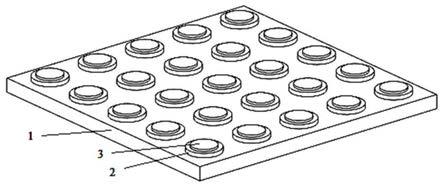
1.本实用新型涉及在坐标测量机等可编程控制检测设备上使用的可提高检测效率的辅具,具体为一种阵列式检测用辅具。
背景技术:2.加工制造领域经常会有大批量的零部件要求对其尺寸、形位公差等进行检测,这些尺寸、形位公差原多用手工检测或应用测长机、工具显微镜、圆柱度仪等不同的检测仪器设备分别进行检测,检测效率非常低。
3.应用坐标测量机等可编程控制检测设备进行检测后,虽可在一台仪器设备上完成大多数检测项目的检测,无需多台检测仪器设备配合,检测效率有所提高,但在坐标测量机上进行检测时,目前采用的方法仍是单件装夹、单件检测的方式,每次只能装夹一个零件,每检测一个零件后,需要人工更换装夹下一个零件,而在装夹过程中坐标测量机需停机等待,当检测批量大时,人工装夹次数多,坐标测量机停机等待时间累计较长,因此整体检测效率仍较低,不能充分发挥坐标测量机等可编程控制检测设备快速、自动化检测的优势。另外,单个零件的检测时间通常较短,且每件零件均需人工进行卸除和装夹,故成批检测时始终需要有人值守,来完成重复机械的零件装夹工作,导致检测人员无法抽身去完成其他工作,整个检测过程人员占用较大。
技术实现要素:4.本实用新型为了解决现有坐标测量机单件装夹检测效率低的问题,提供了一种阵列式检测用辅具。
5.本实用新型是采用如下技术方案实现的:阵列式检测用辅具,包括底板,底板上均布固定有若干强磁铁,强磁铁上方连接固定有定位装置,定位装置由底板背面的螺钉固定。
6.各个定位装置横向间距均为a,纵向间距均为b,且横向位于最外侧的定位装置中心点距对应一侧底板边线的距离等于a/2,纵向位于最外侧的定位装置中心点距对应一侧底板边线的距离等于b/2。
7.使用时在各工位上定位吸附被测零件,使用坐标测量机等可编程控制检测设备在第一个零件上建立检测坐标系并进行检测,其余零件检测时只需按各工位间的横向距离和纵向距离进行偏移即可,无需为每个零件单独建立坐标系,从而节省大量重复建立坐标系的时间,进一步提高检测效率。检测程序编制时采用由左至右,由上至下的顺序循环方式进行,每个零件检测完毕后,程序将检测结果写入数据文件,并自动运行至下一工位继续检测,其间无需人工干预,待全部零件检测完毕后,再进行被测零件更换,开始下一检测周期。也可在其检测过程中间,将已检测完毕的零件进行更换,全部检测完毕后,立即进入下一检测周期,并更换上一检测周期中剩余未更换的零件,从而达到连续运行的目的,将检测效率进一步提高到极致。
8.各个定位装置横向间距均为a,纵向间距均为b,且横向位于最外侧的定位装置中
心点距对应一侧底板边线的距离等于a/2,纵向位于最外侧的定位装置中心点距对应一侧底板边线的距离等于b/2。当多个底板相邻放置时,相邻底板定位装置横向间距为a,纵向间距为b,从而实现底板阵列不论从横向还是纵向均可无限扩展,并且保证各定位装置横向间距纵向间距均不变。
9.本实用新型的有益效果如下:利用合理设计的底板、定位装置等结构,实现了零件的批量装夹检测。本实用新型具有以下优点,零件装夹采用强磁铁吸附装夹,定位准确,装夹牢固,操作方便快捷;零件装夹按规律阵列排放,大大简化坐标测量机等可编程控制检测设备的检测程序编制,通过检测程序的参数化、标准化,还可进一步提高编程效率,降低编程难度;一次可装夹多个零件顺序检测,大大减少装夹次数和设备停机等待次数,提高设备利用率和检测效率,减少人员占用;可通过组合拼接的方式对阵列的行数、列数进行无限扩展,组合拼接方式灵活,适应性强。
附图说明
10.图1为本实用新型结构示意图;
11.图2为底板结构示意图
12.图3为定位圆柱剖视结构示意图;
13.图4为本实用新型阵列组合拼接示意图。
14.图中:1
‑
底板,2
‑
强磁铁,3
‑
定位装置,4
‑
螺钉,5
‑
零件。
具体实施方式
15.阵列式检测用辅具,包括底板1,底板上均布固定有若干强磁铁2,强磁铁2上方连接固定有定位装置3,定位装置3由底板1背面的螺钉4固定。
16.各个定位装置3横向间距均为a,纵向间距均为b,且横向位于最外侧的定位装置3中心点距对应一侧底板1边线的距离等于a/2,纵向位于最外侧的定位装置3中心点距对应一侧底板1边线的距离等于b/2。
17.具体实施过程中,当被测零件的材料为铁磁性材料时,可直接吸附固定零件,当被测零件的材料为非铁磁性材料时,可将被测零件先用铁磁材料制作的转换夹具装夹后再吸附固定在工位上。
18.定位装置可根据被测零件实际形状或定位需求设计为定位销、定位孔、v形槽等各种形式。定位装置的定位误差控制在0.1mm以内。