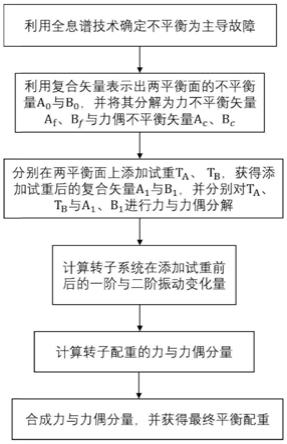
1.本发明涉及一种转子系统动平衡方法。特别是涉及一种基于复合矢量的转子系统全息动平衡方法。
背景技术:2.随着工业技术的迅猛发展,以各种风机、水轮机、燃气轮机等旋转机械为主要组成部分的各类大型装置被广泛地应用到了工业生产之中。作为关键生产设备,其长期稳定、安全以及高效的运行具有重要意义
1.。因此,对旋转机械运行状态的监测以及故障诊断、处理技术的研究十分重要。其中,因转子不平衡在机组运行中产生激振力,进而造成的破坏事故频繁发生,因而对转子不平衡故障的诊断及其处理方法的研究备受关注。
3.传统的动平衡方法,如模态平衡法
2.与影响系数法
3.,以及基于这两类方法的融合与改进都是建立在转子系统模态振型呈平面分布以及各向刚度同性的假设上
4.。而在现实应用中,这一假设通常不成立,转子系统中的阻尼以及负荷作用会使转子模态空间扭曲,并且其普遍存在刚度各向异性的情况
5.。而西安交通大学的屈梁生院士所提出的全息动平衡技术借助于多传感器信息融合的思想,解决了传统方法中对转子振动信息利用不充分的问题
6.。相较于每个测振面上仅配有单个传感器的现场动平衡方法,全息动平衡技术建立在转子支承系统各向异性的基础上,融合了单个测振面上两个传感器的信息,可以弥补单个传感器信息不完整的缺陷,全面地反映了转子在测振面上的振动情况
7.。但传统全息动平衡技术存在的不足之处在于其平衡目标初相矢并不能彻底消除转子系统支承刚度各向异性对不平衡量的准确度测量所带来的影响,即若用传统初相矢来描述不平衡量信息会对平衡结果造成较大误差。
技术实现要素:4.本发明所要解决的技术问题是,为克服现有技术的不足,提供一种能够提高动平衡效果的基于复合矢量的转子系统全息动平衡方法。
5.本发明所采用的技术方案是:一种基于复合矢量的转子系统全息动平衡方法,包括如下步骤:
6.步骤一、利用传感器采集转子两测振面的振动数据,利用全息谱技术判断振动数据是否为不平衡故障数据,是则进行后续的动平衡操作步骤;否则结束;
7.步骤二、采用全息谱技术将具有不平衡故障的转子振动数据提取两个相互独立的参数,构成复合矢量作为平衡目标,将所述的复合矢量分解为力不平衡矢量和力偶不平衡矢量;
8.步骤三、在转子的两配重面上分别添加试重,得到此时的两振动复合矢量,并将两试重与两振动复合矢量进行力与力偶分解;
9.步骤四、转子的工作转速位于一、二阶临界转速之间,转子一阶振动的变化量是由力不平衡矢量决定,转子二阶振动的变化量是由力偶不平衡矢量决定的,根据步骤二与步
骤三中的计算结果,求得转子一阶振动的变化量和转子二阶振动的变化量;
10.步骤五、计算转子所需平衡配重的力不平衡矢量和力偶不平衡矢量;
11.步骤六、将步骤五中配重的力不平衡矢量和力偶不平衡矢量进行合成,即得到所需的平衡配重。
12.步骤二中所述的复合矢量的大小是以转频椭圆长半轴,即振动轨迹幅值的最高点来表示;复合矢量的方位以转频椭圆的初相角来表示。
13.步骤二中将所述的复合矢量分解为力不平衡矢量和力偶不平衡矢量,以复合矢量为平衡目标,将两平衡面的振动复合矢量分别表达为a0与b0,再将两平衡面的振动复合矢量分别分解为转子的力不平衡矢量af、bf与转子的力偶不平衡矢量ac、bc,分解公式如下:
[0014][0015]
步骤三包括:在两配重面上分别添加试重ta、tb,然后测量此时的两振动复合矢量a1、b1,对两试重ta、tb和两振动复合矢量a1、b1分别进行力与力偶分解,分解公式如下:
[0016][0017][0018]
其中,ta、tb为添加的试重;t
af
和t
bf
分别为两试重的力不平衡矢量;t
ac
与t
bc
分别为两试重的力偶不平衡矢量;a'f与b'f分别为两平衡面添加试重后的力不平衡矢量;ac'与bc'分别为两平衡面添加试重后的力偶不平衡矢量。
[0019]
步骤四是根据步骤二与步骤三中的计算结果,按照如下公式求得转子一阶振动的变化量和转子二阶振动的变化量:
[0020][0021]
其中,a'f为平衡面添加试重后的力不平衡矢量;af为转子的力不平衡矢量;ac'为平衡面添加试重后的力偶不平衡矢量;ac为转子的力偶不平衡矢量;ic为配重的力偶不平衡矢量;if为一阶振动的变化量。
[0022]
步骤五所述的转子所需平衡配重的力不平衡矢量和力偶不平衡矢量,计算公式如下:
[0023][0024]
其中,p
af
为与p
bf
分别为两平衡面所需平衡配重的力不平衡矢量;t
af
为试重的力不平衡矢量;af为力不平衡矢量;if为一阶振动的变化量;p
ac
与p
bc
分别为两平衡面所需平衡配重的力偶不平衡矢量;t
ac
为试重的力偶不平衡矢量;ac为转子的力偶不平衡矢量;ic为配重的力偶不平衡矢量。
[0025]
步骤六是采用如下公式得到所需的平衡配重:
[0026][0027]
式中,pa与pb分别为两平衡面的最终配重;p
af
为与p
bf
分别为两平衡面所需平衡配重的力不平衡矢量;p
ac
与p
bc
分别为两平衡面所需平衡配重的力偶不平衡矢量。
[0028]
本发明的一种基于复合矢量的转子系统全息动平衡方法,有益效果如下:
[0029]
1、本发明选取了全息谱技术中转频椭圆的长轴与初相角信息构成复合矢量,并以此为平衡目标进行转子系统的动平衡操作。复合矢量的选择克服了传统初相矢受转子非对称刚度的影响,提高了动平衡效果;
[0030]
2、本发明基于全息谱技术,能将转子系统机组中多个传感器的振动信号进行集成与融合,可以真实全面地表现出设备的运行状态,为在动平衡操作前确诊失衡是否为主导故障提供了技术支撑;
[0031]
3、本发明充分地利用了转子系统的振动信息,减少了现场动平衡过程中的盲目性,提高了安全性,减少了起停车次数和相应的消耗,对工业现场设备的维护提供了有效的技术指导。
附图说明
[0032]
图1是本发明一种基于复合矢量的转子系统全息动平衡方法的流程图;
[0033]
图2是bently rk4转子实验台示意图;
[0034]
图3是复合矢量的原理图;
[0035]
图4a是a测振面的时域图;
[0036]
图4b是a测振面的频域图;
[0037]
图5a是b测振面的时域图;
[0038]
图5b是b测振面的频谱图;
[0039]
图6a是a测振面的时域图;
[0040]
图6b是a测振面的频域图;
[0041]
图7a是b测振面的时域图;
[0042]
图7b是b测振面的频域图。
具体实施方式
[0043]
下面结合实施例和附图对本发明的一种基于复合矢量的转子系统全息动平衡方法做出详细说明。
[0044]
如图1所示,本发明的一种基于复合矢量的转子系统全息动平衡方法,包括如下步骤:
[0045]
步骤一、利用传感器采集转子两测振面的振动数据,利用全息谱技术判断振动数据是否为不平衡故障数据,是则进行后续的动平衡操作步骤;否则结束;
[0046]
所述的全息谱技术,可以通过该技术将转子不平衡故障精准的从其它类故障,例如不对中、油膜涡动等精准识别出来。
[0047]
步骤二、采用全息谱技术将具有不平衡故障的转子振动数据提取两个相互独立的参数,构成复合矢量作为平衡目标,将所述的复合矢量分解为力不平衡矢量和力偶不平衡矢量;
[0048]
所述的复合矢量的大小是以转频椭圆长半轴,即振动轨迹幅值的最高点来表示;复合矢量的方位以转频椭圆的初相角来表示。
[0049]
所述的将所述的复合矢量分解为力不平衡矢量和力偶不平衡矢量,以复合矢量为平衡目标,将两平衡面的振动复合矢量分别表达为a0与b0,再将两平衡面的振动复合矢量分别分解为转子的力不平衡矢量af、bf与转子的力偶不平衡矢量ac、bc,分解公式如下:
[0050][0051]
步骤三、在转子的两配重面上分别添加试重,得到此时的两振动复合矢量,并将两试重与两振动复合矢量进行力与力偶分解;包括:
[0052]
在两配重面上分别添加试重ta、tb,然后测量此时的两振动复合矢量a1、b1,对两试重ta、tb和两振动复合矢量a1、b1分别进行力与力偶分解,分解公式如下:
[0053][0054][0055]
其中,ta、tb为添加的试重;t
af
和t
bf
分别为两试重的力不平衡矢量;t
ac
与t
bc
分别为两试重的力偶不平衡矢量;a'f与b'f分别为两平衡面添加试重后的力不平衡矢量;ac'与bc'分别为两平衡面添加试重后的力偶不平衡矢量。
[0056]
步骤四、转子的工作转速位于一、二阶临界转速之间,转子一阶振动的变化量if是由力不平衡矢量决定,转子二阶振动的变化量是由力偶不平衡矢量决定的,根据步骤二与步骤三中的计算结果,求得转子一阶振动的变化量和转子二阶振动的变化量;
[0057]
是根据步骤二与步骤三中的计算结果,按照如下公式求得转子一阶振动的变化量和转子二阶振动的变化量:
[0058][0059]
其中,a'f为平衡面添加试重后的力不平衡矢量;af为转子的力不平衡矢量;ac'为平衡面添加试重后的力偶不平衡矢量;ac为转子的力偶不平衡矢量;ic为配重的力偶不平衡矢量;if为一阶振动的变化量。
[0060]
步骤五、计算转子所需平衡配重的力不平衡矢量和力偶不平衡矢量;计算公式如下:
[0061][0062]
其中,p
af
为与p
bf
分别为两平衡面所需平衡配重的力不平衡矢量;t
af
为试重的力不平衡矢量;af为力不平衡矢量;if为一阶振动的变化量;p
ac
与p
bc
分别为两平衡面所需平衡配重的力偶不平衡矢量;t
ac
为试重的力偶不平衡矢量;ac为转子的力偶不平衡矢量;ic为配重的力偶不平衡矢量。
[0063]
步骤六、将步骤五中配重的力不平衡矢量和力偶不平衡矢量进行合成,即得到所需的平衡配重。是采用如下公式得到所需的平衡配重:
[0064][0065]
式中,pa与pb分别为两平衡面的最终配重;p
af
为与p
bf
分别为两平衡面所需平衡配重的力不平衡矢量;p
ac
与p
bc
分别为两平衡面所需平衡配重的力偶不平衡矢量。
[0066]
下面给出具体实例。
[0067]
在bently rk4转子实验台上对基于复合矢量的全息动平衡算法进行验证,如图2所示,该实验台主要由转子系统和振动测试系统组成。其中,为充分考虑转子支撑各向异性的影响,信号采集截面a、b分别由两个相互垂直的传感器构成,c、d截面为配重平衡盘,并采用6个电涡流传感器获取a、b截面振动信号以及转速、键相信息。
[0068]
实验所设置的转速为3500r/min,采样频率为4096hz,采样时长为10s,并用dt9837b数采卡对转子振动数据进行采集。
[0069]
图3为复合矢量的原理图,复合矢量的幅值由转频椭圆的长半轴a表示,相位由转频椭圆的初相角α表示。
[0070]
(1)在转子实验台c、d配重盘上分别添加1.6g∠67.5
°
、1.6g∠157.5
°
的重量模拟不平衡量。
[0071]
(2)测量两测振截面的不平衡量a测振面的时域图4a为a测振面的时域图,图4b为a测振面的频域图,其不平衡量用复合矢量表示为11.9462∠110.8345
°
;图5a为b测振面的时域图,图5b为b测振面的频域图,其不平衡量用复合矢量表示为20.4306∠-144.9069
°
。
[0072]
(3)停车,在转子实验台c、d配重盘上分别添加试重1.2g∠225
°
、1.2g∠315
°
,启车
后继续在3500r/min的转速下运行。
[0073]
(4)测量添加试重后两测振面的不平衡量,并用复合矢量表示。其中,图6a为a测振面的时域图,图6b为a测振面的频域图,其不平衡量用复合矢量表示为12.6462∠-144.6318
°
;图7a为b测振面的时域图,图7b为b测振面的频域图,其不平衡量用复合矢量表示为20.5583∠179.5637
°
。
[0074]
(5)将a0=11.9462∠110.8345
°
,b0=20.4306∠-144.9069
°
,a1=12.6462∠-144.6318
°
,b1=20.5583∠179.5637
°
,ta=1.2g∠225
°
,tb=1.2g∠315
°
代入上述平衡配重计算公式中,求得pa=1.5740g∠265.1953
°
,pb=1.7483g∠33.6593
°
,实际添加配重为pa=1.6g∠270
°
,pb=1.7g∠22.5
°
。
[0075]
平衡前后的振动量如下表1所示,从表中可看出基于复合矢量的全息动平衡可有效降低各个通道的幅值,具有良好的平衡效果。
[0076]
表1所提方法平衡效果
[0077][0078]
参考文献
[0079]
[1]秦丽.现场整机动平衡仪的设计与实现[d].长沙:湖南大学,2011.
[0080]
[2]bishop r.the vibration of rotating shafts[j].journal of mechanical engineering science,1959,1(1):50-65.
[0081]
[3]goodman tp.a least-squares method for computing balance corrections[j].journal of engineering for industry,trans of the asme,series b,1964,86(3):273-279.
[0082]
[4]darlow m.balancing of high-speed machinery[m].new york:springer-verlag,1989.
[0083]
[5]liao y,lang g,wu f,et al.an improvement to holospectrum based field balancing method by reselection of balancing object[j].journal of vibration and acoustics,transactions of the asme,2009,131(3):031005.
[0084]
[6]屈梁生,邱海,徐光华.全息动平衡技术:原理与实践[j].中国机械工程,1998,9(001):60-63.
[0085]
[7]廖与禾,张鹏,郎根峰.移相轨迹及其在全息动平衡中的应用[j].西安交通大学学报,2008,42(7):803-806.