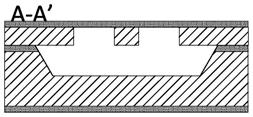
一种mems内腔局部减薄工艺方法及其应用
技术领域
1.本发明属于微电子机械系统(mems)传感器设计领域,涉及一种mems加工工艺,以及采用此工艺方法实现传感器制造的应用。
背景技术:2.mems(micro electro mechanical system)即微电子机械系统,是一种新兴的跨学科高新技术领域,融合了多种微加工技术,能够实现多种信息量的获取、处理与转化。在利用mems技术制造一些传感器器件时,会用到薄膜结构,是在硅晶圆的表面或背面用半导体加工工艺加工出空腔,再通过与衬底键合或填充材料等方式形成密封腔,形成薄膜与空腔的结构。其形成空腔的方法主要包括,一是使用干法或者湿法方式对硅片背面进行各向异性腐蚀,使得局部衬底形成数微米到几十微米厚度的应变膜结构,再将腐蚀过后的硅片与玻璃进行阳极键合形成密封腔;二是采用mems牺牲层技术在硅片表面形成真空的腔体,具体为先在衬底表面淀积牺牲层材料,再在牺牲层上淀积一层应力膜材料,再利用光刻在两侧制作出孔洞进行牺牲层的释放,最后将通孔密封形成密封腔;三是使用两块硅片,其中一块作为器件层,另一块作为衬底,将衬底热氧化形成一层二氧化硅,再在衬底上制作腐蚀制作出腔体,作为器件层的硅片则与带有腔体的衬底进行键合,再通过减薄器件层的厚度到所需的应变膜,形成类似soi硅片的结构和密封腔;四是采用单晶硅或多晶硅作为衬底,首先通过各向异性刻蚀在硅衬底上刻蚀浅槽,其次在对浅槽侧壁进行保护后进行各向同性腐蚀生成互通的空腔,然后采用外延单晶硅或多晶硅方式在衬底上形成了密封腔,最后通过机械抛光使得硅衬底的表面平整。
3.在密封腔与应变膜结构的基础上通过离子注入等方法在晶圆表面制作压敏电阻,通过对压敏电阻施加电压,将因外界压力等因素产生的薄膜形变引起的压敏电阻阻值变化,转化为输出电压的变化,基于这一结构和原理,可以制造多种类型的传感器。在制造此类拥有薄膜结构的高灵敏度传感器件时,除了减小应变膜厚度外,通常会将应变膜结构的局部减薄,设置为十字梁结构,来进一步提高器件的灵敏度,其原理是利用应力集中原理,使应力往十字梁区域集中。其优势在于,十字梁结构实现了应力集中提高了器件的灵敏度,同时增大了结构整体的刚度,改善了传感器的线性度和动态响应特性。
4.但上述一些结构也存在着缺点,利用各向异性腐蚀制作空腔和应变膜,由于其工艺条件较为苛刻,导致器件的一致性和重复性难以保证,难以精确控制应变膜厚度,同时形成的空腔的侧面与硅应变膜存在倾角使得空腔的底部所需要的尺寸远远大于硅应变膜的尺寸,不利于压力传感器的微型化设计;而利用mems牺牲层技术制作的空腔结构,其应变膜通常存在残余应力以及应力梯度,这导致了传感器的灵敏度不高和迟滞误差大等问题;同时,为了提高灵敏度,十字梁结构在制备时,需要在硅片的器件层表面进行腐蚀或刻蚀,导致表面会不平整,不易于后续传感器与电路的集成。
技术实现要素:5.本发明的目标在于针对上述问题,提出了一种mems内腔局部减薄工艺方法及其应用,通过在空腔的内部设置内腔局部减薄结构,该内腔局部减薄结构位于基底内部之中,使得该结构在具有传统十字梁结构的优点的同时,在应变膜结构制备完成后仍保持了衬底表面的平整性,易于传感器与电路集成的制造。
6.具体地,本发明的技术方案如下:
7.一种mems内腔局部减薄方法,包括以下步骤:
8.选择第一衬底,所述第一衬底包括相对的第一表面及第二表面;
9.刻蚀所述第一衬底的第一表面,形成第一凹槽;
10.选择第二衬底,所述第二衬底包括相对的第三表面及第四表面;
11.刻蚀所述第二衬底的第三表面,形成局部减薄结构;
12.键合所述第一衬底的第一表面与所述第二衬底的第三表面,形成包括局部减薄结构的内腔。
13.可选地,所述第二衬底包括单晶硅或者soi衬底。
14.可选地,还包括进一步减薄所述第二衬底的第四表面的步骤。
15.可选地,所述第二衬底的第三表面为soi的顶硅层。
16.可选地,刻蚀所述第二衬底的第三表面,截止于所述soi衬底的埋氧层,形成局部减薄结构。
17.可选地,所述局部减薄结构包括形成在所述第二衬底的第三表面的十字梁结构或者半岛梁膜结构。
18.一种mems压力传感器的制备方法,包括以下步骤:
19.选择第一衬底,所述第一衬底包括相对的第一表面及第二表面;
20.刻蚀所述第一衬底的第一表面,形成第一凹槽;
21.选择第二衬底,所述第二衬底包括相对的第三表面及第四表面;
22.刻蚀所述第二衬底的第三表面,形成局部减薄结构;
23.键合所述第一衬底的第一表面与所述第二衬底的第三表面,形成包括局部减薄结构的内腔;
24.减薄所述第二衬底的第四表面,形成应变膜;
25.在所述应变膜上制作压敏电阻和欧姆接触区。
26.可选地,所述第二衬底包括单晶硅或者soi衬底。
27.可选地,所述压敏电阻组成惠斯通电桥。
28.一种mems基底,包括:
29.叠置的第一衬底及第二衬底,以及封闭在所述第一衬底及第二衬底之间的内腔;
30.其中,所述第一衬底包括相对的第一表面及第二表面;
31.所述第一衬底的第一表面包括第一凹槽;
32.第二衬底包括相对的第三表面及第四表面;
33.所述第二衬底的第三表面包括局部减薄结构;
34.所述第一凹槽与所述局部减薄结对置构成所述内腔。
35.可选地,所述第二衬底包括单晶硅或者soi衬底。
36.可选地,所述局部减薄结构设置在所述soi衬底的顶硅层上。
37.可选地,所述局部减薄结构包括形成在所述第二衬底的第三表面的十字梁结构或者半岛梁膜结构。
38.可选地,所述内腔项面包括部分露出的soi埋氧层。
39.本发明还提出一种mems压力传感器,包括本发明所提出的mems基底。
40.可选地,还包括设置在所述第二衬底的第四表面的压敏电阻。
41.可选地,所述压敏电阻组成惠斯通电桥。
42.可选地,所述第四表面为soi衬底的底层硅的减薄层或者是去除soi埋氧层的顶硅层。
43.与现有技术相比,本发明所提出的技术方案至少具有以下有益效果:
44.(1)mems内腔局部减薄工艺的压阻式压力传感器具有灵敏度高、量程大的优点,相比于传统的平膜结构的压阻式压力传感器,通过设置局部减薄结构,利用了应力集中原理,使应力往局部减薄区域集中,提高了传感器的灵敏度;
45.(2)通过设置隆起的质量块,增大了结构的整体刚度,抑制了硅应变膜大的形变,改善了传感器的线性度和动态响应特性,同时提高了传感器的量程,从而实现了高灵敏度、高线性度、宽量程。
46.(3)相比于传统的正面十字梁结构的压阻式压力传感器,局部减薄的结构通过将空腔设置在第一衬底上,将空腔尺寸控制到与应变膜尺寸相等,解决了因各向异性腐蚀导致的空腔底面面积大于应变膜尺寸的问题,减小了芯片面积;
47.(4)通过将第二衬底有局部减薄结构的面与带有空腔的第一衬底键合,形成了具有内腔局部减薄结构的基底,可以通过对基底的非键合面的减薄来控制应变膜的厚度,使得应变膜厚度不受到soi片的顶层硅厚度限制,并且相比于传统的湿法腐蚀形成空腔,精确度更高、一致性更好;另外,键合过后的后续工艺中没有腐蚀工艺,基底表面保持平整,有利于电路与传感器的集成。
附图说明
48.一个或多个实施例通过与之对应的附图中的图片进行示例性说明,这些示例性说明并不构成对实施例的限定,附图中具有相同参考数字标号的元件表示为类似的元件,除非有特别申明,附图中的图不构成比例限制。
49.图1为本发明的mems内腔局部减薄工艺方法制作的压阻式压力传感器的俯视结构示意图;
50.图2-13为本发明的mems内腔局部减薄工艺方法沿图1中a-a’方向和b-b’方向的工艺流程剖面示意图;
51.图14-19为以本发明的mems基底制备压阻式压力传感器沿图1中b-b’方向的工艺流程剖面示意图。
具体实施方式
52.为使本发明实施例的目的、技术方案和优点更加清楚,下面将结合附图对本发明的各实施方式进行详细的阐述。然而,本领域的普通技术人员可以理解,在本发明各实施方
式中,为了使读者更好地理解本技术而提出了许多技术细节。但是,即使没有这些技术细节和基于以下各实施方式的种种变化和修改,也可以实现本技术所要求保护的技术方案。以下各个实施例的划分是为了描述方便,不应对本发明的具体实现方式构成任何限定,各个实施例在不矛盾的前提下可以相互结合相互引用。
53.图1是为本发明的mems内腔局部减薄工艺方法制作的压阻式压力传感器的俯视结构示意图。
54.其中,图2-10、13中的(a)为沿a-a’方向的剖面示意图、(b)对应于b-b’方向的剖面示意图;图14-19对应于b-b’方向的剖面示意图。
55.实施例1
56.本实施例提出一种mems内腔局部减薄方法,如图2-6所示,包括以下步骤:
57.选择第一衬底1,所述第一衬底1包括相对的第一表面101及第二表面102;
58.选择第二衬底2,所述第二衬底2包括相对的第三表面201及第四表面202,如图2所示;
59.其中,本实施例中的第一衬底例如可选择为硅片、玻璃或者陶瓷等材料,厚度例如为50-800μm;本实施例的第二衬底可选择为n型单晶硅片、p型单晶硅片或者soi(silicon on insulator)片等材料。
60.在本实施例中,第一衬底1以硅片为例,第二衬底2以n型(100)晶面的单晶硅片为例。
61.刻蚀所述第一衬底1的第一表面101,形成第一凹槽103;
62.具体地,为了刻蚀第一凹槽103,先对第一衬底1进行表面热氧化,在第一衬底1的正反两面各生长一层氧化硅3,如图3所示;
63.图形化第一衬底1的第一表面101,通过体硅刻蚀工艺刻蚀出第一凹槽103,如图4所示。
64.刻蚀所述第二衬底的第三表面,形成局部减薄结构;
65.具体地,对第二衬底2的第三表面201图形化并光刻,形成局部减薄结构203,如图4所示;
66.该局部减薄结构203可以是十字梁结构,也可以是硅岛结构。
67.将第一衬底1的第一表面101与第二衬底2的第三表面201进行键合,当然,第一衬底1的第一表面101上还包括氧化层3,形成包括局部减薄结构203的内腔4,如图5所示。
68.进一步地,还可以继续减薄第二衬底2的第四表面202,形成应变膜,从而完全形成一个具有内腔局部减薄结构的基底,用作后续传感器等器件应用,如图6所示。
69.实施例2
70.相对于实施例1,本实施例的第二衬底2采用soi衬底,其中第二衬底soi包括:体硅层204、埋氧层205和顶硅层206,如图7所示。
71.其中,体硅层204的厚度例如为50-800μm、埋氧层205的厚度为1-50μm、顶硅层206的厚度为1-50μm,
72.对第二衬底soi顶硅层进行光刻并图形化,刻蚀soi顶硅层206的局部区域,形成顶硅层局部减薄结构203,如图8所示。
73.刻蚀第一衬底1形成第一凹槽103,以及键合第一衬底1和第二衬底2形成带有内腔
4的基底的步骤与工艺与实施例1相同,此处不再赘述。
74.进一步地,还可以继续减薄第二衬底2的第四表面202,形成应变膜,在本实施例中,可以从soi衬底的体硅层204开始减薄、直至埋氧层205,从而完全形成一个具有内腔局部减薄结构的基底,用作后续传感器等器件应用,如图9-10所示。
75.实施例3
76.相对于实施例1,本实施例的第二衬底2采用soi衬底,其中第二衬底soi包括:体硅层204、埋氧层205和顶硅层206。
77.相对于实施例2,本实施例在制备顶硅层局部减薄结构203时,刻蚀顶硅层206至埋氧层205。
78.刻蚀第一衬底1形成第一凹槽103,以及键合第一衬底1和第二衬底2形成带有内腔4的基底的步骤与工艺与实施例1相同,此处不再赘述。
79.其中顶硅层局部减薄结构203在第一凹槽103的投影小于第一凹槽103区域,即局部减薄结构203位于第一凹槽103的区域内,如图11所示。
80.进一步地,还可以继续减薄第二衬底2的第四表面202,形成应变膜,在本实施例中,可以从soi衬底的体硅层204开始减薄、直至埋氧层205,从而完全形成一个具有内腔局部减薄结构的基底,用作后续传感器等器件应用,如图12所示。
81.实施例4
82.相对于实施例1,本实施例的第二衬底2采用soi衬底,其中第二衬底soi包括:体硅层204、埋氧层205和顶硅层206。
83.相对于实施例2,本实施例在制备顶硅层局部减薄结构203时,刻蚀顶硅层至埋氧层。
84.刻蚀第一衬底1形成第一凹槽103,以及键合第一衬底1和第二衬底2形成带有内腔4的基底的步骤与工艺与实施例1相同,此处不再赘述。
85.其中顶硅层局部减薄结构203在第一凹槽103的投影小于第一凹槽103区域,即局部减薄结构203位于第一凹槽103的区域内。此处与实施例3相同,不再赘述。
86.进一步地,还可以继续减薄第二衬底2的第四表面202,形成应变膜,在本实施例中,可以从soi衬底的体硅层204开始减薄、直至体硅层204的剩余厚度为0.1-50μm,从而完全形成一个具有内腔局部减薄结构的基底,用作后续传感器等器件应用,如图13所示。
87.实施例5
88.本实施提供一种mems压力传感器及其制备方法,该mems压力传感器以实施例1-4所提供的mems基底作为基底,包括以下步骤:
89.在实施例1-4所得到的基底上,在应变膜10的四周依次光刻并通过离子注入等方式,从而制作轻掺杂的压敏电阻5和重掺杂的欧姆接触区6,其中欧姆接触区6主要用于将压敏电阻5与后续的金属引线7相互连、以及压敏电阻5之间相互连,如图14所示;
90.采用apcvd、pecvd或者lpcvd等方法沉积厚度为0.01-1μm的氧化层及厚度为0.03-3μm的氮化层,从而形成绝缘介质层8,如图15所示;
91.光刻并刻蚀掉在欧姆接触区6上方的绝缘介质层8,从而形成引线孔12,如图16所示;
92.溅射金属如au、al、ti等一层或多层金属材料,厚度为0.1-4μm,并光刻,从而形成
金属引线7和金属焊盘15,如图17所示;
93.通过采用apcvd、pecvd或者lpcvd等方法沉积厚度为0.01-1μm的氧化层及厚度为0.03-3μm的氮化层,从而形成保护层11,如图18所示;
94.光刻并去除掉在金属焊盘15上方的保护层11,从而使得金属焊盘15暴露出来,作为测试用的金属焊盘15,如图19所示。
95.本实施例以实施例1得到的基底作为基底,制备mems压力传感器,其它实施例得到的基底制备mems压力传感器大致相同,不再重复描述。
96.有益效果:
97.(1)mems内腔局部减薄工艺的压阻式压力传感器具有灵敏度高、量程大的优点,相比于传统的平膜结构的压阻式压力传感器,通过设置局部减薄结构,利用了应力集中原理,使应力往局部减薄区域集中,提高了传感器的灵敏度;
98.(2)通过设置隆起的质量块,增大了结构的整体刚度,抑制了硅应变膜大的形变,改善了传感器的线性度和动态响应特性,同时提高了传感器的量程,从而实现了高灵敏度、高线性度、宽量程。
99.(3)相比于传统的正面十字梁结构的压阻式压力传感器,局部减薄的结构通过将空腔设置在第一衬底上,将空腔尺寸控制到与应变膜尺寸相等,解决了因各向异性腐蚀导致的空腔底面面积大于应变膜尺寸的问题,减小了芯片面积;
100.(4)通过将第二衬底有局部减薄结构的面与带有空腔的第一衬底键合,形成了具有内腔局部减薄结构的基底,可以通过对基底的非键合面的减薄来控制应变膜的厚度,使得应变膜厚度不受到soi片的顶层硅厚度限制,并且相比于传统的湿法腐蚀形成空腔,精确度更高、一致性更好;另外,键合过后的后续工艺中没有腐蚀工艺,基底表面保持平整,有利于电路与传感器的集成。
101.本领域的普通技术人员可以理解,上述各实施方式是实现本发明的具体实施例,而在实际应用中,可以在形式上和细节上对其作各种改变,而不偏离本发明的精神和范围。