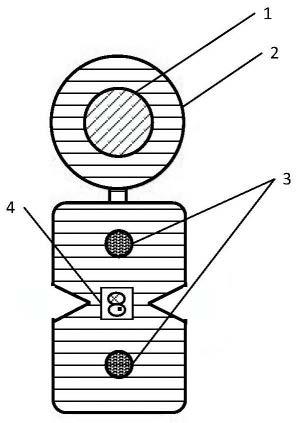
1.本发明涉及一种光缆检测方法,属于光缆检测技术领域。
背景技术:2.随着光纤接入技术的发展,“全光网”战略的全面推进,蝶形光缆的应用愈加广泛。蝶形光缆由于其材料特征、结构特性、以及施工因素等的影响,使得开通时经常发现有损耗增大影响传输性能,甚至断纤的现象,经统计发现,主要原因为光缆弯曲造成的,为此对蝶形光缆全方面抗弯曲性能提出了更高的要求,而且蝶形光缆的检测必不可少。蝶形光缆的结构如图1所示,包括光缆护套2、光缆加强件3、光纤4、以及光缆吊线钢丝1,其中,光缆护套2、光缆加强件3(一般加强件所采用的材质为frp或者金属)和光纤4构成了光缆的主体部分。
3.现有技术中,对成品光缆进行检测的检测范围只括光纤的传输性能、结构、外观等。光缆的拉伸性能、反复弯曲性能、扭转性能、卷挠性能、弯折性能需要经过型式试验检测,型式试验采用抽检的方式,测试时间长,整体需消耗数十米长度的光缆。
4.对于蝶形光缆,型式试验的具体检测过程有两种:
5.1.将光缆吊线钢丝1从蝶形光缆上分离,只对光缆的主体部分进行检测:将主体部分固定在特定的设备上,随后进行多次弯曲卷绕等,查看光纤是否折断,光缆是否破损,衰减损耗是否超标来判断光缆弯曲卷绕性能;
6.2.如图2所示,不剥离光缆吊线钢丝1,考虑到检测的稳定性,将蝶形光缆5整体、水平放置在底座7上,并且通过夹具6进行固定,进而在设备上进行反复弯曲、曲挠、弯折试验,具体试验过程参考标准gb/t 7424.2-2008。
7.然而,虽然光缆在实际使用前已经对弯曲卷挠性能进行测试,但是在实际的蝶形光缆线路敷设过程中,由于地形、固定方式等各种原因会,施工人员对光缆进行纵向弯折或者扭转时,出现光纤衰减或者断裂的现象经常发生,可见现有的弯曲卷绕检测方法检测的并不全面,容易将弯曲卷绕性能低、不合格的光缆流入市场,无法保证客户的需求。
技术实现要素:8.本技术的目的在于提供一种光缆检测方法,用以解决现有现有光缆检测不全面的问题。
9.为实现上述目的,本技术提出了一种光缆检测方法的技术方案,包括以下步骤:
10.1)确定待检测光缆的检测点;所述待检测光缆包括光缆吊线钢丝、光缆加强件、光缆护套以及光纤;
11.2)在检测点处,沿着光缆吊线钢丝,按照设定的弯曲方向将待检测光缆弯曲设定角度;弯曲后,光缆吊线钢丝在外侧;所述设定角度为光缆加强件和光缆护套粘结不紧而引起弯折性能不足的角度;
12.3)弯曲后,查看是否断纤,完成光缆的检测。
13.本发明的光缆检测方法的技术方案的有益效果是:基于现有不合格光缆的研究发现,光缆不合格是由于光缆加强件和光缆护套粘结不紧造成的,因此本发明在对蝶形光缆进行检测时,不去除光缆吊线钢丝,并且按照特定的弯曲方向进行弯曲检测,弯曲后,光缆吊线钢丝在外侧,同时,弯曲的角度为光缆加强件和光缆护套粘结不紧而引起弯折性能不足的角度,进而可以检测出光缆中是否存在光缆加强件和光缆护套粘结不紧的情况,更加全面的蝶形光缆的弯曲性能进行检测,提高了检测的准确性。
14.进一步的,为了提高检测的准确性,所述光纤的型号为g657a2,所述设定角度为60
°
~70
°
。
15.进一步的,为了提高检测的准确性,所述检测点的数量为3~5个。
16.进一步的,为了在提高检测的准确性的基础上避免光缆的浪费,各检测点之间的间隔为5~10公分。
17.进一步的,为了提高检测的准确性,所述待检测光缆为光缆成品盘,所述检测点距外端40~60公分。
附图说明
18.图1是本发明待检测光缆结构的剖面图;
19.图2是现有技术中光缆吊线钢丝不剥离的情况下,蝶形光缆进行型式试验的放置示意图;
20.图3是现有技术中光缆吊线钢丝去除后,弯曲主体部分时光纤的受力示意图;
21.图4是本发明检测蝶形光缆的示意图;
22.图5是本发明光缆加强件和光缆护套的粘结不紧时,弯曲光缆时光纤的受力示意图;
23.图6是本发明光缆加强件和光缆护套的粘结紧密时,弯曲光缆时光纤的受力示意图;
24.图7是本发明弯曲角度的示意图;
25.图中:1为光缆吊线钢丝、2为光缆护套、3为光缆加强件、4为光纤、5为蝶形光缆、6为夹具、7为底座。
具体实施方式
26.光缆检测方法实施例:
27.基于现有技术的检测方法出厂后的光缆,铺设时出现光纤4受损现象进行深入研究,研究发现,找出受损光缆断纤的主要原因:光缆中的光缆加强件3与光缆护套2粘结的不紧,并且发现,光缆中光缆加强件3如果不紧密粘结光缆护套2,会造成光缆在面临小角度弯折或过度扭转的时候,光缆加强件3无法阻止光缆发生形变,这会让原本被保护的光纤4承受较大弯折应力,基于光纤4为玻璃材质耐拉伸不耐弯折的特性,使得光缆极易出现传输性能变差、断纤情况。
28.对现有的检测方法试验后发现,如果按照如图2所示的不去除光缆吊线钢丝1的检测方法,由于光缆本身结构,弯曲时自然倾向在垂直方向(上下箭头的方向)弯曲,此时测试的仅为蝶形光缆5中光纤4本身及周围护套的弯折性能;
29.如果按照如图3所示的检测方法,将光缆吊线钢丝1去除后,光缆的主体部分本身变得相对柔软,再进行弯折检测的时候,主体部分没有吊线钢丝部分的固定,不论光缆加强件3与光缆护套2是否粘结紧密,主体部分的光纤4始终处于一个较大的弯曲半径,测试结果不准确。
30.因此,本发明的主要构思在于,基于现有技术的检测方法检测不全面的问题,由于纵向弯折时,光纤4不仅受到光缆护套2的作用力,还受到光缆加强件3形变时产生的应力,对光缆进行检测时,不去除光缆吊线钢丝1,将光缆整体进行弯曲检测,并且弯曲时,如图4所示,沿着光缆吊线钢丝1,按照设定的弯曲方向将待检测光缆弯曲设定角度,进而查看是否出现断纤的现象。
31.具体的,以蝶形光缆5型号为gjyxch/gjycfch,为例对光缆检测方法进行详细说明,该光缆为金属/非金属加强件、低烟无卤阻燃聚烯经护套、自承式蝶形引入光缆,光缆检测方法包括以下步骤:
32.1)确定待检测光缆的若干检测点。
33.这里所指的待检测光缆为整体光缆,包括光缆吊线钢丝1、光缆加强件3、光缆护套2以及光纤4,并且直接对光缆成品盘进行检测,光缆成品盘中会预留出一定长度专门用于弯曲检测。
34.经研究发现,检测点如果设置一两个,将会由于采样点过少而引起检测结果不准确的问题,因此检测点的数量一般设置为3~5个,并且检测点之间的间隔为5~10公分,并且第一个检测点的位置距离外端为40公分左右(光缆成品盘包括一个光缆的内端和一个光缆的外端,内端为成品盘内部的一端,外端为成品盘外部的一端)。
35.2)在每个检测点处,沿着光缆吊线钢丝1,使用手或者辅助工具捏住光缆,按照设定的弯曲方向将待检测光缆弯曲设定角度,要求弯曲时光缆不能打转。
36.弯曲方向不同,光纤4的受力将不同,为了检测出光缆加强件3和光缆护套2粘结不紧而引起弯折性能不足的光缆,弯曲方向与光缆排列方向相同;光缆排列方向为光缆吊线钢丝1和光纤4连线上,光缆吊线钢丝1指向光纤4的方向,也即如图5、图6所示,弯曲后,光缆吊线钢丝1在外侧。
37.光缆加强件3和光缆护套2的粘结引起光纤4受力不同的原理如下:
38.光缆加强件3和光缆护套2的粘结不紧时,如图5所示,由于光缆吊线钢丝1和光缆加强件3之间有连接部分相连,可以把二者当做一个整体,按照弯曲方向弯折光缆的时候,光缆吊线钢丝1先固定为较小的夹角,同时向下压迫光缆的主体部分,此时由于加强件部分与护套粘结不紧密,加强件将在光缆中出现滑动,无法阻止光缆发生较大应变,造成光缆中光纤4弯曲半径过小,出现断纤。
39.光缆加强件3和光缆护套2粘结紧密时,如图6所示,此时弯折光缆至一定角度的时候,光缆中加强件可以起到阻止主体部分发生较大形变的情况发生,光缆中光纤4处于一个较大的弯曲半径,不会出现断纤受损。
40.关于设定角度,以光纤4的型号为g657a2简述设定角度的确定过程:该光纤4为不敏感光纤,主要材料为玻璃材质,其最小工作弯曲半径为7.5mm,此时双手紧挨弯折的时候(也即设定角度较小)已经远远小于其工作半径,因此,弯折角度不宜过小,否则可能会引起光纤4折断对测试结果造成干扰,所以经过反复试验,如图7所示,推荐弯折60
°
~70
°
,此时
可以筛选出光缆加强件3与光缆护套2粘结不紧密引起的光缆弯折性能不足的光缆。
41.3)对每个检测点弯曲过后,撕开光缆的主体部分,只要检测点处出现一处断纤的现象即表明光缆不合格,所有检测点均未出现断纤的现象才可满足光缆检测的要求。
42.上述实施例中,为了即提高光缆检测的准确性,又减少光缆的浪费,一般设置3~5个检测点,并且各检测点之间的间隔为5~10公分,作为其他实施方式,在不考虑光缆浪费的情况下,本发明对检测点的数量以及各检测点之间的间隔并不做限制。
43.本发明在对蝶形光缆5进行检测时,不去除光缆吊线钢丝1,并且按照特定的弯曲方向进行弯曲检测,弯曲的角度为光缆加强件3和光缆护套2粘结不紧而引起弯折性能不足的角度,进而可以检测出光缆中是否存在光缆加强件3和光缆护套2粘结不紧的情况,避免出现由于光缆加强件3和光缆护套2粘结不紧而造成的断纤或传输性能不好的情况,提高检测的准确性。
44.关于光缆成品盘,一般均会专门有一段长度用于进行弯曲检测,鉴于本发明检测方法的简单性,可以对每个成品盘进行检测,通过改进后的检测方法检测后,光缆敷设跟踪及客户反馈:光缆敷设过程中出现断纤或传输性能不好的情况得到解决,现场施工中极少出现此类异常反馈。