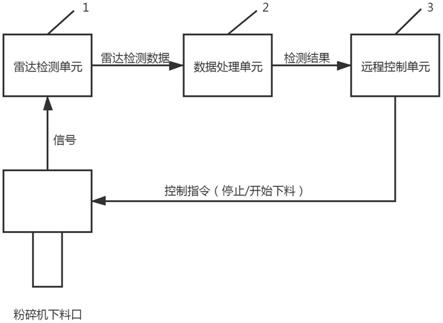
1.本技术涉及激光雷达技术领域,特别涉及一种基于三维激光雷达的用于粉碎机下料的检测系统。
背景技术:2.在粉碎机工作过程中,需要对大块矿石进行粉碎后,通过下料口将碎料排出,但粉碎机的下料口极易被大块矿石或粉碎不及时的原料堵塞,导致粉碎工作中断,当粉碎机的下料口堵塞时,需要经过人工疏通处理后才能继续放料,防止粉碎机卡死。但现有粉碎站下料的检测过程均通过人工进行检测,不仅工作效率低下,自动化水平低,而且现场工作环境恶劣,粉尘、噪声污染严重,对操作人员的生命健康造成严重威胁。
技术实现要素:3.本技术提供了一种基于三维激光雷达的用于粉碎机下料的检测系统,以解决在现有粉碎机下料口需要通过人工进行检测,工作量大,严重影响工作效率的问题。
4.本技术提供了一种基于三维激光雷达的用于粉碎机下料的检测系统,雷达检测单元、数据处理单元和远程控制单元;
5.所述雷达检测单元的输出端与所述数据处理单元的输入端连接,所述雷达检测单元用于获取粉碎机下料口的雷达检测数据,并将所述雷达检测数据发送给数据处理单元;
6.所述数据处理单元的输出端与所述远程控制单元的输入端连接;所述数据处理单元用于根据所述雷达检测数据进行建模,得到粉碎机下料口模型,通过对下料前后的粉碎机下料口模型进行实时比对,得到检测结果,并将所述检测结果发送给所述远程控制单元;
7.所述远程控制单元的输出端与粉碎机连接;所述远程控制单元用于接收来自所述数据处理单元的检测结果,根据所述检测结果控制所述粉碎机进行下料操作。
8.所述雷达检测单元为三维激光雷达。
9.所述数据处理单元包括:数据建模模块、模型比对模块以及远程通信模块;
10.所述数据建模模块的输入端与所述雷达检测单元的输出端连接,所述数据建模模块的输出端与所述模型比对模块的输入端连接,所述数据建模模块用于根据所述雷达检测数据进行建模,得到粉碎机下料口模型;
11.所述模型比对模块的输出端与所述远程通信模块的输入端连接,所述模型比对模块用于通过对下料前后的粉碎机下料口模型进行实时比对,得到检测结果;
12.所述远程通信模块的输出端与所述远程控制单元的输入端连接,所述远程通信模块用于将所述检测结果发送给所述远程控制单元。
13.所述远程通信模块通过以太网或串口将所述检测结果发送至远程控制单元。
14.所述数据处理单元还包括模型存储模块,所述模型存储模块的输入端与所述数据建模模块的输出端连接,所述模型存储模块用于存储所述粉碎机下料口模型。
15.所述数据处理单元还被配置为获取存储在所述模型存储模块中的所述粉碎机下
料口模型,通过对下料前后的粉碎机下料口模型进行比对,得到下料前检测结果,并将所述下料前检测结果发送给所述远程控制单元。
16.所述系统还包括报警指示单元,所述报警指示单元的输入端与所述数据处理单元(2)的输出端连接,所述报警指示单元用于接收来自所述数据处理单元的检测结果,若下料异常,发送报警信息。
17.所述报警指示单元的报警方式可以为声报警或光报警。
18.由以上技术方案可知,本技术公开了一种基于三维激光雷达的用于粉碎机下料的检测系统,包括:雷达检测单元、数据处理单元和远程控制单元,所述雷达检测单元用于获取粉碎机下料口的雷达检测数据,并将所述雷达检测数据发送给数据处理单元,所述数据处理单元用于根据所述雷达检测数据进行建模,得到粉碎机下料口模型,通过对下料前后的粉碎机下料口模型进行实时比对,得到检测结果,并将所述检测结果发送给所述远程控制单元,所述远程控制单元用于接收来自所述数据处理单元的检测结果,根据所述检测结果控制所述粉碎机进行下料操作。本技术通过对粉碎机下料口进行实时建模对比,实现了粉碎机下料过程的自动化检测,提升了工作效率。
附图说明
19.为了更清楚地说明本技术的技术方案,下面将对实施例中所需要使用的附图作简单地介绍,显而易见地,对于本领域普通技术人员而言,在不付出创造性劳动性的前提下,还可以根据这些附图获得其他的附图。
20.图1为本技术提供的一种基于三维激光雷达的用于粉碎机下料的检测系统的应用场景图;
21.图2为本技术提供的所述数据处理单元的结构示意图;
22.图3为本技术提供的一种基于三维激光雷达的用于粉碎机下料的检测系统的一种实施例的连接示意图;
23.图4为本技术提供的一种基于三维激光雷达的用于粉碎机下料的检测系统在另一种实施例下的流程图;
24.图5为本技术提供的一种基于三维激光雷达的用于粉碎机下料的检测系统的工作流程图。
具体实施方式
25.参见图1,本技术提供了一种基于三维激光雷达的用于粉碎机下料的检测系统,其特征在于,包括:
26.雷达检测单元1、数据处理单元2和远程控制单元3;
27.所述雷达检测单元1的输出端与所述数据处理单元2的输入端连接,所述雷达检测单元用于获取粉碎机下料口的雷达检测数据,并将所述雷达检测数据发送给数据处理单元;在本技术一实施例中,所述雷达检测单元1设置在破碎机下料口正上方,可以实时对破碎机下料口进行三维扫描。
28.所述数据处理单元2的输出端与所述远程控制单元3的输入端连接;所述数据处理单元2用于根据所述雷达检测数据进行建模,得到粉碎机下料口模型,通过对下料前后的粉
碎机下料口模型进行实时比对,得到检测结果,并将所述检测结果发送给所述远程控制单元3;
29.所述数据处理单元2接收三维激光雷达的扫描数据,并分析数据得到测量结果,然后发送给后端的远程控制单元3。所述数据处理单元2通过对所述雷达检测数据整合、测量、匹配、比对,从而计算得出当前破碎下料口的物料状态,并将破碎下料口的物料信息上送至远程控制单元3。所述数据处理单元2完成雷达数据的滤波、边缘点清除、强弱信号处理等前置分析;然后计算破碎下料口的信息,通过雷达每帧的数据分析破碎下料口的边缘,计算破碎下料口的物料高度和物料体积。
30.所述远程控制单元3的输出端与粉碎机连接;所述远程控制单元用于接收来自所述数据处理单元2的检测结果,根据所述检测结果控制所述粉碎机进行下料操作。
31.所述基于三维激光雷达的用于粉碎机下料的检测系统的工作过程为:在矿卡卸料前,所述雷达检测单元1扫描破碎机下料口得到雷达检测数据,通过数据处理单元2进行三维建模,给远程控制单元3发送信号,所述远程控制单元3通知矿卡开始放料;矿卡卸料后,所述雷达检测单元1实时对破碎机下料口进行扫描,并通过数据处理单元2进行三维建模,实时将下料后破碎机下料口建模与下料前建模进行比对;卸料前后下料口建模比对出现异常时,及时向远程控制单元3发出信号,所述远程控制单元3暂停矿卡放料;当建模比对达到再次卸料的要求后,向所述远程控制单元3发出信号,进行下一次卸料操作。
32.在本技术一实施例中,所述雷达检测单元1为三维激光雷达。更为具体的是,基于三维激光雷达的精确测量减小了人员估计的误差,提高了测量精度;减少了人员疲劳或注意力不集中导致的漏看问题。
33.在本技术一实施例中,参见图2,所述数据处理单元2包括:数据建模模块21、模型比对模块22以及远程通信模块23;
34.所述数据建模模块21的输入端与所述雷达检测单元1的输出端连接,所述数据建模模块21的输出端与所述模型比对模块22的输入端连接,所述数据建模模块21用于根据所述雷达检测数据进行建模,得到粉碎机下料口模型;
35.所述模型比对模块22的输出端与所述远程通信模块23的输入端连接,所述模型比对模块22用于通过对下料前后的粉碎机下料口模型进行实时比对,得到检测结果;
36.所述远程通信模块23的输出端与所述远程控制单元3的输入端连接,所述远程通信模块23用于将所述检测结果发送给所述远程控制单元3。
37.在本技术一实施例中,所述远程通信模块23通过以太网或串口将所述检测结果发送至远程控制单元3。
38.在本技术一实施例中,参见图3,所述数据处理单元2还包括模型存储模块24,所述模型存储模块的输入端与所述数据建模模块21的输出端连接,所述模型存储模块24用于存储所述粉碎机下料口模型。通过将历史粉碎机下料口模型进行存储,便于快速查找历史模型信息,对历史下料口模型进行分析,提升系统稳定性。
39.在本技术一实施例中,数据处理单元2还被配置为获取存储在所述模型存储模块24中的所述粉碎机下料口模型,通过对下料前后的粉碎机下料口模型进行比对,得到下料前检测结果,并将所述下料前检测结果发送给所述远程控制单元3。通过对下料前的粉碎机下料口模型与历史粉碎机下料口模型进行比对,能够有效监测下料前的所述粉碎机下料口
是否堵塞,通过对下料前的粉碎机下料口进行有效检测,提升工作效率。避免出现粉碎机下料口堵塞的前提下进行下料,造成生产事故。
40.在本技术一实施例中,参见图4,所述系统还包括报警指示单元4,所述报警指示单元4的输入端与所述数据处理单元2的输出端连接,所述报警指示单元4用于接收来自所述数据处理单元2的检测结果,若下料异常,发送报警信息。通过报警信息能够使得操作工人快速知晓当前系统情况,便于操作工人快速排除故障,避免影响粉碎机正常工作,提升工作效率。
41.在本技术一实施例中,所述报警指示单元4的报警方式可以为声报警或光报警。多种报警方式能够满足不同使用环境下的使用需求,使得所述系统的适用性更强。避免由于环境因素导致报警信息没有快速告知操作人员。
42.参见图5,本技术提供的一种基于三维激光雷达的用于粉碎机下料的检测系统的工作过程包括以下步骤:
43.s100:获取下料前的粉碎机下料口的雷达检测数据;
44.更为具体的是,
45.s200:根据所述雷达检测数据进行建模,得到下料前粉碎机下料口模型;
46.s300:获取下料后的粉碎机下料口的雷达检测数据;
47.s400:根据所述雷达检测数据进行建模,得到下料后粉碎机下料口模型;
48.s500:对下料前后的粉碎机下料口模型进行比对计算,判断是否超过预设阈值;
49.若未超过阈值,再次获取下料后的粉碎机下料口的雷达检测数据,重复上述步骤;
50.s600:若超过阈值,控制所述粉碎机停止下料操作。
51.在矿卡卸料前,扫描整个的粉碎口,建立点云坐标模型,此点云坐标模型中的点以雷达位原点。把扫描区域按一定的大小网格化,每个网格内至少有一个雷达点(可根据不同应用情况设置网格大小),每个网格标注不同的id号,在每个网格内取所有点的平均高度,作为网格的高度值。建立下料前后的粉碎机下料口模型,通过对下料前后的粉碎机下料口模型中的相同id号的数据进行比对,根据区域的网格数,分为两种情况:
52.其一为如果有一半的网格的高度值超过阈值,有堵塞的情况产生,需要等待小于阈值后再进行放料;其二为如果有一个网格出现高度超过单独网格的阈值,就是有大块的物料堵塞,也需要进行等待小于阈值后再进行放料。
53.由以上技术方案可知,本技术公开了一种基于三维激光雷达的用于粉碎机下料的检测系统,包括:雷达检测单元、数据处理单元和远程控制单元,所述雷达检测单元用于获取粉碎机下料口的雷达检测数据,并将所述雷达检测数据发送给数据处理单元,所述数据处理单元用于根据所述雷达检测数据进行建模,得到粉碎机下料口模型,通过对下料前后的粉碎机下料口模型进行实时比对,得到检测结果,并将所述检测结果发送给所述远程控制单元,所述远程控制单元用于接收来自所述数据处理单元的检测结果,根据所述检测结果控制所述粉碎机进行下料操作。本技术通过对粉碎机下料口进行实时建模对比,实现了粉碎机下料过程的自动化检测,提升了工作效率。
54.另一方面,本技术的有益效果为:所述系统通过检测自动化减少人员控制环节,减少了成本投入。系统各个季节24小时不间断工作,并能在风、雨、雪、雾、粉尘等天气条件工作,尤其系统在夜间的工作可靠性保持了一个极高的水平,实现完备的测量体系。