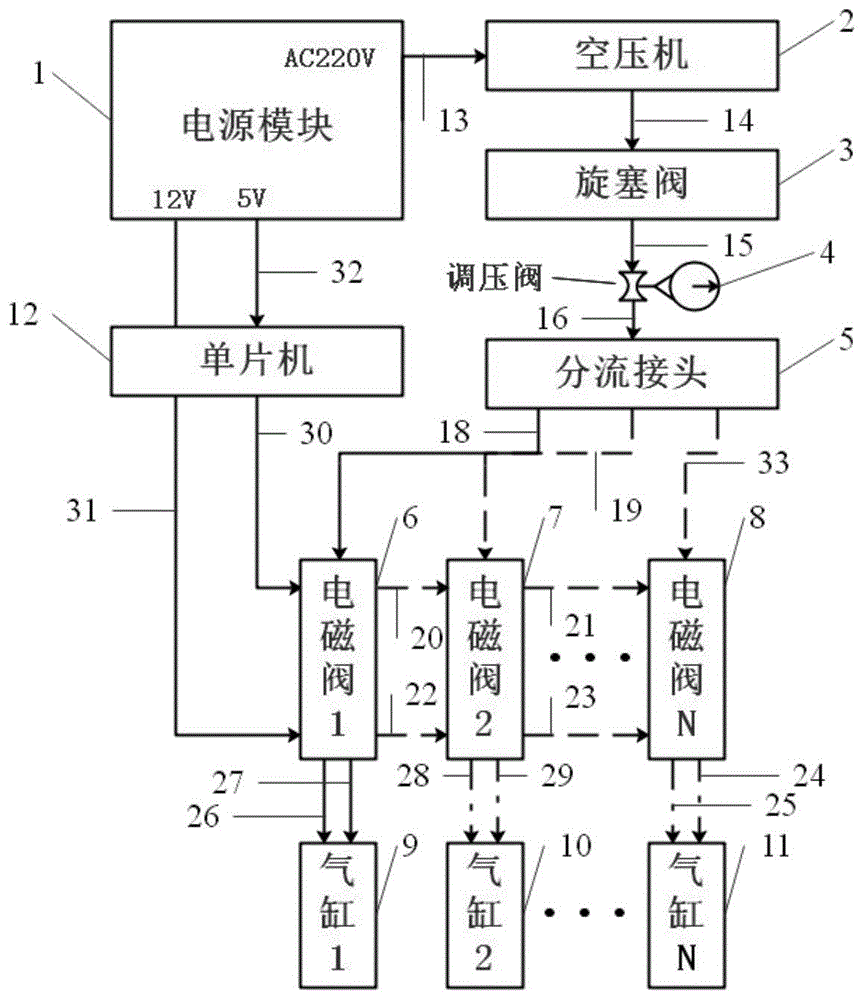
本发明涉及一种气动式变载荷多源冲击实验装置,属于结构状态监测领域。
背景技术:
材料及其构件在服役期间常会遭受不同种类载荷的冲击,导致材料及其构件容易产生损伤或结构变形,致使其力学性能劣化,带来安全隐患。因此对材料及其结构进行状态监测(尤其是冲击监测)有着非常重要的意义。
目前,被广泛应用的冲击装置有:落锤式冲击损伤装置、激振器装置和手持式冲击锤等,然而现有冲击装置均存在冲击方向单一、冲击载荷和时间可控性差、冲击点扩展难度大等不足,一定程度上局限了冲击监测的研究。
技术实现要素:
本发明的目的是提供一种气动式变载荷多源冲击实验装置,通过软件模块使单片机控制电磁阀的通断来间接控制气缸的冲击,以解决传统冲击实验手段可调性差的问题。
为实现上述目的,本发明专利的技术方案为:
一种气动式变载荷多源冲击实验装置,包括硬件模块和软件模块,硬件模块由空压机、旋塞阀、调压阀、分流接头、电磁阀、气缸、单片机、电源模块组成,通过软件模块使单片机控制电磁阀的通断来控制气缸的冲击。
优选地,所述硬件模块中,电源模块通过导线分别与空压机和单片机连接,单片机通过导线与电磁阀连接,空压机、旋塞阀、调压阀、分流接头和若干电磁阀依次通过导气管相连,电磁阀之间通过导气管串联,电磁阀通过导气管与气缸一一对应。
优选地,所述空压机由电动泵,集气腔、电磁阀,总开关组成,总开关设在空压机电磁阀上,该电磁阀通过两根导气管分别与电动泵和集气腔相连。空压机为整个装置提供动力。
优选地,所述旋塞阀安装于空压机集气腔的出气口。旋塞阀起开关作用,当空压机充气时,旋塞阀应关闭,防止腔体漏气。
优选地,所述调压阀通过导气管与旋塞阀连接,旋转调压阀旋钮可调节调压阀出气口的气压,使通入气缸内部气压减小或增大,从而使气缸产生的冲击力变小或增大。调压阀的作用是调节气缸冲击力大小。
优选地,所述分流接头通过导气管与调压阀连接,通过分流接头扩展若干电磁阀、气缸,扩展上限为n,n的最大值为单片机的io口总个数。分流接头的作用是为了产生多源冲击。
优选地,所述电磁阀为二位五通电磁阀,通过导气管与气缸连接,包括进气口、出气口和排气口,内部设有相连的弹簧和阀芯,外设有相连的电磁铁和电开关。电磁阀起控制气缸冲击作用。
优选地,所述气缸中,侧壁设有通气口a和通气口b,内部设有活塞与顶杆相连,活塞可在气缸中自由移动,活塞把气缸内部分为腔体上侧和腔体下侧。气缸为冲击执行元件,受电磁阀直接控制,具有安装方便,可改变冲击位置,冲击角度的特点。
优选地,所述电源模块分别为空压机、单片机、电磁阀供电。
优选地,所述软件模块通过软件程序控制单片机i/o口输出高、低电平,来控制电磁阀的通、断,从而实现控制气缸的冲击。
本发明有益效果是:
本发明提供了一种气动式变载荷多源冲击实验装置,相比传统冲击方式,冲击方式更加多样,冲击位置可调、冲击角度可调、冲击力大小可调、冲击个数可调,并且兼具冲击的稳定性,同时可自动控制、无人值守,满足了多源冲击监测研究的要求。
附图说明
图1是本发明的一种气动式变载荷多源冲击实验装置系统框图。
图2是本发明的电磁阀控制气缸冲击的顶杆弹出示意图。
图3是本发明的电磁阀控制气缸冲击的顶杆缩回示意图。
图4是本发明气缸在冲击过程中的受力分析示意图。
图5是本发明的空压机结构图示意图。
图6是本发明的电磁阀控制气缸冲击的顶杆弹出时气流方向示意图。
图7是本发明的电磁阀控制气缸冲击的顶杆缩回时气流方向示意图。
图8是本发明气缸结构图示意图。
图9是本发明软件模块流程框图。
附图标记:1-电源模块;2-空压机;3-旋塞阀;4-调压阀;5-分流接头;6-电磁阀1;7-电磁阀2;8-电磁阀n;9-气缸1;10-气缸2;11-气缸n;12-单片机;13、30、31、32-导线;14、15、16、18、19、20、21、22、23、24、25、26、27、28、29、33-导气管;34-总开关;35-电磁阀;36、37-导气管;38-集气腔;39-电动泵;40-进气口a;41-排气口d;42-排气口e;43-电磁铁;44-电开关;45-阀芯;46-出气口c;47-弹簧;48-出气口b;49-通气口a;50-通气口b;51-顶杆;52-活塞;53-腔体下侧;54-腔体上侧。
具体实施方式
下面结合附图进一步说明本发明的实施例。
一种气动式变载荷多源冲击实验装置,包括硬件模块和软件模块,硬件模块由空压机2、旋塞阀3、调压阀4、分流接头5、电磁阀、气缸、单片机12、电源模块1组成,通过软件模块使单片机12控制电磁阀的通断来控制气缸的冲击。
所述硬件模块中,电源模块1通过导线分别与空压机2和单片机12连接,单片机12通过导线与电磁阀连接,空压机2、旋塞阀3、调压阀4、分流接头5和若干电磁阀依次通过导气管相连,电磁阀之间通过导气管串联,电磁阀通过导气管与气缸一一对应。
所述空压机2由电动泵39,集气腔38、电磁阀35,总开关34组成,总开关34设在电磁阀35上,电磁阀35通过两根导气管36、37分别与电动泵39和集气腔38相连。空压机2为整个装置提供动力,将空压机2通电,打开总开关34,使其电动泵39工作,将外部空气压入集气腔38,使集气腔内气压逐步高于大气压,当气压上升至空压机额定气压之后空压机停止工作,此时打开旋塞阀3,气流通过导气管输送到气缸,使气缸内部气压大于大气压从而使气缸活塞顶杆弹出,对待冲击结构产生冲击。
所述旋塞阀3安装于空压机2中集气腔38的出气口。旋塞阀3起开关作用,当空压机2充气时,旋塞阀3应关闭,防止腔体漏气。
所述调压阀4通过导气管与旋塞阀3连接,调压阀的作用是调节气缸冲击力大小,旋转调压阀4旋钮可调节调压阀4出气口的气压,使通入气缸内部气压减小或增大,从而使气缸产生的冲击力变小或增大。
所述分流接头5通过导气管与调压阀4连接,分流接头的作用是为了产生多源冲击,通过分流接头5扩展若干电磁阀、气缸,扩展上限为n,n的最大值为单片机的io口总个数。
所述电磁阀为二位五通电磁阀,通过导气管与气缸连接,包括进气口a、出气口b、出气口c、排气口d、排气口e,内部设有相连的弹簧47和阀芯45,外设有相连的电磁铁45和电开关44。电磁阀起控制气缸冲击作用,如说明书附图2和3所示,将电磁阀进气口a通过导气管与分流接头5连接,将电磁阀出气口b通过导气管与气缸通气口a连接,将电磁阀出气口c通过导气管与气缸通气口b连接,当电磁阀中电开关44闭合时,电磁铁产生磁力吸住阀芯45,由于阀芯较长圆柱形主干部分半径小于腔体半径,气体可从a→c,故气流方向为进气口a→出气口c→通气孔b→气缸内部,此时气缸内部下半部分气压逐渐增大,迫使气缸顶杆51弹出,露出大部分顶杆51,从而可造成冲击,同时,气缸内部上半部分多余气体从通气口a→出气口b→排气口d排出,反之,电磁阀中电开关44断开时,电磁铁45的磁力消失并与阀芯45断开,气流方向为进气口a→出气口b→通气孔a→气缸内部,此时气缸内部上半部分气压逐渐增大,迫使气缸顶杆51下降,缩回气缸内部,同时,气缸内部下半部分多余气体从通气口b→出气口c→排气口e排出,当电磁阀不断闭合、断开,可实现气缸造成连续冲击。
所述气缸中,侧壁设有通气口a和通气口b,内部设有活塞52与顶杆51相连,活塞52可在气缸中自由移动,活塞52把气缸内部分为腔体上侧54和腔体下侧53。气缸为冲击执行元件,受电磁阀直接控制,具有安装方便,可改变冲击位置,冲击角度的特点。
结合说明书附图4,并忽略顶杆和活塞重力,所属气缸冲击力分析如下:
f=f1-f2-f(1)
f1=pa(2)
a=πr2(3)
f2+f=(1-α)f1(4)
结合公式(1)、(2)、(3)、(4),得:
f=απpr2(5)
公式(1)中f为气缸的冲击力,f1为气压压力,f2为气压阻力,f摩擦阻力,公式(2)中p为气压大小,a为受压面积,既气缸活塞底部面积(活塞底部为圆形),公式(3)中r为气缸活塞底部半径,公式(4)中α为阻力系数,和气缸活塞或顶杆运动速度有关,具体如下:
当气缸活塞或顶杆速度在0~50mm/s范围时,α≤0.7;
当气缸活塞或顶杆速度在50~500mm/s范围时,0.3≤α≤0.5;
当气缸活塞或顶杆速度大于500mm/s时,α≤0.3;
一般冲击实验中,冲击都为瞬时或快速冲击,故气缸活塞或顶杆速度一般大于500mm/s,α常取0.3;
所述电源模块1分别为空压机2、单片机12、电磁阀供电。
所述软件模块通过软件程序控制单片机i/o口输出高、低电平,来控制电磁阀的通、断,从而实现控制气缸的冲击。具体地,软件模块通过控制高电平的持续时间来控制电磁阀连通的时间,即气缸充气时间,从而控制气缸的行程;并通过软件程序控制单片机每次输出高、低电平的时间间隔来控制冲击时间间隔,特别的,电磁阀的连通也可由低电平控制。软件模块的具体流程如说明书附图9所示。
所述软件模块的功能一为:通过软件程序控制单片机一个i/o口输出一次高、低电平,来控制电磁阀的一次通断,从而实现控制气缸的一次冲击;使单片机具有控制气缸单次冲击功能。
所述软件模块的功能二为:通过软件程序控制单片机一个i/o口输出多次高、低电平,来控制电磁阀的多次通断,从而实现控制气缸的多次冲击,通过程序设置单片机每次输出高、低电平的时间间隔来控制冲击时间间隔;使单片机具有控制气缸多次冲击功能,且冲击次数可设定,冲击时间间隔可设定。
所述软件模块的功能三为:通过软件程序设计循环控制,使冲击不断循环;使单片机具有控制气缸不断循环冲击功能,且循环时间间隔可设定。
所述软件模块的功能四为:通过软件程序控制单片机i/o的个数,来控制多个电磁阀的通断,控制多个气缸的多次冲击;使单片机具有控制多个气缸的功能,且可单独为每个气缸设定冲击次数,冲击间隔。
所述软件模块的功能五为:通过软件程序控制高电平持续时间,即控制了气缸充气时间,充气时间越久,气缸活塞受力越久,积蓄的能量越多,行程越长,特别的,行程最大值受气缸机械结构影响;使单片机具控制控制气缸充气时间功能,从而控制气缸的行程。
实施例1
本实施例是一种气动式变载荷多源冲击实验装置,包括硬件模块和软件模块,如附图所示。本装置通过软件模块使单片机控制电磁阀的通断间接控制气缸冲击,不扩展冲击源(n=1),具体如下:
所述硬件模块由空压机2、旋塞阀3、调压阀4、分流接头5、电源模块1、单片机12、电磁阀6、气缸9组成。所述空压机2、单片机12、电磁阀6均与所述电源模块1有线电连接;所述空压机2、旋塞阀3、调压阀4、分流接头5、电磁阀6、气缸9由导气管相互连接。特别的,所述电源模块1分别给空压机2、单片机12、电磁阀6供ac220v、dc5v、dc12v。
其中,所述空压机2可提供最大为气压0.7mpa,由电动泵39、集气腔38、电磁阀35、充气开关34组成如附图5所示。所述电动泵39、电磁阀34由电源模块1供电,电磁阀35自带稳压。当通电之后,先关闭旋塞阀3,接着打开充气开关34,同时电磁阀35被打开,电动泵39开始工作,空气通过导气管37、电磁阀35、导气管36被电动泵连续压入集气腔38。在本次实施例中,当集气腔内气压上升至0.7mpa,电动泵39、电磁阀35自动关闭。
进一步,打开所述旋塞阀3,由于气压差,在集气腔38内的气体将通过导气管14、旋塞阀3、导气管15、至调压阀4。特别的,所述调压阀4可根据自己需求调节,每个气压值对应所述气缸9的出力值。
进一步,气体从调压阀4通过导气管16至分流接头5,所述分流接头5起扩展冲击源作用。
进一步,气体通过分流接头5之后在通过导气管18输送至所述电磁阀6。
进一步,所述单片机12型号为stc89c52,用于控制所述电磁阀6的通断,并进一步控制所述气缸9的冲击。
其中,所述电磁阀6为二位五通电磁阀,与导气管18相连。所述电磁阀6由进气口40、出气口46、出气口48、排气孔41、排气孔42、阀芯45、电磁铁43、电开关44、弹簧47组成,当所述单片机12控制电磁阀6打开时,电开关44闭合,电磁铁43工作,产生吸力将阀芯45往左方向拉,弹簧47被拉伸,储存一定弹性势能,如附图6,此时,进气口40与出气口46联通,将导气管18的气体输送至气缸9,同时,排气孔41将阀芯45左侧多余气体排除,使阀芯45左侧气压和大气压一致;当所述单片机12控制电磁阀6关闭时,电开关44断开,电磁铁43停止工作,弹簧47将阀芯45往右方向拉,弹簧47收缩,释放弹性势能,如附图7,此时,进气口40与出气口48联通,将导气管18的气体输送至气缸9,同时,排气孔42将阀芯45右侧多余气体排除,使阀芯45右侧气压和大气压一致。
进一步,所述气缸9型号为标准气缸sc32×25,由通气口49、通气口50、活塞52、顶杆51、腔体上侧54、腔体下侧53组成,如附图8所示。所述通气口49、通气口50分别与所述电磁阀6中出气口48、出气口46相连。当所述电磁阀6被打开时,出气口46出气并将持续气体从通气口50引入气缸9的腔体下侧53,使腔体下侧53气压不断上升并大于腔体上侧54,在气压差的作用下,活塞52被迫往上升,带动顶杆51从气缸9内弹出,同时腔体上侧54中多余气体通过通气口49、出气口48被压入电磁阀6,并从排气口41排出;当所述电磁阀6被关闭时,出气口48出气并将持续气体从通气口49引入气缸9的腔体上侧54,使腔体上侧54气压不断上升并大于腔体下侧53,在气压差的作用下,活塞52被迫往下降,带动顶杆51缩回气缸9内,同时腔体下侧53中多余气体通过通气口50、出气口46被压入电磁阀6,并从排气口42排出。
特别的,所述气缸9理论出力表如下:
表1标准气缸sc32×25理论出力表
表1中力的单位为n。实际出力应为理论出力乘以系数α,在一般冲击实验中,冲击都为瞬时或快速冲击,故气缸活塞或顶杆速度一般大于500mm/s,α常取0.3。
实施例2
在实施例1的基础上,将所述气缸9更改为标准气缸sc63×25,其理论出力表如下:
表2标准气缸sc63×25理论出力表
表2中力的单位为n。实际出力值与实施例1中标准气缸sc32×25计算方法一样。
实施例3
在实施例1的基础上,扩展1个冲击源,总冲击源为2个,即n=2。
所述分流接头5将导气管16输送过来的气体分流之后,在通过导气管18、19输送给电磁阀6、7。
进一步,所述单片机12控制所述电磁阀6、7的通断,并进一步控制所述气缸9、10的冲击。
实施例4
在实施例1的基础上,扩展n-1个冲击源,总冲击源为n个,即n为单片机的io口总个数,使单片机12控制n个电磁阀的通断,并进一步控制n个气缸的冲击。本实施例中,单片机型号为stc89c52,共有32个io口可用,故n取32。
实施例5
在实施例1的基础上,用单片机12控制气缸9单次冲击,实现软件模块的功能一。本实施例单片机采用stc89c52,将电磁阀1控制端通过杜邦线与单片机12的p10口相连,接地端与单片机12的gnd相连,在上位机上使用keil4编写程序,使单片机12按下按键“1”后能使p10口输出一个80ms的高电平后持续输出低电平,可使气缸9产生一个充气时间为80ms的冲击。进一步,将编写好的程序利用stx-isp烧录软件将程序通过usb烧录至单片机12。实现功能一程序为:
if(key==1)
{p1=0x01;
delayms(80);
p1=0x00;}
实施例6
在实施例1的基础上,用单片机12控制气缸9多次冲击,实现软件模块的功能二。本实施例单片机采用stc89c52,将电磁阀1控制端通过杜邦线与单片机12的p10口相连,接地端与单片机12的gnd相连,在上位机上使用keil4编写程序,使单片机12按下按键“2”后能使p10口输出多个80ms的高电平100ms低电平,可使气缸9产生多个充气时间为80ms的冲击。进一步,将编写好的程序利用stx-isp烧录软件将程序通过usb烧录至单片机12。实现功能二程序为:
其中for(i=c;i>0;i--)起设定冲击次数作用,:“7”为冲击次数,可根据需求设定;
其中delay2(100)起设置冲击间隔作用,“100”指冲击间隔100ms,可根据需求设定。由于本次实施例气缸采用标准气缸sc32×25,最短间隔为0.1s,故100为最小设定值。
实施例7
在实施例1的基础上,用单片机12控制气缸9循环冲击,实现软件模块的功能三。本实施例单片机采用stc89c52,将电磁阀1控制端通过杜邦线与单片机12的p10口相连,接地端与单片机12的gnd相连,在上位机上使用keil4编写程序,使单片机12按下按键“3”后能使p10口循环输出80ms的高电平100ms低电平,可使气缸9循环产生充气时间为80ms的冲击。进一步,将编写好的程序利用stx-isp烧录软件将程序通过usb烧录至单片机12。实现功能三程序为:
实施例8
在实施例4的基础上,用单片机12控制n个气缸9多次冲击,实现软件模块的功能四。本实施例单片机采用stc89c52,n取4,将电磁阀1-4控制端通过杜邦线与单片机12的p10-p13口相连,接地端与单片机12的gnd相连,在上位机上使用keil4编写程序,使单片机12按下按键“4”后能使p10-p13口按设定次数输出80ms的高电平100ms低电平,可使气缸9按设定次数产生充气时间为80ms的冲击。进一步,将编写好的程序利用stx-isp烧录软件将程序通过usb烧录至单片机12。实现功能四程序为:
本实施例分别控制气缸1-4分别产生7、8、9、10次冲击间隔为80ms的冲击。
实施例9
在实施例5、6、7、8的基础上,delay1(80)起设定充气时间作用,实现软件模块的功能五。“80”指充气80ms,可根据实际需要气缸行程设定。
基于上述过程,通过设定软件模块的各参数后,单片机12即可控制气缸完成一种基于气动的多自由度变载荷多源冲击实验。
虽然,上文中已经用一般性说明及具体实施例对本发明作了详尽的描述,但在本发明基础上,可以对之作些修改或改进,这对本领域技术人员而言是显而易见的。因此在不偏离本发明精神的基础上所做的这些修改或改进,均属于本发明要求保护的范围。