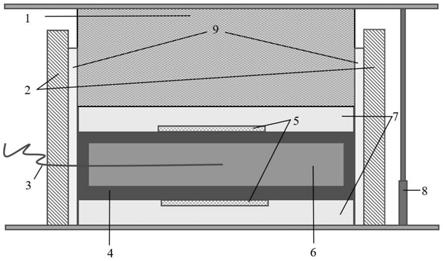
1.本发明涉及材料热物性测技术领域,特别是涉及一种树脂热膨胀系数和固化收缩率测量装置及方法。
背景技术:2.树脂在固化过程中,由于分子聚合形成三维网状结构,导致树脂发生收缩;同时在热流的作用下,树脂基体发生热膨胀,在加热条件下树脂基体发生快速的化学反应,反应放出大量热量,导致温度场发生快速变化,因此影响了反应速率的控制,树脂的热应变和固化收缩应变与树脂的热膨胀系数和固化收缩率密切相关。由于固化过程同时存在热膨胀和固化收缩,且参数不仅随温度发生变化,还会随固化度发生变化,给热膨胀系数和固化收缩率的测量带来困难。
3.于20世纪下半叶至今,针对热固性树脂主要形成了两大测量方法:直接体积测量法和非直接体积测量法。直接体积测量法包含毛细管法、重量法和柱塞式方法;非直接体积测量法主要包含dma、tma、流变仪、比重瓶、fbg、超声波、激光束扫描法、应变仪等方法。其中,毛细管法通过目测读数,由于不能自动输出数据,测量精度受人为因素影响;dma和tma仅能测量已经开始固化后的样品,不利于区分热膨胀与化学收缩,fbg、超声波和应变仪等方法受到树脂与容器壁的粘附、树脂温度控制的缺乏与测量容器内杂质影响,测量结果存在一定误差。
4.上述研究只能单一地获得树脂的固化收缩率,或者树脂在非固化交联阶段的热膨胀系数和固化收缩率,不能同时获得树脂固化过程的热膨胀系数和固化收缩率;重要的是,树脂在固化过程中的任一时刻,热膨胀与化学收缩是同时存在的,如何将热膨胀与化学收缩正确分离开来并准确测量将是研究的重点。且研究表明,固化收缩率与固化度是线性相关的函数,仪器在测量基体收缩的基础上额外需要热分析仪器,如单独进行dsc实验以得到树脂的固化度变化,有可能会有一定的误差。此外,复合材料实际固化过程常伴随有压力,其对树脂的热膨胀系数和固化收缩率有一定的影响。
技术实现要素:5.基于此,本发明的目的是提供一种树脂热膨胀系数和固化收缩率测量装置及方法,
6.为实现上述目的,本发明提供了如下方案:
7.一种树脂热膨胀系数和固化收缩率测量装置,包括:硅橡胶模具、活塞、加热板、热流计、热电偶、树脂试样、位移传感器、数据采集系统和计算机;
8.所述硅橡胶模具用于放置所述树脂试样,所述活塞设置在所述硅橡胶模具上方,用于对所述硅橡胶模具施加压力;所述加热板用于对所述树脂试样进行加热;所述热流计用于测量任一时刻通过所述树脂试样上表面和下表面的热流;所述热电偶设置在所述树脂试样的中心,用于测量任一时刻树脂试样中心截面处的温度变化量;所述位移传感器用于
测量所述树脂试样的厚度变化量;所述数据采集系统分别与所述热流计、所述位移传感器和所述热电偶连接,用于采集所述热流、所述厚度变化量以及所述中心截面处的温度;所述计算机与所述数据采集系统连接,用于根据所述热流、所述厚度变化量以及所述中心截面处的温度变化量计算树脂热膨胀系数和固化收缩率。
9.进一步地,还包括:试样环,用于放置所述硅橡胶模具。
10.进一步地,还包括绝热壁,所述绝热壁设在所述试样环两侧。
11.进一步地,所述加热板包括第一加热板和第二加热板,所述第一加热板设置在所述硅橡胶模具的上表面,用于对所述树脂试样的上表面进行加热;所述第二加热板设置在所述硅橡胶模具的下表面,用于对所述树脂试样的下表面进行加热;
12.进一步地,所述热流计包括第一热流计和第二热流计,所述第一热流计设置在所述第一加热板下表面的中心,用于测量任一时刻通过所述树脂试样上表面的热流,所述第二热流计设置在所述第二加热板上表面的中心,用于测量任一时刻通过所述树脂试样下表面的热流。
13.本发明还提供了一种树脂热膨胀系数和固化收缩率测量方法,所述方法应用于上述的树脂热膨胀系数和固化收缩率测量装置,所述方法包括:
14.对树脂试样进行加热并测量任一时刻通过所述树脂试样上表面和下表面的热流;
15.对所述树脂试样试压并测量所述树脂试样的厚度变化量;
16.测量任一时刻树脂试样中心截面处的温度变化量;
17.根据通过所述树脂试样上表面和下表面的热流,计算树脂试样的固化度;
18.根据所述温度变化量、所述厚度变化量以及所述固化度计算树脂试样的热膨胀系数;
19.根据所述热膨胀系数以及所述固化度的变化量计算树脂试样的固化收缩率。
20.进一步地,所述根据所述温度变化量、所述厚度变化量以及所述固化度计算树脂试样的热膨胀系数,具体包括:
21.根据所述温度变化量、所述厚度变化量计算未开始固化时树脂试样的热膨胀系数以及固化完成后树脂试样的热膨胀系数;
22.根据所述固化度、未开始固化时树脂试样的热膨胀系数以及固化完成后树脂试样的热膨胀系数,计算树脂试样的热膨胀系数。
23.进一步地,固化度的计算公式如下:
[0024][0025]
式中:α(t)为单位时刻树脂试样的固化度;φ为t时刻通过试样上下表面的热流;δh
tot
为树脂固化反应过程中通过其表面的总热流量。
[0026]
进一步地,热膨胀系数的计算公式如下:
[0027]
cte(α)=cte
uncured
(1
‑
α)+αcte
rubbery
[0028]
[0029][0030]
式中:α为t时刻树脂试样的固化度;cte
uncured
为未开始固化时树脂试样的热膨胀系数;cte
rubbery
为固化完成后树脂试样的热膨胀系数;δd1、δd2为树脂在未开始固化阶段和固化完成阶段的厚度变化量;d1、d2为树脂试样在未开始固化阶段和固化完成阶段的初始厚度值;δt1、δt2为树脂试样在未开始固化阶段和固化完成阶段的温度变化量;cte(α)为固化过程中某时刻树脂试样的热膨胀系数。
[0031]
进一步地,固化收缩率的计算公式如下:
[0032][0033]
式中:cs为树脂的固化收缩率;d
i
为试样的初始厚度;d(t,α)为固化过程中任一时刻树脂试样的厚度;δt、δα为一个采样时间内试样温度和固化度的变化量。
[0034]
根据本发明提供的具体实施例,本发明公开了以下技术效果:
[0035]
(1)本发明可以在一次实验后,通过对测量得出的结果进行分析处理,一次性得到树脂试样的固化度、热膨胀系数、固化收缩率;并且仪器可以在恒压以及变压力条件下对树脂样品进行测量,这样就实现了在短时间内测量多个参数的目标,相比单独使用一套设备测定一个参数具有显著优势;
[0036]
(2)本发明基于柱塞式方法进行了改进,通过设备上下端面热流传感器和温度传感器确定树脂的固化度;通过位移传感器获得树脂体积变化,并将树脂体积变化分为纯热膨胀、热
‑
化学和纯橡胶态热膨胀三个阶段,直接获得第一和第三阶段的热膨胀系数,并通过假设热膨胀系数在热
‑
化学阶段随固化度线性变化,分离热
‑
化学阶段的热膨胀和固化收缩作用,从而求解固化收缩率随固化度的变化规律,解决了难以区分树脂固化过程热膨胀和固化收缩的难题;此外,相较于fbg、激光束扫描法等光学方法测量过程中使用的非常专业且昂贵的仪器且对周围环境有严格要求,节约了实验成本;
[0037]
(3)本发明测量方法具有结构兼容性良好、功耗低、操作简单等特点,此外,本发明装置中测试的样品为树脂,但是本发明方法适用于测量其它物质的热膨胀系数,适用范围广。此外,本发明中测量试样中心截面温度采用的超细小k型热电偶厚度仅为0.02mm,对实验过程扰动性极小,这提高了实验测试精度。
附图说明
[0038]
为了更清楚地说明本发明实施例或现有技术中的技术方案,下面将对实施例中所需要使用的附图作简单地介绍,显而易见地,下面描述中的附图仅仅是本发明的一些实施例,对于本领域普通技术人员来讲,在不付出创造性劳动性的前提下,还可以根据这些附图获得其他的附图。
[0039]
图1为本发明实施例树脂热膨胀系数和固化收缩率测量装置的示意图;
[0040]
图2为本发明实施例树脂热膨胀系数和固化收缩率测量方法的流程图;
[0041]
图3为本发明实施例树脂试样固化过程中厚度变化示意图。
具体实施方式
[0042]
下面将结合本发明实施例中的附图,对本发明实施例中的技术方案进行清楚、完整地描述,显然,所描述的实施例仅仅是本发明一部分实施例,而不是全部的实施例。基于本发明中的实施例,本领域普通技术人员在没有做出创造性劳动前提下所获得的所有其他实施例,都属于本发明保护的范围。
[0043]
本发明的目的是提供一种树脂热膨胀系数和固化收缩率测量装置及方法,其测量原理是在对样品施加给定温度和压力的条件下,使用热流计测量薄型圆柱试样上下热流密度,并对测量结果进行处理后得到树脂固化度;此外,在测量热流的同时通过安装在样品模具一侧的位移传感器对树脂样品厚度变化进行测量,通过对测量的数据进行处理可以计算得到树脂固化过程中的热膨胀系数和固化收缩率。
[0044]
为使本发明的上述目的、特征和优点能够更加明显易懂,下面结合附图和具体实施方式对本发明作进一步详细的说明。
[0045]
本发明用于研究在恒压条件下固化期间和/或固化后的纯热固性树脂和复合材料。此外,可以针对大块样品(厚度5~10毫米、直径100毫米)进行实验。该仪器在接近工业环境的条件下工作(即模腔内可调压力高达100kn、温度高达150℃)。
[0046]
如图1所示,树脂热膨胀系数和固化收缩率测量装置,包括:硅橡胶模具4(薄圆柱形硅橡胶模具)、活塞1、加热板7、热流计5、热电偶3(中心超薄型热电偶)、树脂试样6(薄圆柱型树脂试样)、位移传感器7、数据采集系统和计算机。
[0047]
所述硅橡胶模具4((直径100mm,厚度12mm))用于放置所述树脂试样6,其整体是可形变但几乎不可压缩的,即能盛放在室温下为黏稠态的树脂样品,又保证了压力的传递。
[0048]
所述活塞1设置在所述硅橡胶模具4上方,所述活塞1与压机(压力范围0~100kn)连接,用于给圆柱形硅橡胶模具4施加压力,进而给树脂样品施加给定压力。
[0049]
所述加热板7用于对所述树脂试样6进行加热;使树脂试样在恒定或变温度下固化。所述加热板包括第一加热板和第二加热板,所述第一加热板设置在所述硅橡胶模具的上表面,用于对所述树脂试样的上表面进行加热;所述第二加热板设置在所述硅橡胶模具的下表面,用于对所述树脂试样的下表面进行加热。
[0050]
所述热流计5用于测量任一时刻通过所述树脂试样6上表面和下表面的热流;所述热流计5包括第一热流计和第二热流计,所述第一热流计设置在所述第一加热板下表面的中心,用于测量任一时刻通过所述树脂试样上表面的热流,所述第二热流计设置在所述第二加热板上表面的中心,用于测量任一时刻通过所述树脂试样下表面的热流。
[0051]
所述热电偶3(测温范围
‑
20~200℃,热电偶厚度为0.02mm)设置在所述树脂试样6的中心,用于测量任一时刻树脂试样6中心截面处的温度变化量。
[0052]
所述位移传感器7(测量范围0~50.00mm,精度0.01mm)安装于腔体一侧,用于测量所述树脂试样6的厚度变化量;所述数据采集系统分别与所述热流计5、所述位移传感器7和所述热电偶3连接,用于采集所述热流、所述厚度变化量以及所述中心截面处的温度;数据采集系统采样频率≤1hz,这保证了测量精度,测量数据将实时显示在仪器面板上。
[0053]
所述计算机与所述数据采集系统连接,用于根据所述热流、所述厚度变化量以及所述中心截面处的温度变化量计算树脂热膨胀系数和固化收缩率。
[0054]
数据采集系统、计算机与装置间通过rs232端口进行连接。
[0055]
本发明提供的装置还包括试样环9和绝热壁2,试样环9用于放置所述硅橡胶模具4,所述绝热壁2设在所述试样环两侧。绝热壁2用于隔绝圆柱形硅橡胶模具侧面的热量传递,假设测量体内部传热是一维的,样品厚度范围内的温度场和固化度场都被认为一维的。此外,绝热壁同时保证树脂样品在两侧不存在形变,由于不可压缩的弹性体腔,受压的树脂基体表面积不会发生变化。不锈钢试样环在横向的形变是可以忽略不计的,因此,测得的厚度与样品体积及其变化直接相关,故可以用树脂的纵向形变即厚度变化来表征树脂的膨胀量。
[0056]
上述装置的使用方法包括以下几个步骤:
[0057]
(1)连接实验电路
[0058]
开始测试前,将测试仪器、数据采集系统和计算机均已接通电源,并应首先确认以下各事项:
[0059]
rs232接口通信传输正常;
[0060]
活塞能够正常给模具施加压力;
[0061]
上下加热板能够正常升温与降温;
[0062]
装置仪表上中心热电偶、热流计、压力传感器、位移传感器示数正常。
[0063]
确认无误后方可开始进行测试;
[0064]
(2)仪器空载消除误差
[0065]
由于树脂被封装在薄圆柱型硅橡胶模具并放置在不锈钢试样环中,必须先从实验数据中去除实验过程中可能出现的硅胶囊的收缩和热膨胀以及不锈钢试样环、热流传感器和位移传感器的热膨胀的影响。为此,在与树脂实验相似的实验条件下,在同样尺寸的薄圆柱型硅橡胶片上进行了实验。从记录的实验数据中减去施加压力循环中硅橡胶片的厚度变化,即可得到仅与树脂有关的厚度变化。
[0066]
(3)树脂的充注及放置
[0067]
将树脂从保温箱(≤5℃)中取出,为保证树脂与模具贴合紧密,避免产生气泡而影响测量效果,采用真空注射的方法将50ml待测树脂注入薄圆柱形硅橡胶模具中,注射完成后将超细小k型热电偶插入模具中心位置。确保模具密封性后将其放置在测试装置不锈钢试样环中;
[0068]
(4)树脂样品加压
[0069]
树脂样品放置好后,启动压机,压机带动活塞给样品施加给定压力。在本实验过程中,为测量真实工艺条件下树脂固化过程中热膨胀系数和固化收缩率,分别施加以7.85kn、15.7kn、23.55kn(对应压强为1mpa、2mpa、3mpa)的压力;
[0070]
(5)树脂样品加热
[0071]
加压完成后,开启加热开关,按照给定温度对树脂样品进行加热,随着温度升高,树脂将开始发生固化反应。在本实验过程中,为测量真实工艺条件下树脂固化过程中热膨胀系数和固化收缩率,分别施加以100℃、120℃、150℃的温度;
[0072]
(6)数据采集
[0073]
上下加热板开始加热后便开始数据采集,在整个测试过程中,树脂样品受到的压力、树脂样品中心位置处的温度、通过树脂样品上下表面的热流和树脂样品的厚度变化量将实时显示在仪器面板上,且通过数据采集系统记录并存储于计算机中。5~8小时(固化时
间取决于树脂固化温度)后,树脂固化完成,中止数据采集,测试结束。
[0074]
如图2所示,本发明还提供了一种树脂热膨胀系数和固化收缩率测量方法,所述方法应用于上述的树脂热膨胀系数和固化收缩率测量装置,所述方法包括:
[0075]
步骤101:对树脂试样进行加热并测量任一时刻通过所述树脂试样上表面和下表面的热流。
[0076]
步骤102:对所述树脂试样试压并测量所述树脂试样的厚度变化量。
[0077]
步骤103:测量任一时刻树脂试样中心截面处的温度变化量。
[0078]
步骤104:根据通过所述树脂试样上表面和下表面的热流,计算树脂试样的固化度。
[0079]
在整个固化过程中,采集试样中间截面位置处温度变化与通过树脂试样上下表面的热流变化数据,通过对上下表面热流差积分得到反应总放热量,用某时刻放热量占总固化过程总放热量的百分比来表述树脂样品的固化程度。所述树脂试样固化度的计算公式如下:
[0080][0081]
式中:α(t)为单位时刻树脂试样的固化度;φ为t时刻通过试样上下表面的热流;δh
tot
为树脂固化反应过程中通过其表面的总热流量。
[0082]
步骤105:根据所述温度变化量、所述厚度变化量以及所述固化度计算树脂试样的热膨胀系数。具体包括:根据所述温度变化量、所述厚度变化量计算未开始固化时树脂试样的热膨胀系数以及固化完成后树脂试样的热膨胀系数;根据所述固化度、未开始固化时树脂试样的热膨胀系数以及固化完成后树脂试样的热膨胀系数,计算树脂试样的热膨胀系数。
[0083]
在整个固化过程中,使用位移传感器测量实验过程中树脂的厚度变化,而由于反应过程中即涉及到物理膨胀过程也涉及到化学收缩过程,故将树脂的体积变化分为纯热膨胀、热
‑
化学和纯橡胶态热膨胀三个阶段。结合步骤104中求得的树脂固化度,通过混合定律建立热
‑
化学阶段树脂样品热膨胀系数与固化度、纯热膨胀系数和纯橡胶态热膨胀系数之间的数学关系式,进而得到树脂在整个固化过程中的固化度、热膨胀系数和固化收缩率的变化规律。所述树脂试样热膨胀系数和固化收缩率的计算公式如下:
[0084]
cte(α)=cte
uncured
(1
‑
α)+αcte
rubbery
[0085][0086][0087]
式中:α为t时刻树脂试样的固化度;cte
uncured
为未开始固化时树脂试样的热膨胀系数;cte
rubbery
为固化完成后树脂试样的热膨胀系数;δd1、δd2为树脂在未开始固化阶段和固化完成阶段的厚度变化量;d1、d2为树脂试样在未开始固化阶段和固化完成阶段的初始厚度值;δt1、δt2为树脂试样在未开始固化阶段和固化完成阶段的温度变化量;cte(α)为固化过程中某时刻树脂试样的热膨胀系数。
[0088]
步骤106:根据所述热膨胀系数以及所述固化度的变化量计算树脂试样的固化收缩率。
[0089]
树脂在固化过程中的厚度变化主要是由热膨胀与固化收缩两个因素导致的,由实验过程容易知道树脂的实时厚度,那么将树脂样品实时厚度减去树脂样品初始厚度和树脂样品热膨胀量即可求解树脂的固化收缩量,进而求得树脂的固化收缩率。所述树脂试样固化收缩率的计算公式如下:
[0090][0091]
式中:cs为树脂的固化收缩率;d
i
为试样的初始厚度;d(t,α)为固化过程中任一时刻树脂试样的厚度;δt、δα为一个采样时间内试样温度和固化度的变化量。
[0092]
下面对树脂固化度、热膨胀系数和固化收缩率数据处理方法进行详细介绍。
[0093]
固化度:
[0094]
薄圆柱型硅橡胶模具侧边采用绝热措施,假设测量体内部传热是一维的,样品厚度范围内的温度场和固化度场都被认为一维的。由于圆柱形样品的两侧是绝热的,可以通过测量每一时刻通过上表面的热流密度和下表面的热流密度,通过热流差来表示每一时刻通过样品的热流密度:
[0095]
φ=φ1‑
φ2[0096]
式中:φ为单位时刻通过树脂试样上下表面的热流差;φ1为通过试样上表面的热流,由第一热流计实时记录;φ2为通过试样下表面的热流,由第二热流计实时记录。
[0097]
整个固化过程的热流量可以通过对热流曲线进行积分确定:
[0098][0099]
式中:t为树脂固化反应总时间,δh
tot
为树脂固化反应过程中通过其表面的总热流量。
[0100]
由于热固性树脂的固化反应只和温度历史相关,所以可将任意时刻的热流量与反应总热流量的比值定义为其固化度,以表示反应进行的程度:
[0101][0102]
式中:α(t)为单位时刻树脂试样的固化度;φ为t时刻通过试样上下表面的热流;δh
tot
为树脂固化反应过程中释放的总热量。
[0103]
热膨胀系数:
[0104]
树脂固化通常一定在一定固化制度下进行,在树脂样品发生化学反应的过程中,体系的温度不断升高直到反应基本结束。在整个反应过程中,树脂基体会由于受热发生膨胀,这种膨胀表现为树脂体积的变化:
[0105][0106]
式中:cte为热膨胀系数;δv为树脂样品体积变化量;v为树脂样品初始体积大小。
[0107]
在的实验中,树脂样品是一个薄型圆柱体,实验过程中,样品侧面被绝热壁所限
制,故其表面积并不发生变化,故可以仅用厚度变化来表征树脂的体积膨胀:
[0108][0109]
式中:δd为树脂样品厚度变化量,d为树脂样品初始厚度,s为薄圆柱型树脂样品表面积。
[0110]
加热板对树脂样品进行加热,树脂在受热后会逐渐开始发生固化反应,随着固化反应的进行,树脂会由未固化的液体状态逐渐转变为胶态,固化反应完成后树脂将完全转变为橡胶态,如此一来,可以将树脂的体积膨胀(厚度变化)随温度的变化分为如图3所示的三段曲线:
[0111]
ab(纯热膨胀阶段):化学反应并未开始,树脂随温度升高而膨胀,这是一个纯物理变化的过程。故ab段的热膨胀系数即是该段曲线的斜率与初始厚度的比值;
[0112]
bc(热
‑
化学阶段):由于体系的温度的持续升高,除了热膨胀外,还伴随着化学反应的进行而出现的固化收缩;
[0113]
cd(纯橡胶热膨胀阶段):树脂完全固化而处于橡胶态。所以ab段树脂的体积膨胀系数即是该段曲线的斜率与初始厚度的比值。
[0114]
在单一的实验条件下,树脂的化学收缩是不易测定的,而如图3所示,可以通过混合定律将bc段的热膨胀系数表示为下式:
[0115]
cte(α)=cte
uncured
(1
‑
α)+αcte
rubbery
[0116][0117][0118]
式中:α为t时刻树脂试样的固化度;cte
uncured
为未开始固化时树脂试样的热膨胀系数;cte
rubbery
为固化完成后树脂试样的热膨胀系数;δd1、δd2为树脂在未开始固化阶段和固化完成阶段的厚度变化量;d1、d2为树脂试样在未开始固化阶段和固化完成阶段的初始厚度值;δt1、δt2为树脂试样在未开始固化阶段和固化完成阶段的温度变化量;cte(α)为固化过程中某时刻树脂试样的热膨胀系数。
[0119]
将每一时刻的树脂温度变化量δt
i
与厚度变化量δd
i
结合每一时刻树脂试样固化度α与树脂试样原长d
i
代入上式进行计算后即可得到树脂在整个固化过程中的热膨胀系数值。值得注意的是,树脂试样的温度变化量δt
i
的大小取决于数据采集系统的采样频率,即在多少时间间隔内记录一次数据,这将最终影响测量结果,本实验中采样频率≤1hz,实验结果具有较高的精度。
[0120]
固化收缩率:
[0121]
如图3所示,树脂试样在热
‑
化学阶段的厚度变化是由于受热膨胀和固化收缩两个因素影响的,一旦确定了热
‑
化学阶段的树脂热膨胀量,就容易求解此时的固化收缩量。在热
‑
化学阶段,树脂试样的固化收缩量是通过从实验厚度中减去热膨胀量得到的:
[0122]
d
i
csδα=d(t,α)
‑
d
i
(1+cte(α)δt)
[0123]
式中:d
i
为试样的初始厚度;d(t,α)为固化过程中任一时刻树脂试样的厚度;cte(α)为树脂固化过程中任一时刻的热膨胀系数;δt、δα为一个采样时间内试样温度和固化
度的变化量;树脂的固化收缩率定义为:
[0124][0125]
式中:cs为树脂的固化收缩率,这是一个无量纲量。
[0126]
将每一时刻的树脂温度变化量δt与固化度的变化量δα结合每一时刻树脂试样原长d
i
与热膨胀系数cte(α)代入上式进行计算后即可得到树脂在整个固化过程中的固化收缩率值。
[0127]
根据本发明提供的具体实施例,本发明公开了以下技术效果:
[0128]
(1)现有的技术可以通过使用相关仪器单独对固化度、热膨胀和弹性模量及导热系数进行单独测量。然而,想要一一对这些参数的进行测定需要使用许多仪器,这是非常耗时的。本发明的一大突出特点就是可以在一次实验后,通过对测量得出的结果进行分析处理,一次性得到树脂试样的固化度、热膨胀系数、固化收缩率;并且仪器可以在恒压以及变压力条件下对树脂样品进行测量,这样就实现了在短时间内测量多个参数的目标,相比单独使用一套设备测定一个参数具有显著优势;
[0129]
(2)本发明基于柱塞式方法进行了改进,通过设备上下端面热流传感器和温度传感器确定树脂的固化度;通过位移传感器获得树脂体积变化,并将树脂体积变化分为纯热膨胀、热
‑
化学和纯橡胶态热膨胀三个阶段,直接获得第一和第三阶段的热膨胀系数,并通过假设热膨胀系数在热
‑
化学阶段随固化度线性变化,分离热
‑
化学阶段的热膨胀和固化收缩作用,从而求解固化收缩率随固化度的变化规律,解决了难以区分树脂固化过程热膨胀和固化收缩的难题;此外,相较于fbg、激光束扫描法等光学方法测量过程中使用的非常专业且昂贵的仪器且对周围环境有严格要求,节约了实验成本;
[0130]
(3)针对航空航天领域复合材料热物性参数测量,本发明测量方法具有结构兼容性良好、功耗低、操作简单等特点,此外,本发明装置中测试的样品为树脂,但是本发明方法适用于测量其它物质的热膨胀系数,适用范围广。此外,本发明中测量试样中心截面温度采用的超细小k型热电偶厚度仅为0.02mm,对实验过程扰动性极小,这提高了实验测试精度。
[0131]
本说明书中各个实施例采用递进的方式描述,每个实施例重点说明的都是与其他实施例的不同之处,各个实施例之间相同相似部分互相参见即可。
[0132]
本文中应用了具体个例对本发明的原理及实施方式进行了阐述,以上实施例的说明只是用于帮助理解本发明的方法及其核心思想;同时,对于本领域的一般技术人员,依据本发明的思想,在具体实施方式及应用范围上均会有改变之处。综上所述,本说明书内容不应理解为对本发明的限制。