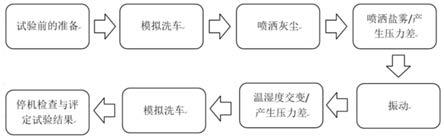
1.本发明属于汽车领域,具体涉及一种空腔内的循环腐蚀试验方法。
背景技术:2.汽车质量网上公开的车门和侧围出现锈穿现象,且不是个例。这说明汽车设计阶段未能进行有效的腐蚀实验,没有及时发现此问题,导致产品上市后,用户在使用过程中出现车门和侧围腐蚀现象。以上问题的发现,不仅产品销售,而且影响企业形象,给企业带来损失。
3.现有技术中,针对白车身和车门常规的静态腐蚀试验,显然不能反应车门和侧围出现锈穿的问题,进而不能提供给汽车设计者有效信息以解决上述问题。
4.如何有效的提供产品腐蚀信息,以在设计阶段解决汽车在使用过程中车门和侧围腐蚀的问题十分必要。
技术实现要素:5.本发明的目的在于提供一种空腔内的循环腐蚀试验方法,用于整车、白车身或四门两盖系统组件的循环腐蚀试验,此方法由静态盐雾试验方法与振动台架相结合的方式,通过试验开始前喷洒灰尘,通过振动和清洗,再结合空腔内外压力差,将灰尘、盐雾、温湿度的变化压入空腔内,加速空腔内的腐蚀,能发现车身结构设计的是否合理,此试验结果为车身结构优化提供理论依据。
6.本发明具体技术方案如下:
7.一种空腔内的循环腐蚀试验方法,包括以下步骤:
8.1)试样清洗;
9.2)喷洒灰尘;
10.3)喷洒盐雾;
11.4)振动;
12.5)湿度交变;
13.6)试样再清洗。
14.步骤1)中所述试样为整车、白车身、四门或两盖的系统组件;以上试样带空腔,进行循环腐蚀试验,可以更好的反应空腔腐蚀情况,以为后续改进提供参考。
15.进一步的,对于白车身为试样的,清洗前进行密封,密封方案采用工装件进行密封,若工装件不满足装车要求时,采用密封材料对工艺孔密封,密封材料不能加速接触面的腐蚀。试样密封后需进行密封性测试。
16.步骤1)试样清洗具体为:在室温下,用水清洗试样,试样表面清洗干净后晾干或擦拭干净后备用;优选的用三级水清洗;
17.步骤1)中,试样清洗是为了模拟洗车,汽车在使用过程中,车辆会接触到雨水和洗车用水,水流会顺着安装件的缝隙流入试样的空腔内(车门、车身等带有空腔的零部件),并
沿着空腔内壁往下走,一部分水流通过排水孔流出,一部分水流会堆积在流水不畅的两板搭接处,此处长期处于潮湿环境中,又经过温湿度变化,堆积处的水膜会经过由厚变薄再变厚的循环过程,加速水膜接触面的腐蚀。
18.步骤2)中所述喷洒灰尘是指取盐灰混合液均匀的喷洒在试验表面,使试样表面处理湿润状态,存在试样表面的盐灰混合液会随着后续盐雾阶段和温湿度阶段形成的水膜流入搭接件的缝隙中,最后进入空腔内,遇到温湿度变化试验,会加速空腔内的电化学腐蚀。
19.所述盐灰混合液是指10g/l
±
0.2g/l的盐灰混合液;所述盐灰混合液具体配置方法为:用水配置50g/l
±
5g/l的氯化钠溶液,取灰尘置于上述氯化钠溶液中混匀,配出灰尘浓度10g/l
±
0.2g/l的盐灰混合液;所使用灰尘满足:iso 12103-1 a2 fine test dust;所用水为三级水;
20.步骤2)中喷洒量按每平方米0.5
±
0.05l进行;
21.步骤2)喷洒灰尘后需静置30min
±
5min备用。
22.步骤3)中喷洒盐雾是50g/l
±
5g/l的氯化钠溶液作为电解液,连续喷洒60
±
5min,在35℃
±
2℃条件下进行;其中,在盐雾喷洒的20
±
5min后,对试样空腔抽负压40
±
5min,盐雾进入空腔内。盐雾的沉淀量控制在2-5ml/80cm2.h,盐雾回收液的ph 6.5-7.2;抽负压采用真空泵进行,优选为藤原1550d,压力大小适宜。有利于盐雾进入空腔,更好的模拟腐蚀试验。
23.步骤3)试验后静置10
±
2min备用。
24.步骤3)具体方法为:将步骤2)处理好的试样放置于多功能腐蚀试验舱内,采用摇臂式喷头与固定喷头相结合的喷雾方式,达到一定量的腐蚀强度和腐蚀均匀度,考察试样的耐腐蚀性能;喷洒盐雾是50g/l
±
5g/l的氯化钠溶液,连续喷洒60min
±
5min小时,其中,在盐雾喷洒的20
±
5min后,对试样空腔抽负压40
±
5min;盐雾的沉淀量控制在2-5ml/80cm2.h,盐雾回收液的ph 6.5-7.2;
25.步骤3)盐雾喷洒阶段试样是静止的,喷洒的流量能满足沉淀量的要求即可。
26.步骤4)中所述振动,时间控制在120min
±
10min,模拟车辆在日常使用过程中的短期行驶过程的振动试验。可根据实际情况选择振动程序,安装调试后开启振动。试样相邻的零部件在振动下会产生相对运动,焊接及搭接处会产生细小的裂纹或缝隙,在整个循环试验过程中,腐蚀介质会进入细小的裂纹及缝隙处,使其发生电化学腐蚀。步骤4)振动利用mts四立柱道路模拟试验机或侧门系统耐久试验台进行。试样为四门或两盖的系统组件采用侧门系统耐久试验台,试样为整车的采用mts四立柱道路模拟实验,试样为白车身的需搭载整车做mts四立柱道路模拟实验。
27.步骤5)湿度交变过程,试验样件移至温湿度交变箱,在整个湿度交变过程中,温度维持不变,仅湿度发生变化;湿度交变按照以下程序依次进行:15分钟温湿度上升至50℃
±
2℃/(95
±
5)%rh—50℃
±
2℃/(95
±
5)%rh存放2小时—50℃
±
2℃/(95
±
5)%rh空腔内抽负压1小时—50℃
±
2℃/(95
±
5)%rh存放6小时20分钟—70
±
5min湿度下降至50℃
±
2℃/(60
±
5)%rh—15
±
2min湿度上升50℃
±
2℃/(85
±
5)%rh—50℃
±
2℃/80-90%rh存放10h
±
10min。
28.通过以上湿度交变过程,模拟实际行驶过程中湿-干-湿的过程,更好的模拟汽车在行驶过程中环境变化,反应实际汽车的空腔腐蚀因素,使腐蚀测试结果更准确。
dust;取一定量的盐灰混合液均匀的喷洒在车门表面,使车门表面处理湿润状态,此步骤不需要振动,存在试样表面的盐灰混合液会随着盐雾阶段和温湿度阶段形成的水膜流入车门搭接件的缝隙中,最后进入空腔内;再遇到温湿度变化试验,会加速空腔内的电化学腐蚀;喷洒量按每平方米0.5l进行,喷洒灰尘后需静置30min再进行步骤3);
45.3)喷洒盐雾:以50g/l的氯化钠溶液作为电解液,将步骤2)处理好的车门放置于腐蚀试验舱内,盐雾喷洒阶段的温度为35℃,其中,在盐雾喷洒的25分钟后,对试样抽负压45分钟(采用藤原1550d),抽负压过程中同时进行盐雾喷洒,盐雾的沉淀量控制在3.0~4.0ml/80cm2.h,盐雾回收液的ph 6.5~7.2,喷洒过程中试样处于静止状态,试验后静置10min再进行步骤4)。
46.4)振动耐久:将步骤3)试验后的车门转移至车门耐久试验台,安装调试后开启2个小时的耐久试验,试样相邻的零部件在振动下会产生相对运动,焊接及搭接处会产生细小的裂纹或缝隙,在整个循环试验过程中,腐蚀介质会进入细小的裂纹及缝隙处,使其发生电化学腐蚀。
47.5)温湿度交变过程:将步骤4)试验后的车门移至温湿度交变箱,温湿度交变程序:15min温湿度上升至50℃/95%rh—50℃/95%rh存放120min—50℃/95%rh抽负压60min—50℃/95%rh存放380min分钟—50℃条件下70min湿度下降至60%rh—50℃条件下15min湿度上升至85%rh—50℃/85%rh存放600min。通过温湿度的交替变化,使试样表面处于“湿-干-湿”交替过程。
48.步骤6)再进行清洗:把车门表面残留的灰尘和盐份清洗干净,便于后续的试验开展和试验结果的评定。
49.步骤1)-步骤6)作为一个循环,共6个循环试验结束后,需对车门表面和空腔内进行腐蚀评价并记录,进行定性或对腐蚀深度评价;
50.试验结束后,需对车门表面和空腔内进行腐蚀评价并记录。通过试验后的剖解图片(图2、图3)可以得出,此试验方法出现的锈蚀位置与售后失效位置(图1)相吻合。从图1可以看出,售后失效位置为车门下边,图1中圈出的位置为车辆使用一段时间后的腐蚀位置,图2、图3中圈出的位置为实验后锈蚀的位置,与图1位置相吻合,本发明方法可以有效反应真实腐蚀情况,设计根据可根据本发明加速空腔内的腐蚀的方法,发现车身结构设计的是否合理,为车身结构优化提供理论依据。