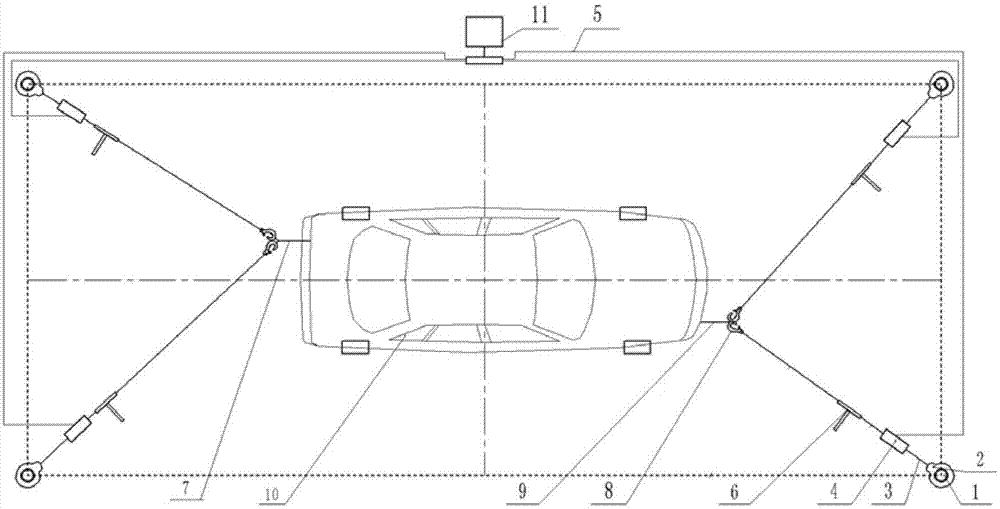
本发明属于车辆测试
技术领域:
,特别是涉及一种消声室内转鼓试验台上车辆动态平衡拉紧方法及束紧装置。
背景技术:
:室内通过噪声测量方法被汽车制造厂商广泛地应用于通过噪声的发生机理、噪声源特性、传递路径状况、部件贡献量分析等工作。室内通过噪声测量通常在装备有转鼓试验台的消声室内进行,车辆在转鼓试验台上进行车辆通过噪声测量时,测试工况有加速、匀速和滑行三个工况。测试车辆的四个轮子放置在试验台上四个柱状转鼓表面主动或被动的相对转动,完成加速、匀速和滑行三个工况的运动。测试过程中测试车辆输出或所受驱动功率有几十至几百千瓦,驱动力非常大。因此,需要对位于试验台上的测试车辆进行拉紧固定,防止被测试车辆窜出造成危险。现有的用于转鼓试验台上车辆的束紧装置一般包含固定立柱、卡箍、钢链、拉紧力调整装置和钢链挂钩。四个立柱分别位于试验台四角,二根位于试验台(对应于车辆)前部,二根位于试验台(对应于车辆)后部。连有钢链的四个卡箍紧扣在立柱上,四根钢链分别与四个拉紧力调整装置一端相连,位于试验台前部的二个拉紧力调整装置的另一端与各自钢链相连,二钢链的另一端均连有挂钩,二挂钩均与固定在车辆前部的牵引杆连接。位于试验台后部的二挂钩均与固定在车辆后部的牵引杆连接。前后钢链均与车辆中轴线成一定的夹角与车辆前后牵引杆连接。车辆静止时,用拉紧力调整装置将车辆将拉紧固定住,然后开始测试,由于车辆设计不同,牵引杆偏心位置不同,用现有装置进行固定和测试时,会产生不平衡力和不平衡力矩,测试过程中车辆摆动明显,轮胎与转鼓之间会产生侧向摩擦力,产生附加轮胎噪声,因此,现有束紧装置影响室内车辆通过噪声测量结果。技术实现要素:鉴于以上所述现有技术的缺点,本发明的目的在于提供一种消声室内转鼓试验台上车辆动态平衡拉紧方法及束紧装置,用于解决现有技术中车辆进行噪声测试时因牵引杆偏心位置不同造成测试过程车辆摆动明显,产生轮胎附加噪声的问题。为实现上述目的及其他相关目的,本发明提供一种消声室内转鼓试验台上车辆动态平衡拉紧方法,其特征在于,包括以下步骤:建立坐标系,根据车辆驱动力及车辆在转鼓试验台上静止时车辆受力状态,计算固定于车辆前牵引杆和后牵引杆的四条钢链的预紧力初始值,预紧钢链;按指定工况运转车辆;实时采集四条钢链拉力;以惯性平衡力系下合外力为零作为约束条件,以合外力矩平方最小为目标函数计算四条钢链的拉力调整值;根据拉力调整值调整钢链拉力;在判定目标函数小于设定值时,开展噪声测试。于本发明的一实施例中,所述建立坐标系,根据车辆驱动力及车辆在转鼓试验台上静止时车辆受力状态,计算固定于车辆前牵引杆和后牵引杆的四条钢链的预紧力初始值,具体包括:建立转鼓试验台的p-x-y-z静坐标系和车辆的o-x’-y’-z’动坐标系;确定前牵引杆受力点、后牵引杆受力点、四个立柱位置、四个车轮与转鼓接触点位置以及车辆质心o位置分别在p-x-y-z静坐标系中坐标;根据车辆驱动力及车辆在转鼓试验台上静止时车辆的受力状态,建立受拉状态下的合外力和合外力矩的静力平衡表达式,计算钢链的预紧力初始值,用以预紧钢链。于本发明的一实施例中,在所述静力平衡表达式,见下式:∑fx=f1x+f2x+f3x+f4x∑fy=f1y+f2y+f3y+f4y+a1ft1+a2ft2+a3ft3+a4ft4+a5ff1+a6ff2+a7ff3+a8ff4∑fz=fn1+fn2+fn3+fn4+gff1=-μfn1ff2=-μfn2ff3=-μfn3ff4=-μfn4∑mx=-fn1l5-fn2l5+fn3l6+fn4l6-a1ft1·h-a2ft2·h-a3ft3h-...a4ft4·h-a5ff1·h-a6ff2·h-a7ff3·h-a8ff4·h∑my=-fn1·l1+fn2·l2-fn3l1+fn4l2∑mz=f1x·(l5+l7)-f1yl3+f2x·(l5+l7)-f2yl3-f3x·(l6+l8)+f3yl4-f4x·(l6+l8)+...f4yl4+a1ft1l1-a2ft2l2+a3ft3l3-a4ft4l4+a5ff1l1-a6ff2l2+a7ff3·l1-a8ff4l2式中,f1x、f2x、f3x、f4x分别为四个钢链拉力在静坐标系x轴的分力;f1y、f2y、f3y、f4y分别为四个钢链拉力在静坐标系y轴的分力;ft1、ft2、ft3、ft4分别为四驱加速时四个车轮所受驱动力;ff1、ff2、ff3、ff4分别为四个轮子所受摩擦力;fn1、fn2、fn3、fn4分别为四个车轮所受转鼓表面的支承力;g为作用于整车质心处垂直地面的重力;μ为滚动阻力系数;l1为车辆左侧与车辆垂直中心线为y’轴的垂直距离;l2为车辆右侧与车辆垂直中心线为y’轴的垂直距离;l3为前牵引杆受力点a与车辆垂直中心线为y’轴的垂直距离;l4为后牵引杆受力点b与车辆垂直中心线为y’轴的垂直距离l5为车辆前侧与车辆水平中心线为x’轴的垂直距离;l6为车辆后侧与车辆水平中心线为x’轴的垂直距离;l7为车辆前侧与前牵引杆受力点a的垂直距离;l8为车辆后侧与后牵引杆受力点b的垂直距离;系数a1、a2、a3、a4、a5、a6、a7、a8根据所述指定工况选取;通过静力平衡表达式解得钢链的预紧力初始值,分别为f10、f20、f30、f40。于本发明的一实施例中,所述指定工况分为:1)车辆为四驱车辆,工况条件有加速工况、匀速工况和滑行工况;2)车辆为前驱车辆,工况条件有加速工况、匀速工况和滑行工况;3)车辆为后驱车辆,工况条件有加速工况、匀速工况和滑行工况。于本发明的一实施例中,所述以惯性平衡力系下合外力为零作为约束条件,以合外力矩平方最小为目标函数计算四条钢链的拉力调整值,具体包括:建立转鼓试验台的p-x-y-z静坐标系和车辆的o-x’-y’-z’动坐标系;根据车辆驱动力及车辆在转鼓试验台上指定工况下车辆的受力状态,建立惯性平衡力系,计算合外力∑f和合外力矩∑m;以惯性力平衡力系下合外力为零作为约束条件,以合外力矩平方最小为目标函数,建立目标函数和优化条件数学模型;采用单目标非线性优化算法求解获得钢链的拉力调整值。于本发明的一实施例中,建立惯性平衡力系,计算合外力∑f和合外力矩∑m,具体包括:∑fx=f1x+f2x+f3x+f4x+ft1x+ft2x+ft3x+ft4x+ff1x+ff2x+ff3x+ff4x∑fy=f1y+f2y+f3y+f4y+ft1y+ft2y+ft3y+ft4y+ff1y+ff2y+ff3y+ff4y∑fz=fn1+fn2+fn3+fn4+gff1=-μfn1,ff2=-μfn2,ff3=-μfn3,ff4=-μfn4,g=mg合外力∑mx=-fn1·ln1x-fn2·ln2x+fn3·ln3x+fn4·ln4x-g·lgx-ft1yh-ft2yh..-ft3yh-ft4yh-ff1yh-ff2yh-ff3yh-ff4yh∑my=-fn1·ln1y+fn2·ln2y-fn3·ln3y+fn4·ln4y+g·lgy+ft1xh+ft2xh..+ft3xh+ft4xh+ff1xh+ff2xh+ff3xh+ff4xh∑mz=f1xl1x-f1yl1y+f2xl2x-f2yl2y-f3xl3x+f3yl3y-f4xl4x+f4yl4y+ft1xlt1x..+ft1ylt1y+ft2xlt2x-ft2ylt2y-ft3xlt3x+ft3ylt3y-ft4xlt4x-ft4ylt4y..+ff1xlf1x+ff1ylf1y+ff2xlf2x-ff2ylf2y-ff3xlf3x+ff3ylf3y-ff4xlf4x..-ff4ylf4y合外力矩式中,f1x、f2x、f3x、f4x、为四个钢链拉力在x轴的分力;f1y、f2y、f3y、f4y为四个钢链拉力在y轴的分力;ft1x、ft2x、ft3x、ft4x为四个驱动力在x轴的分力;ft1y、ft2y、ft3y、ft4y为四个钢驱动力在y轴的分力;ff1x、ff2x、ff3x、ff4x为四个摩擦力在x轴的分力;ff1y、ff2y、ff3y、ff4y为四个摩擦力在y轴的分力;fn1、fn2、fn3、fn4分别为四个车轮所受转鼓表面的支承力;l1x、l2x、l3x、l4x分别为四个钢链拉力在x轴分力与p-x-z平面的垂直距离;l1y、l2y、l3y、l4y分别为四个钢链拉力在y轴分力与p-y-z平面的垂直距离;lt1x、lt2x、lt3x、lt4x为四个驱动力在x轴分力与p-x-z平面的垂直距离;lt1y、lt2y、lt3y、lt4y为四个驱动力在y轴分力与p-y-z平面的垂直距离;lf1x、lf2x、lf3x、lf4x为四个摩擦力在x轴分力与p-x-z平面的垂直距离;lf1y、lf2y、lf3y、lf4y为四个摩擦力在y轴分力与p-y-z平面的垂直距离;h点为p点距离地面的垂直距离;g为作用于整车质心o处垂直地面的重力;lgx为质心o与p-x-z平面的垂直距离;lgy为质心o与p-y-z平面的垂直距离。于本发明的一实施例中,所述建立目标函数和优化条件数学模型,如下:目标函数minfval=∑m2=mx2+my2+mz2约束条件式中,fx、fy、fz分别为车辆所受合外力在x轴、y轴和z轴的分力;mx、my、mz分别为合外力矩分别在x轴、y轴和z轴的分量;△θ为动坐标系的o-y’-z’平面与静坐标系p-y-z平面的角度误差;fn1、fn2、fn3、fn4分别为四个车轮所受转鼓表面的支承力;f1y、f2y分别为与前牵引杆相连的两条钢链拉力在静坐标系y轴的分力;f1、f2、f3、f4分别为四条钢链的拉力;ma为作用于车辆质心o处的驱动力。本发明还提供了一种消声室内转鼓试验台上车辆动态平衡束紧装置,包括立柱、钢链、拉紧力调整装置,所述车辆平衡束紧装置还包括有拉力传感器和监控主机,所述拉力传感器加装于所述钢链,用于实时检测钢链拉力;所述监控主机电性连接所述拉力传感器,用于采集拉力传感器检测的所述钢链拉力,和计算车辆静止时的钢链预紧力初始值以及计算指定工况下的钢链拉力调整数值。于本发明的一实施例中,所述监控主机包括:采集器、处理器、存储器和显示屏;所述采集器用于采集拉力传感器检测获得的钢链拉力;所述处理器分别连接所述存储器、采集器和显示屏,用于车辆静止时钢链预紧力初始值和指定工况下的钢链的拉力调整值;所述存储器,用于供处理器调取计算钢链预紧力初始值和指定工况下的钢链的拉力调整值时所用的数学模型;显示屏,用于显示钢链的预紧力初始值和指定工况下的钢链的拉力调整值。于本发明的一实施例中,所述监控主机无线连接所述拉力传感器。如上所述,本发明的消声室内转鼓试验台上车辆动态平衡拉紧方法及束紧装置,具有以下有益效果:本发明通过拉力传感器测量钢链拉力大小,在指定工况条件下,以惯性平衡力系下合外力为零作为约束条件,以合外力矩平方最小为目标函数获取四条钢链的拉力调整值,通过拉力调整装置调整钢链拉力,实现消声室内转鼓试验台上测试车辆的动态平衡束紧,减少测试过程中车辆摆动和轮胎与转鼓之间产生的侧向摩擦力的可能,降低轮胎噪声,为室内通过噪声测量提供更加真实的模拟环境、提高测量精度。附图说明图1显示为本发明的消声室内转鼓试验台上车辆动态平衡束紧装置的结构示意图。图2显示为本发明的消声室内转鼓试验台上车辆动态平衡拉紧方法的流程图。图3显示为本发明的在转鼓试验台俯视图上不包含安装误差的车辆静止时尺寸图。图4显示为本发明的在转鼓试验台侧视图上不包含安装误差的车辆静止时尺寸图。图5显示为本发明的在转鼓试验台俯视图上包含安装误差的车辆静止时尺寸图。图6显示为本发明的在转鼓试验台侧视图上包含安装误差的车辆静止时尺寸图。图7显示为本发明的在转鼓试验台俯视图上不包含安装误差的车辆静止时受力分析图。图8显示为本发明的在转鼓试验台侧视图上不包含安装误差的车辆静止时受力分析图。图9显示为本发明的在转鼓试验台俯视图上包含安装误差的车辆运行工况下的受力分析图。图10显示为本发明的在转鼓试验台侧视图上包含安装误差的车辆运行工况下的受力分析图。图11显示为本发明的在四驱加速工况下目标函数小于设定值时的拉力f1的波动趋势图。图12显示为本发明的在四驱加速工况下目标函数小于设定值时的拉力f2的波动趋势图。图13显示为本发明的在四驱加速工况下目标函数小于设定值时的拉力f3的波动趋势图。图14显示为本发明的在四驱加速工况下目标函数小于设定值时的拉力f4的波动趋势图。图15显示为本发明的在四驱加速工况下目标函数小于设定值时的目标函数波动趋势图。图16显示为本发明的在四驱加速工况下目标函数不小于设定值时的拉力f1波动趋势图。图17显示为本发明的在四驱加速工况下目标函数不小于设定值时的拉力f2波动趋势图。图18显示为本发明的在四驱加速工况下目标函数不小于设定值时的拉力f3波动趋势图。图19显示为本发明的在四驱加速工况下目标函数不小于设定值时的拉力f4波动趋势图。图20显示为本发明的在四驱加速工况下目标函数不小于设定值时的目标函数波动趋势图。元件标号说明1立柱2卡箍3钢链4拉力传感器5传输线6拉紧力调整装置7后牵引杆8挂钩9前牵引杆10车辆11监控主机s1~s7步骤具体实施方式以下由特定的具体实施例说明本发明的实施方式,熟悉此技术的人士可由本说明书所揭露的内容轻易地了解本发明的其他优点及功效。须知,本说明书所附图式所绘示的结构、比例、大小等,均仅用以配合说明书所揭示的内容,以供熟悉此技术的人士了解与阅读,并非用以限定本发明可实施的限定条件,故不具技术上的实质意义,任何结构的修饰、比例关系的改变或大小的调整,在不影响本发明所能产生的功效及所能达成的目的下,均应仍落在本发明所揭示的技术内容得能涵盖的范围内。同时,本说明书中所引用的如“上”、“下”、“左”、“右”、“中间”及“一”等的用语,亦仅为便于叙述的明了,而非用以限定本发明可实施的范围,其相对关系的改变或调整,在无实质变更技术内容下,当亦视为本发明可实施的范畴。请参阅图1,本发明提供了一种消声室内转鼓试验台上车辆动态平衡束紧装置,包括立柱1、钢链3、拉紧力调整装置6,四根立柱1分别位于转鼓试验台四角,位于转鼓试验台前部的两根所述立柱1通过钢链3连接车辆10的前牵引杆9,位于转鼓试验台后部的两根立柱1通过钢链3连接车辆10的后牵引杆7。所述钢链3一端连有挂钩8,通过挂钩8连接前牵引杆9/后牵引杆7,钢链3另一端连有卡箍2紧扣于立柱1。所述车辆平衡束紧装置还包括有拉力传感器4和监控主机11,在每条钢链3上都加装所述拉力传感器4,用于实时检测钢链3的拉力;所述监控主机11电连接所述拉力传感器4,用于采集拉力传感器4检测的所述钢链3拉力,并计算获取对应所述钢链3拉力的调整值。需要说明的是,监控主机11可以通过无线连接拉力传感器4,拉力传感器4直接连接无线发射装置,由无线发射装置向监控主机11发送钢链3拉力信号;也可以采用传输线5连接拉力传感器4的输出接口。进一步的,所述监控主机11包括:采集器、处理器、存储器和显示屏;所述采集器用于采集拉力传感器4检测获得的钢链3拉力;所述处理器分别连接所述存储器、采集器和显示屏,用于车辆10静止时钢链3的预紧力初始值和指定工况下的钢链3的拉力调整值;所述存储器,用于供处理器调取计算钢链3的预紧力初始值和指定工况下的钢链3的拉力调整值时所用的数学模型;显示屏,用于显示钢链3的预紧力初始值、钢链3拉力和指定工况下的钢链3的拉力调整值。本发明提供一种消声室内转鼓试验台上车辆动态平衡拉紧方法,如图2所示,应用于室内通过噪声测量过程,具体由以下步骤实现:步骤s1,建立坐标系,根据车辆驱动力及车辆10在转鼓试验台上静止时车辆10的受力状态,解算固定于车辆前牵引杆9和后牵引杆7的四条钢链3的预紧力初始值,用以预紧钢链3。需要说明的是,所述步骤s1具体包括:步骤s11,建立静坐标系和动坐标系。所述静坐标系和动坐标系参考图3和图4。所述静坐标系设定为:转鼓试验台水平中心线和垂直中心线相交于p点,定义为静坐标原点p,p点距离地面的垂直距离h,经p点沿转鼓试验台前后方向的垂直中心线为y轴,经p点沿转鼓试验台左右方向的水平中心线为x轴,垂直于p-x-y平面且垂足过p点为z轴。x,y,z轴正方向满足右手定则,形成p-x-y-z静坐标系,静坐标系p-x-y平面平行于地面。所有坐标点都是在静坐标系下度量。按此定义,图3中前牵引杆受力点a、后牵引杆受力点b和四条钢链3在p-x-y平面上。所述动坐标系设定为:车辆水平轴线和垂直中心线相交于车辆质心o点,定义为动坐标原点o,经质心o点且沿车辆10前后方向的垂直中心线为y’轴,经质心o点且沿车辆10左右方向的水平中心线为x’轴,垂直于o-x’-y’平面且垂足过o点为z’轴。x’、y’、z’轴正方向满足右手定则,形成o-x’-y’-z’动坐标系,z’轴平行于z轴,动坐标系o-x’-y’平面平行于静坐标系p-x-y平面。车辆10在停放在转鼓试验台上时,通过专用工具将车轮分别与转鼓试验台的水平中心线和垂直中心线前后对中放置,但由于车辆质心o偏移和安装误差不可避免,因此,车辆o-x’-z’平面、o-y’-z’平面与转鼓p-x-z平面、p-y-z平面不重合,存在位置误差和角度误差,即点o偏离p-x-z平面δy、点o偏离p-y-z平面δx;o-y’-z’与p-y-z平面有一δθ的角度误差。设定δθ顺时针为正,逆时针为负,请参阅图5和图6。步骤s12,确定前牵引杆9受力点a、后牵引杆7受力点b、四个立柱1位置、四个车轮与转鼓接触点位置以及车辆质心位置分别在p-x-y-z静坐标系中坐标:1)前牵引杆受力点a坐标和后牵引杆受力点b坐标:在图5中点a为前牵引杆受力点,点b为后牵引杆受力点,设点a、b的坐标分别为(ax,ay,az)、(bx,by,bz),它们的坐标见下式:a=(ax,ay,az)=((l3·cos△θ+(l5+l7)·sin△θ+△x),((l5+l7)·cos△θ-l3·sin△θ+△y),0)b=(bx,by,bz)=((-(l4·cos△θ+(l6+l8)·sin△θ-△x)),(-((l6+l8)·cos△θ-l4·sin△θ-△y)),0)式中:l3为前牵引杆受力点a与车辆垂直中心线为y’轴的垂直距离;l4为后牵引杆受力点b与车辆垂直中心线为y’轴的垂直距离;l5为车辆前侧与车辆水平中心线为x’轴的垂直距离;l6为车辆后侧与车辆水平中心线为x’轴的垂直距离;l7为前牵引杆受力点a与车辆前侧的垂直距离;l8为后牵引杆受力点b与车辆后侧的垂直距离;△θ为动坐标系的o-y’-z’平面与静坐标系p-y-z平面的角度误差;△x为质心o点偏离p-y-z平面的位置误差;△y为质心o点偏离p-x-z平面的的位置误差。2)立柱坐标:在图5中,a1、a2、a3、a4是四个立柱1与p-x-y平面相交的点,a1坐标为:a2坐标为:a3坐标为:a4坐标为:式中,x0、y0分别为立柱水平方向和垂直方向的间距。在本实施例中,通过前牵引杆受力点a、后牵引杆受力点b点坐标和转鼓试验台四个立柱1的坐标,计算获得在静坐标系中p-x-y平面上四条钢链3分别与x轴的角度θ1、θ2、θ3、θ4。所述计算所述角度θ1、θ2、θ3、θ4的计算公式如下:式中,a1x、a1y为立柱a1坐标;a2x、a2y为立柱a2坐标;a3x、a3y为立柱a3坐标;a4x、a4y为立柱a4坐标;ax、ay为前牵引杆受力点a坐标;bx、by为后牵引杆受力点b坐标。3)四个车轮与转鼓试验台表面接触点坐标:在图5中,t1、t2、t3、t4是四个车轮分别与转鼓试验台表面的接触点;t1:(t1x,t1y,t1z)=(-(l1cos△θ-△x-l5sin△θ),l5cos△θ+△y+l1sin△θ,-h);t2:(t2x,t2y,t2z)=(l2cos△θ+△x+l5sin△θ,l5cos△θ+△y-l1sin△θ,-h);t3:(t3x,t3y,t3z)=(-(l1cos△θ-△x+l6sin△θ),-(l6cos△θ-△y-l1sin△θ),-h);t4:(t4x,t4y,t4z)=(l2cos△θ+△x-l6sin△θ,-(l6cos△θ+l2sin△θ-△y),-h)。式中:l1为车辆左侧与车辆垂直中心线为y’轴的垂直距离;l2为车辆右侧与车辆垂直中心线为y’轴的垂直距离;l5为车辆前侧与车辆水平中心线为x’轴的垂直距离;l6为车辆后侧与车辆水平中心线为x’轴的垂直距离;h为p点距离地面的垂直距离;△θ为动坐标系的o-y’-z’平面与静坐标系p-y-z平面的角度误差;△x为质心o点偏离p-y-z平面的位置误差;△y为质心o点偏离p-x-z平面的的位置误差。4)车辆质心在p-x-y-z静坐标系下的坐标:点o为车辆质心,o:(ox,oy,oz)=(△x,△y,△z)式中,△x为质心o点偏离p-y-z平面的位置误差;△y为质心o点偏离p-x-z平面的的位置误差。△z为点o偏离p-x-y平面的的位置误差。步骤s13,根据车辆驱动力及车辆10在转鼓试验台上静止时车辆10的受力状态,建立受拉状态下的合外力和合外力矩的静力平衡表达式,计算钢链3的预紧力初始值,用以预紧钢链3。参阅图7和图8,描述了车辆10静止状态受力分析图,静止状态受力时不考虑车辆质心o偏移和安装误差。设静止状态o-y’-z’平面与o-y-z重合,o-x’-z’平面与o-x-z平面重合,f1、f2、f3、f4分别为四条钢链3的拉力,拉力方向以图示方向为正方向,将四个方向的拉力f1、f2、f3、f4分解在x、y轴上方便计算,图中的ft1、ft2、ft3、ft4为四驱加速时四个车轮所受驱动力,ff1、ff2、ff3、ff4分别为四个轮子所受摩擦力,fn1、fn2、fn3、fn4分别为四个车轮所受转鼓试验台表面的支承力,g为作用于整车质心处垂直地面的重力,g=mg,m是车辆整备质量。根据车辆10在转鼓试验台上受力状态,建立受拉状态下的合外力和合外力矩的静力平衡表达式,见下式:∑fx=f1x+f2x+f3x+f4x∑fy=f1y+f2y+f3y+f4y+a1ft1+a2ft2+a3ft3+a4ft4+a5ff1+a6ff2+a7ff3+a8ff4∑fz=fn1+fn2+fn3+fn4+gff1=-μfn1ff2=-μfn2ff3=-μfn3ff4=-μfn4∑mx=-fn1l5-fn2l5+fn3l6+fn4l6-a1ft1·h-a2ft2·h-a3ft3h-...a4ft4·h-a5ff1·h-a6ff2·h-a7ff3·h-a8ff4·h∑my=-fn1·l1+fn2·l2-fn3l1+fn4l2∑mz=f1x·(l5+l7)-f1yl3+f2x·(l5+l7)-f2yl3-f3x·(l6+l8)+f3yl4-f4x·(l6+l8)+...f4yl4+a1ft1l1-a2ft2l2+a3ft3l3-a4ft4l4+a5ff1l1-a6ff2l2+a7ff3·l1-a8ff4l2式中,f1x、f2x、f3x、f4x为四个钢链3拉力在静坐标系x轴的分力;f1y、f2y、f3y、f4y为四个钢链3拉力在静坐标系y轴的分力;ft1、ft2、ft3、ft4为四驱加速时四个车轮所受驱动力;ff1、ff2、ff3、ff4分别为四个轮子所受摩擦力;fn1、fn2、fn3、fn4分别为四个车轮所受转鼓试验台表面的支承力;g为作用于整车质心处垂直地面的重力;μ为滚动阻力系数;l1为车辆左侧与车辆垂直中心线为y’轴的垂直距离;l2为车辆右侧与车辆垂直中心线为y’轴的垂直距离;l3为前牵引杆受力点a与车辆垂直中心线为y’轴的垂直距离;l4为后牵引杆受力点b与车辆垂直中心线为y’轴的垂直距离l5为车辆前侧与车辆水平中心线为x’轴的垂直距离;l6为车辆后侧与车辆水平中心线为x’轴的垂直距离;l7为车辆前侧与前牵引杆受力点a的垂直距离;l8为车辆后侧与后牵引杆受力点b的垂直距离;系数a1、a2、a3、a4、a5、a6、a7、a8根据不同工况条件选取。静态时,驱动力、摩擦力为零;为计算预紧拉力,人为地在车辆质心o处施加大小为ma,方向向前的驱动力;为保证实验过程中实施加速时车辆前侧的钢链3拉力大于零,该钢链3拉力应满足:f1>0,f2>0。取l1=l2、l3=l4、l5=l6、l7=l8可得将驱动力作用于车辆质心o,大小为fr=ma,可得静力表达式,如下:静力表达式:f1y+f2y+f3y+f4y+ma=0,由以上条件将合外力和和合外力矩的静力平衡表达式简化为下式:f1·sinθ1+f2·sinθ2+f3·sinθ3+f4·sinθ4+ma=0f1·cosθ1+f2·cosθ2+f3·cosθ3+f4·cosθ4=0其中,θ1、θ2、θ3、θ4、m、a为已知量,f1、f2、f3、f4此时有无穷多组解,因此需增加约束条件,令f3y+f4y=n·ma,n为变量,由人为设定,约束条件添加后求得的f1、f2、f3、f4即为钢链3的预紧力初始值。以加速工况为例,取y方向向后的预紧力的合力f3y+f4y=-1.2ma,可得y方向向前的预紧力为:f1y+f2y=0.2ma,将上述已知量代入静力表达式,此时解得的f1、f2、f3、f4为钢链3的预紧力初始值f10、f20、f30、f40,所述四条钢链3的预紧力初始值大小分别为:式中,θ1、θ2、θ3、θ4分别为在静坐标系中p-x-y平面上四条钢链3分别与x轴的角度;l3为前牵引杆受力点a与车辆垂直中心线为y’轴的垂直距离;l5为车辆前侧与车辆水平中心线为x’轴的垂直距离;l7为车辆前侧与前牵引杆受力点a的垂直距离。根据解得的f10、f20、f30、f40预紧钢链3,车辆10按照指定的测试工况运行,开展后续调试。步骤s2,按指定工况运转车辆10;所述指定工况分为:1)车辆10为四驱车辆,工况条件有加速工况、匀速工况和滑行工况;2)车辆10为前驱车辆,工况条件有加速工况、匀速工况和滑行工况;3)车辆10为后驱车辆,工况条件有加速工况、匀速工况和滑行工况。步骤s3,实时采集四条钢链3拉力;由安装在钢链3上的拉力传感器4测量。步骤s4,根据实时采集的钢链3拉力,以惯性平衡力系下合外力为零作为约束条件,以合外力矩平方最小为目标函数fval解得四条钢链3的拉力调整值,用以调整钢链3拉力;具体的,步骤s41,建立转鼓试验台的p-x-y-z静坐标系和车辆10的o-x’-y’-z’动坐标系;根据车辆驱动力及车辆10在转鼓试验台上指定工况下车辆10的受力状态,建立惯性平衡力系,计算合外力和合外力矩:请参阅图9和图10,描述了转鼓试验台上的车辆10按指定工况运行时的受力分析图,采用p-x-y-z静坐标系和o-x’-y’-z’动坐标系;在指定工况下运行的受力分析时,考虑车辆质心o偏移和安装误差。f1、f2、f3、f4分别为四条钢链3的拉力,拉力方向以图示方向为正方向,将四个方向的拉力f1、f2、f3、f4分解在x、y轴上方便计算,图中的ft1、ft2、ft3、ft4为四驱加速时四个车轮所受驱动力,ff1、ff2、ff3、ff4分别为四个轮子所受摩擦力,fn1、fn2、fn3、fn4分别为四个转鼓表面对车轮的支承力,g为作用于整车质心处垂直地面的重力。参照图9和图10,建立惯性力平衡力系下得到步骤s4中的合外力和合外力矩表达式,合外力矩计算向原点p求力矩,力矩以符合左手定则为正,具体见下式:∑fx=f1x+f2x+f3x+f4x+ft1x+ft2x+ft3x+ft4x+ff1x+ff2x+ff3x+ff4x∑fy=f1y+f2y+f3y+f4y+ft1y+ft2y+ft3y+ft4y+ff1y+ff2y+ff3y+ff4y∑fz=fn1+fn2+fn3+fn4+gff1=-μfn1,ff2=-μfn2,ff3=-μfn3,ff4=-μfn4,g=mg合外力∑mx=-fn1·ln1x-fn2·ln2x+fn3·ln3x+fn4·ln4x-g·lgx-ft1yh-ft2yh..-ft3yh-ft4yh-ff1yh-ff2yh-ff3yh-ff4yh∑my=-fn1·ln1y+fn2·ln2y-fn3·ln3y+fn4·ln4y+g·lgy+ft1xh+ft2xh..+ft3xh+ft4xh+ff1xh+ff2xh+ff3xh+ff4xh∑mz=f1xl1x-f1yl1y+f2xl2x-f2yl2y-f3xl3x+f3yl3y-f4xl4x+f4yl4y+ft1xlt1x..+ft1ylt1y+ft2xlt2x-ft2ylt2y-ft3xlt3x+ft3ylt3y-ft4xlt4x-ft4ylt4y..+ff1xlf1x+ff1ylf1y+ff2xlf2x-ff2ylf2y-ff3xlf3x+ff3ylf3y-ff4xlf4x..-ff4ylf4y合外力矩式中:f1x、f2x、f3x、f4x、为四个钢链3拉力在x轴的分力;f1y、f2y、f3y、f4y为四个钢链3拉力在y轴的分力;ft1x、ft2x、ft3x、ft4x为四个驱动力在x轴的分力;ft1y、ft2y、ft3y、ft4y为四个驱动力在y轴的分力;ff1x、ff2x、ff3x、ff4x为四个摩擦力在x轴的分力;ff1y、ff2y、ff3y、ff4y为四个摩擦力在y轴的分力;fn1、fn2、fn3、fn4分别为四个车轮所受转鼓试验台表面的支承力;l1x、l2x、l3x、l4x分别为四个钢链拉力在x轴分力与p-x-z平面的垂直距离;l1y、l2y、l3y、l4y分别为四个钢链拉力在y轴分力与p-y-z平面的垂直距离;lt1x、lt2x、lt3x、lt4x为四个驱动力在x轴分力与p-x-z平面的垂直距离;lt1y、lt2y、lt3y、lt4y为四个驱动力在y轴分力与p-y-z平面的垂直距离;lf1x、lf2x、lf3x、lf4x为四个摩擦力在x轴分力与p-x-z平面的垂直距离;lf1y、lf2y、lf3y、lf4y为四个摩擦力在y轴分力与p-y-z平面的垂直距离;h点为p点距离地面的垂直距离;g为作用于整车质心o处垂直地面的重力;lgx为质心o与p-x-z平面的垂直距离;lgy为质心o与p-y-z平面的垂直距离。其中,四个钢链3拉力分别在x轴和y轴的分力为:f1x=f1cosθ1,f1y=f1sinθ1f2x=f2cosθ2,f2y=f2sinθ2f3x=f3cosθ3,f3y=f3sinθ3f4x=f4cosθ4,f4y=f4sinθ4四个驱动力分别在x轴和y轴的分力为:ft1x=a1ft1sin△θ,ft1y=a1ft1cos△θft2x=a2ft2sin△θ,ft2y=a2ft2cos△θft3x=a3ft3sin△θ,ft3y=a3ft3cos△θft4x=a4ft4sin△θ,ft4y=a4ft4cos△θ四个摩擦力分别在x轴和y轴的分力为:ff1x=a5ff1sin△θ,ff1y=a5ff1cos△θff2x=a6ff2sin△θ,ff2y=a6ff2cos△θff3x=a7ff3sin△θ,ff3y=a7ff3cos△θff4x=a8ff4sin△θ,ff4y=a8ff4cos△θp-x-z平面、p-y-z平面分别与四个钢链3拉力、四个驱动力、四个摩擦力各自在x轴、y轴分力的垂直距离为:l1x=ay,l1y=axl2x=ay,l2y=axl3x=-by,l3y=-bxl4x=-by,l4y=-bxlt1x=t1y,lt1y=-t1xlt2x=t2y,lt2y=t2xlt3x=-t3y,lt3y=-t3xlt4x=-t4y,lt4y=t4xln1x=t1y,ln1y=-t1xln2x=t2y,ln2y=t2xln3x=-t3yln3y=-t3xln4x=-t4y,ln4y=t4xlgx=△y,lgy=△xlf1x=t1y,lf1y=-t1xlf2x=t2y,lf2y=t2xlf3x=-t3y,lf3y=-t3xlf4x=-t4y,lf4y=t4xln1x=t1y,ln1y=-t1xln2x=t2y,ln2y=t2xln3x=-t3yln3y=-t3xln4x=-t4y,ln4y=t4xlgx=△y,lgy=△x其中,t1x、t1y、t1z为接触点t1的坐标;t2x、t2y、t2z为接触点t2的坐标;t3x、t3y、t3z为接触点t3的坐标;t4x、t4y、t4z为接触点t4的坐标;δx为点o偏离p-y-z平面的位置误差值;δy为点o偏离p-x-z平面的位置误差值;ax、ay为前牵引杆受力点a坐标bx、by为后牵引杆受力点b坐标。在计算拉力、驱动力和摩擦力中,θ1、θ2、θ3、θ4为四条钢链3在p-x-y平面上与x轴夹角,计算公式如下:式中,l3为前牵引杆受力点a与车辆垂直中心线为y’轴的垂直距离;l4为后牵引杆受力点b与车辆垂直中心线为y’轴的垂直距离l5为车辆前侧与车辆水平中心线为x’轴的垂直距离;l6为车辆后侧与车辆水平中心线为x’轴的垂直距离;l7为车辆前侧与前牵引杆受力点a的垂直距离;l8为车辆后侧与前牵引杆受力点b的垂直距离;δx为车辆质心o偏离p-y-z平面的位置误差值;δy为车辆质心o偏离p-x-z平面的位置误差值;x0分别为两立柱1在水平方向的间距;y0分别为两立柱1在垂直方向的间距。图9和图10中驱动力和摩擦力方向是以四驱加速时为例,四驱、前驱或者后驱,在不同工况条件下,驱动力和摩擦力的方向会有不同,所以计算牵引分力、支承力与摩擦力分力时用系数a1、a2、a3、a4、a5、a6、a7、a8来表示不同工况条件下驱动力和摩擦力的方向变化,见下表1-3:表1四驱车辆在不同工况条件下驱动力和摩擦力的方向变化系数表运行工况a1a2a3a4a5a6a7a8加速工况下11111111匀速工况下11111111滑行工况下-1-1-1-11111表2前驱车辆在不同工况条件下驱动力和摩擦力的方向变化系数表运行工况a1a2a3a4a5a6a7a8加速工况下11001111匀速工况下11001111滑行工况下-1-1-1-11111表3后驱车辆在不同工况条件下驱动力和摩擦力的方向变化系数表运行工况a1a2a3a4a5a6a7a8加速工况下00111111匀速工况下00111111滑行工况下-1-1-1-11111在转鼓试验台上,倒拖即转鼓带车轮转动是一种特殊情况,此时车辆10没有动力,由转鼓带动车轮,在倒拖模型时a1、a2、a3、a4、a5、a6、a7、a8的取值针对不同工况从表1-3中选取,此时摩擦力计算采用上述摩擦力和支撑力分力的计算公式,但是此时驱动力需要通过转鼓的力矩t和转鼓的半径r计算,转鼓单元的力矩和转鼓半径r属于已知条件。在试验时,由于钢链3的弹性、轮胎摩擦特性、车辆10放置不对中等因素的影响,其加速度呈现震荡特性,拉力波动幅值为时变函数,可近似表示为:a=a0+△a·sin(ωt);式中,a0为指定工况的加速度大小;△a为拉力波动幅值,通常为a0的5%,ω为加速度波动角频率,ω=2πf,f=2~5hz。由加速度波动可得车辆轮胎驱动扭矩波动表达式:t=[(a0+△a·sin(ωt))·m+μ·(fn1+fn2+fn3+fn4)]·r;式中,fn1、fn2、fn3、fn4分别为四个车轮所受转鼓试验台表面的支承力;m为车辆整备质量;μ为滚动阻力系数。步骤s42,以惯性力平衡力系下合外力为零作为约束条件,以合外力矩平方最小为目标函数fval,建立目标函数和优化条件数学模型;具体的目标函数和优化条件数学模型见下式:目标函数minfval=∑m2=mx2+my2+mz2约束条件式中,fx、fy、fz分别为车辆所受合外力在x轴、y轴和z轴的分力;mx、my、mz分别为合外力矩分别在x轴、y轴和z轴的分量;△θ为动坐标系的o-y’-z’平面与静坐标系p-y-z平面的角度误差;fn1、fn2、fn3、fn4分别为四个车轮所受转鼓表面的支承力;f1y、f2y分别为与前牵引杆9相连的两条钢链3拉力在静坐标系y轴的分力;f1、f2、f3、f4分别为四条钢链3的拉力;ma为车辆质心o处的驱动力。步骤s43,采用单目标非线性优化算法求解获得钢链3的拉力调整值;采用如下求解公式:functionf=fun9(x)globall1;globall2;globall3;globall4;globall5;globall6;globall7;globall8;globaldx;globaldy;globalx00;globaly0;globalm;globalh;globalr;globalg;globalt;globalft1;globalft2;globalft3;globalft4;globalu;globala1;globala2;globala3;globala4;globala5;globala6;globala7;globala8;f=(x(1).*cos((pi+atan(((0.5.*y0)-((l5+l7).*cos(x(9))-l3.*sin(x(9))+dy))/((-0.5.*x00)-...(l3.*cos(x(9))+(l5+l7).*sin(x(9))+dx))))).*((l5+l7).*cos(x(9))-l3.*sin(x(9))+dy)-...x(1).*sin((pi+atan(((0.5.*y0)-((l5+l7).*cos(x(9))-l3.*sin(x(9))+dy))/((-0.5.*x00)-...(l3.*cos(x(9))+(l5+l7).*sin(x(9))+dx))))).*(l3.*cos(x(9))+(l5+l7).*sin(x(9))+dx)+...x(2).*cos((atan(((0.5.*y0)-((l5+l7).*cos(x(9))-l3.*sin(x(9))+dy))/((0.5.*x00)-...(l3.*cos(x(9))+(l5+l7).*sin(x(9))+dx))))).*((l5+l7).*cos(x(9))-l3.*sin(x(9))+dy)-...x(2).*sin((atan(((0.5.*y0)-((l5+l7).*cos(x(9))-l3.*sin(x(9))+dy))/((0.5.*x00)-...(l3.*cos(x(9))+(l5+l7).*sin(x(9))+dx))))).*(l3.*cos(x(9))+(l5+l7).*sin(x(9))+dx)-...x(3).*cos((pi+atan(((-0.5.*y0)-(-((l6+l8).*cos(x(9))-l4.*sin(x(9))-dy)))/((-0.5.*x00)-...(-(l4.*cos(x(9))+(l6+l8).*sin(x(9))-dx)))))).*(-(-((l6+l8).*cos(x(9))-l4.*sin(x(9))-dy)))+...x(3).*sin((pi+atan(((-0.5.*y0)-(-((l6+l8).*cos(x(9))-l4.*sin(x(9))-dy)))/((-0.5.*x00)-...(-(l4.*cos(x(9))+(l6+l8).*sin(x(9))-dx)))))).*(-(-(l4.*cos(x(9))+(l6+l8).*sin(x(9))-dx)))-...x(4).*cos((2.*pi+atan(((-0.5.*y0)-(-((l6+l8).*cos(x(9))-l4.*sin(x(9))-dy)))/((0.5.*x00)-...(-(l4.*cos(x(9))+(l6+l8).*sin(x(9))-dx)))))).*(-(-((l6+l8).*cos(x(9))-l4.*sin(x(9))-dy)))+...x(4).*sin((2.*pi+atan(((-0.5.*y0)-(-((l6+l8).*cos(x(9))-l4.*sin(x(9))-dy)))/((0.5.*x00)-...(-(l4.*cos(x(9))+(l6+l8).*sin(x(9))-dx)))))).*(-(-(l4.*cos(x(9))+(l6+l8).*sin(x(9))-dx)))+...a1.*ft1.*sin(x(9)).*(l5.*cos(x(9))+dy+l1.*sin(x(9)))+a1.*ft1.*cos(x(9)).*(-(-(l1.*cos(x(9))-...dx-l5.*sin(x(9)))))+a2.*ft2.*sin(x(9)).*(l5.*cos(x(9))+dy-l1.*sin(x(9)))-a2.*ft2.*cos(x(9)).*...(l2.*cos(x(9))+dx+l5.*sin(x(9)))-a3.*ft3.*sin(x(9)).*(-(-(l6.*cos(x(9))-dy-l1.*sin(x(9)))))+...a3.*ft3.*cos(x(9)).*(-(-(l1.*cos(x(9))-dx+l6.*sin(x(9)))))-a4.*ft4.*sin(x(9)).*(-(-(l6.*...cos(x(9))-dy+l2.*sin(x(9)))))-a4.*ft4.*cos(x(9)).*(l2.*cos(x(9))+dx-l6.*sin(x(9)))+...a5.*u.*(-x(5)).*sin(x(9)).*(l5.*cos(x(9))+dy+l1.*sin(x(9)))+a5.*u.*(-x(5)).*cos(x(9)).*...(-(-(l1.*cos(x(9))-dx-l5.*sin(x(9)))))+a6.*u.*(-x(6)).*sin(x(9)).*(l5.*cos(x(9))+dy-l1.*...sin(x(9)))-a6.*u.*(-x(6)).*cos(x(9)).*(l2.*cos(x(9))+dx+l5.*sin(x(9)))-a7.*u.*(-x(7)).*...sin(x(9)).*(-(-(l6.*cos(x(9))-dy-l1.*sin(x(9)))))+a7.*u.*(-x(7)).*cos(x(9)).*(-(-(l1.*...cos(x(9))-dx+l6.*sin(x(9)))))-a8.*u.*(-x(8)).*sin(x(9)).*(-(-(l6.*cos(x(9))-dy+l2.*...sin(x(9)))))-a8.*u.*(-x(8)).*cos(x(9)).*(l2.*cos(x(9))+dx-l6.*sin(x(9)))).^2+(-x(5).*(l5.*...cos(x(9))+dy+l1.*sin(x(9)))-x(6).*(l5.*cos(x(9))+dy-l1.*sin(x(9)))+x(7).*(-(-(l6.*cos(x(9))-...dy-l1.*sin(x(9)))))+x(8).*(-(-(l6.*cos(x(9))-dy+l2.*sin(x(9)))))-g.*dy-a1.*ft1.*...cos(x(9)).*h-a2.*ft2.*cos(x(9)).*h-a3.*ft3.*cos(x(9)).*h-a4.*ft4.*cos(x(9)).*h-a5.*u.*...(-x(5)).*cos(x(9)).*h-a6.*u.*(-x(6)).*cos(x(9)).*h-a7.*u.*(-x(7)).*cos(x(9)).*h-a8.*u.*...(-x(8)).*cos(x(9)).*h).^2+((-x(5)).*(-(-(l1.*cos(x(9))-dx-l5.*sin(x(9)))))+x(6).*...(l2.*cos(x(9))+dx+l5.*sin(x(9)))-x(7).*(-(-(l1.*cos(x(9))-dx+l6.*sin(x(9)))))+x(8).*...(l2.*cos(x(9))+dx-l6.*sin(x(9)))+g.*dx+a1.*ft1.*sin(x(9)).*h+a2.*ft2.*sin(x(9)).*h+...a3.*ft3.*sin(x(9)).*h+a4.*ft4.*sin(x(9)).*h+a5.*u.*(-x(5)).*sin(x(9)).*h+...a6.*u.*(-x(6)).*sin(x(9)).*h+a7.*u.*(-x(7)).*sin(x(9)).*h+a8.*u.*(-x(8)).*sin(x(9)).*h).^2;function[g,ceq]=mycon(x)globall1;globall2;globall3;globall4;globall5;globall6;globall7;globall8;globaldx;globaldy;globalx00;globaly0;globalm;globalh;globalr;globalg;globalt;globalft1;globalft2;globalft3;globalft4;globalu;globala1;globala2;globala3;globala4;globala5;globala6;globala7;globala8;g=[];ceq=[x(1).*cos((pi+atan(((0.5.*y0)-((l5+l7).*cos(x(9))-l3.*sin(x(9))+...dy))/((-0.5.*x00)-(l3.*cos(x(9))+(l5+l7).*sin(x(9))+dx)))))+x(2).*...cos((atan(((0.5.*y0)-((l5+l7).*cos(x(9))-l3.*sin(x(9))+dy))/((0.5.*x00)-...(l3.*cos(x(9))+(l5+l7).*sin(x(9))+dx)))))+x(3).*cos((pi+atan(((-0.5.*y0)-...(-((l6+l8).*cos(x(9))-l4.*sin(x(9))-dy)))/((-0.5.*x00)-(-(l4.*cos(x(9))+(l6+...l8).*sin(x(9))-dx))))))+x(4).*cos((2.*pi+atan(((-0.5.*y0)-(-((l6+l8).*cos(x(9))-...l4.*sin(x(9))-dy)))/((0.5.*x00)-(-(l4.*cos(x(9))+(l6+l8).*sin(x(9))-dx))))))+...a1.*ft1.*sin(x(9))+a2.*ft2.*sin(x(9))+a3.*ft3.*sin(x(9))+a4.*ft4.*sin(x(9))+...a5.*u.*(-x(5)).*sin(x(9))+a6.*u.*(-x(6)).*sin(x(9))+a7.*u.*(-x(7)).*sin(x(9))+...a8.*u.*(-x(8)).*sin(x(9));x(1).*sin((pi+atan(((0.5.*y0)-((l5+l7).*cos(x(9))-...l3.*sin(x(9))+dy))/((-0.5.*x00)-(l3.*cos(x(9))+(l5+l7).*sin(x(9))+...dx)))))+x(2).*sin((atan(((0.5.*y0)-((l5+l7).*cos(x(9))-l3.*sin(x(9))+dy))/((0.5.*...x00)-(l3.*cos(x(9))+(l5+l7).*sin(x(9))+dx)))))+x(3).*sin((pi+atan(((-0.5.*y0)-...(-((l6+l8).*cos(x(9))-l4.*sin(x(9))-dy)))/((-0.5.*x00)-(-(l4.*cos(x(9))+(l6+l8).*...sin(x(9))-dx))))))+x(4).*sin((2.*pi+atan(((-0.5.*y0)-(-((l6+l8).*cos(x(9))-l4.*...sin(x(9))-dy)))/((0.5.*x00)-(-(l4.*cos(x(9))+(l6+l8).*sin(x(9))-dx))))))+...a1.*ft1.*cos(x(9))+a2.*ft2.*cos(x(9))+a3*ft3.*cos(x(9))+a4.*ft4.*cos(x(9))+...a5.*u.*(-x(5)).*cos(x(9))+a6.*u.*(-x(6)).*cos(x(9))+.a7.*u.*(-x(7)).*cos(x(9))+a8.*u.*...(-x(8)).*cos(x(9));.x(5)+x(6)+x(7)+x(8)+g];clc;clearall;globalt;globall1;globall2;globall3;globall4;globall5;globall6;globall7;globall8;globaldx;globaldy;globalx00;globaly0;globalm;globalh;globalr;globalg;globalft1;globalft2;globalft3;globalft4;globalu;globala1;globala2;globala3;globala4;globala5;globala6;globala7;globala8;t=;l1=;l2=;l3=;l4=;l5=;l6=;l7=;l8=;dx=;dy=;x00=;y0=;m=;h=;r=;g=;ft1=t/(4*r);ft2=t/(4*r);ft3=t/(4*r);ft4=t/(4*r);u=;a1=;a2=;a3=;a4=;a5=;a6=;a7=;a8=;x0=[0;0;0;0;0;0;0;0;0];a=[];b=[];aeq=[];beq=[];vlb=[;;;;;;;;];vub=[;;;;;;;;];[x,fval]=fmincon(@fun9,x0,a,b,aeq,beq,vlb,vub,@mycon);在求解公式中输入已知参数运行代码可解得x1、x2、x3、x4即为f1、f2、f3、f4为求得的四条钢链3拉力值,其中,已知参数为:l1、l2、l3、l4、l5、l6、l7、l8、m、a0、delta_x(即为△x)、delta_y(即为△y);将求得的钢链3拉力值分别减去对应的钢链3预紧力初始值(即f1j=f1-f10、f2j=f2-f20、f3j=f3-f30、f4j=f4-f40)取得各个拉力调整数值,f1j、f2j、f3j、f4j是四条钢链3的拉力调整值,所述拉力调整值具有正负,正负符号分别代表需要将当前钢链3拉力减小或增大。步骤s5,判定目标函数是否小于设定值;若是,则执行步骤s7;若否,则执行步骤s6后返回至步骤s3;其中,所述设定值为经验值mo,可由多次试验总结,通常为20(n·m)2。步骤s6,根据拉力调整值调整钢链拉力;在调整过程中拉力传感器4会检测钢链3拉力,实时传送给监控主机11在显示屏上显示;参照监控主机11显示的数值不断调整拉力。步骤s7,开展噪声测试。第一实施例以四驱加速工况为例,在求解公式中输入以下参数:代入静力平衡表达式,可解得钢链3预紧力初始值,所述预紧力初始值大小为:f10=98.8n;f20=854.1n;f30=3.7757e+03n;f40=2.4608e+03n。在车辆10试验时,由于钢链3的弹性、轮胎摩擦特性、车辆10放置不对中等因素的影响,其加速度呈现震荡特性,拉力波动幅值为时变函数,可近似表示为:a=a0+△a·sin(ωt);式中,a0为指定工况的加速度大小;△a为拉力波动幅值,通常为a0的5%,ω为加速度波动角频率,ω=2πf,f=2~5hz。按照预紧力初始值将钢链3进行预紧,驱动力ft需要通过转鼓的力矩t和半径r计算,由加速度波动可得车辆轮胎驱动扭矩波动表达式:t=[(a0+△a·sin(ωt))·m+μ·(fn1+fn2+fn3+fn4)]·r代入各参数后可化简得到:t=1122+53·sin(2πft)其中,f=5hz代入单目标非线性优化算法的求解公式中,取得的拉力f1、f2、f3、f4的波动趋势见图11-14,图15为目标函数波动趋势图,从图11至图14可见,拉力f1、f2、f3、f4近似在预紧力初始值f10、f20、f30、f40上下波动,波动周期和加速度波动周期趋于一致。判断目标函数fval是否小于设定值m0;若目标函数小于设定值m0则开始噪声试验;若不满足,则通过拉紧力调整装置6动态调整钢链3的拉力,拉力传感器4测量的一组新的拉力值将作为下一轮的迭代输入到单目标非线性优化算法进行求解,优化计算得到下一组拉力值,直至拉力调整满足目标函数要求。如图16-图20为拉力调整过程中目标函数fval不小于设定值的情况。目标函数fval在某些区域不小于设定值,此时通过改变拉力调整值,重新进行单目标非线性优化算法求解,获取钢链3的拉力新的调整值并调整钢链3拉力,直至目标函数fval小于设定值后再开展噪声测试。在测试过程中监控主机11可以实时计算并在屏幕上显示指定工况下钢链3的拉力调整值和钢链3拉力。综上所述,本发明有效克服了现有技术中的种种缺点而具高度产业利用价值。上述实施例仅例示性说明本发明的原理及其功效,而非用于限制本发明。任何熟悉此技术的人士皆可在不违背本发明的精神及范畴下,对上述实施例进行修饰或改变。因此,举凡所属
技术领域:
中具有通常知识者在未脱离本发明所揭示的精神与技术思想下所完成的一切等效修饰或改变,仍应由本发明的权利要求所涵盖。当前第1页12