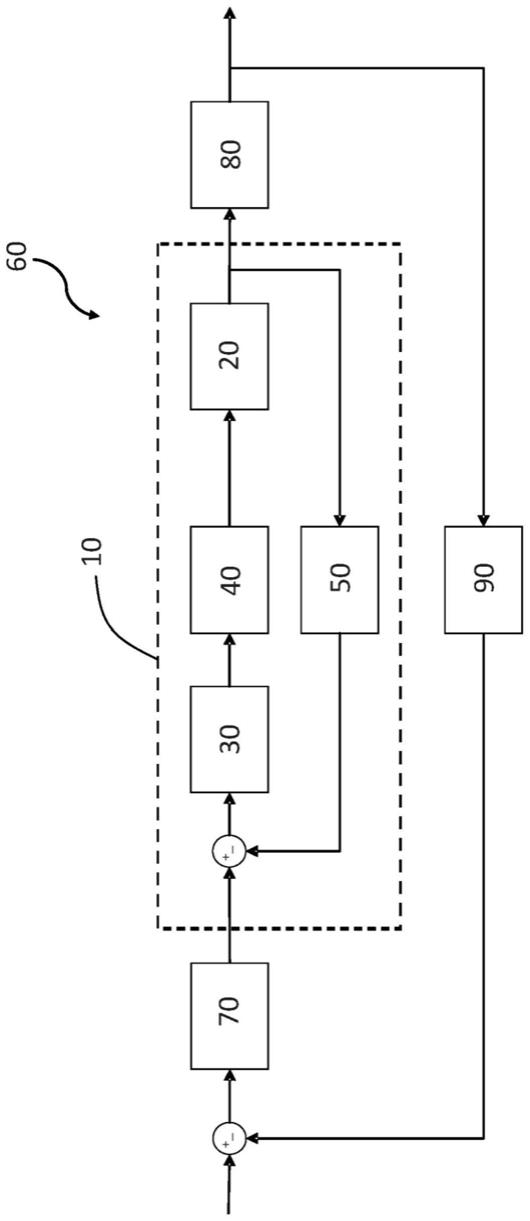
1.本发明涉及一种用于在正常运行中对工艺阀进行连续的功能监控的诊断方法,一种用于工艺阀的诊断模块和一种工艺阀。
背景技术:2.工艺阀可以在大量应用中使用。示例性的实例是食品工业。在那里,例如使用灌装设施,以便将液体灌装到容器中。灌装设施具有工艺阀,所述工艺阀又通常由电磁阀控制。在此,工艺阀被气动地操控,并且又借助于电磁阀控制为此所需的气动压力。
3.从现有技术中已知用于尽可能地保证工艺阀的正确功能的不同方式。
4.ep 1 555 472a示出在用于流体控制的阀中进行功能监控的方法,所述阀具有至少一个用于阀操作的电操作部件,所述电操作部件与用于显示操作部件的当前运行状态的运行状态显示器耦合。所述方法首先包括:借助于光学传感器来光学地检测所显示的运行状态的变化,并且将运行状态变化规定为起始时间点t0。此外,作为运行状态变化的结果借助于检测装置从起始时间点t0起测量在阀输出端处的压力变化,并且产生与压力变化相关联的压力相关的信号。现在验证阀的切换状态,其方式为检查:从起始时间点t0起在特定的时间之后是否存在特定的压力相关的信号。
技术实现要素:5.一个目的在于,及早识别工艺阀的功能故障,而不中断工艺设施的正常运行,使得在运行进行时可以尽可能避免工艺阀的停用。
6.在该上下文中提出一种用于在正常运行中对工艺阀进行连续的功能监控的诊断方法。
7.诊断方法包括:从输送给工艺阀的输入信号中确定具有时间离散的工艺目标值的工艺目标数据。
8.诊断方法还包括:借助于与工艺阀相关联的路程测量系统来确定具有时间离散的工艺实际值的工艺实际数据。
9.根据一个方面,诊断方法包括:通过将工艺目标数据和工艺实际数据相互比较,分析与工艺目标数据相关的工艺实际数据,以便识别以所述方式限定的故障状态。
10.以所述方式,对于诊断仅使用工艺阀的总归存在的路程测量系统,以便确定对应的工艺实际数据,并且对所述工艺实际数据结合从工艺阀的输入信号中确定的工艺目标数据进行评估。有利地,不需要另外的传感装置。诊断可以持久地或持续地在正常运行中进行。
11.根据一个有利的方面,工艺目标值和工艺实际值可以是归一化(无量纲)值。这简化工艺目标值和工艺实际值的直接比较。归一化(无量纲)值可以从工艺阀的对应的位置或姿态推导,所述位置或姿态已借助于路程测量系统检测出。
12.根据另一有利的方面,限定的故障状态包括过低的网络压力、工艺阀的堵塞、泄
漏、压力波动和/或运行时间变化。优选地,识别所有提到的故障状态。
13.一旦工艺实际值以绝对(数值)小于预先限定的变化率的变化率接近工艺目标值,可以识别出过低的网络压力。预先限定的变化率此外与工艺阀的构造、其尺寸和可能也与其他工艺参数相关。预先限定的变化率(作为极限值)因此优选地根据实验来确定。特别明确地,如果在这种情况下工艺实际值仅仅接近工艺目标值到如下程度,即:不低于工艺实际值和工艺目标值之间的预定的最小值间距,那么可以识别出过低的网络压力。最小间距值也能根据需要选择或根据实验确定。
14.一旦工艺实际值的变化率在工艺实际值接近工艺目标值期间在预定的最大时间间隔之内以预先限定的最小值降低至预定的最大变化率,可以识别出工艺阀的堵塞。在多种情况下,变化率在堵塞时几乎直接降低为零。在如下情况下特别明确地识别:当工艺实际值在变化率变化之后不再达到工艺目标值时,即:在一个时间间隔之内工艺实际值并没有接近工艺目标值到小于工艺实际值和工艺目标值之间的预定的最小值间距的程度。
15.一旦随着时间推移工艺实际值距工艺目标值越来越远,可以识别出(例如在管路中的)泄漏,尤其当工艺目标值固定时如此。在如下情况下特别明确地识别,即在此超过工艺实际值和工艺目标值之间的根据需要选择的最小值间距。
16.一旦在工艺目标值不变的情况下工艺实际值在短的限定的时间间隔之内不仅有增大而且有减小,可以识别出压力波动(也通常称作为压力冲击)。尤其,在该时间间隔之内工艺实际值的变化率可以具有多于一次的符号变换。在如下情况下特别确定地识别,即工艺实际值和/或变化率分别在限定的时间间隔开始之前和结束之后相差不大于预先限定的数值。在此也可以根据需要选择预先限定的数值。
17.为了能识别运行时间变化,诊断方法可以包括:通过在正常运行开始之前和/或开始时与工艺目标数据相关地存储工艺实际数据,产生工艺实际参考数据;和将工艺实际数据与相对应的工艺实际参考数据比较。如果在工艺目标数据相同的情况下工艺实际数据的变化率与工艺参考数据的变化率相差(根据需要选择的)预定的最小值间距,那么识别出运行时间变化。
18.此外,提供一种用于工艺阀的计算机实现的诊断模块。诊断模块包括代码,借助于所述代码可以在(微)处理器上运行所描述的诊断方法。
19.此外提供一种用于工艺阀的诊断单元。诊断单元包括:用于工艺阀的输入信号的第一接口;用于与工艺阀相关联的路程测量系统的位置信号的第二接口;存储器,在其上保存有诊断模块的代码;和用于运行代码的处理器,以便运行诊断方法。
20.附加地提供一种工艺阀,所述工艺阀包括具有诊断模块或诊断单元的阀控制机构。
21.原则上,在分析与工艺目标数据相关的工艺实际数据时,进行工艺实际数据与工艺目标数据的比较。
22.由此,识别出工艺阀的故障状态,所述故障状态不是控制故障。
23.尤其为此将工艺实际数据的曲线分布,例如阀姿态关于时间的变化曲线与从工艺目标数据中应预期的曲线分布,即基于工艺目标数据的曲线分布进行比较。
24.用于比较并且基于工艺目标数据的数据也可以称作为应预期的工艺实际数据,其中从工艺目标数据中生成对应的应预期的曲线分布,将其与工艺实际数据的曲线分布比
较,以便辨识表征性的偏差。
25.就此而言可以附加地提出,基于确定的工艺目标数据,首先确定应预期的工艺实际数据,即应预期的曲线分布。在分析中,随后将应预期的工艺实际数据与工艺实际数据比较,即将基于工艺目标数据应预期的曲线分布与工艺实际数据的曲线分布比较。
26.如开头提到那样,相应的数据是借助于路程测量系统已确定的数据,即例如工艺阀的阀姿态。换句话说,工艺实际数据是基于阀姿态或阀位置确定的数据,即借助于路程测量系统确定的数据。
27.因此,可以将实际的阀姿态(工艺实际数据)与预设的阀姿态(工艺目标数据)比较,其中辨识和表征对应的偏差。因此,根据对所确定的偏差的表征,推断出工艺阀的相关的限定的故障状态。
28.因此在比较时,原则上能辨识表征性的偏差,经由所述偏差能够识别出限定的故障状态。
29.这表示,确定基于工艺实际数据的实际存在的曲线分布与基于工艺目标数据的应预期的曲线分布的偏差,其中偏差根据其特征对于限定的故障状态是明确的,使得基于所辨识的偏差识别出限定的故障状态。
30.在正常运行进行时执行故障诊断,其中尤其不在目标值变化时进行比较或仅在之前没有发生目标值变化的所限定的时间段、例如1秒或2秒中进行比较。换句话说,如果工艺目标数据之前是固定的,那么进行比较。因此可以保证,工艺阀总的来说以其实际工艺数据接近目标工艺数据,以便能够探测对应的限定的故障状态。
31.优选地,仅在之前未发生目标值突变或未发生目标值变化时才进行比较。
32.这是由于,根据本发明并不是要检测控制故障,例如调节时间、动作时间或控制偏差。而是要识别持续性的故障状态,尤其是与控制无关的故障状态,因此如果之前没有发生目标值变化,才进行工艺实际数据和工艺目标数据的比较,尤其是它们的曲线分布的比较。
33.虽然分析可以在正常操作中持久地进行,然而如果之前发生目标值变化,那么至少(暂时地)中止比较进而分析,或者丢弃分析结果。
34.换句话说,即根据本发明的诊断方法基于工艺实际数据与工艺目标数据的长期偏差,也就是说在给定目标值的情况下随时间出现的偏差。
35.尤其可以在目标值变化之前不久进行比较。
36.在分析时,尤其在将工艺目标数据和工艺实际数据比较时,也可以确定,工艺目标数据多快,即以何种变化率接近工艺实际数据,以便因此确定,是否存在限定的故障状态之一,尤其是过小的网络压力。为此,将所确定的变化率例如与参考变化率进行比较,工艺实际数据以上述变化率接近相应的工艺目标数据,其中尤其从经验数据和/或历史数据中确定参考变化率。
37.工艺目标数据可以是操控数据,即用于操控工艺阀的数据。
38.因此可以进行曲线形状的比较,使得识别出工艺实际数据的曲线分布的曲线形状与工艺目标数据的曲线分布的曲线形状的对应的特征性的偏差,这又与工艺阀的所属的限定的故障状态关联。
附图说明
39.下面,根据实施例并且参照附图详细阐述本发明的特征和方面。在此示出:
40.‑
图1示出具有工艺阀的工艺控制回路的简化的示意方框图;
41.‑
图2示出具有诊断单元的工艺阀的简化的示意方框图;
42.‑
图3示出具有工艺实际数据和工艺目标数据的示意图的图表,以将在网络压力监控时的表征性特征可视化;
43.‑
图4示出具有工艺实际数据和工艺目标数据的示意图的图表,以将在堵塞识别时的表征性特征可视化;
44.‑
图5示出具有工艺实际数据和工艺目标数据的示意图的图表,以将在泄漏监控时的表征性特征可视化;
45.‑
图6示出具有工艺实际数据和工艺目标数据的示意图的图表,以将在压力波动识别时的表征性特征可视化;以及
46.‑
图7示出具有工艺实际数据和工艺目标数据的示意图的图表,以将在探测运行时间变化时的表征性特征可视化。
具体实施方式
47.在图1中以简化的方框图示出在工艺控制回路60中的工艺阀10。工艺阀10包括执行阀20、控制模块30、执行系统40和路程测量系统50。工艺阀10与工艺控制器70、工艺80和工艺传感器90组合到工艺控制回路60中。工艺传感器90可以是任意传感器并且可以测量物理变量,如例如温度、流量或压力。
48.图2作为简化的方框图示出具有诊断单元100的工艺阀10。包括诊断模块110的诊断单元100连接于工艺阀10,使得诊断模块110可以处理工艺目标值s(下面也简称为“目标值”或“目标数据”)和工艺实际值s(下面也称作为“实际值”或“实际数据”)。
49.诊断单元100包括用于工艺阀的输入信号的第一接口;用于路程测量系统的位置信号的第二接口;存储器,其存储有诊断模块100的代码;和用于运行代码的处理器。计算机实现的诊断模块110包括代码,以便在处理器上运行所描述的诊断方法。替选地,诊断模块110可以作为软件功能直接在工艺阀10的阀控制机构中实现。
50.借助于工艺阀10的路程测量系统50,检测在工艺控制回路60正在运行(控制运行)时的实际数据s。将检测到的实际数据s与已知的目标数据s比较。从表征性的偏差中识别典型的故障,如例如具有网络压力、在配件或驱动器中的堵塞、在驱动器或执行系统中的泄漏、压力波动或运行时间变化的问题。
51.用于在正常运行中对工艺阀10进行连续的功能监控的诊断方法包括以下步骤:
52.‑
从输送给工艺阀10的输入信号中确定具有时间离散的工艺目标值的工艺目标数据s;
53.‑
借助于与工艺阀10相关联的路程测量系统50来确定具有时间离散的工艺实际值的工艺实际数据s;
54.‑
通过将工艺目标数据(s)和工艺实际数据(s)相互比较,分析与工艺目标数据s相关的工艺实际数据s,以便识别限定的故障状态。
55.工艺目标值和工艺实际值是归一化值。优选地,归一化值是无量纲的。
56.限定的故障状态包括过低的网络压力、工艺阀的堵塞、泄漏、压力波动和/或运行时间变化。
57.换句话说,根据简单地分析和比较实际曲线与目标曲线,即实际值的和目标值的曲线走向,可以识别在工艺阀中的典型的故障状态。为此使用在正常运行中的曲线形状。
58.下面根据五个表征性的偏差来阐述实际曲线与目标曲线的比较,所述偏差在图3至7中示出并且在下文中详细描述。
59.在图3至7中关于以秒为单位的时间(在x轴上)示出作为以百分比计的归一化值(在y轴上)的相应的目标数据和实际数据。作为目标曲线203
‑
207,输入信号绘制为实线。分别所属的实际曲线303
‑
307在图3和图4中在第一部分中示出工艺阀的无故障的典型的动作(ansprechen),并且在第二部分中示出数据的表征性的偏差,即典型的故障状态,并且绘制为虚线。
60.图3示出目标曲线203与典型的实际曲线303的如在具有网络压力的问题的情况下出现的表征性的偏差。在时间点t0开始的未受干扰的切换过程中,实际曲线303顺利地朝向目标值的终值e移动。而在时间点t1开始的受干扰的切换过程中,实际曲线303比正常明显更慢地朝向终值e’移动,终值e’不对应于目标值e。然而也可能的是,还未达到目标值e。因此,表征性的不仅是目标值e,而且还有达到目标值e的时间变化曲线。故障例如不仅是根本没有达到目标值e,而是还有虽然达到目标值e,然而这不在限定的时间之内发生。
61.因此,如果工艺实际值303以绝对(数值)小于预先限定的变化率503的变化率接近工艺目标值203,那么识别出过低的网络压力。在上述情况下,工艺实际值并没有接近工艺目标值203到如下的程度:低于在工艺实际值303和工艺目标值203之间的预定的最小值间距403。
62.图4示出如在驱动器堵塞的情况下出现的与目标曲线204的表征性的偏差。在时间点t0开始的切换过程中,实际曲线304达到目标值的终值e。在时间点t1开始的受干扰的切换过程中,实际曲线304在时间点t2示出在终值e”处的尖棱的中断,终值e”不对应于目标值e。直至时间点t3没有达到目标值e。
63.因此,如果工艺实际值304的变化率在工艺实际值304接近工艺目标值204期间在预定的最大时间间隔504之内以预先限定的最小值降低至预定的最大变化率(突然地),那么识别出工艺阀10的堵塞。在上述情况下,在时间间隔之内工艺实际值304并没有接近工艺目标值204如下的程度:低于工艺实际值304和工艺目标值204之间的预定的最小值间距404。
64.图5示出如在泄漏的情况下出现的与目标曲线205的表征性的偏差。在时间点t0的切换过程之后,在时间点t4,实际曲线305达到目标曲线205的终值e。尽管未发生目标值变化从而控制变量也不应改变,但是实际值305在故障情况下向上305a或向下305b离开。在此实际值从公差带405离开。
65.因此,如果随着时间推移工艺实际值305距工艺目标值205越来越远,尽管工艺目标值205是固定的,那么识别出泄漏。标准可以是,是否超过在工艺实际值305和工艺目标值205之间的预定的最小值间距405(前述公差带)。
66.图6示出如在压力波动的情况下出现的与目标曲线206的表征性的偏差。在时间点t0的切换过程之后,在时间点t5,实际曲线306达到目标曲线206的终值e。实际曲线306在时
间点t3和t4之间(δt)示出压力波动的表征性的图示。
67.如果在工艺目标值206不变的情况下工艺实际值306在限定长度的时间间隔之内不仅有增大而且有减小,那么识别出压力波动。在此,工艺实际值306的变化率在该时间间隔之内具有多于一次的符号变换。工艺实际值306或其变化率在压力波动的时间间隔开始之前和结束之后相差不大于预先限定的数值。
68.图7示出两个实际曲线507、307和目标曲线207。在设备新状态中,将工艺阀10的位置/时间变化曲线记录成x/t图示,并且在诊断单元100中作为参考曲线507存储。通过将参考与在正常运行中的x/t变化曲线(例如实际曲线307)比较,例如可以探测出变化的摩擦和由此造成的堵塞风险。
69.诊断方法为此包括:通过在正常运行开始之前和/或开始时与工艺目标数据207相关地存储工艺实际数据507,产生工艺实际参考数据;和在运行进行中将工艺实际数据307与相对应的工艺实际参考数据507比较。如果在工艺目标数据507相同的情况下工艺实际数据307的变化率与工艺参考数据507的变化率相差预定的最小值间距407,那么识别出运行时间变化。
70.附图标记列表
71.10
ꢀꢀꢀꢀꢀꢀꢀꢀꢀꢀꢀꢀ
工艺阀
72.20
ꢀꢀꢀꢀꢀꢀꢀꢀꢀꢀꢀꢀ
执行阀
73.30
ꢀꢀꢀꢀꢀꢀꢀꢀꢀꢀꢀꢀ
控制模块
74.40
ꢀꢀꢀꢀꢀꢀꢀꢀꢀꢀꢀꢀ
执行系统
75.50
ꢀꢀꢀꢀꢀꢀꢀꢀꢀꢀꢀꢀ
路程测量系统
76.60
ꢀꢀꢀꢀꢀꢀꢀꢀꢀꢀꢀꢀ
工艺控制回路
77.70
ꢀꢀꢀꢀꢀꢀꢀꢀꢀꢀꢀꢀ
工艺控制器
78.80
ꢀꢀꢀꢀꢀꢀꢀꢀꢀꢀꢀꢀ
应控制的工艺
79.90
ꢀꢀꢀꢀꢀꢀꢀꢀꢀꢀꢀꢀ
工艺传感器
80.100
ꢀꢀꢀꢀꢀꢀꢀꢀꢀꢀꢀ
诊断单元
81.110
ꢀꢀꢀꢀꢀꢀꢀꢀꢀꢀꢀ
诊断模块
82.203
……
207
ꢀꢀꢀꢀ
目标曲线
83.303
……
307,507
ꢀꢀ
实际曲线
84.403
……
407
ꢀꢀꢀ
预定的最小值间距
85.503
ꢀꢀꢀꢀꢀ
预先限定的变化率
86.504
ꢀꢀꢀꢀꢀ
预定的最大时间间隔
87.s
ꢀꢀꢀꢀꢀꢀꢀ
工艺目标值
88.s
ꢀꢀꢀꢀꢀꢀꢀꢀꢀꢀꢀꢀꢀ
工艺实际值
89.t0
……
t7
ꢀꢀꢀꢀꢀꢀ
时间点
90.e
ꢀꢀꢀꢀꢀꢀꢀꢀꢀꢀꢀꢀꢀ
工艺目标值的终值
91.e
’……
e
”ꢀꢀꢀꢀꢀꢀ
工艺实际值的终值