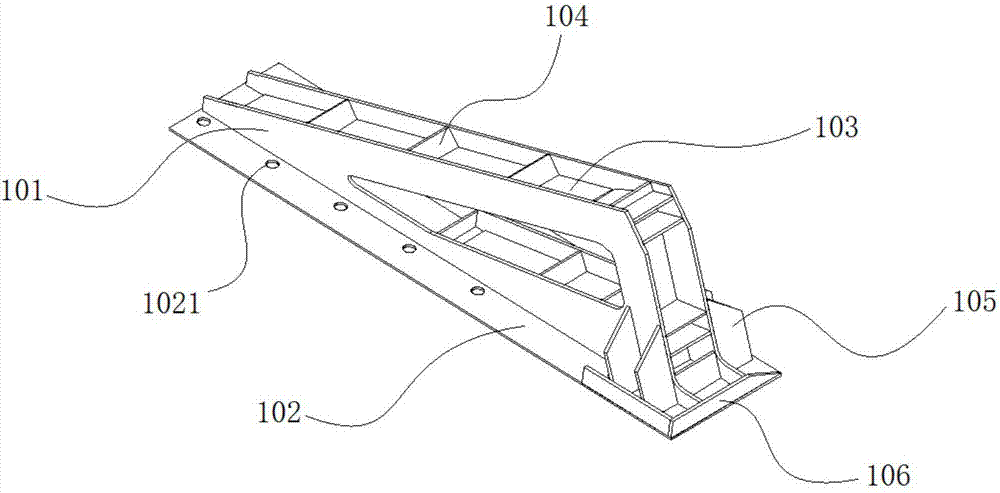
本发明涉及试验器材领域,特别涉及一种用于各加载方向呈空间分布的试验反力装置。
背景技术:
自锚式悬索桥不需要庞大的锚锭,而是把主缆锚固到桥面板或加劲梁的两端,由桥面板或加劲梁承担主缆的水平力和上拔力。因此主缆锚固端的受力情况比较复杂。要了解其受力特性和传力机理,不能完全依据数值模拟得出的结果,还需要进行大比例模型试验。试验中如何模拟主缆对锚固端的作用力成为需要解决的首要问题。
自锚式悬索桥锚固端试验中,如果用主缆张拉的方式模拟锚固端受力,不便于加载装置安装,所以采用千斤顶产生的推力模拟主缆对锚固端的拉力是一种很好的解决方案。
散索锚固是自锚式悬索桥主缆锚固方式中最为常见的一种。然而,散索锚固方式导致主缆力作用方向呈空间分布,对施加千斤顶加载力的反力架提出了严苛的要求。加之自锚式悬索桥试验一般采用较大相似比,缩尺模型的锚固端等效作用力较大。同时,受现有实验室空间限制,模型加载作用点集中,实验室狭小空间内无法密集安装多个空间加载的大吨位通用反力架。
因此,现有反力架在应用于自锚式悬索桥缩尺模型试验时,存在以下不足或缺陷:1)主缆散索后对每个锚固点的合力方向不同,加载方向呈空间分布,而现有通用反力架无法满足这一要求;2)大比例缩尺模型实验需要的加载力值较大,需采用较大吨位的反力架,现有的大型试验特制反力架吨位不能完全满足试验需求;3)现有通用反力架提供的加载点较少,对于多点加载实验的情况,需要安装多个反力架,故安装过程复杂,且占据较大空间。
技术实现要素:
本发明的目的是提供一种针对自锚式悬索桥缩尺模型试验的反力装置及其制作方法,以解决现有技术中存在的问题。
为实现本发明目的而采用的技术方案是这样的,一种大吨位空间多向多点结构试验加载反力装置,包括固定在实验室基础上的2个三角刚架,以及若干千斤顶连接节点和若干横向联系。
所述2个三角刚架对称布置。每个三角刚架包括2块平行布置的三角板和底座板。
所述三角板包括斜向设置的上肢和立肢,以及横向设置的下肢。所述上肢、下肢和立肢为一个整体,构成三角板的三条边。所述2块三角板竖直布置,底端焊接在底座板上。所述2块三角板之间包夹有若干腹板和若干加劲板。各腹板和加劲板均与两侧的三角板焊接。所述底座板上预留有锚孔,受力杆穿过锚孔后与实验室基础的加载孔固定连接。
所述2个三角刚架通过若干个横向联系焊接成整体。
所述千斤顶连接节点一侧与三角刚架焊接,另一侧与千斤顶的底座连接。所述千斤顶的顶垫抵在桥梁试验模型的加载位置。
加载时,千斤顶连接节点受加载力,将力传给上肢和下肢。上肢和下肢将力传递到底座板。底座板通过受力杆将力传递给实验室基础。
进一步,所述下肢包括水平段和倾斜延伸段。每个三角刚架的2块三角板之间包夹有3块腹板。所述3块腹板包括上腹板、下腹板和立腹板。所述上腹板与2块三角板的上肢焊接。所述下腹板与2块三角板的倾斜延伸段焊接。所述立腹板与2块三角板的立肢焊接。
进一步,所述上腹板靠近立腹板的一端焊接有腹板渐变段ⅰ。所述下腹板靠近立腹板的一端焊接有腹板渐变段ⅱ。焊接在立腹板靠近桥梁试验模型一侧板面上的加劲板包括上腹板前分叉ⅰ、上腹板前分叉ⅱ、下腹板前分叉ⅰ和下腹板前分叉ⅱ。焊接在立腹板远离桥梁试验模型一侧板面上的加劲板包括上腹板后分叉ⅰ、上腹板后分叉ⅱ、下腹板后分叉ⅰ和下腹板后分叉ⅱ。所述上腹板后分叉ⅰ和上腹板后分叉ⅱ与腹板渐变段ⅰ焊接。所述下腹板后分叉ⅰ和下腹板后分叉ⅱ与腹板渐变段ⅱ焊接。试验时,千斤顶连接节点将力传递给上腹板前分叉ⅰ、上腹板前分叉ⅱ、下腹板前分叉ⅰ和下腹板前分叉ⅱ,各前分叉将力传递给立腹板,立腹板将力分配给上肢和下肢。所述上腹板后分叉ⅰ和上腹板后分叉ⅱ将力传给腹板渐变段ⅰ。所述下腹板后分叉ⅰ和下腹板后分叉ⅱ将力传给腹板渐变段ⅱ。
进一步,所述上肢的形心线与底座板板面的夹角为27°,倾斜延伸段的形心线与底座板板面夹角为17°,立肢与底座板板面的夹角为77°。
进一步,所述立肢的板面上焊接有梯形板。所述底座板靠近桥梁试验模型一端板面上焊接有前端板。
进一步,所述千斤顶连接节点包括节点横板ⅰ、节点横板ⅱ、节点横板ⅲ、节点横板ⅳ、节点侧板ⅰ、节点侧板ⅱ和节点竖板。所述节点横板ⅰ、节点横板ⅳ、节点侧板ⅰ和节点侧板ⅱ合围出框体结构。这个框体结构的一个敞口被节点竖板封堵,框体结构和节点竖板共同构成箱体结构。所述箱体的内腔中焊接有节点横板ⅱ和节点横板ⅲ。所述节点竖板与底座用螺栓连接。所述箱体的敞口端焊接在三角刚架上。其中,所述节点侧板ⅰ和节点侧板ⅱ分别与三角刚架的2片三角板焊接。所述节点横板ⅰ与上腹板前分叉ⅰ或下腹板前分叉ⅰ焊接。所述节点横板ⅳ与上腹板前分叉ⅱ或下腹板前分叉ⅱ焊接。所述节点横板ⅰ板面上具有圆孔ⅰ。所述节点横板ⅳ板面上具有圆孔ⅱ。加载时,节点竖板受力,将力传递给节点横板ⅰ、节点横板ⅱ、节点横板ⅲ、节点横板ⅳ、节点侧板ⅰ和节点侧板ⅱ。所述节点横板ⅰ和节点横板ⅱ的间距为a,所述节点横板ⅱ和节点横板ⅲ的间距为b,所述节点横板ⅲ和节点横板ⅳ的间距为c。其中,a:b:c为2:3:2。
进一步,所述横向联系采用l型截面。所述横向联系包括前横联、后横联和上横联。所述上横联具有横联加劲板。
进一步,所述底座板在锚孔处设置有垫板。
本发明还公开一种关于上述加载反力装置的制作方法,包括以下步骤:
1)设计反力装置各部分。
2)计算确定反力装置重心,设计反力装置吊点位置。
3)焊接三角刚架。在三角板上焊接临时吊点。2块三角板包夹腹板后,与腹板焊接。将2块三角板整体焊接在底座板上。焊接加劲板。
4)临时固定两个三角刚架,将横向联系与两个三角刚架焊接。
5)解除三角刚架的临时固定,调整千斤顶连接节点的设计,将千斤顶连接节点焊接到三角刚架上。
6)吊装反力装置,采用受力杆将反力装置固定在实验室基础上。将千斤顶的底座与千斤顶连接节点通过螺栓连接。
本发明的技术效果是毋庸置疑的:
a.加载反力装置总加载值可达到1300吨以上,反力架上部加载节点纵向位移控制为10mm,满足大型构件结构试验的需求;
b.可准确模拟自锚式悬索桥主缆对锚固端拉力的实际情况,解决了复杂空间方向加载的问题;
c.反力装置结构合理、尺寸较小且受力明确,解决了反力架空间方向大吨位加载的问题;
d.采用一个反力装置解决多点加载问题,安装方便,节省空间,各个加载点的反力通过结构自身抵消、平衡,减小了反力架对实验室基础的作用力,减少了受力杆的数量。
附图说明
图1为反力装置结构示意图;
图2为三角刚架结构示意图;
图3为三角板结构示意图;
图4为底座板结构示意图;
图5为腹板和加劲板结构示意图;
图6为腹板分叉结构示意图;
图7为千斤顶连接节点结构示意图;
图8为千斤顶连接节点爆炸图;
图9为横板间距比例示意图;
图10为前横联结构示意图;
图11为后横联结构示意图;
图12为上横联结构示意图;
图13为反力装置加载受力示意图;
图14为缩尺试验模型结构示意图。
图中:三角刚架1、三角板101、上肢1011、下肢1012、水平段10121、倾斜延伸段10122、立肢1013、底座板102、腹板103、上腹板1031、腹板渐变段ⅰ10311、下腹板1032、腹板渐变段ⅱ10321、立腹板1033、加劲板104、上腹板前分叉ⅰ1041、上腹板前分叉ⅱ1042、下腹板前分叉ⅰ1045、下腹板前分叉ⅱ1046、上腹板后分叉ⅰ1043、上腹板后分叉ⅱ1044、下腹板后分叉ⅰ1047、下腹板后分叉ⅱ1048、梯形板105、前端板106、千斤顶连接节点2、节点横板ⅰ201、圆孔ⅰ2011、节点横板ⅱ202、节点横板ⅲ203、节点横板ⅳ204、圆孔ⅱ2041、节点侧板ⅰ205、节点侧板ⅱ206、节点竖板207、横向联系3、前横联301、后横联302、竖板3021、横板3022、上横联303、横联加劲板3031、千斤顶4、底座401、顶垫402、实验室基础5、实验室反力墙6、桥梁试验模型7。
具体实施方式
下面结合实施例对本发明作进一步说明,但不应该理解为本发明上述主题范围仅限于下述实施例。在不脱离本发明上述技术思想的情况下,根据本领域普通技术知识和惯用手段,做出各种替换和变更,均应包括在本发明的保护范围内。
实施例1:
自锚式悬索桥主缆锚固方式分为两种:1)主缆采用连续的钢丝绳绕过梁端,并使两股主缆连续为闭合环形;2)主缆通过散索鞍分散,用锚具锚固于桥面板或加劲梁。
本实施例公开一种针对上述第二种锚固方式的缩尺模型试验提出的大吨位空间多向多点结构试验加载反力装置,包括固定在实验室基础5上的2个三角刚架1,以及4个千斤顶连接节点2和3个横向联系3。
参见图1,所述2个三角刚架1对称布置。参见图2,每个三角刚架1包括2块平行布置的三角板101和底座板102。
参见图3,所述三角板101包括斜向设置的上肢1011和立肢1013,以及横向设置的下肢1012。所述上肢1011、下肢1012和立肢1013为一个整体,构成三角板101的三条边。所述下肢1012包括水平段10121和倾斜延伸段10122。常规自锚式悬索桥主缆末端倾角大致为15°~25°。经方案设计及应力分析,确定本实施例中的三角刚架长高比为2.2:1。所述上肢1011的形心线与底座板102板面的夹角为27°,倾斜延伸段10122的形心线与底座板102板面夹角为17°,立肢1013与底座板102板面的夹角为77°。所述立肢1013的板面上焊接有梯形板105,以抵抗千斤顶产生的向外水平分力在下肢1012和底座板102焊接处产生的弯矩。
所述2块三角板101竖直布置,底端焊接在底座板102上。此处的焊缝主要传递剪力,焊缝满足抗剪强度要求。参见图5和图6,为保证构件的稳定性,每个三角刚架1的2块三角板101之间包夹有3块腹板103。所述3块腹板103包括上腹板1031、下腹板1032和立腹板1033。所述上腹板1031与2块三角板101的上肢1011焊接。所述下腹板1032与2块三角板101的倾斜延伸段10122焊接。所述立腹板1033与2块三角板101的立肢1013焊接。所述上腹板1031靠近立腹板1033的一端焊接有腹板渐变段ⅰ10311。所述下腹板1032靠近立腹板1033的一端焊接有腹板渐变段ⅱ10321。为保证构件的稳定性,所述2块三角板101之间还包夹有加劲板104,各加劲板104的间距根据稳定计算结果确定。所述腹板103和加劲板104的板面均与三角板101的板面垂直。焊接在立腹板1033靠近桥梁试验模型7一侧板面上的加劲板104包括上腹板前分叉ⅰ1041、上腹板前分叉ⅱ1042、下腹板前分叉ⅰ1045和下腹板前分叉ⅱ1046。焊接在立腹板1033远离桥梁试验模型7一侧板面上的加劲板104包括上腹板后分叉ⅰ1043、上腹板后分叉ⅱ1044、下腹板后分叉ⅰ1047和下腹板后分叉ⅱ1048。所述上腹板后分叉ⅰ1043和上腹板后分叉ⅱ1044与腹板渐变段ⅰ10311焊接,此处两块板斜向叠加焊接,腹板渐变段ⅰ10311开设有45°~55°的坡口,保证15mm的焊缝高度。所述下腹板后分叉ⅰ1047和下腹板后分叉ⅱ1048与腹板渐变段ⅱ10321焊接,此处两块板斜向叠加焊接。试验时,千斤顶连接节点2将加载力在竖直平面的分量传递给上腹板前分叉ⅰ1041、上腹板前分叉ⅱ1042、下腹板前分叉ⅰ1045和下腹板前分叉ⅱ1046,各前分叉将力传给立腹板1033,立腹板1033将力分配给上肢1011和下肢1012。所述上腹板后分叉ⅰ1043和上腹板后分叉ⅱ1044将力传给腹板渐变段ⅰ10311。所述下腹板后分叉ⅰ1047和下腹板后分叉ⅱ1048将力传递给腹板渐变段ⅱ10321。
参见图4和图13,所述底座板102上预留有锚孔1021,受力杆1022穿过锚孔1021后与实验室基础的加载孔固定连接。所述底座板102在锚孔1021处设置有30mm厚的垫板1023,以扩散受力杆1022的螺栓对底座板102的压力,改善底座板102局部受力性能。加载时锚孔1021周围区域可能产生较大变形,所述底座板102靠近桥梁试验模型7一端板面上焊接有前端板106以减小其变形。
在本实施例中,受力杆1022分为受拉锚杆和受剪锚杆两个部分。根据分析结果,底座板102前部4个锚孔全部受拉,采用直径为48mm抗拉锚杆连接,选用10.9级强度高强锚杆,由于锚杆直径远小于锚孔直径,反力架受力变形后锚杆不会接触毛锚孔壁,故锚杆仅承受拉力。反力架后部20个锚孔全部受压且受剪,采用直径为60mm剪力棒连接,选用qt900球墨铸铁棒。由于φ60mm剪力棒直径接近反力底板锚孔直径(65mm),故加载时剪力棒表面与锚孔壁能够均匀接触,避免出现棒与孔壁接触局部应力集中而导致混凝土压溃,经弹性力学分析,该直径组合产生的局部应力未超过材料容许强度,故满足设计要求。
所述2个三角刚架1通过3个横向联系3焊接成整体。3个横向联系3平衡千斤顶空间加载力的水平分力的同时,还增强了反力装置在吊运过程中的横向稳定性,方便吊装与安装。所述横向联系3采用l型截面。所述横向联系3包括前横联301、后横联302和上横联303。所述前横联301与底座板102和前端板106焊接。所述后横联302包括竖板3021和横板3022。所述横板3022与底座板102焊接。所述竖板3021比横板3022长,延伸到上肢1011,与上肢1011和底座板102焊接。考虑到反力架吊装时吊装钢丝绳对三角刚架有一对向内的水平分力,此时上横联303受压。经过计算分析,上横联有局部失稳的风险。因此,所述上横联303还具有横联加劲板3031。
所述千斤顶连接节点2包括节点横板ⅰ201、节点横板ⅱ202、节点横板ⅲ203、节点横板ⅳ204、节点侧板ⅰ205、节点侧板ⅱ206和节点竖板207。所述节点横板ⅰ201、节点横板ⅳ204、节点侧板ⅰ205和节点侧板ⅱ206合围出框体结构。这个框体结构的一个敞口被节点竖板207封堵,框体结构和节点竖板207共同构成箱体结构。所述箱体的内腔中焊接有节点横板ⅱ202和节点横板ⅲ203。所述节点横板ⅱ202与节点侧板ⅰ205、节点侧板ⅱ206和节点竖板207均焊接。所述节点横板ⅲ203与节点侧板ⅰ205、节点侧板ⅱ206和节点竖板207均焊接。所述节点竖板207与千斤顶4的底座401用螺栓连接。所述千斤顶4的顶垫402抵在桥梁试验模型7上。所述箱体的敞口端焊接在三角刚架1上。其中,所述节点侧板ⅰ205和节点侧板ⅱ206分别与三角刚架1的2片三角板101焊接。所述节点横板ⅰ201与上腹板前分叉ⅰ1041或下腹板前分叉ⅰ1045焊接。所述节点横板ⅳ204与上腹板前分叉ⅱ1042或下腹板前分叉ⅱ1046焊接。所述节点横板ⅰ201板面上具有圆孔ⅰ2011。所述节点横板ⅳ204板面上具有圆孔ⅱ2041。加载时,节点竖板207受力,将力传递给节点横板ⅰ201、节点横板ⅱ202、节点横板ⅲ203、节点横板ⅳ204、节点侧板ⅰ205和节点侧板ⅱ206。所述节点竖板207与节点横板和节点侧板的接触面积较小,如果节点横板间距设计不合理,节点竖板207易产生较大弯矩,不利于节点局部受力。为保证节点受力合理,需要考虑节点横板的间距。所述底座401对节点竖板207作用区域为圆形,经过多次计算分析,所述节点横板ⅰ201和节点横板ⅱ202的间距为a,所述节点横板ⅱ202和节点横板ⅲ203的间距为b,所述节点横板ⅲ203和节点横板ⅳ204的间距为c。其中,a:b:c为2:3:2,节点竖板207受力合理。
参见图13(图中箭头方向为受力方向),每个受力杆件受力形式明确。由于两个三角刚架1平行焊接,四个千斤顶4施加荷载的方向呈空间分布,且四个方向均不相同,三角刚架1的上、下肢轴线和千斤顶连接节点2施加荷载方向的水平投影不同向,加载过程中千斤顶连接节点2受到一对向外的水平力。因此千斤顶连接节点2不仅具有传力作用,还对力在水平方向有转向作用。所述上肢1011和下肢1012主要承受轴向压力,底座板102前面四个锚孔还承受上拔力。加载时,千斤顶连接节点2承受千斤顶4的加载力,将加载力在竖直平面内的分量传递给上肢1011和下肢1012,将上部2个千斤顶4的加载力在水平面内的分量传递给横向联系3,将下部2个千斤顶4的加载力在水平面内的分量传递给梯形板105。所述横向联系3两端承受的加载力水平分量大小相等、方向相反,实现水平力自平衡。所述上肢1011和下肢1012将力传递到底座板102,梯形板105将力传递到底座板102,底座板102通过受力杆1022将力传递给实验室基础5。
根据上述方案,并配合反力墙6及桥梁试验模型7设计完成缩尺试验模型如图14所示。试验基于应力等效原则设计试验缩尺模型,通过调整试验荷载的大小使几何缩尺后的试验模型与原结构保持相同的应力水平。在综合考虑试验加载能力、钢板厚度、钢结构加工条件与试验场地条件等因素确定缩尺比例。进行主缆锚固区模型试验时,先安装桥梁试验模型7和反力装置,然后布置桥梁试验模型7上的测点,最后进行加载、卸载。加载时采用千斤顶4液压加载,连续慢速加载直至结构破坏。千斤顶4产生的推力模拟主缆对锚固端的拉力。卸载时连续慢速卸载。卸载完成后,采集桥梁试验模型7上各测点的数据,绘制相应的应力荷载关系曲线。
值得说明的是,在采用本实施例所公开的加载反力装置进行的主缆锚固区模型试验中,经实测表明,反力装置总加载值可达到1300吨以上,实验室基础5未出现显著破坏特征,此时反力装置上部加载节点纵向位移控制为10mm,满足大型构件结构试验的需求。
实施例2:
本实施例公开一种关于实施例1所述大吨位空间多向多点结构试验加载反力装置的制作方法,包括以下步骤:
1)设计反力装置各部分。其中,确定三角刚架1和模型的位置后,根据模型加载点实际位置和合力线方向确定节点竖板207的空间位置和方向。节点竖板207的尺寸根据千斤顶4的规格确定。根据三角刚架1和节点竖板207的位置关系,以及横板间距确定节点横板尺寸。值得说明的是,参见图14,由于浇筑成型后的模型加载点位置和方向与设计存在误差,为保证空间加载方向准确,模型制作完成后需测量其加载点实际准确位置和方向,根据测量数据对千斤顶连接节点2进行设计调整。
2)焊接三角刚架1。在三角板101上焊接临时吊点。2块三角板101包夹腹板103后,与腹板103焊接。将2块三角板101整体焊接在底座板102上。焊接加劲板104、梯形板105和前端板106。
3)固定两个三角刚架1,将横向联系3与两个三角刚架1焊接。
4)解除三角刚架1固定,由于三角刚架1固定后焊接,钢材受热变形,产生次应力,解除固定后会产生变形。需测量已经焊接好部分的尺寸后,再调整千斤顶连接节点2的设计。调整千斤顶连接节点2的设计,将千斤顶连接节点2焊接到三角刚架1上。
5)计算确定反力装置重心,设计反力装置吊点位置。
6)吊装反力装置,采用受力杆1022将反力装置固定在实验室基础5上。将千斤顶4的底座401与千斤顶连接节点2通过螺栓连接。