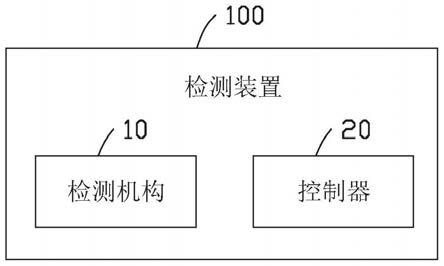
1.本技术涉及治具检测技术领域,具体涉及一种检测装置及检测方法。
背景技术:2.随着3c产品行业的快速发展,人们对产品的外观要求越来越高。现有产品在加工完成后,还需要通过加工装置例如抛光装置对产品进行抛光等加工。加工装置对产品进行加工的方式大致为:将产品固定在加工治具上,待产品固定后,利用加工装置对产品进行加工。加工治具在长时间使用后,加工治具的直线度和对称度可能会发生变化,导致加工装置对产品进行加工时发生加工量偏大或偏小的情况,进而导致产品的加工不合格。目前,通常由作业人员采用手动的方式对加工治具的直线度和对称度进行检测及矫正。
3.然而,作业人员手动对加工治具的直线度和对称度进行检测及矫正,所需的人力成本高且对作业人员的要求高,作业人员的工作量大,检测及矫正效率低,降低加工效率。
技术实现要素:4.鉴于以上内容,有必要提出一种检测装置及检测方法,以实现对加工治具的直线度和对称度的自动检测及矫正,节省人力成本,提高加工效率。
5.本技术第一方面提供一种检测装置,用于对加工治具的直线度及对称度进行检测,包括:检测机构,用于检测所述加工治具;控制器,与所述检测机构耦接,用于获取所述检测机构检测的所述加工治具的直线度数据,根据所述加工治具的直线度数据,确定所述加工治具的角度偏差值,基于所述加工治具的角度偏差值,生成第一控制指令,以控制对所述加工治具进行第一操作;所述控制器还用于根据所述第一操作的操作结果,构建所述加工治具的参考基准区域,获取所述参考基准区域的位置数据及所述检测机构检测的所述加工治具的位置数据;根据所述参考基准区域的位置数据及所述加工治具的位置数据,确定所述加工治具的位置偏差值,基于所述加工治具的位置偏差值得到所述加工治具的对称度检测结果,根据所述加工治具的对称度检测结果,生成第二控制指令,以控制对所述加工治具进行第二操作。
6.在一些实施例中,所述加工治具的直线度数据包括所述加工治具的任意一检测边上的任意两点的坐标数据;所述控制器根据所述加工治具的直线度数据,确定所述加工治具的角度偏差值,包括:基于所述加工治具的任意一检测边上的任意两点的坐标数据,计算所述加工治具的角度偏差值;所述第一操作包括直线度矫正操作;所述控制器基于所述加工治具的角度偏差值,生成第一控制指令,包括:判断所述加工治具的角度偏差值是否为零;如果所述加工治具的角度偏差值不为零,则计算所述加工治具的角度补偿值;基于所述加工治具的角度补偿值,生成第一控制指令,所述第一控制指令用于指示对所述加工治具执行直线度矫正操作直至所述加工治具的角度偏差值为零。
7.在一些实施例中,所述第一操作还包括重新检测,所述第一操作的操作结果包含执行直线度矫正操作后的所述加工治具的角度偏差值为零;所述控制器还用于:获取所述
检测机构检测的直线度矫正操作后的所述加工治具的直线度数据,计算直线度矫正操作后的所述加工治具的角度偏差值。
8.在一些实施例中,所述参考基准区域的位置数据包括所述参考基准区域的每一基准边位于基准位时其上一基准点的坐标数据;所述加工治具的位置数据包括所述加工治具的每一检测边位于基准位时其上一检测点的坐标数据;所述控制器根据所述参考基准区域的位置数据及所述加工治具的位置数据,确定所述加工治具的位置偏差值,包括:选取所述参考基准区域的两个相垂直的基准边作为第一基准边及第二基准边;获取所述检测机构检测的所述第一基准边及所述第二基准边位于基准位时其上一基准点的坐标数据;以及所述加工治具的每一检测边位于基准位时其上一检测点的坐标数据;将平行于所述第一基准边的其中两个检测边上的检测点的坐标数据与第一基准边上的基准点的坐标数据进行比较,计算其中两个检测边的位置偏差值;将平行于所述第二基准边的另外两个检测边上的检测点的坐标数据与第二基准边上的基准点的坐标数据进行比较,计算另外两个检测边的位置偏差值。
9.在一些实施例中,所述第二操作包括对称度矫正操作;所述控制器基于所述加工治具的位置偏差值得到所述加工治具的对称度检测结果,根据所述加工治具的对称度检测结果,生成第二控制指令,包括:判断所述加工治具的各个检测边的位置偏差值是否均为零;如果至少一检测边的位置偏差值不为零,则表明所述加工治具存在对称度偏差,计算所述检测边的位置补偿值;基于所述检测边的位置补偿值,生成第二控制指令,所述第二控制指令用于指示对所述加工治具上所夹紧的工件执行对称度矫正操作。
10.在一些实施例中,所述检测机构包括:检测器;固定支架,与一加工机构可拆卸连接且与所述检测器连接,用于承载所述检测器,所述固定支架包括:连接件,与所述加工机构连接;第一支臂,与所述连接件连接且远离所述加工机构;第二支臂,与所述第一支臂连接,且所述第二支臂远离所述第一支臂的一端与所述检测器连接;及加强件,位于所述第一支臂与所述第二支臂之间且分别与所述第一支臂及所述第二支臂连接。
11.本技术第二方面提供一种检测方法,用于对加工治具的直线度及对称度进行检测,包括:获取一检测机构检测的所述加工治具的直线度数据;根据所述加工治具的直线度数据,确定所述加工治具的角度偏差值;基于所述加工治具的角度偏差值,生成第一控制指令;根据所述第一控制指令,控制对所述加工治具进行第一操作;根据所述第一操作的操作结果,构建所述加工治具的参考基准区域;获取所述参考基准区域的位置数据及所述检测机构检测的所述加工治具的位置数据;根据所述参考基准区域的位置数据及所述加工治具的位置数据,确定所述加工治具的位置偏差值;基于所述加工治具的位置偏差值得到所述加工治具的对称度检测结果,根据所述加工治具的对称度检测结果,生成第二控制指令;根据所述第二控制指令,控制对所述加工治具进行第二操作。
12.在一些实施例中,所述加工治具的直线度数据包括所述加工治具的任意一检测边上的任意两点的坐标数据;所述根据所述加工治具的直线度数据,确定所述加工治具的角度偏差值;基于所述加工治具的角度偏差值,生成第一控制指令的步骤,包括:基于所述加工治具的任意一检测边上的任意两点的坐标数据,计算所述加工治具的角度偏差值;判断所述加工治具的角度偏差值是否为零;如果所述加工治具的角度偏差值不为零,则计算所述加工治具的角度补偿值;基于所述加工治具的角度补偿值,生成第一控制指令,所述第一
控制指令用于指示对所述加工治具执行直线度矫正操作直至所述加工治具的角度偏差值为零。
13.在一些实施例中,所述第一操作还包括重新检测,所述第一操作的操作结果包含执行直线度矫正操作后的所述加工治具的角度偏差值为零;所述检测方法还包括:获取所述检测机构检测的直线度矫正操作后的所述加工治具的直线度数据,计算直线度矫正操作后的所述加工治具的角度偏差值。
14.在一些实施例中,所述构建所述加工治具的参考基准区域的步骤,包括:获取所述检测机构检测的基准治具的基准数据,所述基准数据包括所述基准治具的每一基准边上任意两点的坐标数据;根据所述基准治具的每一基准边上任意两点的坐标数据,构建所述加工治具的参考基准区域。
15.在一些实施例中,所述参考基准区域的位置数据包括所述参考基准区域的每一基准边位于基准位时其上一基准点的坐标数据;所述加工治具的位置数据包括所述加工治具的每一检测边位于基准位时其上一检测点的坐标数据;所述根据所述参考基准区域的位置数据及所述加工治具的位置数据,确定所述加工治具的位置偏差值的步骤,包括:选取所述参考基准区域的两个相垂直的基准边作为第一基准边及第二基准边;获取所述检测机构检测的所述第一基准边及所述第二基准边位于基准位时其上一基准点的坐标数据;以及所述加工治具的每一检测边位于基准位时其上一检测点的坐标数据;将平行于所述第一基准边的其中两个检测边上的检测点的坐标数据与第一基准边上的基准点的坐标数据进行比较,计算其中两个检测边的位置偏差值;将平行于所述第二基准边的另外两个检测边上的检测点的坐标数据与第二基准边上的基准点的坐标数据进行比较,计算另外两个检测边的位置偏差值。
16.在一些实施例中,所述第二操作包括对称度矫正操作;所述基于所述加工治具的位置偏差值得到所述加工治具的对称度检测结果,根据所述加工治具的对称度检测结果,生成第二控制指令的步骤,包括:判断所述加工治具的各个检测边的位置偏差值是否均为零;如果至少一所述检测边的位置偏差值不为零,则表明所述加工治具存在对称度偏差,计算所述检测边的位置补偿值;基于所述检测边的位置补偿值,生成第二控制指令,所述第二控制指令用于指示对所述加工治具上所夹紧的工件执行对称度矫正操作。
17.上述检测装置及检测方法,通过获取检测机构检测的加工治具的直线度数据,根据加工治具的直线度数据,确定加工治具的角度偏差值,基于加工治具的角度偏差值,生成第一控制指令,以控制加工治具进行第一操作,实现对治具的直线度的自动检测及矫正;通过根据第一操作的操作结果,构建加工治具的参考基准区域,获取参考基准区域的位置数据及检测机构检测的加工治具的位置数据,根据参考基准区域的位置数据及加工治具的位置数据,确定加工治具的位置偏差值,基于加工治具的位置偏差值检测加工治具的对称度,根据对称度检测结果,生成第二控制指令,控制对加工治具进行第二操作,实现对加工治具的对称度的自动检测及矫正。加工治具的直线度及对称度依次被检测及矫正,实现了检测及矫正的自动化,无需作业人员手动检测及矫正,降低人力成本,提升检测及矫正效率,有利于提升加工效率。
附图说明
18.图1是本技术一些实施例提供的检测装置的硬件架构图。
19.图2是本技术一些实施例提供的加工装置的平面结构示意图。
20.图3是本技术一些实施例提供的固定支架的立体结构示意图。
21.图4是本技术一些实施例提供的直线度数据的示意图。
22.图5是本技术一些实施例提供的位置偏差值的示意图。
23.图6是本技术一些实施例提供的检测方法的流程示意图。
24.图7是图6所示的s306的一些流程示意图。
25.图8是图6所示的s320的一些流程示意图。
26.主要元件符号说明
27.检测装置
ꢀꢀꢀꢀꢀꢀꢀꢀꢀꢀꢀꢀꢀꢀꢀꢀꢀ
100
28.检测机构
ꢀꢀꢀꢀꢀꢀꢀꢀꢀꢀꢀꢀꢀꢀꢀꢀꢀ
10
29.检测器
ꢀꢀꢀꢀꢀꢀꢀꢀꢀꢀꢀꢀꢀꢀꢀꢀꢀꢀꢀ
12
30.固定支架
ꢀꢀꢀꢀꢀꢀꢀꢀꢀꢀꢀꢀꢀꢀꢀꢀꢀ
14
31.连接件
ꢀꢀꢀꢀꢀꢀꢀꢀꢀꢀꢀꢀꢀꢀꢀꢀꢀꢀꢀ
141
32.第一支臂
ꢀꢀꢀꢀꢀꢀꢀꢀꢀꢀꢀꢀꢀꢀꢀꢀꢀ
142
33.第二支臂
ꢀꢀꢀꢀꢀꢀꢀꢀꢀꢀꢀꢀꢀꢀꢀꢀꢀ
143
34.加强件
ꢀꢀꢀꢀꢀꢀꢀꢀꢀꢀꢀꢀꢀꢀꢀꢀꢀꢀꢀ
144
35.安装件
ꢀꢀꢀꢀꢀꢀꢀꢀꢀꢀꢀꢀꢀꢀꢀꢀꢀꢀꢀ
145
36.控制器
ꢀꢀꢀꢀꢀꢀꢀꢀꢀꢀꢀꢀꢀꢀꢀꢀꢀꢀꢀ
20
37.加工装置
ꢀꢀꢀꢀꢀꢀꢀꢀꢀꢀꢀꢀꢀꢀꢀꢀꢀ
200
38.加工平台
ꢀꢀꢀꢀꢀꢀꢀꢀꢀꢀꢀꢀꢀꢀꢀꢀꢀ
202
39.第一加工机构
ꢀꢀꢀꢀꢀꢀꢀꢀꢀꢀꢀꢀꢀ
204
40.第二加工机构
ꢀꢀꢀꢀꢀꢀꢀꢀꢀꢀꢀꢀꢀ
206
41.第一加工治具
ꢀꢀꢀꢀꢀꢀꢀꢀꢀꢀꢀꢀꢀ
208
42.第二加工治具
ꢀꢀꢀꢀꢀꢀꢀꢀꢀꢀꢀꢀꢀ
210
43.第三加工治具
ꢀꢀꢀꢀꢀꢀꢀꢀꢀꢀꢀꢀꢀ
212
44.第四加工治具
ꢀꢀꢀꢀꢀꢀꢀꢀꢀꢀꢀꢀꢀ
214
具体实施方式
45.下面详细描述本技术的实施方式,所述实施方式的示例在附图中示出,其中自始至终相同或类似的标号表示相同或类似的元件或具有相同或类似功能的元件。下面通过参考附图描述的实施方式是示例性的,仅用于解释本技术,而不能理解为对本技术的限制。
46.在本技术的描述中,需要理解的是,术语“中心”、“纵向”、“横向”、“长度”、“宽度”、“厚度”、“上”、“下”、“前”、“后”、“左”、“右”、“竖直”、“水平”、“顶”、“底”、“内”、“外”、“顺时针”、“逆时针”等指示的方位或位置关系为基于附图所示的方位或位置关系,仅是为了便于描述本技术和简化描述,而不是指示或暗示所指的装置或元件必须具有特定的方位、以特定的方位构造和操作,因此不能理解为对本技术的限制。此外,术语“第一”、“第二”仅用于描述目的,而不能理解为指示或暗示相对重要性或者隐含指明所指示的技术特征的数量。
由此,限定有“第一”、“第二”的特征可以明示或者隐含地包括一个或者更多个所述特征。在本技术的描述中,需要说明的是,“多个”的含义是两个或两个以上,除非另有明确具体的限定。
47.在本技术的描述中,需要说明的是,除非另有明确的规定和限定,术语“安装”、“相连”、“连接”应做广义理解,例如,可以是固定连接,也可以是可拆卸连接,或一体地连接;可以是机械连接,也可以是电连接或可以相互通讯,可以是直接相连,也可以通过中间媒介间接相连,可以是两个元件内部的连通或两个元件的相互作用关系。对于本领域的普通技术人员而言,可以根据具体情况理解上述术语在本技术中的具体含义。
48.在本技术中,除非另有明确的规定和限定,第一特征在第二特征之“上”或之“下”可以包括第一特征和第二特征直接接触,也可以包括第一特征和第二特征不是直接接触而是通过它们之间的另外的特征接触。而且,第一特征在第二特征“之上”、“上方”和“上面”包括第一特征在第二特征正上方和斜上方,或仅仅表示第一特征水平厚度高于第二特征。第一特征在第二特征“之下”、“下方”和“下面”包括第一特征在第二特征正下方和斜下方,或仅仅表示第一特征水平厚度小于第二特征。
49.下文的公开提供了许多不同的实施方式或例子用来实现本技术的不同结构。为了简化本技术的公开,下文中对特定例子的部件和设置进行描述。当然,它们仅仅为示例,并且目的不在于限制本技术。此外,本技术可以在不同例子中重复参考数字和/或参考字母,这种重复是为了简化和清楚的目的,其本身不指示所讨论各种实施方式和/或设置之间的关系。
50.本技术实施例提供一种检测装置,用于对加工治具的直线度及对称度进行检测,包括:检测机构,用于检测该加工治具;控制器,与该检测机构耦接,用于获取该检测机构检测的该加工治具的直线度数据,根据该加工治具的直线度数据,确定该加工治具的角度偏差值,基于该加工治具的角度偏差值,生成第一控制指令,以控制对该加工治具进行第一操作;该控制器还用于根据该第一操作的操作结果,构建该加工治具的参考基准区域,获取该参考基准区域的位置数据及该检测机构检测的该加工治具的位置数据;根据该参考基准区域的位置数据及该加工治具的位置数据,确定该加工治具的位置偏差值,基于该加工治具的位置偏差值得到该加工治具的对称度检测结果,根据该加工治具的对称度检测结果,生成第二控制指令,以控制对该加工治具进行第二操作。
51.本技术实施例还提供一种检测方法,用于对加工治具的直线度及对称度进行检测,包括:获取一检测机构检测的该加工治具的直线度数据;根据该加工治具的直线度数据,确定该加工治具的角度偏差值;基于该加工治具的角度偏差值,生成第一控制指令;根据该第一控制指令,控制对该加工治具进行第一操作;根据该第一操作的操作结果,构建该加工治具的参考基准区域;获取该参考基准区域的位置数据及该检测机构检测的该加工治具的位置数据;根据该参考基准区域的位置数据及该加工治具的位置数据,确定该加工治具的位置偏差值;基于该加工治具的位置偏差值得到该加工治具的对称度检测结果,根据该加工治具的对称度检测结果,生成第二控制指令;根据该第二控制指令,控制对该加工治具进行第二操作。
52.本技术实施例提供的检测装置及检测方法,通过获取检测机构检测的加工治具的直线度数据,根据加工治具的直线度数据,确定加工治具的角度偏差值,基于加工治具的角
度偏差值,生成第一控制指令,以控制加工治具进行第一操作,实现对加工治具的直线度的自动检测及矫正;通过根据第一操作的操作结果,构建加工治具的参考基准区域,获取参考基准区域的位置数据及检测机构检测的加工治具的位置数据,根据参考基准区域的位置数据及加工治具的位置数据,确定加工治具的位置偏差值,基于加工治具的位置偏差值检测加工治具的对称度,根据对称度检测结果,生成第二控制指令,控制对加工治具进行第二操作,实现对加工治具的对称度的自动检测及矫正。加工治具的直线度及对称度依次被检测及矫正,实现了检测及矫正的自动化,无需作业人员手动检测及矫正,降低人力成本,提升检测及矫正效率,有利于提升加工效率。
53.以下将结合附图对本技术的一些实施例进行详细说明。
54.相关技术中,加工治具用于承载/固定/夹紧工件,加工治具设置于一加工装置上。该加工装置还包括加工平台、平台驱动件、治具驱动件、加工机构等结构。加工治具与治具驱动件连接,治具驱动件设置于加工平台上,治具驱动件用于驱动加工治具转动,进而带动工件转动。平台驱动件与加工平台连接,平台驱动件用于驱动加工平台转动,进而带动加工平台上所有的加工治具及工件转动。加工机构用于对加工治具上的工件进行加工,加工治具的数量可以为一个、两个、三个或更多个,加工机构的数量可以为一个、两个、三个或更多个,不同的加工机构可对工件进行不同工艺的加工,例如,不同的加工机构可分别对工件进行粗抛、细抛和精抛。示例性地,加工装置为湿式抛光机,加工机构为湿抛机头,加工平台为机台,机台上设有多个加工治具,加工治具夹紧工件后,机台带动夹紧工件的加工治具转动至与湿抛机头相对应的加工位,治具驱动件驱动加工治具带动工件转动以配合湿抛机头,从而使得湿抛机头对工件实现加工。
55.加工装置在使用的过程中,由于加工平台精度稳定性不佳,导致加工治具的直线度和对称度易出现偏差,为保证加工治具的直线度和对称度的精度,需要定期矫正加工治具的直线度和对称度。为了便于说明加工治具的直线度和对称度,定义加工机构具有x轴移动组件、y轴移动组件及z轴移动组件,x轴移动组件、y轴移动组件及z轴移动组件用于带动加工机构的如抛光头运动以靠近或远离加工治具上的工件。加工治具具有两个长边和两个短边。通常情况下,加工机构的精度较佳,可以作为基准原点,以加工机构的x轴移动组件和y轴移动组件的移动方向为标准的x轴和y轴并构建以加工机构为基准原点的四边形参考区域,四边形参考区域包括与加工治具的长边和短边相对应的长参考边和短参考边。加工治具的直线度可以理解为加工治具的长边与长参考边是否平行、加工治具的短边是否与短参考边平行。如果为是,则加工治具的直线度合格,如果为否,则加工治具的直线度不合格。加工治具的对称度可以理解为加工治具的长边是否与长参考边重合、加工治具的短边是否与短参考边重合,如果为是,则加工治具的对称度合格,如果为否,则加工治具的对称度不合格。
56.请参阅图1,本技术一些实施例提供了一种检测装置。检测装置100用于对加工治具的直线度及对称度进行检测,还可以对加工治具的直线度及对称度进行矫正。检测装置100包括检测机构10及控制器20。检测机构10与控制器20耦接,检测机构10用于检测加工治具的直线度数据及位置数据,并将检测到的加工治具的直线度数据及位置数据传输至控制器20,控制器20根据获取的加工治具的直线度数据及位置数据进行治具的直线度及对称度检测及根据检测的结果对加工治具进行直线度矫正及对称度矫正操作。
57.控制器20可以接收、处理及发送数据,控制器20可以为门电路控制器,还可以为中央处理器(cpu,central processing unit)、其他通用处理器、数字信号处理器(dsp,digital signal processor)、专用集成电路(asic,application specific integrated circuit)、现场可编程门阵列(fpga,field-programmable gate array)或者其他可编程逻辑器件、分立门或者晶体管逻辑器件、分立硬件组件等。通用处理器可以是微处理器或者该通用处理器也可以是任何常规的处理器等,控制器20是检测装置100的控制中心,利用各种接口和线路连接整个检测装置100的各个部分。
58.请参阅图2,本技术的一些实施例以加工治具包括两条长检测边和两条短检测边为例进行说明。加工装置200为湿式抛光机,加工机构包括湿抛机头,加工治具的数量为四个,分别为第一加工治具208、第二加工治具210、第三加工治具212和第四加工治具214,加工机构的数量为两个,分别为第一加工机构204和第二加工机构206,加工平台202可带动所有的加工治具转动以使加工治具在不同的加工位被加工机构进行加工,不同的加工机构可对工件施加不同的加工工艺。
59.请参阅图3,在一些实施例中,检测机构10包括检测器12和固定支架14。固定支架14与加工机构可拆卸连接,且固定支架14与检测器12连接,固定支架14用于承载检测器12。
60.检测器12可以为高精度探头,检测器12可检测加工治具的任意一检测边上的任意点的坐标数据,并将加工治具的任意一检测边上的任意点的坐标数据传输至控制器20。检测器12还用于检测基准治具的每一基准边上的多个基准点的坐标数据,并将基准治具的每一基准边上的多个基准点的坐标数据传输至控制器20。
61.固定支架14包括连接件141、第一支臂142、第二支臂143和加强件144。连接件141、第一支臂142、第二支臂143和加强件144均大致为板状。连接件141与加工机构连接。第一支臂142的一端与连接件141连接,连接件141的横截面积大于第一支臂142的横截面积,使得连接件141能够更好的与加工机构连接。第二支臂143与第一支臂142相垂直且连接于连接件141的另一端,第二支臂143远离第一支臂142的一端与检测器12连接。通过第一支臂142和第二支臂143,使得加工机构在不与加工治具相接触的情况下,检测器12能够与加工治具相对并对加工治具进行检测。加强件144位于第一支臂142和第二支臂143之间且与第一支臂142及第二支臂143分别连接,通过加强件144可以加强固定支架14的强度,防止固定支架14跟随加工机构运动时固定支架14松动而影响检测器12的检测精度。
62.在一些实施例中,固定支架14还可以包括安装件145。安装件145与第二支臂143远离第一支臂142的一端连接,安装件145用于安装检测器12。
63.本实施例中,检测装置100首先对加工治具的直线度进行检测及矫正。控制器20用于获取检测机构10检测的加工治具的直线度数据,根据加工治具的直线度数据,确定加工治具的角度偏差值,基于加工治具的角度偏差值,生成第一控制指令,以控制对加工治具进行第一操作。
64.一些实施例提供的检测装置100对加工治具的直线度进行检测及矫正的一实施过程大致为:加工机构带动固定支架14及检测器12运动,使得检测器12能够检测基准治具的基准数据及加工治具的直线度数据;检测器12将检测到基准治具的基准数据及加工治具的直线度数据传输至控制器20;控制器20获取基准治具的基准数据及加工治具的直线度数据,控制器20根据基准治具的基准数据构建该加工治具的参考基准区域,控制器20根据加
工治具的直线度数据确定加工治具的角度偏差值;控制器20基于加工治具的角度偏差值,生成第一控制指令,以控制治具驱动件带动加工治具进行第一操作。
65.在一些实施例中,加工治具包括四个检测边,分别为两个长检测边和两个短检测边。加工治具的直线度数据包括加工治具的任意一检测边上的任意两点的坐标数据。该检测边可以是任一长检测边或任一短检测边但需是同一检测边上。
66.基准治具包括四个基准边,分别为两个长基准边及两个短基准边。基准治具的基准数据包括基准治具的每一长基准边及每一短基准边上任意两点的坐标数据。
67.控制器20能够根据基准治具的每一长基准边及每一短基准边上任意两点的坐标数据构建该加工治具的参考基准区域。
68.请参阅图4,实线表示控制器20所构建的四边形的参考基准区域,虚线表示加工治具。加工治具的直线度数据包括加工治具的一长检测边上的a点和b点的坐标数据。其中,a点的坐标数据为(x1、y1),b点的坐标数据为(x2,y2),可以理解地,坐标系的原点可以为四边形的基准参考区域的基准原点,或检测器12及加工机构所定义的坐标原点。
69.本实施例中,控制器20根据加工治具的直线度数据,确定加工治具的角度偏差值,具体为:控制器20基于加工治具的任意一检测边上的任意两点的坐标数据,计算加工治具的角度偏差值。
70.示例性地,如图4所示,加工治具的角度偏差值为θ,θ=θ1=θ2,通过a点和b点坐标及反正切函数可知,θ=arctan((y2-y1)/(x2-x1))。如此,计算出加工治具的角度偏差值θ。
71.本实施例中,第一操作包括执行直线度矫正操作。控制器20基于加工治具的角度偏差值θ,生成第一控制指令,具体为:控制器20判断加工治具的角度偏差值θ是否为零,如果加工治具的角度偏差值θ不为零,则表明加工治具的该检测边与参考基准区域的相对应的基准边不平行,加工治具存在直线度偏差;控制器20根据加工治具的角度偏差值,计算加工治具的角度补偿值;控制器20基于加工治具的角度补偿值,生成第一控制指令,第一控制指令用于指示对加工治具执行直线度矫正操作直至加工治具的角度偏差值为零。
72.示例性地,控制器20判断加工治具的角度偏差值θ不为零,即表示加工治具的直线度不合格,加工治具的直线度需要进行矫正。控制器20根据该角度偏差值θ计算加工治具的角度补偿值,角度补偿值可以理解为加工治具需要转动补偿角度才能够使角度偏差值为零,由于加工治具的角度偏差值为θ,相应地,加工治具顺时针旋转θ即可使角度偏差值为零,即角度补偿值为θ。控制器20基于加工治具的角度补偿值θ,生成第一控制指令,第一控制指令为对加工治具执行顺时针转动θ角度。即对加工治具执行直线度矫正操作为控制治具驱动件驱动加工治具顺时针转动θ角度,从而实现对加工治具的直线度矫正。
73.可以理解地,加工机构的数量为多个时,多个加工机构共用一套四边形的参考基准区域。对加工平台202上的所有加工治具的直线度进行检测及矫正时,可以通过一个加工机构进行,也可以通过不同的加工机构进行。不同的加工机构对不同的加工治具的直线度进行检测及矫正时,可以同时进行检测及矫正。
74.可以理解地,在其他的实施例中,控制器20判断加工治具的角度偏差值为零时,表示加工治具的直线度合格,加工治具的直线度不需要进行矫正,检测装置100可继续对加工治具的对称度进行检测及矫正。
75.在一些实施例中,第一操作还可以包括重新检测。第一操作的操作结果包含执行
直线度矫正操作后的加工治具的角度偏差值为零。
76.控制器20根据第一控制指令对加工治具执行直线度矫正操作以后,检测器12重新检测加工治具的直线度数据,控制器20还用于获取检测机构10的检测器12检测执行直线度矫正操作后的加工治具的直线度数据,计算执行直线度矫正操作后的加工治具的角度偏差值;控制器20判断直线度矫正操作后的加工治具的角度偏差值为零时,表示执行第一操作后的加工治具的直线度合格。可以理解地,检测装置100执行第一操作的重新检测时,如果控制器20判断直线度矫正操作后的加工治具的角度偏差值不为零时,例如,控制器20确定执行直线度矫正操作后的加工治具的角度偏差值为θ
′
,则控制器20进一步根据加工治具的角度偏差值θ
′
,计算加工治具的角度补偿值θ
′
,并根据角度补偿值θ
′
,重新生成第一控制指令,指示治具驱动件驱动加工治具顺时针或逆时针旋转θ
′
角度,以对加工治具的直线度再次进行矫正,直至执行直线度矫正操作后的加工治具的角度偏差值为零。经过对加工治具执行第一操作后,实现加工治具的每一检测边与参考基准区域的相对应的基准边相平行,满足直线度要求。
77.本实施例中,检测装置100对加工治具的直线度进行检测及矫正后,再对加工治具的对称度进行检测及矫正。可以理解地,检测装置100对加工治具的对称度进行检测和进行矫正可以分开进行,例如,在对加工装置200进行检测时,检测装置100对加工治具的对称度进行检测,检测后保存相关数据,在加工装置200对该加工治具上所夹紧的工件进行加工时,检测装置100对该加工治具上所夹紧的工件进行矫正。
78.控制器20还用于根据第一操作的操作结果,构建加工治具的参考基准区域,获取参考基准区域的位置数据及检测机构10检测的加工治具的位置数据;控制器20根据参考基准区域的位置数据及加工治具的位置数据,确定加工治具的位置偏差值,基于加工治具的位置偏差值检测加工治具的对称度,根据加工治具的对称度检测结果,生成第二控制指令,以控制对加工治具进行第二操作。
79.一些实施例提供的检测装置100对加工治具的对称度进行检测及矫正的一实施过程大致为:
80.首先,控制器20根据基准治具的基准数据构建该加工治具的参考基准区域。
81.其中,基准治具的基准数据包括基准治具的每一基准边上任意两点的坐标数据。控制器20能够根据基准治具的每一基准边上任意两点的坐标数据构建该加工治具的参考基准区域。在加工治具的直线度及对称度均合格的情况下,加工治具与参考基准区域相重合,该参考基准区域可以理解为加工机构对工件进行加工的区域,还可以理解为,加工治具与该参考基准区域完全重合时,加工机构对工件的加工符合要求。
82.接着,控制器20选取参考基准区域的两个相垂直的基准边作为第一基准边及第二基准边,获取第一基准边位于基准位时其上的一基准点的坐标数据,以及第二基准边位于基准位时其上的一基准点的坐标数据。
83.检测器12进一步用于检测基准治具的四个基准边位于基准位时,四个基准边上的一基准点的坐标数据,并将这四个基准边上的基准点的坐标数据传输至控制器20。其中,基准位是指基准边与x轴平行时所处的位置。控制器20构建参考基准区域后,选取一长基准边作为第一基准边,选取与该长基准边垂直的基准短边作为第二基准边,从获取到的数据中获取第一基准边位于基准位时其上的一基准点的坐标数据,以及第二基准边位于基准位时
其上的一基准点的坐标数据,将第一基准边位于基准位时其上的一基准点的坐标数据中y向坐标值作为第一基准边位于基准位时其上的一基准点的位置数据,将第二基准边位于基准位时其上的一基准点的坐标数据中y向坐标值作为第二基准边位于基准位时其上的一基准点的位置数据。
84.检测器12还进一步用于检测加工治具的四个检测边位于基准位时,四个检测边上的一检测点的坐标数据,并将这四个检测边上的检测点的坐标数据传输至控制器20。
85.然后,控制器20获取检测检测器12检测的加工治具的位置数据。其中,加工治具的位置数据包括加工治具的四个检测边位于基准位时其上一检测点的坐标数据。四个检测边位于基准位时其上一检测点的位置数据分别为四个检测边位于基准位时其上一检测点的坐标数据中y向坐标值。
86.控制器20分别将平行于第一基准边的其中两个检测边上的检测点的坐标数据与第一基准边上的基准点的坐标数据进行比较,判断二者是否相同,若相同,则表明加工治具的这两个检测边的位置无偏差,若不同,则表明加工治具的这两个检测边存在位置偏差,计算加工治具的这两个检测边的位置偏差值;同理,控制器20还进一步分别将平行于第二基准边的另外两个检测边上的检测点的坐标数据与第二基准边上的基准点的坐标数据进行比较,判断二者是否相同,若相同,则表明加工治具的另外这两个检测边的位置无偏差,若不同,则表明加工治具的另外这两个检测边存在位置偏差,计算加工治具的另外这两个检测边的位置偏差值。
87.控制器20进一步基于加工治具的位置偏差值检测加工治具的对称度,根据加工治具的对称度的检测结果,生成第二控制指令,以控制加工机构对加工治具进行第二操作。
88.请参阅图5,实线表示参考基准区域,虚线表示加工治具。图5.1的a1可以理解为参考基准区域的第一基准边l1位于基准位时其上的基准点,图5.3的a2可以理解为参考基准区域的第二基准边l2位于基准位时其上的基准点,图5.1的a3、图5.2的a4、图5.3的a5和图5.4的a6分别为加工治具的四个检测边l1~l4位于基准位时其上的检测点。
89.本实施例中,控制器20根据参考基准区域的位置数据及加工治具的位置数据,确定加工治具的位置偏差值,具体为:基于加工治具的各个检测边位于基准位时其上的检测点的y向坐标数据与对应的基准边位于基准位时其上的基准点的y向坐标数据,计算加工治具的各个检测边的位置偏差值。
90.示例性地,以图5的水平方向为x轴,垂直方向为y轴,将平行于x轴的位置作为基准位,y向坐标数据作为位置数据。图5.1中,第一基准边l1位于基准位,其上的基准点a1的坐标数据为(x1,y1),检测边l1位于基准位,其上的检测点a3的坐标数据为(x3,y3),将检测边l1与第一基准边l1的y向坐标数据相比,计算检测边l1的位置偏差值为y3-y1。图5.2中,控制加工治具旋转180
°
,使检测边l2位于基准位,检测边l2上的检测点a4的坐标数据为(x4,y4),将检测边l2与第一基准边l1的y向坐标数据相比,计算检测边l2的位置偏差值为y4-y1。图5.3中,控制加工治具在图5.1的基础上旋转90
°
,使检测边l3位于基准位,检测边l3上的检测点a5的坐标数据为(x5,y5),对应的第二基准边l2位于基准位,其上的基准点a2的坐标数据为(x2,y2),将检测边l3与第二基准边l2的y向坐标数据相比,计算检测边l3的位置偏差值为y5-y2。图5.4中,控制加工治具在图5.3的基础上旋转180
°
,使检测边l4位于基准位,检测边l4上的检测点a6的坐标数据为(x6,y6),将检测边l4与第二基准边l2的y向坐标数据相比,计
算检测边l4的位置偏差值为y6-y2。
91.本实施例中,第二操作包括执行对称度矫正操作。控制器20基于加工治具的位置偏差值检测加工治具的对称度,根据加工治具的对称度的检测结果,生成第二控制指令,具体为:控制器20判断加工治具的各个检测边的位置偏差值是否均为零。示例性地,y3-y1、y4-y1、y5-y2和y6-y2中至少有一个不为零,则表明加工治具存在对称度偏差。可以理解地,由于加工治具大致为矩形,偏差值不为零的检测边通常为成对出现。
92.控制器20根据不为零的检测边的位置偏差值,计算检测边的位置补偿值。示例性地,y3-y1和y4-y1均不为零,y3-y1例如为10mm,y4-y1例如为-10mm,则检测边l1和检测边l2的位置补偿值为-10mm和10mm。
93.控制器20基于检测边的位置补偿值,生成第二控制指令,第二控制指令用于指示对加工治具上所夹紧的工件执行对称度矫正操作直至加工治具的各个检测边的位置偏差值均为零。示例性地,控制器20基于检测边l1的位置补偿值为-10mm,检测边l2的位置补偿值为10mm,则对加工治具上所夹紧的工件执行对称度矫正操作可以理解为,加工机构对加工治具上的工件的一长边进行加工时,加工机构在参考基准区域的基础上朝靠近工件的方向移动10mm,以使加工机构能够精准地对工件进行加工,对应另一长边加工工件时,加工机构在参考基准区域的基础上朝远离工件的方向移动10mm,以使加工机构能够精准地对工件进行加工。如此,实现对加工治具上所夹紧的工件执行对称度矫正操作。
94.可以理解地,所有的加工治具的对称度检测可通过一个加工机构进行,也可以通过不同的加工机构进行。例如,第一加工治具208、第二加工治具210、第三加工治具212和第四加工治具214的对称度均由第一加工机构204进行检测,第一加工机构204检测所获取的数据及位置补偿值可以和第二加工机构206共用。第一加工机构204检测第一加工治具208的对称度需要进行矫正,一检测边的位置补偿值为-10mm和10mm,第一加工机构204对第一加工治具208上与该检测边对应的工件的边进行加工时,第一加工机构204按照位置补偿值为-10mm和10mm对第一加工治具208所夹紧的工件进行第一加工,第一加工机构204加工完成以后,第一加工治具208转动至与第二加工机构206相对应的加工位,第二加工机构206仍然按照位置补偿值为-10mm和10mm的数据对第一加工治具208所夹紧的工件进行第二加工。其中,第一加工可以为粗抛,第二加工可以为细抛。显然,加工机构的数量包括三个或三个以上时,各加工机构均可以与第一加工机构204共用对称度矫正操作的相关数据。
95.本技术实施例提供的检测装置100,通过获取检测机构10检测的加工治具的直线度数据,根据加工治具的直线度数据,确定加工治具的角度偏差值,基于加工治具的角度偏差值,生成第一控制指令,以控制对加工治具执行直线度矫正操作,实现对加工治具的直线度的自动检测及矫正;通过重新检测加工治具的直线度,确保加工治具的直线度符合要求,提升加工治具的直线度的检测及矫正精度。通过根据第一操作的执行直线度矫正操作的加工治具的直线度为零的结果,构建加工治具的参考基准区域,获取参考基准区域的位置数据及检测机构10检测的加工治具的位置数据,根据参考基准区域的位置数据及加工治具的位置数据,确定加工治具的位置偏差值,基于加工治具的位置偏差值检测加工治具的对称度,根据加工治具的对称度的检测结果,生成第二控制指令,控制对加工治具进行对称度矫正操作,实现对加工治具的对称度的自动检测及矫正。加工治具的直线度及对称度依次被检测及矫正,实现了加工治具的直线度及对称度检测及矫正的自动化,无需作业人员手动
检测及矫正,降低人力成本,提升检测及矫正效率,有利于提升加工效率。
96.请参阅图6,本技术一些实施例提供了一种检测方法。本技术实施例提供的检测方法用于对加工治具的直线度及对称度进行检测。对于需要检测及矫正加工治具的直线度及对称度的加工装置200,可以直接在加工装置200上集成本技术的检测方法所提供的检测功能,或者安装用于实现本技术的检测方法的客户端。再如,本技术所提供的检测方法还可以以软件开发工具包(sdk,software development kit)的形式运行在该加工装置200上,以sdk的形式提供检测功能的接口,控制器20或其他设备通过提供的接口即可实现检测功能。
97.请参阅图6,检测方法包括如下步骤s302-步骤s322。
98.s302,获取一检测机构10检测的加工治具的直线度数据。
99.具体地,将一检测器12通过一固定支架14设置于加工装置200的加工机构上,通过检测器12对加工治具进行检测以获取加工治具的直线度数据。其中,加工治具的直线度数据包括加工治具的任意一检测边上的任意两点的坐标数据。
100.s304,根据加工治具的直线度数据,确定加工治具的角度偏差值。
101.在一些实施例中,加工治具的直线度包括加工治具的任意一检测边上的任意两点的坐标数据。控制器20基于治具的任意一检测边上的任意两点的坐标数据,计算治具的角度偏差值。
102.控制器20根据加工治具的任意一检测边上的任意两点的坐标数据,计算加工治具的角度偏差值。示例性地,检测器12检测到加工治具的一检测边上的两点a和b的坐标数据为(x1、y1)和(x2,y2),则控制器计算加工治具的角度偏差值为θ,其中,θ=arctan((y2-y1)/(x2-x1))。
103.s306,基于加工治具的角度偏差值,生成第一控制指令。
104.控制器20判断加工治具的角度偏差值θ不为零时,计算加工治具的角度补偿值;控制器20基于加工治具的角度补偿值,生成第一控制指令,第一控制指令用于指示对加工治具执行直线度矫正操作。
105.s308,根据第一控制指令,控制对加工治具进行第一操作。
106.具体地,通过步骤s304-步骤s308,根据加工治具的直线度数据,计算得出加工治具的角度偏差值,并基于加工治具的角度偏差值,生成第一控制指令,根据第一控制指令,控制加工装置200的治具驱动件对加工治具进行第一操作。如此,实现对加工治具的直线度进行检测及矫正的功能。
107.在一些实施例中,第一操作还包括重新检测,重新检测的步骤包括如下步骤s310-步骤s312。
108.s310,获取检测机构10检测的直线度矫正操作后的加工治具的直线度数据,计算直线度矫正操作后的加工治具的角度偏差值。
109.s312,判断直线度矫正操作后的加工治具的角度偏差值是否为零。
110.具体地,步骤s310-步骤s312与步骤s302-步骤s304大致相似。如此,对治具进行第一操作后,继续执行步骤s310-步骤s312,可以对治具的直线度进行确认,保证治具的直线度的精度。
111.可以理解地,在其他的实施例中,步骤s310-步骤s312可以省略。
112.请继续参阅图6,对加工治具的直线度进行检测及矫正后,检测方法还执行如下步
骤s314-步骤s322。
113.s314,根据第一操作的操作结果,构建加工治具的参考基准区域。
114.具体地,在加工治具的角度偏差值为零的情况下,以检测器12或加工机构为基准原点构建参考基准区域,该参考基准区域可以理解为加工机构对工件进行加工的区域,还可以理解为,加工治具与该参考基准区域完全重合时,加工机构对工件的加工符合要求。
115.在本实施例中,加工治具的参考基准区域的构建方法为:
116.控制器20获取检测机构10检测的基准治具的基准数据,其中,基准治具的基准数据包括基准治具的每一基准边上任意两点的坐标数据。
117.控制器根据基准治具的每一基准边上任意两点的坐标数据,构建参考基准区域。该参考基准区域包括与加工治具的四个检测边相对应的四个基准边。
118.s316,获取参考基准区域的位置数据及检测机构10检测的加工治具的位置数据。
119.参考基准区域的位置数据包括参考基准区域的每一基准边位于基准位时其上一基准点的坐标数据。
120.加工治具的位置数据包括加工治具的每一检测边位于基准位时其上一检测点的坐标数据。
121.s318,根据参考基准区域的位置数据及加工治具的位置数据,确定加工治具的位置偏差值。
122.在一些实施例中,控制器20选取参考基准区域的两个相垂直的基准边作为第一基准边及第二基准边,参考基准区域的位置数据包括第一基准边位于基准位时其上的一基准点的坐标数据,以及第二基准边位于基准位时其上的一基准点的坐标数据,加工治具的位置数据包括加工治具的每个检测边位于基准位时其上的一检测点的坐标数据。
123.控制器20分别将平行于第一基准边的两个检测边上的检测点的位置数据与第一基准边上的基准点的位置数据进行比较,判断二者是否相同,若相同,则表明加工治具的这两个检测边的位置无偏差,若不同,则表明加工治具的这两个检测边存在位置偏差,计算加工治具的这两个检测边的位置偏差值;同理,控制器20还进一步分别将平行于第二基准边的另外两个检测边上的检测点的位置数据与第二基准边上的基准点的位置数据进行比较,判断二者是否相同,若相同,则表明加工治具的另外这两个检测边的位置无偏差,若不同,则表明加工治具的另外这两个检测边存在位置偏差,计算加工治具的另外这两个检测边的位置偏差值。
124.具体地,通过步骤s316-步骤s318,参考基准区域在构建时会产生位置数据,检测机构10对加工治具的位置数据进行检测,根据参考基准区域的位置数据及加工治具的位置数据,将二者进行对比分析,确定治具的位置偏差值,即加工治具的四个检测边与参考基准区域的偏差。
125.s320,基于加工治具的位置偏差值得到加工治具的对称度检测结果,根据加工治具的对称度检测结果,生成第二控制指令。
126.s322,根据第二控制指令,控制对加工治具进行第二操作。
127.具体地,通过步骤s320-步骤s322,基于加工治具的位置偏差值检测加工治具的对称度,根据加工治具的对称度检测结果,生成第二控制指令,以控制对加工治具进行第二操作。如此,实现对加工治具的对称度进行检测及矫正的功能。
128.请参阅图7,在一些实施例中,第一操作包括执行直线度矫正操作。步骤s306具体包括如下步骤s3062-步骤s3066。
129.s3062,判断加工治具的角度偏差值是否为零。
130.s3064,如果加工治具的角度偏差值不为零,则表明加工治具存在直线度偏差,计算加工治具的角度补偿值。
131.s3066,基于加工治具的角度补偿值,生成第一控制指令,第一控制指令用于指示对加工治具执行直线度矫正操作直至加工治具的角度偏差值为零。
132.具体地,通过步骤s3062-步骤s3066,判断加工治具的角度偏差值不为零时,表示加工治具的直线度需要进行矫正;可以根据角度偏差值计算加工治具的角度补偿值,并基于加工治具的角度补偿值,生成第一控制指令,以对加工治具执行直线度矫正操作。检测方法执行步骤s3066后可执行步骤s308、步骤s314-步骤s322。
133.可以理解地,在其他的实施例中,步骤s306还可以包括步骤s3068。
134.s3068,判断加工治具的角度偏差值为零。
135.具体地,判断加工治具的角度偏差值为零时,则表示加工治具的直线度合格,无需对加工治具的直线度进行矫正,检测方法可继续执行步骤s314-步骤s322。
136.需要说明的是,图7中还包括步骤s304、步骤s308和步骤s314,步骤s304、步骤s308和步骤s314仅为方便说明步骤s306的一些实施例,步骤s306不包括步骤s304、步骤s308和步骤s314,步骤s314也可以理解为步骤s314-步骤s322。
137.请参阅图8,在一些实施例中,第二操作包括执行对称度矫正操作。步骤s320具体可以包括如下步骤s3202-步骤s3206。
138.s3202,判断加工治具的各个检测边的位置偏差值是否均为零。
139.s3204,如果至少一检测边的位置偏差值不为零,则表面加工治具存在对称度偏差,计算检测边的位置补偿值。
140.s3206,基于检测边的位置补偿值,生成第二控制指令,第二控制指令用于指示对加工治具上所夹紧的工件执行对称度矫正操作。
141.具体地,通过步骤s3202-步骤s3206,判断至少一检测边的位置偏差不为零,即加工治具的对称度需要进行矫正;根据不为零的检测边的位置偏差值,计算检测边的位置补偿值,并基于检测边的位置补偿值,生成第二控制指令,以对加工治具上所夹紧的工件执行对称度矫正操作。
142.可以理解地,在其他的实施例中,步骤s320还可以包括步骤s3208。
143.s3208,判断加工治具的各个检测边的位置偏差值均为零。
144.具体地,加工治具的各个检测边的位置偏差值均为零,表示加工治具的对称度无需进行矫正,加工装置200的加工机构在加工对应的加工治具所夹紧的工件时,无需对加工该治具所夹紧的工件进行第二操作。
145.需要说明的是,图8中还包括步骤s318和步骤s322,步骤s318和步骤s322仅为方便说明步骤s320的一些实施例,步骤s320不包括步骤s318和步骤s322。
146.图6至图8详细介绍了本技术的检测方法。本实施例的检测方法,通过获取检测机构10检测的加工治具的直线度数据,根据加工治具的直线度数据,确定加工治具的角度偏差值,基于加工治具的角度偏差值,生成第一控制指令,以控制加工治具执行直线度矫正操
作,实现对加工治具的直线度的自动检测及矫正;通过重新检测治具的直线度,确保加工治具的直线度符合要求,提升加工治具的直线度的检测及矫正精度。通过根据第一操作的执行直线度矫正操作的加工治具的直线度为零的结果,构建加工治具的参考基准区域,获取参考基准区域的位置数据及检测机构10检测的加工治具的位置数据,根据参考基准区域的位置数据及治具的位置数据,确定加工治具的位置偏差值,基于加工治具的位置偏差值检测加工治具的对称度,根据加工治具的对称度检测结果,生成第二控制指令,控制对加工治具进行对称度矫正操作,实现对加工治具的对称度的自动检测及矫正。加工治具的直线度及对称度依次被检测及矫正,实现了加工治具的直线度及对称度检测及矫正的自动化,无需作业人员手动检测及矫正,降低人力成本,提升检测及矫正效率,有利于提升加工效率。
147.对于本领域技术人员而言,显然本技术不限于上述示范性实施例的细节,而且在不背离本技术的精神或基本特征的情况下,能够以其他的具体形式实现本技术。因此,无论从哪一点来看,均应将实施例看作是示范性的,而且是非限制性的,本技术的范围由所附权利要求而不是上述说明限定,因此旨在将落在权利要求的等同要件的含义和范围内的所有变化涵括在本技术内。
148.最后应说明的是,以上实施例仅用以说明本技术的技术方案而非限制,尽管参照较佳实施例对本技术进行了详细说明,本领域的普通技术人员应当理解,可以对本技术的技术方案进行修改或等同替换,而不脱离本技术技术方案的精神和范围。