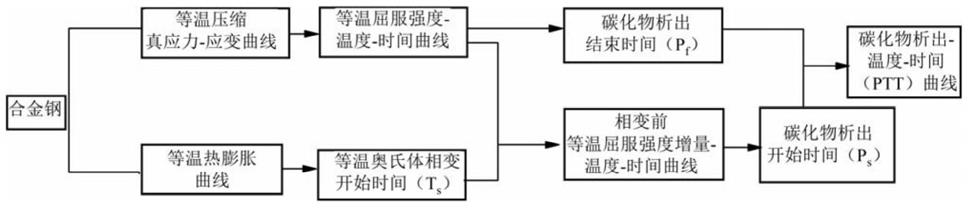
1.本发明属于合金钢热加工技术领域,特别涉及基于等温应力和相变测定碳化物析出动力学曲线的方法。
背景技术:2.通过添加微合金元素和结合控轧控冷工艺控制碳化物以纳米尺寸高密度地在铁素体中析出,能够显著提高钢的强度并保持良好的韧性。合金钢中纳米碳化物在铁素体中的析出温度窗口很窄且析出特性对热处理条件(如应变、等温温度、等温时间)非常敏感,热处理制度的改变会引起强度的显著差异。通常认为在碳化物析出动力学曲线的鼻尖处温度进行等温热处理能够获得最大的析出强化效果。因此测定合金钢奥氏体在等温相变温度等温过程中碳化物的析出动力学曲线对于生产实践的指导具有重要的意义。
3.合金钢在等温相变温度等温过程中会出现奥氏体相变和析出的一个动态变化过程,难以把两者分开和直接确定析出的开始和结束。因此,对奥氏体在等温相变过程中碳化物析出动力学曲线的研究和测定很少。目前,多数的研究是首先对碳化物的形核位置进行设定,然后基于平衡条件下的数学模型计算。实际生产中,奥氏体的等温相变过程都是非平衡态的,而且析出的位置也不是唯一性的。中国授权专利“一种碳化物等温析出动力学曲线测定的方法(cn106018117b)”,通过实验测定合金钢等温相变过程中碳化物析出动力学曲线,该方法通过测定合金钢在不同等温处理后冷却到室温后的压缩应力的差值来判定奥氏体等温析出开始和结束。该方法认为室温压缩应力的差值来源于碳化物的析出。但由于奥氏体发生相变产生的不同组织也会导致压缩应力值的差异,而且由等温相变温度冷却到室温的过程中也会发生析出,这对实验结果存在影响。因此,需寻求一种能够有效分开相变和析出,避免组织差异干扰的方法测定奥氏体等温相变过程中碳化物析出动力学曲线,进而为改进和优化热处理工艺参数获取最佳力学性能提供指导。
技术实现要素:4.鉴于此,本发明提出了一种基于等温应力和相变测定碳化物析出动力学曲线的方法,本方法操作简单且测定的等温屈服强度值能够直观地反映等温过程中碳化物析出强化效应。此外,本方法适用于所有奥氏体等温相变过程中有碳化物析出的钢种。
5.为了实现前述发明目的,本发明提供的基于等温应力和相变测定碳化物析出动力学曲线的方法,包括以下步骤:
6.(1)通过gleeble
‑
3800热模拟试验机获取合金钢在设定温度不同等温时间下的真应力
‑
应变曲线,并取2%应变处的应力值作为等温屈服强度值σ
y
,绘制σ
y
和等温温度
‑
时间变化关系曲线,确定碳化物析出结束时间p
f
。
7.(2)利用gleeble
‑
3800热模拟试验机上配备的热膨胀仪测定合金钢在设定温度下的相变开始时间(t
s
)和结束时间(t
f
)。
8.(3)根据获取的相变开始时间t
s
,绘制合金钢在不同设定温度下相变开始前等温
屈服强度增量随等温时间的变化曲线,确定不同等温温度下碳化物开始析出时间p
s
。
9.(4)根据获取的碳化物的析出开始时间p
s
和结束时间p
f
,绘制合金钢碳化物的析出
‑
温度
‑
时间(ptt)曲线。
10.进一步地,步骤(2)所述的等温相变过程中测定相变动力学曲线的方法,其原理在于:钢中不同相或组织的热膨胀系数从小到大为:马氏体<贝氏体<珠光体<铁素体<奥氏体。等温过程中发生奥氏体相变时必然伴随体积得膨胀而导致热膨胀仪测得的热膨胀曲线出现拐点,通过测得拐点处的时间来判定等温相变开始和结束时间。
11.2.根据权利要求(1)和(2)所述的测定等温相变过程中碳化物析出动力学曲线的方法,其特征在于,所述步骤具体包括:
12.(a)合金钢试样加工成粗糙度ra≤0.4μm的圆柱形试样。
13.(b)用热电偶焊接机把热电偶丝焊接在圆柱形试样正中间,两根热电偶丝距离控制在1mm左右。
14.(c)用高温润滑剂依次在圆柱试样两端连接金属钽片和石墨片。
15.(d)把连接钽片和石墨片的圆柱试样安装在gleeble
‑
3800热模拟试验机实验舱内指定位置的夹具两端,微调主轴轴向位移,使夹头刚好压紧圆柱形试样。
16.(e)把热膨胀仪的石英玻璃夹头夹紧合金样品,并与热电偶丝在样品上的位置处于用一截面上;热膨胀仪的输出数据线与热模拟试验机的传感器接口连接;
17.(f)把热电偶丝的另一端与gleeble
‑
3800热模拟试验机的t1温度通道相连接,然后关上实验舱舱门并抽真空。
18.(g)在gleeble
‑
3800热模拟试验机自带的quizsim软件编写设定的试验工艺流程。
19.(h)实验舱内真空度达到要求后,依次启动操作面板上“run”按钮和点击quizsim软件上的“run”开始运行设定的方案进行试验。
20.(i)一个试验工艺结束后,改变试验工艺参数,重复(a)
‑
(h)进行下一个试验,直至试验结束。
21.(j)试验结束后,将gleeble
‑
3800热模拟试验机采集到的温度、时间、真应变、真应力和热膨胀量数值导入试验机配备的origin软件中,获取设定的不同等温温度和时间下的真应力
‑
应变曲线,以及随时间变化的热膨胀曲线,进而获得等温屈服强度值和不同等温温度下的相变开始和结束时间。
22.进一步地,所加工的圆柱试样要求是长度和直径比不大于2,如φ6
×
10mm,φ10
×
15mm,φ8
×
12mm等其它尺寸的圆柱形试样。
23.进一步地,热电偶焊接机电压设置为34
‑
38v之间。
24.进一步地,热膨胀仪夹持圆柱试样位置符合“上下对正,左右等距”原则。
25.进一步地,启动gleeble
‑
3800试验机运行的真空度要低于1.5
×
10
‑1pa。
26.进一步地,设定试验的工艺流程参数具体为:
27.(1)圆柱形试样在gleeble
‑
3800热模拟试验机上以1
‑
20℃/s加热到1150
‑
1280℃并保温3
‑
10min,使试样充分奥氏体化并溶解除含n化合物的以外的第二相。
28.(2)以10
‑
100℃/s冷到1000
‑
1150℃保温5
‑
15s后变形10
‑
30%,再以10
‑
100℃/s冷到800
‑
950℃等温5
‑
20s后变形10
‑
30%。变形速率为0.5
‑
10.s
‑1。
29.(3)两道次变形后的试样以10
‑
100℃/s分别冷到550
‑
750℃,等温不同时间后变形
10
‑
30%,变形速率为0.5
‑
10s
‑1,等温时间为5
‑
10800s。
30.与现有技术相比,本发明能够实现的有益效果至少如下:
31.本方法可以有效避开合金钢碳化物等温析出过程中相变以及相变组织差异对碳化物析出开始点测定的干扰,并能揭示碳化物析出过程和相变的相互作用。此外,本方法操作简单且测定的等温屈服强度值能够直观地反映等温过程中碳化物析出导致强度增加的量,对改进和优化合金钢热处理工艺参数以获取最佳力学性能提供很好地指导作用。
附图说明
32.图1本发明测定方法的流程图。
33.图2本发明实施例的试验工艺示意图。
34.图3实施例中ti
‑
mo合金钢700℃等温的热膨胀曲线和奥氏体在600
‑
700℃的温度
‑
时间
‑
相变(ttt)曲线示意图。
35.图4实施例中ti
‑
mo合金钢不同等温温度下的等温压缩真应力
‑
应变曲线示意图。
36.图5实施例中ti
‑
mo合金钢等温屈服强度随时间和温度变化曲线示意图。
37.图6实施例中ti
‑
mo合金钢在不同等温温度相变前等温屈服强度增量随等温时间变化曲线示意图。
38.图7实施例中ti
‑
mo合金钢等温过程中碳化物析出
‑
温度
‑
时间(ptt)曲线示意图。
具体实施方式
39.下面结合实施例和附图对本发明方法作进一步的描述,但是需要说明的是,实施例并不构成对本发明保护范围的限定。
40.本发明提供的基于等温应力和相变测定碳化物析出动力学曲线的方法,包括以下步骤:
41.步骤1:获取合金钢在设定温度内不同等温时间下的真应力
‑
应变曲线,并取屈服应力点的应力值作为等温屈服强度值σ
y
,绘制等温屈服强度值σ
y
和等温温度
‑
时间变化关系曲线,确定碳化物析出结束时间p
f
。
42.在本发明其中一个实施例中,通过gleeble
‑
3800热模拟试验机来获取合金钢在设定温度内不同等温时间下的真应力
‑
应变曲线。
43.在本发明其中一个实施例中,没有明显屈服点的材料通常都将偏置2%应变的应力值视作屈服应力点。
44.步骤2:测定合金钢在设定温度下的相变开始时间(t
s
)和结束时间(t
f
)。
45.在本发明其中一个实施例中,利用gleeble
‑
3800热模拟试验机上配备的热膨胀仪获取合金钢等温相变过程中的热膨胀曲线,通过测定热膨胀曲线上的拐点处时间获得到在设定温度下的相变开始时间(t
s
)和结束时间(t
f
)。
46.步骤3:根据获取的相变开始时间t
s
,绘制合金钢试样在设定的不同等温温度下相变开始前的等温屈服强度增量随等温时间的变化曲线,确定不同等温温度下碳化物开始析出时间p
s
。
47.步骤4:根据获取的碳化物的析出开始时间p
s
和结束时间p
f
,绘制合金钢碳化物的析出
‑
时间
‑
温度(ptt)曲线。
48.在本发明其中一个实施例中,选用的材料为含ti
‑
mo微合金钢,其化学成分及其含量是:c为0.04~0.07wt%,si为0.2~0.3wt%,mn为1.5~1.8wt%,ti为0.09~0.12wt%,mo为0.18~0.24wt%,n<0.006%wt%,p<0.01wt%,s<0.010wt%,其余为fe及不可避免的杂质。
49.在本发明其中一个实施例中,合金钢的试样呈圆柱形,长度和直径比不大于2。如φ6
×
10mm、φ10
×
15mm、φ8
×
12mm或其它尺寸的圆柱形试样。
50.在本发明其中一个实施例中,步骤1和步骤2具体包括以下步骤:
51.(a)加工微合金钢试样,试样加工成粗糙度ra≤0.4μm、尺寸为φ10
×
15mm的圆柱形试样。
52.(b)把热电偶焊接机电压调到38v,然后把热电偶丝焊接在圆柱形试样正中间,两根热电偶丝间距控制在1mm左右。
53.在本发明其中一个实施例中,所述热电偶丝采用k型热电偶丝或r型热电偶丝。
54.(c)用高温润滑剂分别在圆柱形试样的两端均分别依次连接金属钽片和石墨片。
55.(d)把连接了金属钽片和石墨片的圆柱形试样安装在实验舱内的夹具夹头两端,微调试热模拟试验机的主轴轴向位移,使夹头刚好压紧圆柱形试样。
56.(e)把热膨胀仪的石英玻璃夹头夹紧合金样品,并与热电偶丝在样品上的位置处于用一截面上;热膨胀仪的输出数据线与热模拟试验机的传感器接口连接;
57.(f)把热电偶丝的另一端与热模拟试验机中的t1温度通道相连接,然后关上实验舱舱门并抽真空。
58.(g)在gleeble
‑
3800热模拟试验机自带的quizsim软件编写设定试验的工艺流程。
59.(h)待实验舱内真空度降低到1.5
×
10
‑1pa后,依次启动gleeble热模拟试验机操作面板上“run”操作按钮和点击quizsim软件上的“run”启动机器和运行设定的试样方案进行试验。
60.(i)一个试验工艺结束后,改变试验工艺参数,重复(a)
‑
(h)进行下一个试验,直至试验结束。
61.(j)试验结束后,将gleeble
‑
3800热模拟试验机采集到的温度、时间、真应变、真应力和热膨胀量数值导入试验机配备的origin软件中,获取设定的不同等温温度和时间下的真应力
‑
应变曲线以及随时间变化的热膨胀曲线,进而获得等温屈服强度值和不同等温温度下的相变开始和结束时间。
62.在本发明中,工艺流程参数设置为:
63.(1)合金钢试样在gleeble
‑
3800热模拟试验机上以1
‑
20℃/s加热到1150
‑
1280℃并保温3
‑
10min,使试样充分奥氏体化并溶解除含n化合物的以外的第二相。
64.(2)以10
‑
100℃/s冷到1000
‑
1150℃保温5
‑
15s后变形10
‑
30%,再以10
‑
100℃/s冷到800
‑
950℃等温5
‑
20s后变形10
‑
30%。变形速率为0.5
‑
10.s
‑1。
65.(3)两道次变形后的试样以10
‑
100℃/s分别冷到550
‑
750℃,等温不同时间后变形10
‑
30%,变形速率为0.5
‑
10s
‑1,等温时间为5
‑
10800s。
66.见图2所示,在本发明的一可行实施例中,ti
‑
mo合金钢的工艺参数和流程具体为:
67.(1)在gleeble
‑
3800热模拟试验机上以10℃/s把试样加热到1200℃并保温5min。
68.(2)以20℃/s冷到1050℃等温10s后变形20%,再以20℃/s冷到900℃等温15s后变
形20%。变形速率为1.0s
‑1。
69.(3)两阶段变形后,试样以30℃/s冷到600
‑
700℃,等温不同时间后变形30%,变形速率为1.0s
‑1,等温时间为5
‑
10800s。
70.图3是ti
‑
mo合金钢在700℃等温的热膨胀曲线和基于热膨胀曲线拐点测定的ti
‑
mo合金钢在600
‑
700℃的等温相变曲线。通过测定等温相变过程热膨胀曲线拐点处(a点和b点)的时间可以得出相变基本在10min内结束,其中在625℃等温时的相变孕育期最长,约为33s。
71.图4是ti
‑
mo合金钢在600
‑
700℃等温5
‑
10800s后的真应力
‑
应变曲线。测取真应力
‑
应变曲线2%应变处的应力值可以获得图5所示的等温屈服强度随温度和时间变化的曲线,其中每条曲线上的两个箭头位置分别代表相变的开始和结束时间。每个等温温度下的等温屈服强度均在相变过程中随等温时间的增加快速增加,这说明相变促进碳化物的析出。相变结束后,继续延长等温时间,等温屈服强度继续增加,当达到峰值强度后,随等温时间的增加而开始下降。显然,相变结束后等温屈服强度继续随等温时间的延长而增加是由于等温过程中析出的碳化物产生的析出强化导致。在等温过程中,峰值应力的出现表明碳化物产生的析出强化效应和钢中由于晶粒长大和位错密度降低导致的强度软化的协调效应匹配下使钢的强度达到最大值,因此,可以定义达到峰值应力的等温时间为等温过程中碳化物的“有效析出”结束时间,即碳化物析出结束时间p
f
。值得注意的是,p
f
并不代表碳化物析出完全结束,而是使钢强度达到最大值的析出时间,而这个时间p
f
也正是生产所需要的。
72.图6是不同等温温度相变前,等温屈服强度增量随时间变化的曲线,另外,为方便观察等温相变前等温屈服强度增量随时间的变化,在每条曲线上的箭头处标出了每个等温温度下的相变开始时间。通常未发生相变前的等温过程中,钢的等温屈服强度随时间的增加基本保持不变,如果等温屈服强度增量大于0,则表明碳化物开始析出并产生了强化效应。另外,析出强化效应与碳化物析出体积分数呈正相关关系,而且析出体积分数随时间的延长而增多,因此等温屈服强度增量大于0时可以认为碳化物开始析出,相同时间内等温屈服强度增量越大,碳化物的析出越早。通过图6可以知,等温时间在5
‑
10s内,在等温温度为625℃和600℃时的等温屈服强度增量大于0,而且在625℃等温5
‑
10s的等温屈服强度增量更大。因此,可以认为在这两个温度下等温5
‑
10s内有碳化物析出产生,而且碳化物在625℃等温时析出的时间更早。进而可以获得等温过程中碳化物析出的开始时间p
s
。同样的方法可以判定碳化物在等温温度为650℃、675℃和700℃时的析出时间和顺序。
73.根据获得的碳化物析出开始时间p
s
和有效的析出结束时间p
f
绘制出了ti
‑
mo合金钢在600
‑
700℃等温过程中碳化物的析出
‑
温度
‑
时间(ptt)曲线,如图7所示。可以看到,碳化物的析出开始曲线呈典型的“c”曲线,最快的析出鼻尖温度位于625℃,时间约为5
‑
10s。其后依次为600℃、650℃、675℃和700℃。其中,650℃、675℃和650℃的析出开始时间在10
‑
20s以内。
74.本发明方法的等温屈服强度增量法结合测定出的等温相变时间,可以有效避开合金钢碳化物等温析出过程中相变对碳化物析出开始点测定的干扰,并能揭示碳化物析出过程和相变的相互作用。使用的等温屈服强度的表征不仅能够更直观地反映等温过程中碳化物析出对钢强化效应的量,并且能够系统地体现等温温度、相变、时间和碳化物析出的相互
协调机制,有助于研究和丰富碳化物的析出机理。此外,本方法操作简单且实用性强。
75.本发明的上述实施例仅仅是为清楚地说明本发明所作的举例,而并非是对本发明的实施方式的限定。对于所属领域的普通技术人员来说,在上述说明的基础上还可以做出其它不同形式的变化或变动。这里无需也无法对所有的实施方式予以穷举。凡在本发明的精神和原则之内所作的任何修改、等同替换和改进等,均应包含在本发明权利要求的保护范围之内。