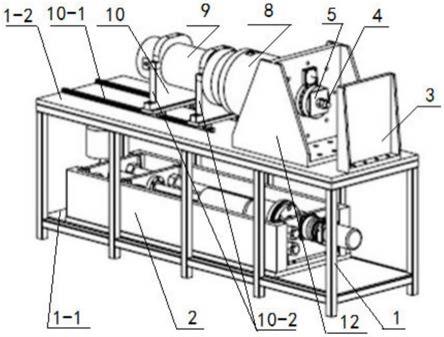
1.本实用新型属于支护系统实验平台技术领域,具体涉及一种锚杆围压拉拔试验设备。
背景技术:2.随着世界经济和工业的飞速发展,对能源的需求越来越大,矿山开采将不可避免地由现阶段的浅部转入深部。与此同时,核工业、国防工业、交通运输业、水利工程等领域,其规模和深度也都高速发展。岩体工程进入深部以后,呈现出高地应力、高水压、高地温条件,再加上工程的扰动,导致工程灾害日趋增多。在这些灾害中,最危险的是由于高地应力引起的灾害。
3.深地能源是我国能源安全的重要保障,多山地形决定了未来铁路公路交通、水利引调水工程等基础设施建设中大量深地工程的出现。然而频发的大强度岩爆灾害是制约深部工程建设和深地资源开采的国际性瓶颈难题。
4.岩体支护是防治岩爆或降低岩爆破坏烈度的最直接有效的手段,然而,支护机制不清、支护理论缺乏导致了当前岩爆支护存在严重盲目性、低效性和不确定性,灾害防护技术和支护设计理论严重滞后于深地工程活动的现状,给国际岩石力学与工程领域带来巨大挑战。因此,支护作用机制与设计理论是亟待解决的重大科学难题,迫切需要开展支护系统的试验,揭示相应的工作机理,测试各类支护单元和系统的承载能力,相关研究成果将为我国深部工程安全建设和深地资源高效安全开采提供关键理论及技术支撑,显著提升我国深部灾害的应对水平及相关领域的科研水平。
5.另外,目前大部分具岩爆风险工程的巷道支护设计仍依赖于经验,通过措施来不断修正支护参数或支护系统的设计,甚至通过不断增加支护强度期望达到防灾减灾的目的,然而常常事与愿违,效果欠佳,主要问题在于两点:
6.1)缺乏系统的支护设计理论予以指导;
7.2)更为重要的是缺乏有效的测试平台对支护设计方案进行性能测试。
8.因此,研发一套先进的深部工程支护系统实验平台,对于深入揭示岩爆冲击地压作用下支护系统的协同工作机制与力学响应、支护单元连接破坏机制,对于推进抗支护系统试验与测试平台建设都具有重大的科学意义和价值,对于提升学院和实验室服务国民经济主战场能力及我国在本领域的学术影响力也将起到积极推动作用。
技术实现要素:9.为了克服现有技术领域存在的上述技术问题,本实用新型提供一种锚杆围压拉拔试验设备, 包括主机框架、围压加载系统、锚杆拉拔保护块、锚杆、锚杆托盘、压力传感器、位移传感器、拉拔油缸、围压室、围压室移动机构,所述主机框架设有双层安装平台:设于主机框架下部的下平台和设于主机框架上部的上平台,所述围压加载系统安装在下平台上,所述上平台上依次固定围压室移动机构、液压缸支撑架和锚杆拉拔保护块,所述围压室安
装在围压室移动机构上并与拉拔油缸连接,围压室内设有试样,所述拉拔油缸安装在液压缸支撑架上,所述拉拔油缸端部设有压力传感器、位移传感器和锚杆托盘,所述锚杆依次穿过锚杆托盘、压力传感器、拉拔油缸后延伸至试样内。
10.所述围压加载系统包括料筒、泵桶、泵加载缸、安装框架和加载系统位移传感器,所述料筒和加载系统位移传感器分别设于安装框架的两端,所述泵桶和泵加载缸安装于安装框架的内部,料筒、泵桶、泵加载缸、加载系统位移传感器依次连接。
11.所述安装框架还设有中间支撑架,所述中间支撑架的两侧分别支撑安装泵桶和泵加载缸。
12.所述围压室移动机构包括滑轨和滑动支架,所述滑轨设有两条,并平行固定在上平台上,所述滑动支架设有两个,并前后设于滑轨上。
13.所述围压室包括围压室桶,所述围压室桶靠近拉拔油缸的一端设有受力垫板和密封法兰,另一端设有围压室进油口。
14.所述锚杆拉拔保护块包括保护块支架和保护块主体,所述保护块主体内设有柔性保护套。
15.本实用新型提供的锚杆围压拉拔试验设备,其有益效果在于,对于深入揭示岩爆冲击地压作用下支护系统的协同工作机制与力学响应、支护单元连接破坏机制,对于推进抗支护系统试验与测试平台建设都具有重大的科学意义和价值,满足多种试验需求,为满足不同类型锚杆试验安装,设计滑动安装同心结构,方便试样安装。
附图说明
16.图1是本实用新型一个实施例的立体结构示意图;
17.图2是本实用新型一个实施例的侧视图;
18.图3是图2的a—a视图;
19.图4是围压加载系统结构示意图。
20.图中标注:
21.1.主机框架;1
‑
1.下平台;1
‑
2.上平台;2.围压加载系统;2
‑
1.料筒;2
‑
2.泵桶; 2
‑
3. 泵加载缸;2
‑
4.安装框架;2
‑
5.加载系统位移传感器;2
‑
6.中间支撑架;3.锚杆拉拔保护块;4.锚杆;5.锚杆托盘;6.压力传感器;7.位移传感器;8.拉拔油缸;9.围压室; 9
‑
1.受力垫板;9
‑
2.密封法兰; 9
‑
3.围压室进油口;10.围压室移动机构;10
‑
1.滑轨;10
‑
2.滑动支架;11.试样;12.液压缸支撑架。
具体实施方式
22.下面参照附图,结合一个实施例,对本实用新型提供的锚杆围压拉拔试验设备进行详细的说明。
实施例
23.参照图1
‑
图4,本实施例的锚杆围压拉拔试验设备包括主机框架1、围压加载系统2、锚杆拉拔保护块3、锚杆4、锚杆托盘5、压力传感器6、位移传感器7、拉拔油缸8、围压室9、围压室移动机构10,所述主机框架1设有双层安装平台:设于主机框架下部的下平台1
‑
1和
设于主机框架上部的上平台1
‑
2,所述围压加载系统2安装在下平台1
‑
1上,所述上平台1
‑
2上依次固定围压室移动机构10、液压缸支撑架12和锚杆拉拔保护块3,所述围压室9安装在围压室移动机构10上并与拉拔油缸8连接,围压室9内设有试样11,所述拉拔油缸8安装在液压缸支撑架12上,所述拉拔油缸8端部设有压力传感器6、位移传感器7和锚杆托盘5,所述锚杆4依次穿过锚杆托盘5、压力传感器6、拉拔油缸8后延伸至试样11内。
24.压力传感器6采用psd
‑
sjth
‑
80t高精度动态传感器。
25.位移传感器7选用于磁悬浮位移传感器,量程200.0mm,分辨率0.2um非线性度0.01%,传感器无限分辨率,重复精度0.005%,工作温度
‑
40
‑
75℃,位移传感器安装于液压缸内部,主要用于液压缸的位移闭环控制和位移监测,在加载时可以用于试样的变形测量。
26.拉拔油缸8为空心加载液压缸,法向设计最大荷载700.0kn,加载液压缸作动器最大行程200.0mm,液压缸重量约为500kg。测量控制精度达到最大力值的
±
0.5%sf,实现同步加载和异步加载控制,实现应力应变控制平滑转换,系统可长时间加载及长时间稳压。
27.拉拔油缸8为不锈钢材质,可防一般性酸碱盐腐蚀;预留多个传感器接口,方便后期扩展。
28.所述围压加载系统2包括料筒2
‑
1、泵桶2
‑
2、泵加载缸2
‑
3、安装框架2
‑
4和加载系统位移传感器2
‑
5,所述料筒2
‑
1和加载系统位移传感器2
‑
5分别设于安装框架2
‑
4的两端,所述泵桶2
‑
2和泵加载缸2
‑
3安装于安装框架2
‑
4的内部,料筒2
‑
1、泵桶2
‑
2、泵加载缸2
‑
3、加载系统位移传感器2
‑
5依次连接。
29.围压加载系统2,提供高精度围压;实时采集压力,对伺服泵实时闭环控制;可按设定进行定恒定压力控制、阶梯压力控制。全自动充油、吸油以及过滤。工作压力:0
‑
50mpa;控制方式:阶梯压力控制、恒压控制;压力控制精度:<0.01mpa;流量范围: 0.1
‑
200ml/min;增压泵缸容积:500ml;过压溢流阀保护。
30.围压加载系统2,采用独立伺服中央数字系统控制,即可实现同步加载也可实现异步加载。
31.本设备在启用时,应用到伺服控制及数据采集系统,qkx
‑
act6伺服控制数据采集控制系统,主要用于真三轴的动静动作控制,剪切设备的动静执行元件控制,水压系统压力精确控制,温控系统的加温及闭环检测控制,系统实现控制所采用的软件基于c++开发,运行于windowsxp或win7操作系统,是现有的编程开发技术。
32.所述安装框架2
‑
4还设有中间支撑架2
‑
6,所述中间支撑架2
‑
6的两侧分别支撑安装泵桶2
‑
2和泵加载缸2
‑
3。
33.所述围压室移动机构10包括滑轨10
‑
1和滑动支架10
‑
2,所述滑轨10
‑
1设有两条,并平行固定在上平台1
‑
2上,所述滑动支架10
‑
2设有两个,并前后设于滑轨10
‑
1上。
34.所述围压室9包括围压室桶,所述围压室桶靠近拉拔油缸8的一端设有受力垫板9
‑
1和密封法兰9
‑
2,另一端设有围压室进油口9
‑
3。
35.围压室9围压大小可调,调整范围是0
‑
50mpa。
36.围压室9设计最大加载力50mpa,最大耐压不低于100mpa,试验仓内部尺寸为:直径
ø
200mm
×
长度l600mm,围压加载可实现加载及卸载试验,实现应力控制平滑过度,系统可长时间加载及长时间稳压等。围压室设计安装在围压室移动机构内,于围压室移动机构连接形成反力结构,围压室方便拆装。围压室内部安装压力传感器,可以直接测量和控制压力。
37.所述锚杆拉拔保护块3包括保护块支架和保护块主体,所述保护块主体内设有柔性保护套。
38.试样放置说明:通过升降车,将试样安装在围压室内;试样安装完成后,将围压室密封;再通过升降车,将围压室安装在围压室移动机构,并进行固定,完成锚杆的锁紧,通过控制程序,给围压室加围压,当满足试验压力时,准备开始实验,通过压力传感器,位移传感器检测拉拔试验过程中的时间
‑
位移曲线,时间
‑
载荷曲线,位移
‑
载荷曲线。