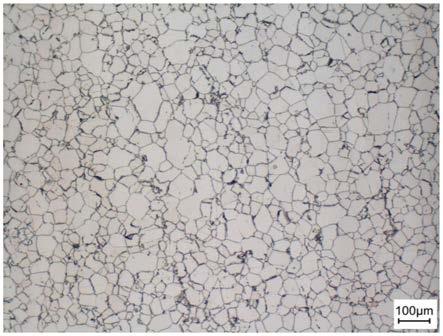
一种gh4169高温合金晶粒腐蚀剂及其应用
技术领域
1.本发明属于金相检测技术领域,具体为一种gh4169高温合金晶粒腐蚀剂及其应用。
背景技术:2.金相检验是高温合金研究和产品研制过程中分析材料显微组织、结构与性能之间联系、优化工艺、提升产品质量的重要手段。金相腐蚀是金相检验中的一项重要工作,合适的腐蚀剂及其配制和使用方法对合金的组织形貌显示具有重要的作用。
3.gh4169是上世纪70年代我国研制的以体心四方γ
″
相和面心立方γ
′
沉淀强化的变形高温合金,是我国高温合金中的骨干材料,由于在-253℃—650℃范围内具有强度高、抗氧化、耐腐蚀、热加工和焊接性能好等优点,在航空航天、核电、燃机、石化等领域得到广泛应用,目前已成为我国用量最大、用途最广、产品种类和规格最全的一类高温合金,其中,在航空发动机中,gh4169合金大量用于制造高压压气机盘、涡轮盘、锻造叶片等关键零部件。然而,由于gh4169合金合金化程度高,容易产生偏析和组织不均匀的现象,目前主要通过金相检测,分析合金中碳化物、碳氮化物、δ相、晶粒度来评判gh4169合金制件的质量,尤其晶粒尺寸对合金的强度、塑性、韧性具有很大的影响。目前,gh4169合金晶粒度常采用甲醇、盐酸混合液电解或用kalling腐蚀剂进行腐蚀,采用甲醇、盐酸混合液电解腐蚀的方法容易腐蚀出δ相,干扰晶粒度的评定,采用kalling腐蚀剂对gh4169高温合金腐蚀时,有时晶界不能完全显示,腐蚀出的晶界模糊不清,容易造成晶粒度评定误差。
4.金相检测是科研和企业在产品研发和生产过程中掌握产品的组织结构和晶粒度,提升产品品质,同时对生产过程出现的质量问题进行分析,进而改变和优化工艺参数,金相腐蚀是金相检测的首要任务,只有利用合适的腐蚀剂腐蚀出产品清晰的晶界,避免干扰相的出现,才能进行晶粒度的评定。
技术实现要素:5.本发明的目的是针对现有技术中存在的问题,提供一种针对gh4169高温合金并能快速腐蚀出合金的晶界的腐蚀剂,且避免δ干扰相的大量出现。
6.为了实现以上发明目的,本发明的具体技术方案为:
7.一种gh4169高温合金晶粒腐蚀剂,由以下成分组成:浓盐酸、过氧化氢、三氯化铁。该三种组分的配比为浓盐酸:过氧化氢:三氯化铁等于90-100ml:2-4ml:5-10g。较通用的kalling腐蚀剂而言,该腐蚀剂未添加水或无水乙醇等稀释剂,腐蚀剂中未引入对δ敏感的含cu
2+
盐组元(如cucl2、cuso4等),避免δ干扰相的大量出现。通过浓盐酸提供强酸性,三氯化铁和过氧化氢增加腐蚀液氧化特性,本方案中的浓盐酸不宜用浓硫酸和浓硝酸替代,浓硫酸和浓硝酸易与过氧化氢发生化学反应分解出气体,在密闭空间有爆炸危险。
8.作为本技术中一种较好的实施方式,浓盐酸:过氧化氢:三氯化铁等于95ml:3ml:7.5g。
9.作为本技术中一种较好的实施方式,所述的浓盐酸为分析纯,质量百分浓度为36%-38%。
10.作为本技术中一种较好的实施方式,所述的过氧化氢为分析纯,质量百分浓度为30%。
11.作为本技术中一种较好的实施方式,所述的三氯化铁(fecl3·
6h2o)为分析纯,纯度≥99%。
12.本发明的另一目的是提供一种gh4169合金高温合金晶粒腐蚀剂的配制方法,该方法包括以下步骤:先按比例称取三氯化铁放入烧杯中,量取盐酸倒入此烧杯中,再量取过氧化氢倒入此烧杯中,用玻璃棒搅拌直至三氯化铁完全融化,即得。
13.本发明的第三个发明目的是提供一种以上所述gh4169合金高温合金晶粒腐蚀剂的使用方法,该方法方法简单,易与操作,使用方法包括以下步骤:
14.s1、对锻后热处理态gh4169合金制件进行取样,并用线切割机切成金相试样;
15.s2、用镶嵌机将步骤s1中切取的试样镶嵌成规则的圆形试样;
16.s3、利用不同粒度金相水砂纸对试样进行研磨;
17.s4、在抛光机上采用金刚石研磨膏对金相试样进行抛光;
18.s5、用清水对抛光后的试样表面进行清洗,随后用无水乙醇冲洗,再用吹风机吹干;
19.s6、将冲洗后的试样放入配置好的gh4169高温合金金相腐蚀剂中,腐蚀液完全浸湿试样表面,腐蚀10-20秒;
20.s7、用清水对腐蚀后的金相试样表面进行冲洗,随后用无水乙醇清洗;
21.s8、用吹风机吹干被腐蚀的表面,用金相显微镜观察金相组织。
22.作为本技术中一种较好的实施方式,所述步骤s1中用线切割机切成15mm
×
15mm
×
15mm的金相试样。
23.作为本技术中一种较好的实施方式,所述步骤s3中先用120目、400目、800目的金相水砂纸对试样进行研磨,再利用1000目、1200目的金相水砂纸进行研磨。
24.作为本技术中一种较好的实施方式,所述步骤s4中抛光机的转速为1200r/min,利用1.5um金刚石研磨膏对金相试样进行抛光,抛光5分钟后观察金相试样表面光亮无划痕时,换干净的抛光布,用清水作润滑剂,抛光1分钟。
25.以浓盐酸、过氧化氢、三氯化铁配制的混合溶液作为腐蚀剂,其腐蚀原理是:一些溶质元素和杂质元素容易在晶界处富集,使得晶界和晶粒内部的电极电位不同,其金相试样腐蚀是电化学腐蚀的过程,在腐蚀液中,形成局部原电池,具有较高负电极电位的晶界为阳极,被溶入腐蚀液中而凹下去,具有较高正电位的晶粒内部保持原来平整高度不变。因而在显微镜下可以清楚看到结晶形貌。
26.与现有技术相比,本发明的积极效果体现在:
27.(一)本发明的gh4169高温合金晶粒腐蚀剂能快速高效地腐蚀出gh4169合金的晶粒形貌,腐蚀效果好,晶界清晰,晶粒完整,避免δ相显示干扰,使产品的晶粒形貌得以观察,便于利用金相显微镜准确测量其晶粒度,通过晶粒度的测量调整和优化gh4169合金的工艺参数,掌握和提升gh4169合金产品质量。
28.(二)本发明可以使科研工作者及生产企业对研发和生产的gh4169合金产品的晶
粒形貌进行测量,判断产品是否满足客户的需求,通过调整工艺参数提高产品质量,降低废品率,为科研和生产带来非常可观的经济效益。
附图说明
29.图1为100ml甲醇+100ml盐酸+3ml过氧化氢,3v电压电解腐蚀10秒gh4169高温合金金相组织图。
30.图2为kalling腐蚀剂:100ml无水乙醇+100ml盐酸+5g氯化铜,化学腐蚀20秒gh4169高温合金金相组织图。
31.图3为本发明实施例1中gh4169合金腐蚀后金相组织图。
32.图4为本发明实施例2中gh4169合金腐蚀后金相组织图。
33.图5为本发明实施例3中gh4169合金腐蚀后金相组织图。
具体实施方式
34.一种gh4169高温合金晶粒腐蚀剂由以下成分组成:浓盐酸、过氧化氢、三氯化铁。该三种组分的配比为浓盐酸:过氧化氢:三氯化铁等于90-100ml:2-4ml:5-10g。
35.进一步地,三种组分配比为浓盐酸:过氧化氢:三氯化铁等于95ml:3ml:7.5g。
36.进一步地,所述的浓盐酸为分析纯,质量百分浓度为36%-38%。
37.进一步地,所述的过氧化氢为分析纯,质量百分浓度为30%。
38.进一步地,所述的三氯化铁(fecl3·
6h2o)为分析纯,纯度≥99%。
39.一种gh4169高温合金晶粒腐蚀剂的配制方法,该方法包括以下步骤:先称取三氯化铁放入烧杯中,量取盐酸倒入此烧杯中,再量取过氧化氢倒入此烧杯中,用玻璃棒搅拌直至三氯化铁完全融化。
40.一种gh4169高温合金晶粒腐蚀剂的使用方法,该方法包括以下步骤:
41.s1、对锻后热处理态gh4169合金制件进行取样,并用线切割机切成金相试样;
42.s2、用镶嵌机将步骤s1中切取的试样镶嵌成规则的圆形试样;
43.s3、利用不同粒度金相水砂纸对试样进行研磨;
44.s4、在抛光机上采用金刚石研磨膏对金相试样进行抛光;
45.s5、用清水对抛光后的试样表面进行清洗,随后用无水乙醇冲洗,再用吹风机吹干;
46.s6、将冲洗后的试样放入配置好的gh4169高温合金金相腐蚀剂中,腐蚀液完全浸湿试样表面,腐蚀10-20秒;
47.s7、用清水对腐蚀后的金相试样表面进行冲洗,随后用无水乙醇清洗;
48.s8、用吹风机吹干被腐蚀的表面,用金相显微镜观察金相组织。
49.进一步地,所述步骤s1中用线切割机切成15mm
×
15mm
×
15mm的金相试样。
50.进一步地,所述步骤s3中先用400目、800目、1000目的金相水砂纸对试样进行研磨,再利用1500目、2000目的金相水砂纸进行研磨。
51.进一步地,所述步骤s4中抛光机的转速为1200r/min,利用2.5um金刚石研磨膏对金相试样进行抛光,抛光5分钟后观察金相试样表面光亮无划痕时,换干净的抛光布,用清水作润滑剂,抛光1分钟。
52.为了使本发明的目的、技术方案及优点更加清楚明白,下面结合具体实施方式对本发明作进一步的详细描述,但不应将此理解为本发明上述主题的范围仅限于下述实施例。在不脱离本发明上述技术思想情况下,根据本领域普通技术知识和惯用手段,做出各种替换和变更,均应包括在本发明的范围内。
53.本技术文件中所采用的原料,如无特殊说明外,均为市售产品。
54.实施例1:
55.一种gh4169高温合金晶粒腐蚀剂,由以下含量组分组成:95ml浓盐酸+3ml过氧化氢+7.5g三氯化铁,其中浓盐酸的质量百分浓度为36-38%,过氧化氢的质量百分浓度为30%,三氯化铁(fecl3·
6h2o)的纯度≥99%,各化学试剂均为分析纯。腐蚀时间为15秒。
56.配制该gh4169高温合金晶粒腐蚀剂时,先称取7.5g三氯化铁放入容量为150ml的烧杯中,量取95ml盐酸倒入此烧杯中,再量取3ml过氧化氢倒入此烧杯中,用玻璃棒搅拌直至三氯化铁完全融化。
57.使用该gh4169高温合金晶粒腐蚀剂时,先对某企业锻造后热处理态的gh4169高温合金进行取样,并用线切割机切成15mm
×
15mm
×
15mm的金相试样,用镶嵌机将切取的试样镶嵌成φ40mm的圆形试样;然后用400目、800目、1000目的金相水砂纸对试样进行研磨,再利用1500目、2000目的金相水砂纸进行研磨;然后在转速为1200r/min的抛光机上利用2.5um金刚石研磨膏对金相试样进行抛光,磨抛5分钟后观察金相试样表面光亮无划痕时,换干净的抛光布,用清水作润滑剂,抛光1分钟;用清水对抛光后的试样表面进行清洗,随后用无水乙醇冲洗,再用吹风机吹干;将冲洗后的试样放入配制好的gh4169高温合金金相腐蚀剂中,腐蚀液完全浸湿试样表面,用秒表及时器进行计时,当腐蚀时间达到15秒后,用竹夹夹出试样,用清水对腐蚀后的金相试样表面进行冲洗,随后用无水乙醇清洗,再用吹风机吹干被腐蚀的表面后用金相显微镜观察金相组织。
58.从图3可以看出,该gh4169高温合金晶粒腐蚀液的腐蚀效果非常好,晶界清晰,晶粒显示完整,没有δ相的干扰,便与利用金相显微镜准确测量其晶粒度。
59.实施例2:
60.一种gh4169高温合金晶粒腐蚀剂,由以下含量组分组成为90ml浓盐酸+2ml过氧化氢+5g三氯化铁,其中浓盐酸的质量百分浓度为36-38%,过氧化氢的质量百分浓度为30%,三氯化铁(fecl3·
6h2o)的纯度≥99%,各化学试剂均为分析纯。腐蚀时间为20秒。
61.配制该gh4169高温合金晶粒腐蚀剂时,先称取5g三氯化铁放入容量为150ml的烧杯中,量取90ml盐酸倒入此烧杯中,再量取2ml过氧化氢倒入此烧杯中,用玻璃棒搅拌直至三氯化铁完全融化。
62.使用该gh4169高温合金晶粒腐蚀剂时,先对某企业锻造后热处理态的gh4169高温合金进行取样,并用线切割机切成15mm
×
15mm
×
15mm的金相试样,用镶嵌机将切取的试样镶嵌成φ40mm的圆形试样;然后用400目、800目、1000目的金相水砂纸对试样进行研磨,再利用1500目、2000目的金相水砂纸进行研磨;然后在转速为1200r/min的抛光机上利用2.5um金刚石研磨膏对金相试样进行抛光,磨抛5分钟后观察金相试样表面光亮无划痕时,换干净的抛光布,用清水作润滑剂,抛光1分钟;用清水对抛光后的试样表面进行清洗,随后用无水乙醇冲洗,再用吹风机吹干;将冲洗后的试样放入配制好的gh4169高温合金金相腐蚀剂中,腐蚀液完全浸湿试样表面,用秒表及时器进行计时,当腐蚀时间达到20秒后,用竹
夹夹出试样,用清水对腐蚀后的金相试样表面进行冲洗,随后用无水乙醇清洗,再用吹风机吹干被腐蚀的表面后用金相显微镜观察金相组织。
63.从图4可以看出,该gh4169高温合金晶粒腐蚀液的腐蚀效果非常好,晶界清晰,晶粒显示完整,没有δ相的干扰,便与利用金相显微镜准确测量其晶粒度。
64.实施例3:
65.一种gh4169高温合金晶粒腐蚀剂,由以下含量组分组成为100ml浓盐酸+4ml过氧化氢+10g三氯化铁,其中浓盐酸的质量百分浓度为36-38%,过氧化氢的质量百分浓度为30%,三氯化铁(fecl3·
6h2o)的纯度≥99%,各化学试剂均为分析纯。腐蚀时间为10秒。
66.配制该gh4169高温合金晶粒腐蚀剂时,先称取10g三氯化铁放入容量为150ml的烧杯中,量取100ml盐酸倒入此烧杯中,再量取4ml过氧化氢倒入此烧杯中,用玻璃棒搅拌直至三氯化铁完全融化。
67.使用该gh4169高温合金晶粒腐蚀剂时,先对某企业锻造后热处理态的gh4169高温合金进行取样,并用线切割机切成15mm
×
15mm
×
15mm的金相试样,用镶嵌机将切取的试样镶嵌成φ40mm的圆形试样;然后用400目、800目、1000目的金相水砂纸对试样进行研磨,再利用1500目、2000目的金相水砂纸进行研磨;然后在转速为1200r/min的抛光机上利用2.5um金刚石研磨膏对金相试样进行抛光,磨抛5分钟后观察金相试样表面光亮无划痕时,换干净的抛光布,用清水作润滑剂,抛光1分钟;用清水对抛光后的试样表面进行清洗,随后用无水乙醇冲洗,再用吹风机吹干;将冲洗后的试样放入配制好的gh4169高温合金金相腐蚀剂中,腐蚀液完全浸湿试样表面,用秒表及时器进行计时,当腐蚀时间达到10秒后,用竹夹夹出试样,用清水对腐蚀后的金相试样表面进行冲洗,随后用无水乙醇清洗,再用吹风机吹干被腐蚀的表面后用金相显微镜观察金相组织。
68.从图5可以看出,该gh4169高温合金晶粒腐蚀液的腐蚀效果非常好,晶界清晰,晶粒显示完整,没有δ相的干扰,便与利用金相显微镜准确测量其晶粒度。
69.前述本发明基本例及其各进一步选择例可以自由组合以形成多个实施例,均为本发明可采用并要求保护的实施例。本发明方案中,各选择例,与其他任何基本例和选择例都可以进行任意组合。本领域技术人员可知有众多组合。
70.以上所述仅为本发明的较佳实施例而已,并不用以限制本发明,凡在本发明的精神和原则之内所作的任何修改、等同替换和改进等,均应包含在本发明的保护范围之内。