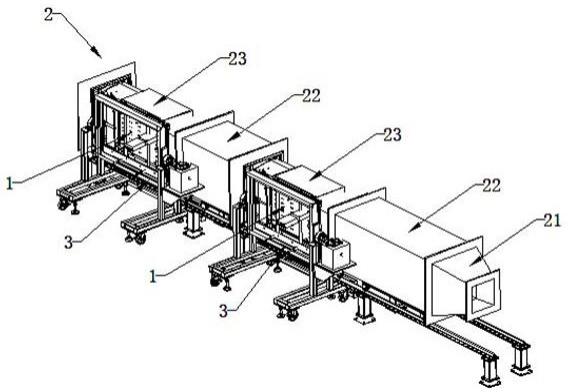
1.本发明涉及轨道交通设备制造领域,具体涉及一种热管散热器温升检测方法及热管散热器检测设备。
背景技术:2.为了保证轨道车辆上的电气设备正常工作,通常将热管散热器贴合在发热的电气设备上进行散热,同时利用轨道车辆行进过程中的气流进一步提高热管散热器的散热效果。
3.热管散热器由:基板、铜管、散热片、外壳通过焊接或组装式加工而成,重量约100kg。为了保证热管散热器的质量,需要在模拟热管散热器的工作环境中对热管散热器进行温升检测,需要将热管散热器翻转90度、呈侧立状态插入风道中进行温升检测。在此过程中需要手工对热管散热器进行吊装、锁螺丝固定、翻转侧立、安装发热快、接电缆、进行检测等多个步骤。操作人员全部靠手工操作,翻转也是人工在地面翻转,发热快是通过m6的螺栓固定在基板上并且每颗螺栓都需要打扭力确保受力平衡,上下料均是通过行车吊卸料,在其过程中操作人员的劳动强度大、操作时间长、检测效率低,而且在地面翻转中容易导致产品油漆碰伤或外壳变形。
4.本发明解决的技术问题是:提供一种热管散热器温升检测方法及热管散热器检测设备,通过手动机械来夹持和翻转热管散热器,通过手动机械将发热块压紧在热管散热器的基板上,通过升降推车卸下和转运热管散热器,通过翻转检测台与风道无缝对接进行温升试验,以减轻检测人员劳动强度大、缩短操作时间、提高检测效率。
5.经专利检索,与本发明有一定关系的专利主要有以下专利:1、申请号为“cn201710701466.8”、申请日为“2017.08.16”、公开号为“cn107300478a”、公开日为“2017.10.27”、名称为“一种svg热管散热器动态特性的测试平台及其应用方法”、申请人为“国网湖南电力公司”的中国发明专利,该发明公开了一种svg热管散热器动态特性的测试平台及其应用方法,测试平台包括温控风道、风洞、控制单元和可控稳压源,温控风道内设有测温模块,且温控风道上设有受控热源,风洞的进风口设有可控风机,测试平台能够快速精确模拟突然故障货负载突变的工况,并在控制单元实时获取试验平台内的温度和风量参数;测试平台的应用方法能够模拟svg热管散热器的负载突变,自动获取svg热管散热器动态特性的各种曲线,包括单受控热源升温试验的第一试验温度t 1 的时间变化曲线,单受控风机加速试验的第一转速v 1 的时间变化曲线,受控热源、受控风机联动试验的试验实测电压u 2 以及第二转速v 2 两者的时间变化曲线,以快速确定被测试热管散热器的动态特性优劣。
6.2、申请号为“cn201821418135.x”、申请日为“2018.08.31”、公开号为“cn209462263u”、公开日为“2019.10.01”、名称为“一种内燃机车用大功率环路热管功率模块及其镜像结构”、申请人为“西安中车永电电气有限公司”的实用新型专利,该实用新型专利涉及一种内燃机车用大功率环路热管功率模块及其镜像结构,包括环路热管散热器,由
110231533 a”、公开日为“2019.09.13”、名称为“温升试验装置及方法、存储介质、计算机设备”、申请人为“中铁检验认证中心有限公司”的中国发明专利,该发明提供一种温升试验装置及方法、存储介质、计算机设备,属于轨道交通车载干式变压器及电抗器性能测试技术领域,装置包括:测量柜1,用于测量被测样品s的功率,其中,所述被测样品s包括一个或多个干式变压器和/或一个或多个干式电抗器;电源接线柜2,与所述测量柜1连接,用于通过调整冷却风量的大小给所述测量柜1供电;冷却设备3,与所述电源接线柜2连接,用于给所述被测样品s降温。本发明可以同时对多个通道及以上的直流电阻连续测量和记录,测量效率高,且不会引入测量误差;能够精确控制风量,测量结果的可靠性高。
11.上述专利均未涉及到热管散热器温升检测方法及热管散热器检测设备。
技术实现要素:12.本发明要解决的技术问题是针对现有技术中存在的缺陷,提供一种热管散热器温升检测方法及热管散热器检测设备。
13.为解决上述技术问题,本发明所采取的技术方案为:一种热管散热器温升检测方法,所述热管散热器包括基板,将热管散热器置于模拟热管散热器工作环境的风道中进行温升检测。
14.进一步地,利用与基板接触的发热块对插入在风道的热管散热器进行加热升温,通过检测风道中空气的压差、温差及基板的温度来判断热管散热器是否合格。
15.热管散热器温升检测方法包括如下步骤:s1:将热管散热器的基板与发热块接触连接;s2:将热管散热器翻转呈侧立状态;s3:将热管散热器插入风道中;s4:将发热块通电升温,检测并记录发热块的功率、基板的温度、风道的通风流量、风道中热管散热器前后的压差及温差;s5:将温升检测后的热管散热器从风道中抽出,更换热管散热器进行温升检测;s6:根据温升检测数据计算并判断热管散热器的质量。
16.本发明还涉及采用上述方法的热管散热器检测设备,包括风道及翻转检测台,所述风道用来模拟热管散热器的工作环境,所述翻转检测台用来夹持热管散热器,并将热管散热器翻转呈侧立状态,并将热管散热器插入风道中进行加热升温。以提高检测精度,减轻检测人员劳动强度大、缩短操作时间、提高检测效率。
17.进一步地,所述风道包括:依次连接的风机、整流段及检测段,所述检测段的一侧设置有与风道垂直的、用于插入热管散热器的插口;在插口的两侧分别设置有温度传感器及压力传感器。根据温度传感器及压力传感器的温升检测数据来计算热管散热器在风道中的温差及压差。
18.进一步地,所述翻转检测台包括:翻转机构、台架及传动机构,所述翻转机构转动设置在台架上,所述传动机构固定在台架上,并与翻转机构转动连接,所述翻转机构在传动机构的带动下相对于台架水平翻转。能够轻松地翻转热管散热器,避免热管散热器在翻转过程中油漆碰伤或外壳变形。
19.进一步地,所述翻转机构包括:翻转框架、转轴、夹持部件及压紧部件,所述转轴固
定设置在翻转框架对称轴位置,所述转轴与台架转动连接;所述夹持部件设置在翻转框架正面的两端,用来夹持热管散热器;所述压紧部件设置在翻转框架的反面,用来将发热块压紧在热管散热器的基板上。利用夹持部件能够快速夹持热管散热器,利用压紧部件能够快速均匀地将发热块压紧在基板上,大大缩短了操作时间、提高了检测效率。
20.进一步地,所述夹持部件包括:纵向滑轨、纵向滑座、纵向丝杆、横向滑轨、横向丝杆及夹块;所述横向滑轨及横向丝杆平行设置在纵向滑座上,所述夹块上设置有夹槽,两块夹块按照夹槽对置的方向设置在横向滑轨及横向丝杆的两端,两块夹块在横向丝杆的带动下沿横向滑轨向中间或向两端滑动,以调整两块夹块的夹槽在横向的间距;两根纵向滑轨平行设置在翻转框架正面的端部的两侧,纵向滑座在纵向丝杆的带动下沿纵向滑轨向中间或向端部滑动,以调整设置在翻转框架两端的两组夹块的夹槽在纵向的间距。能够根据基板的宽度调整两块夹块在横向的间距,能够根据基板的长度调整两组夹块在纵向的间距,夹持部件能够快速牢固地将热管散热器夹持在翻转框架的正面。
21.进一步地,所述压紧部件包括:底板、快夹、压杆、导向柱、推杆、压板及弹力压头,所述压紧部件固定在翻转框架的反面,压杆一端与快夹铰接、另一端与推杆铰接,推杆的另一端与压板连接,多根导向柱固定在压板上,导向柱与底板滑动连接,多个弹力压头固定在压板远离底板一侧;快夹通过压杆及推杆带动压板下压,并通过弹力压头将发热块均匀压紧在基板上。利用压紧部件能够快速均匀地将发热块压紧在基板上。
22.进一步地,所述翻转检测台的下部具有c形开放空间,所述热管散热器检测设备还包括:升降推车,所述升降推车能够推入翻转检测台下部的c形开放空间,并能够在c形开放空间内垂直升降。利用升降推车能够轻松快速地将翻转到倒立位置的热管散热器卸在升降推车,便于将完成温升检测的热管散热器。
23.本发明的有益效果为:通过将热管散热器置于模拟热管散热器工作环境的风道中进行温升检测,能够得到准确的检测数据,确保了热管散热器的性能。由于采用了翻转检测台对热管散热器进行夹持及翻转,并利用翻转检测台将热管散热器插入检测风道,大幅度减轻了检测人员的劳动强度大、缩短了检测时间、提高了检测效率。同时由于采用了升降推车,能够轻松快速地将翻转到倒立位置的热管散热器卸在升降推车上,进一步提高了检测效率。
附图说明
24.图1为热管散热器立体结构示意图,图2为风道正视示意图,图3为风道立体示意图,图4为热管散热器插入风道之前的立体示意图,图5为热管散热器插入风道后的立体示意图,图6为翻转检测台及升降推车立体结构示意图,图7为翻转机构正面立体结构示意图,图8为夹持部件立体结构示意图,图9为翻转机构背面立体结构示意图,图10为压紧部件立体结构示意图,
图11为将热管散热器吊装在翻转检测台上安装时示意图,图12为将热管散热器夹紧在翻转检测台上时示意图,图13为将热管散热器翻转到侧立的检测位置时示意图,图14为将热管散热器翻转到倒立的卸装示意图,图15为采用升降推车将热管散热器顶起卸装时的示意图,图16为采用升降推车将热管散热器卸后转运时的示意图,图中:1—热管散热器、11—基板、12—外壳、2—风道、21—风机、22—整流段、23—检测段、231—检测窗、232—温度传感器、233—压力传感器、3—翻转检测台、31—翻转机构、311—翻转框架、312—转轴、313—夹持部件、3131—纵向滑轨、3132—纵向滑座、3133—纵向丝杆、3134—横向滑轨、3135—横向丝杆、3136—夹块、3137—夹槽、3138—夹槽底面、3139—夹槽斜面、314—压紧部件、3141—底板、3142—快夹、3143—压杆、3144—导向柱、3145—推杆、3136—压板、3137—弹力压头、315—支撑杆、32—台架、33—传动机构、4—升降推车、41—平板、42—滚轮、43—扶手、44—升降部件、5—发热块。
具体实施方式
25.下面通过具体的实施例并结合附图对本发明做进一步的描述:热管散热器1如图1所示:包括基板11、铜管、散热片、外壳12通过焊接或组装式加工而成,重量约100kg。热管散热器1安装使用时需要翻转90度、使基板11呈侧立状态(图1所示状态),将基板11贴合在电气设备上,利用热管散热器1对电气设备散热降温。
26.为了保证热管散热器的质量,在生产后需要对热管散热器进行温升检测。在此检测过程中需要手工对热管散热器1进行吊装、锁螺丝固定、翻转侧立、安装发热块、接电缆等多个步骤。操作人员全部靠手工操作,翻转也是在地面翻转,发热块是通过m6的螺栓固定在基板11上,并且每颗螺栓都需要打扭力确保受力平衡,操作人员的劳动强度大、操作时间长、检测效率低,而且在地面翻转中容易导致产品油漆碰伤或外壳变形。
27.本发明的热管散热器温升检测方法是:将热管散热器1置于模拟热管散热器1工作环境的风道2中进行温升检测。利用与基板11接触的发热块5对插入在风道2的热管散热器1进行加热升温,通过检测风道2中空气的压差、温差及基板11的温度来判断热管散热器1是否合格。以提高检测精度,减轻检测人员劳动强度大、缩短操作时间、提高检测效率。
28.热管散热器温升检测方法包括如下步骤:s1:将热管散热器1的基板11与发热块5接触连接;s2:将热管散热器1翻转呈侧立状态;s3:将热管散热器1插入风道2中;s4:将发热块5通电升温,检测并记录发热块5的功率、基板11的温度、风道2的通风流量、风道中热管散热器1前后的压差及温差;s5:将温升检测后的热管散热器1从风道2中抽出,更换热管散热器1进行温升检测;s6:根据温升检测数据计算并判断热管散热器1的质量。
29.采用上述方法的热管散热器检测设备,包括风道2及翻转检测台3,所述风道2用来模拟热管散热器1的工作环境,所述翻转检测台3用来夹持热管散热器1,并将热管散热器1翻转呈侧立状态,并将热管散热器1插入风道2中进行加热升温。以减轻检测人员劳动强度
大、缩短操作时间、提高检测效率。
30.风道2如图1和2所示:包括:依次连接的风机21、整流段22及检测段23,所示风机21的吸入口与整流段22连接,使风道2处于负压抽风状态。所述整流段22用来使气流稳定,所述检测段23的一侧设置有与风道垂直的、用于插入热管散热器1的插口231;在插口231的两侧分别设置有9个温度传感器232及压力传感器233。为了提高检测效率,可以设置多段整流段22和检测段23,整流段22与检测段23依次间隔设置。根据温度传感器232及压力传感器233的温升检测数据来计算热管散热器1在风道中的温差及压差。
31.所述翻转检测台3如图6所示:包括:翻转机构31、台架32及传动机构33,所述翻转机构31转动设置在台架32上,所述传动机构33固定在台架32上,并与翻转机构31转动连接,所述翻转机构31在传动机构33的带动下相对于台架32水平翻转。能够轻松地翻转热管散热器1,避免热管散热器1在翻转过程中油漆碰伤或外壳变形。所述台架32下部设有滚轮,便于将热管散热器1推入到风道2内。
32.所述翻转机构31如图7所示:包括:翻转框架311、转轴312、夹持部件313及压紧部件314,所述转轴312固定设置在翻转框架311对称轴位置,所述转轴312与台架32转动连接;所述夹持部件313有两组,分别设置在翻转框架311正面纵向(y)的两端,用来夹持热管散热器1。
33.所述夹持部件313如图8所示:包括:纵向滑轨3131、纵向滑座3132、纵向丝杆3133、横向滑轨3134、横向丝杆3135及夹块3136。所述横向丝杆3135两端具有外螺纹,两端外螺纹的旋向相反。所述夹块3136上设置有与横向丝杆3135两端外螺纹配合的内螺纹。所述横向滑轨3134及横向丝杆3135平行设置在纵向滑座3132上。所述夹块3136上设置有夹槽3137,夹槽3137的宽度大于基板11的厚度,以便基板11能够卡入夹槽3137。所述夹槽3137内靠近翻转框架311的一面为夹槽底面3138,所述夹槽底面3138靠近夹槽开口处设置有夹槽斜面3139。两块夹块3136按照夹槽3137对置的方向设置在横向滑轨3134及横向丝杆3135的两端。在横向丝杆3135的带动下,两端的夹块3136沿横向滑轨3134向中间或向两端滑动,以调整两块夹块3136的夹槽3137在横向(x)的间距。
34.两根纵向滑轨3131沿纵向(y)平行设置在翻转框架311正面的端部的两侧,纵向滑座3132在纵向丝杆3133的带动下沿纵向滑轨3131向中间或向端部滑动,以调整设置在翻转框架311两端的两组夹块3136的夹槽3137在纵向(y)的间距。能够根据基板11的宽度调整两块夹块3136在横向(x)的间距,能够根据基板11的长度调整两组夹块3136在纵向(y)的间距,夹持部件313能够快速牢固地将热管散热器1夹持在翻转框架311的正面。
35.所述压紧部件314如图9和图10所示:设置在翻转框架311的反面,用来将发热块5压紧在热管散热器1的基板11上。利用压紧部件314能够快速均匀地将发热块5压紧在基板11上,大大缩短了操作时间、提高了检测效率。
36.所述压紧部件314包括:底板3141、快夹3142、压杆3143、导向柱3144、推杆3145、压板3146及弹力压头3147,所述压紧部件314固定在翻转框架311的反面,压杆3143一端与快夹3142铰接、另一端与推杆3145铰接,推杆3145的另一端与压板3146连接,多根导向柱3144固定在压板3146上,导向柱3144与底板3141滑动连接,多个弹力压头3147固定在压板3146远离底板3141一侧;快夹3142通过压杆3143及推杆3145带动压板3146下压,并通过弹力压头3147将发热块5均匀压紧在基板11上。利用压紧部件314能够快速均匀地将发热块5压紧
在基板11上。
37.所述翻转检测台3的下部具有c形开放空间,所述热管散热器检测设备还包括:升降推车4,所述升降推车4能够推入翻转检测台3下部的c形开放空间,并能够在c形开放空间内垂直升降。利用升降推车4能够轻松快速地将翻转到倒立位置的热管散热器1卸在升降推车4,便于将完成温升检测的热管散热器1。
38.所述升降推车4包括:平板41、滚轮42、扶手43及升降部件44,所述扶手43固定设置在平板41一侧,所述滚轮42设置在平板41下面的周边位置,所述升降部件44设置在平板41下面的中间位置,所述升降部件44为剪刀式千斤顶或液压千斤顶,能够将平板41垂直顶起。
39.热管散热器温升检测步骤如下:步骤一:如图11所示,先将摇动翻转检测台3的传动机构33的手轮,将翻转框架311设有夹持部件313的正面翻转到水平位置,将两根支撑杆315放置翻转框架311上。放置后的支撑杆315的周面的最高处将会稍低于夹槽底面3138,然后将热管散热器1吊装到翻转检测台3的上面,缓慢放下热管散热器1,将基板11放置在两根支撑杆315上。
40.如图12所示:转动横向丝杆3135,调整两块夹块3136在横向(x)的间距大于基板11的宽度。然后转动纵向丝杆3133,调整设置在翻转框架311两端的两组夹块3136的夹槽3137在纵向(y)的间距,使夹槽3137在纵向(y)的间距稍大于基板11的长度。再转动横向丝杆3135,使两端的夹块3136沿横向滑轨3134向中间滑动,当两端的夹块3136的夹槽斜面3139碰到基板11时,基板11继续沿夹槽斜面3139向上滑动,从而将基板11顶起,使得基板11的背面与支撑杆315的周面脱离接触,使得能够从基板11背面抽出支撑杆315,以便在基板11的背面贴合发热块5进行加热升温。最后转动纵向丝杆3133,将基板11沿纵向(y)夹紧,从而将热管散热器1夹持固定在翻转框架311的正面,以便对热管散热器1进行翻转操作。
41.然后将翻转框架311翻转到设有压紧部件的背面朝上的位置,使热管散热器1的基板11背面朝上。将多块发热块5贴合放置在基板11上,压下多个快夹3142的操作杆,快夹3142通过压杆3143及推杆3145带动压板3146下压,并通过弹力压头3147将发热块5均匀压紧在基板11上。
42.步骤二:如图13所示,将翻转框架311翻转到热管散热器1侧立的位置。
43.步骤三:如图4和图5所示,将热管散热器1从插口231插入到风道2内。
44.步骤四:将发热块5通电升温,检测并记录发热块5的功率、基板11的温度、风道2的通风流量、风道中热管散热器1前后的压差及温差。
45.步骤五:如图14至图16所示,将温升检测后的热管散热器1从风道2中抽出,将翻转框架311翻转到热管散热器1倒立的位置。将升降推车4推入倒立的热管散热器1下面,用脚踩踏升降部件44,将平板41顶起接触到热管散热器1。然后转动横向丝杆3135及纵向丝杆3133,松开夹持部件313,再松开升降部件44,使平板41下降,使滚轮42接触地面,推开升降推车4,更换热管散热器1后再进行温升检测。
46.步骤六:根据温升检测数据计算并判断热管散热器1的质量。
47.综上所述:本发明的有益效果为:通过将热管散热器置于模拟热管散热器工作环境的风道中进行温升检测,能够得到准确的检测数据,确保了热管散热器的性能。由于采用了翻转检测台对热管散热器进行夹持及翻转,并利用翻转检测台将热管散热器插入检测风道,大幅度减轻了检测人员的劳动强度大、缩短了检测时间、提高了检测效率。同时由于采
用了升降推车,能够轻松快速地将翻转到倒立位置的热管散热器卸在升降推车上,进一步提高了检测效率。
48.以上实施例仅供说明本发明之用,而非对本发明的限制,有关技术领域的技术人员在不脱离本发明的精神和范围的情况下,还可以做出各种变化或变换,因此所有等同的技术方案也应该属于本发明的保护范围,本发明的保护范围应该由各权利要求限定。