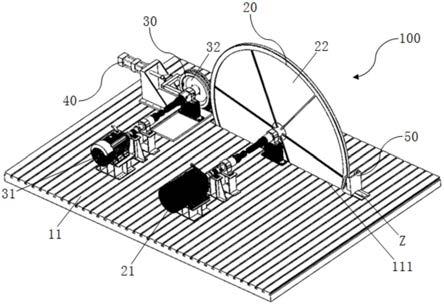
1.本实用新型属于轨道交通领域,具体涉及一种轮轨黏着特性模拟测试装置。
背景技术:2.目前铁道车辆的主要制动方式都是通过车轮和钢轨之间传递的黏着力来实现,轮轨黏着是制约高速铁路运营安全和速度的关键性问题。轮轨间黏着力不足时,极易发生滑行甚至抱死,使得车轮踏面和钢轨出现擦伤以及剥离等损伤。车轮和钢轨的擦伤将会成为列车运行过程中的随机激扰,给列车运行过程中的稳定性和平稳性带来隐患,这种外部激扰会降低列车乘坐舒适度,引发随机振动和噪声,另外激扰会加大对轮对的冲击载荷,降低车轴、滚动轴承和钢轨等部件的寿命,提高车辆和钢轨的维护成本。更为严重的是,黏着力不足会带来制动力降低,迫使制动距离增加,不能做到快速停车,甚至会发生冲出站台、列车相撞等重大安全事故。
3.轮轨关系问题是轨道交通系统的基础性问题,而轮轨关系试验台是研究轮轨关系问题的重要技术装备。轮轨关系试验台按照试验对象可分为整车试验台、转向架试验台、单轮对试验台、单车轮试验台;按照功能试验台可分为滚动试验台、振动试验台和滚动振动试验台。
4.目前国内外对轮轨黏着问题的研究由于受到设备的限制大多局限于中低速。随着我国高速重载铁路的快速发展,轮轨黏着特性与防滑控制问题急需进行理论和试验研究。
5.1986年,西南交通大学王夏鍫教授主持并研制成功国内第一台jd-1型轮轨摩擦学模拟试验机,该试验机与美国伊利诺斯理工学院在1981年研究的iit-gmemd轮轨关系试验机原理相似,采用一个按一定比例制作的车轮模拟实际的车轮,采用一个轨道轮来模拟轨道,模拟比为1:4,轨道轮和车轮可分别由电机驱动,设计有专门的加载装置在车轮上施加垂向、横向载荷,并可以模拟实际运行,对车轮施加激振,配置专门的传感器测试轮轨之间的载荷并反馈到控制台。jd-1型试验机能够完成各种工况下的轮轨磨损试验,包括:直线工况和任一冲角工况,不同横向力和垂向力比值的工况,轮轨表面不同润滑介质的工况,任何载荷下的牵引工况、制动工况,轨道上蛇行运动有关摩擦学研究等。同时,该试验机可进行不同轮轨几何型面和不同轮轨材料匹配的摩擦学试验。jd-1型轮轨摩擦学模拟试验机设计新颖,测试周期短,测试手段先进,建成后完成了《25t轴重货车轮轨模拟试验研究》等诸多省部级课题,并在1991年获得铁道部科学技术进步二等奖。2009年,西南交通大学摩擦学研究所通过该试验机完成轮轨黏着特性的研究,得到轮轨黏着特性与蠕滑率的关系以及轮轨最大接触力位置等试验结论。
6.1994年,西南交通大学牵引动力国家重点实验室研制成功国内第一台机车车辆整车滚动振动试验台。与jd-1型试验机原理相似,该试验台也是通过一个轨道轮来模拟轨道,采用实际的车辆进行试验,由轨道轮带动车轮旋转来模拟车辆的行驶。试验台能够进行轮轨蠕滑系数研究和接触蠕滑理论验证、车辆运行平稳性、车辆蛇行运动稳定性、曲线通过动态模拟、车辆轮轨黏着利用、踏面磨损等试验研究。试验台最大电机功率1200kw,最高试验
速度400km/h,最大可施加25t轴重载荷,轨距可实现1000mm-1676mm可调,能够对轴距1600m-2800mm的转向架进行试验。2005年,张立民、张卫华教授等在该试验台上完成轮轨波磨再现试验。试验采用的是原型尺寸转向架,试验针对6mm,8mm等不同横移量以及270hz,445hz以及1388hz等不同垂向振动频率等参数对轮轨波磨的影响进行研究。
7.1994年浙江大学机械设计研究所,陈扬枝等自行研制了dlg1/15轮轨模拟试验机。该试验机由c6120型车床改装成,通过车床主轴带动轨道轮旋转,再通过轨道轮带动车轮旋转,模拟实际的轮轨接触。试验中采用的车轮是将实际车轮的轮缘小半径r14缩小为r5,将钢轨轨距角的圆弧半径,由原来的r13缩小为r3,改变这些参数后,车轮外径取φ67mm,并且在不同的试验中采用不同的半径,轨道轮外径取400mm。车轮的磨耗量通过称重法来测量。通过该试验机,陈扬枝等完成了轮轨的硬度、速度、冲角等对轮轨磨损的影响等重要的试验。
8.2010年4月中国铁道科学院与德国rank公司签订了比例为1:1,最高速度500km/h的高速轮轨关系试验台的订购协议。该试验台计划于2011年年底建成并投入使用,试验采用的是全尺寸的轮对,最大试验轴重为50t,能够对高速、重载轮轨关系中蠕滑、黏着、轮轨磨耗、接触疲劳等进行试验,该试验台的建成将极大的提高我国铁路轮轨关系的研究能力。
9.综合国内外各种轮轨关系试验台的发展,在2005年以前的试验台均采用轮-轮接触来模拟实际的轮-轨接触,2005年德国的道岔通过测试试验台和2009年日本的新型蠕滑率测试试验机已采用轮-轨接触来模拟实际轮-轨接触。可以看出,在轮轨关系试验的发展过程中,研究人员已逐渐尝试采用轮-轨接触方式对实际的轮轨关系进行试验研究。虽然采用轮-轮接触在一定程度上能较好的模拟轮-轨接触情况,但是,与实际运行中的轮轨关系仍有一定的差距。
10.以上的试验机均为对实际轮轨进行缩尺比例后的试验机,在这类试验机中,轮对模拟轮压覆在轨道模拟轮的上端,通过对轮对模拟轮施加阻碍力矩从而实现实际轮轨制动状态的模拟。
11.综上,目前的实验机存在着以下无法克服的缺陷:1.实践证明越是接近真实比例的试验机试验结就越接近真实情况,缩尺比例的试验机实验结果可靠性不高,且不利于模拟高速工况下的轮轨黏着特性。同时,尽管有部分基于全尺寸试验台进行的黏着特性研究,但其主要是针对牵引工况进行设计,不能充分反映制动黏着特性;2.由于轮轮接触和轮轨接触时,接触点处截面曲率半径的不同,轮轮接触生成的接触斑形状也与轮轨接触时的不同。经研究发现,缩尺比例下的轮轮接触与实际的轮轨接触相比较,由于曲率半径的不同,前者生成的接触斑面积小于后者,进而导致同材料同轴重条件下的轮轮接触与轮轨接触时蠕滑特性的差异,可见,缩尺比例下的轮轮接触与实际线路的轮轨接触相比,仍存在较大差距。
技术实现要素:12.针对现有技术的不足,本实用新型提供一种轮轨黏着特性模拟测试装置,能够大大提高对轮轨黏着特性的模拟精确度且能够显著缩小占用空间。
13.为实现上述目的,本实用新型提供了如下技术方案为:
14.一种轮轨黏着特性模拟测试装置,其特征在于,包括:基座,具有水平安装板;轨道
模拟组件,设置在水平安装板上,包括第一驱动电机和安装在第一驱动电机的输出端的最终轨道模拟轮;轮对模拟组件,设置在水平安装板上,包括第二驱动电机和安装在第二驱动电机的输出端的轮对模拟轮;以及径向加载汽缸,设置在水平安装板上,与最终轨道模拟轮分别位于轮对模拟轮的相对两侧,径向加载汽缸的输出端朝向轮对模拟轮的周面且径向加载汽缸的输出端沿轮对模拟轮的径向设置,其中,最终轨道模拟轮和轮对模拟轮组成摩擦轮传动机构,第一驱动电机和第二驱动电机的输出轴均水平设置。
15.优选地,本实用新型还包括刹车件,设置在水平安装板上,与轮对模拟轮分别位于最终轨道模拟轮的相对两侧,刹车件朝向最终轨道模拟轮的周面可移动地设置。
16.进一步地,水平安装板的上端面预设有移动直导轨,刹车件竖直设置在移动直导轨上,刹车件用于沿最终轨道模拟轮的径向朝向或背向最终轨道模拟轮的周向进行移动。
17.优选地,水平安装板具有避让通孔,最终轨道模拟轮通过避让通孔穿过水平安装板。
18.优选地,最终轨道模拟轮的旋转平面与轮对模拟轮的旋转平面的夹角为arctg(1/15)。
19.优选地,水平安装板的上端面具有多条平行的“t”型凹槽,轨道模拟组件、轮对模拟组件以及径向加载汽缸均通过与“t”型凹槽的螺栓结合可拆卸地设置在水平安装板上。
20.优选地,第一驱动电机的输出轴和第二驱动电机的输出轴上均对应设置有第一扭矩传感器、第二扭矩传感器。
21.与现有技术相比,本实用新型的有益效果是:
22.1.因为本实用新型的轮轨黏着特性模拟测试装置包括:基座、轨道模拟组件、轮对模拟组件以及径向加载汽缸,最终轨道模拟轮和轮对模拟轮组成摩擦轮传动机构,第一驱动电机和第二驱动电机的输出轴均水平设置,因此,本实用新型的轮轨黏着特性模拟测试装置能够以水平分布的模拟形式大大降低了对空间的占用且便于进行相关组成构件的调整。
23.2.因为本实用新型还包括刹车件,与轮对模拟轮分别位于最终轨道模拟轮的相对两侧,刹车件朝向最终轨道模拟轮的周面可移动地设置,因此,本实用新型通过刹车件对最终轨道模拟轮施加制动力矩,从而能够使得刹车件的结构简单且具有良好的制动效率。
24.3.因为本实用新型的水平安装板具有避让通孔,最终轨道模拟轮通过避让通孔穿过水平安装板,因此,本实用新型通过避让通孔使得最终轨道模拟轮的重心更加靠近水平安装板的板面,从而提升了本实用新型的结构稳定性。
附图说明
25.图1为本实用新型的实施例的轮轨黏着特性模拟测试装置的立体示意图;
26.图2为本实用新型的实施例的轮轨黏着特性模拟测试装置的俯视图;
27.图3为本实用新型的实施例的蠕滑率-黏着系数曲线;
28.图中:100、轮轨黏着特性模拟测试装置,11、水平安装板,111、避让通孔,20、轨道模拟组件,21、第一驱动电机,22、最终轨道模拟轮,30、轮对模拟组件,31、第二驱动电机,32、轮对模拟轮,α、旋转平面夹角,40、径向加载汽缸,50、刹车件、z、移动直导轨。
具体实施方式
29.为了使本实用新型实现的技术手段、创作特征、达成目的与功效易于明白了解,以下实施例结合附图对本实用新型的一种轮轨黏着特性模拟测试装置作具体阐述,需要说明的是,对于这些实施方式的说明用于帮助理解本实用新型,但并不构成对本实用新型的限定。
30.如图1所示,本实施例中的轮轨黏着特性模拟测试装置100,包括基座(附图中未标出)、轨道模拟组件20、轮对模拟组件30、径向加载汽缸40以及刹车件50。
31.基座具有水平安装板11,轨道模拟组件20、轮对模拟组件30、径向加载汽缸40以及刹车件50均设置在水平安装板11的上端面,具体地,水平安装板11上端面具有多条平行的“t”型凹槽,轨道模拟组件20、轮对模拟组件30、径向加载汽缸40以及刹车件50均通过与“t”型凹槽的螺栓结合可拆卸地设置在水平安装板11上。
32.水平安装板11还具有避让通孔11,且避让通孔11为长方形通孔。
33.轨道模拟组件20包括第一驱动电机21和安装在第一驱动电机21的输出端的最终轨道模拟轮22,第一驱动电机21的输出轴水平设置,最终轨道模拟轮22通过避让通孔11穿过设置在水平安装板11上,具体地,第一驱动电机21输出第二驱动力矩,第一驱动电机21上设置有第一扭矩传感器(附图中未示出),用于采集第二驱动力矩的数值。
34.轮对模拟组件30包括第二驱动电机31和安装在第二驱动电机31的输出端的轮对模拟轮32,第二驱动电机31的输出轴水平设置,最终轨道模拟轮22和轮对模拟轮32组成摩擦轮传动机构,具体地,第二驱动电机31输出第一驱动力矩,第二驱动电机31上设置有第二扭矩传感器(附图中未示出),用于采集第一驱动力矩的数值。
35.如图2所示,最终轨道模拟轮22的旋转平面与轮对模拟轮32的旋转平面的夹角为α,即为上述的arctg(1/15)。
36.径向加载汽缸40与最终轨道模拟轮22分别位于轮对模拟轮32的相对两侧,径向加载汽缸40的输出端朝向轮对模拟轮32的周面且径向加载汽缸40的输出端沿轮对模拟轮32的径向设置,即最终轨道模拟轮22对轮对模拟轮32周面产生的接触正压力与径向加载汽缸40推动力之间符合平行四边形法则。
37.刹车件50与轮对模拟轮32分别位于最终轨道模拟轮22的相对两侧,刹车件50朝向最终轨道模拟轮22的周面可移动地设置,在本实施例中,刹车件50为放样截面呈“u”型的直线放样实体,刹车件50竖直设置,开口朝向最终轨道模拟轮22的周面设置,并且通过预设在水平安装板11上端面的移动导轨z上,能够沿最终轨道模拟轮22的径向朝向或背向最终轨道模拟轮22进行移动,刹车件50用于通过对最终轨道模拟轮22施加摩擦力来模拟实际列车刹车时的制动力矩。
38.本实施例中轮轨黏着特性模拟测试装置100的实施过程如下:
39.首先,分别启动第一驱动电机21和第二驱动电机31;然后,分别将第一驱动电机21和第二驱动电机31的运行模式调节为恒转矩输出模式;接着,启动径向加载汽缸40及刹车件50,并实时采集用于计算黏着系数和滑移率的相关数据;接着,当滑移率达到试验预设值时则停止数据采集结束一次试验,如若一直未达到预计效果为了试验安全,调整第一驱动电机21和/或第二驱动电机31的恒转矩输出设置来提高刹车件50对最终轨道模拟轮22的摩擦力,使得轮对模拟轮32和最终轨道模拟轮22速度同步后再停止本次试验;接着,重复多次
测量以排除随机误差;接着,计算得出滑移率,绘制如图3所示的黏着系数-滑移率关系曲线并捕捉极值点;最后,通过设置不同的第一驱动力矩和第二驱动力矩的组合对不同行驶速度下的列车进行模拟,从而测量得到的多组黏着系数-滑移率关系曲线,生成三维曲面并得到作为最终测量结果的黏着系数极值点连线。
40.具体地,蠕滑率-黏着系数曲线涉及的参数如下:
[0041][0042]
μ表示黏着系数,f表示黏着力,n表示垂向正压力。
[0043][0044]
t1、t2分别为第一驱动力矩和第二驱动力矩,ir为最终轨道模拟轮的转动惯量,表示最终轨道模拟轮的线速度的导数,r表示最终轨道模拟轮的公称。
[0045]
具体地,轮对模拟轮32的线速度与最终轨道模拟轮22的线速度的大小关系包括大于、等于以及小于,当轮对模拟轮32的线速度大于最终轨道模拟轮22的线速度时,本实用新型模拟车轮对的牵引加速状态,当轮对模拟轮32的线速度等于最终轨道模拟轮22的线速度时,本实用新型模拟车轮对的匀速运动状态,当轮对模拟轮32的线速度小于最终轨道模拟轮22的线速度时,本实用新型模拟车轮对的制动运动状态。轮对模拟轮32和最终轨道模拟轮22的摩擦形式包括干摩擦、颗粒摩擦、水摩擦以及油摩擦,分别对应正常环境场景、沙尘环境场景、水汽环境场景以及含油环境场景的模拟。
[0046]
上述实施方式为本实用新型的优选案例,并不用来限制本实用新型的保护范围,本领域普通技术人员在所附权利要求范围内不需要创造性劳动就能做出的各种变形或修改仍属本专利的保护范围。