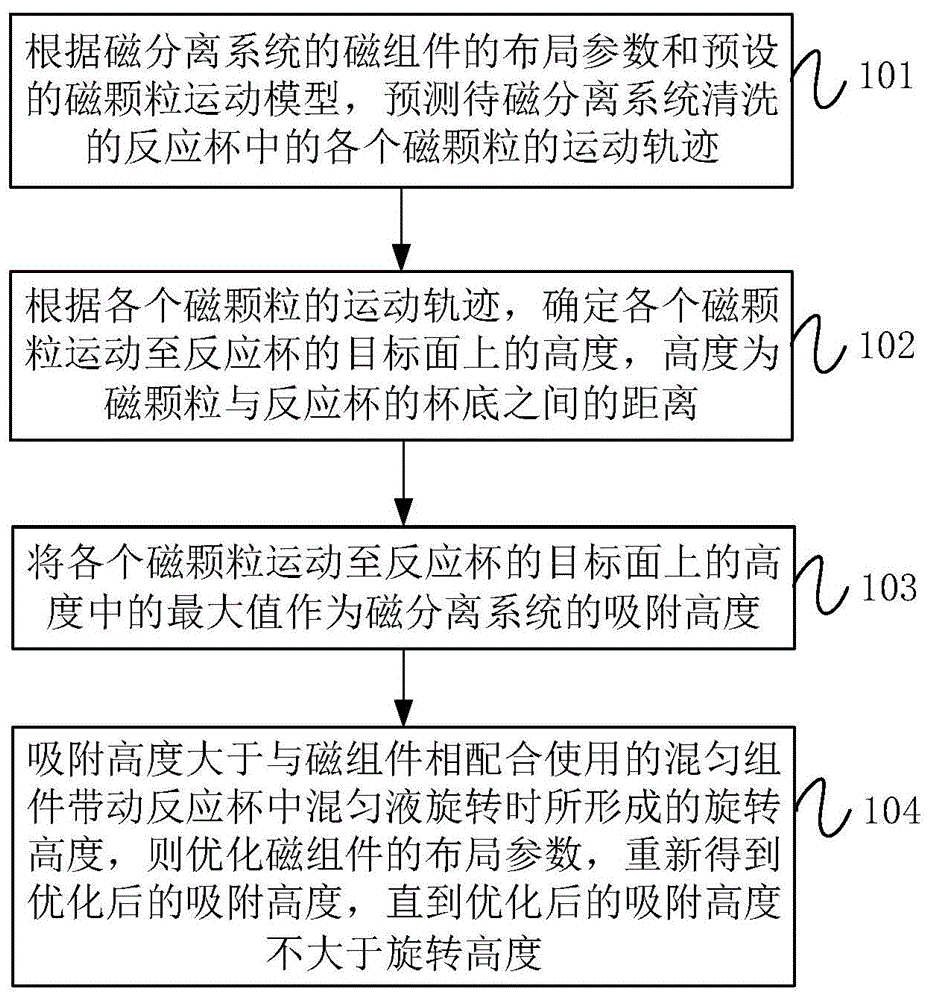
本发明涉及医疗器械领域,尤其涉及一种磁分离系统的参数优化方法和装置、分析仪器、存储介质。
背景技术:
:磁免疫分析仪器中的磁分离系统可以通过磁组件将进入磁分离系统中的反应杯内基液中的磁颗粒分离出来,磁颗粒在磁组件的磁场作用下会运动到反应杯内一侧的杯壁形成磁颗粒团。由此可见,磁组件的磁场分布会影响磁颗粒运动轨迹,从而决定磁颗粒团的高度,即该磁分离系统的吸附高度。其中,磁颗粒团的高度指的是磁颗粒团中处于最高位置处的磁颗粒距离反应杯杯底的距离。现有技术中大多采用经验设计来判断磁分离系统的吸附高度,缺乏对磁颗粒运动的理论分析,因此,当设计出一套新的磁分离系统后,往往要经过多次试验才能判断这套磁分离系统的吸附高度,当吸附高度不合适时,需要调整磁分离系统中磁组件的参数去反复测试,以优化磁组件的磁场分布,从而使吸附高度调整到位,存在工作效率低的问题。技术实现要素:本发明实施例提供了一种磁分离系统的参数优化方法和装置、分析仪器、存储介质,不需要调整磁分离系统中磁组件的布局参数去反复测试,仅仅通过理论模拟就能够得到目标吸附高度,明显地提高了工作效率。第一方面,本发明实施例提供了一种磁分离系统的参数优化方法,该方法包括:根据磁分离系统的磁组件的布局参数和预设的磁颗粒运动模型,预测待磁分离系统清洗的反应杯中的各个磁颗粒的运动轨迹;根据各个磁颗粒的运动轨迹,确定各个磁颗粒运动至反应杯的目标面上的高度,高度为磁颗粒与反应杯的杯底之间的距离;将各个磁颗粒运动至反应杯的目标面上的高度中的最大值作为磁分离系统的吸附高度;若吸附高度大于与磁组件相配合使用的混匀组件带动反应杯中混匀液旋转时所形成的旋转高度,则优化磁组件的布局参数,重新得到优化后的吸附高度,直到优化后的吸附高度不大于旋转高度,其中,旋转高度为混匀液旋转时液面的最高点与反应杯的杯底之间的距离。在第一方面的一些实施例中,磁组件为磁铁,磁组件的布局参数包括磁铁形状、大小、放置位置和磁场强度中的至少一个。在第一方面的一些实施例中,旋转高度由混匀组件中的混匀电机的角速度,与混匀电机连接的偏心头的偏心距,反应杯的大小,以及混匀液的剂量决定。在第一方面的一些实施例中,在预测待磁分离系统清洗的反应杯中的各个磁颗粒的运动轨迹的步骤之后,该方法还包括:根据各个磁颗粒的运动轨迹,预测各个磁颗粒运动至反应杯的目标面上的时间;将各个磁颗粒运动至反应杯的目标面上的时间中的最大值作为磁分离系统的吸附时间;根据磁分离系统的吸附时间,确定磁分离系统的时序设计的最小时间片段。在第一方面的一些实施例中,预设的磁颗粒运动模型由磁颗粒在磁组件的磁场环境受到的磁场力,以及磁颗粒在反应杯的基液中运动时的粘性阻力确定,粘性阻力包括摩擦阻力和形状阻力。在第一方面的一些实施例中,磁颗粒运动模型的表达式为:磁场力的表达式为:粘性阻力的表达式为:其中,为磁颗粒受到的合力,为磁场力,为粘性阻力,m为磁颗粒的质量,为磁颗粒的加速度,μ0为空间磁导率,δx为磁颗粒与所述反应杯中基液的相对磁化系数,δx=χp-χf,χp为磁颗粒的磁化系数,χf为基液的磁化系数,vm为磁颗粒的球体积,b为空间位置的磁通密度,为空间位置的磁通密度的梯度,为摩擦阻力,为形状阻力,为无量纲摩擦阻力系数,为无量纲形状阻力系数,a为磁颗粒的特征面积,ρ为基液的密度,v为磁颗粒相对基液的运动速度。在第一方面的一些实施例中,磁颗粒运动模型的微分形式表达式为:其中,x,y,z为磁颗粒的三维空间坐标,ρ1为磁颗粒的密度,d为磁颗粒的直径,bx,by,bz分别为x,y,z三维空间坐标下的磁通密度分布,分别为x,y,z三维空间坐标下磁通密度的梯度,分别为x,y,z对时间的一阶导数,分别为x,y,z对时间的二阶导数。在第一方面的一些实施例中,磁颗粒运动模型的微分表达式经过有限差分法处理后的数值表达式为:其中,i=1,2,3,…,且磁通密度梯度根据与位置xi、yi、zi空间距离最近的磁场节点的磁通密度计算得到。第二方面,本发明实施例提供了一种磁分离系统的参数优化装置,该装置包括:预测模块,根据磁分离系统的磁组件的布局参数和预设的磁颗粒运动模型,预测待磁分离系统清洗的反应杯中的各个磁颗粒的运动轨迹;磁颗粒运动高度计算模块,根据各个磁颗粒的运动轨迹,确定各个磁颗粒运动至反应杯的目标面上的高度,高度为磁颗粒与反应杯的杯底之间的距离;吸附高度计算模块,将各个磁颗粒运动至反应杯的目标面上的高度中的最大值作为磁组件的吸附高度;磁组件优化模块,若吸附高度大于与磁组件相配合使用的混匀组件带动反应杯中混匀液旋转时所形成的旋转高度,则优化磁组件的布局参数,重新得到优化后的吸附高度,直到优化后的吸附高度不大于旋转高度,其中,旋转高度为混匀液旋转时液面的最高点与反应杯的杯底之间的距离。在第二方面的一些实施例中,该装置还包括:磁颗粒运动时间计算模块,用于根据各个磁颗粒的运动轨迹,预测各个磁颗粒运动至反应杯的目标面上的时间;吸附时间计算模块,用于将各个磁颗粒运动至反应杯的目标面上的时间中的最大值作为磁分离系统的吸附时间;最小时间片段优化模块,用于根据磁分离系统的吸附时间,确定磁分离系统的时序设计的最小时间片段。第三方面,本发明实施例提供了一种分析仪器,该仪器包括:磁分离系统以及如上所述的磁分离系统的参数优化装置。第四方面,本发明实施例提供了一种存储介质,其上存储有程序,程序被处理器执行时实现如上所述的磁分离系统的参数优化方法。该方法可以根据所述磁分离系统的磁组件的布局参数和预设的磁颗粒运动模型,预测得到在磁组件特定的布局参数下的磁分离系统的吸附高度,并且在当吸附高度大于旋转高度时,优化磁组件的布局参数,以及得到优化后的吸附高度,直到优化后的吸附高度不大于旋转高度。相比于现有技术,本发明实施例提供的参数优化方法不需要调整磁分离系统中磁组件的布局参数去反复测试,仅仅通过理论模拟就能够得到磁分离系统的目标吸附高度,明显地提高了工作效率。附图说明从下面结合附图对本发明的具体实施方式的描述中可以更好地理解本发明,其中,相同或相似的附图标记表示相同或相似的特征。图1为本发明实施例的参数优化方法的流程示意图;图2为本发明实施例的磁组件捕获磁颗粒的过程示意图;图3为本发明实施例的磁分离系统的清洗过程示意图;图4为本发明实施例的混匀组件的结构示意图;图5为本发明实施例的偏心头的结构示意图;图6为本发明实施例的反应杯的状态示意图;图7为本发明实施例的反应杯的又一状态示意图;图8为本发明实施例的反应杯的另一状态示意图;图9为本发明实施例的反应杯中混匀液的不同旋转高度的示意图;图10为本发明又一实施例的参数优化方法的流程示意图;图11为本发明实施例的磁颗粒的受力示意图;图12为本发明实施例的两块叠加的磁铁的空间磁场分布示意图;图13为本发明实施例的磁铁捕获磁颗粒的示意图;图14为本发明又一实施例的磁颗粒运动模型的数值解法的流程示意图;图15为本发明实施例的反应杯的又一状态示意图;图16为本发明实施例的反应杯的另一状态示意图;图17为本发明一实施例提供的磁分离系统的参数优化装置的模块示意图;图18为本发明另一实施例提供的磁分离系统的参数优化装置的模块示意图。具体实施方式下面将详细描述本发明的各个方面的特征和示例性实施例。在下面的详细描述中,提出了许多具体细节,以便提供对本发明的全面理解。本发明实施例提供了一种磁分离系统的参数优化方法,该方法不需要调整磁分离系统中磁组件的布局参数去反复测试,仅仅通过理论模拟就能够得到目标吸附高度,明显地提高了工作效率。如图1所示,本发明实施例提供了一种磁分离系统的参数优化方法,该方法包括步骤101至步骤104。在步骤101中,根据磁分离系统的磁组件的布局参数和预设的磁颗粒运动模型,预测待磁分离系统清洗的反应杯中的各个磁颗粒的运动轨迹。其中,磁组件可以为磁铁,磁组件的布局参数包括磁铁形状、大小、放置位置和磁场强度中的至少一个。在步骤102中,根据各个磁颗粒的运动轨迹,确定各个磁颗粒运动至反应杯的目标面上的高度,高度为磁颗粒与反应杯的杯底之间的距离。具体地,如图2所示,在磁颗粒1被磁组件4捕获前,磁颗粒1在反应杯3中的基液2处于均匀分散的状态,在磁组件4开始工作后,磁颗粒1在磁组件4磁场的作用下开始运动,逐渐吸附至反应杯3的靠近磁组件4的杯壁一侧,形成磁颗粒团,即磁颗粒1被磁组件4捕获后的状态。在步骤103中,将各个磁颗粒1运动至反应杯3的目标面上的高度中的最大值作为磁分离系统的吸附高度。也就是说,吸附高度就是磁颗粒团中最靠上的磁颗粒1与反应杯3的杯底之间的距离。在步骤104中,若吸附高度大于与磁组件相配合使用的混匀组件带动反应杯3中混匀液旋转时所形成的旋转高度,则优化磁组件4的布局参数,重新得到优化后的吸附高度,直到优化后的吸附高度不大于旋转高度,其中,旋转高度为混匀液旋转时液面的最高点与反应杯3的杯底之间的距离。该方法可以根据所述磁分离系统的磁组件4的布局参数和预设的磁颗粒运动模型,预测得到在磁组件4特定的布局参数下的磁分离系统的吸附高度,并且在当吸附高度大于旋转高度时,优化磁组件4的布局参数,以及得到优化后的吸附高度,直到优化后的吸附高度不大于旋转高度。相比于现有技术,本发明实施例提供的参数优化方法不需要调整磁分离系统中磁组件4的布局参数去反复测试,仅仅通过理论模拟就能够得到磁分离系统的目标吸附高度,明显地提高了工作效率。为便于本领域技术人员理解,接下来对混匀组件的工作方式进行详细地说明。如图3所示,装有磁颗粒1和基液2的反应杯3进入磁分离系统进行清洗,磁颗粒1吸附在反应杯3的杯壁上,基液2被吸走,清洗后的反应杯3送到混匀组件,注入适量的混匀液,例如,加入100ul的混匀液。然后,如图4所示,混匀组件中的混匀电机5带动偏心头6高速旋转,偏心头6撞击以震荡位于混匀组件的反应杯托盘7上的反应杯3,使反应杯3中的混匀液将杯壁上的磁颗粒团冲刷下来,偏心头6的偏心距过小会使得反应杯3的震荡太弱,混匀液与磁颗粒1不能充分混匀,偏心头6的偏心距过大会使得反应杯3的震荡太强,会有混匀液溅出的风险。其中,混匀电机5的转速可达到4000r/min,偏心头6的结构如图5所示,偏心头6上设有偏心槽601,加入混匀液8后的反应杯3如图6所示。如图7所示,反应杯3中的混匀液8在偏心头6的碰撞和震荡下,混匀液8会沿杯壁旋转。同时,如图8所示,旋转的液面也会上升,从而冲刷杯壁上的磁颗粒团。由于加入的混匀液8的剂量有限,混匀形成的旋转高度是一定的,具体地,旋转高度由混匀组件中的混匀电机5的角速度,与混匀电机5连接的偏心头6的偏心距,反应杯3的大小,以及混匀液8的剂量决定。进一步地,为便于本领域技术人员理解上述旋转高度,接下来对旋转高度进行举例说明。示例性地,混匀液8的剂量为100ul,运用流体仿真技术,可以得到在偏心头6的不同偏心距和混匀电机5的不同角速度下,混匀液8的旋转高度,具体结果如表1所示。表1同时,图9给出了不同旋转高度的示意图,其中,图9a中的旋转高度h1为12mm,图9b中的旋转高度h2为15mm。在图9b所对应的混匀电机5的角速度和偏心头6的偏心距组合下,反应杯3的杯底出现空白,造成的原因是混匀电机5的角速度过大,即混匀电机5旋转过快,或者偏心头6的偏心距设计过大。因此,为了防止出现图9b的现象,偏心距可以设计为1.8-2.2㎜,混匀电机5的角速度可以在125.66r/s左右。为了确保来自磁分离系统的反应杯3的杯壁上的磁颗粒1能够被充分混匀,磁分离系统的吸附高度不能够超过12㎜,在一种更佳的实施方式中,磁分离系统的吸附高度控制在8-10㎜范围内。由上述分析可知,本发明实施例所提供的磁分离系统的参数优化方法可以预测在某种磁场下的磁分离系统的吸附高度,若吸附高度不符合混匀组件的混匀要求,则可以调整磁场分布,直到符合混匀要求。在另外一种可能的实施方式中,如图10所示,在预测待磁分离系统清洗的反应杯中的各个磁颗粒的运动轨迹的步骤之后,该方法还可以包括以下步骤:步骤201、根据各个磁颗粒的运动轨迹,预测各个磁颗粒1运动至反应杯3的目标面上的时间。步骤202、将各个磁颗粒1运动至反应杯3的目标面上的时间中的最大值作为磁分离系统的吸附时间。也就是说,磁分离系统的吸附时间为反应杯3中的磁颗粒1全部吸附至反应杯3的杯壁上的时间。步骤203、根据磁组件4的吸附时间,确定磁分离系统的时序设计的最小时间片段。若最小时间片段过短,那么磁组件4捕获磁颗粒1的时间不够,反应杯3内的磁颗粒1不能够全部吸附在反应杯3的侧壁上,有部分磁颗粒1会被清洗而造成丢失。若最小时间片段过长,虽然可以避免磁颗粒1清洗丢失,但是会造成磁分离系统的工作效率低下。通过本发明实施例的以上步骤,可以从理论上得到磁分离系统在磁组件4特定布局参数下的吸附时间,从而能够根据该吸附时间确定最合适的最小时间片段,同时避免磁颗粒1清洗丢失和工作效率低下的问题。此外,本领域技术人员也可以模拟多种磁组件布局参数下的吸附时间,得到多个吸附时间,然后选择其中的最小值作为最小时间片段的设计依据,从而进一步优化磁分离系统的最小时间片段,提高磁分离系统的通量和工作效率。为便于本领域技术人员具体实施前述预设的磁颗粒运动模型,下面对该模型进行详细地描述。反应杯3内包含基液2和磁颗粒1,磁组件4(例如,磁铁)在捕获磁颗粒1的过程中,如图11所示,磁颗粒1受到的合力如下:其中,为磁颗粒1受到的合力,为磁场力,为磁颗粒1的重力,为磁颗粒1的浮力,为粘性阻力。由于磁颗粒1的直径在0.5-5μm之间,可以忽略磁颗粒1的重力和浮力,因此,预设的磁颗粒运动模型由磁颗粒1在磁组件4的磁场环境受到的磁场力,以及磁颗粒1在反应杯3的基液2中运动时的粘性阻力确定,其中,粘性阻力包括摩擦阻力和形状阻力。由于粘性阻力同时考虑了两种阻力情况,模拟出来的结果会更加准确。在一种可能的实施方式中,磁颗粒运动模型的表达式为:磁场力的表达式为:粘性阻力的表达式为:其中,m为磁颗粒1的质量,为磁颗粒1的加速度,μ0为空间磁导率(h/m),δx为磁颗粒1与反应杯3中基液2的相对磁化系数,δx=χp-χf,χp为磁颗粒的磁化系数,χf为基液的磁化系数,vm为磁颗粒1的球体积(m3),b为空间位置的磁通密度(t),为空间位置的磁通密度的梯度(t/m),为摩擦阻力(n),为形状阻力(n),为无量纲摩擦阻力系数,为无量纲形状阻力系数,a为磁颗粒1的特征面积(m2),ρ为基液2的密度(kg/m3),v为磁颗粒1相对基液2的运动速度(m/s)。进一步地,将磁颗粒1的运动位移s(m),公式(3)和公式(4)带入上述磁颗粒运动模型的表达式(2)中,可以得到磁颗粒运动模型的微分形式表达式为:其中,x,y,z为磁颗粒1的三维空间坐标,ρ1为磁颗粒1的密度,d为磁颗粒1的直径,bx,by,bz分别为x,y,z三维空间坐标下的磁通密度分布,分别为x,y,z三维空间坐标下磁通密度的梯度,分别为x,y,z对时间的一阶导数,分别为x,y,z对时间的二阶导数。由于该微分形式表达式能够模拟磁微粒1在三维空间的运动轨迹,相比于只考虑单一方向的模拟方法,更加符合磁颗粒的实际运动情况。利用上述磁颗粒运动模型的微分表达式的初始条件为:x=a,y=b,z=c,计算得到三维空间坐标的加速度为:接下来,对三维空间坐标下磁通密度的分布和磁通密度的梯度的计算方法进行详细地说明。两块叠加的磁铁的空间磁场分布如图12所示,其中图12中所示的磁力线代表了空间位置的磁通密度b的分布,利用仿真软件可以得到空间离散点的磁通密度,以及对应的位置坐标,表2列举了部分空间区域的磁通密度。表2nodexyzbxbybz131.30e-021.60e-02-3.50e-033.39e-02-2.28e-03-2.13e-03142.00e-021.60e-02-3.50e-031.01e-02-2.01e-03-1.62e-03151.30e-020-3.50e-03-3.21e-022.10e-021.35e-03162.00e-020-3.50e-03-6.91e-03-7.22e-048.79e-04172.00e-021.60e-023.50e-039.82e-03-2.29e-031.41e-03182.00e-0203.50e-03-7.07e-03-5.53e-04-8.50e-04191.30e-021.60e-023.50e-033.35e-02-1.73e-032.09e-03201.30e-0203.50e-03-3.06e-022.23e-02-1.34e-03641.30e-023.75e-04-3.50e-03-3.47e-021.78e-021.61e-03651.30e-027.50e-04-3.50e-03-3.70e-021.31e-021.80e-03661.30e-021.13e-03-3.50e-03-3.82e-028.77e-031.80e-03671.30e-021.50e-03-3.50e-03-3.98e-024.40e-031.85e-03681.30e-021.90e-03-3.50e-03-3.96e-023.67e-041.47e-03691.30e-022.30e-03-3.50e-03-3.98e-02-3.00e-031.44e-03701.30e-022.70e-03-3.50e-03-3.97e-02-6.26e-031.37e-03712.00e-021.11e-03-3.50e-03-7.00e-03-2.18e-037.81e-04722.00e-022.23e-03-3.50e-03-6.84e-03-3.68e-036.80e-04732.00e-021.11e-033.50e-03-7.21e-03-1.93e-03-8.04e-04742.00e-022.23e-033.50e-03-7.16e-03-3.39e-03-7.47e-04…………………磁通密度的梯度的计算方法如下所示:为了便于本领域技术人员具体实施,本发明实施例还提供了上述磁颗粒运动模型的数值解法,下面对该数值解法进行详细地说明。如图13所示,以磁铁捕获磁颗粒1为例,位于两块磁铁叠加线的水平方向,且距离目标面8㎜的磁颗粒1在磁场力和粘性阻力的作用下开始运动。编写求解上述磁颗粒运动模型的微分形式表达式的数值解的算法,计算得到磁颗粒1的运动位移s与时间t之间的关系。以求解x轴的分量为例,如图14所示,数值解法的步骤如下:步骤s301、利用有限差分法对磁颗粒运动模型的微分表达式(5)、(6)和(7)进行处理,磁颗粒运动模型的微分表达式(5)、(6)和(7)经过有限差分法处理后的数值表达式为:其中,i=1,2,3,…。步骤s302、确定磁颗粒1的初始条件,磁颗粒1的初始条件包括磁颗粒1的初始位置坐标和初始加速度,其中,初始位置坐标为(x0,y0,z0),初始加速度为:步骤s303、设置数值表达式的时间增量δt,在一种更优的实施方式中,为了保证算法的精度和计算效率,取δt=1e-6。步骤s304、计算磁通密度b,利用仿真软件模拟磁场的分布,导出磁铁的空间离散点的磁通密度。步骤s305、计算磁通密度的梯度以i为原点建立局部坐标系,磁通密度的梯度可以根据与位置xi、yi、zi空间距离最近的磁场节点的磁通密度计算得到。针对三维空间中的每一位置(xi、yi、zi),利用距离该位置最近的磁场节点的磁通密度计算该位置的磁通密度的梯度,能够针对该位置获得最优地磁通密度的梯度,从而提高模拟结果的准确性。步骤s306、计算磁颗粒1的运动方向,磁颗粒1在不均匀的磁场中运动时,磁颗粒1的加速度方向与磁通密度的最大梯度一致,磁颗粒1在i处时,坐标为(xi,yi,zi),速度为加速度为根据加速度的矢量合成磁颗粒1的下一刻运动的方向。步骤s307、对磁颗粒1运动位置和磁场节点进行耦合,步骤s306计算了磁颗粒1的运动方向,将时间增量δt,位置i的速度和加速度带入磁颗粒运动模型的数值表达式(14)、(15)和(16)中,可以计算得到磁颗粒1沿加速度方向运动到位置(i+1)处的位移增量为δs,此时位置(i+1)与磁场节点不重合,运用最小距离法让位置(i+1)与距其最近的磁场节点耦合,计算下一时刻的位移与方向。步骤s308、设定算法的求解时间和边界条件,例如,可以设置算法允许计算的最长时间为不大于50s,设置磁颗粒1运动到磁场的边界位置时停止计算,此时可以看作磁颗粒1运动到了反应杯3壁处。步骤s309、计算求解轨迹,绘制磁颗粒1运动的三维轨迹,绘制轨迹与运动时间的曲线,根据轨迹曲线能预测磁颗粒1运动到目标面的时间、磁颗粒1吸附在目标面的高度是否高于混匀限定液面,直到设计合理的磁场分布。现对本发明实施例所提供的磁分离系统的参数优化方法的有益效果做如下的总结:通过分析磁颗粒1的运动轨迹和时间,能指导磁分离系统中磁铁的设计,能合理的设计仪器通量。由于抗原、抗体反应物与磁颗粒1结合,磁颗粒1结合物在磁分离系统中被磁铁捕获,通过磁分离系统的注液、洗液组件将多余的结合物清洗掉,形成不含液体的吸附在反应杯3壁面上的干磁颗粒团。干磁颗粒团再进入下一步时序,加入第二种反应溶液,在混匀组件作用下充分混匀反应溶液与干磁颗粒团,使其充分反应。在此过程中,磁铁对磁颗粒1的捕获形态,会影响磁颗粒1与第二种反应溶液的混匀充分的程度,甚至出现干磁颗粒团残留在反应杯3壁上的未混均匀现象。此现象主要是磁铁捕获磁颗粒1时,磁颗粒1朝向磁铁的磁通密度b的最大梯度方向运动(磁铁的磁通密度b的最大梯度在磁铁的棱角位置和叠加线位置处),在目标面上靠近磁铁棱角和叠加线的不同位置形成干磁颗粒的团聚(如图15所示),混匀组件即使让混匀液8的液面达到最大高度也不能将干磁颗粒团拖拽下来,出现了混匀后干磁颗粒团残留在反应杯3壁上的未混匀现象。本发明实施例所提供的磁分离系统的参数优化方法能够分析反应杯3基液2中的磁颗粒1在磁场和流体耦合作用下的运动轨迹,可以预先了解磁颗粒1在设计的磁铁的磁场作用下运动的朝向,指导磁铁设计直至得到想要的磁颗粒1吸附形状和高度,如下图16所示。此外,该参数优化方法还可得到磁颗粒1的运动时间t,可以作为磁分离系统时序设计的依据。磁分离系统中磁铁充分捕获磁颗粒1的时间t作为磁分离系统时序设计的最小时间片段,可以最大化地提高仪器运行通量。依据磁分离系统中磁铁充分捕获磁颗粒1的时间t,可以设计磁分离系统清洗组件的动作时序,在磁颗粒1被充分捕获后,清洗反应杯3内的多余的复合物,使磁颗粒1的丢失率降到最低,仪器的检测结果更稳定。如图17所示,本发明一实施例还提供了一种磁分离系统的参数优化装置,该装置包括:预测模块9、磁颗粒运动高度计算模块10、吸附高度计算模块11和磁组件优化模块12。其中,预测模块9根据磁分离系统的磁组件的布局参数和预设的磁颗粒运动模型,预测待磁分离系统清洗的反应杯中的各个磁颗粒的运动轨迹。磁颗粒运动高度计算模块10根据各个磁颗粒的运动轨迹,确定各个磁颗粒运动至反应杯的目标面上的高度,高度为磁颗粒与反应杯的杯底之间的距离。吸附高度计算模块11将各个磁颗粒运动至反应杯的目标面上的高度中的最大值作为磁组件的吸附高度。磁组件优化模块12若吸附高度大于与磁组件相配合使用的混匀组件带动反应杯中混匀液旋转时所形成的旋转高度,则优化磁组件的布局参数,重新得到优化后的吸附高度,直到优化后的吸附高度不大于旋转高度,其中,旋转高度为混匀液旋转时液面的最高点与反应杯的杯底之间的距离。由此可知,该装置可以通过预测模块9对磁颗粒运动的理论分析,预测待磁分离系统清洗的反应杯中的各个磁颗粒的运动轨迹,再通过磁颗粒运动高度计算模块10根据各个磁颗粒的运动轨迹,确定各个磁颗粒运动至反应杯的目标面上的高度,接着通过吸附高度计算模块11就能够得到在磁组件特定的布局参数下的吸附高度,当吸附高度大于与磁组件相配合使用的混匀组件带动反应杯中混匀液旋转时所形成的旋转高度时,通过优化模块12可以优化磁组件的布局参数,经过理论模拟后重新得到优化后的吸附高度,直到优化后的吸附高度不大于旋转高度。相比于现有技术,本发明实施中的磁分离系统的参数优化装置不需要调整磁分离系统中磁组件的布局参数去反复测试,仅仅通过理论模拟,就能够得到磁分离系统的吸附高度,明显地提高了工作效率。如图18所示,本发明另一实施例还提供了一种磁分离系统的参数优化装置,图18与图17的不同之处在于,图18中示出的磁分离系统的参数优化装置还包括:磁颗粒运动时间计算模块13、吸附时间计算模块14和最小时间片段优化模块15。其中,磁颗粒运动时间计算模块13用于根据各个磁颗粒的运动轨迹,预测各个磁颗粒运动至反应杯的目标面上的时间。吸附时间计算模块14用于将各个磁颗粒运动至反应杯的目标面上的时间中的最大值作为磁分离系统的吸附时间。最小时间片段优化模块15用于根据磁分离系统的吸附时间,确定磁分离系统的时序设计的最小时间片段。通过该实施例可以从理论上得到磁分离系统在磁组件特定布局参数下的吸附时间,从而能够根据该吸附时间确定最合适的最小时间片段,同时避免磁颗粒清洗丢失和工作效率低下的问题。本发明实施例还提供了一种分析仪器,该仪器包括:磁分离系统以及如上所述的磁分离系统的参数优化装置。本发明实施例还提供了一种存储介质,其上存储有程序,程序被处理器执行时实现如上所述的磁分离系统的参数优化方法。“计算机可读存储介质”可以包括能够存储或传输信息的任何介质。机器可读介质的例子包括电子电路、半导体存储器设备、rom、闪存、可擦除rom(erom)、软盘、cd-rom、光盘、硬盘、光纤介质、射频(rf)链路,等等。代码段可以经由诸如因特网、内联网等的计算机网络被下载。需要明确的是,本说明书中的各个实施例均采用递进的方式描述,各个实施例之间相同或相似的部分互相参见即可,每个实施例重点说明的都是与其他实施例的不同之处。对于装置实施例而言,相关之处可以参见方法实施例的说明部分。本发明实施例并不局限于上文所描述并在图中示出的特定步骤和结构。本领域的技术人员可以在领会本发明实施例的精神之后,做出各种改变、修改和添加,或者改变步骤之间的顺序。并且,为了简明起见,这里省略对已知方法技术的详细描述。以上所述的结构框图中所示的功能块可以实现为硬件、软件、固件或者它们的组合。当以硬件方式实现时,其可以例如是电子电路、专用集成电路(asic)、适当的固件、插件、功能卡等等。当以软件方式实现时,本发明实施例的元素是被用于执行所需任务的程序或者代码段。程序或者代码段可以存储在机器可读介质中,或者通过载波中携带的数据信号在传输介质或者通信链路上传送。“机器可读介质”可以包括能够存储或传输信息的任何介质。机器可读介质的例子包括电子电路、半导体存储器设备、rom、闪存、可擦除rom(erom)、软盘、cd-rom、光盘、硬盘、光纤介质、射频(rf)链路,等等。代码段可以经由诸如因特网、内联网等的计算机网络被下载。本发明实施例可以以其他的具体形式实现,而不脱离其精神和本质特征。例如,特定实施例中所描述的算法可以被修改,而系统体系结构并不脱离本发明实施例的基本精神。因此,当前的实施例在所有方面都被看作是示例性的而非限定性的,本发明实施例的范围由所附权利要求而非上述描述定义,并且,落入权利要求的含义和等同物的范围内的全部改变从而都被包括在本发明实施例的范围之中。当前第1页12