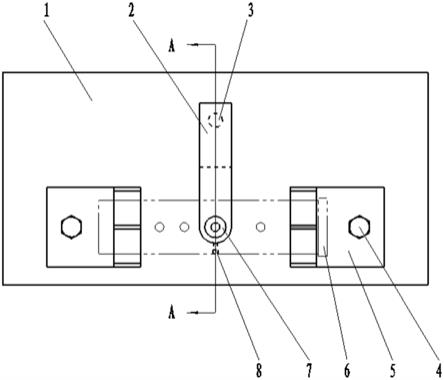
1.本实用新型属于机械加工领域,特别是一种套筒类机械零件的定位检测工装。涉及一种套筒零件定位检测工装,尤其适用于航空套筒零件的自动化检测的定位检测工装。
背景技术:2.套筒类机械零件的用途及为广泛,是机械加工制造及检测中常见的一种结构类型。套类零件主要结构面支承和导向及连接内表面外表面端面内孔尺寸,制造方式所能获得的套类零件在位置精度上相对较低。套类零件的形状精度主要是控制内孔的圆度及圆柱度精度精度。目前,由于套筒工件数量较多,直径相同或者不同的零部件批量大,并且需要检测的尺寸变化较多,尤其是航空套筒类工件,实现测量时套筒类工件孔与孔之间的安装位置要求高,为了保证套筒类工件的最终装配要求,需要对套筒类被测工件进行100%的三坐标检测。三坐标程序自动化检测零件尺寸时,在三个坐标轴的移动和转动方向上均有尺寸及相互位置的要求,需要每次将套筒类被测工件放置在同一指定位置,除可不限制沿两个贯通轴的位置自由度外,其余剩余自由度必须限制,即完全定位。由于套筒类零部件检测时,放置的位置和角度的不同,会直接影响到测量结果的准确性,必须在三坐标检测前,找正被测零件,并使被测零件每一次都放置在指定同一位置,否则无法执行三坐标测量程序自动化走位检测零件尺寸,需要人工干预调整套筒类零部件到同一指定位置才能执行测量程序的自动走位检测零件尺寸。由于套筒类零部件结构相近,直径和长度尺寸变化大,不能有效控制,所以普通简易工装调整非常困难。人力、物力的浪费极大,而且效率低下,不能满足后期的三坐标检测,以及给加工生产带来许多的不便,往往需要多次校正,才能将套筒类被测工件放置在同一指定位置实现三坐标测量程序自动化走位检测零件尺寸。
3.在自动化总装线中,定位、安装套筒等筒形工件时均使用套筒定位装置,该装置普遍采用激光检测装置或气压检测装置,生产成本较高,生产效率低。现有技术由于借助和被测孔相配的芯轴采用百分表找平,实现被测零件的装夹定位,被测零件每次放置的位置不固定。重复定位性不好,稳定性极差。由此可见,套筒类被测工件整个装夹定位过程中找平时间长,工作量大,效率低下,工人反馈意见大,同时受人为影响较大,重复定位性不好,稳定性极差,以及采用组合夹具装夹定位时,需要大量的工装组件,组装多套组合夹具,需要专业的组合夹具组装人员才能完成。组合夹具是指按零件的加工要求,由一套事先制造好的标准元件和部件组装而成的夹具。
4.定位可以提高工件定位表面与定位元件之间的位置精度,以减少或消除过定位引起的干涉。通常工件应该限制的自由度而未予限制的定位,称为欠定位。工件的同一自由度被二个或二个以上的支撑点重复限制的定位,称为过定位。套筒零件虽然结构简单,但尺寸大小不一,通用夹具难以满足要求。由于工件的夹紧与常用的夹紧装置夹紧时不能破坏工件在夹具中占有的正确位置,夹紧力既要保证工件在测量过程中不移动、不转动、不振动,又不因夹紧力过大而使工件表面损伤、变形;所以现有技术针对某些常加工的套筒,采用组合夹具的方式保证。组合夹具不能用于不同直径、长短、大小的套筒类被测工件的装夹定
位。需要大量的工装组件,组装多套组合夹具来满足不同的被测工件,同时需要专业的人员完成组合夹具的组装。由于定位不准确或采用了基准不重合定位等原因,定位过程中还会引入定位误差。
技术实现要素:5.本实用新型的目的是针对现有技术找平时间长,工作量大,效率低下的问题,提供一种结构简单,安装、拆卸方便、通用性强,定位准确可靠,装夹定位不受操作影响的筒体类零件通用定位检测工装,以解决航空套筒类工件三坐标测量定位工装需要人工干预调整套筒类被测工件到同一指定位置才能执行测量程序自动走位检测零件尺寸的问题。
6.本实用新型解决其技术问题所采用的技术方案是:一种套筒类零件定位检测工装,包括:固联在底板1上,沿长度方向与套筒外圆柱面轴心线一致分布的两个v型块5和垂直固联于所述两v型块5之间的联接板2,其特征在于:联接板2是一个直角梯形的悬臂支架,悬臂自由端上装配定位轴7,定位轴7通过悬臂端向的锁紧螺钉8垂直固定在所述悬臂的上端平面上;被测零件6通过被测零件6的孔沿着定位轴7的轴做轴向移动至定位轴7的下端,被测零件6的孔套入定位轴7的轴做孔轴配合,将被测零件6贴合在两v型块5定位槽中,限制被测零件6的回转运动,完成被测零件6的定位装夹。
7.本实用新型相比于现有技术具有如下有益效果:
8.通用性强。本实用新型采用固联在底板1上,沿长度方向与套筒外圆柱面轴心线一致分布的两个v型块5和垂直固联于所述两v型块5之间的联接板2,通用于各种直径、长短、套筒类工件的装夹定位,不需要再另行考虑工装量具,可以实现对工件的快速准确装夹,完成被测零件6的定位装夹。结构简单,占用空间较小,安装、操作拆卸方便省力,降低操作者的劳动强度,可同时实现筒形工件的定位、检测、安装,既节约了成本,又提高了生产线效率。提高工作效率
9.定位准确可靠。本实用新型采用一个直角梯形的悬臂支架构成的联接板2,并在悬臂自由端上装配有定位轴7,可迅速而准确的定位和夹紧,实现工件的快速装夹,减少辅助加工时间,降低加工成本。采用工装加工后,不但定位精确,而且由于各夹紧面都为面接触,夹紧可靠,而且有效地保护了工件已加工面。通过现场多批次零件实际加工检验,该工装完全能够满足工件的加工精度要求,合格率达到100%。解决了套筒类工件三坐标测量定位机构需要人工干预调整筒体类被测工件到同一指定位置才能执行测量程序自动走位检测零件尺寸的问题。
10.本实用新型采用分别通过联接螺钉4固联在底板1上的2个v型块5实现不同直径的套筒类零件的平面旋转运动的限制,通过锁紧螺钉8固定在联接板2上的定位轴7实现回转运动的限制,提高工件的固定速度,大幅度降低辅助加工时间,在很大程度上提高工件的刚性,不仅夹紧可靠,受力平衡,而且有效地保护了工件已加工面。
11.本实用新型采用定位轴7和2个v型块5能够保证被测零件每次装夹完成后都能放置在同一指定位置,等待执行三坐标测量程序自动化走位检测零件尺寸,免去之前每次都需要通过人工干预调整套筒类被测件6到同一指定位置才能执行三坐标测量程序自动化走位检测零件尺寸的过程。缩短了套筒类被测工件的装夹定位时间,提高检测效率。通过本工装的定位轴7和2个v型块5实现被测工件6的快速定位。克服了现有的套筒类工件测量时,套
筒类被测工件装夹定位过程找平时间长,工作量大,效率低下,同时受人为影响较大,重复性不好、稳定性极差,以及采用组合夹具装夹定位时,需要大量的工装组件,组装多套组合夹具,需要专业的组合夹具组装人员才能完成的缺陷。
附图说明
12.下面结合附图和实施例对本实用新型进一步说明。
13.图1是本实用新型套筒类零件定位检测工装的俯视图。
14.图2是图1的a
‑
a向剖视图。
15.图中:1.底板,2.联接板,3.联接销,4.联接螺钉,5.v型块,6.被测零件,7.定位轴,8.锁紧螺钉。
具体实施方式
16.参阅图1
‑
图2。在以下描述的优选实施例中,一种套筒类零件定位检测工装,包括:固联在底板1上,沿长度方向与套筒外圆柱面轴心线一致分布的两个v型块5和垂直固联于所述两v型块5之间的联接板2。联接板2是一个直角梯形的悬臂支架,悬臂自由端上装配定位轴7,定位轴7通过悬臂端向的锁紧螺钉8垂直固定在所述悬臂的上端平面上;被测零件6通过被测零件6的孔沿着定位轴7的轴做轴向移动至定位轴7的下端,被测零件6的孔套入定位轴7的轴做孔轴配合,将被测零件6贴合在两v型块5定位槽中,限制被测零件6的回转运动,完成被测零件6的定位装夹。
17.联接板2通过联接销3固定在底板1上,分布在长度方向的两v型块5通过联接螺钉4固定在底板1上。
18.用联接螺钉4将2个v型块分别固定在底板1长度方向的两端,联接销3将联接板2固定在垂直于2个v型块延线方向的底板1上,定位轴7由锁紧螺钉8固定在联接板2上。
19.以上仅为本实用新型的较佳实施例而已,并非用于限定本实用新型的保护范围。凡在本实用新型的精神和原则之内,所作的任何修改、等同替换、改进等,均应包含在本实用新型的保护范围之内。