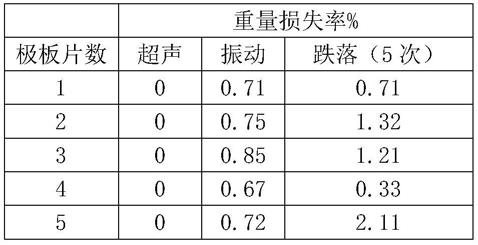
1.本发明属于铅酸蓄电池领域,具体涉及一种用于评价铅酸电池固化质量或/和评价失效电池正极活性物质软化脱落。
背景技术:2.铅酸电池极板固化是蓄电池极板生产过程中重要的工艺过程,它的作用主要是使活性物质与活性物质形成稳定的结构,同时板栅氧化与活性物质粘合形成界面良好的结构等,活性物质的结构和结合层直接影响几乎电池所有的性能,特别是使用寿命。因此选择合适的评价固化质量的方法至关重要。目前评价固化质量好坏的主要采用跌落法,让固化后的极板从固定的高度跌落下来,计算重量损失率。但这种方法误差较大,每个人的操作和跌落高度的偏差均会影响试验结果。因此需要一种规避人为因素导致误差的评价固化质量好坏的方法。
3.同时,铅酸电池的失效解剖分析对于铅酸电池的技术改进是很关键的。目前铅酸电池的失效模式主要为正极活性物质脱落,极板经解剖取出后,一部分结合很差的活性物依然吸附在极板上,一般通过水洗的方式冲刷掉,然后技术人员的经验判断,为定性判断,无法准确比较,主观容易造成判断失误,且水洗容易造成极板正常结构的破坏,影响失效模式的结论判断,因此需要一种定量判断活性物质软化脱落程度的方法。
技术实现要素:4.本发明的目的是克服现有技术的上述不足,而提供一种评价铅酸电池质量的定量方法,用来定性或定量判断固化质量/活性物质的软化脱落程度,减少人为因素。
5.本发明的技术方案是:
6.一种评价铅酸电池质量的定量方法,包括以下步骤:
7.取样数片待评价的极板;
8.各片待评价的极板重量记为w0;
9.将待评价的极板经密封容器置于振动台上,待评价的极板在密封容器内平放,不可叠放;振动台测试选用正弦驻留的方式进行振动,起始频率为≥60hz,定加速度为≥82hz,加速度峰值为≥10g,共振动≥10min;
10.将振动后的各片待评价的极板称重,记为w1;
11.计算各片待评价的极板重量损失率w%=(w0-w1)/w0;
12.根据各片待评价的极板重量损失率取平均值。
13.当用于评价铅酸电池固化质量时:所述待评价的极板为固化后的极板,取样的固化后的极板置于密封环境保存;
14.当用于评价失效电池正极活性物质软化脱落时:所述待评价的极板为失效的正极板;取样方法为:按照电池的解剖流程,切除贮存在常温下的失效的电池的电池盖,然后从电池槽的中间单格处取样数片失效的正极板,常温即环境温度18-28℃;取样的失效的正极
的保存方法:将取样的失效的正极平泡在水中,并放置在室温条件下,室温为18-28℃,空气温度18-28℃,即gb/t 2918规定的标准环境,存储时间不超过10天;振动前用agm隔板纸擦拭失效的正极表面至失效的正极表面无水痕迹。
15.当用于评价失效电池正极活性物质软化脱落时:将振动后的待评价的极板用agm隔板纸擦拭表面至待评价的极板表面无水痕迹,称重,记为w1。
16.所述失效的电池在常温下的生产场所、使用场所或在库房内放置。
17.所述密封容器为白色长方体pp塑料槽,塑料槽上开口处用pe膜密封。
18.塑料槽的高度大于10cm,塑料槽的高度大于10cm,以免极板在振动的过程中飞出,宽和长根据极板的尺寸自行选择,长和宽大于极板5cm即可,根据振动台确定,待评价的生极板不可叠放,平放在塑料槽中,并用胶带固定住pe膜,防止振动时溅出的液体或固体对振动台造成腐蚀。所述的白色塑料槽放在振动台上,用扳手拧紧螺丝将其固定。
19.所述振动台测试选用正弦驻留的方式进行振动,起始频率为60hz,定加速度为82hz,加速度峰值为10g,共振动10min。
20.所述振动台采用蓄电池检测专用振动台,东菱振动台。
21.待评价的生极板的数量为至少10片,可用来做msa分析。
22.铅酸电池固化工艺是铅酸电池至关重要的生产工艺,但一直没有合适的评价固化质量的方法。传统的方法由于人为操作因素误差较大,可以比较质量差异较大的极板,但是无法准确评价质量相当的极板。本发明与现有评价固化质量好坏的跌落方法相比,人为操作误差较小。本发明可用来定性或定量判断固化质量,规避人为因素导致误差,评价生极板固化质量的好坏的数据稳定可靠。
23.铅酸电池的失效分析作为铅酸电池技术开发的重要组成部分,准确的判断电池的失效模式和失效程度对于铅酸电池下一次改进和技术积累至关重要。其中正极活性物质软化脱落是目前铅酸电池最常见的失效模式。正极活性物质软化脱落指的是正极活性物质与板栅或者活性物质与活性物质之间结合松散、连接较差,并有活性物质脱落下来的一种失效模式。常规的评价活性物质软化脱落均为定性判断,主要靠技术人员肉眼判断,或者在一定的水压下冲洗,前者存在主观误判,后者不好控制,易造成连接正常的活性物质冲洗脱落,造成结果偏差。判断失误导致改进或者技术积累存在偏差,带来一定的损失。现有技术中活性物质软化脱落的程度主要靠肉眼判断,且均为定性判断,主观容易造成判断失误,影响失效模式的结论判断。本发明用于评价失效电池正极活性物质软化脱落时,摒弃人为或水洗的方式,采用振动的方法定性或定量分析活性物质的软化程度。本发明采用振动台振动待评价的极板,不采用超声振动。超声振动将功率超声频源的声能转换成机械振动,通过清洗槽壁将超声波辐射到槽子中的清洗液。由于受到超声波的辐射,使槽内液体中的微气泡能够在声波的作用下从而保持振动,从而对固体表面进行擦洗,振动主要集中在固体的表面。对于极板来说,基本上所有的颗粒物质或多或少均会被超声冲洗下来,因此会对极板的表面造成影响,也会带来误差。超声对于较厚的极板无法作用到板栅与活性物质界面,较薄的极板可以。同时,超声对于活性物质软化脱落不是特别严重的极板无法评价。本发明减少人为因素,定量分析活性物质的软化脱落程度。
具体实施方式
24.本发明用于评价铅酸电池固化质量时,适用的范围为固化后的正极板,具体内容如下:
25.取样固化后的正极板(即生极板),若不能马上进行测试,取样固化后的正极板密封保存即可,生极板不用浸水。
26.本发明的取样固化后的正极板取至少10片,固化后的正极板重量记为w0。
27.本发明取样好的固化后的正极板立即进行后续的测试。
28.本发明的测试方法:置于白色长方体pp塑料槽中,塑料槽的高度大于10cm,以免生极板在振动的过程中飞出,宽和长根据极板的尺寸自行选择,生极板平放不可叠放,白色塑料槽上开口处用pe膜密封住,并用胶带固定住pe膜,防止振动时溅出的液体或固体对振动台造成腐蚀。
29.白色塑料槽放在振动台上,用扳手拧紧螺丝将其固定。
30.本发明所用的振动台采用蓄电池检测专用振动台。
31.本发明所用的振动台测试选用正弦驻留的方式进行振动,起始频率为60hz,定加速度为82hz,加速度峰值为10g,共振动10min。振动结束后,用扳手拧松螺丝,将白色塑料槽取下,将其中的极板取出,若无极板需要振动,清理振动台。一次可振动1-4块生极板。
32.接下来进入如下步骤:
33.(1)将振动后的生极板称重,记为w1;
34.(2)计算单片生极板重量损失率w%=(w0-w1)/w0;
35.(3)按照步骤(2)计算每片生极板的重量损失率,然后取平均,比较数值大小,数值越低,固化质量越好。
36.下面以超声对比例、跌落法对比例与本发明的实施例进行对比,对本发明作进一步说明。
37.超声对比例一:
38.取1片生极板,重量记为w0;将生极板置于装满水的超声清洗机中,频率为60khz,功率为300w,时间为10min,将处理后的生极板干燥称重,干燥采用真空干燥箱,干燥温度为60
±
5℃,干燥时间为24
±
5h;记为w1;计算生极板重量损失率w%=(w0-w1)/w0=0。
39.超声对比例二:
40.取2片生极板,重量记为w0;
41.将生极板置于装满水的超声清洗机中,频率为65khz,功率为300w,时间为12min,将处理后的生极板干燥称重,干燥采用真空干燥箱,干燥温度为60
±
5℃,干燥时间为24
±
5h;记为w1;计算各片生极板重量损失率w%=(w0-w1)/w0;根据各片生极板重量损失率取平均值=0;
42.超声对比例三:
43.取3片生极板,重量记为w0;
44.将生极板置于装满水的超声清洗机中,频率为70khz,功率为300w,时间为15min,将处理后的生极板干燥称重,干燥采用真空干燥箱,干燥温度为60
±
5℃,干燥时间为24
±
5h;记为w1;计算各片生极板重量损失率w%=(w0-w1)/w0;根据各片生极板重量损失率取平均值=0;
45.超声对比例四:
46.取4片生极板,重量记为w0;
47.将生极板置于装满水的超声清洗机中,频率为75khz,功率为300w,时间为15min,将处理后的生极板干燥称重,干燥采用真空干燥箱,干燥温度为60
±
5℃,干燥时间为24
±
5h;记为w1;计算各片生极板重量损失率w%=(w0-w1)/w0;根据各片生极板重量损失率取平均值=0;
48.超声对比例五:
49.取5片生极板;将各片生极板重量记为w0;
50.将生极板置于装满水的超声清洗机中,频率为80khz,功率为300w,时间为15min,将处理后的生极板干燥称重,干燥采用真空干燥箱,干燥温度为60
±
5℃,干燥时间为24
±
5h;记为w1;计算各片生极板重量损失率w%=(w0-w1)/w0;根据各片生极板重量损失率取平均值=0;
51.跌落法对比例:
52.取5片生极板,重量记为w0;将生极板从1米高度水平重复跌落5次,将跌落后的待评价的极板称重,记为w1;计算5片生极板重量损失率分别为w%=(w0-w1)/w0=0.71、1.32、1.21、0.33和2.11。
53.本发明实例一:
54.取1片生极板,重量记为w0;
55.将生极板经密封容器置于振动台上,振动台测试选用正弦驻留的方式进行振动,起始频率为60hz,定加速度为82hz,加速度峰值为10g,共振动10min;将振动后的生极板称重,记为w1;计算生极板重量损失率w%=(w0-w1)/w0=0.71。
56.本发明实例二:
57.取2片生极板;
58.将各片生极板重量记为w0;将生极板经密封容器置于振动台上,生极板在密封容器内不可叠放;振动台测试选用正弦驻留的方式进行振动,起始频率为65hz,定加速度为82hz,加速度峰值为10g,共振动12min;将振动后的各片生极板称重,记为w1;计算各片生极板重量损失率w%=(w0-w1)/w0;根据各片生极板重量损失率取平均值=0.75。
59.本发明实例三:
60.取3片生极板;
61.将各片生极板重量记为w0;将生极板经密封容器置于振动台上,生极板在密封容器内不可叠放;振动台测试选用正弦驻留的方式进行振动,起始频率为70hz,定加速度为82hz,加速度峰值为10g,共振动15min;将振动后的各片生极板称重,记为w1;计算各片生极板重量损失率w%=(w0-w1)/w0;根据各片生极板重量损失率取平均值=0.85。
62.本发明实例四:
63.取4片生极板;
64.将各片生极板重量记为w0;将称重后的生极板经密封容器置于振动台上,生极板在密封容器内不可叠放;振动台测试选用正弦驻留的方式进行振动,起始频率为75hz,定加速度为82hz,加速度峰值为10g,共振动15min;将振动后的各片生极板称重,记为w1;计算各片生极板重量损失率w%=(w0-w1)/w0;根据各片生极板重量损失率取平均值=0.67。
65.本发明实例五:
66.取5片生极板;
67.将各片生极板重量记为w0;将生极板经密封容器置于振动台上,生极板在密封容器内不可叠放;振动台测试选用正弦驻留的方式进行振动,起始频率为80hz,定加速度为85hz,加速度峰值为10g,共振动15min;将振动后的各片生极板称重,记为w1;计算各片生极板重量损失率w%=(w0-w1)/w0;根据各片生极板重量损失率取平均值=0.72。
68.本发明的实施例与比对例形成的表格如表一:
[0069][0070]
根据表一,可知超声无法用来评价固化的极板,跌落法得到的重量损失率的数值差异较大,而振动的方法数据较为稳定,可以用来评价固化质量的好坏。
[0071]
本发明用于定量评价活性物质软化脱落程度,适用的范围为失效的正极板,具体内容如下:
[0072]
本发明取样条件,所取失效后的电池应贮存在常温下的生产场所、使用场所或在库房内放置。
[0073]
本发明的取样方法:失效的正极板来自失效电池,失效电池解剖按照常规的解剖流程,待测试的正极板通常在中间三个单格取样,并避免边板,至少取10片正极板。同时取正极板时应避免因外力造成的活性物质脱落。
[0074]
本发明取样后的保存方法:取样的失效的正极板(简称正极板),若不能马上进行后续测试,将制备好的样品轻轻放入水中,浸泡1h,并放置在gb/t 2918规定的标准环境下(室温条件下,空气温度25℃);振动前用agm隔板纸擦拭表面,以看不到明显的水痕迹为准。
[0075]
塑料槽放在振动台上,用扳手拧紧螺丝将其固定。本发明所用的振动台测试选用正弦驻留的方式进行振动,起始频率为80hz,定加速度为82hz,加速度峰值为10g,共振动10min。振动结束后,用扳手拧松螺丝,将白色塑料槽取下,将其中的正极板取出,若无正极板需要振动,清理振动台。
[0076]
接下来进入如下步骤:
[0077]
(1)将振动后的正极板用agm隔板纸擦拭表面,以看不到明显的水痕迹为准,称重,记为w1;不需干燥,只需用agm隔板纸把表面擦干即可,最重要的是在干燥过程中会破坏极板的活性物质结构,导致结果不准确;
[0078]
(2)计算单片正极板活性物质软化脱落率w%=(w0-w1)/w0,w0为电池设计时已知的正极板重量;
[0079]
(3)按照步骤(2)计算每片正极板的软化脱落率,然后取平均,即为最终的活性物质软化率。
[0080]
本发明还可判断极板中部、下部和下部的活性物质软化脱落程度。可将极板分别
裁剪为上、中和下部,分别按照以上方法计算。但裁剪的时候要注意不要破坏极板。
[0081]
本发明所用的东西均为铅酸蓄电池常用的设备,不需额外投入;本发明不采用水洗的方式,避免水洗带来的对活性物质本身结构造成的损坏;本发明不采用人为的方式进行判断活性物质的软化脱落程度;针对失效后的正极板,选用了厚度在4mm和1.8mm的极板做实验,同时,选用经验判断活性物质脱落率在10-20%之间和50%以上的两种1.8mm的极板同时做试验。经验判断方法为靠人工数下脱落活性物质的正极板板栅上的格子有多少。超声法对比例和本发明的振动方法评价的数据如下:
[0082]
下面以1组对比例与本发明的实施例进行对比,对本发明作进一步说明。
[0083]
超声法对比例:
[0084]
取5片失效的正极板用agm隔板纸擦拭表面,以看不到明显的水痕迹为准,失效的正极板重量为电池设计时已知重量w0;将失效的正极板置于装满水的超声清洗机中,频率为80khz,功率为300w,时间为10min,将处理后的正极板用agm隔板纸擦拭表面,以看不到明显的水痕迹为准,称重记为w1;计算待评价的正极重量损失率w%=(w0-w1)/w0。
[0085]
本发明实例:
[0086]
取5片正极板轻轻放入水中浸泡1h,然后用agm隔板纸擦拭表面,以看不到明显的水痕迹为准,正极板重量为w0;将正极板经密封容器置于振动台上,振动台测试选用正弦驻留的方式进行振动,起始频率为80hz,定加速度为82hz,加速度峰值为10g,共振动10min;将振动后的正极板用agm隔板纸擦拭表面,以看不到明显的水痕迹为准,称重记为w1;计算待评价的生极板重量损失率w%=(w0-w1)/w0。
[0087]
本发明评价铅酸电池活性物质软化脱落的定量方法与比对例形成的表格如表二:
[0088][0089]
从测试结果来看,针对较厚的极板,超声振动的方法只能作用于表面,对于界面的作用很小,因此测试的结果也偏小,不准确。而且超声振动的方法针对活性物质软化脱落不是很严重的极板,也不能评价。