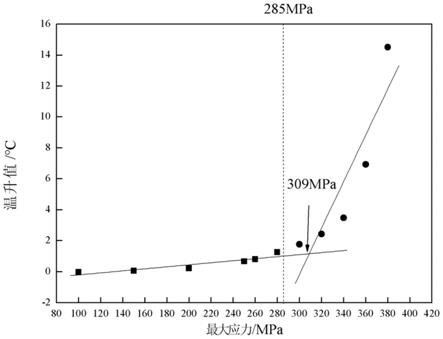
1.本发明涉及一种材料疲劳极限快速预测方法,具体涉及一种基于红外热成像的疲劳极限快速预测方法,属于材料力学性能测定,特别是材料疲劳可靠性评估技术领域。
背景技术:2.疲劳损伤是结构失效的主要形式,工程中有大量事故都是疲劳失效所引起。疲劳极限作为重要疲劳损伤参数,其传统测定方法如升降法和成组法,往往具有试验周期长,所需试样多,耗费时间人力物力巨大等特点;由于是基于数理统计方法,所得数据分散性也较大。因此,寻求更为经济、准确、高效的疲劳极限快速预测方法将具有重大的工程应用价值。
3.近年来,基于红外热成像技术(infrared thermographic technique)预测疲劳极限的方法由于具有实时、无损、非接触等特点广受国内外学者关注。目前基于红外热像技术的疲劳预测方法主要是基于risitano一线法和luong二线法,risitano等在对疲劳加载过程中材料表面温度的实时监测中发现,循环加载应力高于疲劳极限时,材料表面温度稳定阶段的温度值和应力大小有近似线性关系;而循环加载应力低于疲劳极限时,材料基本无明显温度变化,材料的疲劳极限可以通过对不同应力下温度稳定阶段的温升值与应力之间进行线性拟合来确定。luong等研究发现,即便在较低的载荷下,也存在能量耗散引发温升,而当应力升高到一定水平时,材料能量耗散就会发生突变,进而引起温升拐点,因此提出通过将疲劳极限之上和之下的两组温度数据分别进行线性拟合,得到两条直线的交点就是材料的疲劳极限。
4.目前luong提出的二线法具有广泛的应用,然而luong对如何判定温升拐点,进而进行二线拟合并没有给出规定,常常无法获取唯一可靠的疲劳极限值。因此需要结合能量耗散理论和材料疲劳损伤机理研究,确定唯一可信的温升拐点,以此拐点作为分界限进行二线拟合,以获取唯一可信的疲劳极限预测值。
技术实现要素:5.本发明提供了一种基于红外热成像的疲劳极限快速预测方法,用以准确、快速预测材料疲劳极限。
6.为实现上述目的,本发明采用如下技术方案:
7.一种基于红外热成像的疲劳极限快速预测方法,包括如下步骤:
8.(1)获取不同应力疲劳加载下材料表面温升值;
9.(2)利用拉伸实验获取材料弹性极限值;
10.(3)以弹性极限值作为分界限将温升数据分为两组;对两组温升数据分别进行线性拟合得到两直线,将两直线的交点所对应的应力值作为材料疲劳极限预测值。
11.上述疲劳极限快速预测方法,包括以下具体步骤:
12.(1)获取不同应力疲劳加载下材料表面温升值:在材料的试样表面喷涂一层黑色亚光漆,以提高辐射率,确保红外热像仪测温的准确度;进行疲劳试验,采取应力水平逐级
增高的加载方式,加载最大应力从小于材料弹性极限的应力值开始,直至材料在此级应力加载下断裂为止,每级应力循环至温升达到稳定值时停止,充分散热后,增高一级应力继续试验,在疲劳试验过程中,采用红外热像仪同步采集试样表面温度变化;
13.采用热像处理软件对温度数据进行输出和处理,绘制不同应力水平下的实时温度变化与循环周次的曲线图和不同应力水平下的稳定温升变化图;
14.(2)在万能材料试验机上进行拉伸实验,得到材料应力
‑
应变曲线,对弹性段进行线性拟合,弹性段最高点对应的应力即为弹性极限值;
15.(3)以弹性极限值作为分界限将温升数据分为两组,对两组温升数据分别进行线性拟合得到两条直线,两条直线的交点所对应的应力值即为疲劳极限预测值。
16.步骤(1)中,材料试样为矩形横截面试样,试样尺寸需满足gb/t 3075
‑
2008规定。
17.所述疲劳实验的设备为高频疲劳试验机。在疲劳试验的试验过程中,所选用红外热像仪需满足最大采集频率大于1hz,采集精度不小于0.03℃。
18.借助于热像处理软件对温度数据进行输出和处理,绘制不同应力水平下的实时温度变化与循环周次的曲线图;将稳定阶段温度平均值记为t
h
,环境温度记为t
a
,则温升δ
t
‑
t
h t
a
,绘制不同应力水平下的稳定温升变化图。
19.步骤(2)中,根据gb/t 228.1
‑
2010,在万能材料试验机上进行拉伸实验,得到材料的应力
‑
应变曲线;对弹性段进行线性拟合,弹性段最高点对应的应力即为弹性极限。
20.采用升降法来验证本发明疲劳极限预测方法获得疲劳极限预测值的真实性与可靠性,利用升降法获取材料疲劳极限试验值,将本发明方法得到的疲劳极限预测值与试验值进行对比,得到偏差值,结果表明,升降法测试结果与本发明疲劳极限预测值相吻合。
21.根据gb/t 3075
‑
2008,选取材料疲劳试样利用升降法获取疲劳极限,根据标准规定,试样在指定循环周次(本试样为1
×
107)内未出现疲劳断裂即为“通过”,否则,则视为“未通过”。根据实验结果得到疲劳极限值。
22.本发明基于红外热成像疲劳分析方法,具有以下优点:在luong二线法基础上,通过研究能量耗散引起的温升机制转变与材料微观组织演化关系,提出以弹性极限作为分界限对温升数据进行归集,进而进行二线拟合获取疲劳极限预测值。与其他红外热像法相比,该方法具有明确物理意义;与传统获取疲劳极限的方法相比,该方法具有试验过程简单,试验周期短,试验所需试件数量少等先进性,可以被广泛的应用于工程实践。
附图说明
23.图1为本发明实施例的疲劳试样的示意图。
24.图2为本发明实施例的疲劳加载过程示意图。
25.图3为本发明实施例的不同应力加载下温升随时间变化情况。
26.图4为本发明实施例的温升随最大应力的变化情况。
27.图5a为本发明实施例的工业纯钛ta1应力
‑
应变曲线(整体),图5b为本发明实施例的工业纯钛ta1弹性段的应力
‑
应变曲线(局部)。
28.图6为本发明实施例的确定疲劳极限过程。
29.图7为本发明实施例的升降法结果。
具体实施方式
30.下面将结合附图,对本发明实施例中的技术方案进行清楚、完整地描述,显然,所描述的实施例仅仅是本发明一部分实施例,而不是全部的实施例。基于本发明中的实施例,本领域普通技术人员在没有做出创造性劳动前提下所获得的所有其他实施例,都属于本发明保护的范围。
31.以下结合具体实施例,对本发明进行详细说明。
32.本发明所采用的材料为热轧退火态工业纯钛(ta1),试样为矩形横截面试样,其中平行段长度为10mm,宽度为8mm,试样厚度为4mm,具体尺寸如图1所示,加工完成后,用400#、800#、1000#、2500#sic砂纸打磨试样表面,去除表面加工缺陷及氧化物,获得光滑表面。实验前需在试样表面喷涂一层黑色亚光漆,以提高辐射率,确保红外热像仪测温的准确度。
33.疲劳实验设备为高频疲劳试验机。疲劳载荷为拉—拉载荷,应力比为0.1,振动频率为100hz;实验过程中用红外测温系统对试件表面温度的温度进行记录。
34.试验采取应力水平逐级增高的加载方式,加载最大应力分别为100mpa、150mpa、200mpa、250mpa、260mpa、280mpa、300mp、320mpa、340mpa、360mpa、380mpa,每级应力循环60000周次停止,充分散热后,增高一级应力继续试验,加载过程如图2所示。在疲劳试验试验过程中,采用infratec vh680红外热像仪同步采集试样表面温度变化,像素为640
×
480,最大采集频率为60hz,采集精度为0.03℃,红外录制频率为1hz,红外热像仪放置在试样前方0.4m处。
35.借助于irbis 3软件对温度数据进行输出和处理,绘制不同应力水平下的实时温度变化与循环周次的曲线图,如图3所示。将稳定阶段温度平均值记为t
h
,环境温度记为t
a
,则温升δt=t
h
‑
t
a
,绘制不同应力水平下的稳定温升变化图,如图4所示。
36.室温条件下,根据gb/t 228.1
‑
2010,在万能材料试验机上进行拉伸实验,拉伸实验速率为1
×
10
‑3s
‑1,得到工业纯钛ta1应力
‑
应变曲线(图5a),对弹性段进行线性拟合(图5b),弹性段最高点对应的应力即为弹性极限,相关参数如表1所示。
37.表1工业纯钛ta1相关力学性能
[0038][0039]
以弹性极限值285mpa作为分界限将图4所示温升数据分为两组,其中小于285mpa各点为一组,大于285mpa其余各点为另一组,对两组温升数据分别进行线性拟合得到两直线,两直线的交点所对应的应力值即为疲劳极限预测值,经计算,疲劳极限预测值为309mpa,如图6所示。
[0040]
为了验证本发明疲劳极限预测方法的真实性与可靠性,利用升降法获取材料疲劳极限试验值,将疲劳极限预测值与试验值进行对比,得到偏差值。
[0041]
根据gb/t 3075
‑
2008,选取16根工业纯钛ta1试样利用升降法获取疲劳极限,根据标准规定,试样在指定循环周次(本试样为1
×
107)内未出现疲劳断裂即为“通过”,否则,则视为“未通过”,试验结果如图7所示。对试验数据进行统计分析,选取7组数据做平均值,可以得到工业纯钛ta1在1
×
107循环周次下所对应的疲劳极限值为:
[0042][0043]
通过以上试验可以发现,升降法结果与本发明疲劳极限预测值相吻合,证明本发明方法能够实现工业纯钛ta1疲劳极限的快速预测。
[0044]
本发明方法通过获取不同应力疲劳加载下材料表面温升值;利用拉伸实验获取材料弹性极限值;以弹性极限值作为分界限将温升数据分为两组;对两组温升数据分别进行线性拟合得到两直线,将两直线的交点所对应的应力值作为材料疲劳极限预测值。通过本发明的方法最少只需要2根试样,1天时间就能实现材料疲劳极限的预测,且结果与升降法测量结果有很好的一致性,结果具有唯一性、准确性,而利用升降法则需要至少15根试样,3周时间,因此本方法在保证结果准确性的基础上,可实现试样数量和实验时间大幅减少,具有较高的工程实用价值和显著的经济效益。