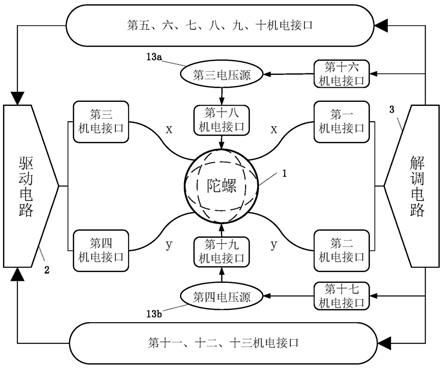
1.本发明涉及一种基于虚拟电旋转的全角陀螺在线校正装置及自动配平方法。
背景技术:2.现代武器装备已经进入小型化、智能化、信息化的时代,基于科里奥利力的微谐振陀螺具有体积小和成本低的优势,正在广泛应用于惯性武器装备中,中美两国也越来越重视陀螺技术的研发,将陀螺技术视为国防技术发展的重要环节。
3.其中,基于速率积分原理的全角微陀螺具有带宽高,量程无限大的优势,能够直接对角度进行测量,突破了传统陀螺精度低和测量范围有限的缺点。
4.全角模式最初是在半球谐振陀螺上成功运行,但由于加工工艺的不足和陀螺制作材料的限制,使得不同模态上的阻尼和刚度并不相同,最终导致陀螺的对称性不足。
5.因此,测量角度的误差会随着时间的增长而积累,造成严重的振荡和漂移,最终影响陀螺的长期稳定性和精准度。国内外的学术界,科研机构以及相关技术企业对此也投入了大量的人力和物力,不断提高运行全角模式的微谐振陀螺的对称性和长期稳定性。
6.经过长期的测试工作表明,基于现有精密加工技术的硅材料不足以继续提升微谐振陀螺的对称性,而石英半球谐振陀螺的造价十分昂贵,且良品率不足。因此,对于现阶段未能实现完全对称的微谐振陀螺,必须采取校正方式才能保证全角模式陀螺的长期稳定。
7.对于全角模式的微谐振陀螺校正方案整体分为以下两种:
8.[1]离线校正方案:
[0009]
离线校正主要是通过实验测试推理得出陀螺误差参数的特性和变化规律,在正式上电运行之前,进行一次性误差校正,能够在短时间内维持陀螺的良好对称性。然而,对于需要长时间运行的全角谐振陀螺来说,运行环境不能确保长期稳定,这就使一次性离线校正效果会随着时间的延长而失效,因此该校正方案不是校正陀螺不对称参数的根本办法。
[0010]
[2]在线校正方案:
[0011]
该校正方案能够在线辨识陀螺的不对称性参数,对变化的不对称误差进行实时补偿,具有长期的有效性和实时性,是校正全角微陀螺不对称性和解决陀螺振荡漂移的根本办法。
[0012]
近年来,国内外研究人员关于全角陀螺的在线实时校正的成果显著,但仍处于特定工况下的限制,输出精度不能达到复杂工况下高精度检测的要求。
[0013]
通过施加高频电信号形成虚拟电旋转引入到陀螺中的方案,最初由美国的analog device公司研究团队以及日本东北大学的研究团队开始涉及,但这两个团队对于虚拟电旋转的应用仅局限于解决全角陀螺的死区问题,对于较低速率的旋转能够进行精准检测。
[0014]
因此,对于虚拟电旋转方案的应用仍待拓展,以解决全角微陀螺的不对称性误差问题。
技术实现要素:[0015]
本发明的目的在于提出一种基于虚拟电旋转的全角陀螺在线校正装置,该装置通过引入永久式高频信号等效为电旋转激励,能够在线辨识谐振陀螺的不对称性误差,再通过直接给陀螺施加静电力,来抵消谐振陀螺的不对称性误差。
[0016]
本发明为了实现上述目的,采用如下技术方案:
[0017]
基于虚拟电旋转的全角陀螺在线校正装置,包括驱动电路和解调电路;其中,驱动电路和解调电路分别通过机电接口与谐振式陀螺相连;
[0018]
驱动电路包括锁相环电路、加法器、乘法器、vga电路、电压源以及压控振荡器;
[0019]
其中,锁相环电路有一个;
[0020]
加法器有四个,即第一加法器、第二加法器、第三加法器以及第四加法器;
[0021]
乘法器有五个,即第一乘法器、第二乘法器、第三乘法器、第四乘法器以及第五乘法器;
[0022]
vga电路包括第一vga电路、第二vga电路、第三vga电路和第四vga电路;
[0023]
电压源有两个,即第一电压源,第二电压源,两个电压源均为电压幅值可调节的电压源;
[0024]
压控振荡器有两个,即第一压控振荡器和第二压控振荡器;
[0025]
机电接口包括第一、第二、第三、第四、第五、第六、第七、第八、第九、第十、第十一、第十二、第十三、第十四、第十五、第十六、第十七、第十八、第十九机电接口;
[0026]
第七机电接口和第九机电接口分别与第一加法器的一个输入端相连;
[0027]
第八机电接口和第十机电接口分别与第二加法器的一个输入端相连;
[0028]
第一加法器和第二加法器的输出端分别与锁相环电路的一个输入端相连;锁相环电路的输出端以及第十一机电接口分别与第一乘法器的一个输入端相连;
[0029]
第一乘法器的输出端分别连接到第二乘法器和第三乘法器的一个输入端上,第十二机电接口连接到第二乘法器另一个输入端,第十三机电接口连接到第三乘法器另一个输入端;
[0030]
第二乘法器的输出端依次与第一vga电路、第三加法器的一个输入端相连,第三乘法器的输出端依次与第二vga电路、第四加法器的一个输入端相连;
[0031]
第一电压源的电压输出端与第十四机电接口相连,第十四机电接口依次与第一压控振荡器、第三vga电路以及第四乘法器的一个输入端相连;
[0032]
第六机电接口与第四乘法器的另一个输入端相连;第四乘法器的输出端与第三加法器的另一个输入端相连;第三加法器的输出端与第三机电接口相连;
[0033]
第二电压源的电压输出端与第十五机电接口相连,第十五机电接口依次与第二压控振荡器、第四vga电路以及第五乘法器的一个输入端相连;
[0034]
第五机电接口与第五乘法器的另一个输入端相连;第五乘法器的输出端与第四加法器的另一个输入端相连;第四加法器的输出端与第四机电接口相连;
[0035]
第三机电接口和第四机电接口分别与谐振式陀螺的两个驱动信号输入端一对一相连;
[0036]
解调电路包括c/v电路、相干解调电路、电压源以及微处理器;
[0037]
其中,c/v电路有两个,即第一c/v电路和第二c/v电路;相干解调电路有两个,即第
一相干解调电路和第二相干解调电路;微处理器有一个;
[0038]
电压源有两个,即第三电压源,第四电压源,两个电压源均为电压幅值可调节的电压源;
[0039]
谐振式陀螺的两个信号输出端分别与第一机电接口以及第二机电接口一对一相连;第一机电接口与第一c/v电路的输入端相连,第二机电接口与第二c/v电路的输入端相连;
[0040]
第一c/v电路的输出端分别与第五机电接口以及第一相干解调电路的输入端相连;第二c/v电路的输出端分别与第六机电接口以及第二相干解调电路的输入端相连;
[0041]
第一相干解调电路的同相信号输出端分别与第七机电接口和微处理器的输入端相连,第一相干解调电路的正交信号输出端分别与第八机电接口和微处理器的输入端相连;
[0042]
第二相干解调电路的同相信号输出端分别与第九机电接口和微处理器的输入端相连,第二相干解调电路的正交信号输出端分别与第十机电接口和微处理器的输入端相连;
[0043]
微处理器的输出端有五个,分别为能量信号输出端、驻波角的余弦信号输出端、驻波角的正弦信号输出端、第一误差校正信号输出端以及第二误差校正信号输出端;
[0044]
能量信号输出端与第十一机电接口相连;
[0045]
余弦信号输出端、正弦信号输出端分别与第十二机电接口、第十三机电接口一对一相连;
[0046]
第一误差校正信号输出端与第十六机电接口相连,第十六机电接口的输出端依次与第三电压源、第十八机电接口以及陀螺相连;
[0047]
第二误差校正信号输出端与第十七机电接口相连,第十七机电接口的输出端依次与第四电压源、第十九机电接口以及陀螺相连。
[0048]
此外,本发明还提出了一种基于虚拟电旋转的全角陀螺自动配平方法,该方法基于上面述及的虚拟科里奥利力的全角陀螺在线校正装置,具体技术方案如下:
[0049]
基于虚拟电旋转的全角陀螺自动配平方法,包括如下步骤:
[0050]
i.首先引入高频电旋转激励作为持续激励源,陀螺的驻波角的响应包括由实际物理旋转引起的低频响应以及由虚拟旋转引起的高频响应;
[0051]
ii.利用微处理器检测驻波角,从陀螺的驻波角的响应中分离由实际物理旋转引起的低频响应,得到由虚拟旋转引起的高频响应;
[0052]
iii.基于高频电旋转的全角微谐振陀螺不对称参数实时配平问题转换成不对称参数的轨迹跟踪问题;其中,由实际情况下的虚拟旋转引起的高频响应,即引入高频激励下陀螺的驻波角的实际轨迹通过微处理器计算得出;在陀螺完全对称且无耦合的理想状态下,即引入高频激励下陀螺的驻波角理想轨迹已知;
[0053]
因此,引入高频激励下,陀螺驻波角的理想轨迹与实际轨迹之间的差,即为陀螺的非对称性误差带来的谐波响应,将该谐波响应等价为外部干扰;
[0054]
iv.构建基于鲁棒式的跟踪控制算法,对步骤iii中陀螺的驻波角的理想轨迹与实际轨迹之间的差,即由陀螺的非对称性误差带来的谐波响应进行跟踪控制;
[0055]
将对误差跟踪控制过程中的反馈量,以静电力的形式直接反馈至陀螺上,等效地
消除谐振陀螺的不对称性误差,从而将陀螺保持在配平状态。
[0056]
优选地,步骤ii具体为:
[0057]
ii.1.经解调电路解调后的能量参数和驻波角的角度参数反馈至驱动电路,使得谐振子在驻波角上位置稳定和能量恒定,从而保持陀螺在驻波角上持续振动;
[0058]
驱动电路产生两路驱动信号,并分别通过第三机电接口和第四机电接口进入陀螺;
[0059]
ii.2.陀螺输出信号经过第一和第二机电接口,分别输出两个模态的模拟量输出信号;
[0060]
ii.3.利用第一c/v电路和第二c/v电路分别对步骤i.2中以上两个模态的模拟量输出信号进行放大处理,此后信号一直是模拟量并进行后续处理;
[0061]
ii.4.经过第一相干解调电路和第二相干解调电路得到的解调信号进入微控制器,并进行结算,得到提取的信号,即驻波角信号θ
m
:
[0062]
θ
m
=θ
z
+a1cos(θ
e
t+φ1)+a2cos(2θ
e
t+φ2)+a3cos(3θ
e
t+φ3)
···
+ν;
[0063]
其中,θ
z
表示低频的实际物理旋转,a1cos(θ
e
t)+a2cos(2θ
e
t)+a3cos(3θ
e
t)+
···
为引入的高频虚拟电旋转所引起的陀螺响应信号;
[0064]
a1为陀螺轨道角的基波的幅值,a
j
为模态分裂、阻尼不匹配引起的谐波的幅值,j=2,3,
···
;是电路电子带来的相位延迟,i=1,2,3,
···
,ν是测量噪声;
[0065]
ii.5.由于电激励信号已知、低频旋转信号可测,且陀螺高频响应解已知,将原始测量信号归纳为如下的估计问题,并在微处理器中完成下述过程:
[0066][0067]
上述方程中为待估计的变量,其中,参数分别为参数a1,a2,a3···
的待估计值,参数分别为参数φ1,φ2,φ3...的待估计值;
[0068]
参数cos(θ
e
t),cos(2θ
e
t),cos(3θ
e
t)
···
为由虚拟电旋转产生的已知量;
[0069]
ii.6.利用代价函数并基于adam自适应最优算法,估计上述待确定的参数的估计值;
[0070]
ii.7.在确定以上参数的估计值之后,将待检测信号的幅值代入驻波角信号θ
m
中,并消除驻波信号θ
m
中的相位差φ1,φ2,φ3...,则求得的驻波角信号θ
m
为:
[0071][0072]
从上述驻波角信号θ
m
中分离由实际物理旋转引起的低频响应θ
z
,得到由虚拟电旋转引起的高频响应,表达式如下:
[0073]
优选地,步骤iii中,陀螺的驻波角的理想轨迹的表达式为:θ=λcos(θ
e
t);
[0074]
则引入高频激励下,驻波角的实际轨迹和理想轨迹的误差为:
[0075][0076]
其中,
[0077]
δω表示谐振频率分裂因数,δq表示品质因数不对称因数;
[0078]
c
xy
表示阻尼耦合因数,k
xy
表示刚度耦合因数;
[0079]
η1(δω,δq,c
xy
,k
xy
)表示由高频激励产生的cos(θ
e
t)分量的系数估计量;
[0080]
η2(δω,δq,c
xy
,k
xy
)表示由高频激励产生的cos(2θ
e
t)分量的系数估计量;
[0081]
η3(δω,δq,c
xy
,k
xy
)表示由高频激励产生的cos(3θ
e
t)分量的系数估计量。
[0082]
优选地,步骤iv中,在对步骤iii中误差进行跟踪控制时,设定参数变化范围的上下界:
[0083]
ω
b
≤δω≤ω
s
,q
b
≤δq≤q
s
,c
b
≤c
xy
≤c
s
,k
b
≤k
xy
≤k
s
;
[0084]
其中,ω
b
、ω
s
分别表示δω的上界和下界;q
b
、q
s
分别表示δq的上界和下界,c
b
、c
s
分别表示c
xy
的上界和下界,k
b
、k
s
分别表示k
xy
的上界和下界;
[0085]
建立误差的能量储存函数s(e):
[0086]
并设计控制律满足如下条件:
[0087]
t表示时间,e(t)表示控制误差,e(0)表示初始误差,s(e(t))表示误差能量函数,s(e(0))表示误差初始能量,f
θ
表示输入控制力,ψ(e,f
θ
)表示能量耗散函数;
[0088]
通过构造上述储能函数和控制律,对陀螺施加静电力校正陀螺的不对称性,则实际驻波角能够良好地跟踪高频虚拟电调制信号。
[0089]
本发明具有如下优点:
[0090]
如上所述,本发明提出了一种基于虚拟电旋转的全角陀螺在线校正装置,该全角陀螺在线校正装置通过引入永久式高频信号等效为电旋转激励,通过微处理器能够在线辨识谐振陀螺的不对称性误差,再通过直接给陀螺(的校正电极)施加静电力,来抵消谐振陀螺的不对称性误差,从而实现对全角模式下陀螺的电修调,最终提高全角模式谐振陀螺的测量可靠性。本发明基于速率积分陀螺要求结构完全对称的理论限制,根据微陀螺由于加工缺陷导致的根本缺陷,校正微谐振陀螺的不对称误差,弥补了现有陀螺对称性的不足。此外,本发明还提出了一种基于虚拟电旋转的全角陀螺自动配平方法,该自动配平方法通过将陀螺的配平问题转化为标准参考信号的轨迹跟踪问题,利于提高动态配平的可靠性。
附图说明
[0091]
图1为本发明实施例中基于虚拟电旋转的全角陀螺在线校正装置的结构示意图;
[0092]
图2为本发明实施例中驱动电路的结构示意图;
[0093]
图3为本发明实施例中解调电路的结构示意图;
[0094]
图4为本发明实施例中低频物理旋转和高频虚拟电旋转叠加信号示意图;
[0095]
图5为本发明实施例中基于虚拟电旋转的全角陀螺自动配平方法的流程示意图。
[0096]
其中,1
‑
陀螺,2
‑
驱动电路,3
‑
解调电路,4
‑
锁相环电路,5a
‑
第一加法器,5b
‑
第二加法器,5c
‑
第三加法器,5d
‑
第四加法器,6a
‑
第一乘法器,6b
‑
第二乘法器,6c
‑
第三乘法器,6d
‑
第四乘法器,6e
‑
第五乘法器,7a
‑
第一vga电路,7b
‑
第二vga电路;
[0097]
7c
‑
第三vga电路,7d
‑
第四vga电路,8a
‑
第一电压源,8b
‑
第二电压源,9a
‑
第一压控振荡器,9b
‑
第二压控振荡器,10a
‑
第一c/v电路,10b
‑
第二c/v电路,11a
‑
第一相干解调电路,11b
‑
第二相干解调电路,12
‑
微处理器,13a
‑
第三电压源,13b
‑
第四电压源。
具体实施方式
[0098]
下面结合附图以及具体实施方式对本发明作进一步详细说明:
[0099]
如图1所示,本实施例述及了一种基于虚拟电旋转的全角陀螺在线校正装置,该装置包括与谐振式陀螺1通过机电接口相连的驱动电路2和解调电路3。
[0100]
其中,机电接口总共有十九个,即:
[0101]
第一、第二、第三、第四、第五、第六、第七、第八、第九、第十、第十一、第十二、第十三、第十四、第十五、第十六、第十七、第十八以及第十九机电接口。
[0102]
驱动电路2通过第三机电接口和第四机电接口与驱动陀螺1相连。其中,第三机电接口向陀螺1传输x轴方向上的信号,第四机电接口向谐振传输y轴方向上的信号。
[0103]
陀螺1通过第一机电接口和第二机电接口与解调电路3相连。其中,第一机电接口、第二机电接口分别用于接收来自陀螺1的x轴方向和y轴方向上的信号。
[0104]
解调电路3对于陀螺1的输出信号进行解调并提取参数,计算得出能量数值和驻波角,并通过第五至第十三机电接口传输反馈信号至驱动电路2,维持驻波方向上的能量控制。
[0105]
如图2所示,驱动电路2包括锁相环电路、加法器、乘法器、vga电路、电压源以及压控振荡器。其中,锁相环电路4有一个。
[0106]
加法器包括第一加法器5a、第二加法器5b、第三加法器5c和第四加法器5d;乘法器包括第一乘法器6a、第二乘法器6b、第三乘法器6c、第四乘法器6d和第五乘法器6e。
[0107]
vga电路有四个,即第一vga电路7a、第二vga电路7b、第三vga电路7c和第四vga电路7d,各个vga电路均为可变增益放大器电路。
[0108]
电压源有两个,即第一电压源8a,第二电压源8b。
[0109]
以上两个电压源均为电压幅值可调节的电压源,以便进行电压幅值调整。第一电压源8a,第二电压源8b均可以采用现有技术中已有的电压源。
[0110]
压控振荡器有两个,即第一压控振荡器9a和第二压控振荡器9b。
[0111]
驱动电路2中各个部件之间的连接关系如下:
[0112]
第七机电接口和第九机电接口分别与第一加法器5a的一个输入端相连;第八机电接口和第十机电接口分别与第二加法器5b的一个输入端相连。
[0113]
第一加法器5a和第二加法器5b的输出端分别与锁相环电路4的一个输入端相连;锁相环电路4的输出端以及第十一机电接口分别与第一乘法器6a的一个输入端相连。
[0114]
第一乘法器6a的输出端分别连接到第二乘法器6b和第三乘法器6c的一个输入端上。
[0115]
第十二机电接口连接到第二乘法器6b的另一个输入端上。
[0116]
第二乘法器6b的输出端依次与第一vga电路7a、第三加法器5c的一个输入端相连。
[0117]
第十三机电接口连接到第三乘法器6c的另一个输入端上。
[0118]
第三乘法器6c的输出端依次与第二vga电路7b、第四加法器5d的一个输入端相连。
[0119]
第一vga电路7a和第二vga电路7b用于提供陀螺1两个模态上的驱动信号。
[0120]
第一电压源8a的电压输出端与第十四机电接口相连,第十四机电接口依次与第一压控振荡器9a、第三vga电路7c以及第四乘法器6d的一个输入端相连。
[0121]
第六机电接口与第四乘法器6d的另一个输入端相连,第四乘法器6d的输出端与第
三加法器5c的另一个输入端相连;第三加法器5c的输出端与第三机电接口相连。
[0122]
第二电压源8b的电压输出端与第十五机电接口相连,第十五机电接口依次与第二压控振荡器9b、第四vga电路7d以及第五乘法器6e的一个输入端相连。
[0123]
第五机电接口与第五乘法器6e的另一个输入端相连,第五乘法器6e的输出端与第四加法器5d的另一个输入端相连;第四加法器5d的输出端与第四机电接口相连。
[0124]
第三机电接口和第四机电接口分别与陀螺1的两个驱动信号输入端一对一相连,如图1所示,第三机电接口与陀螺1的x模态的驱动信号输入端相连。
[0125]
同理,第四机电接口与陀螺1的y模态的驱动信号输入端相连。
[0126]
陀螺1的两个模态上的高频激励信号分别是第一电压源8a和第二电压源8b供给,由于两个电压源的幅值均可分别进行调解,因此,产生的高频激励信号的大小可调整。
[0127]
信号流在驱动电路2中的走向为:
[0128]
第七至第十机电接口分是经过解调电路3后得到的数值,分别是x模态相干解调后的同相信号ix、正交信号qx以及y模态相干解调后的同相信号iy和正交信号qy。
[0129]
利用第一加法器5a将ix和iy相加,利用第二加法器5b将qx和qy相加。
[0130]
锁相环电路4将第一加法器5a和第二加法器5b传输的信号进行处理,输出稳定的带有陀螺谐振频率信息的电压信号数值给第一乘法器6a。
[0131]
第一乘法器6a将锁相环电路4输出的稳定的带有陀螺谐振频率信息的电压信号和第十一机电接口接收的解调电路3的能量信号数值相乘,实现能量控制。
[0132]
经过第一乘法器6a相乘后的信号传输给第二乘法器6b和第三乘法器6c。
[0133]
第二乘法器6b将第一乘法器6a的输出值和第十二接电机口的数值相乘,第三乘法器将第一乘法器6a的输出值和第十三接电机口的数值相乘。
[0134]
其中,第十二和第十三机电接口接收的是微处理器输出的驻波角的余弦值、正弦值。
[0135]
第二乘法器6b的输出值经过第一vga电路7a将增益放大。
[0136]
第三乘法器6b的输出值经过第二vga电路7b将增益放大。
[0137]
由锁相环电路产生陀螺1所需要的谐振频率信号,通过第十一机电接口实现能量控制,再通过第十二机电接口和十三机电接口实现两个模态上的三角函数能量分配,最终输出至第一vga7a和第二vga电路7b形成激励信号,维持驻波角上的振荡。
[0138]
第一电压源8a通过第十四机电接口给第一压控振荡器9a,产生高频电压信号,再通过第三vga电路7c进行增益放大,输出值给第四乘法器6d,再与第六机电接口的数值相乘,产生高频虚拟电旋转的电压信号,第四乘法器6d的输出值再给第三加法器5c。
[0139]
第二电压源8b通过第十五机电接口给第二压控振荡器9b,产生高频电压信号,再通过第四vga电路7d进行增益放大,输出值给第五乘法器6e,再与第五机电接口的数值相乘,产生高频虚拟电旋转的电压信号,第五乘法器6e的输出值再给第四加法器5d。
[0140]
第一vga电路7a的输出值给第三加法器5c,与第四乘法器6d的输出值(即高频激励信号)相加,输出值传给第三机电接口,产生驱动模拟信号进入陀螺1。
[0141]
第二vga电路7b的输出值给第四加法器5d,与第五乘法器6e的输出值(即高频激励信号)相加,输出值传给第四机电接口,产生驱动模拟信号进入陀螺1。
[0142]
驱动电路2采用模拟信号引入虚拟科里奥利力,并且构建了实际的模拟信号电路,
模拟方案相比较数字方案来说,具有控制带宽高,响应速度快,相位延时低等优点。
[0143]
本实施例采用的是高频激励和能量控制后的驱动信号叠加的方式,组合成为谐振式陀螺的驱动信号,在驱动电路增设高频激励方案,两个模态上可以独立增设高频激励信号,再将陀螺两个模态上的输出信号与高频激励信号进行混频处理,保证输入陀螺的信号是陀螺的谐振频率,再通过能量分配(第十二机电接口电路和第十三机电接口电路)来控制两个模态的驱动数值的大小,保持能量恒定,再将两部分信号相加进入陀螺。在产生物理旋转后,通过相干解调将实际物理旋转信息和高频激励信息得到解调,利用高频激励信号检查陀螺的非对称误差,本发明能够在不存在外部旋转的情况下,依旧得到不对称性产生的误差参数。
[0144]
基于陀螺1的谐振频率上包络驻波角信息。相干解调法为传统提取包络信号的方法,引入虚拟电旋转的基波和包含陀螺不对称参数的谐波分别在50hz和100hz左右,这就对如何设置低通滤波器的带宽提出要求。由于mems陀螺的谐振频率在5khz到10khz的范围之间,为了避免引入噪声造成严重的干扰,因而设定相干解调中的低通滤波器的基带信号带宽为50hz以内。为解决高频激励响应与噪声干扰相互矛盾的问题,本实施例提出一种基于自适应信号处理的解调电路方案。
[0145]
如图3所示,解调电路3包括c/v电路、相干解调电路、电压源以及微处理器12。
[0146]
其中,c/v电路有两个,即第一c/v电路10a和第二c/v电路10b。相干解调电路有两个,即第一相干解调电路11a和第二相干解调电路11b。
[0147]
电压源有两个,即第三电压源13a,第四电压源13b。
[0148]
以上两个电压源均为电压幅值可调节的电压源,以便进行电压幅值调整。第三电压源13a,第四电压源13b均可以采用现有技术中已有的电压源。
[0149]
解调电路3中各个部件之间的连接关系如下:
[0150]
第一机电接口与第一c/v电路10a的输入端相连,第一c/v电路10a的输出端分别与第五机电接口以及第一相干解调电路11a的输入端相连。
[0151]
第二机电接口与第二c/v电路10b的输入端相连,第二c/v电路10b的输出端分别与第六机电接口以及第二相干解调电路11b的输入端相连。
[0152]
第一相干解调电路11a的同相信号输出端分别与第七机电接口和微处理器12的输入端相连,正交信号输出端分别与第八机电接口和微处理器12的输入端相连。
[0153]
第二相干解调电路11b的同相信号输出端分别与第九机电接口和微处理器12的输入端相连,正交信号输出端分别与第十机电接口和微处理器12的输入端相连。
[0154]
微处理器12优选采用fpga实现。
[0155]
微处理器12的输出端有五个,分别为能量信号输出端、第一误差校正信号输出端、第二误差校正信号输出端、驻波角的余弦信号输出端以及正弦信号输出端。
[0156]
其中,能量信号输出端与第十一机电接口相连。
[0157]
余弦信号输出端、正弦信号输出端分别与第十二机电接口、第十三机电接口一对一相连。
[0158]
通过微处理器12的能量信号输出端、驻波角的余弦信号输出端以及正弦信号输出端,能够分别输出驻波能量信号以及驻波角的余弦信号和正弦信号,并反馈至驱动电路2中。
[0159]
第一误差校正信号输出端与第十六机电接口相连,第十六机电接口依次与第三电压源13a、第十八机电接口以及陀螺(的校正电极)相连,进行静电校正。
[0160]
其中,第一误差校正信号输出端用于输出校正信号,并控制第三电压源13a输出相应幅值大小的直流电压,该直流电压作为校正静电力作用于陀螺1上。
[0161]
第二误差校正信号输出端与第十七机电接口相连,第十七机电接口依次与第四电压源13b、第十九机电接口以及陀螺(的校正电极)相连,进行静电校正。
[0162]
其中,第二误差校正信号输出端用于输出校正信号,并控制第四电压源输出相应幅值大小的直流电压,该直流电压作为校正静电力作用于陀螺1上。
[0163]
信号流在上述解调电路3中的走向为:
[0164]
陀螺x轴方向上的输出信号经过第一机电接口传输至第一c/v电路10a,进行处理;陀螺y轴方向上的输出信号经过第一机电接口传输至第一c/v电路10b,进行处理。
[0165]
第一c/v电路10a的输出信号传输至第五机电接口和第一相干解调电路11a;第二c/v电路10b的输出信号传输至第六机电接口和第二相干解调电路11b。
[0166]
第一相干解调电路11a经过数字解调后得到x方向上的同相信号ix传输至微处理器12和第七机电接口,解调后得到x方向上的正交信号qx传输至微处理器和第八机电接口。
[0167]
第二相干解调电路11b经过数字解调后得到y方向上的同相信号iy传输至微处理器12和第九机电接口,解调后得到y方向上的正交信号qy传输至微处理器和第十机电接口。
[0168]
将x模态上的同相信号ix、正交信号qx以及y模态方向上的同相信号iy、正交信号qy经过微处理器12后,得到驻波能量信号,驻波角的角度信息和校正信号。
[0169]
驻波能量信号传输至第十一机电接口,驻波角度信息cosθ和s i nθ,分别传输至第十二机电接口和第十三机电接口,校正信号分别传输至第十六机电接口和第十七机电接口。
[0170]
第十六机电接口将校正信号输送至第三电压源13a,第三电压源13a输出相应幅值大小的直流电压,该直流电压作为校正静电力作用于陀螺1上。
[0171]
第十七机电接口将校正信号输送至第四电压源13b,第四电压源13b输出相应幅值大小的直流电压,该直流电压作为校正静电力作用于陀螺1上。
[0172]
本发明实施例中全角陀螺在线校正装置的优势在于:
[0173]
驱动电路2采用模拟信号进行驱动,利于提高带宽和传输速率;两个模态的输出信号分别进入解调电路3进行相干解调,再将两个模态的数值分别进行整合,进入驱动电路2中的锁相环电路,提取两个模态上的谐振频率数值,相比传统方案,频率提取更为精准。
[0174]
通过锁相环电路提取带有谐振频率信息的正弦信号,第十一机电接口通过乘法器与微控制器得到的能量数值相乘,减少了信号传输过程的噪声干扰,此过程可以完成对激励信号的幅值控制;再通过解调电路3中微控制器得到的角度信息反馈至驱动端,对总能量按照驻波角的方向进行能量分解,保证了谐振子在驻波角上的持续振荡。
[0175]
高频激励的引入是采用非同源电压源进行激励,避免了电路噪声的影响;两个模态的输出信号经过放大后,直接利用到高频激励部分,与高频激励信号经过乘法器做混频处理,保证物理旋转和虚拟电旋转经过相干解调后能够完整的保留下来。
[0176]
误差校正方式采用静电力的形式进行校正,通过可变电压源(即第三电压源和第四电压源)产生的精准电压值直接施加到谐振陀螺上,校正陀螺的非对称误差。
[0177]
本实施例基于以上在线自动校正装置还提出了一种基于虚拟电旋转的全角陀螺自动配平方法,以达到在线检测并补偿全角陀螺的不对称性误差的目的。
[0178]
本发明实施例采用基于自适应信号处理算法与传统相干解调相结合的方法,对全角陀螺的驻波角的高频振动信号进行精准检测。为辨识陀螺中的不理想因素,拟通过电压源、压控振荡器以及vga电路产生f=a0sin(ω
e
t)+f
c
的正弦电压信号,从而生成高频激励信号,通过陀螺对于高频激励的响应,来获取陀螺的不对称特性。f
c
为预留的控制输入项。
[0179]
在引入了高频虚拟电旋转,以及对轨道角完成精确近似求解之后,陀螺的x、y两个模态的整体解可表示为:
[0180]
x=acos(θ
z
+a
1 cos(θ
e
t)+a2cos(2θ
e
t)+a
3 cos(3θ
e
t)....)cos(ωt)
[0181]
+qsin(θ
z
+a
1 cos(θ
e
t)+a2cos(2θ
e
t)+a
3 cos(3θ
e
t)....)sin(ωt);
[0182]
y=asin(θ
z
+a
1 cos(θ
e
t)+a
2 cos(2θ
e
t)+a3cos(3θ
e
t)....)cos(ωt)
[0183]
‑
qsin(θ
z
+a
1 cos(θ
e
t)+a
2 cos(2θ
e
t)+a
3 cos(3θ
e
t)....)sin(ωt)。
[0184]
其中,θ
z
为低频的实际物理旋转;a
1 cos(θ
e
t)+a2cos(2θ
e
t)+a
3 cos(3θ
e
t)....为在线自动校正装置引入的高频虚拟电旋转所引起的陀螺响应信号。叠加形成的信号包含低频信号和高频信号,如图4所示。在实际物理过程和应用中,可产生的物理旋转处于较低频段,形成低频旋转信号;引入的高频电旋转处于高频段,形成高频电旋转信号。
[0185]
如图5所示,下面对全角陀螺自动配平方法的步骤进行详细说明:
[0186]
i.首先通过第一电压源和第二电压源引入高频电旋转激励作为持续激励源,陀螺的驻波角的响应包括由实际物理旋转引起的低频响应以及由虚拟旋转引起的高频响应。
[0187]
ii.利用微处理器检测驻波角,分离由实际物理旋转引起的低频响应,得到由虚拟旋转引起的高频响应,即得到引入高频激励下,陀螺的驻波角的实际轨迹。
[0188]
高频驻波角检测技术的具体过程如下:
[0189]
ii.1.经解调电路解调后的参数反馈至驱动电路,使得谐振子在驻波角上位置稳定和能量恒定,从而保持陀螺在驻波角上持续振动;
[0190]
驱动电路产生两路驱动信号,并分别通过第三机电接口和第四机电接口进入陀螺。
[0191]
ii.2.陀螺输出信号经过第一和第二机电接口,分别输出两个模态的模拟量输出信号。陀螺在高频激励下的动态响应推理近似解的形式为:
[0192]
θ=a1cos(θ
e
t)+a2cos(2θ
e
t)+a3cos(3θ
e
t)+
···
;
[0193]
其中,a1为陀螺轨道角的基波的幅值,a2、a3等为模态分裂、阻尼不匹配引起的谐波的幅值。计算得出θ与激励信号a0sin(ω
e
t)的谐波关系,进而制定数字解调和动态配平方案。
[0194]
ii.3.由于陀螺的输出信号极小,因此利用第一c/v电路和第二c/v电路分别对以上两个模态的模拟量输出信号进行放大处理,此后信号一直是模拟量并进行后续处理。
[0195]
ii.4.经过第一相干解调电路和第二相干解调电路得到的解调信号进入微控制器,并进行结算,得到提取的信号,即驻波角信号θ
m
:
[0196]
θ
m
=θ
z
+a1cos(θ
e
t+φ1)+a2cos(2θ
e
t+φ2)+a3cos(3θ
e
t+φ3)
···
+ν;
[0197]
其中,θ
z
表示低频的实际物理旋转;a1cos(θ
e
t)+a2cos(2θ
e
t)+a3cos(3θ
e
t)+
…
为引入的高频虚拟电旋转所引起的陀螺响应信号。
[0198]
a1为陀螺轨道角的基波的幅值,a
j
为模态分裂、阻尼不匹配引起的谐波的幅值,j=2,3,
…
;是电路电子带来的相位延迟,i=1,2,3,
···
,ν是测量噪声。
[0199]
ii.5.由于电激励信号已知、低频旋转信号可测,且陀螺高频响应解已知,将原始测量信号归纳为如下的估计问题,并在微处理器中完成下述过程:
[0200][0201]
上述方程中为待估计的变量,其中,参数分别为参数a1,a2,a3···
的待估计值,参数分别为参数φ1,φ2,φ3...的待估计值。
[0202]
cos(θ
e
t),cos(2θ
e
t),cos(3θ
e
t)
···
为由虚拟电旋转产生的已知量。
[0203]
ii.6.因陀螺运行在嵌入式计算环境的微控制器下,对算法的实时性要求较高。
[0204]
为了保证信号提取的收敛性和准确性,本发明实施例利用代价函数,并基于adam自适应最优算法,估计上述待确定的参数的估计值。
[0205]
adam自适应最优算法是目前较为成熟的适应性矩估计算法,它利用梯度的一阶矩估计和二阶矩估计动态调整每个参数的学习率(具体过程,本实施例不再详述)。
[0206]
adam的优点主要在于经过偏置校正后,每一次迭代学习率都有个确定范围,使得参数比较平稳。但在高频激励条件下的速率积分模式求解上,并未得到应用。
[0207]
基于adam自适应最优算法,设计代价函数j为:
[0208][0209]
并进行如下信号处理流程:
[0210]
t1=ρ1t1+(1
‑
ρ1)j;
[0211]
t2=ρ2t2+(1
‑
ρ2)j2;
[0212][0213]
其中,ρ1,ρ2,ε,σ为adam自适应最优算法的参数,t1,t2为自适应梯度下降的中间变量。
[0214]
其中,ζ为本次待估计变量,ζ’为下次待估计变量。
[0215]
基于adam自适应最优算法利用代价函数,估计得到上述待确定的参数的估计值。
[0216]
ii.7.在确定以上参数的估计值之后,将待检测信号的幅值代入驻波角信号θ
m
中,并消除驻波信号θ
m
中的相位差φ1,φ2,φ3...,则求得的驻波角信号θ
m
为:
[0217][0218]
从上述驻波角信号θ
m
中分离由实际物理旋转引起的低频响应θ
z
,得到由虚拟电旋转引起的高频响应,即引入高频激励下陀螺的驻波角的实际轨迹,表达式如下:
[0219][0220]
至此,完成了对陀螺高频响应的信号的低噪声和高带宽的提取。
[0221]
由于加工工艺不足和材料问题的限制,导致全角微陀螺存在不对称性,具体表现
为模态的谐振频率不同,品质因数不同,模态耦合等不理想因素,这会使得驻波角存在求解不准确和严重非线性的问题。
[0222]
基于陀螺的高频振动响应解,利用已知的物理旋转可将低频信号和高频虚拟电旋转信号进行分离,得到虚拟电旋转的实际响应,利用已知的预期谐波参考频率来设计adam自适应梯度下降算法估计不对称性参数,使得信号提取更为精准,突破了提取信号带宽和信噪比相矛盾的传统缺点。
[0223]
基于上述对于驻波角的精准检测,本发明将陀螺的不对称性因素建模为外部扰动,这就可以将陀螺不理想因素的实时抵消问题转变成控制系统中的轨迹跟踪问题,根据实时跟踪全角陀螺的不对称参数利用静电力将其抵消,形成高性能全角微陀螺。
[0224]
iii.将全角陀螺的在线配平问题转化为高频激励的轨迹跟踪问题。
[0225]
理想条件下的陀螺完全对称且不存在模态耦合,施加高频激励信号后的陀螺驻波角理想轨迹表达式为:θ=λcos(θ
e
t)。
[0226]
实际不理想情况存在模态阻尼和刚度不对称以及模态耦合,这些误差以谐波的形式进入陀螺,进而导致陀螺的响应解,即陀螺的驻波角呈现出非线性。
[0227]
利用已知高频虚拟电旋转的理想轨迹和实际轨迹做差,即可得到全角微陀螺的误差形式为(系统的基于级数形式的误差动力学方程):
[0228][0229]
其中,
[0230]
δω表示谐振频率分裂因数,δq(q值)表示品质因数不对称因数,c
xy
表示阻尼耦合因数,k
xy
表示刚度耦合因数。
[0231]
η1(δω,δq,c
xy
,k
xy
)表示由高频激励产生的cos(θ
e
t)分量的系数估计量。
[0232]
η2(δω,δq,c
xy
,k
xy
)表示由高频激励产生的cos(2θ
e
t)分量的系数估计量。
[0233]
η3(δω,δq,c
xy
,k
xy
)表示由高频激励产生的cos(3θ
e
t)分量的系数估计量。
[0234]
由此可见,全角陀螺的在线配平问题,可等价为高频电激励的轨迹跟踪问题。
[0235]
此问题框架下,陀螺的非对称项带来的谐波等响应被等价为外部干扰,如:
[0236]
微控制器12通过能量控制,能量分配控制以及误差校正控制产生静电力,零差跟踪理想轨迹θ=λcos(θ
e
t),则全角陀螺处于被动态配平的状态。
[0237]
iv.依据陀螺的高频动力学模型,并考虑建模误差(建立动力学模型并不能把所有的误差因素包含在内,因此,建模时存在误差),设计鲁棒式的跟踪控制算法,基于鲁棒式的跟踪控制算法,对步骤iii中误差进行跟踪控制,通过施加静电力将误差减弱甚至抵消。
[0238]
本发明根据每个关键参数的不确定性,设定参数变化范围的上下界,增强该控制方法的鲁棒性同时,也提高了此方法的实用性,具体参数设定为:
[0239]
ω
b
≤δω≤ω
s
,q
b
≤δq≤q
s
,c
b
≤c
xy
≤c
s
,k
b
≤k
xy
≤k
s
。
[0240]
其中,ω
b
、ω
s
分别表示δω的上界和下界;q
b
、q
s
分别表示δq的上界和下界,c
b
、c
s
分别表示c
xy
的上界和下界,k
b
、k
s
分别表示k
xy
的上界和下界。
[0241]
建立误差的能量储存函数s(e):
[0242]
并设计控制律满足如下条件:
[0243]
t表示时间,e(t)表示控制误差,e(0)表示初始误差,s(e(t))表示误差能量函数,s(e(0))表示误差初始能量,f
θ
表示输入控制力,ψ(e,f
θ
)表示能量耗散函数。
[0244]
通过构造上述储能函数和控制律,对陀螺施加静电力校正陀螺的不对称性,则实际驻波角能够良好地跟踪高频虚拟电调制信号。
[0245]
将对误差跟踪控制过程中微处理计算的误差量,转化为静电力并直接反馈在陀螺(校正电极)上,等效地消除谐振陀螺的不对称性误差,将陀螺保持在配平状态。
[0246]
通过以上自动配平方法,利于形成可靠、高性能的直接测量角度的全角陀螺。
[0247]
本发明方法充分考虑了基于级数形式的误差动力学方程,在参数存在区间误差的约束下设计了零误差的高效跟踪控制算法,虽然由级数形式构成的轨道角动力学形式较为复杂,但是通过合理提取影响因素较大的项,即为级数形式系数较大的前几项,构成实际轨迹方程并条件化简,并考虑不理想参数的上下界,可有效地构造收敛的控制律。
[0248]
本发明方法根据完美对称陀螺的高频激励中不存在谐波的特点,将陀螺的动态配平问题转化为了标准参考信号轨迹跟踪的问题,提高了动态配平的可靠性。
[0249]
当然,以上说明仅仅为本发明的较佳实施例,本发明并不限于列举上述实施例,应当说明的是,任何熟悉本领域的技术人员在本说明书的教导下,所做出的所有等同替代、明显变形形式,均落在本说明书的实质范围之内,理应受到本发明的保护。