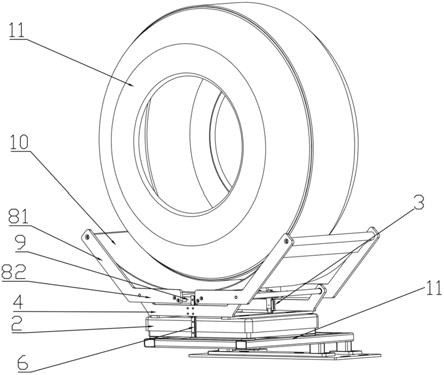
[0001]
本实用新型属于汽车轮胎成型领域,具体涉及一种成型机的胎胚自动称重装置。
背景技术:[0002]
在现有的全钢子午线轮胎制造过程中,胎胚重量的检测为移动式液压称重装置。质检人员检查时,需要推着移动式液压电子称到现场,从成型机存放胎胚工装四工位小车上,将胎胚通过人工翻抬至液压电子称上进重量检测,有些轮胎规格的重量和尺寸比较大,需要两人配合才能完成此项检测工作。因为该检查方式检测效率低,劳动强度大,且存在有一定安全隐患,所以只能对现场生产的胎胚进行抽样检查,无法做到对每条胎胚进行逐条称重记录,从而不能实时有效的控制胎胚重量合格率,也不能做到事前控制,也影响到成型机运行效率。
技术实现要素:[0003]
为了解决现有技术中的问题,本实用新型实施提供一种检测效率高、降低劳动强度以及减少成本的成型机的胎胚自动称重装置。
[0004]
为了实现上述目的,本实用新型采用了以下的技术方案:
[0005]
一种成型机的胎胚自动称重装置,包括
[0006]
底座,其设置在卸胎器一侧;
[0007]
平台秤,其设置在底座上方;
[0008]
支撑机构,其设置在平台秤的上方,包括设置在平台秤上的传动组件以及设置在传动组件上用于承接胚胎的承接件;
[0009]
数字显示控制盒,其与平台秤连接,传送显示称重数值。
[0010]
作为优选方案的,所述传动组件包括安装在平台秤上的承胎支架以及与承胎支架活动连接的至少两个连接件,所述承接件设置在连接件上。
[0011]
作为优选方案的,所述的传动组件上设有两个连接件,所述两个连接件相对设置在承台支架的两侧,所述连接件可在承胎支架上进行开合动作,进而带动承接件的开合。
[0012]
作为优选方案的,所述传动组件还包括滑动件,所述的连接件具有支撑臂以及连接杆,所述连接杆与支撑杆连接于一点并铰接至承胎支架上,所述两个连接杆另一端通过滑动件连接,所述滑动件可相对平台秤上下运动,进而联动连接杆运动,从而实现连接件的开合。
[0013]
作为优选方案的,所述的支撑臂与连接杆初始时形成的夹角不小于90度。
[0014]
作为优选方案的,所述的承接件为帆布兜。
[0015]
作为优选方案的,所述装置上还设有报警提醒件。
[0016]
本实用新型与现有技术相比,具有以下优点:
[0017]
本实用新型设置在卸胎器的左下方,当操作工人按下自动卸胎按钮时,卸胎器开始向左侧直线移动,当卸胎器向左直线移动到本装置位置时停止,后卸胎器开始下降,直至
卸胎器上的胎胚放置在支撑机构的承接件上 ,传动组件收到胎胚的重力作用,带动承接件与胎胚运动,直至卸胎器完全脱开胎胚位置,平台秤开始称重,称重后数值显示在数字显示控制盒上,并通过工业以太网线把数据传输到mes柜上进行记录保存,称重完成后,卸胎器把胎胚托起并上升到等待位时停止上升,停止上升后卸胎器开始向左直线移动,把胎胚放置到胎胚小车上,放置完后卸胎器返回到等待位,成型工序在生产胎胚的过程中,不再通过移动式液压电子称人工的去抽查称重,通过在成型机卸胎器下方加装一套自动称重装置,在轮胎卸到胎胚小车之前对胎胚先进行称重,并把称重后得到的数据在现场显示并传输到生产mes系统上,对每条轮胎的重量数据进行记录,对胎胚称重过程实现自动化,提高了检测效率,降低了工作人员的劳动强度,同时还有对超标准值的进行报警提醒设置,甚至对其进行停机控制,本实用新型在不影响成型设备运行效率的基础上,实现胎胚在线实时检测,来有效的控制胎胚重量合格率,来保证轮胎的一致性。
附图说明
[0018]
图1为本实用新型整体结构示意图;
[0019]
图2为本实用新型结构示意图1;
[0020]
图3为本实用新型结构示意图2;
[0021]
图4为本实用新型结构示意图3;
[0022]
图5为胎胚卸胎机构俯视图。
具体实施方式
[0023]
下面详细描述本发明的实施例,所述实施例的示例在附图中示出,其中自始至终相同或类似的标号表示相同或类似的元件或具有相同或类似功能的元件。下面通过参考附图描述的实施例是示例性的,旨在用于解释本发明,而不能理解为对本发明的限制。
[0024]
在本发明的描述中,需要理解的是,术语
ꢀ“
上”、“下”、“前”、“后”、“左”、“右”、“竖直”、“水平”、“顶”、“底”“内”、“顺时针”、“逆时针”等指示的方位或位置关系为基于附图所示的方位或位置关系,仅是为了便于描述本发明和简化描述,而不是指示或暗示所指的方法或元件必须具有特定的方位、以特定的方位构造和操作,因此不能理解为对本发明的限制。
[0025]
在本发明中,除非另有明确的规定和限定,术语“安装”、“相连”、“连接”、“固定”、“固持”等术语应做广义理解,例如,可以是固定连接,也可以是可拆卸连接,或一体地连接;可以是机械连接,也可以是电连接;可以是直接相连,也可以通过中间媒介间接相连,可以是两个元件内段的连通。对于本领域的普通技术人员而言,可以根据具体情况理解上述术语在本发明中的具体含义。
[0026]
为了使本发明的目的、技术方案及优点更加清楚明白,以下结合附图及实施例,对本发明进行进一步详细说明。应当理解,此处所描述的具体实施例仅用以解释本发明,并不用以限定本发明。
[0027]
如图1至图5所示,一种成型机的胎胚自动称重装置,包括
[0028]
底座1,其通过膨胀螺丝固定在卸胎器13左下方;
[0029]
平台秤2,其设置在底座1上方;
[0030]
支撑机构,其设置在平台秤2的上方,包括设置在平台秤2上的传动组件7以及设置在传动组件7上用于承接胚胎11的承接件10, 所述的承接件10上具有承接胚胎11的承接面,所述传动组件7被构造成可控制承接面展开或者收合的结构;
[0031]
数字显示控制盒8,其与平台秤2连接,传送显示称重数值。
[0032]
本实用新型设置在卸胎器13的左下方,当操作工人按下自动卸胎按钮时,卸胎器13开始向左侧直线移动,当卸胎器13向左直线移动到本装置位置时停止,后卸胎器13开始下降,直至卸胎器13上的胎胚11放置在支撑机构的承接件10上 ,传动组件7收到胎胚11的重力作用,带动承接件10与胎胚11运动,直至卸胎器13完全脱开胎胚11位置,平台秤2开始称重,称重后数值显示在数字显示控制盒8上,并通过工业以太网线把数据传输到mes柜17上进行记录保存,称重完成后,卸胎器13把胎胚11托起并上升到等待位时停止上升,停止上升后卸胎器13开始向左直线移动,把胎胚11放置到胎胚小车14上,放置完后卸胎器13返回到等待位,成型工序在生产胎胚11的过程中,不再通过移动式液压电子称人工的去抽查称重,通过在成型机卸胎器下方加装一套自动称重装置,在轮胎卸到胎胚小车14之前对胎胚11先进行称重,并把称重后得到的数据在现场显示并传输到生产mes系统上,对每条轮胎的重量数据进行记录,对胎胚称重过程实现自动化,提高了检测效率,降低了工作人员的劳动强度,同时还有对超标准值的进行报警提醒设置,甚至对其进行停机控制,本实用新型在不影响成型设备运行效率的基础上,实现胎胚在线实时检测,来有效的控制胎胚重量合格率,来保证轮胎的一致性。
[0033]
进一步地,如图2所示,所述传动组件7包括安装在平台秤2上的承胎支架4以及与承胎支架4活动连接的至少两个连接件8,所述承接件10设置在连接件8上,所述连接件8可联动承接件10运动。
[0034]
进一步地,如图1至图5所示,所述的传动组件7上设有两个连接件8,所述两个连接件8相对设置在承胎支架4的左右两侧,所述连接件8可在承胎支架4上进行开合动作,进而带动承接件10的开合,所述传动组件7还包括滑动件6,所述的连接件8具有两个支撑臂81以及两个连接杆82,所述两个支撑臂81与两个连接杆82,一个支撑臂81与一个连接杆82搭配的方式设置在承胎支架4的前后两侧,支撑臂81上端都与承接件10连接,左右两侧的连接件8可将承接件10合拢或者张开,所述每个连接杆82外侧与其对应的支撑臂81下端连接于一点并铰接至承胎支架4上,所述左右两侧的连接杆82内侧通过滑动件6连接,所述承胎支架4前后两侧中部对称设置有导轨滑块3,所述每个连接件8上都设有导轨底座9,所述滑动件6为导轨,所述导轨与导轨滑块3滑动配合,导轨受到胎胚11力的作用可相对平台秤2直线上下运动,导轨带动导轨底座9向下移动,进而联动连接杆82内侧向下运动,则两个连接杆82外侧则向内侧运动从而实现连接件8的收拢,并完全夹紧胎胚11,而后装置12开始称重,称重后数值显示在数字显示控制盒16上,并通过工业以太网线把数据传输到mes柜17上进行记录保存,称重完成后,卸胎器13把胎胚11托起并上升到等待位时停止上升,停止上升后卸胎器13开始向左直线移动,把胎胚放置到胎胚小车上,放置完后卸胎器返回到等待位;称重的全过程实现自动化,无需人工对胎胚11进行称重,降低了劳动强度;而且采用承接件10与胎胚11接触,而后连接件8运动直至胎胚11与卸胎器13完全脱离,防止胎胚11放置过程中对平台秤2冲击力太多造成损伤,设置连接件8与承接件10结合方式,可起到缓冲作用;同时在胚胎11下降的过程中,连接件8可带动承接件10合拢或者张开,防止胎胚11掉落,造成安全
事故。
[0035]
进一步地,如图2所示,所述的支撑臂81与连接杆82初始时形成的夹角不小于90度,方便胎胚的放置。
[0036]
进一步地,如图1所示,所述的承接件10为帆布兜,防止胎胚11的滑落。
[0037]
进一步地,所述装置12上还设有报警提醒件,对超标准值的进行报警提醒,实现胎胚11在线实时检测,来有效的控制胎胚11重量合格率,来保证轮胎的一致性。
[0038]
应当指出,以上实施例仅是本发明的代表性例子。本发明还可以有许多变形。凡是依据本发明的实质对以上实施例所作的任何简单修改、等同变化与修饰,均应认为属于本发明的保护范围。