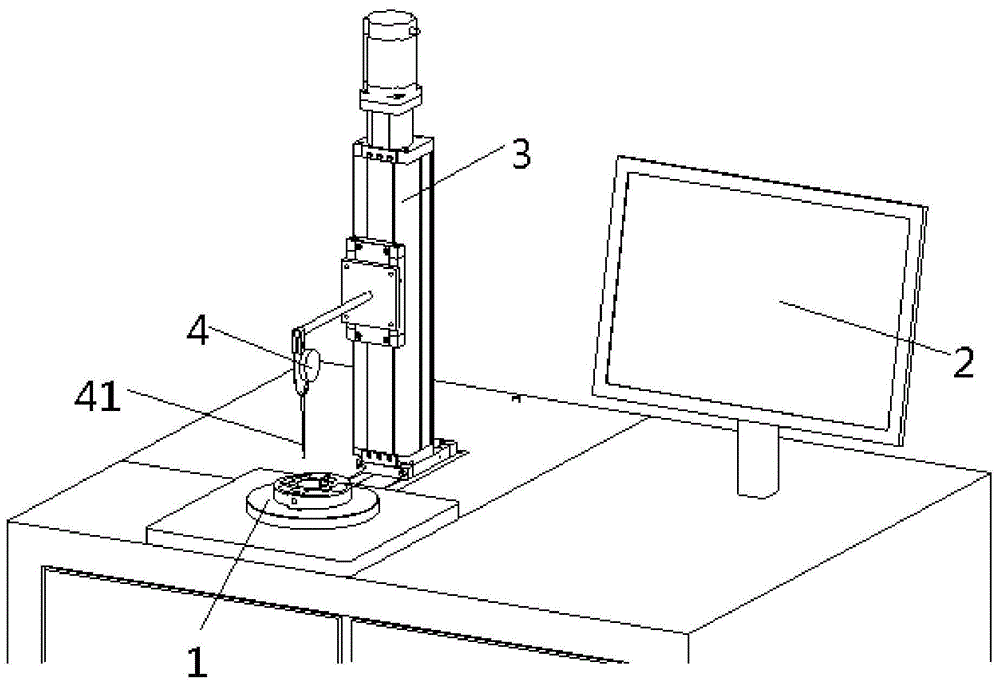
本发明属于转子压缩机检测领域,具体涉及一种用于气缸滑片槽的综合检测装置及方法。
背景技术:
:随着工业技术的发展,对生产过程中的工件精度要求越来越高,制造商需要对生产的工件质量进行检测,以保证机械装置整体的精度要求。目前,传统的气缸滑片槽宽度、平行度和垂直度的主要检测方法是气动量仪和气电测微仪,使用气动量仪检测时,气缸滑片槽宽、平行度和垂直度分别在两个测台上检测;气缸滑片槽偏差值检测方法主要是万工显,万工显对环境要求和测量人员的测量技术要求较高,不适合放在生产线上测量,不利于提高生产线的检测速度。技术实现要素:本发明的目的在于提供一种用于气缸滑片槽的综合检测装置及方法,以解决现有技术中,气缸滑片槽宽度、平行度和垂直度分别在两个测台上检测检测方式繁琐,气缸滑片槽偏差值检测方法对环境要求和测量人员的测量技术要求高的问题。为实现上述目的,本发明采用如下技术方案:一种用于气缸滑片槽的综合检测装置,包括定位模块、操作显示模块、执行机构和千分表;所述定位模块用于定位待检测的气缸滑片槽;所述千分表安装在所述执行机构上,千分表的测量端安装有测头,所述测头用于与气缸滑片槽抵接并测量气缸滑片槽上的点值;所述执行机构用于驱动所述千分表分别在x、y、z三轴方向上移动;所述操作显示模块分别与所述执行机构及千分表电连接,用于控制执行机构的启动、复位、和急停,以及显示测量结果。具体的,所述的定位模块包括,用于定位气缸滑片槽的定位花盘,及用于定位不同型号定位花盘的定位板,所述定位花盘通过定位销安装在所述定位板上。具体的,所述执行机构包括用于驱动所述千分表接近待检测气缸滑片槽、向待检测气缸滑片槽的深度方向移动的z轴带步进电机线轨、用于驱动千分表与气缸滑片槽抵接的x轴带步进电机线轨和用于驱动所述千分表沿气缸滑片槽的长度方向移动的y轴带步进电机线轨;所述千分表通过千分表安装座安装在z轴带步进电机线轨上,所述z轴带步进电机线轨滑动连接在x轴带步进电机线轨上,x轴带步进电机线轨滑动连接在y轴带步进电机线轨上。进一步的,所述测头采用探针球形测头。进一步的,所述千分表测针的测头直径比测针直径大0.2mm。进一步的,所述的千分表为具备数据传输功能的数显千分表,能够直接将测量的数值传输给操作显示模块。本发明的另一个技术方案是,一种气缸滑片槽的综合检测方法,利用所述的综合检测装置,用于测量气缸滑片槽宽度、平行度、垂直度和气缸滑片槽偏差值,具体步骤如下:s1、操作显示模块控制所述千分表的测头下降至零点位置,伸入待测气缸滑片槽;s2、所述千分表的测头在气缸滑片槽内分别沿x、y、z三轴方向上运动,在x轴上运动距离定义为dx,在y轴上运动距离定义为dy、在z轴上运动距离定义为dz,测得气缸滑片槽两个平面上共8个点的千分表读数:a1、a2、a3、a4、a5、a6、a7和a8;s3:所述千分表的测头在气缸滑片槽内运动,测完s2所述8个点后,在滑片槽左侧面设定位置测得一个点的千分表读数:a9;s4:操作显示模块自动计算气缸滑片槽宽度、平行度、垂直度和气缸滑片槽偏差值,并输出计算结果,计算公式如下:(1)槽宽w=max(w1,w2,w3,w4),w1=2dx-(abs(a1)+abs(a2)),w2=2dx-(abs(a3)+abs(a4)),w3=2dx-(abs(a5)+abs(a6)),w4=2dx-(abs(a7)+abs(a8));(2)平行度=max(w1,w2,w3,w4)-min(w1,w2,w3,w4),w1=2dx-(abs(a1)+abs(a2)),w2=2dx-(abs(a3)+abs(a4)),w3=2dx-(abs(a5)+abs(a6)),w4=2dx-(abs(a7)+abs(a8));(3)垂直度v=max(v1,v2,v3,v4),v1=abs(a1-a4),v2=abs(a2-a3),v3=abs(a6-a7),v4=abs(a5-a8);(4)槽偏差值α的计算方式如下:先计算定位点中心到滑片槽中心线的垂直距离d,d={24-(dx-千分表读数3)-槽宽/2cosγ}*cosγ,当d满足23.95≤d≤24.05时,计算槽偏差值α值;根据不同d值,利用不同关系式计算出α值,计算公式如下:d=23.95时,若a4-a5>0,则α=36.38γ4-28.57γ3+7.849γ2+0.786γ-0.099,若a4-a5<0,则α=-22505γ6+49594γ5-22216γ4+3758γ3-241.3γ2+5.213γ+0.117;d=23.96时,若a4-a5>0,则α=-0.312γ3+0.198γ2+1.671γ-0.109,若a4-a5<0,则α=-45256γ6+32043γ5-85188γ4+10381γ3-555.7γ2+11.61γ+0.047;d=23.97时,若a4-a5>0,则α=0.082γ3-0.003γ2+1.702γ-0.083,若a4-a5<0,则α=-11431γ5+8056γ4-2077γ3+234.2γ2-8.557γ+0.157;d=23.98时,若a4-a5>0,则α=0.319γ3-0.171γ2+1.735γ-0.057,若a4-a5<0,则α=-75074γ5+53578γ4-14010γ3+1633γ2-79.19γ+1.277;d=23.99时,若a4-a5>0,则α=-0.312γ3+0.152γ2+1.688γ-0.027,若a4-a5<0,则α=3550γ5-2802γ4+823.6γ3-110.8γ2+8.37γ-0.108;d=24.00时,α=0.082γ3+0.008γ2+1.703γ;d=24.01时,若a4-a5>0,则α=3550γ5-2802γ4+823.6γ3-110.8γ2+8.37γ-0.108,若a4-a5<0,则α=-0.312γ3+0.152γ2+1.688γ-0.027;d=24.02时,若a4-a5>0,则α=-75074γ5+53578γ4-14010γ3+1633γ2-79.19γ+1.277,若a4-a5<0,则α=0.319γ3-0.171γ2+1.735γ-0.05;d=24.03时,若a4-a5>0,则α=-11431γ5+8056γ4-2077γ3+234.2γ2-8.557γ+0.157,若a4-a5<0,则α=0.082γ3-0.003γ2+1.702γ-0.083;d=24.04时,若a4-a5>0,则α=-45256γ6+32043γ5-85188γ4+10381γ3-555.7γ2+11.61γ+0.047,若a4-a5<0,则α=-0.312γ3+0.198γ2+1.671γ-0.109;d=24.05时,若a4-a5>0,则α=-22505γ6+49594γ5-22216γ4+3758γ3-241.3γ2+5.213γ+0.117,若a4-a5<0,则α=36.38γ4-28.57γ3+7.849γ2+0.786γ-0.099。具体的,步骤s4中,当d不满足23.95≤d≤24.05时,则直接判定所测气缸滑片槽不合格,不再进行下一步计算α值。具体的,步骤s3中,所述测得气缸滑片槽两个平面上各四个点的千分表读数:a1、a2、a3、a4、a5、a6、a7和a8的具体方法如下:千分表沿x轴负方向移动距离dx,与待测气缸滑片槽的一个平面在a1点抵接,输出a1点读数;然后千分表沿x轴正方向移动距离2dx,与待测气缸滑片槽另一个平面a2点抵接,输出a2点读数;然后千分表沿z轴负方向移动距离dy,与待测气缸滑片槽平面a3点抵接,输出a3点读数;然后千分表沿x轴负方向移动距离2dx,与待测气缸滑片槽平面在a4点抵接,输出a4点读数;然后千分表沿y轴正方向移动距离dy,与待测气缸滑片槽平面在a5点抵接,输出a5点读数;然后千分表沿x轴正方向移动距离2dx,与待测气缸滑片槽平面在a6点抵接,输出a6点读数;然后千分表沿z轴正方向移动距离dz,与待测气缸滑片槽平面在a7点抵接,输出a7点读数;然后千分表沿x轴负方向移动距离2dx,与待测气缸滑片槽平面在a8点抵接,输出a8点读数。具体的,步骤s3中,在滑片槽左侧面设定位置测得一个点的千分表读数a9的具体方法如下:所述千分表沿y轴负方向移动至y轴坐标-35mm处;测头与定位点中心水平,与待测气缸滑片槽平面在a9点抵接,输出a9点读数。本发明的有益效果如下:本发明综合检测装置,结构较简单,检测精准,实用性更强,将原本分开测量的气缸滑片槽宽度、平行度、垂直度和气缸滑片槽偏差值四个检测项目放在一个检测装置上测量,测量速度快,对环境和检测人员技能要求低,可以在线检测气缸滑片槽偏差值,提高了检测效率;本发明综合检测装置,利用操作显示模块控制执行机构进行检测,检测完成后再操作显示模块输出最终的结果,自动化检测,进一步的加快了检测速度提高了效率;本发明综合检测装置的定位花盘通过定位销安装在所述定位板上,方便安装和拆卸;本发明综合检测装置的千分表前端设有测头;所述测头采用探针球形测头,并且球型测头直径比探针直径大0.2mm,保证测量时在测头不用更换测量方向就可以有效测量dx值;本发明综合检测方法,将工件在定位花盘上定位,千分表在气缸滑片槽内运动,测得气缸滑片槽两个平面上共九个点的千分表读数,操作显示模块自动分别计算气缸滑片槽宽度、平行度、垂直度和气缸滑片槽偏差值并输出计算结果,操作简单,测量快速方便,有利于提高检测效率,降低误判率,简单且更易于操作。附图说明构成本申请的一部分的说明书附图用来提供对本发明的进一步理解,本发明的示意性实施例及其说明用于解释本发明,并不构成对本发明的不当限定。在附图中:图1为本发明综合检测装置的结构示意图;图2为本发明综合检测装置的执行机构结构示意图;图3为本发明综合检测装置的定位模块结构示意图;图4为待检测气缸滑片槽的测点路线示意图;图5为本发明综合检测方法的实施流程图;图6为滑片槽左倾,定位点中心到滑片槽中心线垂直距离ad=23.95时的示意图;图7为滑片槽左倾,定位点中心到滑片槽中心线垂直距离ad=24.05时的示意图;图8为滑片槽右倾,定位点中心到滑片槽中心线垂直距离ad=23.95时的示意图;图9为滑片槽右倾,定位点中心到滑片槽中心线垂直距离ad=24.05时的示意图;图10为本发明槽偏差值测量示意图;其中:1-定位模块,2-操作显示模块,3-执行机构,4-千分表,11-定位花盘,12-定位板,31-z轴带步进电机线轨,32-x轴带步进电机线轨,33-y轴带步进电机线轨,41-测头。具体实施方式下面将参考附图并结合实施例来详细说明本发明。需要说明的是,在不冲突的情况下,本申请中的实施例及实施例中的特征可以相互组合。以下详细说明均是示例性的说明,旨在对本发明提供进一步的详细说明。除非另有指明,本发明所采用的所有技术术语与本申请所属领域的一般技术人员的通常理解的含义相同。本发明所使用的术语仅是为了描述具体实施方式,而并非意图限制根据本发明的示例性实施方式。如图1、2和3所示,一种用于气缸滑片槽的综合检测装置,包括定位模块1、操作显示模块2、执行机构3和千分表4;所述定位模块1用于定位待检测的气缸滑片槽;所述千分表4安装在所述执行机构3上,千分表4的下端安装有测头41,所述测头41用于与气缸滑片槽抵接并测量气缸滑片槽上的点值;所述执行机构3用于驱动所述千分表4分别在x、y、z三轴方向上移动。所述操作显示模块2分别与所述执行机构3及千分表4电连接,用于控制所述执行机构的运动及输出测量和计算结果。所述的操作显示模块2,用于控制执行机构的启动、复位、和急停,还用于参数设定、型号选择测量结果显示;所述的参数具体为千分表4分别在x、y、z三轴方向上移动的距离dx、dy和dz值,以及滑片槽宽、平行度、垂直度和槽偏差值的上/下限标准;所述的型号选择具体为根据不同的工件确定不同的参数设定;具体的,所述的定位模块1,包括用于定位气缸滑片槽的定位花盘11,及用于定位不同型号定位花盘11的定位板12,所述定位花盘11通过定位销安装在所述定位板12上。所述执行机构3包括用于驱动所述千分表4接近待检测气缸滑片槽、向待检测气缸滑片槽的深度方向移动的z轴带步进电机线轨31、用于驱动千分表4与气缸滑片槽抵接的x轴带步进电机线轨32和用于驱动所述千分表4沿气缸滑片槽的长度方向移动的y轴带步进电机线轨33;所述千分表4通过千分表安装座安装在z轴带步进电机线轨31上,所述z轴带步进电机线轨31滑动连接在x轴带步进电机线轨32上,x轴带步进电机线轨32滑动连接在y轴带步进电机线轨33上。所述测头41采用探针球形测头,用于与气缸滑片槽抵接并测量气缸滑片槽上的点值。所述千分表4测针的测头41直径比测针直径大0.2mm。所述的千分表4为具备数据传输功能的数显千分表,能够直接将测量的数值传输给操作显示模块2。本发明的另一技术方案是,一种气缸滑片槽的综合检测方法,利用所述的综合检测装置,用于测量气缸滑片槽宽度、平行度、垂直度和气缸滑片槽偏差值,具体步骤如下:如图4和5所示,具体步骤如下:1)、向操作显示模块2中输入待检测工件的型号和相应的dx、dy和dz值,以及滑片槽宽、平行度、垂直度和槽偏差值的上/下限标准,将待测工件装在定位模块1上;2)、操作显示模块2控制z轴步进电机驱动千分表4下降至零点位置,使测头41伸入待测气缸滑片槽;3)、操作显示模块2控制千分表4沿x轴负方向移动距离dx,测头与待测气缸滑片槽平面在a1点抵接,输出a1点读数;千分表4沿x轴正方向移动距离2dx,测头与待测气缸滑片槽另一个平面a2点抵接,输出a2点读数;千分表4沿z轴负方向移动距离dy,测头与待测气缸滑片槽平面a3点抵接,输出a3点读数;千分表4沿x轴负方向移动距离2dx,测头与待测气缸滑片槽平面在a4点抵接,输出a4点读数;千分表4沿y轴正方向移动距离dy,测头与待测气缸滑片槽平面在a5点抵接,输出a5点读数;千分表4沿x轴正方向移动距离2dx,测头与待测气缸滑片槽平面在a6点抵接,输出a6点读数;千分表4沿z轴正方向移动距离dz,测头与待测气缸滑片槽平面在a7点抵接,输出a7点读数;千分表4沿x轴负方向移动距离2dx,测头与待测气缸滑片槽平面在a8点抵接,输出a8点读数;所述千分表4的测头41在气缸滑片槽内运动,测完s2所述8个点后,在滑片槽左侧面设定位置测得一个点的千分表读数:a9;4)、检测完成后操作显示模块2输出a1、a2、a3、a4、a5、a6、a7、a8和a9的测点值,及槽宽、平行度、垂直度和槽偏差值检测项目结果,显示检测结果相对标准是上偏还是下偏,使作业员快速判断检测结果,并作出相应调整对策;操作显示模块2根据公式计算并输出气缸滑片槽宽度、平行度、垂直度和气缸滑片槽偏差值;气缸滑片槽宽度、平行度、垂直度和气缸滑片槽偏差值的计算公式如下:(1)槽宽w=max(w1,w2,w3,w4),w1=2dx-(abs(a1)+abs(a2)),w2=2dx-(abs(a3)+abs(a4)),w3=2dx-(abs(a5)+abs(a6)),w4=2dx-(abs(a7)+abs(a8));(2)平行度=max(w1,w2,w3,w4)-min(w1,w2,w3,w4),w1=2dx-(abs(a1)+abs(a2)),w2=2dx-(abs(a3)+abs(a4)),w3=2dx-(abs(a5)+abs(a6)),w4=2dx-(abs(a7)+abs(a8));(3)垂直度v=max(v1,v2,v3,v4),v1=abs(a1-a4),v2=abs(a2-a3),v3=abs(a6-a7),v4=abs(a5-a8);(4)槽偏差值槽偏差值是指滑片槽中心线和内孔的交点与内孔中心的连线,和滑片槽的中心线所构成的夹角;槽偏差标准是槽偏差值α小于0.5°,槽中心线和定位孔距离应满足标准d±0.05。槽偏差值α的计算方式如下:先计算定位点中心到滑片槽中心线的垂直距离d;所述定位点中心位于气缸件上,也是定位花盘上定位柱的中心;d={24-(dx-千分表读数3)-槽宽/2cosγ}*cosγ,γ是y轴和槽中心线的夹角;千分表读数3是指千分表在a9点的测量值;当d满足23.95≤d≤24.05时,计算槽偏差值α值;当d不满足23.95≤d≤24.05时,则直接判定所测气缸滑片槽不合格;根据不同d值,利用不同关系式计算出α值,计算公式如下:d=23.95时,若a4-a5>0,则α=36.38γ4-28.57γ3+7.849γ2+0.786γ-0.099,若a4-a5<0,则α=-22505γ6+49594γ5-22216γ4+3758γ3-241.3γ2+5.213γ+0.117;d=23.96时,若a4-a5>0,则α=-0.312γ3+0.198γ2+1.671γ-0.109,若a4-a5<0,则α=-45256γ6+32043γ5-85188γ4+10381γ3-555.7γ2+11.61γ+0.047;d=23.97时,若a4-a5>0,则α=0.082γ3-0.003γ2+1.702γ-0.083,若a4-a5<0,则α=-11431γ5+8056γ4-2077γ3+234.2γ2-8.557γ+0.157;d=23.98时,若a4-a5>0,则α=0.319γ3-0.171γ2+1.735γ-0.057,若a4-a5<0,则α=-75074γ5+53578γ4-14010γ3+1633γ2-79.19γ+1.277;d=23.99时,若a4-a5>0,则α=-0.312γ3+0.152γ2+1.688γ-0.027,若a4-a5<0,则α=3550γ5-2802γ4+823.6γ3-110.8γ2+8.37γ-0.108;d=24.00时,α=0.082γ3+0.008γ2+1.703γ;d=24.01时,若a4-a5>0,则α=3550γ5-2802γ4+823.6γ3-110.8γ2+8.37γ-0.108,若a4-a5<0,则α=-0.312γ3+0.152γ2+1.688γ-0.027;d=24.02时,若a4-a5>0,则α=-75074γ5+53578γ4-14010γ3+1633γ2-79.19γ+1.277,若a4-a5<0,则α=0.319γ3-0.171γ2+1.735γ-0.05;d=24.03时,若a4-a5>0,则α=-11431γ5+8056γ4-2077γ3+234.2γ2-8.557γ+0.157,若a4-a5<0,则α=0.082γ3-0.003γ2+1.702γ-0.083;d=24.04时,若a4-a5>0,则α=-45256γ6+32043γ5-85188γ4+10381γ3-555.7γ2+11.61γ+0.047,若a4-a5<0,则α=-0.312γ3+0.198γ2+1.671γ-0.109;d=24.05时,若a4-a5>0,则α=-22505γ6+49594γ5-22216γ4+3758γ3-241.3γ2+5.213γ+0.117,若a4-a5<0,则α=36.38γ4-28.57γ3+7.849γ2+0.786γ-0.099。为了进一步解释本发明,下面结合具体的实施方式进行槽偏差值的计算方式的验证。如图6、7、8、9和10所示,首先,计算及判定定位点中心到滑片槽中心距离,定位点中心a点设置x轴坐标值为固定值24mm;a9e=dx-千分表读数3,tanγ=|a4-a5|/dy,γ=arctan(|a4-a5|/dy),a9b=槽宽/2cosγ;ab=24-(a9b-a9e)=24-((dx-千分表读数3)-槽宽/2cosγ);d=ad=ab*cosγ={24-(dx-千分表读数3)-槽宽/2cosγ}*cosγ;d的标准范围是23.95~24.05,通过计算的d值判定d是否合格,d判定不合格的直接判定不合格,d值判定合格的进行槽偏差值α角度判定。其次,滑片槽倾斜方向判断;a4=dx-千分表读数1,千分表读数1是指千分表在a4点的测量值;a5=dx-千分表读数2,千分表读数2是指千分表在a5点的测量值;dx为x轴方向设定值,滑片槽左倾时a4>a5,即a4-a5>0,滑片槽右倾时a4<a5,即a4-a5<0。然后,α角度计算及判定,d值标准范围是23.95-24.05,千分表读数精度为3位小数,根据四舍五入原则,将计算的d值精确为23.95、23.96、23.97、23.98、23.99、24.00、24.01、24.02、24.03、24.04、24.05十一个值,检验在d分别为这十一种情况下,α和γ的关系。利用制图工具,将d值分别设定为具体值的十种情况下,分别改变α角度时测量实际γ值,将α和γ两组数据在excel内利用趋势线得出α和γ的函数关系式,具体信息如下:d=23.95时,在制图软件中改变α的角度,并测量γ角度值,自变量(γ)应变量(α)0.0800.140.10.20.20.260.30.320.40.370.5通过趋势线得出函数关系式为:α=36.38γ4-28.57γ3+7.849γ2+0.786γ-0.099;(2)d=23.96时,在制图软件中改变α的角度,并测量γ角度值,自变量(γ)应变量(α)0.06500.1240.10.1820.20.2410.30.2990.40.3580.5通过趋势线得出函数关系式为:α=-0.312γ3+0.198γ2+1.671γ-0.109;(3)d=23.97时,在制图软件中改变α的角度,并测量γ角度值,自变量(γ)应变量(α)0.04900.1080.10.1660.20.2250.30.2830.40.3410.5通过趋势线得出函数关系式为:α=0.082γ3-0.003γ2+1.702γ-0.083;(4)d=23.98时,在制图软件中改变α的角度,并测量γ角度值,自变量(γ)应变量(α)0.03300.0910.10.150.20.2080.30.2670.40.3250.5通过趋势线得出函数关系式为:α=0.319γ3-0.171γ2+1.735γ-0.057;(5)d=23.99时,在制图软件中改变α的角度,并测量γ角度值,自变量(γ)应变量(α)0.01600.0750.10.1330.20.1920.30.250.40.3090.5通过趋势线得出函数关系式为:α=-0.312γ3+0.152γ2+1.688γ-0.027;(6)d=24.00时,在制图软件中改变α的角度,并测量γ角度值,通过趋势线得出函数关系式为:α=0.082γ3+0.008γ2+1.703γ;(7)d=24.01时,在制图软件中改变α的角度,并测量γ角度值,自变量(γ)应变量(α)0.01600.0420.10.1010.20.1590.30.2180.40.2760.5通过趋势线得出函数关系式为:α=3550γ5-2802γ4+823.6γ3-110.8γ2+8.37γ-0.108;(8)d=24.02时,在制图软件中改变α的角度,并测量γ角度值,自变量(γ)应变量(α)0.03300.0260.10.0840.20.1430.30.2010.40.260.5通过趋势线得出函数关系式为:α=-75074γ5+53578γ4-14010γ3+1633γ2-79.19γ+1.277;(9)d=24.03时,在制图软件中改变α的角度,并测量γ角度值,通过趋势线得出函数关系式为:α=-11431γ5+8056γ4-2077γ3+234.2γ2-8.557γ+0.157;(10)d=24.04时,在制图软件中改变α的角度,并测量γ角度值,自变量(γ)应变量(α)0.06600.0360.050.0070.10.0220.150.0520.20.0810.250.110.30.1390.350.1690.40.1980.450.2270.5通过趋势线得出函数关系式为:α=-45256γ6+32043γ5-85188γ4+10381γ3-555.7γ2+11.61γ+0.047;(11)d=24.05时,在制图软件中改变α的角度,并测量γ角度值,自变量(γ)应变量(α)0.08200.0530.050.0230.10.0060.150.0350.20.0650.250.0940.30.1230.350.1520.40.1820.450.2110.5通过趋势线得出函数关系式为:α=-22505γ6+49594γ5-22216γ4+3758γ3-241.3γ2+5.213γ+0.117;通过验证可知,滑片槽左偏和右偏情况下,α和γ关系对称,及滑片槽左偏时d=23.95的情况和滑片槽右偏时d=24.05的情况α和γ的关系相同,以此类推。α角度的判定方法:通过计算得出的d值和判定的滑片槽左偏和右偏,程式自动选择相应α和γ的关系式进行计算,并得出计算结果,α<0.5°时判定合格。另外有一种特殊情况,即a4=a5,这种情况下表示滑片槽无倾斜,只有左右平移,d范围在23.95-24.05,当d=23.95或24.05时,由制图软件测量可得α=0.14°。即当a4=a5时,只需要判断d值,若d值符合要求就为合格。图6~10中,a表示定位点中心,b表示过定位点中心a的水平直线和y轴的交点,c表示滑片槽中心线与内孔交点,d定位点中心a在滑片槽中心线上的垂足,e表示过定位点中心a的水平直线和滑片槽中心线的交点,o表示内孔中心。由技术常识可知,本发明可以通过其它的不脱离其精神实质或必要特征的实施方案来实现。因此,上述公开的实施方案,就各方面而言,都只是举例说明,并不是仅有的。所有在本发明范围内或在等同于本发明的范围内的改变均被本发明包含。当前第1页12