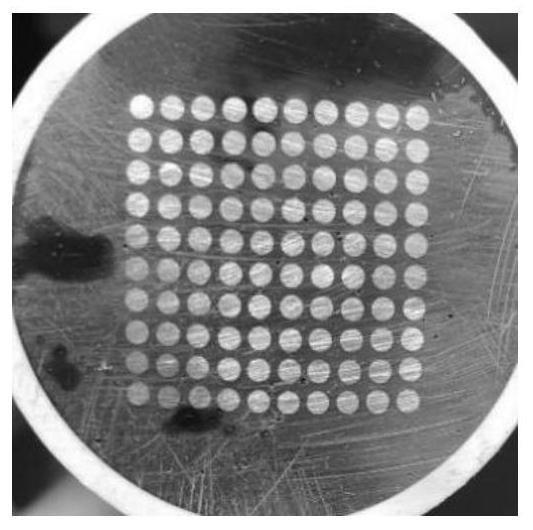
1.本发明属于电化学技术领域,涉及金属材料表面处理以及通过电化学方法对涂层局部腐蚀行为的检测和表征技术范畴,具体涉及一种采用阵列电极和电化学噪声表征有机涂层局部腐蚀行为的方法。
背景技术:2.阵列电极技术的迅速发展,除了得益于丝束电极本身能较准确获得电极表面电化学参数分布信息外,也依赖于与之相匹配的测控系统的不断发展和完善。在丝束电极技术发展的初期,测控系统非常简易,即将电极放置在腐蚀介质中,数字电压表一端通过手动开关与电极丝连接,另一端经辅助电极接入溶液组成电流回路,通过手动开关的选择性闭合测得不同电极丝的电化学信息。此种测试方法操作繁琐,无法实现自动化,而且测试时间较长、测试精度低、数据间的同步性不高。后来,林昌健等建立了由微机控制的丝束电极测控系统,实现了丝束电极测试的自动化,加速了丝束电极技术的应用进程。钟庆东等
7.通过在测量回路中引入阻抗变换和电流放大器,在很大程度上改善了测量的精度。不过,以上测控系统仅局限于腐蚀电位的测试,而halit等建立的丝束电极腐蚀监测系统则通过多重取样自动开关,实现了腐蚀电位和电流的同时测量,极大的促进了丝束电极技术的应用。然而,由于以上测控系统的开关需要专门进行定制,难以实现推广应用。因此,wang等利用基于pxi总线技术的模块化仪器搭建了一套丝束电极测控系统,不仅简化了操作、增加了测量精度和可靠性,而且高速自动切换开关模块的采用还大幅度地缩短了测量时间、提高了测试效率,同时还具有很强的通用性,便于推广使用。不过,由于腐蚀电位与电流需分开测试,数据的同步性需要进一步提高。近来,李焰等又对该测控系统进行了改进和完善,通过增加一个高分辨率数字万用表模块,并利用自动开关模块的高速切换来实现腐蚀电位和电流的交替测量,使测试数据的同步性得到了明显改善,由于在切换电位和电流测量时不必再变更接线端的连接方式,测量过程的自动化程度也进一步提高,便于对局部腐蚀过程进行连续监测。
3.丝束电极测控系统的发展使丝束电极技术在提取电极表面电化学分布信息上更为精确,测试过程更为自动快捷,而模块化测试仪器的出现使系统更为灵活和方便,为丝束电极技术的进一步发展奠定了良好的基础。
4.电化学噪声(electrochemicalnoise,简称en)是指电化学动力系统演化过程中,其电学状态参量(如:电极电位、外测电流密度等)的随机非平衡波动现象。电化学噪声技术有很多优点。首先,作为一种原位无损的监测技术,在测量过程中无须对被测电极施加可能改变腐蚀电极腐蚀过程的外界扰动;其次,它无须预先建立技测体系的电极过程模型;第三,它无须满足阻纳的三个基本条件;最后,检测设备简单,且可以实现远距离监测。
5.电化学噪声是通过高分辨率精密电化学仪器记录下来,所得到的电化学信号通过快速傅立叶转换,将信号从时域转换到频域,通过测试电位和电流的噪声标准差进而得到
可以衡量材料耐蚀性优劣的噪声电阻,进而确定材料的腐蚀速率,并且获取有关材料或者涂层的表面电化学腐蚀过程的相关宝贵信息。
技术实现要素:6.本发明基于一种新型电化学检测手段,具体是提供一种采用阵列电极和电化学噪声表征有机涂层局部腐蚀行为的方法,旨在能够有效评价涂层的不均匀腐蚀特性,此种方法具有等效,快速,高效的优点,通过电化学噪声和阵列电极的联合使用,二者结果能够很好的互相印证(腐蚀电流小的,噪声电阻大),为涂层表面的腐蚀行为提供精准的局部电化学分布信息,准确地评价涂层表面各个部分之间的耐蚀性差异,相比于传统电化学方法能够更加灵敏的分析涂层表面微区的电化学性能的差异。(阵列电极是模拟单个大电极的电极,能够检测金属或者涂层的局部腐蚀行为,能够很好的表征出材料表面不同位置的腐蚀差异,而传统电极得到的是统一均匀的电化学信息,无法分辨不同位置上的腐蚀差异性)。
7.本发明的技术方案为:
8.一种采用阵列电极和电化学噪声表征有机涂层局部腐蚀行为的方法,包括如下步骤:
9.(1)试样的制备:选取碳钢丝,制备成符合正方形阵列化排布的数根电极,绝缘处理后,将电极排列成密集方阵,固化后的电极方阵非工作面分别焊接绝缘铜导线后引出,其工作端面用砂纸打磨干净;
10.(2)钝化液的配制及钝化:所述钝化液的配制采用硅烷偶联剂为主体成分,分子式为xsi(or)3,乙醇和水混合液作为溶剂;所述钝化为将步骤(1)中的试样放入钝化液中,控制钝化温度和时间,再将样品置于烘箱中,控制固化温度和时间,即得到硅烷无机盐复合膜,将配置好的钝化液与不同浓度的纳米zro颗粒混合,涂抹在具有硅烷无机盐复合膜的碳钢阵列电极表面,再置于烘箱中,在温度40~70℃烘干,直至无机膜层紧密地附着于阵列电极表面;
11.(3)电化学测试:将wbe装配好,然后向电解池加入腐蚀液,以饱和甘汞电极sce为参比电极,进行表面电位/电流扫描;扫描采用丝束电极测试仪进行,该仪器内置上述阵列电极,由微机控制循环测量各金属丝的开路电位以及偶接电流。
12.进一步,步骤(3)中电化学噪声测试在溶液中进行,通过与阵列电极进行连接联动,采用三电极系统:以并联连的微电极为工作电极,饱和甘汞电极sce为参比电极,铂电极为对电极;参比电极和对电极都处于溶液中,与微电极形成电连续系统。
13.进一步,步骤(3)中实验过程中的采样频率为1~3hz,采样时间为400~800s。
14.进一步,步骤(3)中电化学噪声数据采取时域分析法中的数学统计分析方法进行分析,其主要参数为噪声电位的标准方差σu;噪声电流的标准方差σi和噪声电阻rn,着重对噪声电阻数据进行统计评价。
15.进一步,步骤(3)中腐蚀液为nacl溶液,na2so4溶液,hcl或h2so4。
16.进一步,步骤(2)中所用硅烷偶联剂为γ-氨丙基三乙氧基硅烷kh550和γ-甲基丙烯酰氧基丙基三甲氧基硅烷kh570。
17.进一步,步骤(2)中控制钝化温度和时间为控制钝化温度为20~60℃,钝化时间为2~5min。
18.进一步,步骤(2)中控制固化温度为80~120℃,固化时间为30~45min。
19.进一步,步骤(2)中不同浓度的纳米zro颗粒为0g/l、0.05g/l、0.10g/l和0.20g/l。
20.根据本发明所述一种采用阵列电极和电化学噪声表征有机涂层局部腐蚀行为的方法,步骤(1)中试样制备的具体步骤为:选取碳钢丝,制备成符合正方形阵列化排布的数根电极,分别用600#、800#、1000#、2000#砂纸依次打磨,再用丙酮和乙醇清洗,丙酮超声:试样经目视检查,符合要求后用清水冲洗后,冷风吹干,然后马上放入丙酮中进行超声清洗后用绝缘漆浸渍碳钢丝,将电极排列成密集方阵,固化后的电极方阵非工作面分别焊接绝缘铜导线后引出;其工作端面依次用200#、600#、800#、金相砂纸逐级打磨干净,无水乙醇和蒸馏水清洗后放入干燥器待用。
21.本发明提供的一种采用阵列电极和电化学噪声表征有机涂层局部腐蚀行为的技术,更具体具有如下的过程和步骤:
22.1.取直径0.6~2.5mm的碳钢丝,制备成符合正方形阵列化排布数根电极(例如100根),分别用600#、800#、1000#、2000#砂纸依次打磨,再用丙酮和乙醇清洗,丙酮超声(频率是40khz~90khz,时间是10~15min):试样经目视检查,符合要求后(表面干净,无杂质)用清水冲洗后,冷风吹干,然后马上放入丙酮中进行超声清洗,超声清洗时间不超过30s。后用绝缘漆(类似于环氧树脂类的,具有一定粘度的物质)浸渍碳钢丝,浸渍5~10min,以确保绝缘良好并防止缝隙腐蚀,将电极排列成密集方阵(例如10
×
10方阵),固化后的10
×
10电极方阵非工作面分别焊接绝缘铜导线后引出。阵列电极的总工作面积为0.785cm2。其工作端面依次用200#、600#、800#、金相砂纸逐级打磨干净(肉眼观察表面无脏东西即可),无水乙醇和蒸馏水清洗后放入干燥器待用。
23.2.钝化液配置:本发明采用硅烷偶联剂为主体成分,分子式为xsi(or)3,采用乙醇和水混合液作为溶剂,所用硅烷为γ-氨丙基三乙氧基硅烷(kh550)和γ-甲基丙烯酰氧基丙基三甲氧基硅烷(kh570)。钝化液的配置过程如下:
24.(1)取一洁净烧杯,向杯中加入80ml无水乙醇,再加入250ml去离子水,放在搅拌器上进行搅拌25min;用天平称取10.0gkh550,逐滴加入(1)中混合液中,控制滴速,避免在溶液中出现白色不溶物,搅拌1.5h后,将溶液密封并静置24~48h;
25.(2)用乙酸调整kh550水解液的ph至3.0~7.0,再加入10.0gkh570,搅拌1h,密封后静置24~48h;用去离子水溶解一定量(300~500ml)的偏钒酸铵钠、氟钛酸铵、氟锆酸钾,逐滴加入硅烷水解液中,定容至200ml。本文采用浸泡的方法,将测试样品放入钝化液中,控制钝化温度20~60℃,2~5min后取出,将样品置于烘箱中,控制合适的固化温度(80~120℃),30~45min后取出,即得到硅烷无机盐复合膜。
26.(3)将配置好的钝化液与不同浓度(0g/l、0.05g/l、0.10g/l、0.20g/l)的纳米zro颗粒混合,平整均匀地涂抹在碳钢阵列电极表面,置于烘箱中,在温度40~70℃的范围内持续烘干30~45min,直至无机膜层紧密地附着于阵列电极表面,待用。
27.3.电化学测试:将wbe(阵列电极,又名丝束电极)装配好,然后向电解池加入约300~500ml的腐蚀液(腐蚀液可以是3.5wt.%nacl溶液,浓度可进行调整,同时也可选择na2so4,hcl或h2so4等),以饱和甘汞电极(sce)为参比电极,进行表面电位/电流扫描。扫描采用丝束电极测试仪进行,该仪器内置10
×
10阵列电路,由微机控制循环测量各金属丝的开路电位以及偶接电流,电极扫描间隔设定为1s,每15min进行一次表面电位与电流的全扫
描。
28.电化学噪声测试在溶液中进行,通过与阵列电极进行连接联动,采用三电极系统:以并联连的100根微电极为工作电极,饱和甘汞电极(sce)为参比电极,铂电极为对电极。参比电极和对电极都处于溶液中,与100根微电极形成电连续系统。本实验过程中的采样频率为1~3hz,采样时间为400~800s。电化学噪声数据采取时域分析法中的数学统计分析方法进行分析,其主要参数为噪声电位的标准方差σu;噪声电流的标准方差σi和噪声电阻rn,本发明着重对噪声电阻数据进行统计评价。
29.有益技术效果
30.本发明引入阵列微电极技术,电化学噪声技术以及扫描电子显微镜(sem)等多种测试表征方法展开对有机膜层的表面状态和电化学性能进行研究,准确的揭示和评价膜层微区腐蚀规律及其相关特征。
附图说明
31.图1为阵列电极的实物图。
具体实施方式
32.为了更好地理解本发明,下面实施例进一步阐明本发明的内容,但发明的内容不仅仅局限于下面的实施例。
33.实施例1
34.一种采用阵列电极和电化学噪声表征有机涂层局部腐蚀行为的技术,具有如下的过程和步骤:
35.1.取直径1mm的碳钢丝,制备成100根电极,分别用600#、800#、1000#、2000#砂纸依次打磨,再用丙酮和乙醇清洗,丙酮超声:试样经目视检查,符合要求后用清水冲洗后,冷风吹干,然后马上放入丙酮中进行超声清洗,超声清洗时间不超过30s。后用绝缘漆浸渍碳钢丝,以确保绝缘良好并防止缝隙腐蚀,将电极排列成密集10
×
10方阵,固化后的10
×
10电极方阵非工作面分别焊接绝缘铜导线后引出。阵列电极的总工作面积为0.785cm2。其工作端面依次用200#、600#、800#、金相砂纸逐级打磨干净,无水乙醇和蒸馏水清洗后放入干燥器待用。
36.2.钝化液配置:本发明采用硅烷偶联剂为主体成分,分子式为xsi(or)3,采用乙醇和水混合液作为溶剂,所用硅烷为γ-氨丙基三乙氧基硅烷(kh550)和γ-甲基丙烯酰氧基丙基三甲氧基硅烷(kh570)。钝化液的配置过程如下:
37.(1)取一洁净烧杯,向杯中加入80ml无水乙醇,再加入250ml去离子水,放在搅拌器上进行搅拌25min;用天平称取10.0gkh550,逐滴加入(1)中混合液中,控制滴速,避免在溶液中出现白色不溶物,搅拌1.5h后,将溶液密封并静置24~48h;
38.(2)用乙酸调整kh550水解液的ph至3.0~7.0,再加入10.0gkh570,搅拌1h,密封后静置24~48h;用去离子水溶解一定量的偏钒酸铵钠、氟钛酸铵、氟锆酸钾,逐滴加入硅烷水解液中,定容至200ml。本文采用浸泡的方法,将测试样品放入钝化液中,控制钝化温度20~60℃,2min后取出,将样品置于烘箱中,控制合适的固化温度(80~120℃),30min后取出,即得到硅烷无机盐复合膜。
39.(3)将配置好的钝化液,不掺杂纳米zro颗粒,平整均匀地涂抹在碳钢阵列电极表面,置于烘箱中,在温度40~70℃的范围内持续烘干30min,直至无机膜层紧密地附着于阵列电极表面,待用。
40.3.电化学测试:将wbe装配好,然后向电解池加入约300ml的腐蚀液,以饱和甘汞电极(sce)为参比电极,进行表面电位/电流扫描。扫描采用丝束电极测试仪进行,该仪器内置10
×
10阵列电路,由微机控制循环测量各金属丝的开路电位以及偶接电流,电极扫描间隔设定为1s,每15min进行一次表面电位与电流的全扫描。
41.电化学噪声测试在溶液中进行,通过与阵列电极进行连接联动,采用三电极系统:以并联连的100根微电极为工作电极,饱和甘汞电极(sce)为参比电极,铂电极为对电极。参比电极和对电极都处于溶液中,与100根微电极形成电连续系统。本实验过程中的采样频率为1~3hz,采样时间为400~800s。电化学噪声数据采取时域分析法中的数学统计分析方法进行分析,其主要参数为噪声电位的标准方差σu;噪声电流的标准方差σi和噪声电阻rn,本发明着重对噪声电阻数据进行统计评价。
42.本发明通过电化学技术对硅烷膜层进行耐蚀性能的表征测试,表面涂覆掺杂0g/l纳米zro颗粒硅烷膜的碳钢阵列电极作为待测电极,以3.5wt.%nacl溶液作为腐蚀液,实验条件为静止,实验温度为25℃。首先通过阵列电极对硅烷膜进行逐点的电位-电流扫描,扫描间隔频率1s;接着通过联动测试手段,对阵列电极表面进行逐点的电化学噪声测试。采样频率为1~3hz,采样时间为400~800s。电化学噪声数据采取时域分析法中的数学统计分析方法进行分析,统计主要参数为噪声电位的标准方差σu;噪声电流的标准方差σi,通过上述两个参数计算得出噪声电阻rn。
43.实施例2
44.试样的制备和钝化液的配制及钝化同实施例1。
45.本实施例通过电化学技术对硅烷膜层进行耐蚀性能的表征测试,表面涂覆掺杂0.05g/l纳米zro颗粒硅烷膜的碳钢阵列电极作为待测电极,以3.5wt.%nacl溶液作为腐蚀液,实验条件为静止,实验温度为25℃。首先通过阵列电极对硅烷膜进行逐点的电位-电流扫描,扫描间隔频率1s;接着通过联动测试手段,对阵列电极表面进行逐点的电化学噪声测试。采样频率为1~3hz,采样时间为400~800s。电化学噪声数据采取时域分析法中的数学统计分析方法进行分析,统计主要参数为噪声电位的标准方差σu;噪声电流的标准方差σi,通过上述两个参数计算得出噪声电阻rn。
46.实施例3
47.试样的制备和钝化液的配制及钝化同实施例1。
48.本实施例通过电化学技术对硅烷膜层进行耐蚀性能的表征测试,表面涂覆掺杂0.10g/l纳米zro颗粒硅烷膜的碳钢阵列电极作为待测电极,以3.5wt.%nacl溶液作为腐蚀液,实验条件为静止,实验温度为25℃。首先通过阵列电极对硅烷膜进行逐点的电位-电流扫描,扫描间隔频率1s;接着通过联动测试手段,对阵列电极表面进行逐点的电化学噪声测试。采样频率为1~3hz,采样时间为400~800s。电化学噪声数据采取时域分析法中的数学统计分析方法进行分析,统计主要参数为噪声电位的标准方差σu;噪声电流的标准方差σi,通过上述两个参数计算得出噪声电阻rn。
49.实施例4
50.试样的制备和钝化液的配制及钝化同实施例1。
51.本实施例通过电化学技术对硅烷膜层进行耐蚀性能的表征测试,表面涂覆掺杂0.20g/l纳米zro颗粒硅烷膜的碳钢阵列电极作为待测电极,以3.5wt.%nacl溶液作为腐蚀液,实验条件为静止,实验温度为25℃。首先通过阵列电极对硅烷膜进行逐点的电位-电流扫描,扫描间隔频率1s;接着通过联动测试手段,对阵列电极表面进行逐点的电化学噪声测试。采样频率为1~3hz,采样时间为400~800s。电化学噪声数据采取时域分析法中的数学统计分析方法进行分析,统计主要参数为噪声电位的标准方差σu;噪声电流的标准方差σi,通过上述两个参数计算得出噪声电阻rn。
52.实施例5
53.试样的制备和钝化液的配制及钝化同实施例1。
54.本实施例通过电化学技术对硅烷膜层进行耐蚀性能的表征测试,表面涂覆掺杂0.30g/l纳米zro颗粒硅烷膜的碳钢阵列电极作为待测电极,以3.5wt.%nacl溶液作为腐蚀液,实验条件为静止,实验温度为25℃。首先通过阵列电极对硅烷膜进行逐点的电位-电流扫描,扫描间隔频率1s;接着通过联动测试手段,对阵列电极表面进行逐点的电化学噪声测试。采样频率为1~3hz,采样时间为400~800s。电化学噪声数据采取时域分析法中的数学统计分析方法进行分析,统计主要参数为噪声电位的标准方差σu;噪声电流的标准方差σi,通过上述两个参数计算得出噪声电阻rn。
55.表1各实施例经处理后各样品性能
[0056][0057][0058]
由上表数据说明此项检测技术能够很好的区分不同试样的腐蚀差异性,并且阵列电极结果与电化学噪声结果一一对应,侧面说明该项技术的准确性和科学性,电流密度,腐蚀电位,被腐蚀电极数目由阵列电极得出;噪声电阻由电化学噪声得出,微观形貌由sem(扫
描电子显微镜)拍摄而得。
[0059]
当然,本技术领域内的一般技术人员应当认识到,上述实施例仅是用来说明本发明,而非用作对本发明的限定,只要在本发明的实质精神范围内,对上述实施例的变换、变形都将落在本发明权利要求的范围内。