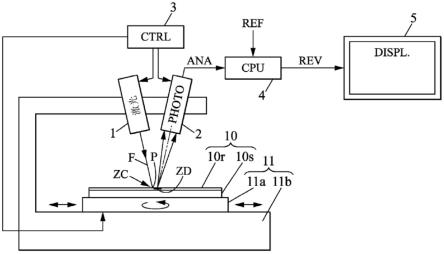
1.本说明书涉及一种用于揭露固体材料片件的表面上所存在的缺陷的光热分析方法和装置。
背景技术:2.已知通过使用光热分析的方法来揭露由至少一种固体材料组成的片件的表面部分中所存在的至少一个缺陷。此方法包括以下步骤:
3./1/将热量注入到片件的表面部分的第一区(称为加热区)中,接着在所注入热量已经部分扩散到所述片件的表面部分的另一区(称为检测区,且不同于加热区)中的周期之后,捕获检测区的至少一个热图像(称为分析图像);以及
4./2/至少针对分析图像的对应于检测区的部分,从分析图像中减去参考图像,以便获得展示此检测区中所存在的至少一个缺陷的揭露图像。
5.在从现有技术(例如,从文献wo 98/39641)已知的此方法中,实行步骤/1/若干次,每次在片件的表面部分内移动加热区以便随连续检测区扫描此表面部分。检测区连同加热区一起在片件的表面部分中移动,且每次重复步骤/1/时捕获新的分析图像。还针对步骤/1/的每一次执行重复步骤/2/。根据文献wo 98/39641,沿着同一扫描路径扫描待分析的同一表面部分两次,但两次是在扫描路径上的相对行进方向中进行。接着,各自已针对扫描路径上的不同行进方向捕获的与同一检测区相关的分析图像彼此相减以形成揭露图像。换句话说,针对第一扫描方向捕获的分析图像用作针对第二扫描方向捕获的分析图像的参考图像。如此获得的揭露图像揭露片件的表面部分中所存在的一些缺陷,其例如呈位于每一缺陷的任一侧的温差的形式,其中温差的符号取决于缺陷所在侧。实际上,如果缺陷导致片件中稍微较高的局部热阻,则缺陷和针对每一扫描方向朝向此缺陷移动加热区之间的热量累积到略微较大的程度。
6.此方法是有效的,但缺点是需要扫描片件的表面部分两次才能获得对应于两个相对扫描方向的分析图像。这导致每一片件的分析周期较长,难以与大规模生产的片件的高生产率调和。
7.技术问题
8.基于此情形,本发明的一目标在于,使得可以通过一种光热分析的方法以每一片件的较短分析周期检查片件。
9.本发明的另一目标是,通过光热分析提供具有比现有技术的已知方法所提供的更高的信噪比值的揭露图像。
技术实现要素:10.为了实现这些或其它目标中的至少一个,本发明的第一方面提出一种新的光热分析方法,其包括如上文所描述的步骤/1/和/2/,但针对其中片件的表面部分在检测区中无缺陷的情况,从分析图像中减去的参考图像对应于检测区中的热辐射分布,其由至少一部
分热量被注入到片件的表面部分中所导致。归因于使用此参考图像,单个分析图像对于每一检测区已足够,因此分析一个片件所需的周期大体上除以二。分析周期所节省的时间在待分析的表面部分较大且需要大量邻接检测区才能完全覆盖时越发显著。
11.此外,因为本发明的方法仅需要针对每一检测区捕获单个分析图像,所以相比于其中每一揭露图像是由若干分析图像的组合产生的方法,每一揭露图像所受到信噪比影响更小。
12.一般来说,对于本发明,分析图像中成像的检测区可包括加热区,但优选地其可相对于此加热区偏离中心或移位,在待分析的表面部分内与其邻接或隔开。
13.同样,一般来说,对于本发明,热量可借助于引导到此加热区上持续给定照射时间的激光束而注入到加热区中。此供应热量的方法实施起来尤其简单且快速。因此,其适于实现每一片件的较短分析周期。
14.在本发明的优选实施方案中,从分析图像中减去的参考图像可通过针对分析图像和热辐射分布的配置模型之间的最佳匹配的搜索而产生,所述热辐射分布的配置模型用于限定片件的表面部分在检测区中无缺陷的情况。
15.有可能用于限定片件的表面部分在检测区中无缺陷的情况的热辐射分布的此模型可对应于此检测区内的热扩散的稳态。确切地说,其可以是由提供温度值作为片件的表面部分内限定的两个几何坐标的函数的等式描述的热扩散的稳态。尤其是,此等式可包括两个几何坐标中的至少一个的高斯函数,所述高斯函数乘以恒定振幅因数,且加上恒定偏移项。
16.或者,从分析图像中减去的参考图像可从片件的表面的被视为不含缺陷的区(称为参考区)的热图像获得。在此情况下,在等同于步骤/1/的加热区和检测区的配置中,在一定的热量已在接近参考区处注入到片件中或注入到此参考区中之后,已捕获用于充当参考图像的此热图像。
17.优选地,通过在待分析的表面部分中运行扫描来实施所述方法,以便能够有效地应用于尺寸大于检测区的尺寸的片件。在此情况下:
[0018]-执行步骤/1/若干次,每次在片件的表面部分内移动加热区,以便在此表面部分中随着加热区的连续位置执行扫描,且针对加热区的每一位置捕获新的分析图像,检测区在片件的表面部分内连同加热区一起移动,使得片件的表面部分中的任意位置包含在检测区中至少一次;以及
[0019]-针对步骤/1/的每一次执行重复步骤/2/,每次使用在步骤/1/执行时指派给位于片件的表面部分中的检测区的参考图像。
[0020]
针对步骤/1/和/2/的不同重复,且为了获得单独地涉及待分析的表面部分中的检测区的相异位置的揭露图像,指派给这些相异检测区的参考图像可相同或不同。
[0021]
针对利用待分析的表面部分的扫描的本发明的此类实施方案,针对步骤/1/的每一次执行,检测区可相对于加热区根据扫描期间此加热区的移动方向向下游移位。因此,所述方法相比于导致检测区中的较渐进加热的配置具有较高的灵敏度。
[0022]
再次,针对利用扫描的此类实施方案,所述方法可进一步包括以下步骤:
[0023]
/3/使用应用于步骤/2/的多次执行期间获得的若干揭露图像的拼接、叠加、平均和/或平滑操作,重建片件的整个表面部分的总体图像,用于展示整个此表面部分中所存在
的缺陷。
[0024]
所述总体图像允许整个表面部分的快速且有效的视觉校验。
[0025]
一般来说,本发明的方法可用于由至少一种固体材料组成的所有类型的片件,包含冶金片件、至少部分由陶瓷材料组成的片件,或至少部分由复合材料组成的片件。确切地说,其可有利地用于分析涡轮喷气发动机或风扇的叶片、发电涡轮机的叶片、封闭或密封发电厂的容器的片件,或用于传动的机械片件。
[0026]
所述片件可任选地包括固体衬底和至少在待分析的表面部分中由此衬底承载的涂层。所述方法可接着用于显露可能存在于涂层中的任何裂缝。
[0027]
本发明的第二方面提出一种用于揭露由至少一种固体材料组成的片件的表面部分中所存在的至少一个缺陷的光热分析装置,此装置包括:
[0028]-热供应构件,其适于将热量注入到片件的表面部分的第一区(称为加热区)中;
[0029]-用于捕获热图像的构件,其被布置成捕获片件的表面部分的另一区(称为检测区且不同于加热区)的热图像(称为分析图像),所述用于捕获热图像的构件经控制以在由热供应构件注入的一部分热量已经从加热区扩散到检测区中的周期之后捕获每一分析图像;
[0030]-图像处理单元,其适于至少针对每一分析图像的对应于检测区的部分,从此分析图像中减去参考图像,以便获得展示此检测区中所存在的至少一个缺陷的揭露图像;以及
[0031]-可选地,扫描构件,其适于在片件的表面部分内移动加热区,以便在此表面部分中随加热区的连续位置执行扫描,所述检测区在片件的表面部分内连同加热区一起移动,使得片件的表面部分中的任意位置包含在检测区中至少一次。
[0032]
图像处理单元被调适成使得,针对所捕获的每一分析图像,针对其中片件的表面部分在检测区中无缺陷的情况,从所述分析图像中减去的参考图像对应于检测区中的热辐射分布,其由至少一部分热量被注入到片件的表面部分中所导致。
[0033]
此光热分析装置适于实施根据本发明的第一方面的方法,可能包含上文描述的优选实施方案和任选的改进。
附图说明
[0034]
参考附图,并通过以下非限制性实施方案的一些实例的详细描述将更清楚地展示本发明的特征和优点,其中:
[0035]
图1是根据本发明的光热分析装置的框图;以及
[0036]
图2示出使用根据本发明的方法扫描待分析的片件的一种可行配置。
具体实施方式
[0037]
为了清楚起见,这些图中所表示的元件的尺寸既不对应于实际尺寸也不对应于实际尺寸比率。此外,这些元件中的一些元件仅象征性地表示。
[0038]
根据图1,用于揭露可能存在于片件10的表面中的缺陷的光热分析装置包括热供应构件1和捕获热图像的构件2。热供应构件1可基于激光源,其中射束f被导向片件10的表面的用于局部接收能量流的区。激光源的波长被选择为使得激光辐射基本上由片件10吸收以便转换成热通量,所述热通量接着在片件10内扩散。此可例如为具有10.6μm(微米)的波长的co2激光产生辐射。片件10中如此生成的热通量致使其表面处在与接收激光束f的区相
隔一定距离处温度的局部增加。用于捕获热图像的构件2(标为photo)具有足够的灵敏度以检测由热供应构件1生成的片件10的表面的温度的局部增加。举例来说,用于捕获热图像的构件2可由微测辐射热计图像传感器组成,所述微测辐射热计图像传感器与被布置成将片件10的表面内的检测区与图像传感器的敏感表面光学耦合的聚焦光学件相关联。
[0039]
可提供控制器3(标为ctrl)用于以协调的方式控制热供应构件1和用于捕获热图像的构件2。光热分析的序列因而包括激活热供应构件1以便将一定的热量注入到片件10的表面的给定区(称为加热区且标为zc)中,且捕获位于片件10的表面内且接近加热区zc的检测区(标为zd)的热图像。加热区zc可对应于围绕片件10的表面中的目标点p的激光束f的横截面。在以热供应构件1的激活开始的给定持续时间之后捕获检测区zd的热图像,以便允许热量从加热区zc扩散到扩散区zd中。可在例如0.01s(秒)和0.5s之间的此持续时间由控制器3控制。由构件2如此捕获的热图像在图1中标为ana,且在本说明书的整体部分中被称作分析图像。其再现区zc中的加热之后由片件10在检测区zd中产生的热辐射辐射的空间变化。这些空间变化是由热量从加热区zc向检测区zd中扩散到片件10中而产生,所述扩散与片件10中在区zc和zd之间以及区zd内可能存在的任何缺陷所导致的扰动组合。热供应构件1和用于捕获热图像的构件2被定向成使得检测区zd接近片件10的表面中的加热区zc。可选地,如果未发生红外图像传感器的饱和,则检测区zd可含有加热区zc。然而,优选地,检测区zd与加热区zc邻接或彼此间隔开较小的分隔间隙。检测区zd的尺寸可为近似6mm(毫米)x 4mm,且加热区zc可以是直径为1mm的圆盘。
[0040]
根据本发明,图像处理单元4适于将分析图像ana与参考图像进行比较。图像处理单元4可由标为cpu的处理器组成,所述处理器经连接用于在输入处接收由用于捕获热图像的构件2递送的分析图像ana,并且还用于接收标为ref且称为参考图像的参考热图像。单元4被设计或编程以计算差分图像,所述差分图像是通过从分析图像ana的强度值点到点地减去参考图像ref的强度值而产生。当在检测区zd中不存在缺陷的情况下参考图像ref对应于片件10内热量的扩散时,所述差分图像以高对比度揭露其中存在的片件10的缺陷。出于此原因,在本说明书的整体部分中,差分图像一直称为用于展示检测区zd中所存在的至少一个缺陷的揭露图像,且已在图1中标为rev。
[0041]
我们现提供用以获得参考图像ref的不同方式。一般来说,有利的是,能够根据至少一个参数将参考图像ref调整为分析图像ana。这些调整参数可包括例如恒定乘法因数和同样恒定的附加项,这些应用于参考图像ref的图像点强度值的集合。尤其是,这些参数可允许消除对应于分析图像ana的捕获的实验情形和对应于参考图像ref的条件之间环境温度值以及注入到加热区zc中的热功率的值的偏差。还可作为补充或替代使用额外调整参数以将参考图像ref调整为分析图像ana,例如片件10中的温度降低的至少一个特性长度。温度降低的此特性长度可允许消除分析图像ana的捕获的实验情形和对应于参考图像ref的条件之间可能存在的热容量和热阻值的差异的影响。一般来说,可使用最佳匹配算法来根据分析图像ana调整参考图像ref的参数。
[0042]
根据本发明的第一可能的实施方案,参考图像ref可由一模型产生,所述模型描述由热量被注入到加热区zc中导致的检测区zd中的热辐射分布,且对应于热扩散的稳态。以已知方式,此稳态模型可对应于以下类型的检测区zd中的温度分布的等式:
其中t表示检测区zd中的局部温度,a是乘法调整因数,b是附加调整项,x和y是片件10的表面中限定的两个笛卡尔坐标,e
(.)
表示基本指数函数e,σ
x
和σy是分别沿着坐标x和y的两个标准偏差,且x0和y0是平行于片件10的表面的热分布模型的平移定位值。除参数a和b外,标准偏差σ
x
和σy的值以及x0和y0的值也可相对于分析图像ana调整。以已知方式,此温度分布是笛卡尔坐标x和y的参数化高斯函数。
[0043]
或者可使用其它模型来提供参考图像ref。确切地说,这些其它模型可考虑片件10的表面上的给定厚度层的存在,所述给定厚度层由不同于片件10的基底部分的涂层材料组成。其它模型还可考虑检测区zd中界面的存在,所述界面在构成片件10的邻近部分的两个不同材料之间,相对于片件10的表面垂直或倾斜地定向。另外其它模型可考虑加热区zc的可变形状,和/或加热区zc相对于检测区zd的可变位置。
[0044]
在本发明的其它可能实施方案中,参考图像ref可以是在表面的被认为不含缺陷的部分中待分析的片件10的利用图像捕获构件1捕获的热图像。表面的被认为不含缺陷的此部分在本说明书的整体部分中一直称为参考区。这些其它实施方案的优点在于以下事实:参考图像ref可对应于例如用于分析图像ana的实验参数。确切地说,注入到加热区zc中的能量的量、环境温度、加热区zc的形状、加热zc区和检测zd区的相对布置、片件10的材料、涂层在此片件的表面上的可能存在等因此可在分析图像ana和参考图像ref之间为相同的。
[0045]
由图像处理单元4计算的揭露图像rev可显示于标为displ的屏幕5上,以供由控制操作者检视。其揭露检测区zd内的片件10的相比于针对参考图像ref有效的扩散行为更改热扩散的方面。这些方面对应于片件10的缺陷,且可以是其表面中所存在的裂缝、不同阶段的杂质、片件10的表面涂层中的破裂等。可选地,为了进一步突出显示这些缺陷,可在图像显示于屏幕5上之前将高通型图像滤波器应用于揭露图像rev。举例来说,索贝尔型图像滤波器可用于此目的。
[0046]
此光热分析方法可尤其适于校验片件10不具有可能导致其后续使用期间的故障的任何缺陷。举例来说,片件10可以是航空涡轮喷气式压缩机的叶片,其由覆盖有薄层10r的固体衬底10s组成。层10r的功能可以是防止腐蚀。因而,本发明的光热分析方法可尤其用于检查层10r中的破裂的程度。
[0047]
如到目前为止对应于注入热量和捕获分析图像的单个序列所描述,为了快速检查可具有大于检测区zd的尺寸的尺寸的片件10的表面部分,可沿着扫描路径sc扫描待分析的片件10的表面部分(见图2)。连续采用的加热区的中心点遵循此扫描路径sc。热供应构件1和用于捕获热图像的构件2的相对位置和定向优选地是恒定的,但可相对于片件10移动。根据光热分析装置的一个可能配置,片件10可安装在支撑件11a上,所述支撑件11a可相对于装置的基底11b移动,所述基底相对于构件1和2固定。片件10可因此平行于其待分析的表面在两个相互垂直的方向中移动,且围绕垂直于这两个方向的轴线旋转。扫描构件11因此包括可移动支撑件11a、基底11b和控制器3的一部分,所述部分专用于以与构件1和2的触发同步的方式控制片件10的移动。
[0048]
图2是片件10的表面的待分析的部分的正视图,其展示扫描路径sc,所述扫描路径sc被设计成使得待分析的表面部分的所有位置包含在检测区内至少一次。加热区的中心点可针对片件10的连续位置在片件10的表面中遵循扫描路径sc,上文描述的静态光热分析的
序列在每一位置处实行。在此情况下,热供应构件1可间歇地和周期性地操作,例如针对片件的每一位置朝向片件10的表面发射激光脉冲。沿着扫描路径sc指示的点p指示加热区的中心的可能连续位置。为了缩短片件10的分析周期,可沿着扫描路径sc连续地按时间顺序实现这些位置p,对应于图2中指示的箭头。因而特别有利的是,为了增加所捕获的分析图像ana的对比度,以及根据本发明计算的揭露图像rev的对比度,在针对待分析的表面部分中的加热区的每一位置一个揭露图像rev的速率下,检测区相对于扫描方向位于加热区的下游。换句话说,待分析的表面中的同一个位置优选地首先在由构件2成像的检测区中出现,然后用作由构件1瞄准的加热区,或位于此加热区附近。图2中,p1指定对应于加热区zc1和检测区zd1的扫描路径sc上的加热区的中心点。所述检测区在针对含有点p1的路段的扫描路径sc上的箭头指示的行进方向中相对于加热区zc1偏移。类似地,p2指定对应于加热区zc2和检测区zd2的扫描路径sc上的加热区的另一中心点,其迟于点p1实现。检测区zd2接着在涉及含有点p2的路段的扫描路径sc上的箭头指示的行进方向中相对于加热区zc2移位。
[0049]
扫描路径sc优选地被设计成使得片件10的待分析的整个表面部分被与所有连续点p相关联的检测区覆盖。因此,对所有揭露图像rev分组可允许在用于在屏幕5上显示的全面的可视化图像中重建片件10的待分析的整个表面部分。可选地,不同检测区的重叠条带可存在于扫描路径sc中的相邻弯曲之间。可在个别揭露图像rev之间使用图像拼接操作,使得总体图像不含归因于其在单独部分中产生而导致的假影。以图像处理领域已知的方式,这些图像拼接操作可包括个别揭露图像的平均强度水平的校正、相邻揭露图像的相对位移以确保跨个别图像的边缘的图像图案的连续性、垂直于个别图像的边缘的图像点的强度水平的平滑等。
[0050]
因此,本发明使得可以通过执行片件10的整个表面部分的仅一次扫描来检查此表面部分。因此,校验的持续时间(称为分析周期)相比于需要在相对行进方向中运行扫描路径两次的光热分析方法得以缩短。当片件10的分析周期主要是归因于扫描而非归因于将片件10安装在可移动支撑件11a上时,分析周期所节省的时间大约为二的倍数。
[0051]
此外,在根据本发明的方法中每一揭露图像rev仅需要捕获单个分析图像ana的条件下,相比于其中从涉及同一检测区的两个分析图像之间的差推断每一揭露图像的现有技术的方法,每一揭露图像rev具有减小的信噪比值。实际上,在这些先前方法中,组合到一起的两个分析图像中的每一个受独立于另一分析图像的热成像噪声的随机热成像噪声影响。当揭露图像的信噪比(标为snr)根据公式以分贝(db)表达时,其中s是片件10的表面中的裂缝处的图像点的强度的变化的最大振幅,且b是如片件10的表面的被认为不含缺陷的参考区中测得的热成像噪声的最大振幅。对于由覆盖有防止腐蚀的薄层的固体衬底组成的待分析的片件,已实现信噪比的2.8到6.3倍的改进。
[0052]
应理解,可通过在保持所列举的优点中的至少一些优点的同时修改上文详细描述的实施方案的次要方面来再现本发明。确切地说,加热区zc可具有任何形状,尤其是,垂直于扫描路径sc定向的直线段的形状。类似地,检测区zd的形状不限于对应于热图像传感器的阵列的长方体。举例来说,检测区zd可具有半圆盘的形状,其焦点叠加在加热区zc的中心上,且可在扫描路径sc上相对于行进方向定向在所述加热区的下游。此外,已经列举的所有数值仅出于说明性目的,且可根据所涉及的应用而改变。