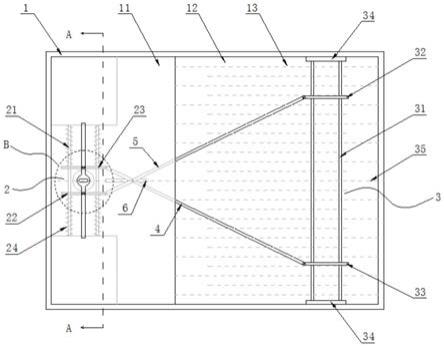
1.本发明属于电池生产测试技术领域,特别涉及一种锂离子电池厚度测试治具。
背景技术:2.在电池制造工艺和电池工艺设计试验中,电芯和电池壳体的厚度是评价电池性能的一个标志。在预充、检测、成品包装出货时均要对电池壳体的厚度进行测量,并将厚度超过厚度上下限的不合格电池筛选出来。特别是现在对锂电池的能量密度要求越来越高,对其厚度控制要求也更加精确。
3.目前的筛选方法一般是通过人工采用卡尺进行测量厚度,由于卡尺特性,测量时均需采用手工划动卡尺方能进行测量,且每个人在测试时用力大小不同,测量厚度误差较大,且生产效率低下;也有一些按照厚度不同的电池设计的不同的检测模具,其缺点是不能通用造成资源浪费。
技术实现要素:4.针对上述问题,本发明提供了一种锂离子电池厚度测试治具,包括方形盒状治具本体,所述治具本体内部左右两侧分别设置有电池限位装置和电池厚度读取装置,所述电池限位装置与电池厚度读取装置之间通过两个长度相同的连接杆一和连接杆二进行连接,所述连接杆一与连接杆二采用交叉成x型设置,所述连接杆一与连接杆二的x型交叉连接处垂直设置有滑动立杆,所述滑动立杆的下端安装在治具本体内底部设置的滑槽内。
5.进一步的,所述电池限位装置包括两根相互平行的滑杆一、以及限位卡板一和限位卡板二,所述滑杆一两端分别固定在治具本体左侧的前后内壁上;所述限位卡板一、限位卡板二相互平行且均安装在两滑杆一上,所述限位卡板二前侧及限位卡板一后侧的滑杆一上均设置有伸缩弹簧,所述伸缩弹簧一端固定在限位卡板一或限位卡板二侧端面上,另一端固定在治具本体内壁上,所述伸缩弹簧一直处于压缩状态。
6.进一步的,所述电池厚度读取装置包括两根相互平行的滑杆二、以及前挡板和后挡板,所述滑杆二两端分别固定在治具本体右侧的前后内壁上,所述前挡板、后挡板相互平行且均安装在两滑杆二上;两个所述滑杆二的前后两端处均设置有滑杆固定座,所述治具本体内部右侧的前后内壁上均设置有滑杆滑轨,两个所述滑杆固定座分别安装在两个滑杆滑轨上并进行自由滑动。
7.进一步的,所述连接杆一两端分别铰接在限位卡板二右端和后挡板左端,所述连接杆二两端分别铰接在限位卡板一右端和前挡板左端。
8.进一步的,所述治具本体内部左侧底面上设置有锂电池固定座,所述锂电池固定座上端面中央设置有锂电池固定孔,所述锂电池固定孔位于两个所述滑杆一的垂直轴心线上,并与两个滑杆一等距离设置。
9.进一步的,所述治具本体左右侧上端面分别设置有左侧封盖、右侧透明封盖,两个所述滑杆一中间的左侧封盖上设置有条形调节孔,所述限位卡板一、限位卡板二上端面中
心处均设置有调节杆,所述调节杆上端贯穿条形调节孔并露出至左侧封盖上方;所述条形调节孔中心处的左侧封盖上设置有锂电池放置孔,所述锂电池放置孔位于锂电池固定孔正上方;所述治具本体内部右侧底面上设置有标准长度计量刻度线,所述标准长度计量刻度线的零刻度线位于滑杆二的中心点处。
10.进一步的,所述限位卡板一、限位卡板二、前挡板、后挡板上均设置有两个滑杆安装孔,所述滑杆安装孔内壁上嵌入设置有若干个万向滚珠,两个所述滑杆一分别设置在限位卡板一和限位卡板二的两个滑杆安装孔中,两个所述滑杆二分别设置在前挡板和后挡板的两个滑杆安装孔中。
11.进一步的,所述滑槽与滑杆一、滑杆二均相垂直,所述滑槽的两内侧壁上均设置有凹槽,所述滑动立杆外壁的下端前后侧均设置有限位块,滑动立杆的两个所述限位块分别卡合在两凹槽内;所述限位块的上下端面、外端面,以及滑动立杆底端面上均设置有滑轮;所述连接杆一、连接杆二均通过轴承安装在滑动立杆上,且所述连接杆一下方、连接杆二上方、连接杆一与连接杆二之间的滑动立杆上均设置有限位密封件。
12.进一步的,所述锂离子电池厚度测试治具,其测试使用方法包括如下步骤:s1、用左手的大拇指、食指分别抵住限位卡板一、限位卡板二上端面的调节杆并将二调节杆沿着条形调节孔互相撑开,使限位卡板一与限位卡板二分离;s2、用右手将待测锂电子电池从左侧封盖上的锂电池放置孔处放置至治具本体内部的锂电池固定座上的锂电池固定孔中固定;s3、左手慢慢松开大拇指和食指,限位卡板一、限位卡板二在伸缩弹簧复位作用下相向靠拢,而电池厚度读取装置在连接杆一和连接杆二的作用下向右侧滑动;s4、最终限位卡板一、限位卡板二稳定地将锂电池固定座上的待测锂电子电池夹在中间,通过右侧电池厚度读取装置处中的前挡板或后挡板至标准长度计量刻度线的零刻度线的距离读数,即可计算出限位卡板一与限位卡板二的间隙距离即待测锂电子电池的厚度h。
13.进一步的,所述锂离子电池厚度h的测试计算公式为:h =( k1+h
3 / 2 +k2+ h
4 / 2)/(l2/l1)
ꢀ‑
(h1/ 2+h
2 / 2),其中,k1为前挡板的后端面至标准长度计量刻度线的零刻度线的距离,通过标准长度计量刻度线可实际读出;k2为后挡板的前端面至标准长度计量刻度线的零刻度线的距离,通过标准长度计量刻度线可实际读出;h1为限位卡板一的厚度;h2为限位卡板二的厚度;h3为前挡板的厚度;h4为后挡板的厚度;l1为滑动立杆轴心至连接杆一与限位卡板二的铰接轴心之间的距离,或滑动立杆轴心至连接杆二与限位卡板一的铰接轴心之间的距离;l2为滑动立杆轴心至连接杆一与后挡板的铰接轴心之间的距离,或滑动立杆轴心至连接杆二与前挡板的铰接轴心之间的距离。
14.本发明提供的一种锂离子电池厚度测试治具,通过在治具本体内部左侧设置的电池限位装置对锂电池进行固定及厚度卡合,再通过采用交叉成x型设置的连接杆一、连接杆二连接有电池厚度读取装置,将锂电子电池的厚度进行放大处理,有效提高厚度的测试精度;在电池限位装置内通过伸缩弹簧控制的限位卡板一、限位卡板二对锂离子电池厚度进行卡合,降低人为测量用力不一对测试结果的影响,准确度高,稳定性强。本发明锂离子电池厚度测试治具,结构紧凑,采用机械方式对锂离子电池厚度进行卡合,降低人为因素影
响,准确度高,稳定性强;通过放大读取数据的方式,测试精度更高,效率较高,能够对不同厚度的锂电池均能够进行测试,通用性好,使用方便。
附图说明
15.为了更清楚地说明本发明实施例或现有技术中的技术方案,下面将对实施例或现有技术描述中所需要使用的附图作一个简单地介绍,显而易见地,下面描述中的附图是本发明的一些实施例,对于本领域普通技术人员来讲,在不付出创造性劳动的前提下,还可以根据这些附图获得其他的附图。
16.图1示出了根据本发明的锂离子电池厚度测试治具的结构俯视图。
17.图2示出了根据本发明图1中b处结构放大图。
18.图3示出了根据本发明图1中a-a结构剖视图。
19.图4示出了根据本发明的滑杆一与限位卡板一的连接结构示意图。
20.图5示出了根据本发明的连接杆一、连接杆二、滑槽、以及滑动立杆的连接结构示意图。
具体实施方式
21.为使本发明实施例的目的、技术方案和优点更加清楚,下面将结合本发明实施例中的附图,对本发明实施例中的技术方案进行清楚、完整地说明,显然,所描述的实施例是本发明一部分实施例,而不是全部的实施例。基于本发明中的实施例,本领域普通技术人员在没有做出创造性劳动前提下所获得的所有其他实施例,都属于本发明保护的范围。
22.实施例1:针对上述问题,参考图1-5,本发明提供一种锂离子电池厚度测试治具,包括方形盒状治具本体1,治具本体1内部左右两侧分别设置有电池限位装置2和电池厚度读取装置3,电池限位装置2与电池厚度读取装置3之间通过两个长度相同的连接杆一4和连接杆二5进行连接,连接杆一4与连接杆二5采用交叉成x型设置,连接杆一4与连接杆二5的x型交叉连接处垂直设置有滑动立杆7,滑动立杆7的下端安装在治具本体1内底部设置的滑槽6内。
23.电池限位装置2包括两根相互平行的滑杆一21、以及限位卡板一22和限位卡板二23,滑杆一21两端分别固定在治具本体1左侧的前后内壁上;限位卡板一22、限位卡板二23相互平行且均安装在两滑杆一21上,限位卡板二23前侧及限位卡板一22后侧的滑杆一21上均设置有伸缩弹簧24,伸缩弹簧24一端固定在限位卡板一22或限位卡板二23侧端面上,另一端固定在治具本体1内壁上。伸缩弹簧24一直处于压缩状态,利用伸缩弹簧24的复位作用,通过限位卡板一22、限位卡板二23对锂电子电池进行卡合。
24.治具本体1内部左侧底面上设置有锂电池固定座25,锂电池固定座25上端面中央设置有锂电池固定孔251,锂电池固定孔251位于两个滑杆一21的垂直轴心线上,并与两个滑杆一21等距离设置。
25.治具本体1左右侧上端面分别设置有左侧封盖11、右侧透明封盖12,两个滑杆一21中间的左侧封盖11上设置有条形调节孔14,限位卡板一22、限位卡板二23上端面中心处均设置有调节杆26,调节杆26上端贯穿条形调节孔14并露出至左侧封盖11上方;条形调节孔14中心处的左侧封盖11上设置有锂电池放置孔15,锂电池放置孔15位于锂电池固定孔251
正上方;治具本体1内部右侧底面上设置有标准长度计量刻度线13,标准长度计量刻度线13的零刻度线35位于滑杆二31的中心点处。
26.电池厚度读取装置3包括两根相互平行的滑杆二31、以及前挡板32和后挡板33,滑杆二31两端分别固定在治具本体1右侧的前后内壁上,前挡板32、后挡板33相互平行且均安装在两滑杆二31上;两个滑杆二31的前后两端处均设置有滑杆固定座34,治具本体1内部右侧的前后内壁上均设置有滑杆滑轨,两个滑杆固定座34分别安装在两个滑杆滑轨上并进行自由滑动。
27.连接杆一4两端分别铰接在限位卡板二23右端和后挡板33左端,连接杆二5两端分别铰接在限位卡板一22右端和前挡板32左端。
28.限位卡板一22、限位卡板二23、前挡板32、后挡板33上均设置有两个滑杆安装孔221,滑杆安装孔221内壁上嵌入设置有若干个万向滚珠222,两个滑杆一21分别设置在限位卡板一22和限位卡板二23的两个滑杆安装孔221中,两个滑杆二31分别设置在前挡板32和后挡板33的两个滑杆安装孔221中。利用万向滚珠222,能够有效提高限位卡板一22、限位卡板二23在滑杆一21上的滑动,能够有效提高前挡板32、后挡板33在滑杆二31上的滑动,使之滑动更流畅。
29.滑槽6与滑杆一21、滑杆二31均相垂直,滑槽6的两内侧壁上均设置有凹槽62,滑动立杆7外壁的下端前后侧均设置有限位块72,滑动立杆7的两个限位块72分别卡合在两凹槽62内;限位块72的上下端面、外端面,以及滑动立杆7底端面上均设置有滑轮73;连接杆一4、连接杆二5均通过轴承安装在滑动立杆7上,且连接杆一4下方、连接杆二5上方、连接杆一4与连接杆二5之间的滑动立杆7上均设置有限位密封件71。
30.上述锂离子电池厚度测试治具,其对锂离子电池厚度进行测试的测试使用方法,包括如下步骤:s1、用左手的大拇指、食指分别抵住限位卡板一22、限位卡板二23上端面的调节杆26并将二调节杆26沿着条形调节孔14互相撑开,使限位卡板一22与限位卡板二23分离;s2、用右手将待测锂电子电池100从左侧封盖11上的锂电池放置孔15处放置至治具本体1内部的锂电池固定座25上的锂电池固定孔251中固定;s3、左手慢慢松开大拇指和食指,限位卡板一22、限位卡板二23在伸缩弹簧24复位作用下相向靠拢,而电池厚度读取装置3在连接杆一4和连接杆二5的作用下向右侧滑动;s4、最终限位卡板一22、限位卡板二23稳定地将锂电池固定座25上的待测锂电子电池100夹在中间,通过右侧电池厚度读取装置3处中的前挡板32或后挡板33至标准长度计量刻度线13的零刻度线35的距离读数,即可计算出限位卡板一22与限位卡板二23的间隙距离即待测锂电子电池100的厚度h。
31.其中,锂离子电池厚度h的测试计算公式为:h =( k1+h
3 / 2 +k2+ h
4 / 2)/(l2/l1)
ꢀ‑
(h1/ 2+h
2 / 2),其中,k1为前挡板32的后端面至标准长度计量刻度线13的零刻度线35的距离,通过标准长度计量刻度线13可实际读出;k2为后挡板33的前端面至标准长度计量刻度线13的零刻度线35的距离,通过标准长度计量刻度线13可实际读出;h1为限位卡板一22的厚度;h2为限位卡板二23的厚度;h3为前挡板32的厚度;h4为后挡板33的厚度;l1为滑动立杆7轴心至连接杆一4与限位卡板二23的铰接轴心之间的距离,或滑动立杆7轴心至连接杆二5与限位
卡板一22的铰接轴心之间的距离;l2为滑动立杆7轴心至连接杆一4与后挡板33的铰接轴心之间的距离,或滑动立杆7轴心至连接杆二5与前挡板32的铰接轴心之间的距离。
32.上述锂离子电池厚度测试治具的各项参数分别为:h1:10mm,h2:8mm,h3:16mm,h4:18mm,l1:6mm,l2:60mm,所以l2/l1为10,即放大倍数为10。
33.利用上述锂离子电池厚度测试治具对若干个锂电子电池的厚度进行测量,读出的测量数据k1、k2,以及通过测试计算公式得到的锂离子电池厚度h数据如下(部分):序号电池型号k1(mm)k2(mm)h(mm)m1ⅰ72727.1m2ⅰ70716.8m3ⅰ71686.6m4ⅰ73727.2m5ⅱ10210513.4m6ⅱ10610714.0m7ⅱ11010814.5m8ⅱ10710614.0m9ⅲ14815022.5m10ⅲ15115223.0m11ⅲ15015122.8m12ⅲ15315323.3实施例2:本发明提供一种锂离子电池厚度测试治具,其结构与实施例1基本相同,不同的在于:本发明的锂离子电池厚度测试治具,其中限位卡板一22、限位卡板二23、前挡板32、后挡板33的厚度均相同,其各项参数分别为:h1:20mm,h2:20mm,h3:20mm,h4:20mm,l1:10mm,l2:50mm,所以l2/l1为5,即放大倍数为5。
34.利用上述锂离子电池厚度测试治具对若干个锂电子电池的厚度进行测量,读出的测量数据k1、k2,以及通过测试计算公式得到的锂离子电池厚度h数据如下(部分):序号电池型号k1(mm)k2(mm)h(mm)n1ⅳ60608.0n2ⅳ61638.8n3ⅳ61628.6n4ⅳ59628.2n5
ⅴ
9810123.8n6
ⅴ
1009923.8n7
ⅴ
10010024.0n8
ⅴ
10210124.6n9ⅵ14214040.4n10ⅵ14014040.0
n11ⅵ14114240.6n12ⅵ14214140.6本发明的一种锂离子电池厚度测试治具,通过标准长度计量刻度线13实际读出的k1与k2之和与锂离子电池厚度h成正比,而且k1与k2之和的增加值与锂离子电池厚度h的增加值之间成倍数关系,其倍数值即为l2/l1的放大倍数。
35.在实施例2中,例如:与n1相比,n7的k1与k2之和的增加值为:n7(k1+k2)-n1(k1+k2)=80mm,锂离子电池厚度h的增加值为:24.0mm
ꢀ‑
8.0mm =16mm,倍数即为:80mm/16mm=5。
36.与n7相比,n10的k1与k2之和的增加值为:n10(k1+k2)-n7(k1+k2)=80mm,锂离子电池厚度h的增加值为:40.0mm
ꢀ‑
24mm =16mm,倍数即为:80mm/16mm=5。
37.同理,其它数据均如此。因此,为了减少利用测试计算公式得到的锂离子电池厚度h数据的繁琐性,可在标准长度计量刻度线13之外再设置一个适用于本发明的锂离子电池厚度h的非标准计量刻度线,通过这个非标准计量刻度线可对实际测量的锂离子电池厚度h直接读出,减少计算过程,提高锂离子电池厚度的测试的工作效率。
38.同时,也可以根据需要,在标准长度计量刻度线13、或非标准计量刻度线上标注某类型需要测试的锂离子电池厚度h的合格区间,一旦对此类型中的某个需要测试的锂离子电池厚度进行实际测量时,右侧的k1、k2超出此合格区间范围,那么此测试的锂离子电池厚度不合格;同理,若右侧的k1、k2在此合格区间范围内,那么此测试的锂离子电池厚度合格。因此,此种方法能够适用于仅需判断锂离子电池厚度是否合格,无需知道其实际厚度的准确数据的情况,能够进一步提高锂离子电池厚度测试的工作效率。
39.本发明提供的一种锂离子电池厚度测试治具,通过在治具本体1内部左侧设置的电池限位装置2对锂电池进行固定及厚度卡合,再通过采用交叉成x型设置的连接杆一4、连接杆二5连接有电池厚度读取装置3,将锂电子电池的厚度进行放大处理,有效提高厚度的测试精度;在电池限位装置2内通过伸缩弹簧24控制的限位卡板一22、限位卡板二23对锂离子电池厚度进行卡合,降低人为测量用力不一对测试结果的影响,准确度高,稳定性强。
40.本发明锂离子电池厚度测试治具,结构紧凑,采用机械方式对锂离子电池厚度进行卡合,降低人为因素影响,准确度高,稳定性强;通过放大读取数据的方式,测试精度更高,效率较高,能够对不同厚度的锂电池均能够进行测试,通用性好,使用方便。
41.需要说明的是,本发明中所使用的术语“向上”、“向下”、“向左”“向右”、“垂直”、“向内”以及类似的表述只是为了说明的目的。且以上所述仅是本发明的较佳实施例而已,并非对本发明做任何形式上的限制,虽然本发明已以较佳实施例揭露如上,然而并非用以限定本发明,任何熟悉本专业的技术人员,在不脱离本发明技术方案的范围内,当可利用上述揭示的技术内容作出些许更动或修饰为等同变化的等效实施例,但凡是未脱离本发明技术方案的内容,依据本发明的技术实质对以上实施例所作的任何简单修改、等同变化与修饰,均仍属于本发明技术方案的范围内。