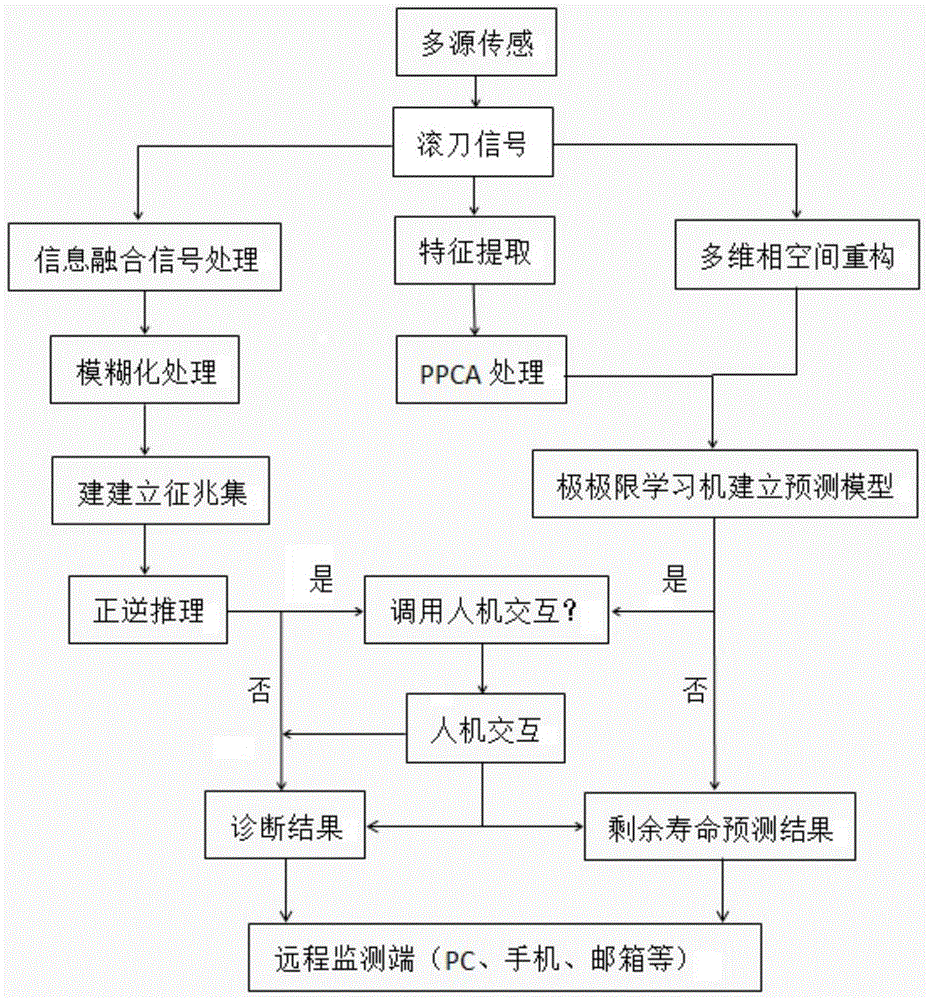
本发明属于刀具监测
技术领域:
,具体涉及一种基于多源信息融合的刀具状态监测及寿命预测系统。
背景技术:
:目前全断面隧道掘进机在施工过程中对刀盘刀具的检查,首先必须停机,无法在掘进过程中观察刀具磨损情况,严重影响了工程进度。刀盘刀具的区域是一个未支护区域,且土仓为密闭的高压环境,对检修人员自身素质要求较高,换刀过程费时费力,且容易出现安全事故。对设备本身而言,刀具损坏后才能进行维修或更换,掘进过程中施工人员无法知道滚刀的工作状态,只有在刀具出现严重损坏对掘进进度造成较大影响时,进行检刀、换刀工作,对施工效率和施工经济性造成影响。目前国内外相关企业已开展了滚刀监测研究,但仍处于起步阶段,但对信息的利用率较低,无法提前预知滚刀的剩余寿命。技术实现要素:针对上述现有技术中描述的不足,本发明提供一种基于多源信息的滚刀监控系统,通过对滚刀相关信号的分析处理,知晓滚刀的工作状态,判断是否出现故障,并预测滚刀剩余寿命,人性化的辅助盾构司机判断是否更换刀具。为解决上述技术问题,本发明所采用的技术方案如下:一种基于多源信息融合的刀具状态监测及寿命预测系统,包括信息采集模块、信号预处理模块、状态监测模块、寿命预测模块和远程监测模块;所述信息采集模块采集滚刀的参数信息,通过信号预处理模块预处理后发送至状态监测模块和/或寿命预测模块,状态监测模块接收滚刀参数信息并处理后输出滚刀状态,寿命预测模块接收滚刀参数并处理后输出滚刀的剩余寿命,状态监测模块和寿命预测模块的输出结果直接现场查看并输送至远程监测模块。具体地,状态监测模块、寿命预测模块的输出结果既可以直接现场查看,还可通过无线通讯模块发送到远程端,供远程相关工程管理人员可通过手机、远程pc端等查看。所述滚刀参数信息,包括工作参数和工艺参数;所述工作参数包括转速、滚刀力、力矩、刀轴振动;转速,通过转速传感器获得,譬如霍尔传感器、编码器或角度传感器;滚刀力和力矩,通过六维力传感器获得;刀轴振动,通过加速度传感器(如重力传感器)或速度传感器获得。所述工艺参数包括刀圈外形轮廓、温度、刀圈磨损量;刀圈外形轮廓,通过测距传感器采集到得到;温度,通过温度传感器获得;刀圈磨损量,通过电涡流传感器获得。所述信号预处理模块对对转速、滚刀力、力矩、刀轴振动、刀圈外形轮廓、温度、刀圈磨损量分别进行信号放大和滤波等预处理。所述状态监测模块,对获得的参数信息进行处理得到滚刀的工作状态,状态监测模块的处理步骤为:s1,提取预处理后的工作参数信息的信号关键特征;提取适用的方法为支持向量机、深度神经网络算法、bp神经网络算法、小波分析算法、主成分分析算法等中的一种或几种的结合。s2,结合信号关键特征和滚刀工艺参数建立征兆集。s2.1,对滚刀工艺参数信息中的温度以及工作参数信息中的力、力矩、刀轴振动幅值计算征兆隶属度μ(x),征兆隶属度μ(x)通式为:参数升高时:参数降低时:其中,参数允许的取值区间是[min,max],正常值落于区间[a,b],且根据征兆隶属度μ(x)的值为滚刀工作状态的判断提供依据。s2.2,根据步骤s2.1得到的征兆隶属度并结合获得的参数信息建立征兆集。所述征兆集,包括参数类型、参数名称和参数属性;所述参数类型,包括工作状态、频域特征、时域特征、相关工艺参数和基本监测信息。所述工作状态包括四个参数,分别为转速状态、负荷状态、振幅与转速的关系、振幅与负荷的关系;所述转速状态的参数属性,包括稳速、变速、速度下降、停转;所述负荷状态的参数属性,包括不变、上升、下降;所述振幅与转速的关系的参数属性,包括随转速变化明显、随转速变化不明显;所述振幅与负荷的关系的参数属性,包括随负荷变化明显、随负荷变化不明显。所述频域特征包括两个参数,分别为幅值和幅值变化;所述幅值的参数属性,包括较大;所述幅值变化的参数属性,包括基本不变、缓慢上升、缓慢下降、突然上升、突然下降、周期性变化、不规则变化。所述时域特征包括两个参数,分别为幅值变化趋势和波形状态;所述幅值变化趋势的参数属性,包括基本不变、缓慢上升、缓慢下降、突然上升、突然下降、周期性变化、不规则变化;所述波形变化的参数属性,包括简谐波形、非周期波形、畸形。所述相关工艺参数包括三个参数,分别为温度、磨损量、管道轮廓;所述温度的参数属性,包括过高、过低;所述磨损量的参数属性,包括过高、偏磨;所述管道轮廓的参数属性,包括正常、变形。所述基本监测信息的参数为滚刀通道信息,滚刀通道信息的参数属性为滚刀编号。s3,将获取的征兆集与滚刀历史数据的知识库、滚刀相关参数阈值的知识库进行对比。s4,将步骤s3得到的结果通过正向推理得到滚刀故障假设集。s5,逆向推理验证故障假设集,若验证正确则将推理结果进行模糊化处理,将模糊量词与数值区间一一对应。所述模糊量词包括肯定、很可能、可能、有点可能、可能性小、不可能;与模糊量词一一对应的数值区间为1、0.8、0.6、0.4、0.2、0。s6,选择阈值报警或人机交互方式在工控机上显示参数信息和推理结果,根据工控机的显示结果判断滚刀的工作状态,从而判断是否进行换刀操作。所述寿命预测模块,对接收到的参数信息进行处理得到滚刀的剩余寿命;所接收到的参数信息包括滚刀力、力矩、温度、磨损量和刀轴振动。寿命预测模块的处理步骤为:s1,对得到的预处理后的参数信息采用多变量相空间重构算法进行相空间重构,作为模型输入端数据:x(t)=(x1(t),x2(t),…,xi(t),…,xk(t));其中:xi(t)表示滚刀第i个参数指标的不同类型信息值,mi为第i个变量的嵌入维数,τi为第i个变量的延迟时间,k为参数指标的个数。s2,获取滚刀退化指标ab,并将滚刀退化指标作为模型输出端数据。s2.1,构建特征空间向量矩阵x。s2.1.1,获得各参数指标波形的时域指标。所述时域指标包括最大值、最小值、平均幅值、峰值、均方根值斜度和峭度。s2.1.2,获取各参数指标的频域指标。所述频域指标,包括振动值的特征频率幅值。s2.1.3,获得的时域指标和频域指标构成特征空间向量矩阵x:其中,特征空间向量矩阵x的行表示同一时刻不同参数指标组成的特征向量;特征空间向量矩阵x的列表示不同时刻的指标组成的特征向量;n为构成特征空间向量矩阵x的参数指标个数,且n≤k。s2.2,将特征空间向量矩阵x标准化并得到协方差矩阵s。s2.3,根据协方差矩阵s得到特征值λ1,λ2,…,λn以及与特征值对应的特征向量v1,v2,…,vn。s2.4,把特征值由大到小排序得到对角矩阵a:s2.5,根据特征向量计算特征空间向量矩阵x的主成分矩阵y:y=xv;v=[v1,v2,…,vn]。s2.6,将主成分矩阵y的第一主成分作为滚刀退化指标ab。s3,结合步骤s1和步骤s2以极限学习机算法构建寿命预测模型:β=[βi1,βi2,…βik]t;ω=[ωi1,ωi2,…ωin]t;式中:β表示第i个隐层节点于第k个输出节点的权重;ω表示第i个隐层节点与第n个输入节点的权重;bi表示第i个隐层节点上的偏置。s4,在线实时采集滚刀工作状态数据信息,更新模型输入端数据和模型输出端数据,并更新修正模型,最终将寿命预测模型的输出值与实际值对比得到寿命预测模型的精度与评价结果。一种滚刀信息监测装置,包括滚刀刀座,在滚刀刀座的滑块端盖内侧安有激光测距传感器,在滚刀刀座的滚刀外端面上安有温度传感器和霍尔传感器,在滚刀刀座的滚刀的外侧壁安有电涡流传感器;在滚刀刀座的c形块上安有六维力传感器和加速度传感器;在滚刀刀座的驱动滑块上安有电池,在驱动滑块上螺杆上安有无线信号发射器;激光测距传感器、温度传感器、霍尔传感器、六维力传感器、加速度传感器、电涡流传感器均通过无线信号发射器发送至盾体内的信号接收器,信号接收器经信号线传输到数据预处理模块,数据预处理模块传输至工控机内,工控机可直接显示处理结果并将处理后的结果发送到远程端进行查看,远程相关管理人员可通过自己的手机、pc端等直接进行查看。本发明的有益效果:本发明通过滚刀监测装置实时监测滚刀受力、磨损量、转速、外形等关键参数实现其可视化管理,通过对滚刀相关信号的分析处理,实时监测滚刀状态并预测滚刀剩余寿命,并与远程端通讯供相关工程管理人员可通过手机、远程pc端等查看,人性化的辅助判断是否更换刀具。附图说明为了更清楚地说明本发明实施例或现有技术中的技术方案,下面将对实施例或现有技术描述中所需要使用的附图作简单地介绍,显而易见地,下面描述中的附图仅仅是本发明的一些实施例,对于本领域普通技术人员来讲,在不付出创造性劳动的前提下,还可以根据这些附图获得其他的附图。图1为实施例1的系统流程图。图2为实施例1寿命预测模型中极限学习网络结构图。图3为实施例2的结构示意图。图4为实施例2各传感器与滚刀刀座的装配示意图。具体实施方式下面将结合本发明实施例中的附图,对本发明实施例中的技术方案进行清楚、完整地描述,显然,所描述的实施例仅仅是本发明一部分实施例,而不是全部的实施例。基于本发明中的实施例,本领域普通技术人员在没有付出创造性劳动前提下所获得的所有其他实施例,都属于本发明保护的范围。实施例1:一种基于多源信息融合的刀具状态监测及寿命预测系统,包括信息采集模块、信号预处理模块、状态监测模块、寿命预测模块和远程监测模块;所述信息采集模块采集滚刀的参数信息,通过信号预处理模块预处理后发送至状态监测模块和/或寿命预测模块,状态监测模块接收滚刀参数信息并处理后输出滚刀状态,寿命预测模块接收滚刀参数并处理后输出滚刀的剩余寿命,状态监测模块、寿命预测模块的输出结果可在现场直接查看,还可通过无线通讯模块发送到远程监测模块,供远程相关工程管理人员可通过手机、远程pc端等查看。具体地,所述滚刀参数信息,包括工作参数和工艺参数;所述工作参数包括转速、滚刀力、力矩、刀轴振动;转速,通过转速传感器获得,譬如霍尔传感器、编码器或角度传感器;滚刀力和力矩,通过六维力传感器获得;刀轴振动,通过加速度传感器(如重力传感器)或速度传感器获得。所述工艺参数包括刀圈外形轮廓、温度、刀圈磨损量;刀圈外形轮廓,通过测距传感器采集到得到;温度,通过温度传感器获得;刀圈磨损量,通过电涡流传感器获得。在进行数据分析前,所述信号预处理模块对对转速、滚刀力、力矩、刀轴振动、刀圈外形轮廓、温度、刀圈磨损量分别进行信号放大和滤波等预处理。当进行状态监测时,所述状态监测模块,对获得的参数信息进行处理得到滚刀的工作状态,状态监测模块的处理步骤为,如图1所示:s1,提取工作参数信息的信号关键特征;提取适用的方法为支持向量机、深度神经网络算法、bp神经网络算法、小波分析算法、主成分分析算法中的一种。s2,结合信号关键特征和滚刀工艺参数建立征兆集。s2.1,对滚刀工艺参数信息中的温度以及工作参数信息中的力、力矩、刀轴振动幅值计算征兆隶属度μ(x),征兆隶属度μ(x)通式为:参数升高时:参数降低时:其中,参数允许的取值区间是[min,max],正常值落于区间[a,b],且根据征兆隶属度μ(x)的值为滚刀工作状态的判断提供依据。s2.2,根据步骤s2.1得到的征兆隶属度并结合获得的参数信息建立征兆集。所述征兆集,包括参数类型、参数名称和参数属性;所述参数类型,包括工作状态、频域特征、时域特征、相关工艺参数和基本监测信息。所述工作状态包括四个参数,分别为转速状态、负荷状态、振幅与转速的关系、振幅与负荷的关系;所述转速状态的参数属性,包括稳速、变速、速度下降、停转;所述负荷状态的参数属性,包括不变、上升、下降;所述振幅与转速的关系的参数属性,包括随转速变化明显、随转速变化不明显;所述振幅与负荷的关系的参数属性,包括随负荷变化明显、随负荷变化不明显。所述频域特征包括两个参数,分别为幅值和幅值变化;所述幅值的参数属性,包括较大;所述幅值变化的参数属性,包括基本不变、缓慢上升、缓慢下降、突然上升、突然下降、周期性变化、不规则变化。所述时域特征包括两个参数,分别为幅值变化趋势和波形状态;所述幅值变化趋势的参数属性,包括基本不变、缓慢上升、缓慢下降、突然上升、突然下降、周期性变化、不规则变化;所述波形变化的参数属性,包括简谐波形、非周期波形、畸形。所述相关工艺参数包括三个参数,分别为温度、磨损量、管道轮廓;所述温度的参数属性,包括过高、过低;所述磨损量的参数属性,包括过高、偏磨;所述管道轮廓的参数属性,包括正常、变形。所述基本监测信息的参数为滚刀通道信息,滚刀通道信息的参数属性为滚刀编号。具体如表1所示。表1s3,将获取的征兆集与滚刀历史数据的知识库、滚刀相关参数阈值的知识库进行对比。s4,将步骤s3得到的结果通过正向推理得到滚刀故障假设集。s5,逆向推理验证故障假设集,若验证正确则将推理结果进行模糊化处理,将模糊量词与数值区间一一对应。所述模糊量词包括肯定、很可能、可能、有点可能、可能性小、不可能;与模糊量词一一对应的数值区间为1、0.8、0.6、0.4、0.2、0。模糊对应关系如表2所示。表2模糊量词肯定很可能可能有点可能可能性小不可能数值区间10.80.60.40.20s6,选择阈值报警或人机交互方式在工控机上显示参数信息和推理结果,根据工控机的显示结果判断滚刀的工作状态,从而判断是否进行换刀操作。而进行寿命预测时,所述寿命预测模块,对接收到的参数信息进行处理得到滚刀的剩余寿命;所接收到的参数信息包括滚刀力、力矩、温度、磨损量和刀轴振动。寿命预测模块的处理步骤为,如图1所示:s1,对得到的参数信息采用多变量相空间重构算法进行相空间重构,作为模型输入端数据:x(t)=(x1(t),x2(t),…,xi(t),…,xk(t));其中:xi(t)表示滚刀第i个参数指标的不同类型信息值,mi为第i个变量的嵌入维数,τi为第i个变量的延迟时间,k为参数指标的个数。s2,获取滚刀退化指标ab,并将滚刀退化指标作为模型输出端数据。s2.1,构建特征空间向量矩阵x。s2.1.1,获得各参数指标波形的时域指标。所述时域指标包括最大值、最小值、平均幅值、峰值、均方根值斜度和峭度。s2.1.2,获取各参数指标的频域指标。所述频域指标,包括振动值的特征频率幅值。s2.1.3,获得的时域指标和频域指标构成特征空间向量矩阵x:其中,特征空间向量矩阵x的行表示同一时刻不同参数指标组成的特征向量;特征空间向量矩阵x的列表示不同时刻的指标组成的特征向量;n为构成特征空间向量矩阵x的参数指标个数,且n≤k。s2.2,将特征空间向量矩阵x标准化并得到协方差矩阵s。s2.3,根据协方差矩阵s得到特征值λ1,λ2,…,λn以及与特征值对应的特征向量v1,v2,…,vn。s2.4,把特征值由大到小排序得到对角矩阵a:s2.5,根据特征向量计算特征空间向量矩阵x的主成分矩阵y:y=xv;v=[v1,v2,…,vn]。s2.6,将主成分矩阵y的第一主成分作为滚刀退化指标ab。s3,结合步骤s1和步骤s2以极限学习机算法构建寿命预测模型,如图2所示:β=[βi1,βi2,…βik]t;ω=[ωi1,ωi2,…ωin]t;式中:β表示第i个隐层节点于第k个输出节点的权重;ω表示第i个隐层节点与第n个输入节点的权重;bi表示第i个隐层节点上的偏置。s4,在线实时采集滚刀工作状态数据信息,更新模型输入端数据和模型输出端数据,并更新修正模型,最终将寿命预测模型的输出值与实际值对比得到寿命预测模型的精度与评价结果。实施例2:一种滚刀信息监测装置,如图3-4所示,包括滚刀刀座100,在滚刀刀座100的滑块端盖101内侧安有激光测距传感器1,在滚刀刀座的滚刀102外端面上安有温度传感器2和霍尔传感器3,在滚刀刀座的滚刀102的外侧壁安有电涡流传感器6;在滚刀刀座的c形块103上安有六维力传感器4和加速度传感器5;在滚刀刀座的驱动滑块104上安有电池8,在驱动滑块104上螺杆105上安有无线信号发射器7;激光测距传感器1、温度传感器2、霍尔传感器3、六维力传感器4、加速度传感器5、电涡流传感器6均通过无线信号发射器7发送至盾体内的信号接收器200,信号接收器200经信号线传输到数据预处理模块300,数据预处理模块300传输至工控机400内,工控机400可直接显示处理结果并将处理后的结果发送到远程端500进行查看,远程相关管理人员可通过自己的手机、pc端等直接进行查看。以上实施方式仅用于对本发明的描述,而非对本发明的限制。对本领域的技术人员来说在不脱离本发明的范围下进行适当的变化或修改是显而易见的,因此所有等同的技术方案也属于本发明的范畴,本发明的专利保护范围由所附的权利要求定义。当前第1页12