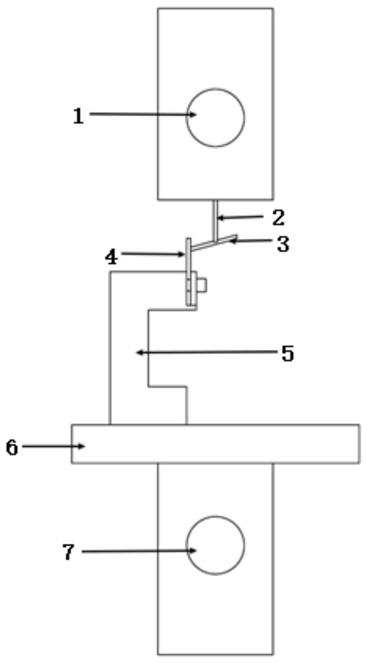
1.本发明属于医疗器械技术领域,具体涉及一种万向螺钉与接骨板结构稳定性试验方法。
背景技术:2.临床上用于骨科内固定的锁定接骨板螺钉系统主要由锁定螺钉和接骨板构成,锁定螺钉与接骨板之间的角度是预先设定的。为了使得植入骨中的锁定螺钉具有最佳的固定效果,则要求锁定螺钉必须按特定的方向植入骨内;由于骨折破损部分的各异,以及不同个体之间的骨骼形状存在差异,因此在临床应用中,这种锁定接骨板螺钉系统常存在锁定螺钉与钢板之间所设定的植入方向和最佳植入方向不一致的矛盾,影响手术效果。现有的锁定螺钉与接骨板的结构稳定性无法得知,因而无法得知其是否满足个体需求,最终严重影响手术效果,甚至可能导致多次手术。
技术实现要素:3.本发明所要解决的技术问题是针对上述现有技术的不足提供一种万向螺钉与接骨板结构稳定性试验方法,其通过测试工装对组合系统施加静压力,同时记录载荷与位移的变化,并输出数据进行分析,对比不同锁紧角度下结构的稳定性能。
4.为实现上述技术目的,本发明采取的技术方案为:
5.一种万向螺钉与接骨板结构稳定性试验方法,其特征在于:包括以下步骤:
6.步骤一:测试样品装配,将万向螺钉与接骨板锁紧,保证锁定后万向螺钉的中心轴线与接骨板螺钉安装孔法向之间的夹角分别为0
°
、5
°
、10
°
、15
°
,共装配完成4组测试样品;
7.步骤二:测试工装安装,将上测试工装固定安装在试验机上接头上,并将下测试工装固定安装在试验机下接头上,保证上测试工装中心轴线与试验机中心对齐;
8.步骤三:测试样品安装,将其中1组测试样品的接骨板固定到试验块上,然后将试验块固定到下测试工装上,保证接骨板纵向轴线与试验机中心轴线平行,调节试验块与下测试工装之间的位置,保证万向螺钉与接骨板锁定中心到上测试工装轴线的距离为15mm,然后将下测试工装与试验机固定;
9.步骤四:打开试验机控制软件,编辑试验方案,设定测试控制方式为位移控制,加载速率为25mm/min,利用试验机通过上测试工装对万向螺钉钉体施加竖直向下的压缩载荷,同时连续记录载荷和位移变化,并输出整个测试过程的载荷与位移数据;
10.步骤五:按照试验方案,开始试验,利用试验机通过上测试工装对万向螺钉加压,记录并输出整个测试过程的位移和载荷数据;
11.步骤六:重复步骤三、步骤四和步骤五,完成万向螺钉与接骨板其余锁紧角度结构的稳定性测试;
12.步骤七:确定极限载荷与极限位移,将试验机输出的原始载荷位移数据输入到originpro2018中,可以得到位移载荷曲线,曲线上纵坐标的最大值为极限载荷,所对应的
横坐标为极限位移。
13.上述的试验块为“u”型结构形式且试验块上设有腰型孔。
14.上述的上测试工装为圆柱棒状结构。
15.上述的下测试工装为矩形板状结构。
16.本发明通过将锁紧后的万向螺钉与接骨板通过试验块、上测试工装、下测试工装与试验机相连,万向螺钉的中心轴线与接骨板螺钉安装孔法向之间的夹角分别为0
°
、5
°
、10
°
、15
°
;然后通过上测试工装对组合系统施加静压力,同时记录载荷与位移的变化,并输出数据进行分析,对比不同锁紧角度下结构的稳定性能;测试样品装配,将万向螺钉与接骨板锁紧,保证锁定后万向螺钉的中心轴线与接骨板螺钉安装孔法向之间的夹角分别为0
°
、5
°
、10
°
、15
°
,共装配完成4组测试样品;测试工装安装,将上测试工装固定安装在试验机上接头上,并将下测试工装固定安装在试验机下接头上,保证上测试工装中心轴线与试验机中心对齐;测试样品安装,将其中1组测试样品的接骨板固定到试验块上,然后将试验块固定到下测试工装上,保证接骨板纵向轴线与试验机中心轴线平行,调节试验块与下测试工装之间的位置,保证万向螺钉与接骨板锁定中心到上测试工装轴线的距离为15mm,然后将下测试工装与试验机固定;打开试验机控制软件,编辑试验方案,设定测试控制方式为位移控制,加载速率为25mm/min,利用试验机通过上测试工装对万向螺钉钉体施加竖直向下的压缩载荷,同时连续记录载荷和位移变化,并输出整个测试过程的载荷与位移数据;按照试验方案,开始试验,利用试验机通过上测试工装对万向螺钉加压,记录并输出整个测试过程的位移和载荷数据;重复操作,完成万向螺钉与接骨板其余锁紧角度结构的稳定性测试;确定极限载荷与极限位移,将试验机输出的原始载荷位移数据输入到originpro 2018中,可以得到位移载荷曲线,曲线上纵坐标的最大值为极限载荷,所对应的横坐标为极限位移;极限载荷为施加在组件上的最大压缩载荷(见图2中a点的载荷),表示该结构保持稳定性所能抵抗的最大力,该值越大,表明稳定性能越好。
17.本发明的优点在于以下几点:解决风力发电机组由于结冰而产生的材料及性能改变的问题,以及解决疲劳载荷变大而影响设备使用的问题,为风力发电机组安全、长时间运行工作提供了保障,最大程度降低了叶片结冰带来的设备故障问题。
附图说明
18.图1是本发明的结构示意图;
19.图2是本发明位移载荷曲线示意图。
20.其中的附图标记为:试验机上接头1、上测试工装2、万向螺钉3、接骨板4、试验块5、下测试工装6、试验机下接头7。
具体实施方式
21.下面结合附图对本发明的具体实施方式作出进一步说明:
22.一种万向螺钉与接骨板结构稳定性试验方法,其特征在于:包括以下步骤:
23.步骤一:测试样品装配,将万向螺钉3与接骨板4锁紧,保证锁定后万向螺钉3的中心轴线与接骨板4螺钉安装孔法向之间的夹角分别为0
°
、5
°
、10
°
、15
°
,共装配完成4组测试样品;
24.步骤二:测试工装安装,将上测试工装2固定安装在试验机上接头1上,并将下测试工装6固定安装在试验机下接头7上,保证上测试工装2中心轴线与试验机中心对齐;
25.步骤三:测试样品安装,将其中1组测试样品的接骨板4固定到试验块5上,然后将试验块5固定到下测试工装6上,保证接骨板4纵向轴线与试验机中心轴线平行,调节试验块5与下测试工装6之间的位置,保证万向螺钉3与接骨板4锁定中心到上测试工装2轴线的距离为15mm,然后将下测试工装6与试验机固定;
26.步骤四:打开试验机控制软件,编辑试验方案,设定测试控制方式为位移控制,加载速率为25mm/min,利用试验机通过上测试工装2对万向螺钉3钉体施加竖直向下的压缩载荷,同时连续记录载荷和位移变化,并输出整个测试过程的载荷与位移数据;
27.步骤五:按照试验方案,开始试验,利用试验机通过上测试工装2对万向螺钉3加压,记录并输出整个测试过程的位移和载荷数据;
28.步骤六:重复步骤三、步骤四和步骤五,完成万向螺钉3与接骨板4其余锁紧角度结构的稳定性测试;
29.步骤七:确定极限载荷与极限位移,将试验机输出的原始载荷位移数据输入到originpro2018中,可以得到位移载荷曲线,曲线上纵坐标的最大值为极限载荷,所对应的横坐标为极限位移。
30.实施例中,试验块5为“u”型结构形式且试验块5上设有腰型孔。方便了接骨板4的安装和调节,大大提高了其操作效率。
31.实施例中,上测试工装2为圆柱棒状结构。方便了上测试工装2与试验机上接头1的连接,同时也方便了万向螺钉3的安装调节。
32.实施例中,下测试工装6为矩形板状结构。方便了下测试工装6与试验机下接头7的连接,同时也方便了试验块5的安装调节。
33.本发明通过将锁紧后的万向螺钉3与接骨板4通过试验块5、上测试工装2、下测试工装6与试验机相连,万向螺钉3的中心轴线与接骨板4螺钉安装孔法向之间的夹角分别为0
°
、5
°
、10
°
、15
°
;然后通过上测试工装2对组合系统施加静压力,同时记录载荷与位移的变化,并输出数据进行分析,对比不同锁紧角度下结构的稳定性能;测试样品装配,将万向螺钉3与接骨板4锁紧,保证锁定后万向螺钉3的中心轴线与接骨板4螺钉安装孔法向之间的夹角分别为0
°
、5
°
、10
°
、15
°
,共装配完成4组测试样品;测试工装安装,将上测试工装2固定安装在试验机上接头1上,并将下测试工装6固定安装在试验机下接头7上,保证上测试工装2中心轴线与试验机中心对齐;测试样品安装,将其中1组测试样品的接骨板4固定到试验块5上,然后将试验块5固定到下测试工装6上,保证接骨板4纵向轴线与试验机中心轴线平行,调节试验块5与下测试工装6之间的位置,保证万向螺钉3与接骨板4锁定中心到上测试工装2轴线的距离为15mm,然后将下测试工装6与试验机固定;打开试验机控制软件,编辑试验方案,设定测试控制方式为位移控制,加载速率为25mm/min,利用试验机通过上测试工装2对万向螺钉1钉体施加竖直向下的压缩载荷,同时连续记录载荷和位移变化,并输出整个测试过程的载荷与位移数据;按照试验方案,开始试验,利用试验机通过上测试工装2对万向螺钉3加压,记录并输出整个测试过程的位移和载荷数据;重复操作,完成万向螺钉3与接骨板4其余锁紧角度结构的稳定性测试;确定极限载荷与极限位移,将试验机输出的原始载荷位移数据输入到originpro 2018中,可以得到位移载荷曲线,曲线上纵坐标的最大值为极限
载荷,所对应的横坐标为极限位移;极限载荷为施加在组件上的最大压缩载荷(见图2中a点的载荷),表示该结构保持稳定性所能抵抗的最大力,该值越大,表明稳定性能越好。
34.以上仅是本发明的优选实施方式,本发明的保护范围并不仅局限于上述实施例,凡属于本发明思路下的技术方案均属于本发明的保护范围。应当指出,对于本技术领域的普通技术人员来说,在不脱离本发明原理前提下的若干改进和润饰,应视为本发明的保护范围。