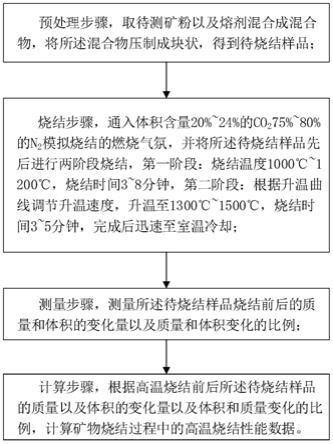
1.本技术涉及领域,具体涉及一种铁矿液相生成比例数据的测定方法以及铁矿烧结设备。
背景技术:2.我国钢铁生产工业发展势头迅猛,钢铁产量已超过10亿吨/年,目前高炉炼铁原料有70%以上依靠烧结工序提供,稳定优质的烧结矿为高炉顺行和提高炼铁效率提供了保证。然而,原料的波动使得烧结生产难以平稳运行,优化配矿方案是解决原料波动的一个有效手段。
3.时至今日,优化配矿研究已经改变了以往只参照化学成分、粒度组成、制粒性能等常温特性对铁矿烧结性能进行评价的方式,更多的考虑铁矿在高温下的烧结行为特性。为了实现科学合理的配矿研究,需要对含铁矿物的基础烧结特性进行研究。
技术实现要素:4.本技术实施例提供一种含铁矿物高温烧结性能测算方法,其能更准确的测算含铁矿物高温条件下烧结性能,为后续配矿方案的优化提供基础。
5.第一方面,本技术实施例提供一种含铁矿物高温烧结性能测算方法,包括如下步骤预处理步骤,取待测矿粉以及熔剂混合成混合物,将混合物压制成块状,得到待烧结样品;烧结步骤,通入体积含量20%~24%的co2以及体积含量75%~80%的n2模拟烧结的燃烧气氛,并将待烧结样品先后进行两阶段烧结,第一阶段:烧结温度1000℃~1200℃,烧结时间3~8分钟,第二阶段:根据升温曲线调节升温速度,升温至1300℃~1500℃,烧结时间3~5分钟,完成后迅速至室温冷却;测量步骤,测量待烧结样品烧结前后的质量和体积的变化量以及质量和体积变化的比例;计算步骤,根据高温烧结前后待烧结样品的质量以及体积的变化量以及体积和质量变化的比例,计算矿物烧结过程中的高温烧结性能数据。
6.根据本技术实施例的一个方面,预处理步骤具体包括筛分待测矿粉,得到粒径0~0.5mm的微矿粉;取熔剂,将微矿粉与熔剂混合均匀,得到混合物;在混合物中加入7~10%质量比例的水,在5~30mpa压力下保压1~5min成型,得到待测样品。
7.根据本技术实施例的一个方面,在烧结步骤之前,还包括预测量步骤,预测量步骤包括取耐热容器以及耐热样品座,测量耐热容器的质量m1和耐热容器的体积v1,测量耐热样品座的体积v2,并测量待烧结样品的质量m3和待烧结样品的体积v3。
8.根据本技术实施例的一个方面,在测量步骤中,待烧结样品烧结完成并冷却后,得到与耐热容器粘结的自由流动部分以及残留在耐热样品座上的烧结残余部分,自由流动部分与耐热容器的结合体为第一测量体,烧结残余部分与耐热样品座为第二测量体;将耐热样品座与耐热容器分离以分离第一测量体以及第二测量体,测量第一测量体的质量m4和第一测量体的体积v4,测量第二测量体的体积v5。
9.根据本技术实施例的一个方面,高温烧结性能数据包括团块体积收缩率lt、自由
流动液相体积lfv、自由流动液相质量lfm、自由流动液相比例lf,计算公式如下:
10.lt=(v2+v3
‑
v5)/v3
×
100%;
11.lfv=v4
‑
v1;
12.lfm=m4
‑
m1;
13.lf=(m4
‑
m1)/m3
×
100%。
14.根据本技术实施例的一个方面,烧结步骤中,第二阶段的升温速度为:80℃~120℃/min。
15.根据本技术实施例的一个方面,在预测量步骤之前,还包括预焙烧步骤,预焙烧步骤包括将待测样品置于900~1100℃环境中预焙烧10~30min。
16.第二方面,本技术实施例提供一种含铁矿物烧结设备,用于烧结如上述的待烧结样品,铁矿烧结设备包括加热装置,包括加热炉以及设于加热炉内的加热管;供气装置,与加热炉内部连通,用于输送烧结气体;进样装置,包括推杆、电动机以及温度传感器,推杆与电动机电连接,温度传感器设于推杆靠近加热炉的一端;控制装置,与加热管、供气装置以及电动机电连接。
17.根据本技术实施例的一个方面,推杆靠近加热炉的一端设有用于固定耐热容器的固定件。
18.根据本技术实施例的一个方面,还包括显示装置,显示装置与控制装置电连接,显示装置能够显示加热炉内的温度。
19.在本技术实施例的含铁矿物高温烧结性能测算方法中,烧结步骤中模拟实际烧结环境,包括烧结温度、烧结气氛以及烧结温度升温速率,更贴合实际烧结情况,能够提升含铁矿物高温烧结性能的测算准确性。
附图说明
20.通过阅读以下参照附图对非限制性实施例所作的详细描述,本技术的其它特征、目的和优点将会变得更明显,其中,相同或相似的附图标记表示相同或相似的特征,附图并未按照实际的比例绘制。
21.图1为根据本技术实施例的含铁矿物高温烧结性能测算方法的流程框图;
22.图2为本技术实施例中的耐热容器以及耐热样品柱的剖视结构示意图;
23.图3为本技术实施例中的待烧结样品烧结后形成自由流动部分的结构示意图;
24.图4为本技术实施例中的含铁矿物烧结设备的结构示意图;
25.图5为申请实施例中的两种含铁矿物不同温度下自由流动液相生成量的理论计算结果图。
具体实施方式
26.为了使本发明的发明目的、技术方案和有益技术效果更加清晰,以下结合具体实施例对本发明进行详细说明。应当理解的是,本说明书中描述的实施例仅仅是为了解释本发明,并非为了限定本发明。
27.为了简便,本文仅明确地公开了一些数值范围。然而,任意下限可以与任何上限组合形成未明确记载的范围;以及任意下限可以与其它下限组合形成未明确记载的范围,同
样任意上限可以与任意其它上限组合形成未明确记载的范围。此外,尽管未明确记载,但是范围端点间的每个点或单个数值都包含在该范围内。因而,每个点或单个数值可以作为自身的下限或上限与任意其它点或单个数值组合或与其它下限或上限组合形成未明确记载的范围。
28.在本文的描述中,需要说明的是,除非另有说明,“以上”、“以下”为包含本数,“一种或多种”中“多种”的含义是两种以上。
29.本发明的上述发明内容并不意欲描述本发明中的每个公开的实施方式或每种实现方式。如下描述更具体地举例说明示例性实施方式。在整篇申请中的多处,通过一系列实施例提供了指导,这些实施例可以以各种组合形式使用。在各个实施例中,列举仅作为代表性组,不应解释为穷举。
30.下面将详细描述本发明的各个方面的特征和示例性实施例。此外,下文中所描述的特征、结构或特性可以以任何合适的方式结合在一个或更多实施例中。
31.目前,关于含铁矿物的烧结性能的相关的测试方法主要有以下几种:
32.现有方法一:将矿粉磨细后根据其化学成分配入熔剂,使团块碱度达到2.0,混合均匀后压制成直径3mm高度3mm的圆柱体,用样品架推入管炉,在空气气氛中以10℃/min的升温速度进行焙烧;用摄像机记录并测量样品高度变化量,得到样品收缩量与温度关系以及液相生成特征温度。然而,该方法未考虑烧结过程各物料接触到熔剂的机会均等,而采用定碱度的方法进行配料,其未考虑气氛和铁矿粒度对液相生成的影响,并且升温速度过慢,与烧结实际不合,对实际烧结配矿的指导意义有限。
33.现有方法二:将铁矿细磨至0~200目后与一定比例消石灰混合压制成三角锥形,在空气气氛中以10
±
2℃/min的升温速度在管炉中进行焙烧,采用摄像机记录并测量升温过程三角锥外形的变化情况来获取铁矿石液相生成特性,得到液相开始生成温度、液相完全生成温度和液相自由流动温度以及12801300℃下液相生成量。该方法也未考虑气氛和铁矿粒度对液相生成的影响,并且升温速度过慢,与实际烧结不符,测试结果对指导实际烧结配矿意义不大。
34.现有方法三:将0~0.5mm的铁矿颗粒破碎至0~200目,配入15%cao纯试剂,在15mpa的压力下压制成直径8mm的圆柱形团块,采用红外快速升温炉模拟烧结升温速度进行快速升温焙烧,并控制气氛为600℃以下空气气氛,600℃以上氮气气氛;冷却后测量生成液相铺展的面积定义为熔体流动指数。这种测试方法对烧结环境的模拟已经非常贴合实际了,但是其仍未考虑矿粉粒度对液相生成的影响;此外,液相铺展的面积除了与液相量有关外,还会受到液相熔体高温粘度的影响,熔体流动指数实际上是一个包含了液相生成量和液相粘度的综合参数,这样一个综合性参数增加了烧结配矿研究的复杂性。
35.目前对于相关研究方法均具有一定的不足,特别是许多方法脱离实际烧结过程,其测量结果和评价体系对实际烧结的指导意义存在争议。因此,一种全新的、科学的、更加符合实际烧结过程的铁矿烧结过程液相生成能力的方法具有十分重要的意义。
36.本技术实施例提供了一种含铁矿物高温烧结性能测算方法。下面结合附图对本技术实施例的含铁矿物高温烧结性能测算方法进行详细描述。
37.图1为本技术实施例的含铁矿物高温烧结性能测算方法的流程框图,如图1所示,本技术实施例的含铁矿物高温烧结性能测算方法包括以下步骤,预处理步骤、烧结步骤、测
量步骤以及计算步骤。预处理步骤包括取待测矿粉以及熔剂混合成混合物,将混合物压制成块状,得到待烧结样品;烧结步骤,通入体积含量20%~24%的co2以及体积含量75%~80%的n2模拟烧结的燃烧气氛,并将待烧结样品先后进行两阶段烧结,第一阶段:烧结温度1000℃~1200℃,烧结时间3~8分钟,第二阶段:根据升温曲线调节升温速度,升温至1300℃~1500℃,烧结时间3~5分钟,完成后迅速至室温冷却;测量步骤包括测量待烧结样品烧结前后的质量和体积的变化量以及质量和体积变化的比例;计算步骤包括根据高温烧结前后待烧结样品的质量以及体积的变化量以及体积和质量变化的比例,计算矿物烧结过程中的高温烧结性能数据。
38.在本技术实施例的含铁矿物高温烧结性能测算方法中,烧结步骤中模拟实际烧结环境,包括烧结温度、烧结气氛以及烧结温度升温速率,更贴合实际烧结情况,能够提升含铁矿物高温烧结性能的测算准确性。
39.在本技术的一些实施例中,预处理步骤具体包括筛分待测矿粉,得到粒径0~0.5mm的微矿粉;取熔剂,将微矿粉与熔剂混合均匀,得到混合物;在混合物中加入7~10%质量比例的水,在5~30mpa压力下保压1~5min成型,得到待测样品。在本技术的实施例中,根据烧结准粒子模型,烧结液相主要由
‑
0.5mm部分黏附粉物料生成,对待测矿粉的粒径进行筛分,将小于0.5mm部分的尾矿粉选出,提升粒子的反应效率,测量结果准确性更高。
40.在本技术的一些实施例中,在烧结步骤之前,还包括预测量步骤,预测量步骤包括取耐热容器1以及耐热样品座2。如图2所示,为本技术实施例中的耐热容器1以及耐热样品柱2的剖视结构示意图。测量耐热容器的质量m1和耐热容器的体积v1,测量耐热样品座的体积v2,并测量待烧结样品的质量m3和待烧结样品的体积v3。
41.在本技术的实施例中,热容器的质量m1、待烧结样品的质量m3可以使用电子天平进行测量,耐热容器的体积v1和耐热样品座的体积v2可以使用阿基米德排水法进行测量,提升测量的准确性。待烧结样品为块状,例如可以是立方体块或者圆柱体块,因此待烧结样品的体积v2可以通过测量其边长或直径之后再进行计算,同样可以得到准确的体积值v3。
42.在本技术的一些实施例中,耐热样品座2包括底座201以及样品座202。底座201与样品座202可拆卸连接。底座201设于耐热容器1中,样品座202设于底座201上。待烧结样品3置于样品座202上。根据上述的实施例,待烧结样品3在高温烧结过程中,产生的自由流动部分沿着样品座202、底座201流动至耐热容器1中,并粘附在耐热容器1的内壁上。如图3所示,为本技术实施例中的待烧结样品烧结后形成自由流动部分的结构示意图。如图3所示,自由流动部分301与耐热容器1结合成一体。烧结残余部分302留在耐热样品座2上。
43.在本技术的一些实施例中,在测量步骤中,待烧结样品烧结完成并冷却后,得到与耐热容器1粘结的自由流动部分以及残留在耐热样品座2上的烧结残余部分,自由流动部分与耐热容器的结合体为第一测量体4,烧结残余部分与耐热样品座为第二测量体5;将耐热样品座与耐热容器分离以分离第一测量体以及第二测量体,测量第一测量体的质量m4和第一测量体的体积v4,测量第二测量体的体积v5。
44.含铁矿物高温烧结过程中,烧结生成的液相在高温状态下呈现流动状态。待测样品置于耐热样品座2上,流动部分将沿着耐热样品座2流至耐热容器中,与其他残余物质进行分离。在耐热容器1中设置耐热样品座2,能够与耐热容器1进行分离,因此便于将流动至耐热容器1中的部分与烧结残余部分进行分离,提升对流动液相部分的测量准确性,以及操
作便利性,有效提升测量效率。
45.在本技术的一些实施例中,底座201与样品座202之间可拆卸连接。烧结完成之后,将样品座202从底座201上拆卸下来,即可将自由流动部分301以及烧结残余部分302彻底分开。上述的结构能够有效提升对自由流动部分301的质量以及体积的测量准确性以及效率。
46.在本技术的一些实施例中,高温烧结性能数据包括团块体积收缩率lt、自由流动液相体积lfv、自由流动液相质量lfm、自由流动液相比例lf,计算公式如下:
47.lt=(v2+v3
‑
v5)/v3
×
100%;
48.lfv=v4
‑
v1;
49.lfm=m4
‑
m1;
50.lf=(m4
‑
m1)/m3
×
100%。
51.根据本技术的实施例,团块体积收缩率lt,计算烧结前后待烧结样品体积的变化比例,体现高温烧结过程中参与反应的含铁氧化物以及熔剂的总体积。自由流动液相体积lfv,计算烧结后待烧结样品的体积变化,自由流动液相质量lfm,计算烧结后待烧结样品的质量变化,上述两个数据能够体现高温烧结过程中,自由流动液相的生成量。自由流动液相比例lf,计算了自由流动部分的质量占待测样品的总质量的比值,反映了待测样品经过高温烧结后能够生成的自由流动相的比例。根据上述的含铁矿物的高温烧结数据,能够为后续优化配矿提供详细、准确的基础资料。
52.在本技术的一些实施例中,烧结步骤中,第二阶段的升温速度为:80℃~120℃/min。根据升温曲线对温度进行控制,能够保证高温烧结过程中烧结温度与实际情况更贴合,提高测算结果的准确性。
53.在本技术的一些实施例中,在预测量步骤之前,还包括预焙烧步骤,预焙烧步骤包括将待测样品置于900~1100℃环境中预焙烧10~30min。焙烧气氛设置为烧结废气成分,900
‑
1100℃时不会有液相生成,此时发生的是结晶水、碳酸盐的分解和固相反应,固相反应较慢,因此加热时间和升温速率对其影响很小,预焙烧可以去除物料烧损并初步形成强度,方便测量工作。
54.本技术实施例还提供一种含铁矿物烧结设备,用于烧结如上述的待烧结样品3。
55.如图4所示,为本技术实施例中的含铁矿物烧结设备的结构示意图。铁矿烧结设备包括加热装置6、供气装置7、进样装置8以及控制装置9。其中,加热装置6包括加热炉601以及设于加热炉601内的加热管602。供气装置7与加热炉601内部连通,用于输送烧结气体。供气装置7通过管道701与加热炉601连通,并将模拟烧结气氛通入加热炉601内。进样装置8,包括推杆801、电动机802以及温度传感器803。推杆801与电动机802电连接,温度传感器803设于推杆801上。耐热容器1设于推杆801上。
56.控制装置9与加热管602、供气装置7以及电动机802电连接。控制装置9可以通知电动机802的运动,从而控制耐热容器1进入、退出加热炉601内。控制装置9与加热管602连接,用于控制加热管602的升温速率以及时间。同时控制装置9可以与温度传感器803连接以获取耐热容器1的实时温度。并且,控制装置9还连接炉内温度传感器901,炉内温度传感器901设于加热炉601内,以获取加热炉601的实时温度情况。
57.在本技术的一些实施例中,推杆801靠近加热炉601的一端设有用于固定耐热容器1的固定件。将耐热容器1固定于推杆801的一端能够保证推杆801带动耐热容器1的运动的
稳定性。
58.在本技术的一些实施例中,还包括显示装置10,显示装置10与控制装置9电连接,显示装置10能够显示加热炉601内的实时温度状况,便于对高温烧结情况进行分析和记录。
59.以下结合具体实施例对本发明作详细说明。
60.对比例
61.以一种典型的磁铁矿精粉和一种褐铁矿粉矿为例,测定不同温度下铁矿的高温烧结性能数据。选取磁铁矿a以及褐铁矿b进行研究。含铁矿物的具体成分见表1。
62.表1
63.矿种tfefeosio2caomgoal2o3loi磁铁矿a63.9929.475.301.790.580.191.61褐铁矿b65.821.541.400.090.061.303.01
64.采用现有方法二对上述的两种含铁矿物的烧结性能进行测试,得到的结果如表2所示。
65.表2
66.矿种测试项目测试结果磁铁矿a液相开始生成温度1280.0 液相完全生成温度1287.5 液相自由流动温度1349.0 1300℃液相生成量70.45褐铁矿b液相开始生成温度1254.0 液相完全生成温度1266.5 液相自由流动温度1281.0 1300℃液相生成量77.83
67.对比例测试结果对于液相生成量和流动性是以温度来表征的而非含量,其使用起来不方便,在后期的优化配矿方案中,对熔剂以及其他物质的添加以及高温烧结的温度控制环节无法起到有效的指导作用。
68.实施例一
69.本实施例采用本技术公开的含铁矿物高温烧结性能测算方法对含铁矿物的烧结性能进行测算。
70.本实施例仍采用磁铁矿a以及褐铁矿b进行研究,其具体成分参见表1。
71.首先,采用热力学计算软件factsage7.0对两种矿不同温度下的自由流动液相生成两进行计算,结果如图5所示。理论计算能得到自由流动液相生成量,图5显示温度越高,液相流动性越好。
72.下面按照本技术实施例中的方法进行含铁矿物的烧结性能数据进行。首先进行预处理步骤,取待测磁铁矿a以及褐铁矿b以及熔剂进行筛分得到粒径0~0.5mm的微矿粉;取熔剂,将微矿粉与熔剂混合均匀,得到混合物;在混合物中加入7~10%质量比例的水,在5~30mpa压力下保压1~5min成型,得到待测样品。再进行预焙烧步骤,预焙烧步骤包括将待测样品置于900~1100℃环境中预焙烧10~30min。焙烧气氛设置为烧结废气成分。
73.然后进行预测量步骤,预测量步骤包括取耐热容器1以及耐热样品座2,并测量耐
热容器的质量m1和耐热容器的体积v1,测量耐热样品座的体积v2,并测量待烧结样品的质量m3和待烧结样品的体积v3。
74.接下来进行烧结步骤,通入体积含量20%~24%的co2以及体积含量75%~80%的n2模拟烧结的燃烧气氛,并将待烧结样品先后进行两阶段烧结,第一阶段:烧结温度1000℃~1200℃,烧结时间3~8分钟,第二阶段:根据升温曲线调节升温速度,升温至1300℃~1500℃,烧结时间3~5分钟,完成后迅速至室温冷却;其中,第二阶段的升温速度为:80℃~120℃/min。
75.然后测量步骤,待烧结样品烧结完成并冷却后,得到与耐热容器粘结的自由流动部分以及残留在耐热样品座上的烧结残余部分,自由流动部分与耐热容器的结合体为第一测量体4,烧结残余部分与耐热样品座为第二测量体5;将耐热样品座与耐热容器分离以分离第一测量体以及第二测量体,测量第一测量体的质量m4和第一测量体的体积v4,测量第二测量体的体积v5。
76.计算步骤,根据高温烧结前后待烧结样品的质量以及体积的变化量以及体积和质量变化的比例,计算矿物烧结过程中的高温烧结性能数据。
77.具体的,高温烧结性能数据包括团块体积收缩率lt、自由流动液相比例lf,计算公式如下:
78.lt=(v2+v3
‑
v5)/v3
×
100%;
79.lf=(m4
‑
m1)/m3
×
100%。
80.对上述两种含铁矿物采用本技术中的含铁矿物高温烧结性能测算方法进行测算,结果见表2。从表2中可以看出,随着温度的升高,总液相生成比例lt增大,自由流动液相比例lf也增大,这与上述的理论计算结果相符,说明本技术中的测试方法准确有效。
81.对比两种不同的矿可以看出,褐铁矿b的液相生成能力优于磁铁矿a。
82.表2
[0083][0084]
上述的测试方法更加贴近理论计算结果以及实际生产的结果,考虑了升温速率、加热温度以及燃烧气氛对烧结性能的影响。
[0085]
依照本技术如上文所述的实施例,这些实施例并没有详尽叙述所有的细节,也不限制该申请仅为所述的具体实施例。显然,根据以上描述,可作很多的修改和变化。本说明书选取并具体描述这些实施例,是为了更好地解释本技术的原理和实际应用,从而使所属技术领域技术人员能很好地利用本技术以及在本技术基础上的修改使用。本技术仅受权利要求书及其全部范围和等效物的限制。