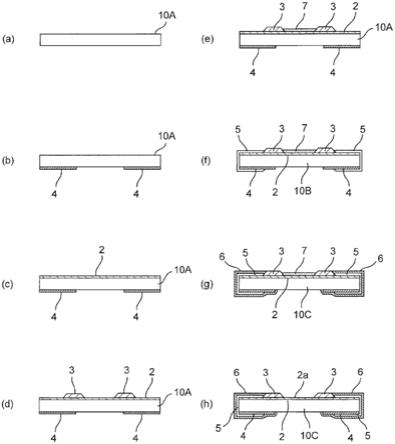
1.本发明涉及一种可以检测出腐蚀环境的累积硫化量的硫化检测传感器的制造方法。
背景技术:2.一般而言,作为芯片电阻器等电子元件的内部电极,虽使用电阻率低的ag(银)系电极材料,但当银暴露于硫化气体时,会成为硫化银。由于硫化银为绝缘物,电子元件可能发生断线等缺陷。因此,近年有些硫化对策,例如于ag添加pd(铯)或au(金)来形成难以硫化的电极、或将电极做成硫化气体难以到达的构造等。
3.然而,对于电子元件而言即使有如上述的硫化对策,在该电子元件长期暴露于硫化气体中的情况、或暴露于高浓度硫化气体中的情况下,仍难以完全防止断线。因此,预先检测断线来防止于未预期时点的故障发生成为必要的。
4.在现有技术中,如专利文献1所记载,提出一种检测电子元件的累积硫化的程度,可以在电子元件硫化断线等故障前检测危险性的硫化检测传感器。
5.在专利文献1中揭露如以下构成的硫化检测传感器:于绝缘衬底上形成以ag为主体的硫化检测体,以覆盖该硫化检测体的方式形成透明有硫化气体透过性的保护膜,同时在绝缘衬底的两侧端部形成连接硫化检测体的端面电极的构成。如上述构成的硫化检测传感器与其他电子元件一起设置到电路衬底上后,当该电路衬底使用于具有硫化气体的环境时,伴随着时间经过,其他电子元件被硫化,而且硫化气体透过硫化检测传感器的保护膜接触到硫化检测体,因此对应硫化气体的浓度与经过时间,构成硫化检测体的银的体积逐渐减少。因此,借由检测硫化检测体的电阻值的变化及断线,而可以检测硫化的程度。
6.又,在专利文献1中,揭露一种为了使硫化检测体可以高感度的检测硫化,不以保护膜覆盖硫化检测体使其露出于外部的硫化检测传感器。在如上述构成的硫化检测传感器的制造方法的情况,如图14(a)所示,准备可分为多个绝缘衬底的大型衬底100,在该大型衬底100的表面形成硫化检测体101,同时在大型衬底100的背面形成一对的背电极102后,在硫化检测体101的中央部形成由可溶性材料构成的保护膜103。接着,将大型衬底100沿着第1间隙来第1次分割为长条状衬底后,在长条状衬底的两端部借由涂布或蒸镀形成端面电极104。然后,将长条状衬底沿着第2间隙来第2次分割为与绝缘衬底相同尺寸的芯片衬底后,借由在该些芯片衬底依序实施ni电镀及sn电镀,形成覆盖硫化检测体101的两端部与端面电极104及背电极102的表面的外部电极105。其后,利用溶剂等将保护膜103除去,如图14(b)所示,可得到露出中央部的硫化检测体101被形成于绝缘衬底100a上的构成的硫化检测传感器。
7.专利文献1:特开2009
‑
250611号公报
技术实现要素:8.【本发明所要解决的问题】
9.若参照专利文献1所记载的上述硫化检测传感器,由于硫化检测体101在露出的状态下设置在电路衬底来被使用,而可对硫化的感度良好并高感度的检测硫化。然而,印刷树脂膏而形成的保护膜103的两端部会成为倾斜面,由于以紧密连接于像这样的保护膜103的倾斜面的方式来形成外部电极105的电镀材料,如图14(b)的箭头p所示,除去保护膜103后的外部电极105的端部会呈尖角状,而会有外部电极105容易剥离的问题。
10.本发明有鉴于现有技术的上述问题,本发明的目的为提供一种可以高感度的检测,并且防止外部电极的剥离的硫化检测传感器。
11.【为解决上述问题的技术方案】
12.为达成上述目的,本发明的硫化检测传感器的制造方法包含:导体形成步骤,在大型衬底的主面形成硫化检测导体;保护膜形成步骤,在前述硫化检测导体上形成包含不可溶性材料的一对第1保护膜,且形成包含可溶性材料的第2保护膜覆盖位在一对前述第1保护膜间的前述硫化检测导体;第1次分割步骤,在前述保护膜形成步骤后,对前述大型衬底进行第1次分割为长条状衬底;端面电极形成步骤,在前述长条状衬底的二分割面形成端面电极;第2次分割步骤,在前述端面电极形成步骤后,对前述长条状衬底进行第2次分割为多个芯片衬底;以及外部电极形成步骤,对前述芯片衬底进行电镀,在一对前述第1保护膜的外侧形成外部电极,且其中,将前述第2保护膜的表面高度设定为相对低于前述第1保护膜的表面高度。
13.经由如包含上述步骤的硫化检测传感器的制造方法,在电镀形成外部电极于将长条状衬底第2次分割所得的芯片衬底时,电镀材料虽附着于第1保护膜的端部,但不附着于第2保护膜,因此在除去第2保护膜使硫化检测导体的硫化检测部露出的制品状态下,紧密连接于第1保护膜的外部电极的端部不会产生角状的尖端部,而可同时具有硫化检测部露出于外部的感度良好的硫化检测传感器,并防止外部电极的剥离。又,由于第2保护膜的表面高度设定为相对低于第1保护膜的表面高度,即使在将端面电极从长条状衬底的端面侧溅镀来形成的情况,可利用第1保护膜阻隔溅镀膜,使其不形成于第2保护膜,在上下方向重迭复数的长条状衬底来进行溅镀时,则可抑止长条状衬底彼此间因包含可溶性材料的第2保护膜的黏着力而相黏的问题。
14.如上述的硫化检测传感器的制造方法中,更包含:内部电极形成步骤,在大型衬底的主面形成连接硫化检测导体的二端部的一对内部电极,且其中,将一对第1保护膜形成为覆盖硫化检测导体与内部电极的重叠部分。由于第1保护膜形成在硫化检测导体与内部电极重叠的积层部分之上,而可使第1保护膜的表面高度容易的相对高于第2保护膜的表面高度。
15.又,如上述的硫化检测传感器的制造方法中,更包含:电阻体形成步骤,在大型衬底的主面形成连接硫化检测导体的二端部的一对电阻体;内部电极形成步骤,形成连接该些电阻体的一对内部电极;以及调整步骤,在电阻体形成电阻值调整用的调整沟,且第1保护膜包含覆盖电阻体的底涂层与保护层,将外部电极形成为覆盖一对内部电极。由于电阻体及内部电极配置在夹设中央部的第2保护膜的对称位置,而可利用安定的状态来重叠多个长条状衬底。
16.又,如上述的硫化检测传感器的制造方法中,更包含:内部电极形成步骤,在大型衬底的主面形成与硫化检测导体具有预设间隔而对向的内部电极;电阻体形成步骤,形成
连接在硫化检测导体与内部电极间的电阻体;以及调整步骤,在电阻体形成电阻值调整用的调整沟,且其中,第1保护膜的一者包含覆盖电阻体的底涂层与保护层,且将第1保护膜的另一者形成在硫化检测导体上。在调整电阻体的电阻值时,可一边将探针连接于以下两者:位在第1保护膜的另一者的外侧的硫化检测导体、及连接于电阻体的内部电极,一边进行调整,而可防止因探针使硫化检测导体的硫化检测部损伤。
17.【发明效果】
18.经由本发明的硫化检测传感器的制造方法,可使硫化检测导体的硫化检测部露出而高感度的检测硫化,并且可防止电镀形成的外部电极的剥离。
附图说明
19.图1为本发明第1实施例的硫化检测传感器的平面图。
20.图2为沿图1的ii
‑
ii线的剖面图。
21.图3为表示该硫化检测传感器的制造步骤的平面图。
22.图4为表示该硫化检测传感器的制造步骤的剖面图。
23.图5为本发明第2实施例的硫化检测传感器的平面图。
24.图6为沿图5的vi
‑
vi线的剖面图。
25.图7为表示该硫化检测传感器的制造步骤的剖面图。
26.图8为本发明第3实施例的硫化检测传感器的平面图。
27.图9为沿图8的ix
‑
ix线的剖面图。
28.图10为表示该硫化检测传感器的制造步骤的剖面图。
29.图11为本发明第3实施例的硫化检测传感器的平面图。
30.图12为沿图11的xii
‑
xii线的剖面图。
31.图13为表示该硫化检测传感器的制造步骤的剖面图。
32.图14为表示现有技术的硫化检测传感器的制造步骤的剖面图。
33.其中,附图标记:
34.10、20、30、40
ꢀꢀꢀꢀꢀꢀꢀ
硫化检测传感器
[0035]1ꢀꢀꢀꢀꢀꢀꢀꢀꢀꢀꢀꢀꢀꢀꢀꢀꢀ
绝缘衬底
[0036]
2、22、33、42
ꢀꢀꢀꢀꢀꢀꢀꢀ
硫化检测导体
[0037]
2a、22a、33a、42a
ꢀꢀꢀꢀ
硫化检测部
[0038]
3、23
ꢀꢀꢀꢀꢀꢀꢀꢀꢀꢀꢀꢀꢀꢀ
第1保护膜
[0039]4ꢀꢀꢀꢀꢀꢀꢀꢀꢀꢀꢀꢀꢀꢀꢀꢀꢀ
背电极
[0040]5ꢀꢀꢀꢀꢀꢀꢀꢀꢀꢀꢀꢀꢀꢀꢀꢀꢀ
端面电极
[0041]6ꢀꢀꢀꢀꢀꢀꢀꢀꢀꢀꢀꢀꢀꢀꢀꢀꢀ
外部电极
[0042]
7、24、35、46
ꢀꢀꢀꢀꢀꢀꢀꢀ
第2保护膜
[0043]
21、31、41
ꢀꢀꢀꢀꢀꢀꢀꢀꢀꢀ
内部电极
[0044]
23、32、43
ꢀꢀꢀꢀꢀꢀꢀꢀꢀꢀ
电阻体
[0045]
34、44、45
ꢀꢀꢀꢀꢀꢀꢀꢀꢀꢀ
第1保护膜
[0046]
34a、44a、45a
ꢀꢀꢀꢀꢀꢀꢀ
底涂层
[0047]
34b、44b、45b
ꢀꢀꢀꢀꢀꢀꢀ
保护层
[0048]
10a、20a、30a、40a
ꢀꢀꢀ
大型衬底
[0049]
10b、20b、30b、40b
ꢀꢀꢀ
长条状衬底
[0050]
10c、20c、30c、40c
ꢀꢀꢀ
芯片状衬底
具体实施方式
[0051]
下面结合附图和实施例,对本发明的具体实施方式作进一步详细描述。图1为本发明第1实施例的硫化检测传感器的平面图。图2为沿图1的ii
‑
ii线的剖面图。
[0052]
如图1及图2所示,第1实施例的硫化检测传感器10主要由长方体形的绝缘衬底1、设置于绝缘衬底1的表面上的硫化检测导体2、以预设间隔设置于该硫化检测导体2上的一对的第1保护膜3、设置于绝缘衬底1的背面的长度方向两端部的一对的背电极4、设置于绝缘衬底1的长度方向两端部的一对的端面电极5、以及设置于端面电极5及背电极4的表面的一对的外部电极6所构成。
[0053]
硫化检测导体2为网版印刷(screen print)以银为主成分的ag系膏并干燥、烧制而成,该硫化检测导体2以覆盖绝缘衬底1的表面的方式形成。
[0054]
第1保护膜3为利用具有以下第2保护膜除去步骤中所使用的溶剂无法溶解的性质的不可溶性材料来构成,且网版印刷环氧(epoxy)系树脂膏并使其加热硬化。第1保护膜3形成在跨过硫化检测导体2的中央部而彼此间隔的两处,如下述,夹设在该一对的第1保护膜3的硫化检测导体2的中央部成为硫化检测部2a的中央部。
[0055]
一对的背电极4为网版印刷以银为主成分的ag系膏并干燥、烧制而成,该些背电极4与硫化检测导体2可利用不同的步骤形成,亦可同时形成。
[0056]
一对的端面电极5为在绝缘衬底1的端面溅镀ni/cr,涂布ag系膏并使其加热硬化。该些端面电极5以覆盖位在第1保护膜3外侧的硫化检测导体2的两端部及对应其的背电极4的方式形成为剖面是
コ
字形。
[0057]
一对的外部电极6为阻障(barrier)层与外部连接层的二层构造所构成,其中阻障层为借由电镀形成的ni电镀层,外部连接层为借由电镀形成的sn电镀层。从端面电极5露出的背电极4的表面及端面电极5的表面全部,经由该些外部电极6而被覆盖。
[0058]
接着,利用图3及图4说明硫化检测传感器10的制造步骤。图3(a)~(h)为使用于制造步骤中大型衬底的俯视平面图。图4(a)~(h)分别为表示沿图3(a)~(h)的长度方向中央部相当于1个芯片的剖面图。
[0059]
首先,如图3(a)及图4(a)所示,准备可分为多个绝缘衬底1的大型衬底10a。在该大型衬底10a预先设有格子状的第1次分割沟及第2次分割沟,借由二分割沟区分的各个方形会成为单个的芯片区域。在图3中,虽以相当于单个的芯片区域的大型衬底10a为代表来显示,以下说明的各步骤实际上是针对相当于多个芯片区域的大型衬底来进行。
[0060]
换句话说,如图3(b)及图4(b)所示,将ag系膏(ag
‑
pd20%)网版印刷在该大型衬底10a的背面后,经由干燥、烧制来形成以预设间隔对向的一对的背电极4(背电极形成步骤)。
[0061]
接着,在大型衬底10a的表面网版印刷以ag为主成分的ag系膏后,经由干燥、烧制,如3(c)及图4(c)所示,形成在大型衬底10a的表面延伸在长度方向的硫化检测导体2(导体形成步骤)。背电极4及硫化检测导体2的形成顺序可相反,背电极4及硫化检测导体2亦可同时形成。
[0062]
接着,在硫化检测导体2的表面网版印刷环氧系树脂膏,经由加热硬化,如3(d)及图4(d)所示,在硫化检测导体2的靠近中央的二处形成具有不可溶性材料的第1保护膜3(第1保护膜形成步骤)。第1保护膜3可为单层构造,亦可经由二层以上的多层构造来形成膜厚较厚的第1保护膜3。
[0063]
接着,以覆盖夹置于一对的第1保护膜3间的硫化检测导体2的露出部的方式网版印刷酚(phenol)树脂等可溶性树脂膏,经由加热硬化,如3(e)及图4(e)所示,形成覆盖一对的第1保护膜3间的硫化检测导体2的第2保护膜7(第2保护膜形成步骤)。第2保护膜7具有溶解于溶剂的性质,且由不溶解于以下步骤的外部电极形成步骤中使用的电镀液的可溶性材料所构成。第2保护膜7的表面高度形成为相对低于第1保护膜3的表面高度。较佳为,利用黏度低于第1保护膜3的低黏度材料来形成第2保护膜7,可较容易形成膜厚较薄的第2保护膜7。
[0064]
接着,沿着第1次分割沟将大型衬底10a第1次分割为长条状衬底10b后(第1次分割步骤),经由在长条状衬底10b的分割面溅镀ni/cr,如图3(f)及图4(f)所示,在长条状衬底10b的二分割面形成一对的端面电极5覆盖硫化检测导体2的长度方向二端部及背电极4的大部分(端面电极形成步骤)。溅镀对上下方向堆叠的多个长条状衬底10b来进行,进行时,由于第1保护膜3比第2保护膜7更突出于上方,设在任意的长条状衬底10b的一对的第1保护膜3会成为邻接于配置在上段侧的长条状衬底10b的下表面。由此,以第1保护膜3来阻隔溅镀膜而可使其不会到达第2保护膜7,而且在以下的步骤,为易于除去第2保护膜7,即使第2保护膜7在低温硬化下仍有黏着力,仍可防止上下重叠的长条状衬底10b彼此因第2保护膜7的黏着力而附着。除了在长条状衬底10b的分割面溅镀ni/cr,亦可经由涂布ag系膏并加热硬化来形成端面电极5。
[0065]
接着,沿着第2次分割沟将长条状衬底10b第2次分割为多个芯片状衬底10c后(第2次分割步骤),经由对该些芯片状衬底10c实施电镀来形成ni
‑
sn电镀层,如图3(g)及图4(g)所示,形成一对的外部电极6覆盖端面电极5的表面整体及背电极4的露出部分(外部电极形成步骤)。
[0066]
接着,将芯片状衬底10c浸渍于不溶解第1保护膜3且溶解第2保护膜7的碱性(alkali)溶液等,来除去第2保护膜7,如图3(h)及图4(h)所示,以使在一对的第1保护膜3间的硫化检测导体2的硫化检测部2a露出(第2保护膜除去步骤),而完成图1、2所示的硫化检测传感器10。另一方面,第2保护膜除去步骤也可以在电路衬底组装后再进行,在该情况,可保护硫化检测部2a直到被组装至电路衬底。
[0067]
如上述说明,在第1实施例的硫化检测传感器10的制造方法中,在电镀形成外部电极6于将长条状衬底10b第2次分割所得的芯片状衬底10c时,由于外部电极6的电镀材料不会附着于第2保护膜7,即使在除去第2保护膜7使硫化检测部2a露出于外部的情况,紧密连接于第1保护膜3的外部电极6的端部仍不会产生角状的尖端部。因此,可具有使硫化检测部2a露出的高感度硫化检测传感器10,亦可防止外部电极6的剥离。又,由于第2保护膜7的表面高度设定为相对低于第1保护膜3的表面高度,即使在从长条状衬底10b的端面侧以溅镀形成端面电极5的情况,可利用第1保护膜3阻隔溅镀膜来阻止溅镀膜形成在第2保护膜7。再者,由于第2保护膜7的表面高度设定为相对低于第1保护膜3的表面高度,在长条状衬底10b上下方向多段重叠进行溅镀时,可抑止因为由可溶性材料构成的第2保护膜7的黏着力使得
长条状衬底10b彼此黏着。
[0068]
图5为本发明第2实施例的硫化检测传感器20的平面图。图6为沿图5的vi
‑
vi线的剖面图。对应于图1、2的部分利用相同的符号,并省略重复的说明。
[0069]
如图5及图6所示,在第2实施例的硫化检测传感器20中,形成一对的内部电极21在绝缘衬底1的表面的长度方向两端部,硫化检测导体22的两端部以重叠该些内部电极21的方式作连接。一对的第1保护膜23以覆盖硫化检测导体22与内部电极21的重叠部分的方式来形成,硫化检测导体22的硫化检测部22a露出于二第1保护膜23间。上述以外的构成,基本上与第1实施例的硫化检测传感器10相同。
[0070]
接着,根据图7所示的剖面图说明本实施的硫化检测传感器20的制造步骤。首先,如图7(a)所示,将ag系膏(ag
‑
pd20%)网版印刷在大型衬底20a的背面后,经由干燥、烧制来形成以预设间隔对向的一对的背电极4(背电极形成步骤)。又,与之同时或者一前一后,在大型衬底20a的表面网版印刷以ag为主成分的ag系膏(ag
‑
pd20%)后,经由干燥、烧制,如7(b)所示,形成以预设间隔对向的一对的内部电极21(内部电极形成步骤)。
[0071]
接着,在大型衬底20a的表面网版印刷ag系膏后,经由干燥、烧制,如7(c)所示,形成连接一对的内部电极21的硫化检测导体22(导体形成步骤)。硫化检测导体22与内部电极21以两者的端部彼此重叠的方式来连接,因此该重叠部分为膜厚较厚的二层构造。
[0072]
接着,以覆盖硫化检测导体22与内部电极21的重叠部分的方式网版印刷环氧系树脂膏,经由加热硬化,如7(d)所示,在硫化检测导体22的两端部形成具有不可溶性材料的第1保护膜23(第1保护膜形成步骤)。
[0073]
接着,在夹置于一对的第1保护膜23间的硫化检测导体22的表面网版印刷酚树脂等可溶性树脂膏,经由加热硬化,如7(e)所示,形成覆盖一对的第1保护膜23间的硫化检测导体22的第2保护膜24(第2保护膜形成步骤)。第2保护膜24具有溶解于溶剂的性质,且由不溶解于以下步骤的外部电极形成步骤中使用的电镀液的可溶性材料所构成。第2保护膜24的表面高度形成为相对低于第1保护膜23的表面高度。
[0074]
接着,沿着第1次分割沟将大型衬底20a第1次分割为长条状衬底20b后(第1次分割步骤),经由在长条状衬底20b的分割面涂布ag系膏并加热硬化,如图7(f)所示,在长条状衬底20b的二分割面形成一对的端面电极5连接内部电极21及背电极4两者(端面电极形成步骤)。除了在长条状衬底20b的分割面涂布ag系膏来形成端面电极5,与前述第1实施例相同的,亦可在长条状衬底20b的分割面溅镀ni/cr来形成端面电极5。
[0075]
接着,沿着第2次分割沟将长条状衬底20b第2次分割为多个芯片状衬底20c后(第2次分割步骤),经由对该些芯片状衬底20c实施电镀来形成ni
‑
sn电镀层,如图7(g)所示,形成一对的外部电极6覆盖端面电极5的表面整体、与内部电极21及背电极4的露出部分(外部电极形成步骤)。
[0076]
接着,将芯片状衬底20c浸渍于不溶解第1保护膜23且溶解第2保护膜24的碱性溶液等,来除去第2保护膜24,如图7(h)所示,以使在一对的第1保护膜23间的硫化检测导体22的硫化检测部2a露出(第2保护膜除去步骤),而完成图5、6所示的硫化检测传感器20。另一方面,第2保护膜除去步骤也可以在电路衬底组装后再进行,在该情况,可保护硫化检测部2a直到被组装至电路衬底。
[0077]
如上述说明,在第2实施例的硫化检测传感器20的制造方法中,于大型衬底20a的
表面形成连接硫化检测导体22的两端部的一对的内部电极21后,因在硫化检测导体22与内部电极21重叠积层部分上形成第1保护膜23,除了与第1实施例相同的作用效果以外,更可达成使第1保护膜23的表面高度容易的相对高于第2保护膜24的表面高度的效果。
[0078]
图8为本发明第3实施例的硫化检测传感器30的平面图。图9为沿图8的ix
‑
ix线的剖面图。对应于图1、2的部分利用相同的符号,并省略重复的说明。
[0079]
如图8及图9所示,在第3实施例的硫化检测传感器20中,形成一对的内部电极31在绝缘衬底1的表面的长度方向两端部,该些内部电极31间串联连接一对的电阻体32及硫化检测导体33。电阻体32被包含底涂层34a与保护层34b的二层构造的第1保护膜34所覆盖,硫化检测导体33的硫化检测部33a露出于该些第1保护膜34间。上述以外的构成,基本上与第1实施例的硫化检测传感器10相同。
[0080]
接着,根据图10所示的剖面图说明本实施的硫化检测传感器30的制造步骤。首先,如图10(a)所示,将ag系膏网版印刷在大型衬底30a的背面后,经由干燥、烧制来形成以预设间隔对向的一对的背电极4(背电极形成步骤)。
[0081]
接着,在大型衬底30a的表面网版印刷以ag为主成分的ag系膏后,经由干燥、烧制,如10(b)所示,在大型衬底30a的表面以彼此具有预设间隔来形成硫化检测导体33与一对的内部电极31(导体形成步骤及内部电极形成步骤)。由此,硫化检测导体33与一对的内部电极31以相同材料同时形成,硫化检测导体33与一对的内部电极31的间隔可没有偏差的来形成。
[0082]
接着,在大型衬底30a的表面表面网版印刷氧化钌等电阻体膏后,经由干燥、烧制,如10(c)所示,两端部形成连接硫化检测导体33及内部电极31的一对的电阻体32(电阻体形成步骤)。
[0083]
接着,以覆盖电阻体32的方式网版印刷玻璃膏,将玻璃膏干燥、烧制而形成底涂层34a后,从底涂层34a之上形成图未表示的调整沟来调整电阻值(调整步骤)。其后,以覆盖底涂层34a的方式来网版印刷环氧系树脂膏,经由加热硬化,如10(d)所示,在硫化检测导体33的两端部形成包含底涂层34a与保护层34b的二层构造的第1保护膜34(第1保护膜形成步骤)。
[0084]
接着,在硫化检测导体33的表面网版印刷酚树脂等可溶性树脂膏,经由加热硬化,如10(e)所示,形成覆盖一对的第1保护膜34间的硫化检测导体33的第2保护膜35(第2保护膜形成步骤)。第2保护膜35具有溶解于溶剂的性质,且具有不溶解于以下步骤的外部电极形成步骤中使用的电镀液的可溶性材料。第2保护膜35的表面高度形成为相对低于第1保护膜34的表面高度。
[0085]
接着,沿着第1次分割沟将大型衬底30a第1次分割为长条状衬底30b后(第1次分割步骤),经由在长条状衬底30b的分割面涂布ag系膏并加热硬化,如图10(f)所示,在长条状衬底30b的二分割面形成一对的端面电极5连接内部电极31及背电极4两者(端面电极形成步骤)。除了涂布ag系膏来形成端面电极5,与前述第1实施例相同的,亦可在长条状衬底30b的分割面溅镀ni/cr来形成端面电极5。
[0086]
接着,沿着第2次分割沟将长条状衬底30b第2次分割为多个芯片状衬底30c后(第2次分割步骤),经由对该些芯片状衬底30c实施电镀来形成ni
‑
sn电镀层,如图10(g)所示,形成一对的外部电极6覆盖端面电极5的表面整体、与内部电极31及背电极4的露出部分(外部
电极形成步骤)。
[0087]
接着,将芯片状衬底30c浸渍于不溶解第1保护膜34且溶解第2保护膜35的碱性溶液等,来除去第2保护膜35,如图10(h)所示,以使在一对的第1保护膜34间的硫化检测导体33的硫化检测部2a露出(第2保护膜除去步骤),而完成图8、9所示的硫化检测传感器30。另一方面,第2保护膜除去步骤也可以在电路衬底组装后再进行,在该情况,可保护硫化检测部2a直到被组装至电路衬底。
[0088]
如上述说明,在第3实施例的硫化检测传感器30的制造方法中,在夹住中央部的硫化检测导体33的两侧分别形成串联连接的电阻体32与内部电极31对后,因在覆盖二电阻体32的位置形成包含底涂层34a与保护层34b的二层构造的第1保护膜34,除了与第1实施例相同的作用效果以外,更可达成使第1保护膜23的表面高度容易的相对高于第2保护膜24的表面高度,而且可作为附有芯片电阻器的硫化检测传感器来使用,又,可经由与一般芯片电阻器相同的步骤,来制造硫化检测传感器30等效果。
[0089]
图11为本发明第4实施例的硫化检测传感器40的平面图。图12为沿图11的xii
‑
xii线的剖面图。对应于图1、2的部分利用相同的符号,并省略重复的说明。
[0090]
如图11及图12所示,在第4实施例的硫化检测传感器40中,于绝缘衬底1的表面的长度方向两端部,以预设间隔形成内部电极41与硫化检测导体42,内部电极41与硫化检测导体42间连接电阻体43。电阻体43被包含底涂层44a与保护层44b的二层构造的第1保护膜44所覆盖,在电阻体43及底涂层44a形成有调整电阻值用的调整沟(图未表示)。又,在硫化检测导体42的中央部形成有包含底涂层45a与保护层45b的二层构造的第1保护膜45。第1保护膜45与电阻体43上的第1保护膜44间露出硫化检测部42a。上述以外的构成,基本上与第1实施例的硫化检测传感器10相同。
[0091]
接着,根据图13所示的剖面图说明本实施的硫化检测传感器40的制造步骤。首先,如图13(a)所示,将ag系膏网版印刷在大型衬底40a的背面后,经由干燥、烧制来形成以预设间隔对向的一对的背电极4(背电极形成步骤)。
[0092]
接着,在大型衬底40a的表面网版印刷以ag为主成分的ag系膏后,经由干燥、烧制,如13(b)所示,在大型衬底40a的表面以彼此具有预设间隔来形成内部电极41与硫化检测导体42(导体形成步骤及内部电极形成步骤)。
[0093]
接着,在大型衬底40a的表面表面网版印刷氧化钌等电阻体膏后,经由干燥、烧制,如13(c)所示,两端部形成连接内部电极41及硫化检测导体42的电阻体43(电阻体形成步骤)。
[0094]
接着,在覆盖电阻体43的位置及硫化检测导体42的中央部网版印刷玻璃膏,将玻璃膏干燥、烧制而形成一对的底涂层44a、45a后,从覆盖电阻体43的底涂层44a之上形成图未表示的调整沟来调整电阻值(调整步骤)。同时,经由将一对的探针接触位在底涂层45a的外侧的硫化检测导体42及内部电极41,而可一边测定电阻体43的电阻值一边进行调整,因此可防止成为硫化检测部42a部分的硫化检测导体42受到探针的损伤。其后,以覆盖二底涂层44a、45a的方式来网版印刷环氧系树脂膏,经由加热硬化,如13(d)所示,在电阻体43上形成包含底涂层44a与保护层44b的二层构造的第1保护膜44,同时在硫化检测导体42的中央部形成包含底涂层45a与保护层45b的二层构造的第1保护膜45(第1保护膜形成步骤)。虽然第1保护膜44、45可为同时形成的相同构成(玻璃材料及树脂材料的二层构造),但由于硫化
检测导体42上的第1保护膜45不需进行调整,亦可仅由环氧树脂等的树脂材料来构成。又,当第1保护膜44与第1保护膜45的位置形成在绝缘衬底1的表面的对称位置,可消除方向性。
[0095]
接着,在硫化检测导体42的表面网版印刷酚树脂等可溶性树脂膏,经由加热硬化,如13(e)所示,形成覆盖一对的第1保护膜44、45间的硫化检测导体42的第2保护膜46(第2保护膜形成步骤)。第2保护膜46具有溶解于溶剂的性质,且由不溶解于以下步骤的外部电极形成步骤中使用的电镀液的可溶性材料所构成。第2保护膜46的表面高度形成为相对低于第1保护膜44、45的表面高度。
[0096]
接着,沿着第1次分割沟将大型衬底40a第1次分割为长条状衬底40b后(第1次分割步骤),经由在长条状衬底40b的分割面涂布ag系膏并加热硬化,如图13(f)所示,在长条状衬底40b的二分割面形成一对的端面电极5连接内部电极41及背电极4两者(端面电极形成步骤)。除了涂布ag系膏来形成端面电极5,与前述第1实施例相同的,亦可在长条状衬底40b的分割面溅镀ni/cr来形成端面电极5。
[0097]
接着,沿着第2次分割沟将长条状衬底40b第2次分割为多个芯片状衬底40c后(第2次分割步骤),经由对该些芯片状衬底40c实施电镀来形成ni
‑
sn电镀层,如图13(g)所示,形成一对的外部电极6覆盖端面电极5的表面整体、与内部电极41及背电极4的露出部分(外部电极形成步骤)。
[0098]
接着,将芯片状衬底40c浸渍于不溶解第1保护膜44、45且溶解第2保护膜46的碱性溶液等,来除去第2保护膜46,如图13(h)所示,以使在一对的第1保护膜44、45间的硫化检测导体42的硫化检测部42a露出(第2保护膜除去步骤),而完成图11、12所示的硫化检测传感器40。另一方面,第2保护膜除去步骤也可以在电路衬底组装后再进行,在该情况,可保护硫化检测部2a直到被组装至电路衬底。
[0099]
如上述说明,在第4实施例的硫化检测传感器40的制造方法中,在形成连接于内部电极41及硫化检测导体42间的电阻体43后,于覆盖电阻体43的位置形成第1保护膜44,并在硫化检测导体42的默认位置形成第1保护膜45,因在二第1保护膜44、45间使硫化检测部42a露出,除了与第1实施例相同的作用效果以外,更可达成在调整电阻体43的电阻值时,将一对的探针接触位在底涂层45a的外侧的硫化检测导体42及内部电极41,而防止硫化检测部42a受到探针的损伤的效果。