级效率异常的诊断方法,该方法能够有效解决如何汽轮机高压缸通流级效率异常的原因。利用该方法对某一具体的汽轮机高压缸及其通流级进行研究分析,根据测量结果绘制出蒸汽膨胀过程线和计算出的级后流量与压力比值关系,诊断出高压缸通流级效率异常的原因。
为达到上述目的,本发明采用如下技术方案来实现:
一种汽轮机高压缸通流级效率异常的诊断方法,包括以下步骤:
在机组还未投入运行时,在汽轮机高压缸的进汽、排汽和各段抽汽管道上安装温度和压力试验测点;在机组投入运行时,在额定进汽参数下试汽轮机高压缸进汽、排汽和各段抽汽的压力和温度,计算汽轮机高压缸通流级效率,根据焓熵图绘制蒸汽在汽轮机高压缸内部的膨胀过程线,并与设计值比较;如果通流级后蒸汽或抽汽温度偏离设计值5℃以上,则改变汽轮机高压缸进汽温度,测试汽轮机高压缸进汽、排汽和各段抽汽的压力和温度,计算汽轮机高压缸通流级效率,判断是否是由漏汽现象造成通流级效率异常;如果通流级后蒸汽抽汽压力偏离设计值1%以上,关闭汽轮机高压缸各段抽汽的电动门,测量进汽、排汽和各段抽汽的压力和温度,计算此时抽汽压力与级后流量比,并进行变工况计算,判断出抽汽压力是否与对应通流级后压力的关系,判断抽汽腔室是否存在流动损失,从而诊断出造成汽轮机高压缸通流级效率偏低的原因。
本发明进一步的改进在于:当机组正常运行时,将汽轮机高压调门开度强制不变,汽轮机进汽在保持机组回热系统正常投入运行,测量高压缸的进汽、排汽和抽汽参数,计算高压缸通流级效率,其计算公式如下:
式中:Hin—通流级进汽焓值,kJ/kg;
Ho'ut—通流级等熵排汽焓,kJ/kg;
Hout—通流级排汽焓,kJ/kg;
在压力保持不变时,改变汽轮机高压缸进汽温度,此时,高压缸通流级真实效率不变,如果汽轮机存在内漏现象,相当于有一部分蒸汽从通流级前直接漏至高压缸排汽或各段抽汽参数,实测的通流级效率会随级前蒸汽温度变化而变化,在调门开度和进汽压力不变的情况下,蒸汽温度变化影响汽轮机进汽比容的变化,蒸汽比容根据国际公式化委员会1967年工业用IFC水和水蒸汽状态方程V=f(P,T),从而会影响汽轮机进汽通流能力,新蒸汽温度下的汽轮机进汽质量流量影响的计算公式如下:
式中:G—初始工况下汽轮机进汽流量,t/h;
G'—变工况下汽轮机进汽流量,t/h;
V—初始工况下汽轮机进汽比容,m3/kg;
V'—变工况下汽轮机进汽比容,m3/kg;
测量靠近汽缸本体的抽汽管内的蒸汽压力代替测量,但是如果因设计或安装的原因导致通流级后蒸汽流动至抽汽管道的流动损失偏大,实测抽汽管道内的蒸汽压力会低于通流级后蒸汽压力,此时计算出的通流级效率会低于实际值,关闭抽汽管道上的电动门后,抽汽管道内的水蒸汽的压力为静压,与通流级后蒸汽压力基本相当;关闭抽汽电动门后,会造成对应通流级后的流量增大,从而会导致级后压力发生变化,汽轮机级后压力与流量的折算公式如下:
式中:G0—初始工况下汽轮机级段通流量,t/h;
G1—变工况下汽轮机级段通流量,t/h;
P0—初始工况下汽轮机级段前压力,MPa;
P01—变工况下汽轮机级段前压力,MPa;
P0—初始工况下汽轮机级段后压力,MPa;
P21—变工况下汽轮机级段后压力,MPa;
根据过热蒸汽在汽轮机通流级内的膨胀特性和汽轮机抽汽管道内蒸汽流动特性,诊断出汽轮机高压缸通流级效率异常的原因。
本发明具有如下的优点:
事先布置好测试通流级效率的相关测点,在机组正常运行时,将汽轮机高压缸进汽调节阀门开度保持不变,测试并分析出汽轮机高压缸进汽参数变化对汽轮机高压缸通流级效率(测试效率)的影响,根据水蒸汽在汽轮机级内的膨胀过程线(膨胀效率)的变化趋势来判断汽轮机高压缸内部是否存在漏汽现象;然后,关闭汽轮机高压缸各段抽汽的电动门,测量进汽、排汽和各段参数,计算此时抽汽压力(静压)与级后流量比,据此判断出抽汽压力是否与对应通流级后的压力一致,最终确定汽轮机高压缸通流级效率异常的原因。
为了提高汽轮机高压缸通流效率诊断的准确性,可以增大汽轮机高压缸进汽温度的变化梯度和变化次数,在测试过程中尽量保持汽轮高压缸进汽压力稳定。
附图说明:
图1为本发明在测点安装示意图。
图2为不同参数下的无内部漏汽现象时的汽轮机高压缸通流膨胀过程线。
图3为不同参数下的有内部漏汽现象时的汽轮机高压缸通流膨胀过程线。
图4为不同参数下的通流级后至抽汽压力测点之间存在流动损失时的汽轮机高压缸通流膨胀过程线。
图5为主蒸汽漏汽至零段抽汽和一段抽汽漏汽量分别为0t/h、2t/h、4t/h和6t/h时的抽汽膨胀过程线。
图6为汽轮机变工况计算流程图。
图7为汽轮机高压缸通流效率诊断方法的流程图。
具体实施方式:
下面结合附图对本发明做进一步地详细说明。
如图1所示,机组还未投入运行时,参考ASME PTC6标准,在汽轮机高压缸的进汽、排汽和各段抽汽管道上安装温度和压力试验测点,压力测点装在上游,压力测量采用精度为0.075级的压力变送器,温度测点布置双重测点,试验专用精密级E型热电偶为一次测量元件,二次仪表采用温度变送器测量,采集系统采用EIC分布式数据采集装置结合英国施伦伯杰公司生产的IMP数据采集板,压力和温度信号送入数据采集系统实现自动存储和记录试验数据。
强制汽轮机高压调阀开度不变,保持主蒸汽压力不变,在进汽温度分别为538℃、523℃和508℃下测试汽轮机高压缸通流级效率,根据焓熵图绘制出的蒸汽膨胀过程线,会出现以下几种情况:
如图2所示,根据测试数据和焓熵图绘制出的蒸汽膨胀过程线基本平行,此时可认为通流级效率偏低是由于高压缸本体效率偏低导致的。
如图3所示,各段抽汽压力基本不变,根据测试数据和焓熵图绘制出的蒸汽膨胀过程线出现熵减现象,违背了热力学第二定律,若测试通流效率的此时可认为通流级效率偏低是与高压缸内部漏汽现象有关。
表1测试工况通流级效率与设计值的比较
如图4所示,各段抽汽温度基本不变,零段抽汽和一段抽汽压力偏低,根据测试数据和焓熵图绘制出的蒸汽膨胀过程线与设计状态偏离,这可能是由于设计制造偏差或测试抽汽压力低于汽轮机级后压力(通流级后至对应抽汽压力测试位置有压损)造成的,各级段效率与如表1所示。
表2测试工况通流级效率与设计值的比较
为了确认是否是由于测试抽汽压力低于汽轮机级后压力造成的,将零段抽汽电动阀V1和零段抽汽电动阀V2(见图),此时由于抽汽流量减小,通流级后的流量会增加(通流级后压力升高),级后压力可通过公式3折算。表3为某压临界600M机组设计状态下投和不投0号高加时的各段抽汽压力及级后流量对比。
表3投和不投0号高加时的各段抽汽压力及级后流量对比
根据表3提供的计算数据可以看出,采用变工况计算得出的汽轮机第零段和第一段抽汽压力与设计值偏差分别为0.17%和0.14%,不影响分析测试结果。
根据关闭抽汽电动门的测试参数,变工况计算至回热系统正常投用状态下,得出的各段抽汽压力与回热系统正常投用时的实测值偏差在0.5%以内,可认为汽轮机通流级效率异常是由于汽轮机通流制造与设计值偏差造成的,如果偏差大于0.5%,将变工况计算得出的压力代替投用回热系统时的实测压力,重新绘制蒸汽膨胀过程线,此时膨胀过程线若与设计状态近似平行,可认为通流效率异常是由于汽轮机通流级后蒸汽到抽汽压力测点之间存在压力损失造成的。
如图5所示,根据设计数据变工况计算出主蒸汽漏汽至零段抽汽和一段抽汽漏汽量分别为0t/h、2t/h、4t/h和6t/h时的抽汽膨胀过程线。
如图6所示,为汽轮机变工况计算详细过程,计算过程保持加热器端差不变,当初参数变化时,重新计算出各通流级后的流量,根据弗留格尔公式计算出新的抽汽压力,反复迭代计算,直至相邻两次计算的压力误差小于0.01%,输出计算结果。
如图7所示,为汽轮机高压缸通流效率异常诊断的详细流程图。
综上所述,本发明一种汽轮机高压缸通流级效率异常的诊断方法,涉及的测试系统简单,测试条件的变化不影响汽轮机组安全性,具有很强的可操作性,变工况计算有成熟的理论支撑,误差在可控范围内,通流级效率异常的准确性较高。