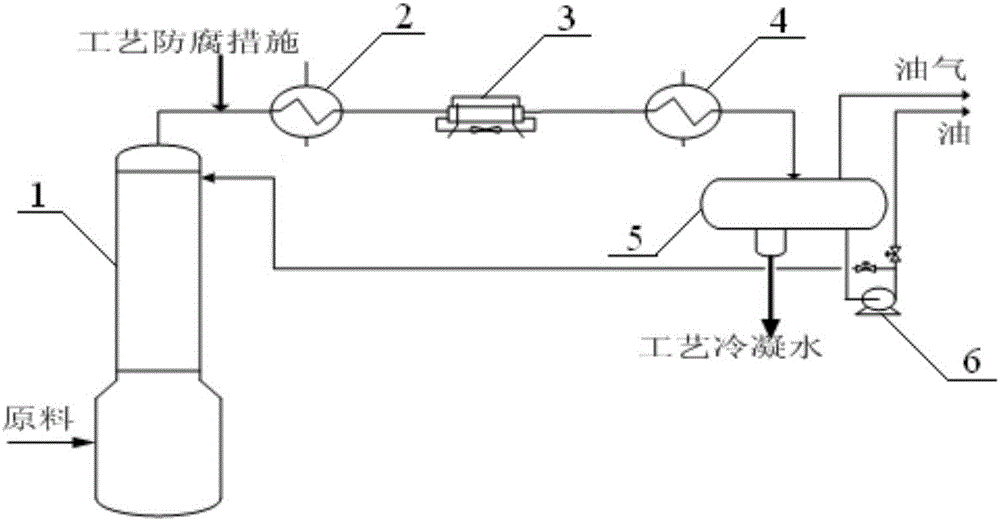
本发明涉及一种腐蚀评价方法,具体涉及一种炼化装置工艺冷凝水腐蚀评价方法。
背景技术:
:炼油化工行业是一个危险性十分突出的行业,在石油加工过程中的任何腐蚀泄漏均可能导致严重的安全生产事故的发生,从而造成生产装置着火、爆炸、人员伤亡、财产损失、环境污染等恶性事故。在石油加工过程中,原油中的酸(例如环烷酸)、硫化物等腐蚀性介质是必然存在的,其会贯穿整个炼化生产过程的装置之中,对炼化装置的设备腐蚀是不可避免的,只是腐蚀严重程度的大小不同而已,因此腐蚀是影响炼油化工装置安全、长周期运行的核心因素。尽管炼化装置腐蚀是不可避免的,但是通过可靠地监测炼化装置腐蚀部位的某些关键参数,通过对这些关键参数的可靠评价,并提出有效、可靠的应对措施,可以使炼化装置的腐蚀得到控制。目前,炼化装置的腐蚀监测部位大致包括两种,一种是在低温腐蚀部位进行腐蚀监测,另外一种是在高温腐蚀部位进行腐蚀监测。低温腐蚀部位一般在炼化装置产品分离塔塔顶馏出物、介质中含有凝结水的环境中,这种凝结水称为工艺冷凝水,对工艺冷凝水中腐蚀介质的含量、介质环境的酸碱性(ph值,范围在0~14)以及腐蚀产物fe2+、fe3+浓度的监测是有必要进行的。介质环境的酸碱性对设备的腐蚀环境有着至关重要的影响,ph值越小表示腐蚀环境酸性越强,此时介质对设备的腐蚀性很强,设备极易发生腐蚀泄漏;ph值越大表示腐蚀环境碱性越强,此时越可能造成腐蚀系统内设备表面的结垢,导致垢下腐蚀越强,同样会造成设备失效或发生腐蚀泄漏。此外,由于腐蚀系统基本材质为碳钢,腐蚀产物的表征指标通常为fe2+、fe3+浓度的大小,fe2+、fe3+浓度越高则系统腐蚀程度越高,反之则越小。目前,炼化行业通常在低温腐蚀系统取得工艺冷凝水样品后,通过化学分析方法检测获得ph值及fe2+、fe3+浓度的确切监测数据,根据监测数据大小依据前期设定ph值上、下限及fe2+、fe3+浓度的上限控制指标进行简单判定,即判断是否超标。上述方式存在以下问题:1)未对超标程度做进一步判断,并且未进一步对超标等级及范围进行划分及警示;2)未对超标造成的腐蚀系统的腐蚀状态及腐蚀影响做进一步分析及说明,技术人员无法得知腐蚀的导致因素、腐蚀的影响及控制方法;3)未给出确切的腐蚀消减控制措施,技术人员无法得知如何应对不同超标或不超标的情况,因此是一种较为粗放并且不精准的腐蚀监控方式;4)无法形成完整有效地指导腐蚀控制的腐蚀评价结论。技术实现要素:本发明提供一种炼化装置工艺冷凝水腐蚀评价方法,该方法能够形成工艺冷凝水腐蚀原因清晰、腐蚀问题明确、腐蚀控制措施有效的腐蚀评价结论。本发明提供一种炼化装置工艺冷凝水腐蚀评价方法,包括如下步骤:获取炼化装置腐蚀系统工艺冷凝水的ph值及fe2+和fe3+浓度;确定ph值对炼化装置腐蚀系统的腐蚀状态和腐蚀影响,并确定对应的腐蚀控制方法;确定fe2+和fe3+浓度对炼化装置腐蚀系统的腐蚀状态和腐蚀影响,并确定对应的腐蚀控制方法;根据ph值及fe2+和fe3+浓度对炼化装置腐蚀系统的腐蚀状态、腐蚀影响及对应的腐蚀控制方法,获取工艺冷凝水的ph值及fe2+和fe3+浓度对炼化装置腐蚀系统的腐蚀状态、腐蚀影响及对应的腐蚀控制方法;对工艺冷凝水的ph值及fe2+和fe3+浓度对炼化装置腐蚀系统的腐蚀状态、腐蚀影响及对应的腐蚀控制方法进行整合。在本发明中,工艺冷凝水指的是炼化装置产品分离塔(即腐蚀系统)塔顶馏出物或介质中所含有的凝结水;fe2+和fe3+浓度指的是工艺冷凝水中fe2+和fe3+的总浓度。本发明的目的在于创建一种炼化装置工艺冷凝水腐蚀评价方法,该方法主要解决由炼化装置低温腐蚀系统获取的工艺冷凝水中ph值及fe2+和fe3+浓度监测数据的定量评价问题,该方法通过确定ph值及fe2+和fe3+浓度等不同腐蚀评价指标对炼化装置腐蚀系统的腐蚀状态及腐蚀影响,并制定对应的腐蚀控制方法,来对新获取的炼化装置腐蚀系统工艺冷凝水的ph值及fe2+和fe3+浓度的监测数据进行腐蚀评价,并且通过对各腐蚀评价结论进行整合,完成了对炼化装置工艺冷凝水的定量腐蚀评价,能够得到工艺冷凝水腐蚀原因清晰、腐蚀问题明确、腐蚀控制措施有效的腐蚀评价结论。进一步地,本发明的炼化装置工艺冷凝水腐蚀评价方法,还包括:确定炼化装置腐蚀系统工艺冷凝水的ph值及fe2+和fe3+浓度的控制指标。具体地,炼化装置腐蚀系统工艺冷凝水的ph值的控制指标为5.5~7.5;炼化装置腐蚀系统工艺冷凝水的fe2+和fe3+浓度的控制指标为≤2mg/l。本发明通过确定工艺冷凝水中ph值及fe2+和fe3+浓度的腐蚀控制指标及指标范围,从而便于对新获取的炼化装置腐蚀系统工艺冷凝水的ph值及fe2+和fe3+浓度的监测数据进行逐步判定,进而通过确定ph值及fe2+和fe3+浓度对炼化装置腐蚀系统的腐蚀状态及腐蚀影响及制定对应的腐蚀控制方法,获得炼化装置腐蚀系统工艺冷凝水的ph值及fe2+和fe3+浓度的腐蚀评价结论,为腐蚀系统的腐蚀评价及腐蚀控制提供了技术指导和依据。在本发明中,ph值对炼化装置腐蚀系统的腐蚀状态为:在ph值>8时,腐蚀系统ph值控制上限严重超标;在7.5<ph值≤8时,腐蚀系统ph值控制上限超标;在ph值为5.5~7.5时,腐蚀系统ph值控制合格;在5≤ph值<5.5时,腐蚀系统ph值控制下限超标;在ph值<5时,腐蚀系统ph值控制下限严重超标。进一步地,ph值对炼化装置腐蚀系统的腐蚀影响为:在ph值>8时,腐蚀系统工艺防腐措施严重过剩,垢下腐蚀显著增大;在7.5<ph值≤8时,腐蚀系统工艺防腐措施过剩,垢下腐蚀增大;在ph值为5.5~7.5时,腐蚀系统腐蚀受控;在5≤ph值<5.5时,腐蚀系统防腐措施不足,酸腐蚀增大;在ph值<5时,腐蚀系统工艺防腐措施严重不足,酸腐蚀显著增大。此外,ph值对应的腐蚀控制方法为:在ph值>8时,立即优化腐蚀系统工艺防腐注剂措施并减少注剂量,立即按“4次/年”进行腐蚀系统易腐蚀管线剩余壁厚监测,在发现壁厚减薄时扩检整个腐蚀系统;在7.5<ph值≤8时,优化腐蚀系统工艺防腐注剂措施、减少注剂量,按“2次/年”进行腐蚀系统易腐蚀管线剩余壁厚监测,在发现壁厚减薄时扩检整个腐蚀系统;在ph值为5.5~7.5时,腐蚀系统工艺防腐注剂措施平稳运行,按“2次/年”进行腐蚀系统易腐蚀管线剩余壁厚监测,在发现壁厚减薄时扩检整个腐蚀系统;在5≤ph值<5.5时,优化腐蚀系统工艺防腐注剂措施、增加注剂量,按“2次/年”进行腐蚀系统易腐蚀管线剩余壁厚监测,在发现壁厚减薄时扩检整个腐蚀系统;在ph值<5时,立即优化腐蚀系统工艺防腐注剂措施并增加注剂量,立即按“4次/年”进行腐蚀系统易腐蚀管线剩余壁厚监测,在发现壁厚减薄时扩检整个腐蚀系统。本发明将ph值划分为上述五个层级,ph值对炼化装置腐蚀系统的腐蚀状态、腐蚀影响及对应的腐蚀控制方法均是建立在上述划分后的五个层级的基础上,因此具有直接的对应性;通过对ph值进行详细划分,从而为腐蚀系统的腐蚀评价及腐蚀控制提供了技术指导和依据,使形成的腐蚀评价结论更加具有针对性,更易于现场技术人员操作,并且易于对腐蚀系统进行明确地控制。在本发明中,fe2+和fe3+浓度对炼化装置腐蚀系统的腐蚀状态为:在fe2+和fe3+浓度>3mg/l时,腐蚀系统fe2+和fe3+浓度控制严重超标;在2mg/l<fe2+和fe3+浓度≤3mg/l时,腐蚀系统fe2+和fe3+浓度控制超标;在fe2+和fe3+浓度≤2mg/l时,腐蚀系统fe2+和fe3+浓度控制未超标。进一步地,fe2+和fe3+浓度对炼化装置腐蚀系统的腐蚀影响为:在fe2+和fe3+浓度>3mg/l时,腐蚀系统腐蚀严重;在2mg/l<fe2+和fe3+浓度≤3mg/l时,腐蚀系统有腐蚀;在fe2+和fe3+浓度≤2mg/l时,腐蚀系统腐蚀不严重。此外,fe2+和fe3+浓度对应的腐蚀控制方法为:在fe2+和fe3+浓度>3mg/l时,立即优化腐蚀系统工艺防腐措施、优化注剂量,按“4次/年”进行易腐蚀管线剩余壁厚监测,在发现壁厚减薄时扩检整个腐蚀系统;在2mg/l<fe2+和fe3+浓度≤3mg/l时,优化腐蚀系统工艺防腐措施、优化注剂量,按“2次/年”进行易腐蚀管线剩余壁厚监测,在发现壁厚减薄时扩检整个腐蚀系统;在fe2+和fe3+浓度≤2mg/l时,腐蚀系统继续平稳运行,按“2次/年”管线测厚进行易腐蚀管线剩余壁厚监测,在发现壁厚减薄时扩检整个腐蚀系统。本发明将fe2+和fe3+浓度划分为上述三个层级,fe2+和fe3+浓度对炼化装置腐蚀系统的腐蚀状态、腐蚀影响及对应的腐蚀控制方法均是建立在上述划分后的三个层级的基础上,因此具有直接的对应性;通过对fe2+和fe3+浓度进行详细划分,为腐蚀系统的腐蚀评价及腐蚀控制提供了技术指导和依据,使形成的腐蚀评价结论更加具有针对性,更易于现场技术人员操作,并易于对腐蚀系统进行明确地控制。在本发明中,对工艺冷凝水的ph值及fe2+和fe3+浓度对炼化装置腐蚀系统的腐蚀状态、腐蚀影响及对应的腐蚀控制方法进行整合的方式可以采用“同项合并、异项保留、突出问题”的整合原则进行整合。即,在工艺冷凝水的ph值及fe2+和fe3+浓度对炼化装置腐蚀系统的腐蚀状态、腐蚀影响及对应的腐蚀控制方法相同时,该腐蚀状态、腐蚀影响及对应的腐蚀控制方法即形成最终的炼化装置工艺冷凝水定量腐蚀评价结论;在工艺冷凝水的ph值及fe2+和fe3+浓度对炼化装置腐蚀系统的腐蚀状态、腐蚀影响及对应的腐蚀控制方法相异时,以腐蚀问题更加突出的腐蚀状态、腐蚀影响及对应的腐蚀控制方法作为最终的炼化装置工艺冷凝水定量腐蚀评价结论。此外,可以采用计算机语言对本发明的上述方法进行编程,从而实现炼化装置工艺冷凝水智能型腐蚀评价过程。本发明的实施,至少具有以下优势:1、本发明的方法实现了对炼化装置工艺冷凝水腐蚀评价中腐蚀控制指标及控制范围的详细划分,从而为腐蚀系统的腐蚀评价及腐蚀控制提供了技术指导和依据。2、本发明的方法明确了腐蚀监测数据在腐蚀系统工艺冷凝水腐蚀过程中表征的腐蚀状态及对腐蚀系统的腐蚀影响,并且依据制定的腐蚀消减控制措施进一步详细明确了腐蚀控制的具体要求及方式。3、本发明的方法能够形成工艺冷凝水腐蚀原因清晰、腐蚀问题明确、腐蚀控制措施有效的腐蚀评价结论,所形成的最终腐蚀评价结论更有针对性,更易于现场技术人员操作,并且易于对腐蚀系统进行明确控制。4、本发明的方法能够形成计算机智能评价语言,从而能够有效提高炼化装置的智能化腐蚀控制水平。5、本发明的方法能够有效提高工艺冷凝水的腐蚀评价水平,防止突发腐蚀事件的发生,进而保障了炼化装置的安全、长周期运行。附图说明此处的附图被并入说明书中并构成本说明书的一部分,示出了符合本公开的实施例,并与说明书一起用于解释本公开的原理。图1为本发明一实施方式的炼化装置腐蚀系统的结构示意图;图2为本发明一实施方式的炼化装置工艺冷凝水腐蚀评价流程图。附图标记说明:1:产品分离塔;2:换热器;3:空冷器;4:水冷器;5:分离罐;6:回流泵。通过上述附图,已示出本公开明确的实施例,后文中将有更详细的描述。这些附图和文字描述并不是为了通过任何方式限制本公开构思的范围,而是通过参考特定实施例为本领域技术人员说明本公开的概念。具体实施方式为使本发明的目的、技术方案和优点更加清楚,下面将结合本发明的附图和实施例,对本发明实施例中的技术方案进行清楚、完整地描述,显然,所描述的实施例是本发明一部分实施例,而不是全部的实施例。基于本发明中的实施例,本领域普通技术人员在没有做出创造性劳动前提下所获得的所有其他实施例,都属于本发明保护的范围。本发明的炼化装置工艺冷凝水腐蚀评价方法,包括如下步骤:1)获取炼化装置腐蚀系统工艺冷凝水的ph值及fe2+和fe3+浓度;2)确定ph值对炼化装置腐蚀系统的腐蚀状态和腐蚀影响,并确定对应的腐蚀控制方法;3)确定fe2+和fe3+浓度对炼化装置腐蚀系统的腐蚀状态和腐蚀影响,并确定对应的腐蚀控制方法;4)根据ph值及fe2+和fe3+浓度对炼化装置腐蚀系统的腐蚀状态、腐蚀影响及对应的腐蚀控制方法,获取工艺冷凝水的ph值及fe2+和fe3+浓度对炼化装置腐蚀系统的腐蚀状态、腐蚀影响及对应的腐蚀控制方法;5)对工艺冷凝水的ph值及fe2+和fe3+浓度对炼化装置腐蚀系统的腐蚀状态、腐蚀影响及对应的腐蚀控制方法进行整合。下面以蒸馏装置常顶腐蚀系统的工艺冷凝水腐蚀评价为例,对本发明的炼化装置工艺冷凝水腐蚀评价方法进行进一步说明。图1为本发明一实施方式的炼化装置腐蚀系统的结构示意图,在图1中示出本发明方法主要应用于炼化装置的腐蚀系统的部位及区域。具体地,如图1所示,原料进入产品分离塔1进行分离,塔顶产物经换热器2、空冷器3和水冷器4进入分离罐5,经分离罐5分离形成工艺冷凝水、油气和油,其中部分油经回流泵6回流至产品分离塔1中。图2为本发明一实施方式的炼化装置工艺冷凝水腐蚀评价流程图;如图2所示,本发明的炼化装置工艺冷凝水腐蚀评价方法,包括如下步骤:步骤一:获取腐蚀系统工艺冷凝水的ph值及fe2+和fe3+浓度;具体地,从上述分离罐5分离形成的工艺冷凝水中取样,得到工艺冷凝水样品;随后,采用化学分析方法对工艺冷凝水样品进行分析,得到工艺冷凝水样品的ph值及fe2+和fe3+浓度监测数据,结果见表1。表1工艺冷凝水的ph值及fe2+和fe3+浓度监测数据步骤二:确定工艺冷凝水中ph值及fe2+和fe3+浓度的控制指标及范围;具体地,工艺冷凝水中ph值及fe2+和fe3+浓度的控制指标及范围见表2。表2工艺冷凝水中ph值及fe2+和fe3+浓度的控制指标及范围根据表2,工艺冷凝水中ph值为5.5~7.5时,腐蚀系统ph值控制合格;工艺冷凝水中fe2+和fe3+浓度≤2mg/l时,腐蚀系统fe2+和fe3+浓度控制未超标。步骤三:确定ph值对腐蚀系统的腐蚀状态;具体地,不同ph值控制范围对腐蚀系统的腐蚀状态见表3。表3不同ph值控制范围对腐蚀系统的腐蚀状态步骤四:根据工艺冷凝水ph值获得腐蚀状态评价结论;具体地,根据表1,实测的腐蚀系统工艺冷凝水ph值监测数据为7.6;根据表3,判定腐蚀系统工艺冷凝水ph值控制上限超标,腐蚀系统的腐蚀状态表示为“腐蚀系统ph值控制上限超标”。根据工艺冷凝水ph值获得的腐蚀状态评价结论为:依据常顶腐蚀系统工艺冷凝水ph值监测数据,ph值腐蚀状态评价认为,常顶腐蚀系统ph值控制上限超标。步骤五:确定ph值对腐蚀系统的腐蚀影响;具体地,不同ph值控制范围对腐蚀系统的腐蚀影响见表4。表4不同ph值控制范围对腐蚀系统的腐蚀影响ph监测数据对腐蚀系统的腐蚀影响ph值>8腐蚀系统工艺防腐措施严重过剩,垢下腐蚀显著增大7.5<ph值≤8腐蚀系统工艺防腐措施过剩,垢下腐蚀增大ph值为5.5~7.5腐蚀系统腐蚀受控5≤ph值<5.5腐蚀系统工艺防腐措施不足,酸腐蚀增大ph值<5腐蚀系统工艺防腐措施严重不足,酸腐蚀显著增大步骤六:根据工艺冷凝水ph值获得腐蚀影响评价结论;具体地,根据表1,实测的腐蚀系统工艺冷凝水ph值监测数据为7.6;根据表4,判定工艺冷凝水ph值对腐蚀系统的腐蚀影响并得出腐蚀影响评价结论,该部分腐蚀影响评价结论同时纳入上述“步骤四”的腐蚀状态评价结论。根据工艺冷凝水ph值获得腐蚀评价结论为:依据常顶腐蚀系统工艺冷凝水ph值监测数据,ph值腐蚀评价认为,常顶腐蚀系统ph值控制上限超标,说明常顶腐蚀系统工艺防腐措施过剩,垢下腐蚀增大。步骤七:确定ph值对应的建议性腐蚀控制措施;具体地,不同ph值控制范围对应的腐蚀系统建议性腐蚀消减控制措施见表5。表5ph值对应的建议性腐蚀控制措施步骤八:根据工艺冷凝水ph值监测数据得到腐蚀控制措施评价结论;具体地,根据表1,实测的腐蚀系统工艺冷凝水ph值监测数据为7.6;根据表5,判定腐蚀系统在该ph值对应的建议性腐蚀消减控制措施评价结论,该部分评价结论同时纳入“步骤四”的腐蚀状态评价结论及“步骤六”的腐蚀影响评价结论。根据工艺冷凝水ph值得到的腐蚀评价结论为:依据常顶腐蚀系统工艺冷凝水ph值监测数据,ph值腐蚀评价认为,常顶腐蚀系统ph值上限超标,说明常顶腐蚀系统工艺防腐措施过剩,垢下腐蚀增大。建议:1)优化腐蚀系统工艺防腐注剂措施、减少注剂量;2)按“2次/年”进行腐蚀系统易腐蚀管线剩余壁厚监测,发现减薄,扩检整个系统。步骤九:确定fe2+和fe3+浓度对腐蚀系统的腐蚀状态;具体地,不同fe2+和fe3+浓度控制范围对腐蚀系统的腐蚀状态见表6。表6fe2+和fe3+浓度对腐蚀系统的腐蚀状态步骤十:根据工艺冷凝水fe2+和fe3+浓度监测数据得到腐蚀状态评价结论;具体地,根据表1,实测的腐蚀系统工艺冷凝水fe2+和fe3+浓度为0.28mg/l,依据表6,判定腐蚀系统fe2+和fe3+浓度控制下的腐蚀系统的腐蚀状态并得出腐蚀状态评价结论。根据工艺冷凝水fe2+和fe3+浓度获得的腐蚀状态评价结论为:依据常顶腐蚀系统工艺冷凝水fe2+和fe3+浓度监测数据,fe2+和fe3+浓度腐蚀状态评价认为,常顶腐蚀系统fe2+和fe3+浓度未超标。步骤十一:确定fe2+和fe3+浓度对腐蚀系统的腐蚀影响;具体地,不同fe2+和fe3+浓度控制范围对腐蚀系统的腐蚀影响见表7。表7fe2+和fe3+浓度对腐蚀系统的腐蚀影响步骤十二:根据工艺冷凝水fe2+和fe3+浓度监测数据得到腐蚀影响评价结论;具体地,根据表1,实测的腐蚀系统工艺冷凝水fe2+和fe3+浓度为0.28mg/l,依据表7,判定腐蚀系统fe2+和fe3+浓度控制下对腐蚀系统的腐蚀影响并得出腐蚀影响评价结论;该部分腐蚀影响评价结论同时纳入“步骤十”的腐蚀状态评价结论。根据工艺冷凝水fe2+和fe3+浓度获得的腐蚀评价结论为:依据常顶腐蚀系统工艺冷凝水fe2+和fe3+浓度监测数据,fe2+和fe3+浓度腐蚀评价认为,常顶腐蚀系统fe2+和fe3+浓度未超标,说明腐蚀系统腐蚀不严重。步骤十三:确定fe2+和fe3+浓度对应的建议性腐蚀控制措施;具体地,不同fe2+和fe3+浓度控制范围对应的腐蚀系统建议性腐蚀消减控制措施见表8。表8fe2+和fe3+浓度对应的建议性腐蚀控制措施步骤十四:根据工艺冷凝水fe2+和fe3+浓度监测数据得到腐蚀控制措施评价结论;具体地,根据表1,实测的腐蚀系统工艺冷凝水fe2+和fe3+浓度为0.28mg/l,依据表8,判定腐蚀系统在该fe2+和fe3+浓度控制下的腐蚀系统腐蚀消减控制措施,并得出腐蚀控制措施评价结论;该部分腐蚀评价结论同时纳入“步骤十”的腐蚀状态评价结论及“步骤十二”的腐蚀影响评价结论。根据工艺冷凝水fe2+和fe3+浓度的腐蚀评价结论为:依据常顶腐蚀系统工艺冷凝水监测数据,fe2+和fe3+浓度腐蚀评价认为,常顶腐蚀系统fe2+和fe3+浓度未超标,说明腐蚀系统腐蚀不严重。建议:1)腐蚀系统继续平稳运行;2)按“2次/年”管线测厚进行易腐蚀管线剩余壁厚监测,发现减薄,扩检整个系统。步骤十五:根据上述“步骤八”及“步骤十四”组合形成腐蚀系统工艺冷凝水腐蚀评价结论及建议性腐蚀控制措施。具体地,组合形成的常顶腐蚀系统腐蚀评价结论为:依据常顶腐蚀系统工艺冷凝水监测数据,ph值腐蚀评价认为:常顶腐蚀系统ph值上限超标,说明常顶腐蚀系统工艺防腐措施过剩,垢下腐蚀增大。建议:1)优化腐蚀系统工艺防腐注剂措施、减少注剂量;2)按“2次/年”进行腐蚀系统易腐蚀管线剩余壁厚监测,发现减薄,扩检整个系统。依据常顶腐蚀系统工艺冷凝水监测数据,fe2+和fe3+浓度腐蚀评价认为:常顶腐蚀系统fe2+和fe3+浓度未超标,说明腐蚀系统腐蚀不严重。建议:1)腐蚀系统继续平稳运行;2)按“2次/年”管线测厚进行易腐蚀管线剩余壁厚监测,发现减薄,扩检整个系统。步骤十六:对“步骤十五”形成的腐蚀系统工艺冷凝水腐蚀评价结论进行整合;具体地,腐蚀评价结论的整合原则是:“同项合并、异项保留、突出问题”。整合后的常顶腐蚀系统工艺冷凝水腐蚀评价结论为:依据常顶腐蚀系统工艺冷凝水监测数据,ph值腐蚀评价认为:常顶腐蚀系统ph值上限超标,说明常顶腐蚀系统工艺防腐措施过剩,垢下腐蚀增大。fe2+和fe3+浓度腐蚀评价认为:常顶腐蚀系统fe2+和fe3+浓度未超标,说明腐蚀系统腐蚀不严重。建议:1)优化腐蚀系统工艺防腐注剂措施、减少注剂量;2)按“2次/年”进行腐蚀系统易腐蚀管线剩余壁厚监测,发现减薄,扩检整个系统。可以理解的是,依本发明上述方式(或步骤)形成的智能(计算机语言)判断过程及结论均将受本专利保护。本领域技术人员在考虑说明书及实践这里公开的发明后,将容易想到本公开的其它实施方案。本发明旨在涵盖本公开的任何变型、用途或者适应性变化,这些变型、用途或者适应性变化遵循本公开的一般性原理并包括本公开未公开的本
技术领域:
中的公知常识或惯用技术手段。说明书和实施例仅被视为示例性的,本公开的真正范围和精神由下面的权利要求书指出。应当理解的是,本公开并不局限于上面已经描述并在附图中示出的精确结构,并且可以在不脱离其范围进行各种修改和改变。此外,依本发明上述方式(或步骤)形成的智能(计算机语言)判断过程及结论均将受本专利保护。当前第1页12