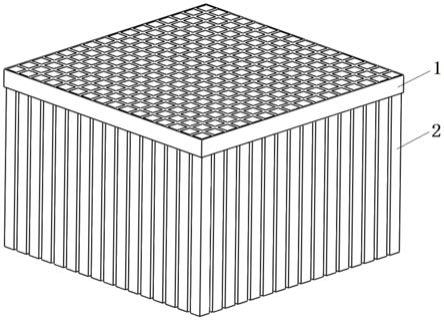
1.本发明属于催化剂磨损测量判定领域,具体涉及一种催化剂磨损判定方法。
背景技术:2.催化剂是scr脱硝工艺的核心,被广泛应用于燃煤电厂烟气净化系统中。其中,蜂窝式催化剂应用广泛,其基材采用二氧化钛加活性成分一体压制煅烧成型。由于我国电厂普遍采用高温高尘布置,烟气中飞灰含量高,烟气携带飞灰对催化剂端面进行冲刷,造成催化剂磨损。催化剂单体紧密安装在催化剂模块内,催化剂模块亦紧密相靠安装于脱硝反应器内。随反应时间延长,被烟气吹损的催化剂的磨损情况无法清晰反映,也就无法得知催化剂的磨损原因。
3.而准确的掌握磨损的区域位置及磨损的程度,对电厂意义重大,具体如下:1、若磨损区域比较明显有规则,则说明脱硝反应器流场存在问题,烟气流速和入射角存在偏斜,是流场优化的有力的佐证;2、若局部区域磨损严重,电厂可根据此情况准备替换单体,避免此处发生坍塌穿孔;3、根据磨损情况,电厂可以评估催化剂再生的可行性,及时准备填充的单体数量。
技术实现要素:4.本发明的目的是提供一种催化剂磨损判定方法,以解决现有无法清晰得到被烟气吹损的催化剂的磨损情况及无法得知催化剂磨损原因的问题。
5.为达到上述目的,本发明采用的技术方案是:一种催化剂磨损判定方法,其包括如下步骤:s1、准备基准台、测柱,基准台具有上表面、位于上表面下的下表面,基准台上开设有多个贯通其上表面和下表面的安装孔,安装孔的位置与催化剂上孔的位置对应,测柱可活动地穿设在基准台上的安装孔内;s2、将测柱对应该催化剂模块的单元体上的孔后下压基准台,直至基准台的下表面与该单元体的上表面相抵,再检测得到每个测柱伸出基准台的距离;s3、计算测柱伸出基准台的距离与该测柱的长度的差值,该差值为该单元体对应的孔的磨损长度;s4、根据磨损长度设置催化剂磨损等级,并基于该催化剂模块的每个单元体在脱硝反应器中的位置,制作记载有单元体对应所属磨损等级的磨损分布图,其中,每个单元体对应的磨损等级在磨损分布图中的位置与该单元体在脱硝反应器中的位置一致。
6.优选地,所述的测量方法还包括:s5、建立脱硝反应器流场三维模型,获得脱硝反应器内需要测试的催化剂模块上游流场流速分布图;s6、将步骤s5中磨损分布图中对应不同磨损等级的不同磨损区域,与步骤s5中流场流速分布图对应该磨损区域的流场的烟气流速分布区域进行比对,以分析不同磨损区域
的催化剂磨损的原因。
7.优选地,步骤s1中,所述的基准台的上表面与下表面平行;所述的测柱设置有多个,所述的测柱具有上表面、位于所述的上表面下的下表面,所述的测柱的上表面与下表面平行,每一个测柱的长度相等。
8.优选地,步骤s1中,每一个所述的测柱的上表面与所述的基准台的上表面均齐平,所述的测柱的下表面位于所述的基准台的下表面下。
9.优选地,步骤s2中,通过检测部件检测所述的测柱伸出基准台的间距;步骤s3中,通过控制单元计算测柱伸出基准台的间距与该测柱的长度的差值。
10.优选地,步骤s4中,基于该单元体上孔的分布,制作记载有每个孔对应所属磨损等级的磨损分布图,其中,每个孔对应的磨损等级在磨损分布图中的位置与该孔在单元体上的位置一致。
11.优选地,步骤s4中,将需要测试的催化剂模块分为多个区域,每个区域包含多个单元体,对每个单元体均进行测试,得到每个单元体上孔对应的所属磨损等级;再将每个区域的多个单元体的磨损等级进行平均得到平均磨损等级,基于该区域在脱硝反应器中的位置,制作记载有每个区域对应所属磨损等级的磨损分布图。
12.优选地,步骤s4中,磨损等级划分为0、ki,0代表无磨损,ki代表磨损长度大于0。
13.优选地,ki 设定为1、2、3、4,1代表磨损长度大于等于15cm,2代表磨损长度为10~15cm,3代表磨损长度为5cm~10cm,4代表磨损长度小于等于5cm。
14.优选地,步骤s2中,当基准台的下表面与该单元体的上表面相抵时,测柱始终穿设在基准台上的安装孔内。
15.由于上述技术方案运用,本发明与现有技术相比具有下列优点:本发明提供的催化剂磨损测量判定方法,可获得催化剂磨损分布准确的可视化图像,基于磨损分布图和需要测试的催化剂模块上游流场流速分布图,可进一步判定催化剂磨损原因,为脱硝反应器内流场改造提供有力佐证。同时,通过对催化剂的磨损测量及可视化分析,可以准确统计催化剂磨损的总量,为电厂采购替换单体提供了准确依据;可清楚得知催化剂的磨损情况,根据磨损情况,电厂可以评估催化剂再生的可行性,及时准备填充的单体数量。
附图说明
16.附图1为基准台的结构示意图;附图2为基准台的俯视图;附图3为测柱的结构示意图;附图4为基准台、测柱在初始状态下的结构示意图;附图5为基准台、测柱在初始状态下的侧视图;附图6为基准台、测柱在测试状态下的结构示意图;附图7为实施例的磨损分布图;附图8为实施例的脱硝反应器的流场速度图;附图9为实施例的催化剂上游流场速度分布图。
17.以上附图中,1-基准台,11-基准台的上表面,12-安装孔,2-测柱,3-催化剂模块截面,4-流场分
布截面。
具体实施方式
18.下面结合附图所示的实施例对本发明作进一步描述。
19.一种催化剂磨损判定方法,其包括如下步骤:s1、准备基准台1、测柱2,基准台1具有上表面11、位于上表面下的下表面,基准台1上开设有多个贯通其上表面和下表面的安装孔12,安装孔12的位置与催化剂上孔的位置对应,测柱2可活动地穿设在基准台1上的安装孔12内;基准台1的结构如下:参见图1和图2,其具有上表面11、位于上表面下的下表面,基准台1的上表面11与下表面平行,基准台1上开设有多个贯通上表面11和下表面的安装孔12,安装孔12为通孔,安装孔12的位置与待测量的催化剂上孔的位置对应。
20.测柱2的结构如下:参见图3,测柱2为长条形,测柱2设置有多个,每一个测柱2可活动地穿设在基准台1的安装孔12内。测柱2具有上表面、位于上表面下的下表面,测柱2的上表面与下表面平行。每一个测柱2的长度均相等,当计算测柱2伸出基准台1的距离时,计算简单。测柱2均布在基准台1的安装孔12内,测柱2数量与待测催化剂单元体孔数一致(一般为18
×
18,20
×
20,22
×
22)。
21.基准台1的安装孔12、测柱2的截面与待测量的催化剂上的孔的截面一致,如截面为方形、圆形或波浪形。在测试时,测柱2不会伸入催化剂的孔内,若测柱2、待测量的催化剂上的孔的截面均为正方形,测柱2的边长略大于待测量的催化剂上的孔的边长。
22.基准台1的截面与待测量的催化剂的上表面一致,如待测量的催化剂的上表面为方形,基准台1的截面为方形,基准台1为方体。
23.催化剂的孔的磨损长度小于或等于催化剂的孔的长度,则测柱2的长度小于或等于催化剂的孔的长度,如测柱2的长度范围为5-100cm,测柱2长度可为20~30cm。或者,如测柱2的长度大于催化剂的孔的长度的四分之一。
24.s2、确定需要测试的催化剂模块,该模块包括多个单元体,将测柱2对应该催化剂模块的单元体上的孔后下压基准台1,直至基准台1的下表面与该单元体的上表面相抵,再检测得到每个测柱2伸出基准台1的距离。步骤s2为测试状态。
25.在步骤s1中(初始状态),每一个测柱2的上表面与基准台1的上表面11均齐平,或每一个测柱2的上表面与基准台1的上表面11之间保持间距,测柱2的下表面位于基准台1的下表面下,以每一个测柱2的上表面与基准台1的上表面11均齐平为最优,便于在检测状态下检测部件检测每一个测柱2伸出基准台1的距离。
26.测试时的工作过程如下:将每个测柱2对应催化剂的孔,按压基准台1,直至基准台1的下表面与催化剂的上表面相抵,此时每一个测柱2的下表面与催化剂对应的孔边沿相抵,测柱2不会伸入催化剂的孔内。
27.在初始状态、测试状态下,测柱2始终穿设在基准台1上的安装孔12内不会脱离基准台1,即测试柱不会脱离基准台1的安装孔12,则测柱2与基准台1上的安装孔12紧密配合,具体是指:在初始状态(测柱2未受力)下,测柱2不会在安装孔12内上下移动,可自由固定,即测柱2位置不变;当测试时,对基准台1施加力,测柱2可在安装孔12内上下移动。
28.测柱2的上端设置有防脱部,防脱部与基准台1上的安装孔12相配合,防脱部用于
限制测柱2在自身重力作用下向下移动而脱离基准台1上的安装孔12。防脱部与测柱2呈t型,基准台1上的安装孔12为相对应的台阶孔,使得初始状态下,防脱部的上表面与基准台1的上表面11齐平;或基准台1上的安装孔12不是台阶孔而是直径统一的通孔,在初始状态下,防脱部的上表面高于基准台1的上表面11,在测试过程中不影响测试结果。
29.基准台1、测柱2均由金属制成,如不锈钢。
30.s3、计算测柱2伸出基准台1的距离与该测柱2的长度的差值,该差值为该单元体对应的孔的磨损长度;通过控制单元计算测柱2伸出基准台1的间距与该测柱2的长度的差值,控制单元用于接收检测部件发送的检测结果,并根据检测结果计算测柱2伸出基准台1的距离与该测柱2的长度的差值,该差值为催化剂的孔的磨损长度;通过检测部件检测测柱2伸出基准台1的间距,若在初始状态下,每一个测柱2的上表面与所述的基准台1的上表面11均齐平,在测试状态下,测柱2伸出基准台1的间距为测柱2的上表面与基准台1的上表面11之间的间距。
31.检测部件选用距离传感器,距离传感器设置在基准台1上表面,距离传感器可设置多个,多个距离传感器与多个测柱2一一对应。距离传感器可能是pcr雷达传感器,或者,红外测距传感器,或者,超声波测距传感器,或者,激光测距传感器;在本实施例中,距离传感器采用激光测距传感器,距离传感器用于检测测柱2伸出基准台1的距离。
32.在步骤s1中(初始状态),每一个测柱2的上表面与基准台1的上表面11均齐平(参见图4和图5),即测柱2的上表面与基准台1的上表面11之间的间距为0。在步骤s2中(测试时,参见图6),检测部件检测测柱2伸出基准台1的距离,该距离即为测柱2的上表面与基准台1的上表面11之间的间距,控制单元计算测柱2的上表面与基准台1的上表面11之间的间距与该测柱2的长度的差值。相对应的测试结果如下:若测柱2的上表面高于基准台1的上表面11,当测柱2的上表面伸出基准台1的上表面11的间距越大,催化剂的孔磨损相对较小(磨损长度相对较小),当测柱2的上表面伸出基准台1的上表面11的间距越小,催化剂的孔磨损相对较大(磨损长度较大);或者,测柱2的上表面低于基准台1的上表面11,催化剂的孔磨损较大(磨损长度较大);或者,测柱2的上表面与基准台1的上表面11齐平,说明催化剂的孔无磨损。
33.s4、根据磨损长度设置催化剂磨损等级(磨损等级对应不同的磨损长度范围),并基于该催化剂模块的每个单元体在脱硝反应器中的位置,制作记载有单元体对应所属磨损等级的磨损分布图,其中,每个单元体对应的磨损等级在磨损分布图中的位置与该单元体在脱硝反应器中的位置一致。
34.依次对模块内的全部单元体使用基准台1和测柱2进行按压得到此模块所有单元体的磨损等级,根据模块在脱硝反应器内位置,依次对应统计所有模块中单元体的磨损信息。
35.制作磨损分布图时,因测柱2测得该单元体上一个孔的磨损长度,该单元体上每个孔对应一个磨损等级,基于该单元体上孔的分布,制作记载有每个孔对应所属磨损等级的磨损分布图,其中,每个孔对应的磨损等级在磨损分布图中的位置与该孔在单元体上的位置一致。
36.或者,制作磨损分布图时,将需要测试的催化剂模块分为多个区域,每个区域包含多个单元体,对每个单元体均进行测试,得到每个单元体上孔对应的所属磨损等级;再将每
个区域的多个单元体的磨损等级进行平均得到平均磨损等级,基于该区域在脱硝反应器中的位置,制作记载有每个区域对应所属磨损等级的磨损分布图。如将一个模块分解成3
×
6个区域,每个区域含4个单元体,可使用4个基准台1、测柱2组合,一次性测量4个单元体磨损情况,将4个单元体的磨损等级进行平均得到平均磨损等级,在平面图上标注每个模块的位置,在平面图上对应不同区域位置填写对应的所属平均磨损等级,以减小工作量。
37.步骤s4中,磨损等级划分为0、ki,0代表无磨损,ki代表磨损长度大于0。
38.在一个实施例中,ki 设定为1、2、3、4,1代表磨损长度大于等于15cm,2代表磨损长度为10~15cm,3代表磨损长度为5cm~10cm,4代表磨损长度小于等于5cm,磨损分布图参见图7。
39.磨损分布图具体是指:将统计的磨损等级数据,使用云图形式表示,即在平面图上标注每个模块的位置,对模块中不同的单元体进行分区,在平面图上对应单元体位置填写对应的所属磨损等级(在每个区域框内标上数值),同时通过不同颜色来标记不同磨损等级,使用不同的深浅的颜色依次对应,即使用颜色的深浅与磨损严重程度相对应,即颜色越深,磨损越严重,如若4代表磨损最严重,则将填写4的格子用最深的颜色涂画,若3代表磨损程度次之,则将填写3的格子用稍浅的颜色涂画,依次类推,方便清晰查看磨损区域。
40.通过磨损分布图对催化剂磨损情况进行可视化统计,可清楚得知单元体的磨损情况,根据图上的磨损等级标记,可得知不同区域的催化剂磨损程度,以更换磨损较为严重的单元体,无需在现场对每个单元体一一查看,大大节约时间,操作员在脱硝反应器内停留时间大大减少,测量操作安全性高,且可精确得知催化剂磨损情况,若用人眼一一观察,因单元体多且每个单元体的催化剂的孔多,无法精确得知催化剂磨损情况,又因脱硝反应器内环境恶劣,不仅费时费力,还影响操作者的健康。
41.当得到磨损分布图后,为进一步判定催化剂磨损原因,判定方法还包括:s5、建立脱硝反应器流场三维模型,获得脱硝反应器内需要测试的催化剂模块上游流场流速分布图。
42.脱硝反应器流场三维模型根据电厂实际烟气条件和脱硝反应器尺寸,使用cfd数值模拟方法对脱硝反应器流场进行了模拟,建立与催化剂结构、脱硝反应器内部结构一致的模型。
43.s6、将步骤s5中磨损分布图中对应不同磨损等级的不同磨损区域,与步骤s5中流场流速分布图对应该磨损区域的流场的烟气流速分布区域进行比对,以分析不同磨损区域的催化剂磨损的原因。
44.磨损分布图中的模块对应的单元体分布与流场流速分布图的模块对应的单元体分布一一对应,即磨损分布图中每一个磨损区域对应流场流速分布图的流场的烟气流速分布。
45.具体地,若一个磨损区域对应的流场的烟气流速高于预设流速范围(预设流速范围设定为4-6m/s),判断该磨损区域中催化剂磨损由流场的烟气高流速造成,则需调整该流场,如调整对应该磨损区域的流场的流速;若对应该磨损区域的流场的烟气流速低于预设流速范围(预设流速范围设定为4-6m/s),则判断该磨损区域中催化剂磨损自身强度低造成。
46.通过步骤s5、s6可进一步判断催化剂磨损原因,可进行相应改进,在后续实际应用
中提前调整(如调整流场的烟气流速),避免催化剂磨损,延长催化剂使用寿命。
实施例
47.某燃煤电厂脱硝装置安装3层蜂窝式催化剂,催化剂模块为6
×
7布置,催化剂长度为1.2米,孔数为18
×
18孔。运行2年后,发现催化剂出现严重的磨损情况,但无法明确磨损的准确分布和严重程度,也无法确定是否和脱硝反应器流场相关。
48.使用本发明的催化剂磨损测量判定方法对催化剂磨损情况进行可视化统计。
49.首先将一个模块分解成3
×
6个区域,每个区域含4个单元体。使用4个基准框组合,一次性测量4个单元体磨损情况。将每个区域所有磨损等级数值进行平均,得到每个区域的磨损等级平均值。将催化剂模块按其在脱硝反应器中的位置,依次绘制与平面图上。
50.在每个区域框内标上磨损等级平均值,且使用不同的深浅的颜色依次对应。图7中数字含义:4为完全贯穿或磨损达15cm以上;3为磨损在10~15cm;2为磨损在5cm~10cm;1为磨损在5cm以下。根据图7,清晰的反映了催化剂层的磨损分布情况,主要集中在脱硝反应器前墙,后墙也有部分区域发生磨损。
51.根据电厂实际烟气条件和脱硝反应器尺寸,使用cfd数值模拟方法对脱硝反应器流场进行了模拟,其中速度场分布如下图8、图9所示,图9中,3代表测试的催化剂模块截面,4代表测试的催化剂模块上方的流场分布截面。从模拟结果看,脱硝反应器上层催化剂上游速度分布在靠近前墙的区域出现了高速区,在靠后墙部分区域亦出现部分高度区。显然易见,流速的高速区易造成催化剂的磨损。此与磨损可视化云图中(图7)磨损严重区域完全对应,因此可以推断流场的烟气流速不均是导致催化剂磨损的重要原因,因此有必要对流场进行改造。
52.通过催化剂磨损测量判定方法,电厂获得了催化剂磨损分布准确的可视化图像,为其流场改造提供了有力的佐证。同时,通过对催化剂的磨损测量及可视化分析,可以准确统计催化剂磨损的总量,为电厂采购替换单体提供了准确依据,若局部区域磨损严重,电厂可根据此情况准备替换单体,避免此处发生坍塌穿孔;可清楚得知催化剂的磨损情况,根据磨损情况,电厂可以评估催化剂再生的可行性,及时准备填充的单体数量。
53.上述实施例只为说明本发明的技术构思及特点,其目的在于让熟悉此项技术的人士能够了解本发明的内容并据以实施,并不能以此限制本发明的保护范围。凡根据本发明精神实质所作的等效变化或修饰,都应涵盖在本发明的保护范围之内。