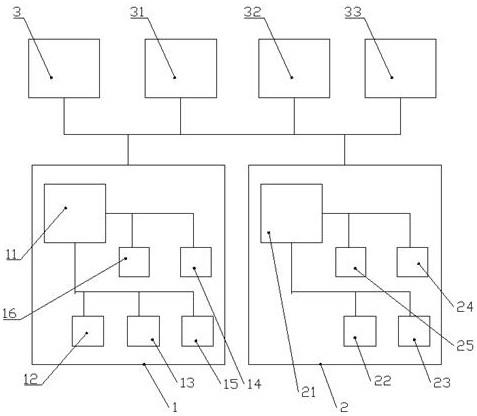
1.本发明涉及绝缘子加工领域,特别涉及一种炼胶用自动称重系统。
背景技术:2.绝缘子是一种特殊的绝缘控件, 能够在架空输电线路中起到重要作用。早年间绝缘子多用于电线杆,慢慢发展于高型高压电线连接塔的一端挂了很多盘状的绝缘体,它是为了增加爬电距离的,通常由玻璃或陶瓷制成,就叫绝缘子。绝缘子不应该由于环境和电负荷条件发生变化导致的各种机电应力而失效,否则绝缘子就不会产生重大的作用,就会损害整条线路的使用和运行寿命。
3.绝缘子的一般由芯棒、伞裙、连接金具几个部分共同组成,伞裙设置在芯棒的外表面上,连接金具分别连接在芯棒的两侧。上述组成中,伞裙在进行成型的过程中,采用的是胶料注塑的方式成型的,这一过程,需要先通过开炼机或密炼机对硅橡胶进行混炼,然后再将混炼后的胶料送给捏合机进行捏合处理,并由捏合机将加工好的胶料送至注塑机中对芯棒进行注塑。
4.在开炼机或密炼机进行混炼的过程中,需要根据不同的配比要求,将不同重量的原料一同加入开炼机或密炼机中进行混炼,在进行称重的过程中,传统的方式时采用单一的电子秤来对原料进行称重,这样的方式在进行称重时存在着诸多问题:首先,电子秤上显示的数据都是通过人工进行读取的,这样的方式会由于光线亮度、电子秤显示屏的亮度等等问题,而不可避免的会存在着读取错误的现象,影响到后续的加工;其次,在使用电子秤对物料进行称重的过程中,由于生产的配方并不仅仅局限于一种,即会对多种不同的配方进行生产,也就会使用到多种不同的物料,而且即使会使用到相同的物料,但是对于物料的一些性能参数的要求也不一样,这也就要求操作工在进行称重前,需要先确认称重的物料的种类以及具体的性能参数,而人工识别的方式只能通过物料包装袋上附带的参数说明表来进行判断,这种识别方法也不可避免的会有识别错误的现象的发生,而且人工识别非常的麻烦,由于配方的种类很多,操作工无法将所有的配方全部记住,因此,需要先提前将生产用的对应的配方打印后贴在对应的生产区域,以方便操作工进行观察对照识别,非常的麻烦,而且还容易导致配方的泄露;另外,对于这些原料自身的性能参数要求,不论是直接外购还是自行生产,都不能保证原料的参数要求100%全部满足要求,不可避免的会有不符合要求的原料夹杂在其中,如果采用这类原料进行生产,最终成型出的伞裙也无法满足要求,浪费了其他的原料,报废品的数量也增加,降低了产品的合格率。
技术实现要素:5.本发明要解决的技术问题是提供一种炼胶用自动称重系统,能够对不同的原料进行自动称重,方便对原料种类的识别,降低报废品的产生,提高产品的合格率。
6.为解决上述技术问题,本发明的技术方案为:一种炼胶用自动称重系统,其创新点在于:包括
胶料、粉料称量单元,包括第一电脑终端、第一电子秤、第二电子秤、第一扫码器、第一指示灯、第一打印机,所述第一电脑终端至少包括一显示器,第一电子秤、第二电子秤、第一扫码器、第一指示灯、第一打印机均接入第一电脑终端,其中,第一电子秤、第二电子秤用于对胶料或粉料进行称重并将重量数据反馈给第一电脑终端,第一扫码器用于对胶料或粉料的包装袋上的条码进行扫描并将扫描结果反馈给第一电脑终端,第一指示灯用于接收第一电脑终端发送过来的信号,并显示不同颜色的灯光,第一打印机用于将第一电脑终端内的文件进行打印;油料称量单元,包括第二电脑终端、第三电子秤、第二扫码器、第二指示灯、第二打印机,所述第二电脑终端至少包括一显示器,第三电子秤、第二扫码器、第二指示灯、第二打印机均接入第一电脑终端,其中,第三电子秤用于对油料进行称重并将重量数据反馈给第二电脑终端,第二扫码器用于对油料的包装袋上的条码进行扫描并将扫描结果反馈给第二电脑终端,第二指示灯用于接收第二电脑终端发送过来的信号,并显示不同颜色的灯光,第二打印机用于将第二电脑终端内的文件进行打印;控制单元,包括服务器、配方管理终端、生产管理终端、原料管理终端,所述服务器与胶料、粉料称量单元、油料称量单元、配方管理终端、生产管理终端、原料管理终端均相连,其中,服务器用于接收胶料、粉料称量单元、油料称量单元反馈的信号,并经过内部处理后,再将处理信号反馈给胶料、粉料称量单元或油料称量单元,配方管理终端、生产管理终端、原料管理终端均用于向服务器内导入数据或对服务器内的数据进行修改。
7.进一步的,炼胶用自动称重系统的称重管理方法包括下述步骤:s1 :原料管理首先,原料在入库前,需要先对原料的基础信息进行定义,原料的基础信息包括原料代码、名称、计量单位、最佳质保期、最长质保期,在原料入库时,再对原料的条码追溯标识,包括入库日期、生产厂家、原料批次、质保期;其次,根据上述信息,建立原料条形码标识:根据入库单信息,输入原料代码、供应商代码、批号、生产日期、数量,由服务器记录每批原料入库的检验报告编号及检验结果,检验结果包括合格、不合格、备注、检验员;然后,自动称重系统依据上述情形打印条形码,根据需要选择大标签条形码或小标签条形码,并将条形码贴/挂在原料的包装袋上,供称量扫描识别;s2 :配方管理技术部统一对服务器内的每一种产品的配方进行维护管理,并且对生产的每一配方进行存档,保证原始生产文档的完整性,并且只有经过授权的人员才能维护配方和在服务器中查阅配方,其他人员无法看到配方;由技术部人员对每种配方设置一个配方编号、名称并录入服务器内,并保存以下基础信息:称量顺序号、原料代码、称量单位、标准重量、上限值、下限值;技术部根据生产计划下达生产配方,并自动形成产品批号,再由自动称重系统根据配方单自动计算各原料的理论用量值,供领料参考;s3 :生产管理在生产前,由生产管理人员在生产管理终端设置当天的生产计划,生产计划包括生产日期、产品编号、名称、生产数量、规格信息、配方编号、配料重量、产品批次、作业流水
号;在生产过程中,由生产管理人员对生产过程加以监控,包括配料、包装的生产过程的记录与完成情况或进度,同时生产管理人员统计某段时间内原料实际用量与理论用量值,便于成本控制;s4 :称重管理首先,配料人员根据生产管理人员设定的生产计划,开始配料称重的准备工作,自动称重系统自动按照称量顺序列出原料代码、标准重量、上限值、下限值;然后,配料人员开始进行取料,在取料时,为防止取料错误,由配料人员采用第一扫码器或第二扫码器扫描物料包装袋上的条形码,并将扫描信息传输给服务器,由服务器来检测所取物料是否正确,若服务器检测到原料品类不正确或过有效期,则将该信号反馈给对应位置的第一指示灯或第二指示灯,由对应的第一指示灯或第二指示灯亮红色警示灯进行警示,并且配料人员不能进行下步操作;若服务器检测到原料正确,则由配料人员继续进行下一步,由配料人员对原料进行称重,并通过第一电脑终端或第二电脑终端的显示屏、第一指示灯或第二指示灯反映称量状态,称重点一共有两个,胶料、粉料、硫化剂共用一个称量点,即通过胶料、粉料称量单元进行称重,第一电子秤的规格为150kg/10g,第二电子秤的规格为6kg/1g,第一电子秤用于对大重量的原料进行称重,第二电子秤用于对小重量的原料进行称重,由自动称重系统自动切换第一电子秤、第二电子秤,油料一个称量点,即通过油料称量单元进行称重,第三电子秤规格为6kg/1g;在配料人员进行称重时,当称重低于下限值时,第一指示灯或第二指示灯亮黄色指示灯,当称重高于上限值时,第一指示灯或第二指示灯亮红色指示灯,当称重位于公差范围内时,第一指示灯或第二指示灯亮绿色指示灯,同样的,称量若超过设定的公差范围,则配料人员不能进行下一步称量,只有在公差范围内,才能对下一个配料进行称量,直至完成所有原料的称重;每批次称量结束,自动称重系统自动保存配料记录,并自动生成配料批号,以供质量追溯,记录内容至少包括生产批次、配方编号、产品编号、各原料的实际用量、公差、每种原料所用的生产厂家、生产批号、入库日期、配料日期、时间、当天配料序号,配料人,并由自动称重系统根据设置选项打印投料标识卡;s5 :安全管理设置系统管理、原料管理、配料称量、投料操作、配方管理、生产管理不同的账号,来区分操作权限,以保证自动称重系统及操作安全,系统管理员有权对多个操作者分别赋予不同的操作权限及密码并可查看、修改,同时自动称重系统定时自动备份功能,确保数据安全。
8.进一步的,所述步骤s4中,在对原料进行称重时,根据需要将原料分成三份,称量三次,以方便分批投料。
9.进一步的,所述步骤s4中,在配料称量前对电子秤进行强制校对,每个生产班次在工作前需用标准砝码进行演示配方操作,如电子秤无异常才能进行正式的配料称量操作。
10.本发明的优点在于:本发明的自动称重系统,通过胶料、粉料称量单元、油料称量单元、控制单元之间的相互配合,从而实现了对原料的自动称重、读数等操作,无需再由人
工判断,也就避免了因人工操作而导致的称重不准等不良现象,保证后续加工的顺利进行,相对应的也就降低报废品的产生,提高产品的合格率。
11.基于本发明的自动称重系统,再配合称重管理方法,对生产过程的关键环节加以控制,从原料源头抓起,实现原料批次管理并建立条形码标识,对原料配料称量环节进行控制,有效防止人为因素在配料称量中的影响,确保产品质量的稳定性,实现产品质量由产后检测转变为产前、产中控制和产后溯源,从生产源头上强化和提高产品的质量和安全性,保证产品全程优质、安全、高效生产。
12.配料称重的准确与否,对产品的质量其至关重要的作用,本发明的自动称重系统系统采用条码识别,计算机控制技术,防止人为差错,确保称重准确、完整,称重结束,系统自动保存配料记录,以供质量追溯,记录内容不仅包括生产批次、产品编号、各原料的实际用量、更为重要的是记录每种原料所用的生产厂家、生产批号、入库日期等更为关键的信息。
附图说明
13.下面结合附图和具体实施方式对本发明作进一步详细的说明。
14.图1为本发明的炼胶用自动称重系统的连接示意图。
具体实施方式
15.下面的实施例可以使本专业的技术人员更全面地理解本发明,但并不因此将本发明限制在所述的实施例范围之中。
16.如图1所示的一种炼胶用自动称重系统,包括胶料、粉料称量单元1,包括第一电脑终端11、第一电子秤12、第二电子秤13、第一扫码器14、第一指示灯15、第一打印机16,第一电脑终端11至少包括一显示器,第一电子秤12、第二电子秤13、第一扫码器14、第一指示灯15、第一打印机16均接入第一电脑终端11,其中,第一电子秤12、第二电子秤13用于对胶料或粉料进行称重并将重量数据反馈给第一电脑终端11,第一扫码器14用于对胶料或粉料的包装袋上的条码进行扫描并将扫描结果反馈给第一电脑终端11,第一指示灯15用于接收第一电脑终端11发送过来的信号,并显示不同颜色的灯光,灯光包括红色灯光、黄色灯光、绿色灯光,第一打印机16用于将第一电脑终端11内的文件进行打印,第一扫码器14、第一打印机16通过usb线与第一电脑终端11实现数据互通,第一电子秤12、第二电子秤13、第一指示灯15通过232数据线与第一电脑终端11实现数据互通。
17.油料称量单元2,包括第二电脑终端21、第三电子秤22、第二扫码器23、第二指示灯24、第二打印机25,第二电脑终端21至少包括一显示器,第三电子秤22、第二扫码器23、第二指示灯24、第二打印机25均接入第一电脑终端21,其中,第三电子秤22用于对油料进行称重并将重量数据反馈给第二电脑终端21,第二扫码器23用于对油料的包装袋上的条码进行扫描并将扫描结果反馈给第二电脑终端21,第二指示灯24用于接收第二电脑终端21发送过来的信号,并显示不同颜色的灯光,灯光包括红色灯光、黄色灯光、绿色灯光,第二打印机25用于将第二电脑终端21内的文件进行打印,第二扫码器23、第二打印机25通过usb线与第二电脑终端21实现数据互通,第三电子秤22、第二打印机25通过232数据线与第二电脑终端21实
现数据互通。
18.控制单元,包括服务器3、配方管理终端31、生产管理终端32、原料管理终端33,服务器3与胶料、粉料称量单元1、油料称量单元2、配方管理终端31、生产管理终端32、原料管理终端33均相连,其中,服务器3用于接收胶料、粉料称量单元1、油料称量单元2反馈的信号,并经过内部处理后,再将处理信号反馈给胶料、粉料称量单元1或油料称量单元2,配方管理终端31、生产管理终端32、原料管理终端33均用于向服务器3内导入数据或对服务器3内的数据进行修改,服务器3通过网线与胶料、粉料称量单元1、油料称量单元2、配方管理终端31、生产管理终端32、原料管理终端33之间进行数据互通。
19.本发明的自动称重系统,通过胶料、粉料称量单元、油料称量单元、控制单元之间的相互配合,从而实现了对原料的自动称重、读数等操作,无需再由人工判断,也就避免了因人工操作而导致的称重不准等不良现象,保证后续加工的顺利进行,相对应的也就降低报废品的产生,提高产品的合格率。
20.上述的自动称重系统的称重管理方法包括下述步骤:s1 :原料管理首先,原料在入库前,需要先对原料的基础信息进行定义,原料的基础信息包括原料代码、名称、计量单位、最佳质保期、最长质保期,在原料入库时,再对原料的条码追溯标识,包括入库日期、生产厂家、原料批次、质保期。
21.其次,根据上述信息,建立原料条形码标识:根据入库单信息,输入原料代码、供应商代码、批号、生产日期、数量,由服务器记录每批原料入库的检验报告编号及检验结果,检验结果包括合格、不合格、备注、检验员。
22.然后,自动称重系统依据上述情形打印条形码,根据需要选择大标签条形码或小标签条形码,并将条形码贴/挂在原料的包装袋上,供称量扫描识别。
23.s2 :配方管理技术部统一对服务器内的每一种产品的配方进行维护管理,并且对生产的每一配方进行存档,保证原始生产文档的完整性,并且只有经过授权的人员才能维护配方和在服务器中查阅配方,其他人员无法看到配方。
24.由技术部人员对每种配方设置一个配方编号、名称并录入服务器内,并保存以下基础信息:称量顺序号、原料代码、称量单位、标准重量、上限值、下限值。
25.技术部根据生产计划下达生产配方,并自动形成产品批号,再由自动称重系统根据配方单自动计算各原料的理论用量值,供领料参考。
26.s3 :生产管理在生产前,由生产管理人员在生产管理终端设置当天的生产计划,生产计划包括生产日期、产品编号、名称、生产数量、规格信息、配方编号、配料重量、产品批次、作业流水号。
27.在生产过程中,由生产管理人员对生产过程加以监控,包括配料、包装的生产过程的记录与完成情况或进度,同时生产管理人员统计某段时间内原料实际用量与理论用量值,便于成本控制;s4 :称重管理首先,配料人员根据生产管理人员设定的生产计划,开始配料称重的准备工作,自
动称重系统自动按照称量顺序列出原料代码、标准重量、上限值、下限值。
28.然后,配料人员开始进行取料,在取料时,为防止取料错误,由配料人员采用第一扫码器14或第二扫码器23扫描物料包装袋上的条形码,并将扫描信息传输给服务器3,由服务器3来检测所取物料是否正确,若服务器3检测到原料品类不正确或过有效期,则将该信号反馈给对应位置的第一指示灯15或第二指示灯24,由对应的第一指示灯15或第二指示灯24亮红色警示灯进行警示,并且配料人员不能进行下步操作。
29.若服务器3检测到原料正确,则由配料人员继续进行下一步,由配料人员对原料进行称重,并通过第一电脑终端11或第二电脑终端21的显示屏、第一指示灯15或第二指示灯24反映称量状态,称重点一共有两个,胶料、粉料、硫化剂共用一个称量点,即通过胶料、粉料称量单元1进行称重,第一电子秤12的规格为150kg/10g,第二电子秤13的规格为6kg/1g,第一电子秤12用于对大重量的原料进行称重,第二电子秤13用于对小重量的原料进行称重,由自动称重系统自动切换第一电子秤12、第二电子秤13,油料一个称量点,即通过油料称量单元2进行称重,第三电子秤22规格为6kg/1g。
30.在配料人员进行称重时,当称重低于下限值时,第一指示灯15或第二指示灯24亮黄色指示灯,当称重高于上限值时,第一指示灯15或第二指示灯24亮红色指示灯,当称重位于公差范围内时,第一指示灯15或第二指示灯24亮绿色指示灯,同样的,称量若超过设定的公差范围,则配料人员不能进行下一步称量,只有在公差范围内,才能对下一个配料进行称量,直至完成所有原料的称重。
31.每批次称量结束,自动称重系统自动保存配料记录,并自动生成配料批号,以供质量追溯,记录内容至少包括生产批次、配方编号、产品编号、各原料的实际用量、公差、每种原料所用的生产厂家、生产批号、入库日期、配料日期、时间、当天配料序号,配料人,并由自动称重系统根据设置选项打印投料标识卡;在对原料进行称重时,根据需要将原料分成三份,称量三次,以方便分批投料。
32.在配料称量前对电子秤进行强制校对,每个生产班次在工作前需用标准砝码进行演示配方操作,如电子秤无异常才能进行正式的配料称量操作。
33.s5 :安全管理设置系统管理、原料管理、配料称量、投料操作、配方管理、生产管理不同的账号,来区分操作权限,以保证自动称重系统及操作安全,系统管理员有权对多个操作者分别赋予不同的操作权限及密码并可查看、修改,同时自动称重系统定时自动备份功能,确保数据安全。例如:对于原料包装袋上的贴的条形码,只有原料管理账号才可完成操作;对于配方管理中的配方导入、产品批号等等,只有配方管理账号才可完成操作;在进行原料称重时,只有配料称量账号才可完成操作。
34.基于本发明的自动称重系统,再配合称重管理方法,对生产过程的关键环节加以控制,从原料源头抓起,实现原料批次管理并建立条形码标识,对原料配料称量环节进行控制,有效防止人为因素在配料称量中的影响,确保产品质量的稳定性,实现产品质量由产后检测转变为产前、产中控制和产后溯源,从生产源头上强化和提高产品的质量和安全性,保证产品全程优质、安全、高效生产。
35.配料称重的准确与否,对产品的质量其至关重要的作用,本发明的自动称重系统系统采用条码识别,计算机控制技术,防止人为差错,确保称重准确、完整,称重结束,系统
自动保存配料记录,以供质量追溯,记录内容不仅包括生产批次、产品编号、各原料的实际用量、更为重要的是记录每种原料所用的生产厂家、生产批号、入库日期等更为关键的信息。
36.本行业的技术人员应该了解,本发明不受上述实施例的限制,上述实施例和说明书中描述的只是说明本发明的原理,在不脱离本发明精神和范围的前提下,本发明还会有各种变化和改进,这些变化和改进都落入要求保护的本发明范围内。本发明要求保护范围由所附的权利要求书及其等效物界定。