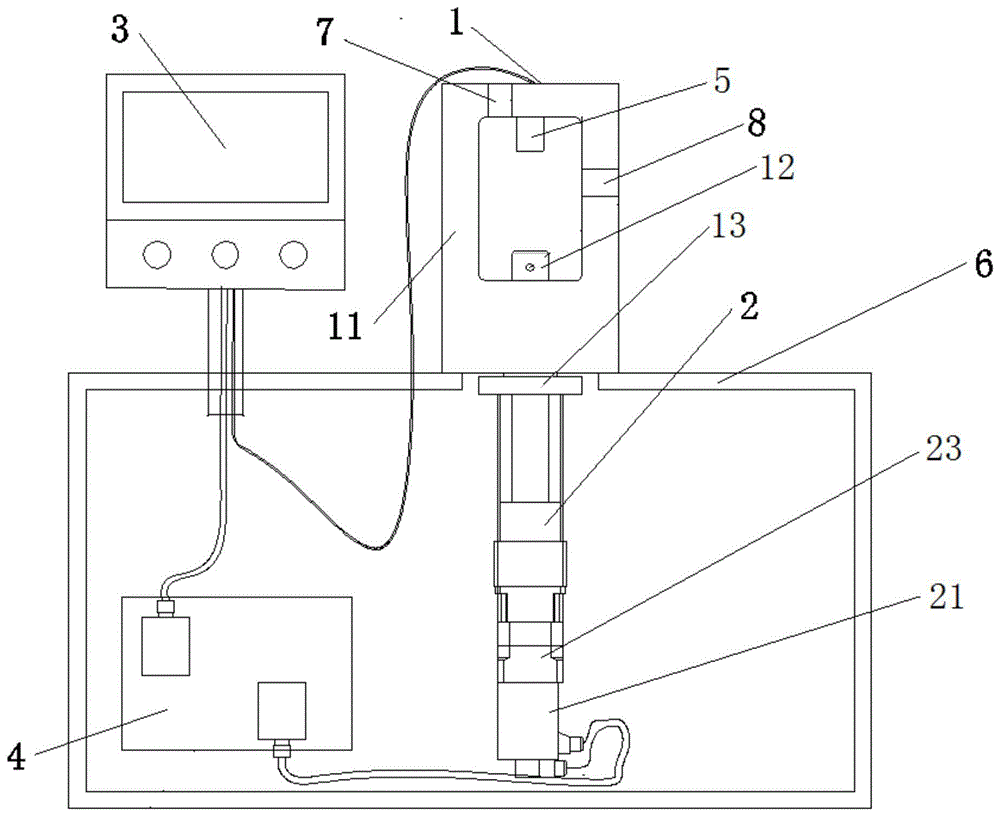
本发明涉及一种具有机械臂的微型重载单轴压力测试系统及测试方法,属于岩石力学试验
技术领域:
。
背景技术:
:《岩体力学》(或称《岩石力学》)是采矿工程、地质工程、水利水电工程、隧道工程、岩土工程、石油天然气开发工程、地下建筑工程等工科专业的核心课程,在该课程学习过程中,试验是必不可少的环节。岩石强度测试作为必做的试验项目,对辅助理论教学,培养学生动手操作能力、简历系统的岩石强度知识结构,具有重要作用和意义。岩石强度测试,包括岩石的抗压强度试验、岩石的抗拉强度试验、岩石的抗剪强度试验等,然而现有的岩石力学试验仪器以面向科研工作为主,其高购置成本、高维护费用和操作复杂的特点决定其必须由专职试验员操作,这些仪器很难面向学生开放,因而学生在试验学习中只能被动地听试验员讲解,不能动手操作,试验教学效果较差。而且,用于科研工作的岩石力学试验仪器体积大、重量大、液压系统结构复杂,不适用于学校的试验教学场地和多台套分组试验。现有岩石强度测试中动、静载荷的施加常采用油压加载方式,如中国专利文件cn110031321b公开的一种动静载叠加式岩石力学试验机及试验方法和中国专利文件cn111220463a公开的一种岩石单轴抗压强度预测系统与方法,这种加载结构在出现油路系统漏油问题时设备的检修操作复杂,设备维护成本高。已公布的用于学生操作的便携式剪切仪用油压压力杆施加压力,岩石点荷载试验仪用摇式油泵施加压力(付志亮,《岩石力学试验教程》,2010,66-67,70-71)在操控油压加压装置时存在试件载荷不稳定,读数不准确,无法获得全应力-应变试验结果以及岩石强度本构关系,而且现有技术中使用的位移传感器采用间隔输出数据,应变数据无法精准对应应力变化,影响岩石强度本构关系的确定。有鉴于此,本发明提供一种微型重载、测试精度高、易于操控的单轴压力测试系统,该系统测试方法简捷,试验数据完整,有利于学生获得完整的试验结果,理解岩石强度本构关系。技术实现要素:针对现有技术的不足,本发明提供一种具有机械臂的微型重载单轴压力测试系统,微型重载、测试精度高、易于操控,测试方法简捷,试验数据完整,有利于学生获得完整的试验结果,理解岩石强度本构关系。本发明还提供上述具有机械臂的微型重载单轴压力测试系统的测试方法。本发明的技术方案如下:一种具有机械臂的微型重载单轴压力测试系统,包括加载机构、传动机构、控制机构、配电机构和支撑座,其中,支撑座上设置加载机构,传动机构穿过支撑座连接加载机构,传动机构连接至控制机构,传动机构和控制机构均连接至配电机构,通过配电机构对传动机构和控制机构进行供电,控制机构控制传动机构对加载机构施加载荷。优选的,加载机构包括刚性框架和单轴机械臂,刚性框架设置于支撑座上,单轴机械臂通过折叠式法兰连接至刚性框架,通过单轴机械臂对刚性框架内的试件施加载荷。进一步优选的,刚性框架为一体浇筑实心方体刚性金属框架,连接强度高,刚性框架包括左立柱、右立柱、上梁和下梁,刚性框架的长×宽×高≥25×8×40cm,左立柱和右立柱的厚度均≥5cm,上梁的厚度≥5cm,下梁的厚度≥8cm,通过控制刚性框架尺寸,增大左立柱、右立柱和下梁的厚度提高刚性框架的承载能力,进而提高刚性框架对微型或标准试件的试验强度,实现微型重载。优选的,刚性框架材质采用金属材质低碳钢或铸铁,具体材质可根据实际需要进行调整,通过低碳钢或铸铁材质保证刚性框架加载时的变形符合刚度要求。优选的,刚性框架内顶端设置压力传感器,压力传感器对应单轴机械臂,压力传感器连接控制机构,通过压力传感器记录试件的受力情况。优选的,刚性框架内分别设置轴向形变光栅尺和径向形变光栅尺,通过轴向形变光栅尺和径向形变光栅尺记录试件受力后轴向和径向变化。优选的,传动机构包括伺服电机、减速机和滚珠丝杠,伺服电机通过轴键连接减速机,减速机通过联轴器连接滚珠丝杠,滚珠丝杠穿过支撑座和刚性框架连接单轴机械臂,伺服电机、减速机和滚珠丝杠为自下而上同轴加固连接。通过伺服电机控制滚珠丝杠运动,进而驱动单轴机械臂进行伸缩,通过控制单轴机械臂位移量,直接确定试件轴向变形,避免使用位移传感器,使应变数据精准对应应力变化。优选的,联轴器和折叠式法兰之间固定连接拉筋,保证整体直线度,提高固定强度。优选的,单轴机械臂顶端设置压头,方便安置试件,保证测试时试件受力均匀,通过下置压头配合刚性框架,共同提高微型重载能力。进一步优选的,单轴机械臂的位移精度数值≤0.1μm/s。上述具有机械臂的微型重载单轴压力测试系统在进行抗压强度和压缩蠕变测试时的测试方法,操作步骤如下:(1)制作圆柱形试件,记录试件尺寸、密度和比重,然后启动配电机构和控制机构,系统处于待机状态;(2)将试件放置于压头,控制机构控制伺服电机运转,通过滚珠丝杠带动单轴机械臂上升,进而带动试件上升,当压力传感器出现读数时停止伺服电机运转;(3)设定取样周期和压缩速度,然后开始压缩试验,伺服电机开始运转,通过滚珠丝杠带动单轴机械臂继续上升,伺服电机以≤0.1μm/s的位移加载速度或者以≤10n/s的压力加载速度进行加载,控制机构同时显示试件载荷数值及试件轴向形变和径向形变数值,并自动保存试验数据;(4)当试件出现破裂时,暂停伺服电机,记录此时轴向形变光栅尺显示的试件上端和下端位置,然后继续启动伺服电机进行压缩试验;(5)试件完全破坏时,停止压缩试验,导出试验数据,整个试验过程控制机构始终记录试件载荷数值、轴向形变和径向形变量。上述具有机械臂的微型重载单轴压力测试系统在进行抗拉测试时的测试方法,操作步骤如下:(1)制作圆柱形试件,记录试件尺寸、密度和比重,然后启动配电机构和控制机构,系统处于待机状态;(2)将试件放入巴西劈裂夹具内,再将巴西劈裂夹具放置在压头上,控制机构控制伺服电机运转,通过滚珠丝杠带动单轴机械臂上升,进而带动巴西劈裂夹具上升,当压力传感器出现读数时停止伺服电机运转;(3)设定取样周期和压缩速度,然后开始抗压试验,伺服电机开始运转,通过滚珠丝杠带动单轴机械臂继续上升,伺服电机以≤0.1μm/s的位移加载速度或者以≤10n/s的压力加载速度进行加载,巴西劈裂夹具受力拉伸试件,控制机构同时显示试件载荷数值及试件轴向形变和径向形变数值,并自动保存试验数据;(4)当试件出现破裂时,暂停伺服电机,记录此时轴向形变光栅尺显示的试件上端和下端位置,然后继续启动伺服电机进行抗压试验;(5)巴西劈裂夹具内试件完全破坏时,停止抗压试验,导出试验数据,整个试验过程控制机构始终记录试件载荷数值、轴向形变和径向形变量。上述具有机械臂的微型重载单轴压力测试系统在进行点载荷强度测试时的测试方法,操作步骤如下:(1)制作圆柱形试件,记录试件尺寸、密度和比重,然后启动配电机构和控制机构,系统处于待机状态;(2)在压头上放置圆锥状点载荷压头,将试件放在圆锥状点载荷压头上,试件上部放置圆锥状点载荷压头,测量试件上部的圆锥状点载荷压头与压力传感器之间距离,然后将测量距离设定为运行距离,控制机构控制伺服电机运转,通过滚珠丝杠带动单轴机械臂上升设定距离,此时试件上部的圆锥状点载荷压头刚好接触压力传感器;(3)设定取样周期和压缩速度,然后开始点载荷强度试验,伺服电机开始运转,通过滚珠丝杠带动单轴机械臂继续上升,伺服电机以≤0.1μm/s的位移加载速度或者以≤10n/s的压力加载速度进行加载,控制机构同时显示试件载荷数值及试件轴向形变和径向形变数值,并自动保存试验数据;(4)当试件出现破裂时,暂停伺服电机,记录此时轴向形变光栅尺显示的试件上端和下端位置,然后继续启动伺服电机进行点载荷强度试验;(5)试件完全破坏时,停止点载荷强度试验,导出试验数据,整个试验过程控制机构始终记录试件载荷数值、轴向形变和径向形变量。上述操作步骤可以在试件产生变形初期至完全破坏过程中,通过轴向形变光栅尺补充监测变形量,预设精密滚珠丝杠的前进导程,实现位移加载精密控制,从而获得试件的完全应力-应变曲线,能针对不同强度的不同材料试件进行测试,扩大了设备的应用范围。本发明的有益效果在于:1、本发明通过刚性框架配合下置压头实现了微型重载,且测试精度高、易于操控,测试方法简捷,试验数据完整,有利于学生获得完整的试验结果,理解岩石强度本构关系。2、本发明通过控制机构调整伺服电机工作,利用滚珠丝杠结构传动加载,避免了液压加载的复杂系统,从而精简了测试系统结构,利于设备的维护,节约维护成本。3、本发明对传动机构的精准控制实现了对单轴机械臂的精准定位,尤其是试件达到破坏变形前,单轴机械臂的前进位移量即试件轴向变形量,提高了试件轴向位移测试精度。4、本发明通过更换不同测试压头,能开展单轴抗压强度、点荷载强度、单轴拉伸强度和单轴压缩蠕变测试试验,提高了测试效率。5、本发明基于其微型重载的特点,除了测试岩石强度,还可以测试其它材料的力学强度,提高了试验设备的应用范围和利用率,同时其体积小、刚度大、操控简便,更加适用于试验教学。6、岩石强度测试试验中刚性框架的刚度影响着应力应变测试结果的准确性,若是中型或微型的组装式主体框架,当输出载荷较大时,主体框架的变形量容易对试验结果产生影响,致使试验结果误差大,如要满足试验结果误差小、获得应力应变的全过程曲线,则要求框架体积足够大、框架材料足够厚重,从而造成整个试验设备体积庞大。所以为了减小试验误差,提高精度,目前试验机普遍做成中型或者大型设备,体积大,占用面积大。作为教学试验设备,由于空间受限,一个学院或者一个单位往往只配备一台试验机,在进行压力教学试验时,一般都是由老师示范学生围观,教学效果差。本发明将试验机的刚性框架一体浇筑成整体,当输出载荷大于等于100kn时,在满足重型加载强度和主体框架刚度要求的条件下,将现有的的中型或大型设备做成微型的,同样的空间可以放置多台,在兼顾试验精度前提下满足了教学需求,同时也免去了组装的麻烦。附图说明图1为本发明的结构示意图;图2为本发明的传动结构示意图;图3为本发明的传动结构局部示意图;图4为本发明的传动机构剖视图;图5为本发明实施例1中的低碳钢数值模拟应力分布图;图6为本发明实施例1中的铸铁数值模拟应力分布图;图7为本发明实施例1中的低碳钢数值模拟应变分布图;图8为本发明实施例1中的铸铁数值模拟应变分布图;其中:1、加载机构;2、传动机构;3、控制机构;4、配电机构;5、压力传感器;6、支撑座;7、轴向形变光栅尺;8、径向形变光栅尺。11、刚性框架;12、单轴机械臂;13、折叠式法兰;21、伺服电机;22、滚珠丝杠;23、减速机;24、拉筋;25、轴键;26、联轴器。具体实施方式下面通过实施例并结合附图对本发明做进一步说明,但不限于此。实施例1:如图1-4所示,本实施例提供一种具有机械臂的微型重载单轴压力测试系统,包括加载机构1、传动机构2、控制机构3、配电机构4和支撑座6,其中,支撑座6上设置加载机构1,传动机构2穿过支撑座6连接加载机构1,传动机构2连接至控制机构3,传动机构2和控制机构3均连接至配电机构4,通过配电机构4对传动机构和控制机构进行供电,通过控制机构控制传动机构对加载机构施加载荷。配电机构为供电电路,通过外接电源为控制机构和传动机构供电。加载机构1包括刚性框架11和单轴机械臂12,刚性框架11设置于支撑座6上,单轴机械臂12通过折叠式法兰13连接至刚性框架11,通过单轴机械臂对刚性框架内的试件施加载荷。单轴机械臂为常规伸缩臂,内部设置中空内腔,滚珠丝杠通过中空内腔连接单轴机械臂。刚性框架11为一体浇筑实心方体刚性金属框架,连接强度高,刚性框架包括左立柱、右立柱、上梁和下梁,刚性框架的长×宽×高为25×8×40cm,左立柱和右立柱的厚度均为5cm,上梁的厚度为5cm,下梁的厚度为8cm,通过控制刚性框架尺寸,增大左立柱、右立柱和下梁的厚度提高刚性框架的承载能力,进而提高刚性框架对微型试件的试验强度,实现微型重载。刚性框架11材质采用低碳钢或铸铁,通过低碳钢或铸铁材质保证刚性框架加载时的变形符合刚度要求。刚性框架内部为压力室,压力室与刚性框架相接内侧四角设计导圆弧。为保证刚性框架在加载时产生的变形符合刚度要求,采用数值模拟分别对铸铁和低碳钢两种材质的刚性框架施加100kn的载荷,刚性框架的应力、应变和变形位移如图5-图8所示,由图5-图8可得100kn压力下低碳钢和铸铁的应力、位移和应变表,如表1所示,低碳钢和铸铁的应力分别达到8.31x108n/m2和9.34x108n/m2,变形位移分别为5.46x10-2mm和5.79x10-2mm,应变分别为3.26x10-3和3.51x10-3,两种材料的刚性框架的刚度和变形位移完全可以实现微型重载,满足教学要求。图5-图6中vonmises为应力,图7-图8中estrn为应变。表1:100kn压力下低碳钢和铸铁的应力、位移和应变表材料应力(n/m2)变形位移(mm)应变低碳钢8.31x1085.46x10-23.26x10-3铸铁9.34x1085.79x10-23.51x10-3刚性框架11上梁上设置压力传感器5,压力传感器对应单轴机械臂,压力传感器连接控制机构,通过压力传感器记录试件的受力情况。刚性框架11上梁上设置轴向形变光栅尺7,轴向形变光栅尺记录试件达到破坏荷载后继续加载的轴向形变,右立柱上径向形变光栅尺8,通过轴向形变光栅尺和径向形变光栅尺记录试件受力后轴向和径向变化。轴向形变光栅尺和径向形变光栅尺的测量精度为0.01mm,压力传感器、轴向形变光栅尺和径向形变光栅尺共同组成监测机构,监测机构连接控制机构3,控制机构为计算机控制系统,操控传动机构运动和记录监测机构的监测数据。传动机构2包括伺服电机21、减速机23和滚珠丝杠22,伺服电机21通过轴键25连接减速机23,减速机23通过联轴器26连接滚珠丝杠22,滚珠丝杠22穿过支撑座6和下梁连接单轴机械臂,伺服电机、减速机和滚珠丝杠为自下而上同轴加固连接。通过伺服电机控制滚珠丝杠运动,进而驱动单轴机械臂进行伸缩,通过控制单轴机械臂位移量,直接确定试件轴向变形,避免使用位移传感器,使应变数据精准对应应力变化。所述伺服电机可精准的控制转动速度,通过减速机和滚珠丝杠能够降低电机的转速,增大伺服电机动力输出,将旋转运动转换为直线运动,控制单轴机械臂直线运动。联轴器26和折叠式法兰13之间固定连接拉筋24,保证整体直线度,提高固定强度。单轴机械臂顶端设置压头,方便安置试件,保证测试时试件受力均匀,通过下置压头配合刚性框架,共同提高微型重载能力。单轴机械臂的位移精度数值为0.1μm/s。本测试系统采用精密数控电子伺服压力系统,去掉了复杂的油路供压系统,精简了设备的构造,从而达到节能减耗的效果;通过滚珠丝杠控制机械臂实现精准的行为控制,提高了位移测量的精度,本测试系统还具有微型重载、整体结构刚度高的优点,整体刚度不小于106kn/m,能承受不小于100kn重荷载,属于微型重载单轴压力测试机,测试过程采用智能控制系统,具有操控简单、使用方便的特点。上述具有机械臂的微型重载单轴压力测试系统在进行抗压强度和压缩蠕变测试时的测试方法,操作步骤如下:(1)制作圆柱形试件,记录试件尺寸、密度和比重,然后启动配电机构和控制机构,系统处于待机状态;(2)将试件放置于压头,控制机构控制伺服电机运转,通过滚珠丝杠带动单轴机械臂上升,进而带动试件上升,当压力传感器出现读数时停止伺服电机运转;(3)设定取样周期和压缩速度,然后开始压缩试验,伺服电机开始运转,通过滚珠丝杠带动单轴机械臂继续上升,伺服电机以0.1μm/s的位移加载速度进行加载,控制机构同时显示试件载荷数值及试件轴向形变和径向形变数值,并自动保存试验数据;(4)当试件出现破裂时,暂停伺服电机,记录此时轴向形变光栅尺显示的试件上端和下端位置,然后继续启动伺服电机进行压缩试验;(5)试件完全破坏时,停止压缩试验,导出试验数据,整个试验过程控制机构始终记录试件载荷数值、轴向形变和径向形变量。实施例2:一种如实施例1所述的具有机械臂的微型重载单轴压力测试系统在进行抗拉测试时的测试方法,操作步骤如下:(1)制作圆柱形试件,记录试件尺寸、密度和比重,然后启动配电机构和控制机构,系统处于待机状态;(2)将试件放入巴西劈裂夹具内,再将巴西劈裂夹具放置在压头上,控制机构控制伺服电机运转,通过滚珠丝杠带动单轴机械臂上升,进而带动巴西劈裂夹具上升,当压力传感器出现读数时停止伺服电机运转;(3)设定取样周期和压缩速度,然后开始抗压试验,伺服电机开始运转,通过滚珠丝杠带动单轴机械臂继续上升,伺服电机以0.1μm/s的位移加载速度进行加载,巴西劈裂夹具受力拉伸试件,控制机构同时显示试件载荷数值及试件轴向形变和径向形变数值,并自动保存试验数据;(4)当试件出现破裂时,暂停伺服电机,记录此时轴向形变光栅尺显示的试件上端和下端位置,然后继续启动伺服电机进行抗压试验;(5)巴西劈裂夹具内试件完全破坏时,停止抗压试验,导出试验数据,整个试验过程控制机构始终记录试件载荷数值、轴向形变和径向形变量。实施例3:一种如实施例1所述的具有机械臂的微型重载单轴压力测试系统在进行点载荷强度测试时的测试方法,操作步骤如下:(1)制作圆柱形试件,记录试件尺寸、密度和比重,然后启动配电机构和控制机构,系统处于待机状态;(2)在压头上放置圆锥状点载荷压头,将试件放在圆锥状点载荷压头上,试件上部放置圆锥状点载荷压头,测量试件上部的圆锥状点载荷压头与压力传感器之间距离,然后将测量距离设定为运行距离,控制机构控制伺服电机运转,通过滚珠丝杠带动单轴机械臂上升设定距离,此时试件上部的圆锥状点载荷压头刚好接触压力传感器;(3)设定取样周期和压缩速度,然后开始点载荷强度试验,伺服电机开始运转,通过滚珠丝杠带动单轴机械臂继续上升,伺服电机以10n/s的压力加载速度进行加载,控制机构同时显示试件载荷数值及试件轴向形变和径向形变数值,并自动保存试验数据;(4)当试件出现破裂时,暂停伺服电机,记录此时轴向形变光栅尺显示的试件上端和下端位置,然后继续启动伺服电机进行点载荷强度试验;(5)试件完全破坏时,停止点载荷强度试验,导出试验数据,整个试验过程控制机构始终记录试件载荷数值、轴向形变和径向形变量。当前第1页12