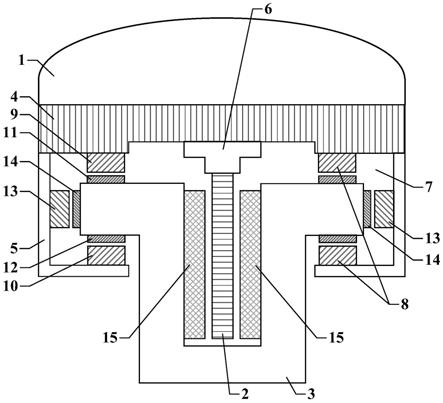
[0001]
本发明属于高速磁浮与电磁推进技术领域,具体涉及一种采用差动悬浮导向与双边直线电机的超高速磁浮试验系统。
背景技术:[0002]
磁悬浮系统按悬浮机理主要分为电磁悬浮型(ems:electromagnetic suspension)和电动悬浮型(eds:electrodynamic suspension)两类,二者分别利用电磁吸力和电动斥力实现悬浮;若按运行速度可分为四类:低速(≤100km/h)、中速(100~350km/h)、高速(350~600km/h)和超高速(≥600km/h)。与传统的轮对、滑块、轴承等接触式机械支撑相比,磁悬浮系统采用无接触式悬浮支撑,可有效弥补机械支撑在磨损、振动、噪音等方面的本征缺陷,在高速尤其超高速应用领域展现出显著的技术优势和良好的发展前景。
[0003]
目前,中车四方研制的高速磁浮试验样车主要基于德国tr磁浮列车方案,悬浮导向和直线电机等核心关键部件的结构参数没作改动,仅实现静态悬浮和低速试跑缺乏说服力,亟需高速下的动态试验验证;但由于采用了单边直线同步电机牵引方案,导致该试验样车的加速能力有限(≤0.15g),若开展600km/h运行测试则需修建试验线≥20km,总投资≥100亿,短期内很难实现,导致一些关键技术如悬浮导向、直线电机、气动力学等无法得到高速下的充分验证。
[0004]
此外,电磁吸力和电动斥力两种悬浮方案各有优缺点:吸力方案的优点在于能够实现静浮、系统控制能力强、算法可操作空间大,缺点是高速下存在涡流效应可能导致电磁力衰减进而影响系统动态性能;斥力方案的优点在于系统结构简单、能够实现自稳定、无需外加主动控制,缺点是静态与低速下无法悬浮、低速段电动阻力较大、系统因阻尼小容易产生振荡。无论哪种悬浮方式,都缺少高速下的直线运动试验验证;此外,即使现有一些低速直线和高速旋转试验平台,都只能针对单一悬浮方式开展试验,无法基于同一平台实现两种悬浮方案的试验集成。
[0005]
最后,直线电机通常采用双边定子结构以提高短距加速与制动能力,但动子一般可分为感应(异步)和永磁(同步)两种。感应动子较轻,系统有效载荷比高;永磁动子虽然较重,但稳态下的功率因数较高。与悬浮导向一样,现有条件难以做到基于同一平台实现两种电机动子方案的试验集成。
技术实现要素:[0006]
本发明的目的是针对上述技术的不足,提供一种抗干扰能力强、建造成本低且周期短、可实现短距加速与制动的采用差动悬浮导向与双边直线电机的超高速磁浮试验系统,可实现电磁吸力与电动斥力两型悬浮导向方案的互换性试验。
[0007]
为实现上述目的,本发明所设计的采用差动悬浮导向与双边直线电机的超高速磁浮试验系统,包括气动流线外壳、支撑走行机构、差动式悬浮磁体、差动式导向磁体、直线电机动子、直线电机双边定子及轨道基建;所述支撑行走机构包括上层车体框架、两个对称布
置在上层车体框架下表面两侧的下层l型托臂和固定安装在上层车体框架下底面的动子固定座;所述轨道基建的枕部伸入下层l型托臂与上层车体框架围合形成的悬浮腔内;所述差动式悬浮磁体竖向布置在悬浮腔内,所述轨道基建上设置有与所述差动式悬浮磁体相配合的悬浮轨面;所述差动式导向磁体横向布置在悬浮腔内,所述轨道基建上设置有与所述差动式导向磁体相配合的导向轨面;所述直线电机双边定子布置在轨道基建的中央腔内;所述直线电机动子位于直线电机双边定子之间且安装在动子固定座上。
[0008]
进一步地,所述差动式悬浮磁体包括2n个差动式悬浮磁体单元,n为自然数,其中n个差动式悬浮磁体单元均匀布置在一侧下层l型托臂与上层车体框架围合形成的悬浮腔内,另外n个差动式悬浮磁体单元均匀布置在另一侧下层l型托臂与上层车体框架围合形成的悬浮腔内,且两侧的差动式悬浮磁体单元呈一一对称布置;每个所述差动式悬浮磁体单元包括上部悬浮磁体和下部悬浮磁体,上部悬浮磁体固定在上层车体框架的下表面与轨道基建枕部的上部悬浮轨面呈上下正对应布置,下部悬浮磁体固定在下层l型托臂横板的上表面与轨道基建枕部的下部悬浮轨面呈上下正对应布置。
[0009]
进一步地,所述差动式导向磁体包括2m个差动式导向磁体单元,m为自然数,其中m个差动式导向磁体单元均匀布置在一侧下层l型托臂竖板的内侧面,另外m个差动式导向磁体单元均匀布置在另一侧下层l型托臂竖板的内侧面,且两侧的差动式导向磁体单元呈一一对称布置;每个所述差动式导向磁体单元与轨道基建枕部外端面的导向轨面呈正对应布置。
[0010]
进一步地,所述直线电机双边定子包括两个直线电机定子单元,一个直线电机定子单元布置在轨道基建中央腔内的一侧表面,另一个直线电机定子单元布置在轨道基建中央腔内的另一侧表面,两个直线电机定子单元沿中央腔的中心面呈对称布置;直线电机动子插入两个直线电机定子单元之间并安装在动子固定座上,且直线电机动子的中心面与中央腔的中心面重合。
[0011]
进一步地,两个所述下层l型托臂沿上层车体框架的对称面对称且呈相对布置,且轨道基建中央腔的中心面与上层车体框架的对称面重合,动子固定座的对称面与上层车体框架的对称面重合。
[0012]
进一步地,所述上部悬浮磁体、下部悬浮磁体和差动式导向磁体单元采用纯电励磁或混合励磁电磁铁;对应地,上部悬浮轨面、下部悬浮轨面和导向轨面采用硅钢叠片结构。
[0013]
进一步地,所述上部悬浮磁体、下部悬浮磁体和差动式导向磁体单元采用阵列形式的永磁体;对应地,上部悬浮轨面、下部悬浮轨面和导向轨面采用实心铜板结构。
[0014]
进一步地,所述直线电机动子为感应电机动子或永磁电机动子;对应地,两个直线电机定子单元均采用硅钢叠片结构。
[0015]
与现有技术相比,本发明具有以下优点:
[0016]
1)采用直线电机双边定子结构,可实现法向加速度的抵消,因此电机可以具有很高的运行加速度,可在较短的距离带动试验车加速至所需的峰值速度;即本发明能以较低的成本、较短的周期填补当前缺乏但亟需的磁浮系统高速试验条件;
[0017]
2)电磁吸力和电动斥力两型悬浮导向方案在结构上可以切换,基于本发明试验系统可对两型方案进行充分的技术验证和性能对比,为超高速磁浮系统的研发和悬浮导向方
案的选择提供理论依据与试验支撑。同理,异步感应和永磁同步两型电机动子方案在结构上可以切换,基于本发明试验系统可对两型方案进行充分的技术验证和性能对比,为超高速磁浮系统的研发和直线电机方案的选择提供理论依据与试验支撑;
[0018]
3)与导向系统类似,本发明悬浮系统也采用差动式结构,可有效克服高速下的气动效应尤其垂向气动干扰;与传统最大下落加速度仅1g的单边式悬浮相比,差动式悬浮的最大上拉和下落加速度均可设计为远大于1g,因此具有更强的抗干扰能力,系统的稳定性和安全性更好。
附图说明
[0019]
图1是本发明采用差动悬浮导向与双边直线电机的超高速磁浮试验系统结构示意简图;
[0020]
图2为本发明采用电磁吸力悬浮导向方案的结构简图;
[0021]
图3为本发明采用电动斥力悬浮导向方案的结构简图;
[0022]
图4为本发明采用感应动子直线电机方案的结构简图;
[0023]
图5为本发明采用永磁动子直线电机方案的结构简图。
具体实施方式
[0024]
下面结合附图和具体实施例对本发明作进一步的详细说明。
[0025]
如图1所示采用差动悬浮导向与双边直线电机的超高速磁浮试验系统,包括气动流线外壳1、支撑走行机构、差动式悬浮磁体、差动式导向磁体、直线电机动子2、直线电机双边定子及轨道基建3;其中,支撑行走机构包括上层车体框架4、两个下层l型托臂5和动子固定座6。两个下层l型托臂5对称布置在上层车体框架4下表面的两侧,即一个下层l型托臂5的竖板顶端固定在上层车体框架4下表面的一侧,另一个下层l型托臂5的竖板顶端固定在上层车体框架4下表面的另一侧,两个下层l型托臂5沿上层车体框架4的对称面对称且呈相对布置;轨道基建3的枕部伸入下层l型托臂5与上层车体框架4围合形成的悬浮腔7内,且轨道基建3中央腔的中心面与上层车体框架4的对称面重合;轨道基建3上设置有与差动式悬浮磁体相配合的悬浮轨面,轨道基建3上设置有与差动式导向磁体相配合的导向轨面;动子固定座6安装在上层车体框架4的下底面,且动子固定座6的对称面与上层车体框架4的对称面重合。
[0026]
差动式悬浮磁体包括2n个差动式悬浮磁体单元8(n为自然数),其中n个差动式悬浮磁体单元8均匀布置在一侧下层l型托臂5与上层车体框架4围合形成的悬浮腔7内,另外n个差动式悬浮磁体单元8均匀布置在另一侧下层l型托臂5与上层车体框架4围合形成的悬浮腔7内,且两侧的差动式悬浮磁体单元8呈一一对称布置。每个差动式悬浮磁体单元8包括上部悬浮磁体9和下部悬浮磁体10,上部悬浮磁体9固定在上层车体框架4的下表面,与轨道基建3枕部的上部悬浮轨面11呈上下正对应布置;下部悬浮磁体10固定在下层l型托臂5横板的上表面,与轨道基建3枕部的下部悬浮轨面12呈上下正对应布置。上部悬浮磁体9和下部悬浮磁体10组成差动式悬浮磁体,分别与铺设于轨道基建3枕部表面的上部悬浮轨面11、下部悬浮轨面12发生作用,产生差动式电磁吸力或电动斥力,与试验车重力抵消以实现系统的悬浮。
[0027]
差动式导向磁体包括2m个差动式导向磁体单元13(m为自然数),其中m个差动式导向磁体单元13均匀布置在一侧下层l型托臂5竖板的内侧面,另外m个差动式导向磁体单元13均匀布置在另一侧下层l型托臂5竖板的内侧面,且两侧的差动式导向磁体单元13呈一一对称布置。每个差动式导向磁体单元13与轨道基建3枕部外端面的导向轨面14呈正对应布置。一侧差动式导向磁体单元和另一侧差动式导向磁体单元组成差动式导向磁体,分别与铺设于轨道基建3枕部表面的一侧导向轨面14、另一侧导向轨面14发生作用,产生差动式电磁吸力或电动斥力,与试验车横向干扰力抵消以完成系统的导向。
[0028]
因此,差动式悬浮磁体与悬浮轨面、差动式导向磁体与导向轨面均可根据不同类型的悬浮导向试验需求进行更换。本实施例中,悬浮轨面和导向轨面均采用硅钢叠片或实心金属材质制作。
[0029]
直线电机双边定子包括两个直线电机定子单元15,一个直线电机定子单元15布置在轨道基建3中央腔内的一侧表面,另一个直线电机定子单元15布置在轨道基建3中央腔内的另一侧表面,且两个直线电机定子单元15沿中央腔的中心面呈对称布置;直线电机动子2插入两个直线电机定子单元15之间并安装在动子固定座6上,且直线电机动子的中心面与中央腔的中心面重合。直线电机动子与固定于轨道基建3内表面的两侧直线电机定子单元15配合作用产生电磁加速或制动力。
[0030]
下层l型托臂5作为上部悬浮磁体9、下部悬浮磁体10以及差动式导向磁体单元13的安装固定基座。当进行不同类型的悬浮导向试验时,上层车体框架4和动子固定座6可保持不变,只需更换下层l型托臂5即可。另外,本实施例中,支撑走行机构采用高强度轻质的铝或钛合金材料制造,可降低车重以减小对能量存储与调控系统的指标需求,进而降低全系统的建造成本。气动流线外壳1布置于试验车上部,经过气动优化设计并用减阻材料制造,以减小试验车高速运动下的气动阻力,并改善尾流、湍流等气动分布特性。
[0031]
如图2所示,本实施例采用电磁吸力型悬浮导向方案。电磁吸力悬浮与导向磁体采用基于纯电励磁或永磁-电磁混合励磁的电磁铁,相应的上部悬浮轨面11、下部悬浮轨面12和两侧导向轨面14采用硅钢叠片结构。其中,下部悬浮磁体9采用混合励磁电磁铁,由硅钢叠片铁芯、内置或表贴式永磁体、调控线圈组成;永磁体可提供稳态偏置力以抵消重力实现“零功率”悬浮,可降低悬浮能耗同时提高浮重比。上部悬浮磁体10采用纯电励磁电磁铁,由硅钢叠片铁芯、调控线圈组成,用于增大悬浮系统动态调节的下落加速度,提升系统的控制效果和抗干扰能力。在悬浮控制系统的作用下,下部悬浮磁体和上部悬浮磁体分别与其对应的吸力悬浮硅钢叠片轨面相互作用产生两个动态可调的电磁吸力,二者的差动合力与试验车的重力抵消,从而实现系统的稳定悬浮。同理,两侧差动式导向磁体单元13均采用纯电励磁电磁铁,由硅钢叠片铁芯、调控线圈组成,在导向控制系统的作用下,分别与两侧面的吸力导向硅钢叠片轨面相互作用产生一对动态可调的差动式电磁吸力,二者的合力与试验车的横向干扰力抵消,从而实现系统的导向对中。
[0032]
如图3所示,本实施例采用电动斥力型悬浮导向方案。电动斥力悬浮与导向磁体采用基于halbach阵列形式的永磁体,相应的上部悬浮轨面11、下部悬浮轨面12和两侧导向轨面14采用实心铜板结构。其中,下部悬浮磁体9和上部悬浮磁体10均由多块粘接永磁体、外围封装、安装基座等组成。当试验车受到直线电机牵引力开始运动时,上部悬浮磁体和下部悬浮磁体分别与其对应的斥力悬浮实心铜板轨面相互作用产生两个随速度变化的电动斥
力,当车速达到一定值时,二者的差动合力与试验车的重力抵消,从而实现系统的稳定悬浮。同理,两侧差动式导向磁体单元13均由多块粘接永磁体、外围封装、安装基座等组成,当试验车运动速度达到一定值时,分别与两侧导向实心铜板轨面相互作用产生一对随速度变化的差动式电动斥力,二者的合力与试验车的横向干扰力抵消,从而实现系统的导向对中。
[0033]
结合图4、图5所示,本实施例直线电机动子2分别采用感应电机动子和永磁电机动子方案。其中,感应电机动子采用低密度的实心铝板制作,以减轻动子自重、提升电机的有效载荷;永磁电机动子采用高剩磁的钕铁硼材料削极、拼接制成,以提高电机的效率同时降低推力波动。两个直线电机定子单元15均采用硅钢叠片结构,以降低高速运动下的涡流效应对电机性能产生的不利影响。
[0034]
本发明采用直线电机双边定子结构,可实现法向加速度的抵消,因此电机可以具有很高的运行加速度,可在较短的距离带动试验车加速至所需的峰值速度;即本发明能以较低的成本、较短的周期填补当前缺乏但亟需的磁浮系统高速试验条件。
[0035]
另外,电磁吸力和电动斥力两型悬浮导向方案在结构上可以切换,基于本发明试验系统可对两型方案进行充分的技术验证和性能对比,为超高速磁浮系统的研发和悬浮导向方案的选择提供理论依据与试验支撑。同理,异步感应和永磁同步两型电机动子方案在结构上可以切换,基于本发明试验系统可对两型方案进行充分的技术验证和性能对比,为超高速磁浮系统的研发和直线电机方案的选择提供理论依据与试验支撑。
[0036]
最后,与导向系统类似,本发明悬浮系统也采用差动式结构,可有效克服高速下的气动效应尤其垂向气动干扰;与传统最大下落加速度仅1g的单边式悬浮相比,差动式悬浮的最大上拉和下落加速度均可设计为远大于1g,因此具有更强的抗干扰能力,系统的稳定性和安全性更好。