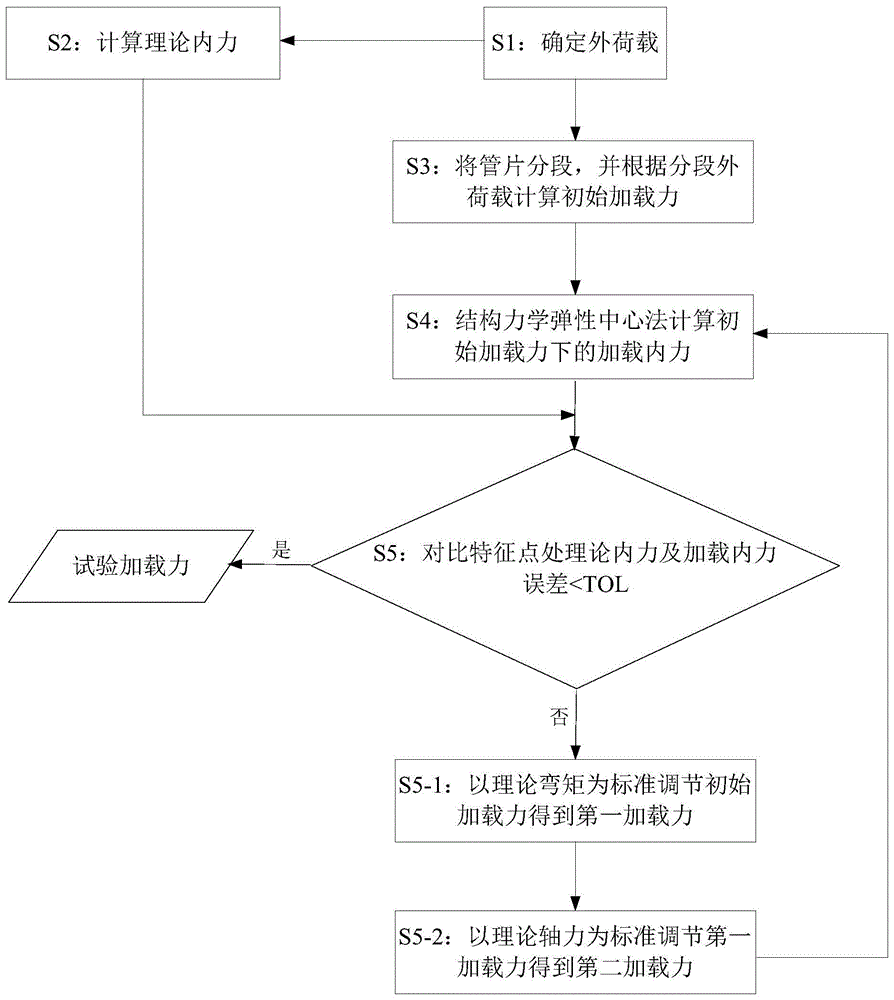
本发明涉及隧道领域,特别涉及圆形隧道预制衬砌管片的整环结构试验。
背景技术:
:随着我国经济的迅速发展和城市化进程的进一步加速,城市交通拥堵问题日益突出,严重影响着人们的出行和生活。作为解决城市交通拥堵问题的重要措施,近年来地铁隧道的建设如火如荼地开展。因功能需求和赋存环境的不同,隧道结构的设计存在一定差异。为了确保工程的安全,新型隧道结构在复杂水土荷载条件下的安全性与设计的合理性通常需通过整环结构试验来验证。准确还原结构真实的内力情况直接关系到整环结构试验的准确性,因此在整环结构试验中精确计算试验加载力的方法尤为重要。目前,关于试验加载力的计算并无统一的计算方法,常用的方法主要为:(1)衬砌分段水土荷载的合力直接作为千斤顶径向加载的试验加载力;(2)将水土荷载的合力分解为切向力和径向力,舍去切向力,留取径向力作为千斤顶径向加载的试验加载力;(3)其他方法。为了保证试验装置的平衡,上述方法往往将轴对称模型简化为中心对称模型,因此所获得的管片内力往往与实际管片内力相差较大,无法真实反映管片的受力变形特性。由此可见,建立一种能够精确计算隧道管片整环结构试验中试验加载力的方法尤为重要,通过提高试验加载力的精确度来实现准确模拟隧道管片的受力情况,以提高整环结构试验结果的准确性,对隧道工程将具有指导意义。技术实现要素:本发明的目的在于克服现有技术的缺陷,提供一种隧道管片整环结构试验中精确计算试验加载力的方法,本方法能够提高整环结构试验加载力的计算精度,以管片在外荷载下的理论内力中的理论弯矩和理论轴力为标准,分两次调整初始加载力,使调整后的初始加载力更加接近管片所受的外荷载,以调整后的初始加载力作为最终的试验加载力,提高了管片整环结构试验的准确性。为实现上述目的,本发明采用的技术方案是:一种隧道管片整环结构试验中精确计算试验加载力的方法,包括如下步骤:s1:确定管片的外荷载;s2:计算所述管片在所述外荷载下的理论内力;s3:将所述管片分为多段,每段设置一个加载点,根据所述外荷载计算出每个所述加载点处的初始加载力p0,i;s4:根据结构力学弹性中心法计算出所述管片在所有所述初始加载力p0,i下的加载内力;s5:于所述管片上选取若干个特征点,对比每个所述特征点处的所述理论内力和所述加载内力,并对误差进行如下调整:s5-1:根据所述理论内力中的理论弯矩与所述加载内力中的加载弯矩计算出所有所述特征点处的平均误差比k,再以所述平均误差比k作为第一次误差调整标准,用每个所述初始加载力p0,i乘以所述平均误差比k得到第一加载力p1,i,求解方程如下:所述平均误差比k为所述第一加载力p1,i为p1,i=kp0,i其中,m为特征点的数量,mj为特征点j处的理论弯矩,m0,j为特征点就j处的初始加载弯矩;s5-2:根据所述理论内力中的理论轴力、所述初始加载内力中的加载轴力及所述平均误差比k计算出所述第一加载力p1,i的平均加载力增量δp,再以所述平均加载力增量δp作为第二次误差调整标准,用每个所述第一加载力p1,i加上所述平均加载力增量δp得到第二加载力p2,i,求解方程如下:所述平均加载力增量δp为所述第二加载力p2,i为p2,i=p1,i+δp其中,nj为特征点j处的理论轴力,n0,j为特征点j处的初始加载轴力;δnj为特征点j处在单位加载力(即1n)下的轴力。通过上述两次误差调整,得到更加接近实际外荷载的试验加载力,提高了试验加载力的计算精度,进而提高了管片整环结构试验的准确性。本发明一种隧道管片整环结构试验中精确计算试验加载力的方法的改进在于,所述初始加载力p0,i的计算方法如下:对每段管片所受的外荷载求解合力f0,i,并将每个所述合力f0,i分解成径向力r0,i和切向力t0,i;求解微调系数μ,使所述径向力r0,i在y轴方向上平衡,再通过所述微调系数μ得出所述初始加载力p0,i,求解方程如下:当n为奇数时,所述微调系数μ为则所述初始加载力p0,i为当n为偶数时,所述微调系数μ为则所述初始加载力p0,i为其中,n为加载点的数量的一半,θi为加载点i处初始加载力p0,i与y轴的夹角。通过上述方法计算出的初始加载力,比传统的直接将分段外荷载合力作为初始加载力的方法所计算出的初始加载力更加接近管片的实际受力情况。本发明一种隧道管片整环结构试验中精确计算试验加载力的方法的改进在于,在步骤s5中,至少选取四个所述特征点,且四个所述特征点分别位于所述管片的拱顶、拱底、两腰位置处。由于调整误差的过程需要大量的计算,所以在实际调整时,可以选一些能够反应管片受力特征的特征点,而管片的拱顶、拱底、两腰位置的受力最为典型,最能够反应出管片的主要受力特征,因此,将此四处位置作为特征点来进行对比和计算,得到统一的误差调整标准,这样既减轻了计算量,又能保证计算的准确性。本发明一种隧道管片整环结构试验中精确计算试验加载力的方法的改进在于,将所述第二加载力p2,i作为调整后的初始加载力p0,i’代入步骤s4。通过上述迭代调整方式,使试验加载力更加接近管片所受的外荷载,使试验更真实的还原管片的受力情况。本发明的方法,能够精确计算隧道管片整环结构试验中的试验加载力,使试验加载力更加接近管片所受的外荷载,能够更加真实地反映出管片的受力变形特性,提高了管片整环结构试验的准确性。附图说明为了更清楚地说明本发明实施例中的技术方案,下面将对实施例描述中所需要使用的附图作简单地介绍,显而易见地,下面描述中的附图仅仅是本发明的一些实施例,对于本领域普通技术人员来讲,在不付出创造性劳动的前提下,还可以根据这些附图获得其他的附图。图1示出了本发明实施例的计算方法流程图;图2示出了本发明实施例外荷载分布示意图;图3示出了本发明实施例的加载点布局图;图4示出了本发明实施例中某加载点处外荷载的合力分解示意图;图5示出了本发明实施例的管片半结构切割状态示意图。具体实施方式以下通过特定的具体实例说明本发明的实施方式,本领域技术人员可由本说明书所揭露的内容轻易地了解本发明的其他优点与功效。本发明还可以通过另外不同的具体实施方式加以实施或应用,本说明书中的各项细节也可以基于不同观点与应用,在没有背离本发明的精神下进行各种修饰或改变。目前,关于整环结构试验的试验加载力的常用计算方法主要为:(1)衬砌分段水土荷载的合力直接作为千斤顶径向加载的试验加载力;(2)将水土荷载的合力分解为切向力和径向力,舍去切向力,留取径向力作为千斤顶径向加载的试验加载力;(3)其他方法。为了保证试验装置的平衡,上述方法往往将轴对称模型简化为中心对称模型,因此所获得的管片内力往往与实际管片内力相差较大,无法真实反映管片的受力变形特性。本发明提供了一种对上述方法(2)中的试验加载力进行迭代调整的计算方法,以实际外部荷载计算出的理论内力为标准,将试验加载力控制在一定误差范围内,以实现准确模拟隧道管片的受力情况,提高整环结构试验结果的准确性。下面结合附图和具体实施例对本发明做进一步详细说明。参阅图1~3所示,本实施例提供了一种隧道管片整环结构试验中精确计算试验加载力的方法,该方法包括如下步骤:s1:确定管片的外荷载;根据实际工程设计情况确定管片所承受的外部荷载,包括水土荷载、地面超载等。s2:计算所述管片在所述外荷载下的理论内力;计算管片理论内力的方法有惯用法、均质圆环法等,具体可根据实际工程设计需求来选取合适的理论方法,本实施例根据管片情况选取均质圆环法计算出外荷载下的理论内力,该理论内力包括理论弯矩m和理论轴力n。s3:将所述管片分为多段,每段设置一个加载点,根据所述外荷载计算出每个所述加载点处的初始加载力p0,i;具体地,将管片沿圆周方向等分2n段,每段设置一个千斤顶加载点,在实际试验时可根据千斤顶的数量确定n的值,n的值越大,模拟外部荷载就越准确,本实施例的n值为15,即将管片分成30段,每段圆弧角度为π/15,然后根据每段圆弧上的外荷载计算每个加载点处的初始加载力p0,i。本实施例选用如下方式求解初始加载力p0,i:首先,配合图4所示,将每段圆弧上的外荷载于加载点处求解合力f0,i,然后将每个合力f0,i沿管片的径向和切向分解成径向力r0,i(见表1)和切向力t0,i。然后,为保证试验加载的平衡性,根据力的平衡原理,求解微调系数μ,此处仅考虑径向力r0,i的平衡,忽略圆形管片的切向力t0,i影响,通过使得径向力r0,i在y轴方向平衡(即使x轴以上的所有径向力的合力与x轴以下的所有径向力的合力相互抵消)求得微调系数μ,再根据微调系数μ得到初始加载力p0,i,计算方程如下:因为n=15为奇数,所以微调系数μ按方程(1)求解:则初始加载力p0,i为θi为加载点i处初始加载力p0,i与y轴的夹角。本实施例求解微调系数μ=0.0146,通过调整系数μ得到的初始加载力p0,i(见表1)。s4:根据结构力学弹性中心法计算出所述管片在所有所述初始加载力p0,i下的加载内力;具体地,配合图5所示,取管片的半结构,将管片沿y轴方向切割,然后根据结构力学弹性中心法,计算出每个加载点处同时以初始加载力p0,i对管片施力时的管片的加载内力(该加载内力包括加载弯矩m0和加载轴力n0),由于结构力学弹性中心法为现有算法,此处将不再赘述求解过程。s5:于所述管片上选取若干个特征点,对比每个所述特征点处的所述理论内力和所述加载内力,并对误差进行如下调整:由于调整误差的过程需要大量的计算,所以在实际调整时,可以选一些特征点,仅需针对这些特征点来进行对比和计算,得到统一的误差调整标准,这样既减轻了计算量,又能保证计算的准确性。建议选择一些能够反应管片受力特征的特征点,可以选择管片上性能较为薄弱的位置作为特征点,如管片的接缝点处;或者选择与一侧外荷载力的方向保持一致的位置作为特征点,如管片的拱顶、拱底和两腰处。本实施例所选择的特征点即为管片的拱顶、拱底和两腰位置,下面是本实施例以这四个特征点为基准对误差加以调整的步骤:s5-1:根据所述理论内力中的理论弯矩m(见表2)与所述加载内力中的加载弯矩m0计算出所有所述特征点处的平均误差比k,再以所述平均误差比k作为第一次误差调整标准,用每个所述初始加载力p0,i乘以所述平均误差比k得到第一加载力p1,i,求解方程如下:所述平均误差比k为所述第一加载力p1,i为p1,i=kp0,i(4)其中,m为特征点的数量,mj为特征点j处的理论弯矩,m0,j为特征点就j处的初始加载弯矩;s5-2:根据所述理论内力中的理论轴力n(见表2)、所述初始加载内力中的加载轴力n0及所述平均误差比k计算出所述第一加载力p1,i的平均加载力增量δp,再以所述平均加载力增量δp作为第二次误差调整标准,用每个所述第一加载力p1,i加上所述平均加载力增量δp得到第二加载力p2,i,该第二加载力p2,i即为试验加载力,求解方程如下:所述平均加载力增量δp为所述第二加载力p2,i为p2,i=p1,i+δp(8)其中,nj为特征点j处的理论轴力,n0,j为特征点j处的初始加载轴力;δnj为特征点j处在单位加载力(即1n)下的轴力。通过上述方法,对初始加载力p0,i先后以理论弯矩m和理论轴力n为标准进行了两次调整,从弯矩和轴力两个方向上降低了加载内力对比理论内力的误差,使试验加载力更加接近实际的外荷载,提高了试验加载力的计算精度及管片整环结构试验的准确性。较佳地,为了使试验加载力更加接近管片所受的外荷载,使试验更真实的还原管片的受力情况,可以将步骤s5中得到的第二加载力p2,i作为调整后的初始加载力p0,i’(见表1)代入步骤s4中重新计算加载内力,并第二次与理论内力对比,并调整误差,如此形成迭代调整,调整次数越多,所得到的试验加载力的值就越精确。不过考虑到实际计算量,可以根据行业经验,设定一个误差标准tol,若加载内力与理论内力对比的误差小于该误差标准tol时,即可将该加载内力对应的初始加载力p0,i作为实际试验时的试验加载力,若加载内力与理论内力对比的误差不小于误差标准tol时,再进行步骤s5-1和s5-2的误差调整,直至调整到误差小于误差标准tol时停止迭代。本实施例经过两次迭代得到最终符合要求的试验加载力p0,i”(见表1)。表1试验加载力迭代调整数据表2特征点理论内力拱顶左腰拱底右腰弯矩m(kn·m)250-216181-216轴力n(kn)2272252024072520以上所述仅是本发明的较佳实施例而已,并非对本发明做任何形式上的限制,虽然本发明已以较佳实施例揭露如上,然而并非用以限定本发明,任何熟悉本专业的技术人员,在不脱离本发明技术方案的范围内,当可利用上述揭示的技术内容作出些许更动或修饰为等同变化的等效实施例,但凡是未脱离本发明技术方案的内容,依据本发明的技术实质对以上实施例所作的任何简单修改、等同变化与修饰,均仍属于本发明技术方案的范围内。当前第1页12