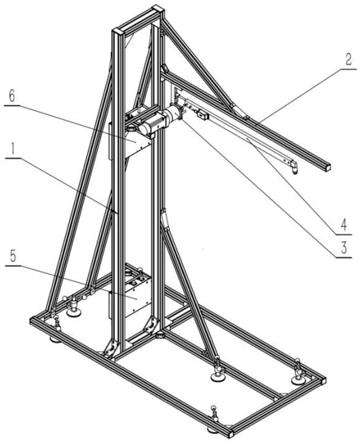
1.本发明涉及一种高速弓网综合检测系统,具体地涉及一种接触网定位器坡度检测系统及检测方法。
背景技术:2.高速弓网综合检测装置为在综合检测列车安装的车载式接触网检测设备,随着综合检测列车在高速铁路上巡回检测运行,对高速铁路接触网的参数和状态、高速弓网关系进行综合性检测。接触网为通过受电弓供给机车/动车组电能的架空导线系统,主要由支柱、基础、支持结构及接触悬挂等组成。接触网几何参数为表征接触网所处空间位置特征的参数,主要包含接触线高度、坡度、横向偏移、相对位置等。接触网定位器坡度为定位器连线的延长线相对于两钢轨轨面的斜度(应用于z型限位定位器)。
3.定位器坡度是影响列车运行安全的重要指标之一。列车高速通过支持装置时,因受电弓的升弓压力,接触线及定位器会有一定程度的抬升,但抬升不应侵入受电弓包络线内,以避免受电弓通过时碰撞定位器导致打弓而造成接触网运营事故。因此对定位器坡度的范围有一定的要求。我国当前的接触网检修维护中,对静态定位器坡度有明确的检修维护要求;根据《tg/gd 124-2015高速铁路接触网运行维修规则》,静态定位器坡度的限界值为4
°
~15
°
。现场一般通过角度仪对静态定位器坡度进行测量,然后根据标准进行静态定位器坡度缺陷的检测。所以定位器坡度的检测是一项重要的接触网安全性检测项目。
4.高速弓网综合检测装置主要通过激光扫描法、图像识别法和超声波等非接触式方法测量定位器坡度。采用在实际运营线路上动态检验被测产品检验测量准确性的方式,因支持装置静态测量值与动态测量值随所配电力机车与轨道、电力机车与接触网间的相互位置的不一致及不可重复性,所以无法精确检测被测产品的真实性能。而现有的静态检测方法只能简单模拟定位器坡度,需要人工手动摆放模拟定位器的坡度位置,不能准确模拟定位器的实际工作状态和定位坡度值,且操作繁琐,定位精度低,重复性差。
5.为了实现动态检测定位器坡度是否在安全范围内,高速铁路供电安全检测监测系统(6c)中的高速弓网综合检测装置(1c)明确提出了定位器坡度检测的要求,并通过tj/gd007-2014《高速弓网综合检测装置(1c)暂行技术条件》对性能指标进行了明确规定。为了验证高速弓网综合检测装置(1c)性能是否达到暂行技术条件的要求,需要对装置在标准定位器坡度条件下的检测准确性进行检验。
6.现有的模拟标准目标,一种方案是在简单的支架上放置一细长圆棒模拟定位器,通过人工摆设模拟定位器,利用水平仪与角度尺结合确定定位器标准坡度,并通过系绳固定模拟定位器位置,作为检测标准目标,检验被测产品测量数值的准确性。但这种方案模拟定位器的坡度标准目标值由人工测定,人工固定,因人在回路的影响,造成测定坡度标准目标值时,作为定位基准的0点不精准,测量的值与真实值有较大偏差;同时,在人工固定模拟定位器时,很可能由于人为原因,造成测量后的值发生变化,致使真实值与目标值产生较大误差,精度低,重复性也差,满足不了作为检验标准的要求。另一种方案是用分度头夹持模
拟定位器,通过手摇分度头来模拟不同的定位器坡度标准目标值。该种方案部分解决了人工固定模拟定位器时产生的误差,但其定位基准的0点仍需人工确定,转动的角度也需人工计算确定,存在人在回路,其真实值与目标值同样存在较大误差。
7.以上两种方案均是简化了定位器相关结构,需设计专门的算法才能识别,与被测产品应用的识别算法有较大出入,不能真实反映产品的情况。
技术实现要素:8.为克服现有技术中存在的缺陷,本发明采用一种全新的形式,通过采用类似定位器真实安装情况的支撑结构,利用高精度伺服电机及减速机构,带动模拟定位器转动到目标位置,结合高精度倾角传感器,通过专用的嵌入式软件,实时反馈模拟定位器的角度信息,并通过无线发送到专用控制平板电脑上,对检测目标值进行实时显示与控制。整体系统指示的标准目标值准确度高,定位基准0点精度高,一致性好,重复性好,检测过程简单快捷。
9.本发明的技术方案如下:
10.一种接触网定位器坡度检测系统,包括支架系统、模拟定位管部件、角度控制系统、模拟定位器系统和电气系统,其中模拟定位管部件垂直固定于支架系统上;角度控制系统与模拟定位管部件固定连接;模拟定位器系统位于模拟定位管部件下方,其一端与角度控制系统连接,由角度控制系统驱动转动;电气系统与角度控制系统和模拟定位器系统通讯连接和电连接,用于向角度控制系统和模拟定位器系统供电并发送控制指令和接收检测信息。
11.优选地,所述支架系统包括底架部件和垂直于底架部件安装的支柱部件,所述模拟定位管部件和角度控制系统固定于支柱部件上。
12.优选地,所述底架部件底部设有多个能够调节高度的支脚。
13.优选地,所述底架部件与支柱部件之间固定连接有斜支撑架。
14.优选地,所述角度控制系统包括伺服电机、减速机和减速机吊架,伺服电机与减速机传动连接,并通过螺栓固定在一起,固定在一起的伺服电机和减速机通过减速机吊架固定于模拟定位管部件上。
15.优选地,所述模拟定位器系统包括模拟定位钩和加装了高精度倾角传感器的制式矩形铝合金定位器,模拟定位钩通过键配合安装到减速机的输出轴上,制式矩形铝合金定位器与模拟定位钩固连,并通过电机端盖及紧定螺钉固定,高精度倾角传感器固定在制式矩形铝合金定位器上。
16.优选地,所述电气系统包括供电模块、控制模块和执行模块;所述供电模块包括漏电保护器、滤波器和开关电源,将输入的ac220v电压进行稳压处理后,分为两路,1路为ac220v,供给所述伺服电机,1路通过开关电源转换为dc24v,供给控制模块和高精度传感器;控制模块包括伺服驱动器、wifi服务器和主控器,伺服驱动器受主控器控制,主控器所需角度信息通过运算,转换为伺服电机所需的固定位置,通过控制伺服驱动器执行;wifi服务器与工业平板电脑建立无线连接,将平板电脑指令接收到主控器,并将主控器相关信息反馈给工业平板电脑;主控器连接高精度倾角传感器、伺服驱动器和wifi服务器,接收工业平板电脑指令,计算确定伺服电机位置并控制伺服驱动器执行,同时接收高精度倾角传感
器数据,得到当前角度信息,形成大闭环;执行模块编码器,其通过刹车器、所述伺服电机与所述减速机执行伺服控制器给出的相应指令及反馈自身信息。
17.本发明还涉及一种接触网定位器坡度检测方法,包括如下步骤:
18.(1)打开系统电源开关;
19.(2)模拟定位器归“0”;
20.(3)设备自校;
21.(4)接收平板电脑发送过来的指令,如果指令指示模拟定位器角度与原角度相同,则模拟定位器不动,如指令指示的模拟定位器角度与原角度不同,则控制模块通过伺服电机控制模拟定位器旋转,使其运行到指定的角度。
22.优选地,模拟定位器的角度值范围为0-20度,小于0度或大于20度系统无动作。
23.本发明的接触网定位器坡度检测系统在满足测量精度的前提下,将定位器系统简化,具有占地小、操作方便、安全性高和节约成本等优点。
附图说明
24.为了更容易理解本发明的技术方案和有益的技术效果,通过参照在附图中示出的本发明的具体实施方式来对本发明进行详细的描述。该附图仅绘出了本发明的典型实施方式,并不构成对本发明的保护范围的限制,其中:
25.图1是根据本发明的一个实施方式的接触网定位器坡度检测系统的结构示意图;
26.图2是图1所示接触网定位器坡度检测系统的电气系统示意图;
27.图3是图1所示接触网定位器坡度检测系统工作流程图。
具体实施方式
28.下面将结合附图1-3对本发明作进一步的详细说明。
29.本发明设计的系统主要由支架系统、模拟定位管部件、角度控制系统、模拟定位器系统及电气系统及组成。被测产品放置于合适位置(一般是车顶安装距离),整个系统开机后,用手持无线管理系统控制模拟定位器旋转到设定角度处,模拟定位系统中的角度传感器实时反馈测得的角度值并反馈给手持无线管理系统,用于对比验证被测产品测得的数值的误差是否在合格范围内。
30.如图1所示,支架系统1是整个系统的安装基础,主要由底架部件、支柱部件及其各辅助支撑架等组成。底架部件处于系统的底部,是整个系统的基座;支柱部件及各辅助支撑架安装于底架部件上,作为模拟定位管部件2的支撑主体;支架系统设计有专门的单向支撑结构,单向托住角度控制系统3后部,减小角度控制系统因重力产生的偏差,并保证产品安全性。该支架系统1通过设计合理的底架结构,各部件通过专用的直角或特定角度连接件固定到一起,利用安装在各关键支点的支脚部件,便于调节底架的支撑状态到平衡点,结合安装在支柱部件各关键点处的斜支撑架,保证了支架系统的稳固性,避免了因底架不平及支柱部件长悬臂梁结构造成的上部结构的过度晃动,造成模拟定位器晃动而角度指示不准,致使作为检测目标的自身的误差过大,影响被测产品检验的准确性及可信性。
31.模拟定位管部件2通过专用连接件固定安装于支柱部件上,通过设计与真实定位管、定位器支座近似结构及安装位置,便于被测产品的图像算法识别出定位器,从而避免或
减少被测产品为了适应检测目标而修改算法程度,使检测结果更接近实际应用,更准确可信。
32.角度控制系统3包括伺服电机、减速机及减速机吊架。伺服电机与减速机通过4个角上的螺栓固定到一起,通过中间的抱箍把电机与减速机传动连接到一起;两个部件固定好后用4螺栓与减速机吊架安装到一起,再用专用安装螺栓安装到模拟定位管部件上。该部件的伺服电机通过接收电气系统中的控制模块发送的驱动指令,执行相应动作,包括归“0”点、给定角度、单点动作等,并设有程序自动控制功能,可一键执行系列动作,并通过自动刹车器控制动作的准确性;减速机是将伺服电机的快速转动减速到我们需要的速度,保证设备运行平稳,动作执行过程顺畅,便于被测产品识别;减速机吊架用于将合装好的伺服电机及减速机安装到模拟定位管上,同时兼顾模拟位器的限位作用,保证系统的安全性。
33.模拟定位器系统4包括模拟定位钩、加装了高精度倾角传感器的制式矩形铝合金定位器,通过2个螺栓安装到支架系统1上。模拟定位钩通过键配合安装到减速机的输出轴上,矩形铝合金定位器通过2个轴肩螺钉与模拟定位钩固连到一起,实现带动矩形铝合金定位器按需要转动的功能,并通过电机端盖及紧定螺钉固定,防止模拟定位钩从减速机轴上脱落。高精度倾角传感器通过4个螺钉固定在制式矩形铝合金定位器上。模拟定位钩参考制式定位钩的外形尺寸,对安装结构进行了适应性改进,以便于安装到角度控制系统上及模拟定位器固定成一体,并保证安装精度。为了尽可能的接近真实定位器,系统采用了制式矩形铝合金定位器,去掉了原定位钩,并在背面加装了高精度倾角传感器,不影响被测产品的识别。电源盒5通过4个螺栓安装于支柱部件上,其中安装有供电模块,用于系统的电源管理。电源盒5通过2条电缆与控制盒6连接到一起,给控制盒6供电。控制盒6通过4个螺栓安装于支柱部件上,其中安装有控制模块,用于控制系统的各功能实现。控制盒6通过4条电缆分别与伺服电机、高精度倾角传感器连接到一起,实现给伺服电机供电、控制抱闸、控制编码器、读取倾角传感器数值的功能。
34.如图2所示,所述电气系统包括供电模块、控制模块和执行模块;所述供电模块包括漏电保护器、滤波器和开关电源,将输入的ac220v电压进行稳压处理后,分为两路,1路为ac220v,供给所述伺服电机,1路通过开关电源转换为dc24v,供给控制模块和高精度传感器;控制模块包括伺服驱动器、wifi服务器和主控器,伺服驱动器受主控器控制,主控器所需角度信息通过运算,转换为伺服电机所需的固定位置,通过控制伺服驱动器执行;wifi服务器与工业平板电脑建立无线连接,将平板电脑指令接收到主控器,并将主控器相关信息反馈给工业平板电脑;主控器连接高精度倾角传感器、伺服驱动器和wifi服务器,接收工业平板电脑指令,计算确定伺服电机位置并控制伺服驱动器执行,同时接收高精度倾角传感器数据,得到当前角度信息,形成大闭环;执行模块编码器,其通过刹车器、所述伺服电机与所述减速机执行伺服控制器给出的相应指令及反馈自身信息。
35.工业平板电脑搭载win10系统,在其上配置了本系统配套的专用应用软件,用于查看设备状态,执行操作命令,反馈命令信息等。
36.如图3所示,打开系统电源开关,上电启动后模拟定位器将自动运行到“0”点,在此处,主控器将进行设备自检,得到“0”点与水平位置的差值,之后接收平板电脑发送过来的指令,如果指令指示模拟定位器角度与原角度相同,则模拟定位器不动,如指令指示的模拟定位器角度与原角度不同,则模拟定位器将运行到指定的角度。装置一直处于接收指令状
态,平板电脑最迟500ms会发送一次指令到装置。
37.控制模块通过伺服系统控制模拟定位器旋转,设定模拟定位器的角度值范围为(0-20)度,小于0度或大于20度系统无动作,以保护系统自身。伺服系统角度分辨率为0.001度,倾角传感器精度为0.005度,系统整体角度精度≤0.1度。
38.本发明可以以其他具体的形式进行体现,但并不会脱离本发明的保护范围,本发明的保护范围仅由所附的权利要求限定。