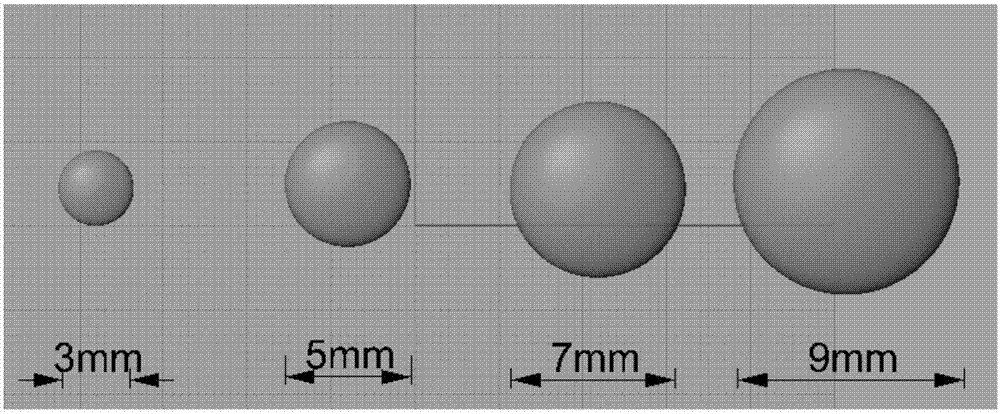
本发明属于岩土试验领域,涉及三维定孔隙人工多孔石制备方法。
背景技术:
多孔介质指由岩石类固体骨架和骨架内部大量孔隙组成的多相混合介质,其广泛存在于自然界,岩石类多孔介质则主要是混凝土、砖,以及各类岩石、岩体等岩石类材料。由于多孔介质内存在大量形态复杂、分布各异的连通、非连通孔隙空间,使得无论天然还是人造多孔介质均难以对多孔介质的内部结构进行准确的数学描述。然而多孔介质的孔洞形态、孔隙度、孔隙比面,以及孔洞的连通、非连通等孔隙结构特征极大影响着多孔介质的渗透、传热、压缩、强度等物理特性。物理特性通常采用室内试验和数值模拟进行研究,但相比极度依赖模拟参数和边界条件的数值分析方法,室内试验具有高度的可靠性和准确性。然而由于天然试验样本的孔隙结构差异,以及取样过程的孔隙结构损伤,同组试验中试样间孔隙结构不统一,试验试样的孔隙特征难以准确定量描述和表征,因此有必要研发出能够同时满足3维孔隙形态、孔隙度、孔隙比面的定孔隙岩石类多孔介质试样制备方法,进行定孔隙多孔介质室内试验,分析孔隙特征对岩石类多孔介质的渗透、传热、压缩、强度等物理特性影响。该方法对岩石类多孔介质的渗透、传热、压缩、强度等物理特性研究具有重要意义。
·当前人工多孔介质试样制备,要么基于表征单元rev将多孔介质等效为连续介质,直接对岩石、混凝土取芯、制备试验试样,忽略内部孔隙结构影响;要么对制备好多孔介质试样,进行高精度、高成本、高人工的ct扫描,并采用3d重构多孔介质内部3维孔隙结构形态;要么对人工类岩石材料填充一定尺寸、体积的气泡,制备类岩石多孔介质试样。但以上方法均无法生成内部孔隙结构特征相同的试样组,且要么难以准确定量内部孔隙结构,要么孔隙形态单一,要么制备成本高昂。无法制备同时满足给定三维孔隙形态、孔隙度、孔隙比面的定孔隙岩石类多孔介质试样组。
1.难以定量描述内部孔隙结构特征
通常情况下,多孔介质通过表征体单元rev直接将多孔介质等效为连续介质,无法定量描述孔隙形态、孔隙分布、孔隙度,以及孔隙比面等重要孔隙参数;而对多孔介质试样的ct扫描,再3维重构多孔介质内部孔隙结构的方法,由于ct扫描成本和后续处理的人力成本使得实际常规试验中难以推广;气泡填充的岩石类人工多孔介质,气泡尺寸差异较大,气泡形态多变,也难以直接定量描述内部孔隙结构特征。
2.试验中试样孔隙结构差异明显
由于试验中试样的本身孔隙结构差异,以及取样过程的孔隙结构损伤,使得同组试验中试样与试样间的孔隙结构差异明显,即便准确获取了所有试样的内部孔隙结构,但孔隙结构的明显差异,增加了试验结果分析的难度和准确性。
3.试样制备和内部孔隙结构生成成本高
试验中岩石类多孔介质直接取样需对试样进行取芯、打磨成型等工作,单个试样的制样成本也在100人民币左右;与此同时,试样的ct扫描费用,3d内部孔隙结构重建费用和人工成本高昂。
4.无法制备同时满足给定3维孔隙形态、孔隙度、孔隙比面的定孔隙岩石类多孔介质试样
当前人工多孔介质制备采用加入气泡的方法,由于气泡形态较为单一,尺寸差异较大,其孔隙形态、孔隙度、孔隙比面难以控制,难以生成三维定孔隙人工多孔石,因此迫切需要寻找新的三维定孔隙人工多孔石的制备方法。
技术实现要素:
有鉴于此,本发明的目的在于提供三维定孔隙人工多孔石的制备方法。
为实现上述发明目的,本发明提供如下技术方案:
1、三维定孔隙人工多孔石制备方法,所述方法包括以下步骤:
s1:制备孔洞模板;
s2:制备孔洞柔性模具;
s3:制备三维琼脂孔洞模型;
s4:制备琼脂多孔石;
s5:多孔石循环水煮脱脂。
优选的,s1中所述孔洞的形态为规则孔洞、任意孔洞以及天然孔洞中的任意一种。
优选的,s1中所述规则孔洞的形态参数按照以下方法获得:根据规则模型的尺寸通过理论计算得到规则孔洞的形态参数;所述任意孔洞的形态参数按照以下方法获得:通过3d扫描或者计算机进行三维建模获得任意孔洞的形态参数;所述天然孔洞的形态参数按照以下方法获得:向天然孔洞内注入树脂或者将包裹天然孔洞的岩石进行酸性溶解,得到天然孔洞的硬化树脂模版,再采用3d扫描获得天然孔洞的形态参数。
优选的,s1中所述制备孔洞模板的制备方法为:s1中所述规则孔洞的模板包括规则的钢制或者玻璃质制品的孔洞模板;所述的任意孔洞以及天然孔洞的孔洞模板制备方法为:根据孔洞的形态参数利用3d打印方法制备得到孔洞模板。
优选的,所述孔洞柔性模具的制备方法包括如下步骤:
1)按照100:1~1.5的质量比将柔性硅胶与水混合配制成柔性无气硅胶溶液,并将其倒入模具制备盒中;
2)对密度大于硅胶溶液的模版,以足够的模版间距,将孔洞模版逐一规则放入硅胶溶液中,模版将最终沉入模具制备盒底部,与模具制备盒底部接触;对密度与硅胶溶液相近的孔洞模版,将孔洞模版以一定间距用胶水固定在模具制备盒底部;
3)待柔性硅胶凝固成型,将其从模具制备盒中取出,翻转柔性硅胶模具,将孔洞模版由顶部小孔抠出,即可得到孔洞柔性模具。
优选的,所述琼脂模型的制备方法包括如下步骤:
1)配制琼脂浆液:首先将固态琼脂放入常温水中浸泡吸水60~90min,洗净琼脂,然后进行蒸煮至琼脂完全液化形成琼脂浆液,过0.5mm的细筛;
2)琼脂注浆:将琼脂浆液通过x型排气注浆针孔从孔洞柔性模具顶部的小孔向柔性模具进行缓慢匀速的针孔注浆,直至琼脂浆液从顶部小孔溢出后停止,形成琼脂注浆后的柔性模具;
3)琼脂模型排气:将琼脂注浆后的柔性模具密闭包裹后放入高频振动器中,放入恒温箱进行恒温高频振动,所述恒温的温度为90~100℃,所述高频振动的频率大于300hz;所述振动时间大于30min;
4)三维琼脂孔洞模型:将高频振动后的琼脂柔性模具取出,降温静置直至琼脂硬化,将硬化后的三维琼脂孔洞模型从模具内直接挤出得到三维琼脂孔洞模型。
优选的,所述琼脂浆液中还可以添加粒径小于0.5mm的重晶石粉末。
优选的,所述琼脂人工石浇筑成型的方法按照如下步骤进行:
1)首先根据实际需要琼脂人工多孔石的孔洞形态、孔洞尺寸分布,以及总孔洞含量,确定多孔石的人工石浆液材料,以及浆液配比;
2)然后将琼脂模型与人工石浆液均匀混合并浇筑成型,生成内部孔洞包裹琼脂的琼脂多孔石。
优选的,所述多孔石循环水煮脱脂的具体方法为:将琼脂多孔石放入定量的沸水中进行循环高温水煮,并定量更换水溶液,直至更换出来的水溶液降温后无明显的胶体产生后停止高温水煮,将多孔石取出即可得到人工多孔石。
本发明的有益效果在于:
1、基于三维孔洞形态和琼脂物理特性,开发本发明提供了可以定量描述孔隙内部结构特征的三维定孔隙人工多孔石的制备方法,能够制备得到孔隙形态、孔隙度、孔隙比面确定的岩石类多孔介质;
2、本发明公开了孔隙结构差异内微小的三维定孔隙人工多孔石制备方法,减小试样间的内孔隙结构差异,减小试验偏差,提高试验精度。
3、本发明公开了的三维定孔隙人工多孔石制备方法具有低成本、低能耗、低人工的有点,能够促进内孔隙影响下的岩石类多孔介质物理特性的研究。
4、本发明公开了的三维定孔隙人工多孔石制备方法能够确定孔隙形态、孔隙度、孔隙比面,从而解决当前三维定孔隙人工多孔石无法生成的问题。
附图说明
为了使本发明的目的、技术方案和有益效果更加清楚,本发明提供如下附图进行说明:
图1为孔洞球形玻璃孔洞模版图;
图2为柔性硅胶模具制作示意图;
图3为高温琼脂浆液配置示意图;
图4为柔性模具针孔琼脂注浆示意图;
图5为柔性模具排气消气示意图;
图6为不同形态孔洞模版生成示意图;
图7为人工多孔介质石定孔隙度、孔隙形态、级配示意图;
图8为琼脂人工多孔石制备示意图;
图9为人工多孔石脱脂示意图。
具体实施方式
下面将对本发明的优选实施例进行详细的描述。实施例中未注明具体条件的实验方法,通常按照常规条件或按照制造厂商所建议的条件。
下面将结合附图,对本发明的优选实施例进行详细的描述。
实施例1
制备具有规则孔洞形态的三维定孔隙人工多孔石:
(1)直接选用常见易得的玻璃质制品作为规则的玻璃孔洞模板,如图1所示;
(2)制备孔洞柔性模具:首先按照100:1的质量比将柔性硅胶与水混合配制成柔性无气硅胶溶液,并将其倒入模具制备盒中并没过玻璃孔洞模板2mm以上;再将玻璃孔洞模板逐一按照等间距放入硅胶溶液中,使玻璃孔洞模板沉入硅胶溶液中并与硅胶溶液和模型盒底部接触,产生柔性模具顶部的注浆小孔;待硅胶凝固成型后将柔性硅胶模具从模具制备盒中取出,玻璃球与模具制备盒接触形成小孔,再挤出玻璃孔洞模板后即可得到孔洞柔性模具,如图2所示;
(3)制备琼脂模型:配制琼脂浆液:首先将固态琼脂放入常温水中浸泡吸水60~90min,洗净琼脂,然后进行蒸煮至琼脂完全液化形成琼脂浆液,过0.5mm的细筛,为了增加孔洞模型的密度可以添加粒径小于0.5mm的少量重晶石粉末,如图3所示;其次将琼脂浆液通过x型排气注浆针孔从孔洞柔性模具顶部的小孔向柔性模具进行缓慢匀速的针孔注浆,如图4所示,直至琼脂浆液从顶部小孔溢出后停止,形成琼脂注浆后的柔性模具;考虑浆液的干缩和模具内的空气残留,整个针孔注浆完成后,需再注入约孔洞1/10体积的琼脂浆液;然后将琼脂注浆后的柔性模具放置在振动台上进行振动,以大于300hz的频率振动时间超过30min;提高琼脂浆液的流动性,进而将注浆后柔性模具内的残余空气排出,随后将柔性模具放入密闭缸中,通过压力罐施加400kpa以上的高围压,高围压作用下,琼脂浆液中的微气泡将自动消失,从而最终提高了琼脂多孔石生成质量。最后,高压24h,待琼脂凝固成型,如图5所示;最后将琼脂柔性模具取出,降温静置直至琼脂硬化,将硬化后的三维琼脂孔洞模型从模具内直接挤出即可得到琼脂模型;
(4)制备琼脂多孔石:首先根据实际需要琼脂人工多孔石的孔洞形态、孔洞尺寸分布,以及总孔洞含量,确定多孔石的人工石浆液材料,以及浆液配比;然后将琼脂模型与人工石浆液均匀混合并浇筑成型,生成内部孔洞包裹琼脂的琼脂多孔石;
(5)多孔石循环水煮脱脂:将琼脂多孔石放入定量的沸水中进行循环高温水煮,并定量更换水溶液,直至更换出来的水溶液降温后无明显的胶体产生后停止高温水煮,将多孔石取出即可得到具有规则孔洞形态的三维定孔隙人工多孔石。
(6)利用上述步骤(5)中得到的循环高温水煮时间以及更换水溶液的次数可以进行批量的具有规则孔洞形态的三维定孔隙人工多孔石的制备。
实施例2
制备具有任意孔洞形态的三维定孔隙人工多孔石:
(1)通过3d扫描或者计算机进行三维建模获得任意孔洞的形态参数,将得到的任意孔洞的形态参数利用3d打印等方法制备得到孔洞模板;
(2)制备孔洞柔性模具:首先按照100:1.3的质量比将柔性硅胶与水混合配制成柔性无气硅胶溶液,并将其倒入模具制备盒中;其次对于密度大于硅胶溶液的模版,以足够的模版间距,将孔洞模版逐一规则放入硅胶溶液中,模版将最终沉入模具制备盒底部,和底部模具制备盒接触。对于对密度约等于硅胶人溶液的孔洞模版,可以将孔洞模版以一定间距用胶水固定在模具制备盒底部;最后待柔性硅胶凝固成型,将其从模具制备盒中取出,翻转柔性硅胶模具,将孔洞模版由顶部小孔抠出,即可得到孔洞柔性模具;
(3)制备琼脂模型:首先配制琼脂浆液:首先将固态琼脂放入常温水中浸泡吸水60~90min,洗净琼脂,然后进行蒸煮至琼脂完全液化形成琼脂浆液,过0.5mm的细筛,为了增加孔洞模型的密度可以添加粒径小于0.5mm的少量重晶石粉末;其次将琼脂浆液通过x型排气注浆针孔从孔洞柔性模具顶部的小孔向柔性模具进行缓慢匀速的针孔注浆,直至琼脂浆液从顶部小孔溢出后停止,随后将琼脂注浆后的柔性模具密闭包裹后放入高频振动器中,并统一加入恒温箱进行恒温高频振动排气,所述高温为保证琼脂液化温度90~100℃,以大于300hz的频率振动时间超过30min;随后将柔性模具放入密闭缸中,通过压力罐施加400kpa以上的高围压,高围压作用下,琼脂浆液中的微气泡将自动消失,从而最终提高了琼脂多孔石生成质量。最后,高压24h,待琼脂凝固成型;最后将琼脂柔性模具取出,降温静置直至琼脂硬化,将硬化后的三维琼脂孔洞模型从模具内直接挤出即可得到琼脂模型;
(4)制备琼脂多孔石:首先根据实际需要琼脂人工多孔石的孔洞形态、孔洞尺寸分布,以及总孔洞含量,确定多孔石的人工石浆液材料,以及浆液配比;然后将琼脂模型与人工石浆液均匀混合并浇筑成型,生成内部孔洞包裹琼脂的琼脂多孔石;
(5)多孔石循环水煮脱脂:将琼脂多孔石放入定量的沸水中进行循环高温水煮,并定量更换水溶液,直至更换出来的水溶液降温后无明显的胶体产生后停止高温水煮,将多孔石取出即可得到制备具有任意孔洞形态的三维定孔隙人工多孔石;
(6)利用上述步骤(5)中得到的循环高温水煮时间以及更换水溶液的次数可以进行批量的制备具有任意孔洞形态的三维定孔隙人工多孔石的制备。
实施例3
制备具有天然孔洞形态的三维定孔隙人工多孔石:
(1)选择具有天然孔洞出露的的岩石,从出露小孔注入环氧树脂,待树脂硬化后,将注入树脂的岩石放入盐酸溶液中,通过盐酸溶液腐蚀消融多余的岩石,得到不与酸性溶液反映的树脂孔洞模型;
(2)制备孔洞柔性模具:按照100:1.5的质量比将柔性硅胶与水混合配制成柔性无气硅胶溶液,并将其倒入模具制备盒中;其次对于密度大于硅胶溶液的模版,以足够的模版间距,将孔洞模版逐一规则放入硅胶溶液中,模版将最终沉入模具制备盒底部,和底部模具制备盒接触。对于对密度约等于硅胶人溶液的孔洞模版,可以将孔洞模版以一定间距用胶水固定在模具制备盒底部;最后待柔性硅胶凝固成型,将其从模具制备盒中取出,翻转柔性硅胶模具,将孔洞模版由顶部小孔抠出,即可得到孔洞柔性模具;
(3)制备琼脂模型:首先将固态琼脂放入常温水中浸泡吸水60~90min,洗净琼脂,然后进行蒸煮至琼脂完全液化形成琼脂浆液,过0.5mm的细筛,为了增加孔洞模型的密度可以添加粒径小于0.5mm的少量重晶石粉末;其次将琼脂浆液通过x型排气注浆针孔从孔洞柔性模具顶部的小孔向柔性模具进行缓慢匀速的针孔注浆,直至琼脂浆液从顶部小孔溢出后停止,随后将琼脂注浆后的柔性模具密闭包裹后放入高频振动器中,并统一加入恒温箱进行恒温高频振动排气,所述高温为保证琼脂液化温度90~100℃,以大于300hz的频率振动时间超过30min;随后将柔性模具放入密闭缸中,通过压力罐施加400kpa以上的高围压,高围压作用下,琼脂浆液中的微气泡将自动消失,从而最终提高了琼脂多孔石生成质量。最后,高压24h,待琼脂凝固成型;最后将琼脂柔性模具取出,降温静置直至琼脂硬化,将硬化后的三维琼脂孔洞模型从模具内直接挤出即可得到琼脂模型;
(4)制备琼脂多孔石:首先根据实际需要琼脂人工多孔石的孔洞形态、孔洞尺寸分布,以及总孔洞含量,确定多孔石的人工石浆液材料,以及浆液配比;然后将琼脂模型与人工石浆液均匀混合并浇筑成型,生成内部孔洞包裹琼脂的琼脂多孔石;
(5)多孔石循环水煮脱脂:将琼脂多孔石放入定量的沸水中进行循环高温水煮,并定量更换水溶液,直至更换出来的水溶液降温后无明显的胶体产生后停止高温水煮,将多孔石取出即可得到具有天然孔洞形态的三维定孔隙人工多孔石;
(6)利用上述步骤(5)中得到的循环高温水煮时间以及更换水溶液的次数可以进行批量的具有天然孔洞形态的三维定孔隙人工多孔石的制备。
如图6为规则孔洞形态、任意孔洞形以及天然孔洞形态的模版生成示意图。
如图7所示,制备孔隙度60%的50mm×100mm的圆柱形岩石多孔介质,其孔洞为粒径3mm、5mm、7mm、9mm的球形颗粒,3mm、5mm、7mm、9mm粒径孔洞的体积百分比如表所示,分别为39.01%、32.83%、20.79%、7.37%。由试样的体积、孔隙度、孔洞粒径百分比,可以计算试样所需各个粒径琼脂球形颗粒的个数分别为715、130、30、5,进而从批量生产的球形琼脂颗粒选择相应数量颗粒。
如图8所示,将配置好的人工石浆液与选择好的琼脂球体孔洞均匀混合,然后倒入试样制备模具中,完成岩石类多孔介质的浇筑,浇筑完成后的岩石类多孔介质比面为0.807mm。
如图9所示,将制备好的琼脂人工多孔石试样放入铁质容器中,加入定量水溶液过量的水溶液将从排水阀自动排出。由于琼脂高温易溶于水,高温水煮一定时间后孔洞内的琼脂将逐渐转移到水溶液中,为此可以取出一定量的水煮后水溶液,煮干水溶液监测琼脂含量,从而确定出,需经过多少次的高温水煮可得到不含琼脂的岩石类人工多孔介质。
最后说明的是,以上优选实施例仅用以说明本发明的技术方案而非限制,尽管通过上述优选实施例已经对本发明进行了详细的描述,但本领域技术人员应当理解,可以在形式上和细节上对其作出各种各样的改变,而不偏离本发明权利要求书所限定的范围。