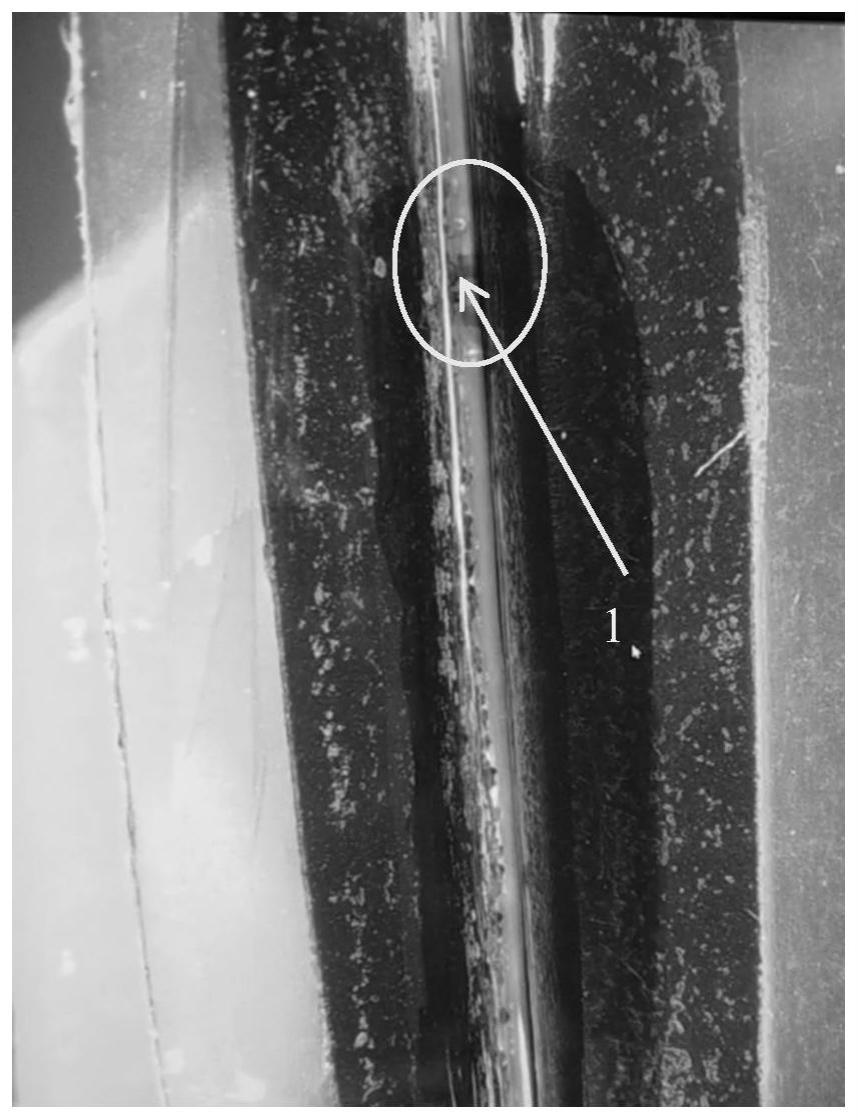
1.本发明涉及锂离子电池领域,尤其是一种锂离子电池绝缘失效的可视化表征方法。
背景技术:2.锂离子电池的内绝缘不良,特别是软包锂离子电池的内绝缘不良会造成电池电量的损失,关系到电池自放电问题,严重时,内绝缘还会造成电池包装失效,随着使用时间的延续,一旦问题显现,不仅使企业面临巨大的售后压力,还会造成电池和电池系统的安全问题。
3.为了在电池出厂前将内绝缘不良的电池筛选出来,业内通常在装配完成后测试负极和铝塑膜铝层之间的实际绝缘阻抗,中国专利公开号cn203519797u,公开了一种软包装锂离子电池腐蚀胀气隐患检测装置,其特征在于,包括控制箱、短路测试仪、和测试气缸,控制箱设置在操作台上,控制箱侧部固定测试气缸,测试气缸的活塞杆端部连接绝缘测试座,绝缘测试座上设有钢质的刺刀和铜质的探针,刺刀和探针与短路测试仪电连接。其不足之处在于,这一方法虽然能够检测出绝缘不良的电芯,但是,采用绝缘阻抗测试的方法并不能得知绝缘失效点的具体位置,而且,锂离子电池通常采用电解液贫液的设计来避免产气等其他问题,这使得此种检测方法往往效用不彻底,难以从根本上解决内绝缘电芯流出的问题。
4.中国专利公开号cn104390957b,公开了一种铝塑膜检测方法,其特征在于,包括下列步骤:取一个待测铝塑膜,向待测铝塑膜的凹腔中注入硫酸铜溶液使硫酸铜溶液注满凹腔;给待测铝塑膜安置正极耳和负极耳,使正负极耳与硫酸铜溶液导通,再将注有硫酸铜溶液的铝塑膜凹腔封装,使正负极耳固定并突出于铝塑膜外;将正负极耳分别连接于一个电源正极和负极,通电预定时间后,打开待测铝塑膜检查是否有红色部分,如出现红色部分则判断待测铝塑膜该部位有缺陷。其不足之处在于,软包的封装工艺是锂离子电池当中最复杂,难度最高的工艺技术,涉及到封装过程中的各种问题,同时,其对制程稳定性也要求极其高,实际生产过程中往往难以连续保证,这一方法通过置换反应能够判断出绝缘失效点位置,但无法判断失效点直接的连接关系,难以对电池封装中的内绝缘失效问题进行完全的认识,不能直接指导工艺过程的调整,且检测过程复杂,技术要求较高。
技术实现要素:5.本发明是为了克服现有技术对绝缘失效通路示踪能力不充分的不足,公开一种简便、快捷、可实时检测、准确定位绝缘失效点,并使绝缘失效通路直观显示的一种锂离子电池绝缘失效的可视化表征方法。
6.为了实现上述发明目的,本发明采用的技术方案如下:一种锂离子电池绝缘失效的可视化表征方法,包括以下步骤:a) 对铝塑膜层采用失效点锁定法锁定pp层上的绝缘失效区域;
b) 对锂离子电池铝塑膜进行化学剥离,得到铝塑膜的pp层;c) 将示踪剂涂覆在pp层绝缘失效区域的一侧,晾干,并用密封层密封;d) 将pp层涂覆有示踪剂的一侧朝下,置于光学显微镜下,对未涂覆示踪剂一侧的失效区域滴加溶剂,观察,确定表面缺陷点、绝缘失效点、绝缘失效通路。
7.采用失效点锁定法锁定绝缘失效区域,减小待测试区域面积,方便针对性检测绝缘失效通道;通过化学剥离pp层,防止物理剥离带来的机械损伤,因为pp层耐酸碱性较强,化学剥离不会增加或改变pp层的绝缘失效点和绝缘失效通路;普通渗透剂渗透性能较强,pp层本身也会在一定程度被侵染造成干扰,不利于对绝缘失效通道进行检测,涂覆渗透能力弱的示踪剂并对pp层一侧进行密封,排除渗透作用和外源色光的干扰;在pp层另一侧滴加溶剂时,溶剂在重力作用和毛细作用下,贯穿绝缘失效通路,溶剂对示踪剂的溶解作用,使绝缘失效通路中充满示踪剂的溶液,在光学显微镜下便可直接观察到绝缘失效点、绝缘失效通路及表面缺陷。
8.进一步的,步骤a中,失效点锁定法为负极短接铝塑膜铝层腐蚀法或电镀液电镀法中的一种。
9.进一步的,步骤b中,化学剥离采用的试剂为盐酸、硝酸、硫酸、氢氧化钠、氢氧化钾溶液中的至少一种。
10.进一步的,步骤c中,示踪剂为天然染料、合成染料、有机油性油墨中的至少一种。
11.进一步的,步骤c中,示踪剂为记号笔油墨。
12.进一步的,步骤c中,密封层为与示踪剂颜色相同的不透明胶带。
13.进一步的,步骤d中,溶剂为甲醇、乙醇、丙酮、乙酸乙酯、dmf、二氯甲烷、环己烷、石油醚中的至少一种。
14.进一步的,步骤d中,示踪剂溶解并贯穿pp层两侧绝缘失效区域的为绝缘失效通路,绝缘失效通路与绝缘失效区域的相交点即为绝缘失效点,其余绝缘失效区域内的染色点为表面缺陷点。
15.由于采用以上的技术方案,本发明具有这样的有益效果:通过溶剂对示踪剂的溶解作用,使示踪剂的溶液贯穿于绝缘失效通路中,使绝缘失效通路可视化,充分了解绝缘失效模式;绝缘失效通路与绝缘失效区域的相交点即为绝缘失效点,即可将绝缘失效点与表面缺陷区分开来。本发明的电池绝缘失效的可视化表征方法,对绝缘失效点、绝缘失效通路、表面缺陷的示踪快捷简便,可实时检测,为锂离子电池的绝缘失效模式分析和工序调整改进提供了重要的参考依据。
附图说明
16.图1为使用负极短接铝塑膜铝层腐蚀法锁定绝缘失效区域1的结果图。
17.图2为在光学显微镜下对图1确定的失效区域的观测图。
18.图3为本发明在光学显微镜下对pp层进行绝缘失效检测时滴加溶剂前后的对比图。
19.图4为光学显微镜下对图3检测到的绝缘失效通道的观测图。
20.其中,1、绝缘失效区域;2、表面缺陷点;3、粘合界面;4、界面缺陷点;41、第一界面缺陷点;42、第二界面缺陷点;43、第三界面缺陷点;5、局部缺陷;6、绝缘失效通路;71、第一
绝缘失效点;72、第二绝缘失效点。
具体实施方式
21.下面结合附图与具体实施方式对本发明做进一步的描述。
22.a)使用负极短接铝塑膜铝层腐蚀法对铝塑膜进行处理,如图1所示,确定pp层上的绝缘失效区域1;b)用2m的氢氧化钠处理绝缘失效的铝塑膜,将铝箔层溶解,使pp层剥离出来;在光学显微镜下对绝缘失效区域1进行观测,如图2所示,可清晰观察到pp层的一侧在热封过程中形成的大量的表面缺陷点2,在粘合界面3上可以清晰的观察到若干界面缺陷点4,在粘合界面3的另一侧也可以观测到若干局部缺陷5存在,绝缘失效通道为表面缺陷点与界面缺陷点、局部缺陷互相连接贯通形成;c)在pp层一侧涂覆完全覆盖绝缘失效区域1的黑色记号笔油墨,自然晾干,粘贴黑色胶带,完全覆盖绝缘失效区域1;d)如图3a所示,将pp层涂覆有黑色记号笔油墨的一侧朝下,置于在光学显微镜下,对未涂覆示踪剂一侧的失效区域滴加一滴乙醇,观察绝缘失效区域1,如图3b所示,可见,在重力作用和毛细作用下,溶剂在绝缘失效通道6内快速扩散,溶解位于下侧的黑色记号笔油墨,使绝缘失效通道6变得清晰可见;如图4所示,对黑色记号笔油墨示踪的绝缘失效通道6进行进一步放大观察,可见,在pp层粘合界面上有相邻的第一界面缺陷点41、第二界面缺陷点42、第三界面缺陷点43被染色,而在可观察的所有局部缺陷中只有局部缺陷5被染色,说明局部缺陷5参与了绝缘失效通道6的形成,由此可确定与局部缺陷5相连的第二绝缘失效点72;另外,可见,第一绝缘失效点71、第一界面缺陷点41、局部缺陷5、第二绝缘失效点72互相连接形成了贯穿的绝缘失效通路6;由于溶剂无法进入独立的内部缺陷,也无法通过表面缺陷点进入独立的局部缺陷区域,而粘合界面3上的第二界面缺陷点42、第三界面缺陷点43也被黑色记号笔油墨染色,表明第二界面缺陷点42、第三界面缺陷点43并非独立的内部缺陷,也不是由表面缺陷点2向粘合界面3延伸得到的独立的局部缺陷,而是与界面缺陷点41相连通的,形成了一块较大的缺陷区域,从而参与了绝缘失效通道6的形成,导致了溶剂进入染色。黑色记号笔油墨对第一绝缘失效点71、第一界面缺陷点41、第二界面缺陷点42、第三界面缺陷点43、局部缺陷5、第二绝缘失效点72的染色处理,使绝缘失效通道6可视化程度提高,使失效模式清晰完整的展现出来,为相关专业人员对工艺过程的调整优化提供了指导方向。