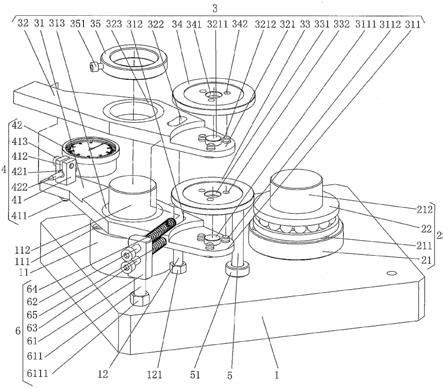
1.本实用新型属于纺织机械零件检测装置技术领域,具体涉及一种凸轮外缘曲线参数检测装置。
背景技术:2.前述的凸轮主要指用于织机开口运动的共轭凸轮,前述的凸轮外缘是凸轮边缘的轮廓面(以下同)。如业界所知,前述织机主要有五大运动,即开口运动、引纬运动、打纬运动、卷取运动和送经运动。前述开口是在织机上按照织物组织要求将经纱上下分开而形成梭口,完成开口运动的装置即为开口装置。开口装置的特点是利用双凸轮积极控制综框的升降运动,具体而言,由一组装配于中心轴(也称“凸轮轴”或“主轴”)上的共轭凸轮和提综臂滚轮(与共轭凸轮的凸轮外廓相配合)的相对运动并通过连杆来带动综框作上下运动而得以形成梭口,因此前述共轭凸轮是凸轮开口装置中的十分重要的部件,也就是说,凸轮开口是织机的一种重要开口方式。
3.由于前述凸轮(即“共轭凸轮”,以下同)的加工精度的优劣会直接影响凸轮开口装置运行的正确性、平稳性,甚至会影响到凸轮开口装置整体的使用寿命,因而提高凸轮加工过程中的精度对于保障凸轮装置运行的诸如前述正确平稳效果具有十分重要的积极意义。前述的提高凸轮精度实质上是提高凸轮外缘曲线参数的精度,而要提高或者称保障凸轮外缘曲线参数的精度,则需要在凸轮制造过程中,对其轮廓(也称“轮缘”)参数即凸轮外缘曲线参数进行检测。
4.鉴于目前存在对凸轮的轮廓度检测精度低、检测效率低、检测者的检测作业强度大等问题,因而设置结构简单、操作方便、检测效率高并且检测精度理想的凸轮曲线参数检测装置具有积极意义。
5.在公开的中国专利文献中虽然可见诸与凸轮检测相关的技术信息,如cn106767328b推荐的“一种精磨凸轮型线检测装置”和cn104742016b介绍的“一种平面共轭凸轮轮廓检测和磨削加工装置的控制方法”,等等,但是并非限于例举的前述专利技术均不足以全面地体现申请人在前面提及的得以达到业界期望的诸效果的程度,下面将要介绍的技术方案便是在这种背景下产生的。
技术实现要素:6.本实用新型的任务在于提供一种有助于体现结构的简练性、检测时操作的便捷与高效性、检测精度高并且具有对检测数据的良好的可视性、检测者检测操作强度低的凸轮外缘曲线参数检测装置。
7.本实用新型的任务是这样来完成的,一种凸轮外缘曲线参数检测装置,包括一长方体并且长度为宽度的1.5至2.5倍的检测平台,在该检测平台的左端朝向上的一侧并且位于检测平台的宽度方向的居中位置固定有一形状呈圆柱体的检测板枢转支承座,在检测平台朝向上的一侧并且在对应于检测板枢转支承座的右前方的位置以纵向状态设置有一检
测板限位杆;一凸轮检测枢转支承机构,该凸轮检测枢转支承机构设置在检测平台的右端朝向上的一侧并且位于检测平台的宽度方向的居中位置;一凸轮轮廓面贴靠支承机构,该凸轮轮廓面贴靠支承机构转动地设置在所述检测板枢转支承座上,并且该凸轮轮廓面贴靠支承机构的前端在对应于所述凸轮检测枢转支承机构的左侧的状态下空套在所述检测板限位杆上;一凸轮轮廓面偏差值显示机构,该凸轮轮廓面偏差值显示机构设置在凸轮轮廓面贴靠支承机构的后端;一测前校正芯杆,该测前校正芯杆在对应于所述凸轮检测枢转支承机构的左侧与所述凸轮轮廓面贴靠支承机构的前端右侧之间的位置插拔配合在所述检测平台上;一检测板推力机构,该检测板推力机构在对应于所述凸轮轮廓面贴靠支承机构的前端左侧的位置设置在所述检测平台朝向上的一侧并且在对凸轮检测状态下与凸轮轮廓面贴靠支承机构的前端左侧面接触。
8.在本实用新型的一个具体的实施例中,所述检测板枢转支承座通过间隔分布的检测板枢转支承座固定螺钉固定在所述检测平台的左端朝向上的一侧,并且在检测板枢转支承座的上端向上延伸有一直径小于检测板枢转支承座的直径的检测板轴承配合轴头;所述检测板限位杆的下端与检测板限位杆座固定,而该检测板限位杆座在对应于所述检测板枢转支承座的右前方的位置与检测平台朝向上的一侧固定;所述凸轮轮廓面贴靠支承机构与所述检测板轴承配合轴头转动配合;所述凸轮轮廓面偏差值显示机构随所述凸轮轮廓面贴靠支承机构绕所述检测板轴承配合轴头的转动而转动;所述测前校正芯杆的下端在对应于凸轮检测枢转支承机构的左侧的位置与测前校正芯杆固定座插拔配合,而该测前校正芯杆固定座与所述检测平台朝向上的一侧固定;所述凸轮轮廓面贴靠支承机构在所述检测板推力机构对其前端左侧面施加推力的状态下与检测过程中临时转动地套置在凸轮检测枢转支承机构上的凸轮轮廓面贴靠。
9.在本实用新型的另一个具体的实施例中,所述凸轮检测枢转支承机构包括一凸轮支承轴承座和一凸轮支承轴承,凸轮支承轴承座设置在所述检测平台的右端朝向上的一侧并且通过凸轮支承轴承座固定螺钉与所述检测平台固定,在该凸轮支承轴承座朝向上的一侧的中心位置向上延伸有一直径小于凸轮支承轴承座的直径的凸轮临时套置轴,凸轮支承轴承套置在凸轮临时套置轴上并且该凸轮支承轴承的底部的四周支承在凸轮支承轴承座朝向上的一侧的四周边缘部位;在检测凸轮曲线的过程中,凸轮临时转动地套置在凸轮临时套置轴上并且凸轮的底部支承于凸轮支承轴承上;所述的凸轮支承轴承为压力轴承。
10.在本实用新型的又一个具体的实施例中,所述凸轮轮廓面贴靠支承机构包括下检测板、上检测板、下检测盘、上检测盘和挡套,下检测板的长度方向的中部转动地套置在所述检测板轴承配合轴头上,在下检测板的前端朝向上的一侧构成有一下检测盘腔,在下检测板上并且在对应于下检测盘腔的后方的位置开设有一下检测板限位杆让位孔,上检测板位于下检测板的上方,该上检测板的长度方向的中部同样转动地套置在所述检测板轴承配合轴头上,在上检测板的前端朝向上的一侧构成有一上检测盘腔,在上检测板上并且在对应于上检测盘腔的后方的位置开设有一上检测板限位杆让位孔,该上检测板限位杆让位孔与所述下检测板限位杆让位孔相对应,下检测盘设置在所述下检测盘腔内并且与下检测板的前端固定,上检测盘设置在所述上检测盘腔内并且与上检测板的前端固定,挡套在对应于上检测板的上方的位置固定在所述检测板轴承配合轴头上,并且由配设在挡套上的锁止螺钉锁定;在对临时转动地套置在所述凸轮临时套置轴上的凸轮检测凸轮曲线的过程中,
所述下检测盘以及上检测盘与凸轮轮廓面贴触;所述凸轮轮廓面偏差值显示机构设置在所述下检测板的后端并且与上检测板的后端的右侧面贴触;设置在所述检测平台朝向上的一侧的所述检测板推力机构与所述下检测板以及上检测板的前端左侧面接触;所述检测板限位杆的上端由下而上依次穿过所述下检测板限位杆让位孔以及上检测板限位杆让位孔。
11.在本实用新型的再一个具体的实施例中,在所述下检测板的长度中部设置有一下检测板轴承,而在所述上检测板的长度方向的中部设置有一上检测板轴承,下检测板轴承以及上检测板轴承的不转动的内圈套固在所述检测板轴承配合轴头上;所述下检测板限位杆让位孔以及上检测板限位杆让位孔为椭圆形孔。
12.在本实用新型的还有一个具体的实施例中,在所述下检测盘腔朝向上的一侧并且位于中央位置构成有一下检测盘配合轴头并且在围绕该下检测盘配合轴头的四周间隔配设有一组下检测盘固定螺钉,在下检测盘的中心位置开设有一下检测盘配合轴头孔,并且在该下检测盘配合轴头孔的四周间隔开设有一组下检测盘固定螺钉孔,所述下检测盘配合轴头探入所述下检测盘配合轴头孔内,所述的一组下检测盘固定螺钉旋入所述下检测盘固定螺钉孔内;在所述上检测盘腔朝向上的一侧并且位于中央位置构成有一上检测盘配合轴头并且在围绕上检测盘配合轴头的四周间隔配设有一组上检测盘固定螺钉,在上检测盘的中心位置开设有一上检测盘配合轴头孔并且在围绕该上检测盘配合轴头孔的四周间隔开设有一组上检测盘固定螺钉孔,所述上检测盘配合轴头探入所述上检测盘配合轴头孔内,所述的一组上检测盘固定螺钉旋入所述上检测盘固定螺钉孔内。
13.在本实用新型的更而一个具体的实施例中,所述凸轮轮廓面偏差值显示机构包括一百分表固定座和一百分表,百分表固定座通过百分表固定座螺钉固定在所述下检测板的后端朝向上的一侧,并且该百分表固定座具有一百分表顶针套固定槽,百分表通过百分表顶针套在对应于百分表顶针套固定槽的位置以水平悬臂状态与百分表固定座固定并且由配设在百分表固定座上的顶针套固定槽夹紧螺钉夹紧,百分表的百分表顶针伸展到百分表顶针套外并且与所述上检测板的后端的右侧面贴触。
14.在本实用新型的进而一个具体的实施例中,所述检测板推力机构包括推力弹簧螺杆座、上推力弹簧螺杆、下推力弹簧螺杆、上推力弹簧和下推力弹簧,在推力弹簧螺杆座的下端构成有一推力弹簧螺杆座固定柱,该推力弹簧螺杆座固定柱的底部固定在所述检测平台朝向上的一侧,上推力弹簧螺杆以及下推力弹簧螺杆彼此上下横向平行,并且左端与推力弹簧螺杆座固定,而右端以水平悬臂状态分别对应于所述上检测板以及下检测板的前端左侧,上推力弹簧套置在上推力弹簧螺杆的右端并且该上推力弹簧的右端与上检测板的前端左侧面接触,下推力弹簧套置在下推力弹簧螺杆的右端并且该下推力弹簧的右端与下检测板的前端左侧面接触。
15.在本实用新型的又更而一个具体的实施例中,在所述检测平台上并且在对应于所述推力弹簧螺杆座固定柱的位置固定有一固定柱座,推力弹簧螺杆座固定柱的下端与该固定柱座固定。
16.在本实用新型的又进而一个具体的实施例中,所述的固定柱座为一外六角螺母并且与所述检测平台朝向上的一侧焊接固定,所述推力弹簧螺杆座固定柱的下端以螺纹固定方式与固定柱座固定。
17.本实用新型提供的技术方案的技术效果在于:由于整体结构相对简练,因而可由
凸轮生产厂商依需自行制作并且制作方便以及十分廉价;由于当要对凸轮的凸轮曲线进行检测时,只要将凸轮临时安放于凸轮检测枢转支承机构上,并且由检测板推力机构迫使凸轮轮廓面贴靠支承机构的前端与凸轮轮廓面贴靠,通过人为转动凸轮,凸轮轮廓面精度误差便可通过凸轮轮廓面贴靠支承机构的后端致动凸轮轮廓面偏差值显示机构,致动程度由凸轮轮廓面偏差值显示机构显示,因而不仅检测时的操作方便省力,而且检测效率高;由于凸轮轮廓面偏差值显示机构具有良好的检测数据的可视性,因而能保障理想的检测精度。
附图说明
18.图1为本实用新型的实施例结构图。
19.图2为本实用新型对凸轮进行检测状态的示意图。
具体实施方式
20.为了能够更加清楚地理解本实用新型的技术实质和有益效果,申请人在下面以实施例的方式作详细说明,但是对实施例的描述均不是对本实用新型方案的限制,任何依据本实用新型构思所作出的仅仅为形式上的而非实质性的等效变换都应视为本实用新型的技术方案范畴。
21.在下面的描述中凡是涉及上、下、左、右、前和后的方向性或称方位性的概念都是以图1所处的位置状态为例的,因而不能将其理解为对本实用新型提供的技术方案的特别限定。
22.实施例:
23.请参见图1,示出了几何形状呈长方体并且长度优选为宽度的1.5至2.5倍,较好地为1.8至2.2倍,最好为2倍(本实施例选择长度为宽度的2倍)的一检测平台1,在该检测平台1的左端朝向上的一侧并且位于检测平台1的宽度方向的居中位置固定有一形状呈圆柱体的检测板枢转支承座11,在检测平台1朝向上的一侧并且在对应于检测板枢转支承座11的右前方的位置以纵向状态设置有一检测板限位杆12;示出了一凸轮检测枢转支承机构2,该凸轮检测枢转支承机构2设置在检测平台1的右端朝向上的一侧并且位于检测平台1的宽度方向的居中位置;示出了一凸轮轮廓面贴靠支承机构3,该凸轮轮廓面贴靠支承机构3转动地设置在前述检测板枢转支承座11上,并且该凸轮轮廓面贴靠支承机构3的前端在对应于前述凸轮检测枢转支承机构2的左侧的状态下空套在前述检测板限位杆12上;示出了一凸轮轮廓面偏差值显示机构4,该凸轮轮廓面偏差值显示机构4设置在凸轮轮廓面贴靠支承机构3的后端;示出了一测前校正芯杆5,该测前校正芯杆5在对应于前述凸轮检测枢转支承机构2的左侧与前述凸轮轮廓面贴靠支承机构3的前端右侧之间的位置插拔配合在前述检测平台1上;示出了一检测板推力机构6,该检测板推力机构6在对应于前述凸轮轮廓面贴靠支承机构3的前端左侧的位置设置在前述检测平台1朝向上的一侧并且在对凸轮检测状态下与凸轮轮廓面贴靠支承机构3的前端左侧面接触。
24.在本实施例中,前述的宽度方向即为检测平台1的短边方向,该短边方向即为图1所示位置状态的自前向后的方向,前述的长度为长边方向,图1所示位置状态的自左向右的方向。
25.前述检测板枢转支承座11通过间隔分布的检测板枢转支承座固定螺钉111固定在
前述检测平台1的左端朝向上的一侧,并且在检测板枢转支承座11的上端向上延伸有一直径小于检测板枢转支承座11的直径的检测板轴承配合轴头112;前述检测板限位杆12的下端与检测板限位杆座121固定,而该检测板限位杆座121在对应于前述检测板枢转支承座11的右前方的位置优选以焊接方式与检测平台1朝向上的一侧固定;前述凸轮轮廓面贴靠支承机构3与前述检测板轴承配合轴头112转动配合;前述凸轮轮廓面偏差值显示机构4随前述凸轮轮廓面贴靠支承机构3绕前述检测板轴承配合轴头112的转动而转动;前述测前校正芯杆5的下端在对应于凸轮检测枢转支承机构2的左侧的位置与测前校正芯杆固定座51插拔配合,而该测前校正芯杆固定座51与前述检测平台1朝向上的一侧固定;前述凸轮轮廓面贴靠支承机构3在前述检测板推力机构6对其前端左侧面施加推力的状态下与检测过程中临时转动地套置在凸轮检测枢转支承机构2上的凸轮轮廓面贴靠。由图2所示,前述测前校正芯杆固定座51具有一测前校正芯杆插孔511,前述测前校正芯杆5与该测前校正芯杆插孔511插拔配合。
26.前述凸轮检测枢转支承机构2包括一凸轮支承轴承座21和一凸轮支承轴承22,凸轮支承轴承座21设置在前述检测平台1的右端朝向上的一侧并且通过凸轮支承轴承座固定螺钉211与前述检测平台1固定,在该凸轮支承轴承座朝向上的一侧的中心位置向上延伸有一直径小于凸轮支承轴承座21的直径的凸轮临时套置轴212,凸轮支承轴承22套置在凸轮临时套置轴212上并且该凸轮支承轴承22的底部的四周支承在凸轮支承轴承座21朝向上的一侧的四周边缘部位;在检测凸轮曲线的过程中,凸轮临时转动地套置在凸轮临时套置轴212上并且凸轮的底部支承于凸轮支承轴承22上;前述的凸轮支承轴承22为压力轴承。
27.请参见图2,上面提及的凸轮包括一标准凸轮7和一被检测凸轮8,在检测状态下,即在检测凸轮曲线的过程中,标准凸轮7和被检测凸轮8自下而上依次套置在前述凸轮临时套置轴212上。本实用新型中所述的凸轮曲线实质上为凸轮轮廓面。
28.继续见图1,前述凸轮轮廓面贴靠支承机构3包括下检测板31、上检测板32、下检测盘33、上检测盘34和挡套35,下检测板31的长度方向的中部转动地套置在前述检测板轴承配合轴头112上,在下检测板31的前端朝向上的一侧构成有一下检测盘腔311,在下检测板31上并且在对应于下检测盘腔311的后方的位置开设有一下检测板限位杆让位孔312,上检测板32位于下检测板31的上方,该上检测板32的长度方向的中部同样转动地套置在前述检测板轴承配合轴头112上,在上检测板32的前端朝向上的一侧构成有一上检测盘腔321,在上检测板32上并且在对应于上检测盘腔321的后方的位置开设有一上检测板限位杆让位孔322,该上检测板限位杆让位孔322与前述下检测板限位杆让位孔312相对应,下检测盘33设置在前述下检测盘腔311内并且与下检测板31的前端固定,上检测盘34设置在前述上检测盘腔321内并且与上检测板32的前端固定,挡套35在对应于上检测板32的上方的位置固定在前述检测板轴承配合轴头112上,并且由配设在挡套35上的锁止螺钉351锁定;在对临时转动地套置在前述凸轮临时套置轴212上的凸轮(指被检测凸轮8)检测凸轮曲线的过程中,前述下检测盘33以及上检测盘34与凸轮轮廓面贴触;前述凸轮轮廓面偏差值显示机构4设置在前述下检测板31的后端并且与上检测板32的后端的右侧面贴触;设置在前述检测平台1朝向上的一侧的前述检测板推力机构6与前述下检测板31以及上检测板32的前端左侧面接触;前述检测板限位杆12的上端由下而上依次穿过前述下检测板限位杆让位孔312以及上检测板限位杆让位孔322。
29.在前述下检测板31的长度中部设置有一下检测板轴承313,而在前述上检测板32的长度方向的中部设置有一上检测板轴承323,下检测板轴承313以及上检测板轴承323的不转动的内圈套固在前述检测板轴承配合轴头112上;前述下检测板限位杆让位孔312以及上检测板限位杆让位孔322为椭圆形孔。
30.在前述下检测盘腔311朝向上的一侧并且位于中央位置构成有一下检测盘配合轴头3111并且在围绕该下检测盘配合轴头3111的四周间隔配设有一组下检测盘固定螺钉3112,在下检测盘33的中心位置开设有一下检测盘配合轴头孔331,并且在该下检测盘配合轴头孔331的四周间隔开设有一组下检测盘固定螺钉孔332,前述下检测盘配合轴头3111探入前述下检测盘配合轴头孔331内,前述的一组下检测盘固定螺钉3112旋入前述下检测盘固定螺钉孔332内;在前述上检测盘腔321朝向上的一侧并且位于中央位置构成有一上检测盘配合轴头3211并且在围绕上检测盘配合轴头3211的四周间隔配设有一组上检测盘固定螺钉3212,在上检测盘34的中心位置开设有一上检测盘配合轴头孔341并且在围绕该上检测盘配合轴头孔341的四周间隔开设有一组上检测盘固定螺钉孔342,前述上检测盘配合轴头3211探入前述上检测盘配合轴头孔341内,前述的一组上检测盘固定螺钉3212旋入前述上检测盘固定螺钉孔342内。
31.继续见图1,前述凸轮轮廓面偏差值显示机构4包括一百分表固定座41和一百分表42,百分表固定座41通过百分表固定座螺钉411固定在前述下检测板31的后端朝向上的一侧,并且该百分表固定座41具有一百分表顶针套固定槽412,百分表42通过百分表顶针套421在对应于百分表顶针套固定槽412的位置以水平悬臂状态与百分表固定座41固定并且由配设在百分表固定座41上的顶针套固定槽夹紧螺钉413夹紧,百分表42的百分表顶针422伸展到百分表顶针套421外并且与前述上检测板32的后端的右侧面贴触。
32.前述检测板推力机构6包括推力弹簧螺杆座61、上推力弹簧螺杆62、下推力弹簧螺杆63、上推力弹簧64和下推力弹簧65,在推力弹簧螺杆座61的下端构成有一推力弹簧螺杆座固定柱611,该推力弹簧螺杆座固定柱611的底部固定在前述检测平台1朝向上的一侧,上推力弹簧螺杆62以及下推力弹簧螺杆63彼此上下横向平行,并且左端与推力弹簧螺杆座61固定,而右端以水平悬臂状态分别对应于前述上检测板32以及下检测板31的前端左侧,上推力弹簧64套置在上推力弹簧螺杆62的右端并且该上推力弹簧64的右端与上检测板32的前端左侧面接触,下推力弹簧65套置在下推力弹簧螺杆63的右端并且该下推力弹簧65的右端与下检测板31的前端左侧面接触。
33.由图1所示,在前述检测平台1上并且在对应于前述推力弹簧螺杆座固定柱611的位置固定有一固定柱座6111,推力弹簧螺杆座固定柱611的下端与该固定柱座6111固定。
34.前述的固定柱座6111为一外六角螺母并且与前述检测平台1朝向上的一侧焊接固定,前述推力弹簧螺杆座固定柱611的下端以螺纹固定方式与固定柱座6111固定,即以螺纹固定方式与外六角螺母的内螺纹固定。
35.应用例:
36.请参见图2并且结合图1,在图2中示出了上面已提及的并且在检测时套置在凸轮临时套置轴212上的标准凸轮7和被检测凸轮8,在对被检测凸轮8的凸轮曲线进行检测之前,先将一把杆9插入构成于标准凸轮7上的标准凸轮把杆临时插入孔(图中未示出)以及被检测凸轮8上的被检测凸轮对把杆临时插入孔81,也就是说把杆9同时插置于标准凸轮7与
被检测凸轮8上(检测完成后撤离)。同样在检测之前,将测前校正芯杆5插置于测前校正芯杆固定座51的测前校正芯杆插孔511,使下检测盘33以及上检测盘34的盘缘贴靠于测前校正芯杆5,接着对百分表42调零操作,使百分表的表值指针423指向百分表42的示值的零位置,再接着拔除测前校正芯杆5,此时在检测板推力机构6的结构体系的上推力弹簧64以及下推力弹簧65分别同时对上检测板32以及下检测板31的前端左侧面的推力下,使上检测盘34以及下检测盘35分别与被检测凸轮8的凸轮曲线即轮廓面以及标准凸轮7的凸轮曲线即轮廓面接触。检测者通过前述把杆9使标准凸轮7以及被检测凸轮8绕前述凸轮临时套置轴212转动,当被检测凸轮8的凸轮曲线即轮廓面存在瑕疵例如凸起或凹陷的偏差情形时,会使上检测板32的后端产生向左或向右的偏摆,上检测板32的后端的前述偏摆会使其后端右侧面对百分表顶针422产生作用,并且同时由表值指针23指向正偏差示值或负偏差示值,检测人员可凭此示值而判定被检测凸轮8的合格与否。具体而言,不论是出现正偏差示值还是负偏差示值,只要偏差示值超出了规定要求的范围,被检测凸轮8便判为不合格。在对前一个被检测凸轮8检测完毕后,无需再全面重复上述测前准备的动作过程,而只需要拔离把杆9,将检测完毕的被检测凸轮8取离,百分表回零(百分表指针23指向零位值),将下一有待于检测的被检测凸轮8放置到凸轮临时套置轴212上并使其支承在先前放入的标准凸轮7上,再插入把杆9进行与上述雷同方式的检测。由于每检测一个被检测凸轮8所耗费的时间仅为2min左右,因而效率是十分令人满意的。
37.综上所述,本实用新型提供的技术方案弥补了已有技术中的缺憾,顺利地完成了发明任务,如实地兑现了申请人在上面的技术效果栏中载述的技术效果。