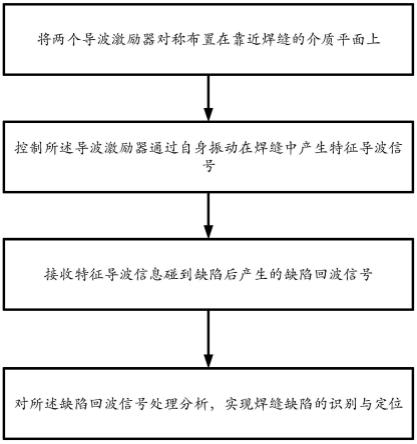
1.本发明属于无损检测领域,特别涉及一种焊缝缺陷检测方法及其装置。
背景技术:2.石油储罐是石油、化工行业必不可少的存储设备,石油罐的密封性至关重要,一旦出现石油或其他化工产品的泄露会导致重大的安全隐患,对其进行实时的结构健康检测具有重要的意义。为了保证储罐的结构完整性,需要将储罐的各个部分以焊接的形式进行连接,因此焊缝是储罐的重要组成部分。焊缝结构在长期服役期间,由于周围复杂环境以及集中应力的影响,相较于正常钢板更易于产生裂纹腐蚀等缺陷。造成结构失效问题,严重时会引发安全事故。
3.传统的无损检测方法采用超声波逐点扫查方法,这种方法需要复杂的预处理工作,例如表面除锈。而且检测前需要将储罐清空,需要耗费大量的人力物力。超声导波检测是一种新型的无损检测方法,只需要有限空间内布置少量传感器既可以获取试件内部缺陷尺寸和位置信息,完成大面积检测。现有技术中公开一种超声导波检测方法,将传感器以圆周的形式布置在具有对接焊缝的钢板上,利用散射矩阵法进行缺陷识别检测。然而在长距离焊缝检测中,超声导波在板中是沿各个方向传播的,在传播过程中,超声导波遇到一些特殊结构时将发生模态转换,并伴有能量损失,使得板中的信号变的复杂,接收到的回波信号也比较微弱,难以进行分析,特殊结构指的是支架、焊缝等。
4.因此研究超声导波在焊缝处以及周围的模态变化,探索导波与焊缝的工作机理显得十分必要。现有技术中公开了一种基于电磁超声原理的高频导波焊缝检测探头,包括用于封装探头内所有材料的外壳,用于在管道的焊缝处产生偏置磁场的永磁体,缠绕于永磁体上用于激励高频导波的感应线圈一,缠绕于永磁体上用于接收高频导波信号的感应线圈二及分别与感应线圈一、感应线圈二连接用于传输信号至主机的两个信号连接头。利用电磁超声原理,无需耦合剂,可以实现非接触检测,因此能适用于检测高温和带防腐层的管道焊缝检测。探头激发的高频导波将周向环绕焊缝传播,检测效率大大提高。但是所需要的仪器设备复杂,转换效率相对较低。另外现有技术公开了一种将导波换能器安装在被检焊缝一端的对接焊缝无损检测系统,但是在焊缝检测时,需要与焊缝表面接触,焊缝表面非常粗糙有较多的凸起和凹陷,将激励传感器压紧在焊缝表面时,会出现耦合不紧密,以至于导波信号无法高效地在焊缝中传播的现象。
5.因此现有技术中还没有出现一种操作简单、结构简洁,并且可以实现非接触式检测焊缝缺陷的设备。值得解释的是此处的非接触式指的是与被测量装置非直接接触,而是与被测装置相离较近的介质平台接触,避免被测量装置的表面凹凸不平导致的误差。
技术实现要素:6.针对上述问题,本发明公开了一种焊缝缺陷检测方法,所述焊缝缺陷检测方法包括以下步骤:
7.将两个导波激励器对称布置在靠近焊缝的介质平面上;
8.控制所述导波激励器通过自身振动在焊缝中产生特征导波信号;
9.接收特征导波信息碰到缺陷后产生的缺陷回波信号;
10.对所述缺陷回波信号处理分析,实现焊缝缺陷的识别与定位。
11.进一步的,对所述缺陷回波信号处理分析的具体步骤如下:
12.对接收的焊缝缺陷回波信号进行滤波去噪、波谷分离;
13.提取缺陷回波信号时域和频域特征,进行检测识别。
14.进一步的,对焊缝缺陷进行定位的具体步骤如下:
15.获取缺陷回波信号和第一始发波的时间间隔t1、缺陷回波信号和第二始发波的时间间隔t2和获得测量获得的焊缝长度s1,利用波速一致性计算得到缺陷与导波接收传感器之间的距离s;
16.根据缺陷与导波接收传感器之间的距离s对缺陷进行定位;
17.其中:
18.s=t2*(s1/t1)。
19.进一步的,所述导波激励器与焊缝的之间的距离小于设定值。
20.本发明还公开了一种焊缝缺陷检测装置,所述焊缝缺陷检测装置包括两个导波激励器3、两个导波接收传感器4、数据采集器5和计算机6;
21.两个所述导波激励器3紧靠焊缝对称布置在靠近焊缝的介质平面上,用于通过自身振动在焊缝中产生特征导波信号;
22.所述导波接收传感器4与所述导波激励器3平行设置在所述介质平面上,用于接收所述特征导波信号碰到缺陷后产生的缺陷回波信号;
23.所述数据采集器5与所述导波接收传感器4和所述计算机6分别连接,用于采集所述缺陷回波信号的数据,并传输给所述计算机6;
24.所述计算机6与所述采集单元信号连接,用于对所述缺陷回波信息进行处理分析,实现对焊缝缺陷的识别与定位。
25.进一步的,所述焊缝缺陷检测装置还包括波形发生器1、功率放大器2;
26.所述波形发生器1用于根据波形参数输出检测所需的波形;
27.所述功率放大器2与所述波形发生器1和所述导波激励器3信号连接,用于将所述波形进行放大后加载到所述导波激励器3。
28.进一步的,所述导波激励器3以汉宁窗调至的正弦脉冲波形作为激励信号。
29.进一步的,所述波形发生器1用于接收所述正弦波脉冲信号波形参数,输出检测波形;所述功率放大器2用于对所述检测波形进行放大;所述导波接收传感器4用于接收回波信号,并发送给数据采集器5;所述计算机6用于对所述缺陷回波信号处理分析实现焊缝识别与定位。
30.进一步的,所述计算机6用于对所述缺陷回波信号处理分析实现焊缝缺陷的识别包括对接收的焊缝缺陷回波信号进行滤波去噪、波谷分离,提取缺陷回波信号时域及频域特征,进行检测识别。
31.进一步的,所述计算机6用于对所述缺陷回波信号处理分析实现焊缝缺陷的定位包括获取缺陷回波信号和第一始发波的时间间隔t1、缺陷回波信号和第二始发波的时间间
隔t2和获得测量获得的焊缝长度s1,利用波速一致性计算得到缺陷与导波接收传感器4之间的距离s;根据缺陷与导波接收传感器4之间的距离s对缺陷进行定位;
32.缺陷与导波接收传感器4之间的距离s的约束关系如下:
33.s=t2*(s1/t1)。
34.本发明能够实现在不接触焊缝的情况下实现焊缝内缺陷的精准识别和快速定位。控制所述导波激励器与焊缝的之间的距离小于设定值是为了减小导波激励器与焊缝的之间的距离对检测结果的影响。
35.本发明的其它特征和优点将在随后的说明书中阐述,并且,部分地从说明书中变得显而易见,或者通过实施本发明而了解。本发明的目的和其他优点可通过在说明书、权利要求书以及附图中所指出的结构来实现和获得。
附图说明
36.为了更清楚地说明本发明实施例或现有技术中的技术方案,下面将对实施例或现有技术描述中所需要使用的附图作一简单地介绍,显而易见地,下面描述中的附图是本发明的一些实施例,对于本领域普通技术人员来讲,在不付出创造性劳动的前提下,还可以根据这些附图获得其他的附图。
37.图1示出了根据本发明实施例中的焊缝缺陷检测方法流程图;
38.图2示出了根据本发明实施例中的导波激励器距焊缝距离与焊缝特征导波强度关系;
39.图3是处理根据本发明实施例中的焊缝缺陷检测装置示意图。
40.图中:1、波形发生器;2、功率放大器;3、导波激励器;4、导波接收传感器;5、数据采集器;6、计算机。
具体实施方式
41.为使本发明实施例的目的、技术方案和优点更加清楚,下面将结合本发明实施例中的附图,对本发明实施例中的技术方案进行清楚、完整地说明,显然,所描述的实施例是本发明一部分实施例,而不是全部的实施例。基于本发明中的实施例,本领域普通技术人员在没有做出创造性劳动前提下所获得的所有其他实施例,都属于本发明保护的范围。
42.本发明公开了一种焊缝缺陷检测方法,如图1所示,所述焊缝缺陷检测方法包括以下步骤:
43.将两个导波激励器对称布置在靠近焊缝的介质平面上;
44.控制所述导波激励器通过自身振动在焊缝中产生特征导波信号;
45.接收特征导波信息碰到缺陷后产生的缺陷回波信号;具体的,采用两个导波接收传感器同时分别接收两股缺陷回波信号,所述导波接收传感器分别与导波激励器平行布置。
46.对所述缺陷回波信号处理分析,实现焊缝缺陷的识别与定位。实现非接触式焊缝缺陷检测,值得解释的是此处的非接触式指的是与焊缝不是直接接触,而是与焊缝相离较近的介质平台接触,避免由于焊缝的表面凹凸不平导致的误差。
47.具体的,所述导波激励器在接收到电压激励信号后自身会产生特定频率的振动,
这种振动带动所述介质平面振动,进而通过耦合带动焊缝处质点振动。
48.值得解释的是焊缝的特征导波信号是指沿着焊缝传播的导波模态,焊缝特征导波具有能量衰减慢,可以沿着焊缝长距离传播,十分有利于实现长距离下的焊缝表面及内部缺陷的高效准确检测。焊缝中的导波作为一种特殊的波导,可将内部能量最大程度的汇集并引导其沿着焊缝传播,即焊缝结构具有“能陷效应”。根据光的折射定律,当导波传播到两种不同的介质的交界面时会发生反射和折射,且满足折射定律:
[0049][0050]
其中aw、a
p
表示焊缝中和板中的入射角和折射角,折射角的大小与两种介质的声阻抗密切相关,声阻抗差别越大,导波中波的泄漏就越少。vw、v
p
为焊缝中和板中的传播速度,当vw》v
p
时,波的传播满足全反射条件,声波在焊缝与板的交界面处无折射,能量完全限制在焊缝中。依据板中的导波频散特性可知,导波的相速度与频厚积成反比。在对接焊缝中,由于焊缝余高的存在,焊缝的厚度一般会大于周围板材的厚度,相同频率下,频厚积较大,因而焊缝区域的相速度较小。当满足全反射条件时,整个焊缝结构相当于一个全反射层,将大部分导波“限制”在其中。而不满足全反射条件时,导波能量会出现向外扩散的现象,这种沿着焊缝传播的导波模态即被称之为焊缝的特征导波信号。
[0051]
示例性的,控制两个所述导波激励器分别施加相同水平剪切方向或轴向载荷的具体步骤如下:将电压激励信号加载到对称布置在焊缝两侧的导波激励器以产生特定的振动模式。这种振动会带动传感器下表面质点振动,进而带动焊缝处质点振动,在焊缝中激励所需要的导波模态。根据能陷效应原理,导波能量会集中在焊缝内部并沿长度方向传播,对称激励布置可以在焊缝中产生特征导波信号。
[0052]
当所述特征导波在传播过程中遇到缺陷时,导波会与缺陷进行相互作用,发生反向传播的缺陷回波信号,另一部分会透过缺陷继续向前传播,直到焊缝断面处反射回来。在焊缝两侧布置导波接收传感器接收焊缝缺陷回波信号。根据飞行时间算法实现对焊缝缺陷的检测定位。
[0053]
具体的,对所述缺陷回波信号处理分析的具体步骤如下:对接收的焊缝缺陷回波信号进行滤波去噪、波谷分离;提取缺陷回波信号时域及频域特征,进行检测识别。两路接收信号都对缺陷回波进行识别,提高识别准确率。
[0054]
进一步的,对焊缝进行定位的具体步骤如下:
[0055]
获取缺陷回波和第一始发波的时间间隔t1、缺陷回波和第二始发波的时间间隔t2和获得测量获得的焊缝长度s1,利用飞行时间算法计算得到缺陷与导波接收传感器之间的距离s;根据缺陷与导波接收传感器之间的距离s对缺陷进行定位。缺陷与导波接收传感器之间的距离s的约束关系如下:
[0056]
s=t2*(s1/t1)。
[0057]
示例性的,利用飞行时间算法计算得到缺陷与导波接收传感器之间的距离具体包括以下步骤,提前测量波速,获取回波的时间,缺陷与导波接收传感器之间的距离等于波速与回波时间的乘积的一半。
[0058]
进一步的,为了便于后续信号处理与分析,选择汉宁窗调制的正弦脉冲波形作为
激励信号。
[0059]
进一步的,为了减小导波激励器与焊缝的距离对特征导波能量的影响,所述导波激励器与焊缝的之间的距离小于设定值,即小于p点的距离。具体的,图2中示出了导波激励器与焊缝之间的距离大小与特征导波信号强弱之间的关系。示例性的,如图2所示,经过仿真实验,得知特征导波信号随着导波激励器与焊缝之间的距离变大而变弱。具体的,特征导波能量的变化趋势为在导波激励器与焊缝之间的距离小于0.2cm时,特征导波能量在高能量处缓慢下降;在0.2cm-0.4cm处时,特征导波能量从高能量向低能量快速下降;距离超过0.4cm后,特征导波能量处于低能量状态,缓慢下降,其中p点表示特征导波能量变化最快的位置,如果激励传感器与焊缝距离大于图中p点所示的距离,能量会在到达焊缝前大幅度衰减,导致焊缝内传播导波能量过小,降低缺陷回波强度,影响焊缝缺陷检测准确性。因此,为保证激励传感器下方质点振动能量可以有效辐射到焊缝中,需将传感器距焊缝的距离控制在p点以内。
[0060]
本发明还公开了一种焊缝缺陷检测装置,如图3所示,所述焊缝缺陷检测装置包括波形发生器1、功率放大器2、两个导波激励器3、两个导波接收传感器4、数据采集器5和计算机6;
[0061]
两个所述导波激励器3紧靠焊缝对称布置在靠近焊缝的介质平面上,用于通过自身振动在焊缝中产生特征导波信号;
[0062]
所述导波接收传感器4与所述导波激励器3平行设置在所述介质平面上,用于同时接收所述特征导波信号碰到缺陷后产生的缺陷回波信号。
[0063]
所述数据采集器5与所述导波接收传感器4和所述计算机6分别连接,用于采集所述缺陷回波信号的数据,并传输给所述计算机6;两个所述导波接收传感器4同时工作接收信号,两路信号在后处理过程可以通过波形对比来进行系统的校准。
[0064]
所述计算机6与所述采集单元信号连接,用于对所述缺陷回波信息进行处理分析,实现对焊缝缺陷的识别与定位。
[0065]
所述波形发生器1用于根据波形参数输出检测所需的波形;
[0066]
所述功率放大器2与所述波形发生器1和所述导波激励器3信号连接,用于将所述波形进行放大后加载到所述导波激励器3。
[0067]
进一步的,所述导波激励器3以汉宁窗调至调制的正弦脉冲波形作为激励信号。
[0068]
进一步的,所述计算机6用于对接收的焊缝缺陷回波信号进行滤波去噪、波谷分离;提取缺陷回波信号时域及频域特征,进行检测识别。
[0069]
进一步的,所述计算机6用于获取缺陷回波和第一始发波的时间间隔t1、缺陷回波和第二始发波的时间间隔t2和获得测量获得的焊缝长度s1,利用波速一致性计算得到缺陷与导波接收传感器4之间的距离s;根据缺陷与导波接收传感器4之间的距离s对缺陷进行定位;
[0070]
缺陷与导波接收传感器4之间的距离s的约束关系如下:
[0071]
s=t2*(s1/t1)。
[0072]
尽管参照前述实施例对本发明进行了详细的说明,本领域的普通技术人员应当理解:其依然可以对前述各实施例所记载的技术方案进行修改,或者对其中部分技术特征进行等同替换;而这些修改或者替换,并不使相应技术方案的本质脱离本发明各实施例技术
方案的精神和范围。