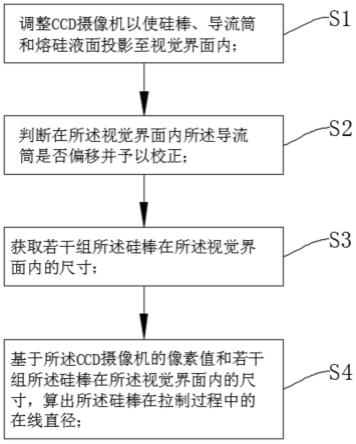
1.本发明属于直拉单晶工艺技术领域,尤其是涉及一种等径制程中硅棒在线直径的检测方法。
背景技术:2.在现阶段单晶炉在拉制单晶硅棒的过程中,单晶硅棒的直径控制主要为人员操作机台手动控制,当ccd检测出一个虚拟的测量信号值时,人员透过炉体外的观察窗上的测径仪对单晶硅棒外径进行模拟测量,以获得正在拉制的单晶硅棒的在线模拟的实测直径。而因单晶硅棒在单晶炉内距离较远,导致不同人员测量的在线直径值不同。单晶硅棒拉制完出炉后,再采用游标卡尺检测实际直径,对比之后发现,极易出现单晶硅棒由于人员测试不准确导致与实际直径相差较大,一炉次的多颗单晶不合格,生产成本损失较大。
3.而且在人工操作过程中,无法直接对导流筒的位置以及ccd摄像头的位置进行准确校正,这些亦都会影响检测结果的准确性。
技术实现要素:4.本发明提供一种等径制程中硅棒在线直径的检测方法,解决了现有技术中人工检测等径硅棒的在线实际直径值准确率低,导致生产成本高、工作效率低的技术问题。
5.为解决上述技术问题,本发明采用的技术方案是:
6.一种等径制程中硅棒在线直径的检测方法,步骤包括:
7.调整ccd摄像机以使硅棒、导流筒和熔硅液面投影至视觉界面内;
8.判断在所述视觉界面内所述导流筒是否偏移并予以校正;
9.获取若干组所述硅棒在所述视觉界面内的尺寸;
10.基于所述ccd摄像机的像素值和若干组所述硅棒在所述视觉界面内的尺寸,算出所述硅棒在拉制过程中的在线直径。
11.进一步的,所述调整ccd摄像机以使硅棒、导流筒和熔硅液面投影至视觉界面内,步骤包括:
12.获取等径时硅棒、导流筒及熔硅液面的投影几何图形,并使所述硅棒、所述导流筒及所述熔硅液面的投影几何图形均汇聚于同一个所述视觉界面内;
13.调整所述ccd摄像机角度以使所述硅棒投影几何图形与所述导流筒投影结合图形同轴心设置;
14.所述硅棒投影几何图形的圆心与所述视觉界面的中心重合。
15.进一步的,在所述硅棒投影几何图形的圆心与所述视觉界面的中心重合之后,还包括:
16.调整所述ccd摄像机的焦距以使所述导流筒投影几何图形的水平直径与所述硅棒投影几何图形的水平直径重叠设置。
17.进一步的,所述判断在所述视觉界面内所述导流筒是否偏移并予以校正,具体包
括:
18.获取所述导流筒投影几何图形的横向直径两端分别至所述视觉界面两侧边的水平直线距离;
19.再依次确定获得的所述导流筒投影几何图形的横向直径两端分别至所述视觉界面两侧边的水平直线距离是否相同;
20.若不相同,继续调整所述ccd摄像机,以使所述导流筒投影几何图形的横向直径两端分别至所述视觉界面两侧边的水平直线距离相同。
21.进一步的,若相同;
22.再在靠近所述导流筒投影几何图形的横向直径两端侧,取任两个相对于纵向轴线对应设置的所述导流筒与所述熔硅液面之间的圆弧夹角面;
23.并计算出其角度差,以确定所述导流筒与所述熔硅液面的水平偏移量。
24.进一步的,所述角度差绝对值的标准范围为0-3
°
。
25.进一步的,任两个相对于纵向轴线对应设置的所述导流筒与所述熔硅液面之间的圆弧夹角面位于所述导流筒投影几何图形的横向直径两端。
26.进一步的,若所述角度差超出其标准范围,则
27.调整所述导流筒的上下高度,以调整所述导流筒的水平偏移量。
28.进一步的,所述获取若干组所述硅棒在所述视觉界面内的尺寸,包括:
29.在所述硅棒投影几何图形上取n个直径尺寸测试值,其中,n≥4且为整数;
30.去掉最大和最小的直径尺寸测试值,并计算剩余(n-2)个的平均直径尺寸测试值。
31.进一步的,所述基于所述ccd摄像机的像素值和若干组所述硅棒在所述视觉界面内的尺寸,算出所述硅棒在拉制过程中的在线直径,具体包括:
32.获取所述ccd摄像机像素值;
33.根据获取的所述硅棒的平均直径尺寸测试值,使所述像素值除以获取的所述硅棒的平均直径尺寸测试值再乘以修正系数,获得的结果即可获得所述硅棒的在线直径值;
34.其中,所述系数为4-4.5。
35.采用本发明设计的一种等径制程中硅棒在线直径的检测方法,可自动并判断导流筒和ccd的位置是否偏移并可根据判断结果进行自动校准其位置,再基于ccd拍摄到的视觉图像图中硅棒的投影直径,再经中位置平均滤波算法对测得的实时在线硅棒直径进行平均计算,以获得精准的实时在线硅棒直径,与拉之后的实际直径相比,再现性好且精确率高。
附图说明
36.图1是本发明一实施例的一种等径制程中硅棒在线直径的检测方法的流程图;
37.图2是本发明一实施例的视觉界面上的结构示意图。
38.图中:
39.10、视觉界面20、导流筒30、熔硅液面
40.40、硅棒
具体实施方式
41.下面结合附图和具体实施例对本发明进行详细说明。
42.本实施例提出一种等径制程中硅棒在线直径的检测方法,如图1所示,
43.步骤包括:
44.s1、调整ccd摄像机以使硅棒、导流筒和熔硅液面投影至视觉界面内。
45.在单晶拉制过程中,为了实时监控到单晶炉体内石英坩埚内的熔硅液面30的位置情况以及硅棒40的在线拉制情况,会在主室炉体外侧设置一ccd摄像机,倾斜设置的ccd摄像机通过其相机所辐射的区域,可将等径时所拉制的硅棒40、导流筒20及熔硅液面30均投影在外设的终端设备的界面上,也即是把硅棒40、导流筒20及熔硅液面30的投影几何图形均汇聚于同一个视觉界面10内,投影的几何图形如图2所示。
46.由于ccd摄像机只能全面照射到导流筒20的下沿面和硅棒40外径,无法全部照射到熔硅液面30的全部面积,同时由于硅棒40的外径小于导流筒20下端面的内径,故在视觉界面10上,看到的导流筒20下端面内径的投影几何图形为圆形,相应地,硅棒40的投影几何图形也为圆形。而熔硅液面30的投影几何图形为一圆弧形结构,且位于硅棒40的投影几何图形和导流筒20的投影几何图形之间,且其弧度凸向于硅棒40的投影几何图形一侧并靠近导流筒20的投影几何图形设置。
47.先调整ccd摄像机的照射角度以使硅棒40的投影几何图形与导流筒20的投影结合图形同轴心设置,且是硅棒40的投影几何图形的圆心与视觉界面10的中心重合。也即是确保导流筒20、和硅棒40是同轴心设置,并位于石英坩埚的中心轴线上,这一才能保证硅棒40拉制的质量。
48.进一步的,还包括调整ccd摄像机的焦距以使导流筒20的投影几何图形的水平直径与硅棒40的投影几何图形的水平直径重叠设置;并使导流筒20的投影几何图形的圆心与硅棒40的投影几何图形的圆心均与视觉界面10的中心线连接点所在的位置重叠相同。
49.s2、判断在视觉界面内导流筒是否偏移并予以校正。
50.先获取导流筒20的投影几何图形的横向直径ab两端分别至视觉界面10两侧边c和d之间的水平直线距离ac和bd。
51.再依次确定ac水平直线距离和bd水平直线距离是否相同。
52.若不相同,则继续调整ccd摄像机,以使导流筒20的投影几何图形的横向直径两端分别至视觉界面10两侧边的水平直线距离ac和bd相同,也即是,保证导流筒20的投影几何图形的圆心、硅棒40的投影几何图形的圆心均位于视觉界面10的中间位置处。
53.若相同,再在靠近导流筒20投影几何图形的横向直径ab两端侧,抓取任两个相对于纵向轴线对应设置的导流筒20与熔硅液面30之间的圆弧夹角面的矩形框a和b;优选地,矩形框a和矩形框b为位于直径ab两端,目的是便于确定导流筒20相对于熔硅液面30的水平偏移量。
54.计算出在矩形框a内的圆弧夹角面和在矩形框b内的圆弧夹角面的切线角度θ1和θ2;再计算出两角度差值
△
θ,以确定导流筒20与熔硅液面30的水平偏移量。
55.其中,角度差值
△
θ的绝对值的标准范围为0-3
°
。
56.若角度差值
△
θ超出其标准范围,也即是导流筒20相对于熔硅液面30具有一定的偏移量,就是表明导流筒20在安装时不到位,使导流筒20水平偏移,这样会引起单晶直径测量不合格。
57.则调整导流筒20的上下高度,以使在矩形框a内的圆弧夹角面和在矩形框b内的圆
弧夹角面的切线角度θ1和θ2;再计算出两角度差值
△
θ的绝对值在标准范围0-3
°
内。
58.s3、获取若干组硅棒在视觉界面内的尺寸。
59.沿硅棒40的投影几何图形的同一顺向的方向内,依次获取若干组硅棒20在视觉界面10内的尺寸,包括:
60.在硅棒40的投影几何图形上取n个直径尺寸测试值,其中,n≥4且为整数。
61.利用中位值平均滤波法算出直径尺寸测试值,即是去掉最大和最小的直径尺寸的测试值,并计算剩余(n-2)个的平均直径尺寸的测试值,也就是测得的视觉界面10上获得的硅棒40的实时在线直径的投影值。
62.这种计算方法,既能抑制随机干扰,又能滤除明显的脉冲干扰。
63.s4、基于ccd摄像机的像素值和若干组硅棒在视觉界面内的尺寸,算出硅棒在拉制过程中的实际在线直径。
64.获取ccd摄像机的像素值;
65.根据的硅棒40的平均直径尺寸的测试值,使ccd摄像机的像素值除以平均直径尺寸的测试值之后,再乘以修正系数,即可获得硅棒40的实时拉制中的在线直径值。
66.其中,系数为4-4.5。
67.例如:
68.若正在拉制的规格为直径为210mm单晶硅棒。
69.在硅棒40的投影几何图形上顺时针依次选取6个直径尺寸测试值,分别为21.1mm、21.5mm、21.7mm、21.4mm、21.4mm、21.3mm,中位值平均滤波法算出平均直径尺寸的测试值为21.4mm。
70.若ccd摄像机的像素值为1024pixel,则像素值除以测试值为1024/21.4≈47.85;其中,系数为4.4,则
71.47.85
×
4.4=210.54mm,即为硅棒40实时在线直径值。
72.且该测试值与标准规格210mm相差较小,表示按照本方法获得的在线直径精准且可靠。
73.采用本发明设计的一种等径制程中硅棒在线直径的检测方法,可自动并判断导流筒和ccd摄像机的位置是否偏移并可根据判断结果进行自动校准其位置,再基于ccd摄像机拍摄到的视觉图像图中硅棒的投影直径,再经中位置平均滤波算法对测得的实时在线硅棒直径进行平均计算,以获得精准的实时在线硅棒直径,与拉之后的实际直径相比,再现性好且精确率高。
74.可有效校正因人员安装导流筒或ccd摄像机不到位使导流筒偏移或ccd摄像机的摄像头偏移而引起的单晶直径测量不合格的发生;也有效防止因人为装配热场不平整而导致单晶硅棒直径检测波动范围大的发生;同时还避免因人为使用测径仪校准差异大而导致单晶直径检测不准确的风险发生。避免ccd摄像头位置偏差导致直径检测超出设定直径区间;实现自动判定、自动校准和自动计算的功能,提高测试的精确度和稳定度。
75.以上对本发明的实施例进行了详细说明,所述内容仅为本发明的较佳实施例,不能被认为用于限定本发明的实施范围。凡依本发明申请范围所作的均等变化与改进等,均应仍归属于本发明的专利涵盖范围之内。