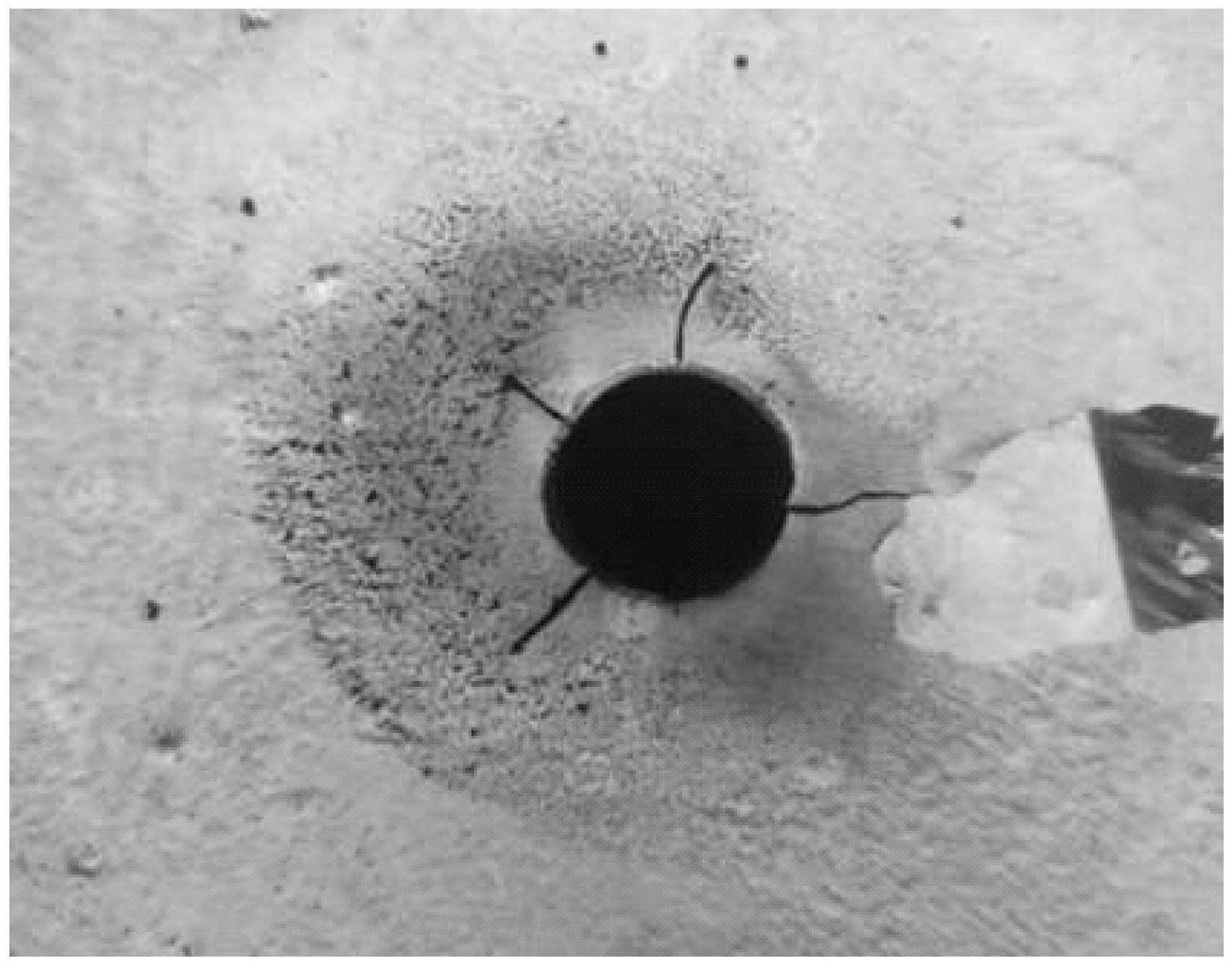
1.本发明属于火电机组汽水管道无损检测技术领域,特别是一种汽水管道管座开孔外壁放射状裂纹爬波检测方法。
背景技术:2.火力发电厂的主要汽水管道如主蒸汽、再热热段蒸汽、再热冷段蒸汽以及抽汽等管道上连接着许多机炉外小管,如放空气管、压力取样管、蒸汽取样管、疏水管等。机组运行过程中,因机炉外管管路设计、阀门泄漏等原因,会出现饱和水回流至主管道的情况,随着机组运行时间的增长,饱和水回流次数增加,在开孔周围逐渐萌生裂纹并逐步延伸增大,最终在管孔处发生泄漏。对于管道开孔处沿内壁开裂的放射状裂纹,一般采用超声横波检测即可发现缺陷,但对于管道开孔处沿外壁开裂的的放射状裂纹(如图1所示),现有的无损检测方法难以检出此类缺陷,一旦裂纹扩展管道发生泄漏会造成机组非计划停运,甚至可能发生高温蒸汽泄漏伤人事故。在役火电机组大管径汽水管道开孔表面放射状裂纹的无损检测成为了本领域技术人员亟需解决的问题。
技术实现要素:3.针对上述情况,为克服现有技术之缺陷,本发明之目的就是提供一种汽水管道管座开孔外壁放射状裂纹爬波检测方法,可有效解决在在役火电机组大管径汽水管道开孔表面放射状裂纹的无损检测,以防止开孔裂纹扩展导致管道泄漏事故的发生。
4.本发明解决的技术方案是:
5.一种汽水管道管座开孔外壁放射状裂纹爬波检测方法,包括以下步骤:
6.步骤一,确定扫查路径
7.以管座角焊缝周围母管道外壁为检测面,建立被检汽水管道管座开孔俯视图的二维图形,在二维图形上沿开孔圆周方向作n个平均分布的放射状模拟裂纹缺陷q
n
,其中n=1,2,3,4
…
,每个模拟裂纹缺陷q
n
的尺寸为长5mm、宽0.2mm、深3mm,以每个模拟裂纹缺陷q
n
沿长度方向的中心点作垂直线l
n
,每个探头放置位置z
n
位于对应的每条垂直线l
n
上,每个探头放置位置z
n
具体满足以下条件:位于探头放置位置z
n
上的探头前沿正对对应模拟裂纹缺陷,探头与管座角焊缝的最小距离s满足1mm≤s≤5mm;
8.将所有探头放置位置z
n
(z1、z2…
z
n
)依次连成一段圆滑过渡的曲线,即为汽水管道外壁管座开孔放射状裂纹的扫查路径,扫查路径为以管座开孔为圆心的同心圆,管座开孔的半径为r,则探头移动过程中,探头前沿垂直中心线始终保持与以管座开孔圆心为中心、半径为r+2.5mm的圆相切;
9.步骤二,仪器设备选择及参数设置
10.扫查仪器采用a型脉冲反射式超声检测仪,探头选择长焦距爬波双晶并列式探头;
11.对a型脉冲反射式超声检测仪及探头进行性能测试,设置基础参数,并配合标准试块bzsk
‑
1,制作dac曲线,所述标准试块bzsk
‑
1上设置模拟裂纹,制作dac曲线的具体步骤:
将探头置于标准试块bzsk
‑
1上,探头前沿距离模拟裂纹10mm,测出最强反射波,a型脉冲反射式超声检测仪调到80%屏高,然后依次测出探头前沿距离模拟裂纹分别为20mm、30mm、40mm、50mm处模拟裂纹波高,然后在示波屏上绘制出一条距离
‑
波幅曲线,该距离
‑
波幅曲线即为dac曲线,dac曲线用于评断缺陷的当量大小;
12.步骤三,扫查
13.探头置于被检汽水管道管座角焊缝附近,探头前端与管座角焊缝的最小距离满足1mm≤s≤5mm,保持探头与被检工件稳定接触,沿扫查路径进行360
°
环向扫查,保证探头前沿垂直中心线与以管座开孔为中心、半径为r+2.5mm的圆始终相切,扫查速度不应超过150mm/s;
14.步骤四,缺陷识别
15.按步骤四进行扫查,对缺陷进行定量和位置的测定,得到最大反射波幅值及指示长度,所有超过步骤二得到的距离
‑
波幅曲线高度的反射波均判定为缺陷波;
16.缺陷波幅的测定:缺陷最大反射波幅与距离
‑
波幅曲线高度的差值
△
即为缺陷波幅,记为sl
±△
db;
17.缺陷的位置测定:根据探头在探测面上的位置和最高反射波在示波屏上的水平位置来确定缺陷在管孔周围的位置,并做好记录;
18.缺陷长度的测定:采用单侧半波高度法(6db法)测定其指示长度,具体方法如下:移动探头,找到缺陷最强反射波,将波高调到80%屏高,向外侧移动探头,当波高降到40%屏高时,在探头中心线所对应的位置上作好标记,标记到开孔边缘的距离即为缺陷的指示长度。
19.超声爬波的产生是利用超声波传播到两种异质界面处发生的波形转换,如图2所示,如果入射波速和折射波速满足下列关系c
l1
<c
s2
<c
l2
时(其中,c
l1
为入射声波在第一介质中的纵波声速,c
l2
为入射声波在第二介质中的纵波声速,c
s2
为入射声波在第二介质中的横波声速),当入射角α=arc sin(c
l1
/c
l2
)时,纵波的折射角等于90
°
时,就会在第二种介质中激发爬波,爬波理论上是平行于表面传播的纵波。爬波检测具有以下特点:1)爬波适用于表面粗糙的工件近表面或薄件中的缺陷的检验,用于管座开孔外壁检测可以不需要考虑管座角焊缝及管座本身的影响;2)爬波探头可以通过选择适当的f
·
d值(f为探头频率,d为晶片直径)改变对表面附近缺陷的敏感程度;3)爬波只对表面层几个毫米深度的区域敏感,一般范围为1mm~9mm;4)爬波衰减比较严重,声程较短,一般有效声程不超过50mm。
20.超声爬波检测技术由于采用大入射角楔块,声波进入工件后可产生纵向表面爬波、体积内纵波和两种类型的横波。由于一次爬波的角度在75
°
~83
°
之间,几乎垂直于被检工件的厚度方向,与工件中垂直方向的裂纹接近成90
°
,因此对于垂直性裂纹有较好的检测灵敏度。同时,爬波检测受工件表面刻痕、不平整、凹陷等的干扰较小,所以爬波检测技术被广泛运用于近表面的裂纹检测。因此,采用超声爬波检测技术检测汽水管道管座开孔外壁放射状裂纹具有很高的可行性。
21.本发明通过汽水管道管座开孔外壁放射状裂纹的特点,确定了扫查路径,通过在带有模拟裂纹的标准试块上进行监测,绘制出距离
‑
波幅曲线,用于评断缺陷的当量大小,最后通过在被检汽水管道管上沿扫查路径进行360
°
环向扫查,最后基于距离
‑
波幅曲线进行缺陷识别,得到缺陷的波幅、位置和长度,从而解决在在役火电机组大管径汽水管道开孔
表面放射状裂纹的无损检测的问题,防止开孔裂纹扩展导致管道泄漏事故的发生,经实际应用,准确率达到99.9%以上,实现汽水管道管座开孔外壁放射状裂纹的有效检测,有良好的社会和经济效益。
附图说明
22.图1为汽水管道管座开孔外壁放射状裂纹示意图。
23.图2为汽水管道管座开孔剖视图。
24.图3为被检汽水管道管座开孔俯视图的二维图形。
25.图4为本发明探头楔块的立体图。
26.图5为本发明探头楔块的主视图。
27.图6为本发明探头楔块的侧视图。
28.图7为本发明标准试块bzsk
‑
1的主视图。
29.图8为本发明标准试块bzsk
‑
1a区域的侧视图。
30.图9为本发明标准试块bzsk
‑
1b区域的侧视图。
31.图10
‑
13为本发明管道管座开孔放射状裂纹对比试块dbsk1~dbsk4的俯视示意图。
32.图14超声爬波检测技术不同界面上的波形转换原理图。
具体实施方式
33.以下结合附图对本发明的具体实施方式作进一步详细说明。
34.由图1
‑
14给出,本发明一种汽水管道管座开孔外壁放射状裂纹爬波检测方法以汽水管道管座开孔外壁放射状裂纹为检测对象,如图2所示,管座通过管座角焊缝固定在母管开孔外侧,母管道半径为r,管座角焊缝边缘到母管开孔中心距离为d,本发明方法适用于母管道半径r≥150mm,管座角焊缝边缘到母管开孔中心距离d≤50mm的汽水管道开孔外壁放射状裂纹的无损检测,包括以下步骤:
35.步骤一,确定扫查路径
36.以管座角焊缝周围母管道外壁为检测面,建立被检汽水管道管座开孔俯视图的二维图形,如图3所示,在二维图形上沿开孔圆周方向作n个平均分布的放射状模拟裂纹缺陷q
n
,其中n=1,2,3,4
…
,每个模拟裂纹缺陷q
n
的尺寸为长5mm、宽0.2mm、深3mm,以每个模拟裂纹缺陷q
n
沿长度方向的中心点作垂直线l
n
,每个探头放置位置z
n
位于对应的每条垂直线l
n
上,每个探头放置位置z
n
具体满足以下条件:位于探头放置位置z
n
上的探头前沿正对对应模拟裂纹缺陷,探头与管座角焊缝的最小距离s满足1mm≤s≤5mm;
37.将所有探头放置位置z
n
(z1、z2…
z
n
)依次连成一段圆滑过渡的曲线,即为汽水管道外壁管座开孔放射状裂纹的扫查路径,扫查路径为以管座开孔为圆心的同心圆,管座开孔的半径为r,则探头移动过程中,探头前沿垂直中心线始终保持与以管座开孔圆心为中心、半径为r+2.5mm的圆相切;
38.步骤二,仪器设备选择及参数设置
39.扫查仪器采用a型脉冲反射式超声检测仪,探头选择长焦距爬波双晶并列式探头;
40.所述长焦距爬波双晶并列式探头的参数要求为:管座角焊缝边缘至管孔中心点的
具体即扫查声程一般大于20mm,因此,选择焦点水平距离为20mm的长焦距爬波探头;探头频率择5mhz,单个晶片面积为6mm
×
8mm,满足表面层附近裂纹缺陷的敏感程度。
41.如图4所示,探头楔块的长度l=20mm,宽度d=8mm,由于被检汽水管道检测面为曲面,扫查路径过程中被检工件与探头检测面接触的部位为不断变化的曲面,为保证探头检测面与被检工件的耦合效果,如图5所示,在探头楔块沿长度(l=20mm)方向预设一定的弧度(曲面半径为r=500mm的凹面);探头楔块宽度方向后侧1.5mm宽度的部位没有超声波声束经过,如图6所示,在该部位沿长度(l=20mm)方向预设一定的弧度(曲面半径为r=50mm的凹面,如图),进一步增强耦合效果。
42.所述a型脉冲反射式超声检测仪的性能要求为:对a型脉冲反射式超声检测仪的垂直线性、水平线性进行测试,要求a型脉冲反射式超声检测仪垂直线性误差不超过4%,水平线性误差不超过1%;
43.爬波双晶并列式探头的性能要求为:对爬波双晶并联式探头进行测试,声束轴线水平偏离角不应大于2
°
,最大检测距离50mm处信噪比大于6db,主声束垂直方向偏离无明显的双峰。
44.a型脉冲反射式超声检测仪及探头的基础参数设置为:收发模式选择双晶模式,探头角度选择82
°
~85
°
,校准声速设置为5900mm/s,前沿设置为8mm。
45.对a型脉冲反射式超声检测仪及探头进行性能测试,设置基础参数,并配合标准试块bzsk
‑
1,制作dac曲线,所述标准试块bzsk
‑
1上设置模拟裂纹,制作dac曲线的具体步骤:将探头置于标准试块bzsk
‑
1上,探头前沿距离模拟裂纹10mm,测出最强反射波,a型脉冲反射式超声检测仪调到80%屏高,然后依次测出探头前沿距离模拟裂纹分别为20mm、30mm、40mm、50mm处模拟裂纹波高,然后在示波屏上绘制出一条距离
‑
波幅曲线,该距离
‑
波幅曲线即为dac曲线,dac曲线用于评断缺陷的当量大小;
46.如图7
‑
9所示,所述标准试块bzsk
‑
1长200mm、宽50mm、高50mm,沿中心线分为a、b两个区域,a、b两个区域的四周侧面均呈曲面,a、b两个区域的曲面上沿周向分别设置有深3mm、宽0.2mm的通槽构成的模拟裂纹,a区域4个曲面的曲率半径r分别为r
a1
=150mm、r
a2
=200mm、r
a3
=250mm、r
a4
=300mm,b区域4个面的曲率半径分别为r
b1
=350mm、r
b2
=400mm、r
b3
=450mm、r
b4
=500mm。
47.制作距离
‑
波幅曲线时,探头放置在标准试块bzsk
‑
1上的面选择与被检母管道曲率相近的曲面,具体原则如下:
48.当母管道曲率半径150mm≤r
母
<175mm,选择曲率半径r
a1
=150mm的曲面;当母管道曲率半径175mm≤r
母
<225mm,选择曲率半径r
a2
=200mm的曲面;当母管道曲率半径225mm≤r
母
<275mm,选择曲率半径r
a3
=250mm的曲面;当母管道曲率半径275mm≤r
母
<325mm,选择曲率半径r
a4
=300mm的曲面;当母管道曲率半径325mm≤r
母
<375mm,选择曲率半径r
b1
=350mm的曲面;当母管道曲率半径375mm≤r
母
<425mm,选择曲率半径r
b2
=400mm的曲面;当母管道曲率半径425mm≤r
母
<475mm,选择曲率半径r
b3
=450mm的曲面;当母管道曲率半径r
母
≥475mm,选择曲率半径r
b4
=500mm的曲面。
49.扫查时扫查灵敏度的确定方法为:将探头置于试块上,找出距探头前沿10mm、深度为3mm模拟裂纹的最强反射波,调整到80%屏高,作为基准灵敏度。在基准灵敏度基础上提高增益6db作为扫查灵敏度。
50.步骤三,扫查
51.探头置于被检汽水管道管座角焊缝附近,探头前端与管座角焊缝的最小距离满足1mm≤s≤5mm,保持探头与被检工件稳定接触,沿扫查路径进行360
°
环向扫查,保证探头前沿垂直中心线与以管座开孔为中心、半径为r+2.5mm的圆始终相切,扫查速度不应超过150mm/s;
52.步骤四,缺陷识别
53.按步骤四进行扫查,对缺陷进行定量和位置的测定,得到最大反射波幅值及指示长度,所有超过步骤二得到的距离
‑
波幅曲线高度的反射波均判定为缺陷波;
54.缺陷波幅的测定:缺陷最大反射波幅与距离
‑
波幅曲线高度的差值
△
即为缺陷波幅,记为sl
±△
db;
55.缺陷的位置测定:根据探头在探测面上的位置和最高反射波在示波屏上的水平位置来确定缺陷在管孔周围的位置,并做好记录;
56.缺陷长度的测定:采用单侧半波高度法(6db法)测定其指示长度,具体方法如下:移动探头,找到缺陷最强反射波,将波高调到80%屏高,向外侧移动探头,当波高降到40%屏高时,在探头中心线所对应的位置上作好标记,标记到开孔边缘的距离即为缺陷的指示长度。
57.检测方法的验证:
58.制作管道管座开孔放射状裂纹对比试块dbsk1~dbsk4,如图9
‑
13所示,母管道规格为φ800mm
×
100mm,管座规格为φ30mm
×
10mm,对比试块dbsk1开孔周围加工有2个人工缺陷,缺陷1长5mm
×
宽0.2mm
×
深3mm、缺陷2长5mm
×
宽0.2mm
×
深6mm;对比试块dbsk2开孔周围加工有2个人工缺陷,缺陷3长10mm
×
宽0.2mm
×
深3mm、缺陷4长20mm
×
宽0.2mm
×
深3mm;对比试块dbsk3开孔周围加工有2个人工缺陷,缺陷5长10mm
×
宽0.2mm
×
深3mm、缺陷6长10mm
×
宽0.2mm
×
深6mm;对比试块dbsk4开孔周围加工有2个人工缺陷,缺陷7长5mm
×
宽0.2mm
×
深3mm、缺陷8长20mm
×
宽0.2mm
×
深3mm。按本发明方法对管道管座开孔放射状裂纹对比试块开孔周围区域进行扫查。
59.试验结果如下表所示:
60.序号缺陷编号缺陷尺寸缺陷位置最大波高缺陷实测长度1缺陷1长5mm
×
宽0.2mm
×
深3mm轴向中心线sl+3.8db6mm2缺陷2长5mm
×
宽0.2mm
×
深6mm轴向中心线sl+5.6db7mm3缺陷3长10mm
×
宽0.2mm
×
深3mm环向中心线sl+5.2db11mm4缺陷4长20mm
×
宽0.2mm
×
深3mm环向中心线sl+6.0db21mm5缺陷5长10mm
×
宽0.2mm
×
深3mm轴向中心线sl+5.5db11mm6缺陷6长10mm
×
宽0.2mm
×
深6mm轴向中心线sl+8.6db12mm7缺陷7长5mm
×
宽0.2mm
×
深6mm环向中心线sl+5.5db6mm8缺陷8长20mm
×
宽0.2mm
×
深6mm环向中心线sl+9.1db22mm
61.经检测,缺陷1最大反射波高sl+3.8db,长度测量值为6mm;缺陷2最大反射波高sl+5.6db,长度测量值为7mm;缺陷3最大反射波高sl+5.2db,长度测量值为11mm;缺陷4最大反射波高sl+6.0db,长度测量值为21mm;缺陷5最大反射波高sl+5.5db,长度测量值为11mm;缺陷6最大反射波高sl+8.6db,长度测量值为12mm;缺陷7最大反射波高sl+5.5db,长度测量值
为6mm;缺陷8最大反射波高sl+9.1db,长度测量值为22mm。
62.检测结果表明该检测方法能有效检测出对比试块中所有的人工模拟缺陷,能检出的最小缺陷为长5mm
×
宽0.2mm
×
深3mm;能够准确的测定出缺陷位置;能够较为准确的测量出缺陷长度,误差小于等于2mm,综上,该检测方法能够实现汽水管道管座开孔外壁放射状裂纹的有效检测。