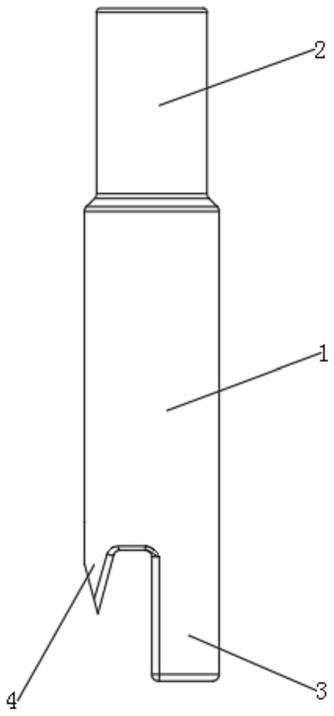
1.本发明属于整体压气机或涡轮叶片检测技术领域,具体涉及一种叶片检测工装及使用该工装的快速检测方法。
背景技术:2.整体式压气机,涡轮零部件本就属于高难度制造零部件,叶片结构复杂且均为异型件,结合增材制造带来的叶片零件变形,表面粗糙度等因素影响,给压气机,涡轮叶片检测带来了很大的挑战。查阅相关资料和文献,现在常规检测方案一般分为两类:一是采用精密设备检测,精密设备本身价格昂贵,要求检测人员技术水平高,且检测周期长;二是,通过组合工装检具检测,其制造成本高、周期长、通用性差。此外,两种常规检测方案都仅适用于零部件最后工序检测,过程检测的实用性及经济性较差。
技术实现要素:3.针对现有技术中存在的上述问题,本发明的目的在于提供一种检测结构简单、操作方便、检测精度高,适用于整体压气机或涡轮叶片检测的检测工装及使用该工装的快速检测方法。
4.本发明提供如下技术方案:一种叶片检测工装,包括工装主体,所述工装主体的上端设有安装段,其下端设有检测结构,所述安装段安装在高度检测设备上,所述检测结构包括基准段及检测段。
5.优选的,所述基准段的底端设有校准基准面,其内侧设有检测基准面,所述检测基准面上设有第一对中线。
6.优选的,所述检测段的内、外两侧均为倾斜面,内、外两侧的倾斜面之间形成检测边线。
7.优选的,所述检测段的外侧设有与第一对中线相对应的第二对中线。
8.优选的,所述检测边线位于校准基准面的上方。
9.优选的,所述校准基准面与检测边线之间的距离d1为4-8mm;检测基准面与检测边线之间的距离d2为3-10mm。
10.一种叶片检测工装的快速检测方法,包括以下步骤:步骤1、将带有叶片的零件放置在检测平台上,并将工装主体上的安装段安装到检测设备;步骤2、调整高度检测设备,使得校准基准面与检测平台的基准面接触,并将高度检测设备设置归零;步骤3、移动高度检测设备,将检测基准面紧贴零件上待检测叶片的叶尖,并将该叶尖的顶端对准第一对中线,然后控制高度检测设备,降低工装主体的高度,直到工装主体上的检测边线与待检测叶片的棱边贴紧,记录高度检测设备上的高度数值;步骤4、重复步骤3的操作,记录同一个叶片的若干组测量数值,取若干组测量数值
的平均值作为最终测量值,并将最终测量值通过公式计算转换为叶片的高度值,将该高度值与叶片的设计要求值对比,判断叶片是否合格。
11.通过采用上述技术,与现有技术相比,本发明的有益效果如下:1)本发明中,通过设置的基准段,能够快速地对高度检测设备进行校零,并准确找取检测时的工装放置位置;通过设置的检测段,,配合高度检测设备能够对叶片的高度进行检测;检测段上的检测边线与叶片之间形成线接触或者面接触,便于检测人员进行精准的数据读取,减少人工读取误差;2)本发明中,校准基准面与检测边线之间、检测基准面与检测边线之间的距离保证在一定的范围内,能够适应不同被测零件叶片长度以及不同大小的零件空间;3)本发明整体结构简单、基准找取方便、测量快捷、检测效率高、检测精度准确,适用范围广,能够满足增材制造过程每一步工序叶片检测。
附图说明
12.图1为本发明检测工装的主视结构示意图;图2为本发明检测工装的立体结构示意图;图3为本发明实施例中,涡轮零部件的主视结构示意图;图4为本发明实施例中,涡轮零部件的俯视结构示意图;图5为本发明实施例工装对零件进行测试时的结构示意图。
13.图中:1、工装主体;2、安装段;3、基准段;301、校准基准面;302、检测基准面;303、第一对中线;4、检测段;401、检测边线;a、零件。
具体实施方式
14.为了使本发明的目的、技术方案及优点更加清楚明白,以下结合说明书附图及实施例,对本发明进行进一步详细说明。应当理解,此处所描述的具体实施例仅仅用以解释本发明,并不用于限定本发明。
15.相反,本发明涵盖任何由权利要求定义的在本发明的精髓和范围上做的替代、修改、等效方法以及方案。进一步,为了使公众对本发明有更好的了解,在下文对本发明的细节描述中,详尽描述了一些特定的细节部分。对本领域技术人员来说没有这些细节部分的描述也可以完全理解本发明。
16.请参阅图1-5,一种叶片检测工装,包括工装主体1,工装主体1的上端设有安装段2,安装段2螺纹安装在高度尺上;工装主体1的下端设有检测结构;其中,工装主体1、安装段2及检测结构采用3d打印成型,成型快不受结构限制。
17.具体的,检测结构包括相对设置的基准段3及检测段4,,分别设置在工装主体1下端的两侧。
18.具体的,基准段3为半圆柱体,其底端面为校准基准面301,内侧面为检测基准面302,检测基准面302上设有第一对中线303。
19.具体的,检测段4的内外连侧均为倾斜面,两个倾斜面之间形成一条边线,该边线为检测边线401;检测段4的外侧设有与第一对中线303相对应的第二对中线402,便于检测时检测人员观察。
20.具体的,检测边线401与校准基准面301之间存在高度差,检测边线401与校准基准面301之间的竖直距离d1为4mm,检测边线401与检测基准面302之间的水平距离d2为5mm。
21.使用本实施例工装进行叶片快速检测的方法,包括以下步骤:步骤1、将带有叶片的零件a水平放置在检测平台上,并将工装主体1上的安装段2安装到高度尺上;步骤2、调整高度尺,使得校准基准面301与检测平台的基准面接触,并将高度尺设置归零,该基准面可以是能与检测零件a建立关系的任何面;步骤3、将检测基准面302紧贴零件a上待检测叶片的叶尖,并将该叶尖的顶端对准第一对中线303,然后控制高度尺,逐渐降低工装主体1的高度,直到工装主体1上的检测边线401与待检测叶片的棱边贴紧,记录高度尺上的高度数值;步骤4、重复步骤3的操作,记录同一个叶片的三组测量数值,取三组测量数值的平均值作为最终测量值,并将最终测量值减去d1的值即转换为叶片的高度值,将该高度值与叶片的设计要求值对比,判断叶片是否合格。
22.还可以根据检测的高度值计算叶片的其他尺寸值,计算示例:如附图3、4所示,设计上以涡轮零部件理论圆形边界为测量起点向圆心方向以直径为0.5mm递减分布给出对应理论高度值h,如下表1:
ꢀ‑
1(靠近外沿方向)0(图纸标注)12
……
直径(mm)198.5198197.5197
……
高度(mm)27.1927.2327.2927.35
……
背侧高度5.435.415.395.37
……
表1理论高度值h以零件超差允许值决定,若测出高度值偏大,说明叶片上翘收缩变形,如需判断是叶片整体收缩还是单边上翘变形,需增加测量对应叶片另一侧的高度(即背侧高度),根据测量数据与理论数据对比。
23.若测量值偏小,说明叶片下塌外延变形,如需判断是叶片整体下塌还是单边下塌变形,需增加测量对应叶片另一侧的高度(即背侧高度),根据测量数据与理论数据对比。
24.上面中高度值是根据零件实际状态确定的(如:带基板,线切割后,机加工后等)直径方向是唯一确定的。上表中高度值为机加工后的值。
25.本实施例中的工装采用3d打印,成型快且不受结构限制、能够满足增材制造过程每一步工序叶片检测的需求;本实施例中的快速检测方法适用普通检测工具,如高度尺、深度尺等,价格便宜、适用性好。
26.以上所述仅为本发明的较佳实施例而已,并不用以限制本发明,凡在本发明的精神和原则之内所作的任何修改、等同替换和改进等,均应包含在本发明的保护范围之内。