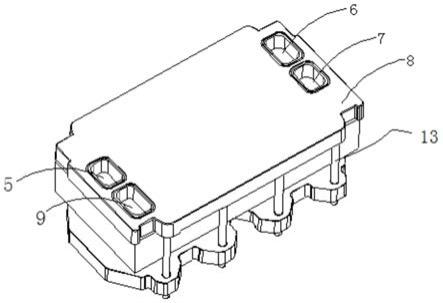
[0001]
本发明涉及燃料电池,尤其是涉及一种燃料电池双极板渗漏的批量检测工装和方法。
背景技术:[0002]
伴随燃料电池技术日趋成熟,作为一种零污染,高效率,可以将化学能直接转变为电能的发电设备已经被越来越多的应用于通讯基站、车载动力、分布式电源等领域。
[0003]
双极板是燃料电池的核心零部件之一,起到分配气体,传导热量和电能的作用。由于额定工作状态下,燃料电池单节的电压值较低,为了实现大功率输出,一般需要超过一百甚至几百片单电池来实现。因而这对双极板质量一致性控制要求很高。
[0004]
为了提高燃料电池电堆的功率密度,以及减小阻值。燃料电池双极板的厚度要求越来越薄,这对无论是金属板还是石墨板均提出了严格的防渗漏指标要求。
[0005]
通常为了提高极板渗漏检测的节拍,将极板多片堆叠后泡水里,极板冷却腔通有一定压力的气体,以此直观地观察极板在水里冒泡的情况来实现,虽然可以快速筛查出有问题的极板,但是该检测方法还是有如下几个缺点:
[0006]
1、无法定位每块极板上的渗漏位置;
[0007]
2、无法直观判定每块极板上渗漏点的渗漏严重程度。
[0008]
3、组装成真堆后的双极板末端检测,该方法严重占用设备资源,从大批量生产来说非常不可取。
技术实现要素:[0009]
本发明的目的就是为了克服上述现有技术存在的缺陷而提供一种可定位渗漏位置且可批量检测的燃料电池双极板渗漏的批量检测工装和方法,该方法可以实现在制板前端多一道检测,筛选出合格的双极板用于末端装堆集成,有效提高一次性装堆的成功率,实现电堆的批量化生产。
[0010]
本发明的目的可以通过以下技术方案来实现:一种燃料电池双极板渗漏的批量检测工装,双极板包括冷却流体入口,空气入口,冷却流体出口和空气出口以及连接冷却流体入口和冷却流体出口的冷却流体通道,连接空气入口和空气出口的空气流道,其特征在于,所述的工装包括上端板、下端板、拉杆,多片双极板堆叠在上端板和下端板之间,并通过拉杆固定,相邻双极板以及双极板与上端板和下端板之间通过密封件密封,所述的上端板和下端板上设有荧光显色剂溶液入口和荧光显色剂溶液出口,以及热空气入口和热空气出口,其中荧光显色剂溶液入口与双极板的冷却流体入口连通,荧光显色剂溶液出口与双极板的冷却流体出口连通,热空气入口与双极板的空气入口连通,热空气出口与双极板的空气出口连通。
[0011]
所述的荧光显色剂溶液入口和荧光显色剂溶液出口通过循环管道连接至荧光显色剂溶液储罐,并在循环管道上设有泵和加热器。
[0012]
所述的荧光显色剂溶液储罐内装有浓度为200-2000ppm的水溶性荧光剂。
[0013]
所述的水溶性荧光剂包括二苯乙烯衍生物、苯基吡唑啉衍生物、苯并咪唑衍生物、苯并唑衍生物、香豆素衍生物、和萘二甲酰亚胺衍生物或氧杂蒽环的酮二钠盐。
[0014]
所述的水溶性荧光剂在365nm~405nm紫外光下呈现荧光。
[0015]
所述的热空气入口通过管道连接空压机,并在管道上设有空气加热器。
[0016]
通过热空气入口输入工装内的热空气温度为40-80℃。
[0017]
堆叠在上端板和下端板之间的双极板的片数为2-200片。
[0018]
采用上述燃料电池双极板渗漏的批量检测工装进行检测的方法,包括以下步骤:
[0019]
第一步:将双极板堆叠在上端板和下端板之间,每块双极板用密封件隔开;
[0020]
第二步:使用去离子水或者防冻液作为溶剂,水溶性荧光剂作为溶质,配置浓度为200-2000ppm的荧光显色剂溶液;
[0021]
第三步:将配置好的荧光显色剂溶液加温至40-80℃,泵入工装,从荧光显色剂溶液入口流入各双极板的冷却流体入口,流经冷却流体通道,从冷却流体出口流至荧光显色剂溶液出口,使冷却流体通道内的流体压力保持在20-200kpa,流速为0.1-1m/s,静置1-7天;同时,通过热空气入口引入40-80℃热空气,流经双极板的空气通道,从热空气出口排出;
[0022]
第四步;静置结束后将工装中的荧光显色剂溶液抽出,打开工装,将双极板(10)逐片拆解;
[0023]
第五步;将测试结束的双极板放入暗室,在紫外线灯下,检测各双极板的渗漏情况。
[0024]
双极板上出现荧光反应的区域即为双极板泄漏点区域,根据荧光反应区域的面积大小,半定量渗漏程度。
[0025]
与现有技术相比,本发明使用荧光显色剂在多片堆叠极板上实现高效检测渗漏的方法,同步完成一批双极板漏点的精准定位及半定量级别的漏量评估。具体方法是,将配置好的液体显色剂带温泵入多片堆叠的极板检测装置内,在一定时间内使极板冷却腔内保持高压力,极板主流场单侧引入热空气循环。引入热空气是为了保证渗漏的荧光剂中水分能尽快蒸发,防止荧光剂的渗漏流动扩散误导对渗漏位置及渗漏量的判定。保持足够时长后,将显色剂溶液泵出,并吹扫冷却腔体。打开多片堆叠极板装置,取出极板并置于暗室,使用紫外光观测极板两侧显色情况,从而可以直观并准确地看到每块双极板的渗漏程度及渗漏点。
[0026]
本发明通过一定时间的荧光剂示踪渗透多片堆叠极板,可以批量高效检测极板的气密性,精确定位漏点及半定量渗漏情况,缩短检测节拍,大大提高极板筛查效率,从制板前端多一道工序筛选合格双极板,以保证末端组堆的一次性合格率。
附图说明
[0027]
图1为双极板的结构示意图;
[0028]
图2为本发明燃料电池双极板渗漏的批量检测工装结构示意图;
[0029]
图3为本发明燃料电池双极板渗漏的批量检测工装剖面图。
具体实施方式
[0030]
下面结合附图和具体实施例对本发明进行详细说明。
[0031]
实施例1
[0032]
一种燃料电池双极板渗漏的批量检测工装,双极板的结构如图1所示,包括三进三出口和各流体通道,本申请检测时需用到其中冷却流体入口1,空气入口2,冷却流体出口3和空气出口4以及连接冷却流体入口1和冷却流体出口3的冷却流体通道,连接空气入口2和空气出口4的空气流道。
[0033]
如图2-3所示,所述的工装包括上端板8、下端板12、拉杆13,多片双极板10堆叠在上端板8和下端板12之间,并通过拉杆13固定,相邻双极板10以及双极板10与上端板8和下端板12之间通过密封件11密封,所述的上端板8和下端板12上设有荧光显色剂溶液入口5和荧光显色剂溶液出口7,以及热空气入口6和热空气出口9,其中荧光显色剂溶液入口5与双极板10的冷却流体入口1连通,荧光显色剂溶液出口7与双极板10的冷却流体出口3连通,热空气入口6与双极板10的空气入口2连通,热空气出口9与双极板10的空气出口4连通。
[0034]
所述的荧光显色剂溶液入口5和荧光显色剂溶液出口7通过循环管道连接至荧光显色剂溶液储罐,并在循环管道上设有泵和加热器。所述的荧光显色剂溶液储罐内装有浓度为200-2000ppm的水溶性荧光剂。所述的水溶性荧光剂包括二苯乙烯衍生物、苯基吡唑啉衍生物、苯并咪唑衍生物、苯并唑衍生物、香豆素衍生物、和萘二甲酰亚胺衍生物或氧杂蒽环的酮二钠盐。本实施例中选用的水溶性荧光剂为含有1000ppm的市售二苯乙烯衍生物,其在紫外光(365nm~405nm)下呈现荧光。
[0035]
所述的热空气入口6通过管道连接空压机,并在管道上设有空气加热器。
[0036]
采用上述燃料电池双极板渗漏的批量检测工装进行检测的方法,包括以下步骤:
[0037]
第一步:将多片双极板10(本实施例中以8片双极板为例)堆叠在上端板8和下端板12之间,每块双极板10用密封件11隔开,并通过拉杆13固定;
[0038]
第二步:使用去离子水或者防冻液作为溶剂,市售二苯乙烯衍生物作为溶质,配置浓度为1000ppm的荧光显色剂溶液;
[0039]
第三步:将配置好的荧光显色剂溶液装在荧光显色剂溶液储罐中,通过泵输入加热器,加温至60℃,泵入工装,从荧光显色剂溶液入口5流入各双极板的冷却流体入口1,流经冷却流体通道,从冷却流体出口3流至荧光显色剂溶液出口7,使冷却流体通道内的流体压力保持在100kpa,流速为0.5m/s,静置5天;同时,空气压缩机将空气输入加热器,加温至60℃,输入热空气入口6引入双极板10的空气入口2,流经双极板的空气通道,从空气出口4流出,然后通过热空气出口9排出;
[0040]
第四步;静置结束后将工装中的荧光显色剂溶液抽出,打开工装,将双极板10逐片拆解;
[0041]
第五步;将测试结束的双极板放入暗室,在紫外线灯下,检测各双极板的渗漏情况,双极板上出现荧光反应的区域即为双极板泄漏点区域,根据荧光反应区域的面积大小,半定量渗漏程度。
[0042]
实施例2
[0043]
本实施例中采用的水溶性荧光剂为含有200ppm的市售苯基吡唑啉衍生物。
[0044]
堆叠在上端板8和下端板12之间的双极板10为两片,泵入工装的荧光显色剂溶液
和热空气的温度均为40℃,冷却流体通道内的流体压力保持在100kpa,流速为0.4m/s,静置7天,其余同实施例1。
[0045]
实施例3
[0046]
本实施例中采用的水溶性荧光剂为含有2000ppm的市售香豆素衍生物。
[0047]
堆叠在上端板8和下端板12之间的双极板10为200片,泵入工装的荧光显色剂溶液和热空气的温度均为60℃,冷却流体通道内的流体压力保持在200kpa,流速为1m/s,静置1天,其余同实施例1。