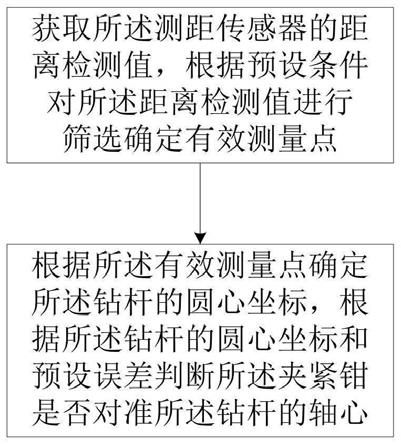
1.本发明涉及石油钻井技术领域,具体而言,涉及一种钻杆检测方法、电子设备及存储介质。
背景技术:2.随着现代信息技术与智能制造技术的快速发展,自动化钻井也有了很大的发展,钻修井铁钻工是近年来石油装备自动化中的新产品,其作用在于能对钻杆或套管进行自动上扣、卸扣操作。在铁钻工进行上扣、卸扣操作时,需要铁钻工的主钳和背钳分别紧紧地夹住钻杆接箍上、下两部分,由于夹紧的压力可达10mpa以上,必须确保铁钻工钳体能准确夹住钻杆或者套管,否则极易发生安全事故。
3.在现有的钻修井铁钻工设备中,主要通过以下方式实现对钻杆的夹紧:(1)标定钻杆接箍所在位置,记录铁钻工各运动电机控制参数;(2)根据标定后存储的铁钻工各运动电机控制参数,控制铁钻工移动至钻杆接箍处,并控制主钳和背钳夹紧钻杆接箍上下两部分。但是,通过参数进行控制属于开环控制,易产生误差,影响到钻杆的杆径测量及轴心检测。
技术实现要素:4.本发明解决的问题是如何有效实现钻杆的杆径测量及轴心检测。
5.为解决上述问题,本发明提供一种钻杆检测方法,基于钻杆检测系统实现钻杆检测,所述钻杆检测系统包括铁钻工、测距传感器和安装定位板,所述铁钻工的夹紧钳适于抱紧所述钻杆,所述安装定位板安装在所述铁钻工上,且所述安装定位板的开口方向与所述铁钻工的开口方向相同,所述测距传感器设置在所述安装定位板上且用于检测与所述钻杆的距离,所述钻杆检测方法包括:获取所述测距传感器的距离检测值,根据预设条件对所述距离检测值进行筛选确定有效测量点;根据所述有效测量点确定所述钻杆的圆心坐标,根据所述钻杆的圆心坐标和预设误差判断所述夹紧钳是否对准所述钻杆的轴心。
6.本发明所述的钻杆检测方法,通过测距传感器所检测的检测值,根据预设条件筛选后确定有效测量点进而确定钻杆圆心坐标,从而能够结合预设误差判断夹紧钳是否对准钻杆的轴心以实现钻杆的检测,由于只需要进行简单的运算即能获得钻杆轴心相对于铁钻工夹紧钳的位置信息,对检测装置硬件要求低,运算速度快能够实时反馈钻杆轴心位置,自动检测铁钻工钳体中心和钻杆轴心是否对齐,因而能够快速高效实现钻杆的检测,实现自动连续作业,提高工作效率。另外,通过设置在铁钻工上的安装定位板实现测距传感器的安装,由于安装定位板的开口方向与铁钻工的开口方向相同,因此有利于钻杆由宽度为l的u型开口进入及退出,且只需要测距传感器从开口方向进入u型槽后,测距传感器就能直接对准钻杆进行检测,不需要额外调试工作,因而有利于快速高效实现钻杆的检测。
7.可选地,所述钻杆检测系统包括多个所述测距传感器,所述测距传感器的数量确定方法包括:根据第一公式确定所述测距传感器的数量,所述第一公式包括:
[0008][0009][0010]
其中,g表示所述测距传感器所需的最少个数,l表示所述铁钻工的开口的宽度,d
min
表示所述铁钻工工作中所需要抓取的最小杆径,e表示相邻两个所述测距传感器布置距离的修正参数,d表示相邻两个所述测距传感器实际中心距离。
[0011]
本发明所述的钻杆检测方法,根据第一公式来确定所需测距传感器的最少个数,即根据现场实际设置情况来确定所需测距传感器的最少个数,有利于在满足检测的前提下降低成本。
[0012]
可选地,在所述第一公式中,当满足时,最小杆径的所述钻杆在所述铁钻工的u型槽任意处均可被至少三个所述测距传感器检测到。
[0013]
本发明所述的钻杆检测方法,通过设置当满足时,最小杆径的钻杆在所述铁钻工的u型槽任意处均可被至少三个所述测距传感器检测到,从而实现测距传感器对钻杆的有效检测。
[0014]
可选地,所述根据预设条件对所述距离检测值进行筛选确定有效测量点包括:将各个测距传感器的距离检测值分别与预设检测距离进行比较,将小于及等于所述预设检测距离的所述距离检测值所对应的测量点确定为所述有效测量点。
[0015]
本发明所述的钻杆检测方法,根据预设检测距离筛选有效测量点,剔除不合理数据,有利于实现测距传感器对钻杆的准确检测。
[0016]
可选地,所述根据所述有效测量点确定所述钻杆圆心坐标包括:
[0017]
根据所述有效测量点确定三个有效坐标点,将所述有效坐标点代入圆方程x2+y2+dx+ey+f=0中,得到系数解如下:
[0018][0019][0020][0021]
其中,三个所述有效坐标点分别表示为(x1,y1)、(x2,y2)和(x3,y3);
[0022]
所述钻杆的圆心坐标表示为
[0023]
本发明所述的钻杆检测方法,根据有效测量点得到有效坐标点后,将有效坐标点代入圆方程进行相应运算即可得到钻杆圆心坐标,运算速度快,且有效降低了硬件成本。
[0024]
可选地,所述根据所述钻杆圆心坐标和预设误差判断所述夹紧钳是否对准所述钻杆的轴心包括:
[0025]
当所述钻杆圆心坐标满足时,判断所述夹紧钳对准所述钻杆的轴心,否则判断未对准,其中,δ表示所述预设误差,所述预设误差表示实际工况允许对齐的误差。
[0026]
本发明所述的钻杆检测方法,根据预设误差作为夹紧钳对准钻杆的轴心的判断条件,有利于完成钻杆检测,从而保证钻杆的对齐效果。
[0027]
可选地,所述钻杆检测方法还包括:当判断所述夹紧钳未对准所述钻杆的轴心时,根据实时检测的所述钻杆的圆心坐标反馈所述钻杆的轴心位置,直至所述钻杆的轴心调整至与所述夹紧钳对准。
[0028]
本发明所述的钻杆检测方法,通过设置在夹紧钳未对准钻杆的轴心时,根据实时检测的钻杆圆心坐标反馈钻杆的轴心位置直至钻杆的轴心调整至与夹紧钳对准,从而能够实现钻杆的快速对齐。
[0029]
可选地,所述钻杆检测方法还包括:根据所述有效测量点确定所述钻杆的杆径尺寸,所述钻杆的杆径尺寸表示为
[0030]
本发明所述的钻杆检测方法,根据有效测量点确定钻杆的杆径尺寸,在完成钻杆轴心对齐检测的同时,能够完成对杆径的测量,进而有利于铁钻工在夹紧中针对不同杆径钻杆夹紧时的控制参数进行调整。
[0031]
本发明还提供一种电子设备,包括存储有计算机程序的计算机可读存储介质和处理器,所述计算机程序被所述处理器读取并运行时,实现如上所述的钻杆检测方法。所述钻杆检测系统与上述钻杆检测方法相对于现有技术所具有的优势相同,在此不再赘述。
[0032]
本发明还提供一种计算机可读存储介质,所述计算机可读存储介质存储有计算机程序,所述计算机程序被处理器读取并运行时,实现如上所述的钻杆检测方法。所述计算机可读存储介质与上述钻杆检测方法相对于现有技术所具有的优势相同,在此不再赘述。
附图说明
[0033]
图1为本发明实施例的钻杆检测方法的流程示意图;
[0034]
图2为本发明实施例的铁钻工钳主体的结构示意图;
[0035]
图3为本发明实施例的测距传感器的安装示意图;
[0036]
图4为本发明实施例的安装有测距传感器的安装定位板安装在铁钻工钳主体上的示意图。
具体实施方式
[0037]
为使本发明的上述目的、特征和优点能够更为明显易懂,下面结合附图对本发明的具体实施例做详细的说明。
[0038]
如图1所示,本发明实施例提供一种钻杆检测方法,基于钻杆检测系统实现钻杆检测,所述钻杆检测系统包括铁钻工、测距传感器和安装定位板,所述铁钻工的夹紧钳适于抱紧所述钻杆,所述安装定位板安装在所述铁钻工上,且所述安装定位板的开口方向与所述铁钻工的开口方向相同,所述测距传感器设置在所述安装定位板上且用于检测与所述钻杆的距离,所述钻杆检测方法包括:获取所述测距传感器的距离检测值,根据预设条件对所述
距离检测值进行筛选确定有效测量点;根据所述有效测量点确定所述钻杆的圆心坐标,根据所述钻杆的圆心坐标和预设误差判断所述夹紧钳是否对准所述钻杆的轴心。
[0039]
具体地,在本实施例中,结合图2至图4所示,钻杆检测方法基于钻杆检测系统实现钻杆检测,钻杆检测系统包括铁钻工、测距传感器和安装定位板,铁钻工的夹紧钳能够抱紧钻杆,安装定位板安装在铁钻工上,且安装定位板的开口方向与铁钻工的开口方向相同,测距传感器设置在安装定位板上且用于检测与钻杆的距离。当铁钻工进行上卸扣作业时,钻杆由宽度为l的u型开口进入,直到钻杆中心和一对夹紧钳夹紧中心对齐时,夹紧钳向中间收紧,并抱紧钻杆,从而确保铁钻工钳体能准确夹住钻杆,提高了施工安全性。结合图4所示,安装定位板整体呈u型,两边可以通过螺栓固定在钳主体上,另一边则适于安装测距传感器,测距传感器从开口方向进入u型槽后,测距传感器就能直接对准钻杆进行检测。
[0040]
以铁钻工钳体中心建立坐标系xoy,结合图3和图4所示,x1,x2,x3,x4测距传感器在xoy直角坐标系中的坐标分别用a,b,c,d表示如下:
[0041]
a:
[0042]
b:
[0043]
c:
[0044]
d:
[0045]
其中,x1至x4分别表示x1,x2,x3,x4测距传感器的检测值。
[0046]
结合图3所示,安装定位板为一个u型板,主要作用在于为测距传感器(优选为激光测距传感器)安装定位,并可安装于铁钻工钳主体上,结合图4所示,将安装定位板安装于铁钻工钳主体上的示意图;以u型板中心线为x1轴,o1为圆心,建立如图2所示的直角坐标系x1o1y1,将安装定位板安装于铁钻工主体上时需令直角坐标系x1o1y1和xoy重合(理想情况下需重合,一般满足精度要求即可)。其中,图3中,a表示测距传感器左端到原点o1的距离,b表示安装定位板的宽度,c表示最接近x1轴的测距传感器轴心到x1轴的距离,d表示相邻两个测距传感器实际中心距离,m表示安装定位板的长度。
[0047]
当钻杆进入铁钻工钳体可检测u型区域后,分别读取所有测距传感器的距离检测值,由于会出现距离检测值大于l
max
(安装定位板左端到铁钻工钳主体u型开口的距离)的超限程(检测到相对比较远的地方),或是无返回值(未检测到值)的情况,因此需要根据预设条件对距离检测值进行筛选确定有效测量点。
[0048]
在确定有效测量点后,可根据有效测量点获得有效坐标点来确定钻杆圆心坐标。在确定钻杆圆心在铁钻工钳主体坐标系xoy的坐标后,可以确定钻杆轴心相对于铁钻工夹紧钳中心的相对位置,进而结合预设误差可以判断夹紧钳是否对准钻杆的轴心。通过测距传感器所检测的检测值,根据预设条件筛选后确定有效测量点进而确定钻杆圆心坐标,从而能够结合预设误差判断夹紧钳是否对准钻杆的轴心以实现钻杆的检测,实时反馈钻杆轴心相对夹紧钳相对位置,自动检测铁钻工钳体中心和钻杆轴心是否对齐,因而能够快速高效实现钻杆的检测,相对人工对准方式能够实现自动连续作业,提高工作效率。
[0049]
且对于不同杆径的钻杆、套管,本实施例方案均能适用,当钻杆杆径变化后无需对钻杆接箍,且当标定后的钻杆接箍位置发生偏移后无需重新标定。另外,由于本实施例只检测某一截面,当钻杆和测距传感器间产生相对抖动时,也能对倾斜钻杆进行测量。现有技术中通常采用激光扫描面来实现钻杆的非接触检测,一般需要激发一个平行扫描光束,并在另一端放置接收器,本实施例既不需要设置专门的激光接收装置,且只需要测量截面的几个点即可完成管径及轴心检测。
[0050]
在本实施例中,通过测距传感器所检测的距离检测值,根据预设条件筛选后确定有效测量点进而确定钻杆圆心坐标,从而能够结合预设误差判断夹紧钳是否对准钻杆的轴心以实现钻杆的检测,由于只需要进行简单的运算即能获得钻杆轴心相对于铁钻工夹紧钳的位置信息,对检测系统硬件要求低,运算速度快能够实时反馈钻杆轴心位置,自动检测铁钻工钳体中心和钻杆轴心是否对齐,因而能够快速高效实现钻杆的检测,实现自动连续作业,提高工作效率。另外,通过设置在铁钻工上的安装定位板实现测距传感器的安装,由于安装定位板的开口方向与铁钻工的开口方向相同,因此有利于钻杆由宽度为l的u型开口进入及退出,且只需要测距传感器从开口方向进入u型槽后,测距传感器就能直接对准钻杆进行检测,不需要额外调试工作,因而有利于快速高效实现钻杆的检测。
[0051]
可选地,所述钻杆检测系统包括多个所述测距传感器,所述测距传感器的数量确定方法包括:根据第一公式确定所述测距传感器的数量,所述第一公式包括:
[0052][0053][0054]
其中,g表示所述测距传感器所需的最少个数,l表示所述铁钻工的开口的宽度,d
min
表示所述铁钻工工作中所需要抓取的最小杆径,e表示相邻两个所述测距传感器布置距离的修正参数,d表示相邻两个所述测距传感器实际中心距离。
[0055]
具体地,在本实施例中,由于测距传感器在检测时既要满足有效检测区域能覆盖铁钻工u型槽(铁钻工的开口为u型开口的情况),又要满足测距传感器数量尽量少,因此根据第一公式来确定所需测距传感器的最少个数,即根据现场实际设置情况来确定所需测距传感器的最少个数,有利于在满足检测的前提下降低成本。
[0056]
在本实施例中,根据第一公式来确定所需测距传感器的最少个数,即根据现场实际设置情况来确定所需测距传感器的最少个数,有利于在满足检测的前提下降低成本。
[0057]
可选地,在所述第一公式中,当满足时,最小杆径的所述钻杆在所述铁钻工的u型槽任意处均可被至少三个所述测距传感器检测到。
[0058]
具体地,在本实施例中,当满足时,任意设计(包括最小杆径)的钻杆在u型槽内任一地方均可同时被至少3个传感器检测到,其余传感器检测值则会出现大于l
max
的超限程,或是无返回值的情况,从而实现测距传感器对钻杆的有效检测。
[0059]
在本实施例中,通过设置当满足时,最小杆径的钻杆在所述铁钻工的
u型槽任意处均可被至少三个所述测距传感器检测到,从而实现测距传感器对钻杆的有效检测。
[0060]
可选地,所述根据预设条件对所述距离检测值进行筛选确定有效测量点包括:将各个所述测距传感器的所述距离检测值分别与预设检测距离进行比较,将小于及等于所述预设检测距离的所述距离检测值所对应的测量点确定为所述有效测量点。
[0061]
具体地,在本实施例中,以四个测距传感器为例,根据预设检测距离l
max
对得到的各传感器的距离检测值xn(n=1,2,3,4)进行判断和筛选,若xn≤l
max
,则xn属于有效测量点,超过l
max
的属于超限程的不合理数据,需要剔除。
[0062]
在本实施例中,根据预设检测距离筛选有效测量点,剔除不合理数据,有利于实现测距传感器对钻杆的准确检测。
[0063]
可选地,所述根据所述有效测量点确定所述钻杆的圆心坐标包括:
[0064]
根据所述有效测量点确定三个有效坐标点,将所述有效坐标点代入圆方程x2+y2+dx+ey+f=0中,得到系数解如下:
[0065][0066][0067][0068]
其中,三个所述有效坐标点分别表示为(x1,y1)、(x2,y2)和(x3,y3);
[0069]
所述钻杆的圆心坐标表示为
[0070]
具体地,在本实施例中,若有效测量点个数n=3,则取该3个有效测量点分别代入对应的坐标公式,获得3个有效坐标点;若有效测量点个数n》3,则从中随机选取三个点代入坐标公式中获得3个有效坐标点。
[0071]
以三个有效坐标点(x1,y1)、(x2,y2)和(x3,y3)为例,分别代入圆方程x2+y2+dx+ey+f=0中,联立方程组(将三个有效坐标点视为已知值,将系数视为未知值)求解得到相应的系数解d0,e0和f0,由于圆方程可以表示为:从而能够确定钻杆圆心坐标为且杆径尺寸为
[0072]
在本实施例中,根据有效测量点得到有效坐标点后,将有效坐标点代入圆方程进行相应运算即可得到钻杆圆心坐标,运算速度快,且有效降低了硬件成本。
[0073]
可选地,所述根据所述钻杆圆心坐标和预设误差判断所述夹紧钳是否对准所述钻杆的轴心包括:
[0074]
当所述钻杆圆心坐标满足时,判断所述夹紧钳对准所述钻杆的轴心,否则判断未对准,其中,δ表示所述预设误差,所述预设误差表示实际工况允许对齐的误差。
[0075]
具体地,在本实施例中,根据钻杆圆心在铁钻工钳主体坐标系xoy的坐标可检测钻杆轴心相对于铁钻工夹紧钳中心的相对位置,当时,可判定钻杆轴心已对齐铁钻工夹紧钳中心,可以进行下一步的夹紧操作,其中δ为实际工况允许对齐的误差,即预设误差。
[0076]
在本实施例中,根据预设误差作为夹紧钳对准钻杆的轴心的判断条件,有利于完成钻杆检测,从而保证钻杆的对齐效果。
[0077]
可选地,所述钻杆检测方法还包括:当判断所述夹紧钳未对准所述钻杆的轴心时,根据实时检测的所述钻杆的圆心坐标反馈所述钻杆的轴心位置,直至所述钻杆的轴心调整至与所述夹紧钳对准。
[0078]
具体地,在本实施例中,由于只需要进行简单的运算即能获得钻杆轴心相对于铁钻工夹紧钳的位置信息,运算速度快能够实时反馈钻杆轴心位置,因此能够在夹紧钳未对准钻杆的轴心时,根据实时的检测值所确定的钻杆的圆心坐标对钻杆的轴心调整进行指导,直至钻杆的轴心调整至与夹紧钳对准。其中,钻杆的轴心调整既可以是人工调整,也可以通过电机根据实时钻杆轴心位置自动调整铁钻工位置,以实现与钻杆轴心的相对位置调整。
[0079]
在本实施例中,通过设置在夹紧钳未对准钻杆的轴心时,根据实时检测的钻杆圆心坐标反馈钻杆的轴心位置直至钻杆的轴心调整至与夹紧钳对准,从而能够实现钻杆的快速对齐。
[0080]
可选地,所述钻杆检测方法还包括:根据所述有效测量点确定所述钻杆的杆径尺寸,所述钻杆的杆径尺寸表示为
[0081]
具体地,在本实施例中,由于圆方程可以表示为:因此杆径尺寸等于圆方程右侧开方后的两倍,即由于上述圆方程既能表示轴心也能表示杆径,因此在完成钻杆轴心对齐检测的同时,能够完成对杆径的测量,进而有利于铁钻工在夹紧中针对不同杆径钻杆夹紧时的控制参数进行调整。
[0082]
在本实施例中,根据有效测量点确定钻杆的杆径尺寸,在完成钻杆轴心对齐检测的同时,能够完成对杆径的测量,进而有利于铁钻工在夹紧中针对不同杆径钻杆夹紧时的控制参数进行调整。
[0083]
本发明另一实施例提供一种电子设备,包括存储有计算机程序的计算机可读存储介质和处理器,所述计算机程序被所述处理器读取并运行时,实现如上所述的钻杆检测方法。其中,电子设备与测距传感器连接,电子设备可以是单片机、plc(programmable logic controller,可编程逻辑控制器)等设备。
[0084]
本发明另一实施例提供一种计算机可读存储介质,所述计算机可读存储介质存储有计算机程序,所述计算机程序被处理器读取并运行时,实现如上所述的钻杆检测方法。
[0085]
虽然本发明公开披露如上,但本发明公开的保护范围并非仅限于此。本领域技术人员在不脱离本发明公开的精神和范围的前提下,可进行各种变更与修改,这些变更与修
改均将落入本发明的保护范围。