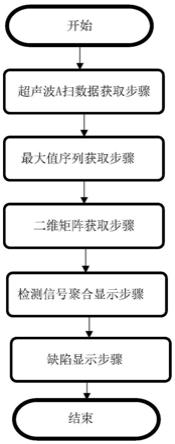
1.本发明涉及数字处理领域,具体地,涉及一种适用于轧辊的超声波检测信号聚合显示方法及系统,尤其涉及一种轧辊超声波检测信号聚合及显示方法。
背景技术:2.在轧辊超声波检测中,用户非常希望了解轧辊缺陷深层次的缺陷信息,包括缺陷在深度和强度方面的分布,同时还需要知道缺陷在轧辊轴向上的位置分布。但现有的信号处理方法无法完全聚合一根轧辊上的所有缺陷,也无法同时显示缺陷在深度和强度方面的分布以及缺陷在轧辊轴向上的位置分布。
3.专利文献cn101949896b公开了一种轧辊超声波检测装置,包括探头控制箱、下位机和上位机,其特征在于:还包括超声波探头组件;所述探头控制箱与下位机双向通讯,其根据所述下位机的指示控制所述探头组件的机械运动与定位,并控制所述探头组件中的各超声波传感器依次发射超声波脉冲信号,同时接收所述各超声波传感器的各个通道的回波信号,并按时间序列将所述回波信号送往所述下位机;所述下位机将其接收到的所述回波信号进行检波和采样处理后转变为视频信号送至所述上位机中显示。该专利在轧辊缺陷深层次的缺陷信息聚合显示上仍有待提升的空间。
技术实现要素:4.针对现有技术中的缺陷,本发明的目的是提供一种适用于轧辊的超声波检测信号聚合显示方法及系统。
5.根据本发明提供的一种适用于轧辊的超声波检测信号聚合显示方法,包括:超声波a扫数据获取步骤:采集目标结构上设定位置的超声波a扫数据,获取按时间采样序列值信息;最大值序列获取步骤:根据按时间采样序列值信息,获取时间采样最大值序列信息;二维矩阵获取步骤:根据时间采样最大值序列信息,获取时间采样最大值序列二维矩阵信息;检测信号聚合显示步骤:根据时间采样最大值序列二维矩阵信息,获取检测信号聚合显示结果信息;缺陷显示步骤:根据检测信号聚合显示结果信息,获取缺陷位置分布信息;所述缺陷位置分布信息指导缺陷在目标结构上的位置分布状态。
6.优选地,所述缺陷显示步骤包括:缺陷深度分布显示步骤:根据检测信号聚合显示结果信息,获取缺陷深度分布信息;缺陷强度分布显示步骤:根据检测信号聚合显示结果信息,获取缺陷强度分布信息;所述缺陷深度分布信息指导缺陷在目标结构上的深度分布状态;所述缺陷强度分布信息指导缺陷在目标结构上的强度分布状态。
7.优选地,所述超声波a扫数据获取步骤包括:超声波a扫数据获取子步骤:取得轧辊在轴向上第1个位置的所有周向超声波a扫数据a1、a2、a3
……
am,即轧辊在轴向上第1个位置一共拥有m个周向超声波a扫数据,其中a1是由a1a1、a1a2、a1a3、a1a4
……
a1an组成的按时间采样序列值,a2是由a2a1、a2a2、a2a3、a2a4
……
a2an组成的按时间采样序列值,a3是由a3a1、a3a2、a3a3、a3a4
……
a3an组成的按时间采样序列值,am是由ama1、ama2、ama3、
ama4
……
aman组成的按时间采样序列值,在a1、a2、a3
……
am中,均具有n个按时间采样序列值,m、n为正整数;所述最大值序列获取步骤包括:最大值序列获取子步骤:将a1a1、a2a1、a3a1
……
ama1作为一个集合,取得其中的最大值,记为aa1;将a1a2、a2a2、a3a2
……
ama2作为一个集合,取得其中的最大值,记为aa2,以此类推,取得aa3、aa4、aa5、aa6
……
aan;将aa1、aa2、aa3、aa4、aa5、aa6
……
aan记为轧辊在轴向上第1个位置p1的周向超声波a扫数据的时间采样最大值序列p1a。
8.优选地,所述二维矩阵获取步骤包括:二维矩阵获取子步骤:获取轧辊在轴向上第2个位置、第3个位置
……
第k个位置所对应的序列p2a、p3a
……
pka;p1a、p2a、p3a
……
pka即构成一个二维矩阵;所述检测信号聚合显示步骤包括:检测信号聚合显示子步骤:将p1a、p2a、p3a
……
pka这个二维矩阵上的点用亮度梯度或者颜色梯度显示出来,获取检测信号聚合显示结果信息;所述检测信号聚合显示结果信息将轧辊的超声波a扫数据按照轴向位置全部聚合在一个二维平面上。
9.优选地,还包括:缺陷统计图表获取步骤:根据缺陷位置分布信息、缺陷深度分布信息以及缺陷强度度分布信息,获取缺陷统计图表信息。
10.根据本发明提供的一种适用于轧辊的超声波检测信号聚合显示系统,包括:超声波a扫数据获取模块:采集目标结构上设定位置的超声波a扫数据,获取按时间采样序列值信息;最大值序列获取模块:根据按时间采样序列值信息,获取时间采样最大值序列信息;二维矩阵获取模块:根据时间采样最大值序列信息,获取时间采样最大值序列二维矩阵信息;检测信号聚合显示模块:根据时间采样最大值序列二维矩阵信息,获取检测信号聚合显示结果信息;缺陷显示模块:根据检测信号聚合显示结果信息,获取缺陷位置分布信息;所述缺陷位置分布信息指导缺陷在目标结构上的位置分布状态。
11.优选地,所述缺陷显示模块包括:缺陷深度分布显示模块:根据检测信号聚合显示结果信息,获取缺陷深度分布信息;缺陷强度分布显示模块:根据检测信号聚合显示结果信息,获取缺陷强度分布信息;所述缺陷深度分布信息指导缺陷在目标结构上的深度分布状态;所述缺陷强度分布信息指导缺陷在目标结构上的强度分布状态。
12.优选地,所述超声波a扫数据获取模块包括:超声波a扫数据获取子模块:取得轧辊在轴向上第1个位置的所有周向超声波a扫数据a1、a2、a3
……
am,即轧辊在轴向上第1个位置一共拥有m个周向超声波a扫数据,其中a1是由a1a1、a1a2、a1a3、a1a4
……
a1an组成的按时间采样序列值,a2是由a2a1、a2a2、a2a3、a2a4
……
a2an组成的按时间采样序列值,a3是由a3a1、a3a2、a3a3、a3a4
……
a3an组成的按时间采样序列值,am是由ama1、ama2、ama3、ama4
……
aman组成的按时间采样序列值,在a1、a2、a3
……
am中,均具有n个按时间采样序列值,m、n为正整数;所述最大值序列获取模块包括:最大值序列获取子模块:将a1a1、a2a1、a3a1
……
ama1作为一个集合,取得其中的最大值,记为aa1;将a1a2、a2a2、a3a2
……
ama2作为一个集合,取得其中的最大值,记为aa2,以此类推,取得aa3、aa4、aa5、aa6
……
aan;将aa1、aa2、aa3、aa4、aa5、aa6
……
aan记为轧辊在轴向上第1个位置p1的周向超声波a扫数据的时间采样最大值序列p1a。
13.优选地,所述二维矩阵获取模块包括:二维矩阵获取子模块:获取轧辊在轴向上第2个位置、第3个位置
……
第k个位置所对应的序列p2a、p3a
……
pka;p1a、p2a、p3a
……
pka即构成一个二维矩阵;所述检测信号聚合显示模块包括:检测信号聚合显示子模块:将p1a、
p2a、p3a
……
pka这个二维矩阵上的点用亮度梯度或者颜色梯度显示出来,获取检测信号聚合显示结果信息;所述检测信号聚合显示结果信息将轧辊的超声波a扫数据按照轴向位置全部聚合在一个二维平面上。
14.优选地,还包括:缺陷统计图表获取模块:根据缺陷位置分布信息、缺陷深度分布信息以及缺陷强度度分布信息,获取缺陷统计图表信息。
15.与现有技术相比,本发明具有如下的有益效果:
16.1、本发明能够满足了用户判断轧辊内部缺陷的需求,使用本发明,用户可以清楚直观的判断缺陷的埋深、大小及检测工艺细微特征。解决了传统方法无法处理和显示过渡层扩散裂纹等缺陷的问题;
17.2、本发明能够在轴向上显示缺陷的位置,使用本发明可以显示缺陷在轴向上的位置,在复核缺陷时可以快速的定位;
18.3、本发明能够避免漏检,使用本发明,在数值处理中采用了最大值保留方法,最终显示结果中保留了所有最大值缺陷信息,不会造成漏检。
附图说明
19.通过阅读参照以下附图对非限制性实施例所作的详细描述,本发明的其它特征、目的和优点将会变得更明显:
20.图1为本发明的方法流程示意图。
21.图2为本发明的系统框架示意图。
具体实施方式
22.下面结合具体实施例对本发明进行详细说明。以下实施例将有助于本领域的技术人员进一步理解本发明,但不以任何形式限制本发明。应当指出的是,对本领域的普通技术人员来说,在不脱离本发明构思的前提下,还可以做出若干变化和改进。这些都属于本发明的保护范围。
23.如图1、图2所示,根据本发明提供的一种适用于轧辊的超声波检测信号聚合显示方法,包括:超声波a扫数据获取步骤:采集目标结构上设定位置的超声波a扫数据,获取按时间采样序列值信息;最大值序列获取步骤:根据按时间采样序列值信息,获取时间采样最大值序列信息;二维矩阵获取步骤:根据时间采样最大值序列信息,获取时间采样最大值序列二维矩阵信息;检测信号聚合显示步骤:根据时间采样最大值序列二维矩阵信息,获取检测信号聚合显示结果信息;缺陷显示步骤:根据检测信号聚合显示结果信息,获取缺陷位置分布信息;所述缺陷位置分布信息指导缺陷在目标结构上的位置分布状态。
24.优选地,所述缺陷显示步骤包括:缺陷深度分布显示步骤:根据检测信号聚合显示结果信息,获取缺陷深度分布信息;缺陷强度分布显示步骤:根据检测信号聚合显示结果信息,获取缺陷强度分布信息;所述缺陷深度分布信息指导缺陷在目标结构上的深度分布状态;所述缺陷强度分布信息指导缺陷在目标结构上的强度分布状态。
25.优选地,所述超声波a扫数据获取步骤包括:超声波a扫数据获取子步骤:取得轧辊在轴向上第1个位置的所有周向超声波a扫数据a1、a2、a3
……
am,即轧辊在轴向上第1个位置一共拥有m个周向超声波a扫数据,其中a1是由a1a1、a1a2、a1a3、a1a4
……
a1an组成的按
时间采样序列值,a2是由a2a1、a2a2、a2a3、a2a4
……
a2an组成的按时间采样序列值,a3是由a3a1、a3a2、a3a3、a3a4
……
a3an组成的按时间采样序列值,am是由ama1、ama2、ama3、ama4
……
aman组成的按时间采样序列值,在a1、a2、a3
……
am中,均具有n个按时间采样序列值,m、n为正整数;所述最大值序列获取步骤包括:最大值序列获取子步骤:将a1a1、a2a1、a3a1
……
ama1作为一个集合,取得其中的最大值,记为aa1;将a1a2、a2a2、a3a2
……
ama2作为一个集合,取得其中的最大值,记为aa2,以此类推,取得aa3、aa4、aa5、aa6
……
aan;将aa1、aa2、aa3、aa4、aa5、aa6
……
aan记为轧辊在轴向上第1个位置p1的周向超声波a扫数据的时间采样最大值序列p1a。
26.优选地,所述二维矩阵获取步骤包括:二维矩阵获取子步骤:获取轧辊在轴向上第2个位置、第3个位置
……
第k个位置所对应的序列p2a、p3a
……
pka;p1a、p2a、p3a
……
pka即构成一个二维矩阵;所述检测信号聚合显示步骤包括:检测信号聚合显示子步骤:将p1a、p2a、p3a
……
pka这个二维矩阵上的点用亮度梯度或者颜色梯度显示出来,获取检测信号聚合显示结果信息;所述检测信号聚合显示结果信息将轧辊的超声波a扫数据按照轴向位置全部聚合在一个二维平面上。
27.优选地,还包括:缺陷统计图表获取步骤:根据缺陷位置分布信息、缺陷深度分布信息以及缺陷强度度分布信息,获取缺陷统计图表信息。
28.具体地,在一个实施例中,一种适用于轧辊的超声波检测信号聚合显示方法包括:
29.步骤1、取得轧辊在轴向上第1个位置的所有周向超声波a扫数据a1、a2、a3
……
am,即轧辊在轴向上第1个位置一共拥有m(m为正整数)个周向超声波a扫数据。其中a1是由[a1a1、a1a2、a1a3、a1a4
……
a1an]组成的按时间采样序列值,a2是由[a2a1、a2a2、a2a3、a2a4
……
a2an]组成的按时间采样序列值。即在a1、a2、a3
……
am中,均具有n(n为正整数)个按时间采样序列值;
[0030]
步骤2、将a1a1、a2a1、a3a1
……
ama1作为一个集合,取得其中的最大值,记为aa1;将a1a2、a2a2、a3a2
……
ama2作为一个集合,取得其中的最大值,记为aa2;以此类推,取得aa3、aa4、aa5、aa6
……
aan;
[0031]
步骤3、将[aa1、aa2、aa3、aa4、aa5、aa6
……
aan]记为轧辊在轴向上第1个位置(p1)的周向超声波a扫数据的时间采样最大值序列p1a;
[0032]
步骤4、重复步骤1~步骤3,得到轧辊在轴向上第2个位置、第3个位置
……
第k个位置所对应的序列p2a、p3a
……
pka;p1a、p2a、p3a
……
pka即构成一个二维矩阵。
[0033]
步骤5、将[p1a、p2a、p3a
……
pka]这个二维矩阵上的点用亮度或者颜色梯度显示出来,就成为一张显示图。这张图将一根轧辊的超声波a扫数据按照轴向位置全部聚合在一个二维平面上,并同时显示缺陷在深度和强度方面的分布以及缺陷在轧辊轴向上的位置分布。
[0034]
本领域技术人员可以将本发明提供的适用于轧辊的超声波检测信号聚合显示方法,理解为本发明提供的适用于轧辊的超声波检测信号聚合显示系统的一个实施例。即,所述适用于轧辊的超声波检测信号聚合显示系统可以通过执行所述适用于轧辊的超声波检测信号聚合显示方法的步骤流程实现。
[0035]
根据本发明提供的一种适用于轧辊的超声波检测信号聚合显示系统,包括:超声波a扫数据获取模块:采集目标结构上设定位置的超声波a扫数据,获取按时间采样序列值
信息;最大值序列获取模块:根据按时间采样序列值信息,获取时间采样最大值序列信息;二维矩阵获取模块:根据时间采样最大值序列信息,获取时间采样最大值序列二维矩阵信息;检测信号聚合显示模块:根据时间采样最大值序列二维矩阵信息,获取检测信号聚合显示结果信息;缺陷显示模块:根据检测信号聚合显示结果信息,获取缺陷位置分布信息;所述缺陷位置分布信息指导缺陷在目标结构上的位置分布状态。
[0036]
优选地,所述缺陷显示模块包括:缺陷深度分布显示模块:根据检测信号聚合显示结果信息,获取缺陷深度分布信息;缺陷强度分布显示模块:根据检测信号聚合显示结果信息,获取缺陷强度分布信息;所述缺陷深度分布信息指导缺陷在目标结构上的深度分布状态;所述缺陷强度分布信息指导缺陷在目标结构上的强度分布状态。
[0037]
优选地,所述超声波a扫数据获取模块包括:超声波a扫数据获取子模块:取得轧辊在轴向上第1个位置的所有周向超声波a扫数据a1、a2、a3
……
am,即轧辊在轴向上第1个位置一共拥有m个周向超声波a扫数据,其中a1是由a1a1、a1a2、a1a3、a1a4
……
a1an组成的按时间采样序列值,a2是由a2a1、a2a2、a2a3、a2a4
……
a2an组成的按时间采样序列值,a3是由a3a1、a3a2、a3a3、a3a4
……
a3an组成的按时间采样序列值,am是由ama1、ama2、ama3、ama4
……
aman组成的按时间采样序列值,在a1、a2、a3
……
am中,均具有n个按时间采样序列值,m、n为正整数;所述最大值序列获取模块包括:最大值序列获取子模块:将a1a1、a2a1、a3a1
……
ama1作为一个集合,取得其中的最大值,记为aa1;将a1a2、a2a2、a3a2
……
ama2作为一个集合,取得其中的最大值,记为aa2,以此类推,取得aa3、aa4、aa5、aa6
……
aan;将aa1、aa2、aa3、aa4、aa5、aa6
……
aan记为轧辊在轴向上第1个位置p1的周向超声波a扫数据的时间采样最大值序列p1a。
[0038]
优选地,所述二维矩阵获取模块包括:二维矩阵获取子模块:获取轧辊在轴向上第2个位置、第3个位置
……
第k个位置所对应的序列p2a、p3a
……
pka;p1a、p2a、p3a
……
pka即构成一个二维矩阵;所述检测信号聚合显示模块包括:检测信号聚合显示子模块:将p1a、p2a、p3a
……
pka这个二维矩阵上的点用亮度梯度或者颜色梯度显示出来,获取检测信号聚合显示结果信息;所述检测信号聚合显示结果信息将轧辊的超声波a扫数据按照轴向位置全部聚合在一个二维平面上。
[0039]
优选地,还包括:缺陷统计图表获取模块:根据缺陷位置分布信息、缺陷深度分布信息以及缺陷强度度分布信息,获取缺陷统计图表信息。
[0040]
使用本发明的设备可以使用户不漏检地清楚直观的判断缺陷的埋深、大小及检测工艺细微特征。解决了传统方法无法处理和显示过渡层扩散裂纹等缺陷的问题。减少爆辊事故,同时减少轧辊辊耗,具有有较高的应用价值。本发明可以在其它圆柱或圆管工件的超声检测中推广应用。
[0041]
本发明能够满足了用户判断轧辊内部缺陷的需求,使用本发明,用户可以清楚直观的判断缺陷的埋深、大小及检测工艺细微特征。解决了传统方法无法处理和显示过渡层扩散裂纹等缺陷的问题;本发明能够在轴向上显示缺陷的位置,使用本发明可以显示缺陷在轴向上的位置,在复核缺陷时可以快速的定位;本发明能够避免漏检,使用本发明,在数值处理中采用了最大值保留方法,最终显示结果中保留了所有最大值缺陷信息,不会造成漏检。
[0042]
本领域技术人员知道,除了以纯计算机可读程序代码方式实现本发明提供的系统
及其各个装置、模块、单元以外,完全可以通过将方法模块进行逻辑编程来使得本发明提供的系统及其各个装置、模块、单元以逻辑门、开关、专用集成电路、可编程逻辑控制器以及嵌入式微控制器等的形式来实现相同功能。所以,本发明提供的系统及其各项装置、模块、单元可以被认为是一种硬件部件,而对其内包括的用于实现各种功能的装置、模块、单元也可以视为硬件部件内的结构;也可以将用于实现各种功能的装置、模块、单元视为既可以是实现方法的软件模块又可以是硬件部件内的结构。
[0043]
以上对本发明的具体实施例进行了描述。需要理解的是,本发明并不局限于上述特定实施方式,本领域技术人员可以在权利要求的范围内做出各种变化或修改,这并不影响本发明的实质内容。在不冲突的情况下,本申请的实施例和实施例中的特征可以任意相互组合。